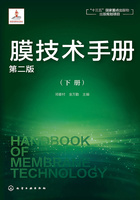
12.3 气体分离膜制造方法
有机聚合物膜从结构形态上可分为对称均质膜与非对称膜,其制膜技术存在很大的差异。同一种膜材料制成的分离膜,由于不同的制膜工艺和工艺参数,膜性能差别很大,所以制膜工艺对聚合物分离膜具有重要意义,制膜技术直接决定了膜的最终结构和性能。理想膜制备技术将使得膜保持接近或超过其材料的本征分离性能(表皮结构无孔缺陷),同时具有较大渗透通量(分离层超薄化),并具有较好的机械性能(具备机械支撑层)。
聚合物膜可以制成致密的或多孔的、对称的或非对称的、平板的或中空纤维的。气体分离膜常用的制造方法有[259]:熔融法、水上展开法、包覆法、相转变法和界面聚合法等。均质膜通过溶液浇铸、熔融挤压等方法来制备,其渗透通量很小,实际应用较少,一般用于表征膜材料性能。而非对称膜一般由超薄的致密皮层与多孔支撑层构成,由于非对称膜的通量大且易于大规模生产,目前大部分工业应用以非对称膜为主。根据制备方法,非对称膜制备可分为相转化法和复合膜法,而相转化法又是制造非对称膜的主要工艺,因此本节重点介绍相转化法制膜工艺。
12.3.1 烧结法
烧结法是把大小一定的聚合物微细粉末置于模具中,在一定温度下挤压,使粒子的表面变软而相互黏结形成多孔体,最后进行机械加工即得到膜[260]。
烧结法通常用来制造多孔膜,膜孔径大于1μm。
制膜过程中常掺进另一种不相熔的添加剂(如淀粉等),待烧结完成后,再萃取出。此法多用于制造聚乙烯和聚四氟乙烯等多孔膜。
12.3.2 拉伸法
拉伸法用于结晶聚合物制造微孔膜。它把部分结晶的聚合物薄膜,通过单向或双向牵伸,形成有微细裂纹的多孔膜。拉伸法[259,261]制造工艺首先用高速挤出聚合物,使聚合物在接近熔点下形成高取向结晶膜,冷却后,短时间内(数秒)拉伸到300%,破坏结晶构造,得到宽为20~250nm细长裂纹。
12.3.3 熔融法
对于没有适合溶剂的聚合物材料,通常采用熔融挤压法成膜。熔融法通常用来制造均质膜。它是把聚合物加热到熔融态,挤压成平板膜或由喷丝头挤出,冷却后可得到均质无孔膜[259]。熔融挤压法纺丝效率很高,可以高速纺丝,而且多孔喷丝头制造工艺也很成熟。
12.3.4 核径迹法
核径迹法[33,262]制造工艺大致可分两步,首先将聚合物薄膜暴露于重离子束中,受轰击发生高分子链降解;然后在酸浴中浸蚀,形成圆柱孔。可通过调节聚合物薄膜的性质、辐射条件、蚀刻时间和蚀刻温度等因素控制膜的孔径分布、孔道尺寸和孔隙率。如孔密度可由照射时间控制,调节酸处理时间和温度便可控制所需的孔径。核径迹法制得的膜孔径分布很窄,可以制成膜孔径在0.02~10μm不同规格的膜。应用中子蚀刻的高聚物材料主要有聚酯和聚碳酸酯两类。
12.3.5 水面展开法
水面展开法是将聚合物溶液倒在水面上,在表面张力作用下,铺展成薄膜,随着溶剂不断挥发,聚合物膜慢慢形成,得到固体薄膜[263]。这种薄膜机械强度差,需要将其覆盖到多孔基膜上制成复合膜,且要求采用多层覆盖。水面展开法装置简单,但在连续制膜过程中稳定性较差,铸膜液体系的溶剂必须和水不混溶,同时要求制膜环境非常洁净。
12.3.6 相转化法
相转化法利用铸膜液与周围环境进行溶剂、非溶剂传质交换,原来的稳态溶液变成非稳态而产生液-液相转变为两相:即最终形成膜的聚合物富相与形成孔的聚合物贫相,最后固化形成膜结构。这种方法操作简单,可用于制备各种形态的膜,因此成为最常用的制膜工艺。相转化膜有两个特点:皮层与支撑层为同一材料;皮层与支撑层同步制备形成。常用的相转化制膜方法有蒸汽诱导相分离法、溶剂蒸发凝胶法、热致相分离法和液-液相分离法等[264,265]。
12.3.6.1 蒸汽诱导相分离法
在利用相转化法制备高分子膜时,溶剂与非溶剂的交换对成膜速率有很大影响,而成膜速率又决定着最终形成的膜结构。若将初生态膜先置于非溶剂蒸汽氛围(常用水蒸气)中暴露一段时间,再将其浸没到非溶剂凝胶浴中固化成膜,被称为蒸汽诱导相分离法(VIPS)[266],如图12-31所示。多数研究认为,由于蒸汽中的非溶剂量有限,相分离在成膜过程中发生比较缓慢,膜的断面最终形成对称结构,避免了直接采用非溶剂诱导相分离法(NIPS)成膜时出现的大孔缺陷。

图12-31 蒸汽诱导相分离的工艺示意图
1,7—聚合物溶液;2—齿轮泵;3,8—芯液;4—中空纤维膜;5—蒸汽氛围;6—凝胶浴
聚合物浓度和环境湿度对蒸汽诱导分离膜的孔径结构有重要影响。从表12-33可以明显看到,随着相对湿度降低,水进入铸膜液中速度变慢,延缓相分离速度,粗化时间延长,形成较大的膜孔。铸膜液中聚合物浓度增加会增加黏度,限制聚合物迁移,导致膜孔变小[267]。
表12-33 相对湿度(RH)和聚合物浓度对聚砜膜孔径的影响 单位:μm

水蒸气诱导时间对暴露在空气侧的铸膜液组成及聚合物聚集状态都有影响(表12-34),当水蒸气诱导时间较短时,空气侧界面处铸膜液的溶剂挥发较少,因此,空气侧界面处铸膜液组成和聚合物聚集状态变化不大。但随着水蒸气诱导时间的延长,进入膜表面的水量增多,有利于聚合物贫相核的生长,因而水蒸气诱导时间从2min延长至5min时,膜的表面孔增大,数量增多,孔隙率增加。
表12-34 不同水蒸气诱导时间制得PVDF膜的孔隙率

膜气体通量见表12-35。水蒸气诱导时间较短时,溶剂与非溶剂的传质交换量少,此时浸入凝固浴,界面铸膜液发生快速凝胶分相,使表面孔的粗化生长终止,故气体通量较小;随着水蒸气诱导时间的延长,从环境中进入到铸膜液中的水量增多,膜的表面孔增大,孔的数量增多。而膜内为海绵状结构,连通性较好,所以气体通量增大较多。
表12-35 水蒸气诱导时间对PVDF膜的气体透过性能影响

测试条件:温度25℃。过膜压差:50kPa。
12.3.6.2 溶剂蒸发凝胶法
溶剂蒸发凝胶法是把包含聚合物、低沸点溶剂和非溶剂的铸膜液暴露在空气中,随着溶剂蒸发,铸膜液中非溶剂浓度不断增加,当铸膜液进入非稳态时,产生液-液相分离而形成膜[268]。用蒸发凝胶法可以得到具有致密皮层和多孔支撑层的非对称膜。
对多孔膜,铸膜液由聚合物和混合溶剂配制而成,混合溶剂中包括大量低沸点良溶剂和少量高沸点的不良溶剂。将铸膜液在支撑板上铺展后,易挥发的良溶剂迅速逸出,留下的是不易挥发的不良溶剂和聚合物,产生液-液相分离形成膜。
根据实际经验,溶剂与不良溶剂的沸点至少相差30~40℃。形成的膜孔结构与孔空隙率受不良溶剂影响,用低浓度非溶剂时,膜具有封闭孔结构、低空隙率;用中等浓度非溶剂时,形成既有开放又有封闭的混合结构;用高浓度非溶剂时,得到完全开放的孔结构。
制膜环境也影响膜结构,高浓度的溶剂蒸气延缓凝胶化,而高空气流速和温度则加速凝胶发生。
简单的溶剂蒸发法在实际制膜中很少应用。
12.3.6.3 热致相分离法
热致相分离法(TIPS)[269-271]是利用一种潜在溶剂,它在高温时是溶剂,在较低温度时又是非溶剂,在高温下与聚合物配制成均一铸膜液,将溶液平铺成一定厚度的平板状或纺丝制备成中空纤维状后,再以一定的速度冷却或淬冷溶液,使之发生相分离后固化,用常见且对环境较为友好的试剂萃取出分散在膜前体中的稀释剂,最后形成微孔结构。潜在溶剂可以是单一溶剂,也可以是溶剂与非溶剂组成的混合溶剂。
用热致相分离的聚合物一般具有可结晶性。当温度低于铸膜液熔点时,聚合物从溶液中结晶出来,形成呈平衡的纯结晶态和液态两相,使混合自由能降低,称之为固-液分相。
图12-32中曲线A为双节线,曲线B为旋节线,在双节线以上区域溶液为均相的体系,而在旋节线以下区域为不稳区,双节线和旋节线之间区域为亚稳区,将发生成核-生长相分离。在发生液-液相分离后,孔形态取决于旋节相分离还是成核-生长机理。到相分离后期,如果按成核-生长机理,如图12-33(a),形成的液滴是独立的,最后溶剂去除后,形成封闭的多孔结构;如果按旋节相分离机理,形成的液滴相互连接,溶剂去除后形成了相互贯穿的连通孔,如图12-33(b)所示[269]。

图12-32 聚合物/稀释剂二元体系温度-浓度相图[270]

图12-33 两种分相机理下液滴粗化过程[270]
冷却速率是决定膜孔结构的关键参数。根据所用溶剂、非溶剂的不同,用热致相分离法可以制造微孔滤膜或非对称膜,它可以应用于许多以前由于溶解度差而不能用沉浸相转化法制膜的聚合物。目前热致相分离法制膜主要用在聚烯烃,如聚丙烯、聚-4-甲基-1-戊烯等。
12.3.6.4 湿法制膜
湿法制膜是把事先配制好的铸膜液在支撑体上流延后,立即浸入凝胶浴成膜。由湿法相分离得到的膜一般是皮层有孔的非对称膜,适合于用作复合膜的底膜。
12.3.6.5 干法制膜
干法制膜或称完全蒸发法,是最简单的制膜方法。它是将铸膜液倒在支撑体上(如玻璃板、聚四氟乙烯板或聚酯无纺布等),用刮刀使之铺展或不用刮刀使之自然铺展开,置于特定环境中待溶剂蒸发后,最后形成均质膜。测试膜材料渗透系数时所用的致密膜通常用此法制造。
12.3.6.6 干-湿法制膜
干-湿法制膜也称沉浸凝胶法,是由Loeb和Sourirajan提出的,所以也称L-S法[272],是目前实际应用最多的相转化制膜法,该方法的成膜过程是先将临近热力学不稳定组成的铸膜液进行低沸点溶剂或非溶剂的挥发,提高初生膜表面的聚合物浓度,形成致密皮层;然后浸入凝胶浴中进行溶剂/非溶剂的交换,产生液-液分相,直至凝胶固化成膜。1962年Loeb和Sourirajan首先用L-S法得到醋酸纤维素反渗透膜,在同等膜厚下,非对称醋酸纤维素膜透水量比同样材质均质膜提高10倍左右。Riley等[273]通过电子显微镜观察发现这种膜具有非对称结构:即非常薄而致密的皮层(0.2μm)以及海绵状疏松的多孔支撑层。非对称醋酸纤维素膜成功研制是膜技术发展史上一个里程碑,提高了人们对膜结构的认识。用沉浸凝胶法可以制造微孔滤膜、超滤膜、反渗透膜、纳滤膜、气体分离膜、渗透汽化膜等多种类型分离膜。
干-湿法制膜工艺过程如图12-34所示。其中包括三个基本制膜步骤:

图12-34 干-湿法制膜工艺过程
①配制铸膜液 铸膜液中通常包含聚合物、溶剂(相对聚合物而言)、非溶剂(相对聚合物而言),一般要求溶剂和非溶剂可以任何比例互溶;
②铸膜液刮在玻璃板上,制成有一定厚度初生膜或用纺丝设备纺成中空纤维初生膜;
③初生膜在空气(或含有要求组分的气相氛围)暴露一定时间后,随即浸入沉淀浴(通常是水、醇类等),浴中非溶剂向膜相内扩散,同时初生膜中溶剂向沉淀浴外扩散,在膜相与浴相界面上发生溶剂、非溶剂传质交换。使初生膜中非溶剂浓度增加,产生非稳态,导致液-液相分离。如果溶剂外扩散速率大于非溶剂内扩散速率,膜界面上聚合物浓度提高,表面将形成高浓度聚合物致密层。致密层的形成使溶剂外扩散速率下降,使膜液内聚合物浓度较低,形成多孔支撑层。随着溶剂与非溶剂不断交换,液-液相分离后的膜液富相进入玻璃化转变区,产生玻璃化转变而凝胶成固态,最后得到具有表皮层致密、底层疏松多孔的非对称膜。
分离膜的最终结构及性能主要取决于聚合物铸膜液的热力学性质以及成膜过程中溶剂与非溶剂的相互交换传质动力学(包括初生膜在气相氛围中蒸发、沉淀浴与铸膜液界面上发生溶剂与非溶剂传质交换等)。
通常将制膜过程视为热力学等温过程,Strathmann等[274]引入三角相图直观地表征聚合物制膜液的热力学性质。如图12-35所示[275],双节线把相图分为单相区和两相区,旋节线把两相区又分为亚稳区和不稳区。制膜液相分离产生的聚合物富相和贫相组成位于双节线上,由结线连接,膜液组成在相图中的位置反映了其热力学状态,Cp为临界点[276,277]。

图12-35 膜的相分离路线
一般热力学液-液分相有成核-增长的双节线分相和旋节线分相两种分相机制[278]。①为凝胶(或玻璃化转变)分相,③为旋节线分相,②和④为成核增长机理。一般相转化膜的气体分离膜皮层通过①凝胶分相形成,支撑层由②贫聚合物相成核增长分相形成。
采用图12-35所示的三元相图解释膜孔形成机理,制膜液在分相过程中经过的路线决定了膜的结构[279]。当体系组成变化沿均相进入①区发生玻璃化转变而凝胶固化,形成固态相;对于双节线分相过程,体系组成变化从临界点上方进入双节线和旋节线之间的亚稳分相区②时,发生聚合物贫相成核的液-液分相,由溶剂、非溶剂和少量聚合物所组成的贫相小滴溶液分散于连续的富聚合物相中,这些小液滴在浓度梯度的推动下不断增大,直到周围的连续相经结晶、凝胶化或玻璃化转化等相转变而固化为止,期间贫相小液滴的聚结形成多孔结构。当体系组成变化从位于临界点下方的组成进入双节线和旋节线之间的亚稳分相区④时,发生富聚合物相成核的液-液分相,富聚合物相小液滴将分散于由溶剂、非溶剂和少量聚合物形成的连续贫相中,这些富聚合物相小液滴在浓度梯度的推动下增大,直到聚合物固化成膜为止,但此路线形成的膜是机械强度较低的乳胶粒结构[265,280,281]。
对于旋节线液-液分相,体系的组成变化正好从临界点组成进入旋节线内的不稳区③,体系迅速形成由贫聚合物相微区和富聚合物相微区相互交错而成的液-液分相体系,所形成的结构为双连续结构,即贫相和富相完全互相交错连接,这种结构经聚合物的相转变固化作用将最终形成双连续膜结构形态[265,282]。
相转化法制膜过程中,随着制膜液中非溶剂含量的增加,在到达相图中的双节线组成时,体系原有的热力学平衡被打破,将自发地进行液-液分相。为了获得良好的膜性能,需要精确控制成膜过程中的各个影响因素。热力学相图能预测聚合物溶液体系是否适合制膜、将发生何种相分离、分相后聚合物富相凝胶固化的难易,从而在一定程度上预测膜结构。但相转化是一个复杂的非平衡过程,热力学平衡相图只提供聚合物溶液体系是否以及发生何种分相的情况,而实际分相固化过程是一个动力学过程,不同的分相类型决定了不同的膜结构,图12-36展示了瞬时与延迟两种相分离方式膜液组成不同的路径变化情况,(a)铸膜液进入沉淀浴后组成线立刻穿透双节线发生瞬时相分离,(b)铸膜液进入沉淀浴后组成线在一定时间内仍在液相区而不发生相分离,即延时相分离。可以说膜具体的结构形态是由动力学因素所决定,瞬时分相通常形成指状孔结构膜,而延时相分离形成海绵状结构膜,如图12-37所示[283]。

图12-36 制膜液进入凝胶浴后(t<1s)的组成路径[283]

图12-37 分相类型对膜结构的影响
对聚合物-溶剂-非溶剂(通常用水)三元铸膜液体系,用干-湿法制备的非对称分离膜通常有表面微孔缺陷,需要界面涂覆填塞其缺陷,方可用以气体分离。为克服此弊端,采用三元以上组分铸膜液,在铸膜液添加低沸点溶剂,通过成膜过程中低沸点溶剂大量蒸发使膜表面聚合物浓度提高,可以得到完整无缺陷的膜皮层。
目前的研究主要集中于铸膜液组成(包括聚合物浓度、有机溶剂种类、溶剂与非溶剂比率)、凝胶浴组成、凝胶浴温度、纺丝温度、干纺距离、芯液组成、芯液速度、牵伸倍数等因素对相转化过程热力学和动力学及固化后膜结构和性能的影响。
Khayet等[284]分析了相分离过程中热力学和动力学对中空纤维膜形态和内表面结构的影响,发现非溶剂的选择对于PVDF-HEP中空纤维膜的形态、结构及其直接接触膜蒸馏过程的性能有重要影响。利用N,N-二甲基乙酰胺(DMAC)水溶液作为芯液,随着芯液中DMAC含量增加,芯液的凝胶能力减弱,相分离过程变慢,中空纤维膜的内表面孔隙率增加,孔径变大,内层的指状孔减少直到消失,形成开放的海绵状孔,孔径分布变窄,内表面粗糙度增加,穿透压降低,直接接触式膜蒸馏过程的通量增加。利用Hansen溶解度参数理论计算出不同非溶剂组成与溶剂之间的Hansen溶解度参数差值,随着非溶剂中DMAC含量增加,Hansen溶解度参数差值变小,非溶剂与混合溶剂(DMAC和TEP)之间的相互作用减弱,纺丝溶液在热力学上更稳定,在动力学上分相速度更慢。Hansen溶解度参数理论可以用于指导任何非溶剂致相分离的热力学和动力学过程分析。
Khayet等[285]指出高贯通性的海绵状孔和消除中空纤维膜的外皮层可以提高直接接触膜蒸馏的通量。他们采用双通道喷头纺制PVDF-HEP中空纤维膜,双通道喷头的外通道通入不同组成的外凝胶浴,利用Hansen溶解度参数理论对凝胶浴组成进行优化。在外凝胶浴中加入DMAC可制备多孔的外表面,降低膜厚,增加内表面的孔径和粗糙度,提高直接接触膜蒸馏产水量。在内外凝胶浴都采用50%DMAC水溶液时,膜蒸馏过程的水通量达到最大值,比仅用50%DMAC水溶液为外凝胶浴的膜水通量提高两倍。
Yip等[286]结合热质耦合传递、膜收缩、扩散理论和自由体积理论、聚合物溶液/气相界面传质,以及Alosy和Duda提出的摩擦扩散模型,提出了一种非溶剂气相分离过程模型。将传质路径和三元相图结合,模拟了四种三元体系(醋酸纤维素/丙酮/水、聚偏氟乙烯/DMAC/水、聚砜/N-甲基吡咯烷酮(NMP)/水、聚醚酰亚胺/NMP/水)。通过与文献数据比对,证实了该模型可以准确预测相对湿度、溶剂挥发度、空气流速、蒸发温度、初始膜厚度和聚合物浓度等不同参数在蒸汽诱导相分离过程(VIPS)中对膜特征(分相时间、非对称结构、孔等特征)的影响。得到以下结论:相对湿度越大,越容易分相,分相时间越短。存在临界相对湿度,当大于该湿度时即使铸膜液中没有水也可以发生分相;增加空气流速有利于相分离,减少分相时间,减小膜厚度;提高蒸发温度有利于降低分相时间,蒸发温度过低可能不会发生分相;膜初始厚度的降低有利于加快分相,减小分相时间,聚合物浓度梯度随膜厚度的增加而增加;初始聚合物浓度越高,膜孔越少。
Khare等[287]采用VIPS工艺,通过控制潮湿空气的暴露时间、相对湿度、空气温度和气流速度获得具有独特形貌的膜。建立了水/NMP/聚醚砜(PES)/PVP四元系统的VIPS模型,使用有限差分方程进行数值求解。数学模型预测瞬时厚度和聚合物浓度以及膜内的组成是随相分离时间和距蒸汽/铸膜液界面的距离的函数。模型预测表明:水的转移导致膜厚度的增加,以及在蒸汽/铸膜液界面(顶表面)处聚合物质量分数减少,这种聚合物浓度的降低可以解释特征性沙漏形态的演变。模型预测还表明:通过增加溶液中的传质系数或降低PES∶PVP质量比,可以增加从最小孔到膜表面区域的不对称程度。
Su等[288]通过红外显微(FTIR-microscope)技术,测定了分子量为25000和120000的PMMA溶液在非溶剂诱导相分离过程(NIPS)中与非溶剂接触时的聚合物组成变化,结合三元相图确定了铸膜液在亚稳区的停留时间,分析其停留时间与得到的膜结构之间的关系。研究发现在NIPS过程中,存在一个临界停留时间。当铸膜液在亚稳区停留时间小于临界停留时间时,形成致密多孔结构(旋节分解结构,SD结构);当铸膜液在亚稳区停留时间大于临界停留时间时,形成大孔胞腔结构(成核生长机制,NG结构)。这很好地解释了在NIPS过程中,膜倾向于在两相界面处形成致密结构的原因。利用临界停留时间和聚合物浓度关系,建立了致密层厚度与聚合物浓度之间的数学模型,可以预测聚合物在NIPS成膜过程中,膜结构从细孔结构转变为大孔胞腔结构的位置。
根据Henis传质阻力模型,非对称膜分离皮层只要有百万之一孔隙率的缺陷,膜对气体分离系数就远低于聚合物材料本征值,需要涂层堵缺陷。不但增加后续工艺,而且涂层对工艺过程要求很严格,不是简单操作即可涂上。有不少学者开展研制无或少缺陷、超薄皮层研究[289-291]。Ismail等[291]通过控制聚合物浓度、溶剂比(低挥发性溶剂与高挥发性溶剂的比例)、强迫对流蒸发时间和纺丝喷头剪切速率等制膜变量,采用正交设计和响应面法研究了这些变量及其相互作用对膜结构和性能的主要影响,优化膜的形成过程,制备出基本无缺陷的非对称膜。
12.3.6.7 双浴法制膜
湿法工艺制备的膜一般是皮层含有孔缺陷的非对称膜,需要涂层形成复合膜,以满足气体分离对膜性能的要求。而双浴法工艺是制造皮层无缺陷非对称膜的方法。该工艺的关键是初生膜在凝胶前,先经过一非溶剂浴(第一浴),短时间内带走膜表面皮层溶剂,使膜表面聚合物浓度达到很高,然后进入凝胶浴(第二浴)凝胶,可得皮层无缺陷非对称膜结构。
Kim等[292]采用双浴法制备出皮层致密无缺陷的非对称气体分离膜,纺丝液用聚砜和NMP溶剂配制,第一浴采用聚乙二醇(PEG),当纺丝液进入聚乙二醇浴时,其组成进入①区发生了凝胶(见图12-35),形成致密初生态皮层;第二浴采用水作为凝胶浴,当初生态纤维进入水浴时发生旋节相分离,得到无缺陷致密皮层和支撑层球状结构多孔支撑层。研究表明,在PEG浴中存在最佳停留时间(30s),O2/N2分离系数接近聚砜材料本征值(见表12-36)。
表12-36 双浴法制备的聚砜中空纤维气体分离膜性能[292]

注:1GPU=10-6cm3(STP)/(cm2·s·cmHg)。
Chung等[293]采用双凝胶浴技术制备了用于肾透析的聚醚砜中空纤维膜,第一个凝胶浴采用弱凝胶值异丙醇(PA),而水作为第二凝胶浴。其优点是可以更好地控制内外皮层形态,制备具有致密内皮层和松散外支撑层结构透析膜。
12.3.6.8 共挤出法制膜
有的高性能膜材料价格昂贵,分离层与支撑层用同一材料制成中空纤维膜,其材料成本高;还有一些膜材料机械性能较差或者黏度太小,不易制成单层中空纤维膜。制备复合膜是这些材料能用于工业化制膜的一条途径。传统的复合膜制备方法如涂覆和界面聚合等都是支撑层与功能层分开制备,既费时费力又增加了制膜的成本。1992年Ekiner等[294]发明了三通道喷头共挤出法制备双层非对称中空纤维膜技术,其优势是一步制成支撑层与功能层,减少了制膜步骤和制膜过程中产生缺陷的因素。
如图12-38所示,共挤出法是指支撑层与功能层使用不同聚合物配制的制膜液,支撑层制膜液与功能层制膜液同时从三通道喷头中挤出,经凝胶浴固化一步成膜。三通道喷头结构如图12-39所示[295,296],内插管通芯液,中环走支撑体铸膜液,采用廉价聚合物溶液,外环是分离层材料。丁晓莉等[295]外环采用Matrimid 5218/NMP/THF溶液,中环采用廉价聚合物PSF/NMP溶液,经凝胶浴凝胶后,得到中空纤维复合膜,外皮层是致密分离层,内外聚合物交界处是多孔结构,对气体渗透无阻力,所制得中空纤维膜氧气渗透性能为8.93GPU,O2/N2分离系数为7.61。

图12-38 中空纤维复合膜制造工艺示意图

图12-39 用于制造中空纤维复合膜三通道喷头及膜断面SEM照片
12.3.7 包覆法
包覆法是一种复合膜的制造方法。它把均匀的聚合物溶液,用涂布、喷涂、浸渍或者轮涂等手段包覆到多孔底膜上,然后再进行界面聚合或等离子聚合,使其形成薄膜层,得到复合膜。根据起分离作用的功能层不同,可将该类型复合膜分为两种:一种是支撑层起分离作用,涂层材料常采用硅橡胶等高渗透性低选择性的材料,此时涂层主要起堵孔作用,如Prism聚砜-硅橡胶复合膜[11,12]等;另一种是涂层起分离作用,支撑层单纯地起机械支撑作用,对气体渗透几乎没有阻力,如有机蒸气回收和富氧过程使用的硅橡胶/多孔支撑层复合膜、界面聚合制备的含氨基的促进传递膜等。
用包覆法制备复合膜最初用于反渗透膜制备过程。用相转化法制备的非对称反渗透膜水通量与致密分离层的厚度成反比,所以降低致密层厚度是提高膜透水速度的有效途径。根据高分子溶液的松弛理论可计算出醋酸纤维素/丙酮体系反渗透膜的最小皮层厚度,再变薄非常困难。另外,相转化法制备的非对称膜在使用过程中由于过渡层的存在,膜易被压密,使透水量下降。假如分别制备致密皮层和多孔支撑层,既可以降低致密皮层的厚度,又可以消除引起压密的过渡层,这就是当年复合膜制造工艺的基本思路。
与相转化法制备的非对称膜相比,复合膜具有以下特点[297,298]:
①如果相转化法制备的非对称膜材料价格较高,支撑层材料可采用廉价材料,此时采用复合膜形式可以省去大量昂贵材料;
②拓宽了非对称膜材料范围,一些材料很难通过相转化法制成非对称膜,比如材料本身质地较脆,此时可以通过制备成复合膜实现非对称形式;
③复合膜的制作,一般是先制作多孔支撑层,然后直接在多孔支撑层上以各种方法制作超薄皮层。
复合膜超薄皮层的制作方法主要包括聚合物溶液涂覆、界面聚合或交联和共挤出法。复合膜性能受支撑层制备条件和皮层制备方法等因素的限制,支撑层影响主要包括:支撑层材料性质、制备条件、预湿等前处理,要求其有适当大小的孔密度、孔径和孔径分布,有良好的耐压密性和物化稳定性;分离层主要受包括涂层液浓度、涂层次数、涂层时环境温湿度、涂层液溶剂等因素的影响。另外还可采用中间层和保护层来制备复合膜[299,300]。
12.3.8 界面聚合法复合膜制造方法
12.3.8.1 界面聚合制膜原理及其特点
界面聚合反应利用逐步增长聚合机理,以有机化学中经典的Schotten-Bauman(肖顿-鲍曼)反应为依据[301],是制备高分子量聚合物的有效方法,其制备复合膜的过程如图12-40所示。首先,将多孔支撑体(通常是微滤膜或超滤膜)浸入含有活泼单体或预聚物(最常用的是胺类)的水溶液中,并晾干一定时间;然后,将此膜浸入含有另一种活泼单体(通常是酰氯)的有机相溶液中,两种单体在界面处发生反应,并在多孔支撑体上形成致密的聚合物皮层;最后,对生成的膜进行后处理(如热处理等)制得复合膜。如果选用的支撑体亲水性较差、疏水性很强,在界面聚合制膜时也可以先将支撑体浸入有机相,而后再浸入水相。

图12-40 界面聚合法制备复合膜示意图
界面聚合法制备复合膜具有如下优点:①反应具有自抑制性,初始膜的形成会阻碍水相单体向反应区扩散[302],可制得厚度小于50nm的薄膜;②反应在两相界面处进行,界面反应对反应物的纯度没有特别要求;③界面聚合易于制得无缺陷的聚合物薄膜,这是由于反应具有自抑制性和自密封性[303];④界面聚合膜的分离层与支撑层结合较为牢固,这是由于分离层与支撑层之间存在的分离层/支撑层互嵌的界面区[304];⑤界面聚合制膜易于放大到工业规模。
12.3.8.2 界面聚合法在气体分离膜制备中的应用
自从Morgan 和Kwolek[305,306]提出界面聚合的概念以来,许多膜领域的专家对界面聚合法制膜进行了深入研究,并成功制备出了商业使用的超薄复合型反渗透膜,现被广泛用于制备反渗透膜、纳滤膜,但界面聚合制备气体分离膜的研究还处于实验室水平。
Chern[307,308]等以亚甲基双苯胺为水相单体,1,2,4,5-四酰氯苯为有机相单体,在聚砜超滤膜上制备了聚酰亚胺复合膜,所制膜纯气测试性能:CO2渗透系数为44.12Barrer,CO2/CH4理想分离因子为20.51。Petersen等[309]以商品化的多功能胺和对苯二甲酰氯的衍生物为反应单体,在聚醚酰亚胺超滤膜上制备一系列聚酰胺复合膜。其中,经过硅橡胶涂覆的复合膜CO2纯气渗透速率为109.6GPU,CO2/N2理想分离因子为30。Son等[310]采用界面聚合法在硅橡胶支撑体上,制备了聚吡咯复合膜,O2渗透系数为40.2Barrer,O2/N2理想分离因子为17.2。
王志课题组首次采用界面聚合法制备出了含氨基的促进传递膜[311],对界面聚合制备气体分离膜的工艺进行了系统研究,对界面聚合过程中单体浓度和种类、溶剂种类、反应时间和后处理等工艺条件进行考察。赵卷等[311,312]以三乙烯四胺(TETA)、四乙烯五胺等若干种多胺为水相单体,均苯三甲酰氯(TMC)为有机相单体,在聚砜或聚醚砜(PES)超滤膜上制备了一系列含伯氨基和仲氨基的促进传递膜,并考察了制膜条件(如单体种类、单体浓度、反应时间和热处理等)对膜性能的影响。通过优化界面聚合制膜工艺,聚(TETA-TMC)/PES复合膜的CO2渗透速率可达到13.3GPU,CO2/CH4分离因子为94.1。除界面聚合工艺的研究之外,王明明等[313,314]采用TMC为油相单体,二氨基苯甲酸钠和4,7,10-三氧-1,13-癸烷二胺为水相单体,制备了含有羧酸根基团和醚氧基团的抗氧化高性能复合膜,所制膜CO2渗透速率可达5831GPU,CO2/N2分离因子可达86。李诗纯等[315]选用TMC为油相单体,DGBAmE以及含叔胺的N,N'-双(3-氨丙基)甲胺共同为水相单体,制备兼具扩散选择机制、溶解选择机制和反应选择机制的多选择机制膜,其复合膜的CO2渗透速率可达1600GPU,CO2/N2分离因子可达138,同时具有良好的长时间运行稳定性,并且在实际操作温度35~50℃下仍保持较好的CO2分离性能。
12.3.8.3 界面聚合成膜机理研究进展
国内外学者对界面聚合制备复合膜的工艺条件进行了较为深入的研究,但关于界面聚合成膜机理的研究报道却较少。成膜过程中的界面聚合反应决定了复合层的结构,进而影响着膜性能。因此加深对成膜机理的认识,对复合膜的制备具有重要意义。
由于界面聚合反应速率极快[对胺和酰氯均相体系而言,速率常数约为102~104L/(mol·s)[316]],生成的膜较薄,且聚合过程比较复杂(涉及单体扩散、聚合反应、聚合物相分离、聚合物相增长等多个过程)[317],很难直接监测整个成膜过程。一些研究者基于反应体系中的物料衡算方程,建立了用于描述界面聚合反应过程中聚合物膜宏观性质(如膜厚度)变化的数学模型,但这种宏观模型无法预测膜的微观性质(如分子量分布等)变化。Karode等[318,319]首次建立了用于描述界面聚合反应过程所形成聚合物膜分子量分布的数学模型,随后对聚合物膜的分相过程提出了新观点,提出聚合物分相由成核增长和旋节线分相两种机理控制,并建立了新的模型。Dhumal等[317]对Karode的模型[319]做了进一步改进,建立了可同时预测聚合膜分子量分布和结晶度的新模型。
随着实验技术的进步,一些研究者利用实验手段对界面聚合成膜机理进行了研究,使用的技术主要有pH技术(pH值法)[320,321]、光反射技术(LRI方法)[322]、悬滴界面张力技术(PDR方法)[322,323]等。
Yadav等[321]使用pH技术对己二胺和己二异氰酸酯界面聚合反应制备聚脲微胶囊的成膜动力学进行在线监测。通过在线测定pH值随反应时间的变化,可间接测定己二胺随反应时间的变化,进而得到聚合反应速率的相对大小。LRI方法的原理是根据高分子材料在固态和液态时所表现出的不同光学性质来对界面聚合的反应动力学进行研究[324]。Krantz等[322]在研究界面聚合反应过程中悬滴界面张力变化时发现,浓度为2%的MPD和浓度为0.1%的TMC反应成膜初期,悬滴的表面张力急速下降,在20s时达到自抑制状态;随后悬滴的表面张力缓慢下降,他们认为交联反应缓慢进行使得悬滴的表面张力逐渐下降。
袁芳、于型伟等[325-327]采用视频光学接触角测定仪(OCA)和粒子成像测速仪(PIV)对低反应活性N-甲基二乙醇胺(MEDA)与均苯三甲酰氯(TMC)界面聚合成膜过程进行了研究。通过视频光学接触角测量仪在线观测界面聚合的成膜过程,探寻了界面聚合过程的成膜机理:①水相单体在有机相中的扩散速率大于有机相在水相中的扩散速率,因此界面聚合膜朝有机相侧生长;②界面处存在的水相单体浓度梯度会导致界面不稳定性,并产生凸起结构,而这种凸起结构会随制膜条件(有机溶剂、酸接受剂的种类等)的变换而改变;③界面聚合反应形成的初生膜会因为其巨大的表面能而处于热力学不稳定状态,所以初生膜表面形成均匀分布的针孔缺陷,进而导致水相液滴穿过针孔表现出胞状结构。随着聚合反应的进行,新形成的较大的胞状结构不断将原有的较小的胞状结构覆盖,最终形成粗糙的复合膜。此外,袁芳等[328]还研究了界面聚合制备气体分离复合膜的制备-结构-性能关系:有机相单体浓度主要控制复合膜分离层的厚度,而水相单体浓度主要控制复合膜分离层的交联度。在保证形成完整的分离层的前提下,适当降低有机相单体浓度和增加水相单体浓度能够获得具有高CO2渗透速率和高CO2/N2分离因子的复合膜。
反渗透膜、纳滤膜以及气体分离膜应用的分离物系不同,理想的膜结构和性质有着巨大差异。实用的气体分离复合膜要具备致密均匀的膜结构,且没有对气体分子无选择性的缺陷。在典型的气体分离过程中,1m2膜面积上只要有一个缺陷,就可能使膜失去选择性。尽管已经有商品化的反渗透膜、纳滤膜,但用界面聚合法制备出真正商品化的气体分离膜仍有较长的路要走。
12.3.9 炭膜制备方法
炭膜是由聚合物前驱体在惰性气氛下经高温(>500℃)热解炭化制备而成的一种新型高性能的炭基多孔膜材料。炭膜制备过程主要包括:前驱体聚合物膜制备、预处理、炭化处理以及后处理等工艺过程。聚合物前驱体分热塑性前驱体与热固性前驱体。热塑性聚合物前驱体,包括聚芳醚酮类、聚醚砜酮类、聚丙烯腈、聚醚酰亚胺等;热固性聚合物前驱体,包括聚酰亚胺、聚糠醇、酚醛树脂和纤维素衍生物等。二者制备工艺大体相同,但热固性聚合物前驱体不需要预处理过程。以下为热塑性聚合物前驱体制备炭膜过程[329,330]。
(1)前驱体聚合物膜的制备
将一定量的干燥聚合物溶解在溶剂中,加热搅拌溶解,经离心、脱泡和静置后,在玻璃板上刮涂成薄层铸膜液,放在恒温台上进行溶剂蒸发。将所形成的初生膜从玻璃板上剥离,放置真空烘箱中真空干燥,脱除膜内残余溶剂后得到聚合物膜。
(2)预处理过程
热塑性聚合物前驱体需要在空气氛围中进行预处理,形成稳定的交联网状结构,限制炭化过程中聚合物发生熔融和分子链间相互滑移,保持膜的形态和自由体积,使得炭膜结构完整、气体渗透系数好。
将聚合物膜剪成膜片,放置于马弗炉中进行预处理。升温程序为:以5℃/min的升温速率从室温升高至终温T-50℃,以2℃/min升高至T-30℃,再以1℃/min升高至终温T,恒温30min,然后自然或快速降温至室温,降温速率如图12-41所示。预处理气氛为流动的干燥空气。

图12-41 预处理过程中自然降温和快速降温方式下的降温速率
(3)炭化过程
膜的炭化过程是在加热炉中进行,以流动氮气(99.99%)为惰性氛围。将预处理后膜样品夹在石墨板之间,平放在管式炉恒温区域,将炉口密封。升温程序为:以5℃/min的升温速率从室温升至400℃,然后以3℃/min的升温速率升温至终温,恒温60min,最后自然降至室温得到碳分子筛膜。
12.3.10 热致重排聚合物膜制备方法
热致重排聚合物(thermally rearranged polymers,TR-polymer)通常是由官能化的聚酰亚胺或者聚酰胺等前驱体通过高温热处理生成的具有刚性骨架的产物。
具体制备过程如下:配制一定浓度的聚酰亚胺或聚酰胺溶液,在玻璃板上铺制成膜或纺制成中空纤维膜,脱净溶剂后,置于气氛保护的管式炉或马弗炉中,高温烧结即可得到热致重排聚合物膜。重排过程中,邻位官能基团与酰亚胺键或酰胺键发生反应,如图12-42所示[68]。

图12-42 官能化前驱体热致重排过程
通常,以聚酰亚胺为前驱体的热致重排膜具有高的气体渗透性和选择性,但重排所需的温度较高,要求严格的惰性气氛或真空环境;而聚酰胺可以在较温和的环境下发生热环化,得到的膜机械性能较好。表12-37是以聚酰亚胺和聚酰胺为前驱体的热致重排条件以及所得热致重排聚合物膜的性能比较。
表12-37 6FAP-6FDA-API热重排过程和6FAP-6FC-PHA热环化过程的对比[331]

在聚酰亚胺或者聚酰胺的邻位引入可以发生Claisen重排的烯丙基醚[332],可以将分子重排温度降低约200℃,反应机理如图12-43所示。在相同的热处理条件下,通过Claisen热致重排可以得到更高的热重排率。

图12-43 Claisen热致重排机理
12.3.11 混合基质膜制备方法
混合基质膜(mixed matrix membrane,MMM)是通过在有机膜中引入无机粒子来提高有机膜的分离性能,并且保持有机膜韧性好、易加工成型的特点,实现有机膜与无机膜的优势互补。MMM制备过程的包括:无机颗粒/聚合物共混液配制、铸膜液处理及成膜、MMM高温后处理等工艺过程。以下简述MOFs/聚合物混合基质膜制备方法。
(1)MOFs/聚合物共混液配制[333]
将一定量MOFs加入有机溶剂中,室温下,进行高速机械搅拌/超声处理,交替重复多次,得到MOFs分散液;将一定量的干燥的聚合物溶解在溶剂中,加热搅拌得到聚合物稀溶液。采用Priming方法,即一定温度下先将少量聚合物溶液加入高速搅拌的MOFs分散液中,待完全均匀混合后将剩余聚合物溶液分批加入,形成MOFs/聚合物共混稀溶液。
(2)铸膜液处理及成膜
把MOFs/聚合物共混稀溶液加热搅拌,用气体吹脱溶剂,浓缩至固含量w=20%以上;然后经搅拌/超声,交替重复多次,滤布过滤,真空脱泡后制成铸膜液;刮涂在光滑玻璃板上,放入真空烘箱中加热脱除溶剂成膜。
(3)高温后处理
膜成形后自玻璃板取下,放入真空烘箱中继续高温热处理。热处理过程:逐段升温,每段温度间隔30℃左右、稳定时间12h;待加热完成后,自然降至室温即得到混合基质膜。
影响MOFs/聚合物混合基质膜制备过程的因素:两相间空隙缺陷及分散相粒子的团聚是影响混合基质膜气体渗透分离性能的主要因素。除选择分散相和有机基质外,制膜条件也是膜制备的关键因素,像MOFs含量、加料方式和后处理温度等均会影响混合基质膜性能。例如,采用Priming加料方式,将MOFs分散液和聚合物溶液共混配制铸膜液,可以抑制MOFs与聚合物间的相界面缺陷,如图12-44所示;又如,后处理温度升至溶剂沸点以上,可以解吸在MOFs孔结构中残留制膜溶剂,可使气体渗透系数显著增加[334]。

图12-44 Cu3(BTC)2/Ultem1000混合基质膜的断面电镜图
12.3.12 气体分离膜制造工艺
12.3.12.1 平板膜制造工艺
在实验室可在恒温、恒低湿度箱体内,直接在平整的玻璃板上流延成膜,隔离空气中湿气水平静置若干天,待溶剂完全蒸发得到致密膜,如图12-45(a)所示。

图12-45 流延法制备致密膜和非对称膜示意图
图12-45(b)是流延法制备非对称膜工艺示意图,在恒温、恒湿或一定溶剂蒸气气氛的箱体内,直接在平整的玻璃板上涂上聚合物溶液薄膜(可以固定玻璃板移动刮刀或固定刮刀移动玻璃板),根据需要蒸发一定时间后,然后在相应配方凝固浴中浸泡一定时间,发生非溶剂与溶剂交换,等完全固化后,放入水浴中把溶剂置换出来,可得到多孔非对称膜或致密皮层非对称膜。膜的厚度可以通过固定在刮刀上的微调螺丝调节。
除实验室用膜用玻璃板作为成膜基体外,在工业生产中,通常采用直接在支撑材料上流延成膜。膜与支撑材料构成一体,制得的膜强度高,性能稳定。图12-46(a)是平板膜连续制造装置示意图。聚合物溶液通过刮刀均匀涂布在无纺布上,溶剂在气隙中逐渐汽化形成致密的表层;当无纺布上的薄膜连同初生的致密层浸入凝固浴中,溶剂和非溶剂快速交换,在液膜中形成连续的富聚合物相和离散的贫聚合物相,即形成非对称膜,如图12-46(b)。

图12-46 平板膜制造工艺
除铸膜液配方是影响膜性能重要因素外,成膜条件如环境温度、湿度、气速、凝胶条件、刮膜速度、进水角度、支撑材料等均对膜性能有重大影响。
对于大规模连续制膜的成膜基体,要求其透气性好、耐酸、耐碱、基体材料的缩水率与膜凝胶收缩率一致、成膜后基体与膜不剥离。聚酯无纺布价格便宜,均匀性、一致性、热稳定性好;经热压光处理,表面光洁、无粘毛,常用作基体材料。表12-38列出部分用于分离膜的无纺布(100%聚酯纤维)的性能参数。
表12-38 部分用于分离膜的无纺布参数

12.3.12.2 中空纤维膜制造工艺
中空纤维膜具有自身耐压力特点,这与平板膜需要支撑体不同。此外,中空纤维膜还具有比表面积大的优点(参见表12-55),因此中空纤维膜在膜分离领域获得了广泛应用。图12-47是中空纤维膜制备过程及喷头结构示意图。

图12-47 中空纤维膜纺丝工艺及喷头示意图
纺丝液经脱泡过程后,用计量泵从喷丝头挤出,经溶剂从初生态膜表面短时间蒸发后,进入凝胶浴,凝胶后的纤维膜再经洗涤,最后缠绕在收丝筒上。
纺中空纤维膜通常使用内插式喷丝头。喷丝头常用结构如图12-47所示,外环通聚合物溶液,内管由计量泵往中空纤维膜中空供芯液,以阻止初生中空纤维膜出喷头后塌瘪。芯液可使用纯水或一定溶剂组成的水溶液。
纺中空纤维膜的材料要求可纺性好,如醋酸纤维素(CA)、聚砜(PSF)、聚丙烯腈(PAN)共聚物等都是常用的聚合物膜材料。中空纤维膜性能受纺丝条件影响很大,根据铸膜液配方及纺丝条件制备中空纤维多孔膜、中空纤维梯度密度膜以及皮层致密无缺陷的中空纤维膜等。
表12-39列出聚砜梯度密度非对称膜纺丝条件和气体渗透性能;表12-40(a)、(b)分别列出皮层致密无缺陷聚酰亚胺非对称膜的纺丝条件和气体渗透性能。
表12-39 聚砜梯度密度非对称膜纺丝条件(第二代聚砜膜)[336]

表12-40(a) 聚酰亚胺(Matrimide5218)非对称膜纺丝条件[337]

注:纺丝温度50℃。凝胶水浴温度20~25℃。
表12-40(b) 聚酰亚胺(Matrimide5218)非对称膜气体渗透分离性能[337]

一般而言,用于制备非对称膜的膜液包括聚合物、混合溶剂(高挥发性与低挥发性)以及非溶剂组分,通过调控非溶剂组成使得膜液逼近热力学不稳定限,即非常接近浊点的组成。在制备过程中,膜液以一定的剪切速率由喷头挤出,首先经过干纺阶段,在这个阶段通过施加强制对流迫使外表面膜液内的低沸点溶剂发生挥发,进而使得膜表皮的聚合物浓度提高,形成初生皮层,且皮层以下的膜液仍处于可流动状态;接着初生膜进入凝胶浴发生液-液分相,在这个阶段膜的主体结构主要通过溶剂-非溶剂交换以及膜内组分相分离形成[338]。事实上干纺阶段形成的表皮层,对膜内主体与凝胶浴之间的传质形成阻力。Strathmann等[274]通过实验发现表皮层的扩散系数比其下的膜主体扩散系数要低两个数量级。表皮层所形成的阻力直接影响到其下膜主体在凝胶浴内发生的溶剂非溶剂交换速率,从而使得其下支撑层发生不同的液-液分相及凝胶,进而影响到所形成的分离膜支撑层结构。在膜制备过程中当非溶剂诱导的分相发生时,在贫聚合物相内发生成核现象,并在富聚合物相内生长变大,膜最终成型后贫聚合物相形成多孔结构而富聚合物相形成相对致密的膜主体结构。某些情况下聚合物稀相内的核会增大形成大孔结构,这主要是由于从周围聚合物溶液向核内的溶剂扩散速率高于反向的非溶剂扩散所导致的[339]。只要核周围是稳定的(没有新核产生且核内没有凝胶现象发生),核生长增大就会继续发生。这样就会在膜内形成直径20~100μm的锥形(或指状)或者球形大孔,这些大孔在膜承受较高压力时成为可能引起膜破裂的位点。
12.3.12.3 膜制备过程的主要影响因素
铸膜液配方、成膜条件如环境温度、湿度、环境气流速率、凝胶条件、纺丝速度、芯液组成等影响膜性能重要因素。后处理及干燥方式对膜性能也有重大影响。
(1)铸膜液配方
①聚合物浓度 一般而言,随着铸膜液中聚合物含量增加,初凝胶时皮层铸膜液中聚合物浓度越高,膜孔径和孔隙率都减小,最后形成膜的皮层较厚,膜对气体渗透速率低,分离系数越接近材料本征值。
②溶剂选择 相转化法制造高分子膜,需要配制铸膜液溶液,合适的溶剂通常遵循以下三条原则:
a.溶剂与聚合物的溶解度参数相近原则,即组分间溶解度参数越接近,混合自由焓越小,溶解性能越好;
b.溶剂与聚合物的极性相近原则,即相似相溶;
c.溶剂与聚合物的路易斯酸、碱性相配原则。
溶解过程中通过溶剂与高分子间路易斯酸、碱的配对作用,溶剂分子向高分子中可溶剂化点位扩散,增加高分子链的可移动性,最终形成均匀的高分子溶液。成膜过程中由于凝胶中溶剂分子与高分子间的路易斯酸碱配对作用调节了高分子的聚集态结构,对改善膜的气体透过性特别有效[336]。
常用于制备气体分离膜的聚合物溶剂有N,N-二甲基甲酰胺(DMF)、N,N-二甲基乙酰胺(DMAC)、二甲基亚砜(DMSO)、六甲基磷酰胺(HMPA)、N-甲基吡咯烷酮(NMP)、磷酸三乙酯(TEP)、磷酸三甲酯(TMP)、四甲基脲(TMU)等,其相应的物性见表12-41[340,341]。DMAC、DMF和NMP是常用溶剂,它们对多数聚合物溶解能力强、毒性低,且都与非溶剂水具有良好的相溶性。
表12-41 常见有机溶剂的热力学特性

注:δds为溶剂溶解度参数的色散分量;δps为溶剂溶解度参数的极化分量;δhs为溶剂参数的氢键分量;δts为溶剂浓度参数;Ds-w为溶剂在水中的扩散系数;Dw-s为水在溶剂中的扩散系数。
可以把溶剂分为3类:a. DMSO、NMP,趋于形成指状孔结构;b. TMP、DMAc、TMU、DMF,指状孔和海绵状共存;c. HMPA、TEP,趋于形成海绵状孔结构。
常用成膜聚合物的溶解度参数见表12-42。
表12-42 聚合物的溶解度参数

Zadhoush等[342]研究了不同溶剂的溶解能力对聚砜膜结构及性能的影响。他们发现当采用2-吡咯烷酮作为溶剂时,所制备的聚砜膜具有多孔皮层及网状结构,大孔较少;当NMP作为溶剂时,所制备的聚砜膜表现出致密皮层及明显的蜂窝状及指状孔结构。与NMP相比,2-吡咯烷酮对聚砜的溶解能力差,它的加入使得该铸膜体系膜液的黏度明显增大,同时它与聚砜链之间形成的氢键作用也使得该体系的相分离发生延迟。膜性能的评价结果与其结构相对应,即弱溶剂2-吡咯烷酮的加入使得膜的通量增加而分离性能下降。
Bottino等[343-345]分别考察了DMAC、DMF、DMSO、HMPA、NMP、TEP和TMU七种溶剂对PVDF膜结构影响:a. DMF为溶剂时,在膜上表层形成大而短的指状孔,其余部分属于海绵状结构;b. DMAC、TMU和TMP为溶剂时,形成的孔径适中,上表层比下表层致密,指状孔几乎横贯整张膜;c. DMSO和NMP为溶剂时,形成大量宽而长的不规则指状孔,并且指状孔相互连通形成较大的空腔;d. MPA为溶剂时,则在整个海绵状孔中间夹杂着短的指状孔和孤立的洞;e. TEP为溶剂时,趋于形成海绵状结构,指状孔小部分存在。
③低沸点非溶剂选择[346-348] 干-湿法相转化制膜工艺中,非溶剂添加剂也是常用的组分,当挥发性溶剂组分蒸发后,铸膜液进入分相区发生分相,形成孔状结构。低沸点添加剂的加入有利于减小网络尺寸,使膜的结构趋于细密。由于添加剂的快速挥发,在膜的表面会形成一层较厚的致密皮层,例如四氢呋喃(THF)、丙酮、乙醇、丙醇、乙酸等的加入,使膜的平均孔径减小,通量降低,选择性提高。
Koros等[280]将干-湿相分离工艺应用于纺丝工艺,制备了用于气体分离的不对称聚砜中空纤维。由THF组成的纺丝溶液作为挥发性溶剂,DMAC为挥发性较弱的溶剂,乙醇为非溶剂,在初生的中空纤维膜与水的混凝之前,诱导其相分离,见图12-48。通过正交实验设计,优化了纤维的渗透性能选择性。表皮厚度为120nm,O2/N2分离系数5.8,O2渗透速率(P/L=8.8GPU,皮层基本无缺陷。

图12-48 干/湿纺丝过程中早期的相分离情况
Han等[349]研究了通过添加不同量PVP以改变膜液黏度后对PSF/NMP铸膜体系所制备膜性能的影响。他们发现向该体系内添加非溶剂PVP后,一方面因组成更接近相分离点而促进膜液的热力学相变;另一方面膜液的黏度变大又会导致膜液相变动力学受到阻碍。因此,聚砜铸膜体系分相行为受到这两种因素的共同控制。在低PVP添加量(约5%)时,膜液的热力学相变起主要控制作用,所制备的膜分离层薄,大孔多,故通量较大;当PVP添加量较高时,膜液黏度的急剧增加导致分相动力学速率的变慢,完全抵消了其对热力学分相行为的促进作用,故发生延迟相分离使得所制备的膜皮层变厚,孔减小,故而通量较低。
Ismail等[350]研究了PEI铸膜体系溶剂比例(非挥发性溶剂/挥发性溶剂)对膜结构及性能的影响。他们发现减小溶剂比例,即增加膜液中挥发性溶剂THF的添加量可使得膜的致密皮层变厚,膜表面孔隙率变低。这主要归因于干纺阶段膜表面挥发性溶剂THF的挥发导致膜表面聚合物浓度发生明显增加。他们的研究证明了膜液的聚合物浓度、溶剂比、强制对流挥发时间、剪切速率等是控制非对称膜致密皮层完整度的关键因素。
(2)预挥发/干程、纺丝速度的影响
对于干法、干/湿法相转化,挥发时间的变化不仅改变了铸膜液的组成,也改变了铸膜液中聚合物的聚集态结构,因而对膜的形态结构有着复杂的影响。随着预蒸发时间的延长,由于溶剂的挥发,使初生膜暴露于空气一侧的表层中聚合物浓度局部增大,所形成的膜表面层中的网络孔较小。
①气流影响 与平板膜相比,中空纤维膜通过干湿纺制备的过程明显不同:中空纤维膜的高速纺丝决定了初生膜在干纺阶段的停留时间只能保持在1/100~1/10s的水平,远远短于平板膜的3~10s的挥发时间;而优点在于可以很方便地控制膜液出喷头的温度,使得其非常接近膜液中挥发性溶剂的沸点。这样初生膜离开喷头进入干纺阶段后,膜液内的低沸点溶剂会发生闪蒸现象,减少此阶段气体对流促使溶剂挥发的依赖,使得初生膜皮层的聚合物浓度提高,有助于形成致密皮层。同时通过对干纺阶段施加N2对流以调节空气中所含水分,即调节相对湿度对干纺阶段的影响[337]。
②纺丝速度影响溶液流变与剪切速度 在中空纤维膜制备过程中,高黏度的聚合物膜液从喷头高速挤出,其所承受的剪切流变将会影响聚合物链的规整度及膜成型过程中的凝胶机理,此方面的研究逐渐引起重视。Shilton等[351]以聚砜铸膜体系为对象,系统研究了溶液流变的影响,他们发现不同温度下流变对膜液分相表现出不同的影响。在低温(-15.0℃)下即使无剪切膜液仍有可能发生相变;在中低温(-5.0℃)下70s-1的剪切速率即有可能诱发膜液发生相变;在相对高温(-5.0℃以上)情况下,400~1000s-1的剪切速率也不能诱发膜液发生相变。
对强制对流纺丝体系而言,高剪切速率与低凝胶强度的芯液结合有利于制备出高选择系数的聚砜中空纤维膜。高剪切情况下可促使经过喷头挤出的聚合物链发生重排,聚合物链的重排将提高膜表面分离层的规整度,进而促使膜的分离系数得到提高,使得所制备的中空纤维膜表现出高于材料本征分离系数的分离性能[352]。
Lai等[350]希望通过对制膜过程中流变学进行研究,不通过热处理和涂层等后处理手段直接制备无缺陷和超薄皮层的不对称气体分离膜。他们选用聚砜/DMAC/THF/乙醇制膜体系进行研究,发现聚合物浓度、铸膜液中低沸点溶剂和高沸点溶剂的组成、强制对流蒸发时间和制膜过程的剪切速率对于皮层的厚度和皮层完整性有重要影响。铸膜液中聚合物和低沸点溶剂增加,蒸发时间延长导致分离膜皮层变厚,表面孔隙率降低。增加制膜过程中铸膜液的剪切速率,可以减小皮层厚度,增加皮层中分子取向。在剪切速率小于381s-1之前,皮层的形成主要是通过旋节分相过程,随着剪切速率增加,氮气、氢气的渗透速率和选择性都有所提高。当剪切速率超过381s-1之后,剪切力对聚合物的分相过程造成影响,形成多孔皮层,氮气渗透速率增加、氢气的渗透速率和选择性都有所降低。通过改变纺丝过程中制膜液的流变性能可以制备出无缺陷、超薄皮层的不对称气体分离膜。
(3)非溶剂凝胶浴及其温度选择
在相分离法制膜过程中,气相或液相的非溶剂与铸膜液接触传质改变液态膜的组成,并进而分相成膜,这是关键的一步,决定了膜的结构和性能。这里非溶剂的选择是重要的,其组成和性质对溶剂与非溶剂之间的传质动力学与成膜体系的分相热力学性质有很大影响。对其选择也有一些经验可以遵循:如溶剂与非溶剂必须互溶,强非溶剂易造成瞬时分相,形成孔状结构;弱非溶剂大多是延时分相,形成海绵状结构。
作为绝大多数聚合物溶液的强非溶剂的自来水是常用的非溶剂凝胶浴。另外,醇类也很常用。Bottino等[353]研究了水、甲醇及其水混合物、乙醇及其水混合物、甘油及其水混合物、溶剂水混合物、正丁醇、四氯化碳、氯仿、乙醚、四氯乙烯、四氯乙烷等各种非溶剂对磺化聚偏氟乙烯相分离成膜过程的影响,结果显示在弱凝胶浴组成下,膜结构均为海绵状结构,将弱非溶剂加到强非溶剂水中时,随着弱非溶剂浓度的增加,膜结构依次从指孔状结构转变成海绵状结构,并且膜通量减小。Deshmukh等[354]在PVDF/DMAC体系下得到的结论相同。吴庸烈等[355]研究了不同浓度的甲醇和乙醇水溶液对膜结构的影响,发现对不同的非溶剂体系,膜结构的转变点处凝胶浴的平均溶解度参数是相同的。Cheng等[356]则在水中加入了一定量的溶剂,认为凝胶浴中加入溶剂后减慢了传质速度,从而影响了膜结构。
M.Khayet等[285]研究了外凝胶浴对PVDF-HFP膜结构及性能的影响。他们发现通过向凝胶水浴中添加溶剂DMAC,可以避免形成膜致密皮层,所制备膜的通量明显增加。DMAC的加入明显减弱了凝胶水浴对膜液的分相能力,使得所制备的膜更多孔且孔更大。当DMAC在内/外凝胶浴中的浓度同时达到50%~60%时,所制备的膜表现出内侧通孔、外侧无皮层、断面呈海绵状孔的整体结构。
毛智明等[357]研究了凝胶浴温度对溶剂法纤维素中空纤维膜结构与性能的影响。他们以N,N-二甲基乙酰胺为非溶剂添加剂制备了纤维素非对称中空纤维膜,考察了外凝胶浴温度对纤维素非对称中空纤维膜结构和性能的影响。实验结果证明,随外凝胶浴温度的升高,膜的相转化速率逐渐变快,由延迟相分离向瞬间相分离过渡,在外凝胶浴温度为65℃时,膜外皮层厚度明显减小且断面出现更多的指状孔结构。
凝胶浴温度的提高使膜厚和透水速度增加[358],这是由于高的凝胶浴温度使凝胶剂分子运动的速度加快,具有较高的能量,易于扩散进入初生膜,加速高分子在聚集过程的凝胶化。由于凝胶剂扩散速率的加快,容易形成较疏松的膜结构,使膜的透水速度加快,膜的厚度也因固化前处于高度溶胀状态(固化剂大量进入),结构疏松而增厚。
总之,通过调整非溶剂凝胶浴的溶解度参数、传质特性等可以改变液态膜中溶剂与非溶剂之间的相对传质速度调整液态膜组成,并改变相分离体系的热力学特性,从而改变膜结构和性能。
芯液的选择对于中空纤维膜的制备至关重要。Wang等[359]研究了水和乙醇在PVDF/DMAC体系中作为芯液对膜结构和性能的影响,结果表明乙醇作为芯液所制备的膜内壁的皮层消失,有效孔隙率增大,气体渗透通量增大。
(4)膜的后处理
对固化后的湿膜进行后处理是极其重要的程序,它会对分离膜的最终渗透性能产生巨大影响。将膜浸入一定温度的热水中加热一段时间,一般来说可以达到减小孔隙率和孔径、提高膜的选择渗透性的效果。这是因为当温度升高到膜的玻璃化温度之上时,链段运动开始解冻,分子链段运动的弛豫时间缩短,相邻链段在成膜时引起的残余应力或分子间相互作用力的影响下互相接近,引起大分子的迁移运动,从而缩小了部分空隙,减小了膜孔径。
在后处理过程中,膜内残留的溶剂及非溶剂应该被有效去除,干燥时纤维膜发生相应收缩并确定最终的膜结构。
表12-43中序号1、3是湿膜采用直接空气干燥;2、4是采用先用乙醇置换,然后再用己烷置换乙醇,最后是空气干燥。
表12-43 干燥方式的中空纤维膜气体渗透性能的影响

注:1、2和3、4样品分别采用不同的制备方法。
从表12-43中可很明显地看出,两种不同干燥方式所得到膜性能截然不同。直接空气干燥时,由于水的沸点比溶剂(NMP)低,首先蒸发掉,留下来的溶剂使膜表面及其附近的微孔重新融合,使膜皮层变厚。如果先用乙醇、己烷进行置换,膜内残留溶剂可基本上被置换掉,不会发生膜内微孔再融合现象,所以膜皮层较薄,渗透速率比较大,且分离系数有所减少。
Peinemann等[360]研究了不同后处理方法对PEI膜性能的影响,主要包括在不同温度下用水对膜进行处理(90℃下2h,20℃下4h);室温下丙酮或乙醇处理2h。他们发现高温水及室温丙酮处理后的PEI膜经70℃干燥后膜的氧气渗透速率更高。室温下水处理的PEI膜导致了较厚的致密皮层,其氧气渗透速率极低。这主要是因为膜内的溶剂未充分去除,在干燥过程中因为溶剂的存在使得聚合物发生再溶解,造成了膜内原来的多孔结构致密化。在铸膜液中的非溶剂丁内酯含量较高的情况下,因为膜内残留的溶剂含量更低,使得后处理对膜结构及性能的影响程度变小。在水处理情况下温度越高对膜内残留溶剂的清洗效果更好,所制备的分离膜最终气体渗透性能也更优越。
在湿态膜的干燥过程中,在聚合物与水相互作用力较强的情况下,往往会出现随着水挥发导致的毛细管力使得孔结构坍塌造成的膜结构致密化,极大地破坏了其气体渗透分离性能。这是因为相分离法成膜的非溶剂一般为水,成膜后残留在孔中的稀相液的主要成分是水,其表面张力高达72.3mN/m,而膜中孔径一般在10-8~10-6m数量级,根据Laplace方程,在干燥过程中其毛细管应力高达1.45~145bar,所以用低表面张力的有机溶剂置换水来避免如此高的毛细管应力造成毛细管坍塌,减少膜的孔隙率。科学家们一直致力于寻找一种合适的干燥方法。1964年,Riley等[361]尝试使用四氯化碳来萃取湿态CA反渗透膜中的水分,尽管效果尚可,但是实验证明这种方法耗时太长。1969年Kenneth等[362]采用不同浓度下不同种类的表面活性剂浸泡CA膜,然后置空干燥,发现可以很好地避免在干燥过程中造成的膜收缩。1970年Gantzel和Merten[363]采用-10℃快速冷却与真空升华方法干燥CA反渗透膜,干膜的N2渗透速率为3.1×10-6cm3(STP)/(cm2·s·cmHg),He对N2的分离系数为34,虽然低于CA的本征值97,但是已经表现出一定的气体分离能力。1988年Lui等[364]采用不同的溶剂置换方法干燥CA膜,他们发现湿态膜表面存在一个临界孔径,经溶剂置换干燥后可以具备最优的CO2与CH4分离性能。介兴明等[365]为避免纤维素的膜结构被破坏,采用乙醇-正己烷-空气干燥方法制备纤维素干膜样品,得到了较好的膜结构保留。在所有这些干燥方法中,溶剂置换法(即先采用低碳醇置换膜内的水,再采用非极性低沸点的正己烷置换膜内低碳醇,非极性的正己烷挥发对膜结构影响极小)因为相对较为简单的工艺与较好的效果而被认为是最可取的干燥方法。
Wang等[366]比较了用甲醇、乙醇、1-丙醇、正己烷置换干燥的情况下膜的性能,发现用有机非溶剂处理后膜通量提高了3~4倍,膜孔径稍有增加,但增加的通量主要是由有效孔隙率的增加提供的。Deshmukh等[354]发现在这三种醇中,用甲醇处理的膜通量稍低,可能是因为甲醇的快速挥发,使膜在干燥前残留一部分水分从而发生收缩。Cheng等[356]在制膜过程中则采用了先用乙醇再用正己烷分步置换、干燥的处理方式。这是由于乙醇与水有良好的相溶性,然而乙醇较水易挥发,干燥时最后仍残留较多的水,所以进一步用正己烷置换乙醇水以达到满意的效果。
12.3.12.4 支撑层孔结构形成机理
(1)支撑层中指状孔形成
用光学显微镜或电子显微观察膜断面结构,可观察到两类不同膜结构,如图12-49[342]。

图12-49 分离膜断面的电镜照片[342]
一类是由快速凝胶(即瞬时相分离)制备的膜,断面是“空腔孔”或称“指状孔”结构,包括形态各异的大空腔,有指状、锥形和泪滴等形状。通常这类膜具有高孔隙率和高渗透速率,但分离系数或截留率低,而且机械强度差,耐压性能不好,适用微孔过滤或超滤。空腔孔通常在瞬间相分离情况下产生,其生长速度比凝胶前峰的移动速度快,增加铸膜液的黏度或调整溶剂/非溶剂配对延迟相分离都能降低大空腔的生成趋势[265,339,368]。另一类是在相对慢凝胶过程中所形成的膜,断面是海绵状结构。这类膜具有低孔隙率和低渗透速率,分离系数或截留率较高,能耐较高压力,适用于反渗透或气体分离。
指状孔既可能出现在膜的外(内)表面附近,也可能离开表面出现在膜断面内部。通常指状孔结构的膜耐压强度差,使用过程中易被压密,渗透速率衰减快。尤其对中空纤维膜,严重时膜会被压塌,以至不能使用。因此,希望在制膜中消除支撑层指状孔结构。
针对聚合物-溶剂-非溶剂体系,许多研究者发现抑制指状孔规律,归纳如下:
a.选择相溶性差溶剂/非溶剂作制膜溶剂/沉淀剂;
b.增加铸膜液配方中聚合物浓度,或者在浸入沉淀浴前,先预蒸发溶剂,提高铸膜液中聚合物浓度;
c.向铸膜液中添加少量非溶剂;
d.向沉淀浴中添加溶剂等。
指状孔形成过程可分为两个过程:初生孔核产生;核成长而形成指状孔。
伴随成膜机理的研究,出现了许多描述大空腔形成的理论或假说,指状孔形成机理已有不少文献报道。关于初生孔核的成因,粗分为机械作用现象、界面现象和液-液相分离现象;核孔成长也可分为扩散成长和对流成长。下面选择较主要的工作予以介绍。
①Strathmann模型[367] Strathmann认为大空腔是浸入后皮层收缩产生的应力作用的结果。当铸膜液浸入沉淀浴后,在膜表面形成固态皮层。由于聚合物松弛慢,在膜液收缩时所产生的应力不能及时释放,致使皮层破裂而形成初生孔核。当新形成孔核壁上膜液脱溶剂而发生收缩时,使核孔不断成长,直至孔壁固化,形成指状孔结构。
②Matz模型[369] Matz和Ray等认为大空腔与界面现象有关。针对醋酸纤维素/丙酮/水体系,Matz等[369]认为在沉浸过程中,水与丙酮传质交换,膜液/沉淀浴界面的张力减少到0。这时,界面变得极不稳定,使水很容易浸入膜液,形成初生核孔。孔核底部由于与浴接触,丙酮浓度低而固化;孔核顶部则由于膜液本体中丙酮扩散进入使得浓度高,仍保持低界面张力,使水不断向内浸入,最后形成指状孔结构。Ray等[370]认为铸膜液表面溶剂蒸发使气液形成大的浓度梯度,因而产生了界面过量分子作用势梯度,使在界面存在的浓度随机扰动不断扩大,形成铸膜液表面孔洞结构。
③Smolders模型(或称成核-成长模型)[368] Smolders等注意到:指状孔出现在膜皮层下,而且往往瞬时相分离产生指状孔,而延时相分离则是海绵状结构, 因此认为液-液相分离是指状孔的成因。他们提出了指状孔形成的成核-成长机理,即当铸膜液与沉淀浴接触发生瞬时分离时,在皮层下产生贫相细核,这初始核当于新的沉淀浴,与其下面铸膜液接触。当核中溶剂浓度高时,将发生延时相分离,没有新核产生。在延时时间内,铸膜液本体中溶剂不断向核中扩散,核将持续成长,直至周围聚合物固化,最后形成指状孔结构;皮层下相分离的非均相性造成扩散前沿不规整,它决定大空腔前锋的位置。当核中非溶剂浓度高时,又发生瞬时相分离,这样初始细核的生长被抑制,通常形成海绵状结构。因此,增大铸膜液的黏度不会抑制指状孔,但抑制初始核产生或者抑制核生长,均可有效消除膜内指状孔产生。
④Koros等[371]对膜表面下层的大空穴形成原因进行探讨,指出大空穴的尺寸和存在位置主要由动力学因素所影响,局部的溶剂和非溶剂间的交换速率比与聚合物富相形成速率之间的竞争决定大空腔的生长。在相分离过程中,聚合物贫相被聚合物富相所包围,因水的扩散速率大于溶剂的扩散速率,相邻的聚合物贫相和富相之间存在水的浓度差,导致二者之间存在水的渗透压。当贫相与富相之间的渗透压大于二者之间聚合物固化后的强度时,聚合物贫相可使周围的聚合物富相破裂而继续生长,形成大空穴。反之则聚合物贫相生长停止,形成海绵状结构。
用成核-生长模型可以较好解释上述抑制指状孔产生的经验规律。事实上抑制指状孔规律中a、b、c是抑制初始核生长;而d是使铸膜液倾向于延时相分离发生,从而抑制核产生。明显地,影响液-液相分离的因素也是影响指状孔形成的因素,其中较主要是选择溶剂/非溶剂对。例如,相溶好的溶剂/非溶剂DMSO/H2O、DMAC/H2O、DMF/H2O和NMP/H2O配对,用于多种聚合物如聚酰胺、聚砜、醋酸纤维素等制膜,所形成的膜都有指状孔结构。大空腔的形成十分复杂,不同形状大空腔的成因不尽相同,试图用一种理论解释大空腔的形成机理目前尚有困难。
(2)支撑层中海绵状结构形成
任何有助于减缓凝胶速度的措施,如选用相互扩散系数小的溶剂/非溶剂对,或在凝胶介质中加入各种添加剂,或增加铸膜液或其表层聚合物浓度,均有利于形成海绵状结构。具体方法如下:
①聚合物浓度:当聚合物浓度高于临界点浓度时,则会形成具有良好机械性能的类似胞腔状的结构。
②添加剂影响:分为高分子添加剂和低分子添加剂,添加剂引入会改变铸膜液的热力学和动力学性质。添加剂引入一方面降低铸膜液的热力学稳定性,促进相分离;另一方面提高铸膜液的黏度,延缓相分离。添加剂的分子量和加入量决定哪方面起主导作用。加入高分子量的PVP容易形成海绵状孔[372],当聚砜铸膜液中司盘80的含量增加到15%时,聚砜膜的结构从指状孔变为海绵状孔[373]。
③溶剂/非溶剂体系:溶剂与聚合物相溶性越好,成膜聚合物在非溶剂中分相、固化的速度越慢,越易形成均一的海绵状结构[374]。换言之,当溶剂与非溶剂之间溶解度参数的差值|Δδ|越小时,铸膜液在凝固浴中成膜越慢,越容易延时分相,易形成海绵状孔[375]。
④凝固浴的组成:向凝固浴中加入一定量的溶剂,可以降低溶剂与非溶剂之间的扩散速率,有助于形成海绵状孔[376]。在凝胶浴中加入一定量的弱非溶剂(如醇类等),会延迟相分离速度,形成海绵状孔[354]。
⑤成膜温度:温度对成膜过程的影响分为两方面,一方面,升温有利于提高铸膜液的热力学稳定性;另一方面,温度的升高会加快分子扩散速率,同时降低体系黏度,降低传质阻力。因此,凝固浴温度对膜结构和性能的影响随着制膜体系不同而不同,需要针对特定体系进行系统实验和深入分析[358]。
⑥空气湿度:如果空气浴中含水量较大,聚合物溶液空气浴过程中会吸收空气中的水分,从而使得表面产生分相,形成薄膜,浸入凝固浴后铸膜液主体与凝固浴中非溶剂的传质阻力因为这层薄膜的存在而变大,分相过程极其缓慢,这种分相过程可以制备具有多孔表面和网兜状断面结构的膜,这种方法一般用于制备大孔径多孔膜[377]。
⑦空气浴时间:当铸膜液中含有挥发性溶剂时,随着在空气浴中溶剂的蒸发,溶液组成进入两相区并发生分相,浸入凝固浴后铸膜液表面的分相会极大降低成膜速率,通过这种方法可制得具有对称结构的海绵状超滤膜[348]。