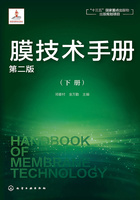
12.4 相转化成膜机理
12.4.1 铸膜液体系热力学
聚合物分离膜目前已在工业上得到广泛应用,各应用领域均对膜材料和膜结构提出了不同的要求,对于微滤和超滤膜,膜的孔隙率和孔径将最终决定其过滤效率,而对于气体分离膜而言,膜材料的选择性、渗透性和致密皮层结构决定了其分离效率。要获得适用的膜结构,就需要对成膜机理进行研究,以实现对膜结构的控制,获得性能优异的选择性分离膜。从铸膜液到聚合物膜形成机理分别有:聚合物溶液直接玻璃化转化而凝胶固化、贫相的成核与生长、富相的成核与生长及旋节线分相四个基本过程[378-380]。因此,成膜机理的研究一直是膜研究领域中非常重要的部分。
(1)液-液相分离过程
Loeb-Sourirajan法所得到膜结构是由液-液相分离产生的,其结构将取决于铸膜液体系的相图形态。一般高分子铸膜液体系包含聚合物、溶剂、非溶剂三元组分,但为了调节膜结构、改善膜性能,往往还在铸膜液中加入其他添加剂,因此高分子铸膜液体系通常包含三元以上组分。但三元以上铸膜液体系的相图难以在平面上描述。
图12-50是三元体系等温自由能曲面,当均匀聚合物溶液由于非溶剂浸入变成不稳定时,将导致液-液相分离使混合Gibbs自由能最低。如果体系组成落在B、D之间,将分成组成为B、D两相,该过程称为液-液相分离。相分离可依据成核-生长机制和旋节相分离机制。

图12-50 三元体系等温自由能曲面图
三元体系完整的相图如图12-51所示[379,380]。细分为四个区域,图中S是单相溶液区,由聚合物-溶剂轴和浊点线或称双节线(binodal)构成;浊点线右边B区-C区-D区是液-液两相区。在两相区,旋节线(spinodal)又划出亚稳区(B区与D区)和非稳区(C区),在各区域相分离机制是不同的。浊点线与旋节线之间是亚稳区,相分离是成核-生长机制,即当组分进入B区时,在稀相产生核,其中超过临界尺寸的核将不断成长,直至核聚结而形成膜结构[378-380];旋节线右边是非稳区,相分离是增幅分解机制,即膜液中浓度波动在非稳区将持续增长,最后形成网络结构膜[381]。结线表示富相与贫相对应的平衡浓度。玻璃化转变线以上A区域是固态单相区,当铸膜液组分进入该区形成固态。

图12-51 完整的三元聚合物/溶剂/非溶剂体系相图
A—玻璃化转变凝胶固化区;B、D—液-液两相区(成核-生长机制);C—液-液两相区(旋节相分离机制)
CP是临界点浓度,它决定液-液相分离时是稀相成膜还是富相成核。如果膜液在CP点以下D区相分离,初生核在富相产生,连续相是稀相,最终形成的膜结构将是松散的[379],没有机械强度而不能使用。因此实用的膜均要求在CP点以上发生相分离,使最终膜结构中富相是连续相,具备一定的机械性能。
在成膜过程中,聚合物溶液体系是否以及发生何种液-液分相过程主要由溶液的热力学因素所决定。而实际浸入凝胶分相制膜为一动力学过程,膜的具体结构形态通常由制膜过程的动力学因素所决定。当制膜液浸入凝胶浴后,薄膜内溶剂将向凝胶浴中扩散,而凝胶浴中的非溶剂也将向薄膜内扩散,浸入凝胶成膜为一动力学双扩散过程。随着双扩散过程的不断进行,体系将发生热力学液-液分相。当铸膜液沿路径SA变化直接达到玻璃化转变线,产生玻璃化转变,形成均质、致密玻璃态膜;当铸膜液沿路径S
B改变时,膜液组成将穿过浊点线进入亚稳区,这时在稀相产生初始核,大于临界核的初始核快速增长,导致液-液相分离,随着溶剂与非溶剂的不断交换,富相组分浓度将沿着浊点线上升,当穿过玻璃化转变线进入固相A区而被固化成膜。前者对应着皮层形成,后者对应着支撑层形成,因而可解释非对称膜结构的形成机理。
根据体系发生液-液分相的快慢,通常存在两种不同形式的液-液分相行为,即瞬时液-液分相(制膜液浸入凝胶浴后迅速分相成膜)和延时液-液分相(制膜液浸入凝胶浴中一定时间后才分相成膜)。上述两种不同的液-液分相行为原则上将形成两种不同的膜结构形态。瞬时液-液分相将得到相对多孔的膜表层,这种分相行为将形成多孔膜[如微滤(MF)和超滤(UF)膜]。而延时液-液分相通常将得到致密的膜表层,这种分相行为将形成具有致密表层和多孔底层的聚合物膜[如气体分离(GS)和渗透汽化(PV)膜]。
铸膜液所选用组分不同,相图也随之改变。图12-52是P84聚酰亚胺铸膜液体系对不同非溶剂的相图,水非溶剂性最强,乙醇与异丙醇差不多,丙酮非溶剂性最弱。

图12-52 P84/NMP/非溶剂相图[382]
根据分离对象要求,选定成膜聚合物材料,膜结构可以通过改变溶剂/非溶剂配对来调整,可以制造致密膜、非对称多孔膜(指状孔或海绵状孔)、非对称皮层致密膜(指状孔或海绵状孔)等。同一聚合物用不同配方制备的膜性能也不相同,表12-44是不同溶剂对膜性能的影响[383],用DMF作溶剂的聚酰亚胺(PI)膜渗透系数最小,但分离系数最高。
表12-44 不同溶剂对6FDA/PMDA-TMMDA聚酰亚胺膜分离性能的影响

注:6FDA/PMDA-TMMDA聚酰亚胺为六氟二酐/均苯四甲酸二酐、四甲基甲烷二胺聚酰亚胺。
表12-45列出了常用于制备气体分离膜的铸膜液体系,可供参考。
表12-45 气体分离膜的铸膜液体系

双节线通常用浊点法测定。常用测试方法有以下两种。①用非溶剂滴入事先配制好的不同浓度溶剂-聚合物溶液,计算浊点产生时的各组分浓度,得到浊点线。浊点用目视或光透射法观察,测试装置见图12-53。②把用同一非溶剂/溶剂比例下配制的不同聚合物浓度的溶液,冷却使各溶液依次变浊,得到浊点温度,内插得到所需温度的聚合物浓度;然后改变非溶剂/溶剂比例,得到浊点线,装置及数据处理见图12-54[385]。方法①装置简单,测试方便;方法②精度比较高。

图12-53 浊点测试装置
1—滴定管;2—温度计;3—磁力搅拌器; 4—分相滴定瓶;5—转子

图12-54(a) 浊点法测定浊点温度的装置示意图
1—激光;2—恒温槽;3—毛细管;4—旋转轮;5—电动机; 6—温度计;7—检测器;8—记录仪;9—低温恒温器

图12-54(b) 三种假定二元体系的浊点温度
为了得到完整的双节线,可使用外推式(12-69)[407]。
(12-69)
式中,ϕNS、ϕS、ϕP分别为非溶剂、溶剂和聚合物体积分数;a与b是截距与斜率,可由聚合物低浓度区数据求得,再外推到高浓度区求浊点线。对更高浓度区,式(12-69)线性关系不成立,浊点线只是近似值。
针对常用浊点滴定方法操作麻烦,Catharina Kahrs等[408]发展了一种新的相图分相结线(Tie-Tie法)的确定方法,见图12-55。首先将一定质量的聚合物膜液(PES/NMP)加入已知质量的离心管内,并向管内加入足够量的非溶剂水促使其发生液-液分相。通过改变非溶剂水的添加量,可以得到不同组成的液-液分相,即可以确定相图中的不同位置的两相结线。

图12-55 分相结线(双节线)实验测试手段
液-液分相后,将离心管放入离心机中充分离心,使得其中的两相发生彻底分离,富聚合物相即为离心管底部的凝胶状物质,其上则为贫聚合物相。在接下来的相组成分析过程中,针对溶剂是否具有挥发性将采取不同的方法。鉴于大多数铸膜体系的溶剂都是非挥发性的,故仅对此情况进行描述。
把贫聚合物相移走后分别对两相进行称重,并将富聚合物相通过定量DMAC的充分溶解形成均匀溶液。接下来即可对彻底分离后的贫聚合物相和富聚合物相进行组分分析:溶液中的固相聚合物浓度使用分子排阻色谱法确定,而溶剂/非溶剂等液相组成由气相色谱确定。
分子排阻色谱法首先需要确定PES浓度的标定曲线,即将PES溶解于DMAC中,并制备成PES含量w=0.036%~1.0%浓度不等的溶液,采用这些不同浓度的标本,通过分子排阻色谱法,得到不同的分析结果,进而形成标定曲线。PES分子量则通过已知不同分子量的聚苯乙烯所得到的标准曲线进行确定。
制备三种不同溶剂/非溶剂混合液相,并经过气相色谱分析,可以得到标准曲线用于各溶液样本中液相溶剂/非溶剂具体组成的标定。
图12-52和图12-56~图12-61列出常用铸膜液体相图可供参考。

图12-56 CA/[EMIM]OAc/Ac/NMP/H2O相图[384]
注:CA为醋酸纤维素;[EMIM]OAc为1-乙基-3-甲基咪唑乙酸盐; Ac为丙酮;NMP为N-甲基-2-吡咯烷酮;非溶液为H2O

图12-57 不同温度下三元体系相图[276]

图12-58 不同温度下PES/NMP/H2O相图[401]

图12-59 TPX/氯仿/醇类三元体系相图[394]

图12-60 6FDA-DAM/溶剂/非溶剂相图[401]

图12-61 PSF/混合溶剂(NMP/THF=70/30,质量比)+H2O四元体系相图[409]
(2)浊点线及结线计算[276,282,410-412]
由于实验手段限制,用浊点法只能测得低浓度聚合物铸膜液的浊点线,通常聚合物浓度在20%以内。对于聚合物浓度相对较高的体系,可以应用溶液理论来描述体系相图,其中Flory-Huggins理论由于其物理概念清晰,方程处理简单明了,并且积累了大量基础数据,在铸膜液相图计算中最为常用。
对三元体系铸膜液,根据Flory-Huggins理论,体系的Gibbs自由能用式(12-70)表示。
(12-70)
式中,下标1、2、3分别表示非溶剂、溶剂和聚合物;ni和ϕi分别表示组分i的摩尔数和体积分数;R、T分别为气体常数和热力学温度;χ12和χ13分别为非溶剂-溶剂和非溶剂-聚合物之间的相互作用参数;χ23为溶剂和聚合物之间的相互作用参数。
u2、u3、v3是浓度函数,按式(12-71)计算
(12-71)
组分i的化学位由式(12-72)计算
(12-72)
得到
(12-73)
(12-74)
(12-75)
式中,s=V1/V2,r=V1/V3分别是组分摩尔体积比。
成膜过程中,随着溶剂扩散出来和非溶剂进入,聚合物溶液中非溶剂含量的不断增加,当到达相图中的双节分相线组成时,体系原有的热力学平衡被打破,并将自发地进行液-液分相而形成的两相。这时,形成的两相应满足相化学势平衡。
根据两相平衡时化学位相等,
(12-76)
上标“'”表示聚合物富相或浓相,“″”表示聚合物贫相或稀相。
各相中各组分浓度应归一,即
(12-77)
方程(12-76)可用最小二乘法求解,目标函数F为
(12-78)
上式是多元非线性偏微分方程,可采用数值方法如单纯法、牛顿法[413]或Marquardt法求解,具体计算时使目标函数达到最小值,来决定稀相与富相组分浓度值,即得到浊点线和结线。
(3)旋节线及临界点计算
①旋节线方程 对组分数为n体系的旋节线方程为
(12-79)
式中,G表示独立组分变量Gij的n-1阶行列式,是参考组分摩尔体积;
表示单位体积Gibbs自由能。
②临界点方程 临界点位于旋节线顶点上,因此从对旋节线方程求导可得到临界点的附加条件
(12-80)
式中,是用单元取代G中的i行而形成的行列式。
对三元体系,如选择组分1作为参考组分,得到旋节线方程,
(12-81)
式中,
则得到临界点方程为
(12-82)
(4)二元组分相互作用参数χij
铸膜液体系是强非理想溶液,Flory-Huggins理论采用组分间相互作用参数来表征溶液的非理想性质。对三元组分体系,共有3个相互作用参数χij,非溶剂-聚合物和溶剂-聚合物可根据Hildebrand方程进行估算。
(12-83)
δ是溶解度参数,与其色散分量δd、偶极分量δp和氢键分量δh有关,可用式(12-84)计算。
(12-84)
常见聚合物和溶剂的溶解度参数见表12-42和表12-46。
表12-46 常用溶剂的溶解度参数[283]

对低分子非溶剂-溶剂的χij可以通过活度系数γ计算。
(12-85)
式中,ΔGE/RT是超额Gibbs自由能。
(12-86)
式中,γi、γj是活度系数,其值可从汽-液平衡数据求得,还可以通过其他途径如活度系数方程或基团加和法得到。表12-47列出常用聚合物/溶剂/非溶剂三元铸膜液的相互作用参数值,可供计算相图参考。
表12-47 聚合物/溶剂/非溶剂相互作用参数值[266]

Sadeghi等[414]对原有的Flory-Huggins模型进行修正,把Ruzette和Mayes可压缩正则解理论(compressible regular solution theory of Ruzette and Mayes)引入原始Flory-Huggins模型中,得到了新的与浓度有关的相关相互作用参数方程,无需事先实验测定相关相互作用参数。应用改进的模型计算得到的聚合物/溶剂/非溶剂三元体系相图,与实验结果吻合较好。Sadeghi等模型具有通用性,为相图计算提供了简单易行的方法。
(5)铸膜液固化过程-玻璃化转变分析
用液-液相分离制造的膜一般具有非对称结构。通常认为致密皮层由液-液相分离前聚合物溶液结晶、凝胶或玻璃化转变形成;多孔支撑层是由液-液相分离形成。
对于无定形聚合物溶液不存在结晶、半结晶现象,凝胶是有可能形成的,如图12-62。但通常凝胶过程很慢,如对PPO/DMAC体系,Gaides等[415]测定的结果表明,溶液形成凝胶至少需要1h,这远大于溶液在沉浸过程中产生沉淀所需的时间。

图12-62 PPO/三氯乙烯/甲醇三元体系的相图
Burghardt等[416]用溶液玻璃化转变来解释液-液相分离后溶液固化。聚合物溶液由于添加溶剂或非溶剂而使玻璃化转变温度Tg下降,制膜用的聚合物溶液的浓度在w=15%~40%。其Tg在室温以下,如图12-63所示。

图12-63 聚醚砜在各种溶剂中的玻璃化转变温度(虚线代表聚砜在DMAC中的玻璃化转变温度)
通常人们在室温制膜,固化也应在室温(25℃)进行。当将铸膜液浸入沉淀浴后,膜液中溶剂与凝胶浴中的非溶剂相互交换,产生液-液相分离,随着溶剂与非溶剂交换继续进行,富相聚合物浓度不断增加,玻璃化转变温度提高,如图12-63所示。达到室温(25℃)时,富相发生玻璃化转变而被固化[417]。
实验室及工业上制膜通常使用水作为沉淀剂。因为水与常用制膜溶剂的玻璃化转变温度接近(见表12-48),由水和溶剂组成的混合溶剂的聚合物溶液的玻璃化转变温度和纯溶剂溶液接近,如图12-64[417]。因此,在室温发生玻璃化转变时,无论是混合溶剂溶液还是纯溶剂溶液,聚合物浓度是相同的,固化线在相图上是一条水平线(见图12-62和图12-64)。
表12-48 溶剂、非溶剂玻璃化转变温度[417]


图12-64 纯NMP和H2O/NMP=1/9时玻璃化转变温度
不同溶剂组成的聚合物溶液在室温发生玻璃化转变时浓度是不同的(见图12-63),对不同溶剂聚合物溶液制成的铸膜液,如果玻璃化转变时,聚合物浓度越高,那么最终形成的膜皮层就越薄,膜的气体渗透量就越大。
曹义鸣等[411]应用聚合物自由体积理论计算PSF/DMAC/EtOH和PSF/DMAC/THF体系在发生玻璃化转变时的温度,其结果表明:上述两体系在发生玻璃化转变时,聚合物溶液的浓度高于PSF/DMAC体系,即当液-液相分离后,聚合物富相固化时的聚合物的浓度比PSF/DMAC体系更高,形成比PSF/DMAC体系更为致密的皮层。
12.4.2 铸膜液在蒸发过程传质动力学
用Loeb-Sourirajan法制造非对称膜,通常经过三个基本步骤,即配制铸膜溶液、铸膜液在空气中预蒸发和沉浸到非溶剂浴中凝胶,后两者是膜形态形成过程。在铸膜液配方给定后,后两者实际上决定着最终膜结构。在蒸发阶段,人们关心的是在沉浸前铸膜液中各组分浓度的改变。
传质动力学模型基于基本扩散方程和连续性方程,或利用不可逆热力学化学位梯度建立关联组分的通量微分方程,描述相分离前铸膜液组成随时间和空间分布,计算浸入瞬间的组成轨迹,根据组成轨迹曲线在相图位置、延迟时间和组分浓度分布等,判断相分离类型、解释非对称结构形成、皮层厚度或指状孔形成机理等。
传质动力学模型可分为两大类,一类是根据Fick定律建立的;另一类是根据不可逆热力学理论建立的,下面列出常见几类传质动力学模型,并给予简要说明。
(1)William模型(Fick型传质动力学模型)[418]
William结合气相传质,研究CA/丙酮两元体系传质动力学问题,如图12-65。考虑到随着丙酮蒸发,铸膜液将产生收缩,气-液相界面发生移动,推导出蒸发过程传质动力学方程。

图12-65 双组分制膜液蒸发成膜过程
①膜相传质动力学方程
(12-87)
②气相传质动力学方程
(12-88)
边界条件及初始条件
(12-89)
(12-90)
③膜厚变化方程
(12-91)
William用该模型研究蒸发过程中非对称膜结构的形成,表明:初生皮层形成时间随铸膜液厚度增加而增加;气相传质是影响膜相传质的重要因素。
(2)Shojaie模型(不可逆热力学型传质动力学模型)[419]
Shojaie等应用不可逆热力学理论,推导出CA/丙酮/H2O三元体系蒸发传质动力学方程(如图12-66)。他们注意到随着丙酮蒸发,膜液温度将下降,并给出相应的传热方程。

图12-66 干式铸膜形成过程的物理示意图
①传质动力学方程
膜相:
(12-92)
气相:
(12-93)
②传热方程
膜相:
(12-94)
支撑玻璃板:
(12-95)
界面移动:
(12-96)
用Shojaie模型可以研究蒸发过程温度、铸膜液组成等对成膜过程影响。研究表明:蒸发过程中膜相温度的下降,降低了可挥发性组分蒸气压,对传质影响很大。通过改变膜液组分浓度和铸膜液初始膜厚,用蒸发方法可以得到非对称膜、对称膜或致密膜等不同结构。如增加初始膜厚,将得到较厚皮层的非对称膜;减少铸膜液水含量,最后得到致密无孔膜。
Matsuyama等[420,421]研究了PVDF/DMF/H2O体系传质动力学过程,用传质动力学数学模型计算了PVDF/DMF铸膜液置于气相中水蒸气在膜液表面沉积及向内部传递的传质过程。计算得到的PVDF/DMF铸膜液吸收气相中水蒸气而产生液-液相分离现象以及铸膜液重量变化规律都与实验结果一致。此外,他们还根据熔点下降给出等温结晶线。
12.4.3 铸膜液在沉浸过程传质动力学
成膜过程伴随着溶剂和非溶剂的交换,相分离正是通过膜界面上溶剂和非溶剂交换使铸膜液组成穿入浊点线而达到的。因此相分离前铸膜液内组成轨迹线位置对膜结构形成至关重要。如图12-51所示,如果膜界面组成随着A途径变化,膜表面将由均相区进入凝胶区而发生玻璃化转变,最终得到具有致密皮层膜;如果膜界面组成随B途径进行,那么膜表面将直接进入液-液相分离区而分相,最后富相固化而得到多孔皮层膜。
铸膜液中组成随时间改变,由于通常膜厚很薄(几十至几百微米),并且有时膜是在沉浸瞬间形成,很难用实验手段在短时间内正确测定膜内组分浓度分布。因此通常采用适当的传质模型描述溶剂和非溶剂交换动力学,来了解膜内聚合物浓度变化途径。
传质动力学模型也可分为两大类,一类是基于Fick定律建立的;另一类是基于不可逆热力学理论建立的,下面列出常见几类传质动力学模型,并给予简要说明。
(1)Fick型传质动力学模型
①Mchugh模型[422] Mchugh和Yilmaz在忽略沉淀浴相传质阻力下,应用Fick扩散方程建立聚合物-溶剂-非溶剂三元体系在沉浸过程的传质动力学方程。为简化计算,他们采用拟二元方法,即把三元体系转化为二元问题处理。
膜相传质方程
(12-97)
边界条件:
(12-98)
初始条件:
(12-99)
(12-100)
明显地,膜液中溶剂快速扩散到沉淀浴中,沉淀浴中传质阻力不容忽视。如果铸膜液沉浸到非溶剂浴中将形成非对称膜结构;如果铸膜液暴露在空气中将导致多孔膜结构。因此,完整的传质动力学模型还应包括凝胶浴相传质动力学方程。
②Tsay模型[423] Tsay和Mchugh进一步发展Mchugh和Yilmaz的传质动力学模型,放宽了界面浓度不变的条件,假设界面浓度随时间变化。
膜相:
(12-101)
(12-102)
沉淀浴:
(12-103)
膜/浴界面移动:
(12-104)
用Tsay模型可以计算相分离延时时间,但计算结果同时也表明,Tsay模型中界面聚合物浓度随时间减少。这与通常在实验中观察到的界面聚合物浓度随时间增加的现象相悖。
(2)不可逆热力学型传质动力学模型
①Cohen传质动力学模型[424] Cohen等应用不可逆热力学理论建立的处理三元体系(H2O/丙酮/CA、H2O/乙酸/CA、EtOH/甲苯/PS)传质动力学方程,但仅考察膜侧传质动力学问题。
(12-105)
(12-106)
边界及初始条件
(12-107)
(12-108)
(12-109)
式中,m是固定在膜表面的移动坐标。把空间固定坐标转换到膜表面移动坐标是根据式(12-110)进行的。
(12-110)
在膜表面m=0,在膜和支撑界面上m=M。
Cohen等假设沉浸过程为稳态传质,由式(12-105)~式(12-110)推导出
(12-111)
式中,σ是膜-浴界面上溶剂自膜内往浴中扩散速率与非溶剂由浴中往膜内扩散速率的比值。代入化学位表达式,即可从上式计算膜内组成轨迹线。因Cohen等在计算中采用稳态假设,很明显与成膜过程非稳态传质矛盾,但可以从膜内组成轨迹线解释膜非对称结构产生机理。
一个简单的例子可说明Cohen等的工作是有缺陷的。当σ=1时,意味着溶剂自膜中扩散出的量与非溶剂扩散进入的量相等,这时聚合物浓度应保持不变,相图上组分轨迹线应是水平线,但计算结果并非如此。
②Reuvers模型[425,426] Reuvers和Smolders等把不可逆热力学理论和Stefan-Maxwell方程应用到CA/丙酮铸膜液沉浸到水浴中传质动力学研究,考虑了由于溶剂扩散到水浴中而产生的膜界面移动(如图12-67所示),建立CA/丙酮/H2O体系传质动力学模型。

图12-67 不同浸没时间下相分离过程的传质过程
膜相传质方程
(12-112)
(12-113)
水浴相传质方程
(12-114)
界面移动方程:
(12-115)
初始条件:
(12-116)
(12-117)
边界条件:
(12-118)
(12-119)
(12-120)
式中,下标p和b分别表示膜相和沉淀浴相;Lij是热力学唯象系数,根据Onseger倒易关系,Lij=Lji。式(12-115)是由于溶剂和非溶剂交换速率不相等导致界面发生移动的速度,边界条件式(12-118)意味着在任何时间界面两侧都处于相平衡。
计算步骤:
a.选定两相界面组分浓度;根据边界条件相平衡条件式(12-118),计算界面上浴侧组分浓度;
b.根据式(12-112)求膜侧组分的浓度分布;
c.由式(12-113)计算界面上溶剂自膜中流出的流量和非溶剂流入的流量;
d.根据式(12-115)计算界面移动速率;
e.由式(12-114)求浴中组分分布;
f.根据式(12-115)计算界面上非溶剂自浴中流出的流量和溶剂流入的流量;
g.比较c和f步骤得到的流量,如相等则计算结束,如不相等则返回步骤a重新计算,直到相等。
Reuvers模型采用化学位作为推动力和应用不可逆热力学理论处理非线性传质问题,避免了Fick扩散方程要处理扩散系数随浓度变化和耦合扩散等一些困难问题。
但由于Reuvers模型中假定界面上膜相与液相处于热力学平衡,而且在整个计算过程中平衡浓度值保持不变。这假设仅在短时间内成立。因此Reuvers模型虽然能正确预测瞬时相分离和延时相分离两种相转变现象存在,但不能准确预测相分离延时时间。
建立在连续性方程和扩散方程基础上的传质动力学模型十分复杂,其准确性依赖于组分化学位的热力学描述以及动力学参数、微分方程的边界条件和初始条件的确定是否正确。传质动力学模型存在以下不足:
a. Flory-Huggins理论是场平均理论,只适用于较高浓度聚合物溶液,但铸膜液相转变所产生的贫相和沉淀浴中聚合物浓度极低,可近似为零,采用Flory-Huggins理论计算化学位会带来较大的误差;
b.膜侧扩散方程建立在单一相基础上,只能描述分相前的传质行为,不能提供分相后到固化这段时间内的信息;
c.膜侧与浴侧边界上相平衡假定背离了成膜过程非平衡态事实;
d.伴随溶剂挥发,铸膜液温度将发生变化,存在热质耦合传递过程,应考虑温度影响[286]。
传质模型可以计算任何时间和膜内任何位置的组成浓度,作为一种初步的估算还是十分有用的。不断有学者进行研究,对上述模型进行了改进[427-430]。
Kim等[429]利用传质理论在铸膜液与凝胶浴界面处建立了新的边界条件,而不是基于铸膜液与凝胶浴之间的瞬时平衡假设,尤其适用于传质速度极快的条件。
Lee等[431]改进传质模型:a.除浓度梯度产生的扩散外,还考虑了密度差引起的对流对传质通量贡献,密度差对流可以使传质通量增加近两个数量级,这对早期非对称膜功能层形成有显著影响;b.铸膜液和凝胶浴非溶剂浴界面上的平衡浓度可变,从初始的非平衡值变化到平衡值,解除了铸膜液和非溶剂浴界面上浓度瞬时平衡假设。
为克服Flory-Huggins场平均理论不足, Akthakul等[432]采用晶格玻尔兹曼(LB)方法模拟非对称膜在非溶剂诱导相分离制备过程中的结构演化,晶格玻耳兹曼(LB)方法是一种能正确描述流体宏观行为的介观模型,粒子分布的统计平均值引起了宏观输运,动力学行为由Boltzmann方程的连续模型来描述。
Lin等[433]建立了新的耗散粒子动力学(DPD)模拟方法,用于研究非溶剂诱导相分离(NIPS)的成膜过程。考虑了溶剂-非溶剂相互作用、聚合物浓度和非溶剂温度等因素,研究膜非对称形态与致密皮层厚度、亚层多孔性等。
Junior等[434]建立了相场模型(phase-field model)方法,预测聚合物膜形态。采用依赖各组分体积分数关系的扩散通量方程,通过质量守恒定律和热力学方法检验了模型的一致性,该模型的应用不局限于旋节区域内聚合物初始浓度的计算。
Tang等[435]采用粗粒度的耗散粒子动力学(DPD)模拟方法,研究非溶剂诱导相分离(NIPS)过程中聚合物分子量对膜结构和形态的影响,得到了聚醚砜浓度对膜结构影响大于聚醚砜分子量影响的结论。
传质动力学模型是高度非线性偏微分方程组,且膜侧与浴侧组分浓度相差很大,方程求解有相当难度,需要很高技巧。Karode等[428]提出了一种改进算法,对三元铸膜液体系,在膜形成过程中允许对膜内组分扩散分布进行数值积分,而不需要像Reuvers等采用差分迭代;界面组成由一套联立方程计算,不需要用户对界面组成进行反复迭代,该算法很容易从三元体系扩展到四元体系。
蒙特卡罗方法被引入研究成膜过程相分离问题。He等[436]采用蒙特卡罗方法模拟了聚合物溶液中溶剂和非溶剂的扩散行为,以及旋节线分相到成核-生长的机理的转变机制。Liu等[437]使用蒙特卡罗方法和聚合物链胀落晶格模型,研究含两亲性嵌段共聚物制膜体系热力学和动力学行为。Wallace[438]采用蒙特卡罗方法研究了非对称膜的相分离问题。
虽然膜结构研究很大程度上依赖于利用扩散模型计算出的铸膜液组成变化,但实验方法如磁共振成像也被用来研究铸膜液中组分扩散现象,Laity等[439]用它来追踪二醋酸纤维素溶液在浸没水中凝固时的组成和结构变化。
12.4.4 传质动力学模型应用实例
传质动力学模型把铸膜液组成描述为空间和时间的函数,把某时刻组成在相图上表示构成组成轨迹线,不同时刻组成轨迹线构成铸膜液中各组分浓度变化的形貌。根据其形貌与相图各区域相对位置关系,可以得到一些预测膜结构的有用信息,例如:①膜的收缩程度;②界面处的聚合物浓度;③界面附近聚合物浓度较高区域的厚度;④聚合物浓度的整体分布。其中,第①点与最终膜的厚度有关,从第②、③点可以得到最终膜皮层结构的信息,而第④点则对应于膜的支撑层孔分布情况。尤其改变铸膜液配方时,比较不同配方的组成轨迹线可以定性预测配方对膜厚度、皮层结构和支撑层等影响。
(1)判断成膜机理-瞬时分相和延时分相
由模拟计算得到的组成轨迹线以及光透射实验,Reuvers等[425,426]提出了延迟时间的概念:根据铸膜液发生相分离的时间,把相分离分为瞬时相分离和延时相分离两类。瞬时相分离是指铸膜液置于气相中或沉浸到沉淀浴中时,相分离瞬间产生;而延时相分离则要经过一段时间后相分离才产生。两种不同相分离机制所得到的膜结构完全不同,瞬时相分离形成较薄皮层和多孔结构的非对称膜结构,而延时相分离则得到较厚致密的皮层和海绵状亚层结构,且随着延时时间的增长,形成的膜越致密。
采用光透射法可以测定铸膜液相分离时间,测试装置如图12-68所示[425]。方法:首先把一定厚度膜液刮在玻璃板上,然后膜面朝下放置在测试槽中,平缓地加入沉淀剂。沉淀剂与膜液接触瞬间设为时间t=0。当膜液未发生液-液相分离前,膜液是透明的,光穿过膜液强度不变,记录仪记录下一条直线。当膜液发生液-液相分离时,透过膜液的光强将明显减弱,这时所对应的时间即为膜液发生液-液相分离时间,如图12-69。

图12-68 用光透射法测定铸膜液相分离时间的实验设备
1—聚光源;2—凝胶浴;3—铸膜液;4—支撑玻璃板; 5—光接收器;6—光电转换器;7—记录仪

图12-69 透光率随时间的变化
Reuvers等[425]用传质动力学方程计算得到的组成轨迹线穿过三元相图中浊点线时间快慢来判断铸膜液是发生瞬时相分离还是延时相分离。如果轨迹线没有穿过浊点线而位于外侧,那么液-液相分离将在玻璃板侧膜液浓度开始改变时发生,即延时相分离。如果轨迹线很快穿过浊点线,进入液-液两相区,立即发生相分离,为瞬时相分离。
图12-36给出了流延制膜液浸入凝固浴瞬间聚合物薄膜内的组成变化曲线,对应以上两类相分离。图12-36(a)表明在制膜液浸入凝胶浴瞬间(t<1s),薄膜表层下面已迅速发生液-液分相——瞬时分相。而图12-36(b)则表明,当体系发生延时液-液分相时,在制膜液浸入凝胶浴瞬间(t<1s),薄膜表层以下的组成均未进入分相区域,仍处于互溶均相状态,未发生液-液分相,需再经过一定时间(几秒钟)的物质交换,才能进入液-液分相状态——延时分相。
(2)阐明膜非对称结构形成机理
图12-70是由Reuvers模型[426]计算得到的PES-NMP-H2O铸膜液内在沉浸过程的浓度分布。在很短时间内,膜内聚合物浓度为很陡的曲线,在膜-浴界面附近,PES浓度非常高,沿膜-支撑体侧方向,浓度急剧下降。固化后,将得到非对称结构膜,高浓度聚合物处成为致密皮层;而低浓度聚合物处形成多孔结构。从组成路径或浓度分布可以定性预测最终膜的皮层、亚层孔和支撑层孔结构。

图12-70 聚合物在铸膜液内沉浸过程中的浓度分布图
(3)通过计算机模拟计算,并与实验相结合,考察制膜工艺参数对膜结构及性能的影响[238,441,442]
①铸膜液聚合物浓度影响。图12-71是用传质动力学模型计算的铸膜液内组成轨迹线结果。从图中可见,铸膜液中聚合物初始浓度越高,膜-浴界面附近聚合物浓度也越高,最后得到膜皮层越厚,而且皮层上孔也越少,膜的渗透速率也越小。

图12-71 醋酸纤维素/二烷/水体系中不同醋酸纤维素浓度时铸膜液内组分轨迹
②凝胶浴组成影响。凝胶浴可用纯水作凝胶剂,也可用在水中加入一定量溶剂,不同组成凝胶浴对铸膜液相分离有很大影响,图12-72对不同组成凝胶浴所计算的CA/二烷/水三元体系铸膜液内组成轨迹线结果。凝胶浴采用纯水和w=0.185二
烷水溶液。从图中可见,两者均发生瞬时相分离,但随着凝胶浴中加入二
烷,组成轨迹线穿透浊点线的程度减弱,这意味着相分离时间延长。事实上,当凝胶浴中二
烷浓度超过w=0.19后,组成轨迹线不再穿过浊点线,发生延时相分离,这已为实验所证实[441,442]。

图12-72 在醋酸纤维素/二烷/水体系中改变
凝胶浴组成计算的铸膜液内组成轨迹线
③铸膜液中非溶剂影响。研究铸膜液组成时,常常考察如何调整铸膜液中聚合物和溶剂的比例,而实际上如向铸膜液加入非溶剂,对铸膜液相分离影响很大。随着铸膜液中加入的非溶剂量增加,组成轨迹线愈移近浊点线,发生相分离所需的时间愈短。当非溶剂浓度越过某值时,相分离类型也要发生改变,可以从延时相分离转为瞬时相分离,如图12-73和图12-74所示[441,442]。

图12-73 醋酸纤维素/丙酮/水体系随水在铸膜液中含量(w=0,12.5%和20%)变化的组分变化轨迹

图12-74 CA/丙酮/水体系铸膜液中加入不同量水的相分离时间
a、b延时相分离;c、d瞬时相分离
Radovanovic等[443]把Reuvers模型应用到异丙醇/DMAC/PSF三元体系。他们首先测定膜/沉淀浴界面上非溶剂、溶剂流量,通过流量拟合来计算传质模型中未知参数值;再用求得数值计算铸膜液从瞬时相分离转变(Ⅱ)到延时相分离(Ⅰ)的铸膜液初始浓度,与实验所得结果是相吻合的,如图12-75所示。

图12-75 异丙醇/DMAC/PSF三元体系中Ⅰ型和Ⅱ型相分离膜的初始聚合物浓度
④预测相转化法制备膜的形貌。Mohsenpour等[412]以Flory-Huggins理论为基础,构建以(溶剂-聚合物轴与双节线距离)/(溶剂-添加剂间相互作用参数)为无量纲热力学参数,考察了相互作用参数和组分(溶剂、非溶剂、聚合物和添加剂)摩尔体积对双节线和膜形态的影响。随着无量纲热力学参数的增大,膜形貌趋向于多孔。当双节线越接近溶剂/聚合物轴时,沉淀路径越快穿过双节线,从而导致较大的孔隙尺寸和指状形态。如果黏度显著增加,相分离速率降低,孔隙变小,形成海绵状形态。
在过去的几年里,有关相转化膜文献大量涌现,Guillen[444]综述了许多常用非溶剂诱导相分离聚合物膜的制备,讨论了膜制备的关键因素包括聚合物类型和浓度、溶剂类型、非溶剂类型和组成、聚合物溶液添加剂和膜浇铸条件,旨在选择合适的聚合物-溶剂-非溶剂体系和铸膜条件,为制备具有理想渗透分离性能、形态结构稳定的膜提供指导。