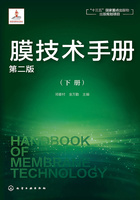
12.2 气体分离膜材料及分离原理
12.2.1 膜分类
气体分离膜按膜结构形态分成对称膜与非对称膜(不对称膜)两大类,如图12-1所示。

图12-1 分离膜的结构形态分类
对称膜厚度范围为10~200μm,传质阻力取决于整张膜的厚度。对称膜中致密膜的结构最为紧密,渗透通量很小,工业过程实际应用很少,主要用在实验室表征材料的本征渗透分离性能。其制备方法主要包括溶液浇铸和熔融挤压等。对称膜中的多孔膜按其孔径大小还可分为分子流、表面扩散流、毛细管冷凝作用和分子筛分作用等。但多孔膜与非多孔膜界限难以截然分开,通常认为如果气体透过膜主要受通道(即孔)的大小影响,是多孔膜;而通过高分子链热运动间隙(即自由体积)透过膜的是非多孔膜。一般高分子膜的自由体积约1nm3,因此认为多孔膜的下限孔径约为1nm。
非对称膜由多孔支撑层和致密皮层构成,皮层厚度通常为0.05~0.3μm,支撑层厚度约50~200μm。传质阻力主要取决于皮层厚度,支撑层承受机械压力。其制备方法主要是溶液相分离法。还可以采用复合膜形式制造非对称膜,非对称膜的皮层与支撑层由不同材料制造。目前工业用膜大多采用非对称膜。
12.2.2 气体分离膜材料(按材料化学分类)
膜材料是膜技术的核心,其性能优劣会直接影响气体分离性能、应用范围、使用条件及寿命等。理想的气体分离膜材料应同时具有高透气性和选择性、良好的机械性能、优良的热性能和化学稳定性以及成膜加工性能、材料价格便宜等。气体分离膜可以由多种材料制备,主要有高分子聚合物材料[21]、无机材料和杂化材料等。
12.2.2.1 有机高分子膜材料
有机膜是研究最早、发展最成熟的一类气体分离膜,具有以下优点:
①膜材料种类多,可满足不同分离过程的要求;
②材料价格便宜,具有经济竞争优势;
③材料柔韧性好,易于膜加工成各种型式(如平板式、管式和中空纤维式等)及组装成膜组件;
④制膜工艺已经成熟,制膜成本较低,易于规模化生产。
作为气体膜材料需满足以下要求:
①高通量和高选择性。但膜的渗透性和选择性往往矛盾,通常膜材料的渗透性越好,其选择性会越差,反之亦然,即渗透性和选择性受Robeson上限的限制[22]。因此,对特定待分离体系,选择聚合物材料必须考虑均衡的透过性及选择性。
②较好的机械强度和耐热性。不少气体分离膜在数十个大气压下操作,要求膜材料具有一定机械强度及抗压能力。一般机械强度随温度升高而降低,当温度太高时膜会发生蠕变破坏。理论上聚合物材料的使用温度上限是其玻璃化转变温度,但由于受聚合物膜内非平衡态自由体积衰减和原料气中可塑化气体或杂质等影响,实际上膜使用温度远低于其玻璃化转变温度[23]。
③较强的耐化学腐蚀性。膜在实际操作过程中必然要与一些极性的气体甚至液体组分相接触,如果膜不具备较好的耐化学性能,就会与原料发生反应,从而影响膜的性能,乃至减少膜的寿命[24]。
④作为膜材料,聚合物必须价格低廉且容易制备,所用溶剂最好能与水互溶,规模化生产时安全性好,制膜经济性好,以保证竞争力。
聚合物作为气体分离膜材料已经研究了几十年,且已被市场接受。表12-4列出了部分商用聚合物膜材料的气体选择透过性。影响气体渗透的聚合物材料本身主要因素有:聚合物性质(包括不饱和程度、交联、结晶度和取代基的性质等)、聚合物摩尔质量、聚合物的自由体积和分子链段迁移率等。渗透分子大小和形状等也是影响气体渗透率的主要因素,文献[25]详细讨论了膜特性、聚合物结构与分离效果之间的关系。
表12-4 部分商用聚合物膜材料的气体选择透过性

注:1Barrer=10-10cm3(STP)·cm/(cm2·s·cmHg)。
目前市场用的膜材料大多是工程塑料,为进一步改善膜材料渗透分离性能,可以对膜材料进行功能化改性,文献[26]详述了各种功能化改性策略,针对气体通过膜传质是扩散控制还是溶解控制两种方式,提出:扩散控制膜主要是通过引入官能团促进或抑制链的堆积来控制非晶聚合物的自由体积,但此类膜的气体渗透性和选择性受Robeson上限限制。溶解控制利用与某些渗透分子具有化学相互作用的官能团增加气体溶解度,并提供增强扩散渗透途径,这种功能化膜气体渗透性能可超越Robeson上限限制,但经常会受到杂质影响导致化学功能失活。
20世纪90年代末,俄罗斯科学院Topchiev石油化工合成研究所(Topchiev Institute of Petrochemical Synthesis,Russian Academy of Sciences)开发并定期更新的“玻璃态聚合物的气体分离特性”数据库,列有大量高分子材料对气体的渗透系数数据可供查阅。利用该数据库还可以用基团贡献法计算新型聚合物的渗透系数。另外,数据库还附有正电子湮灭寿命光谱测量的聚合物自由体积信息。
气体分离膜中常用的有机高分子材料主要包括以下几类:纤维素类衍生物、聚砜类、聚酰胺类、聚酰亚胺类、聚酯类、聚烯烃类、乙烯类聚合物、含硅聚合物、含氟聚合物以及甲壳素类等[27]。
纤维素(结构式见图12-2)是自然界最为丰富的天然高分子,来源广泛且可以再生,是最廉价且具备优异性能的膜材料[28,29],纤维素及其衍生物是应用研究最早、应用较多的膜材料,主要包括纤维素、醋酸纤维素、硝酸纤维素等。其中醋酸纤维素具有较高的气体透过率和较高气体选择系数,可制成O2/N2分离膜和CO2/CH4分离膜。

图12-2 纤维素的化学结构式
因醋酸纤维素膜具有较高抗高碳烃类气体塑化能力,UOP公司用它制成卷式膜已广泛用到天然气脱碳市场。然而,利用纤维素材料制备的气体分离膜主要缺点是易被压密,热稳定性较差[30]。
聚砜是机械强度好、耐热、耐酸碱、价格较便宜的膜材料,且在N-甲基吡咯烷酮(NMP)、二甲基亚砜(DMSO)以及N,N-二甲基乙酰胺(DMAC)等常用非质子极性溶剂中具有良好的溶解性图12-3是一些常用的商用聚砜材料的化学结构式,该材料使用范围广,除了用于微滤和超滤以外,还是多种商品复合膜(如反渗透膜、气体分离膜等)的支撑层材料,本身也可用于制备气体分离膜。最早商业化应用的Prism膜分离器的材料就是双酚A型聚砜,经硅橡胶涂层后用于合成氨驰放气、炼厂气中氢气的回收等。聚砜材料的气体分离膜主要缺点是气体渗透性和选择性不够高(常温下聚砜材料的O2渗透系数和O2/N2分离系数分别为1.0Barrer和6左右)。除双酚A型聚砜外,其他常见的聚砜材料如聚芳醚砜(PES)、酚酞型聚醚砜(PES-C)、聚芳砜等都可用于制作气体分离膜。

图12-3 商用聚砜材料的化学结构式
聚酯类树脂具有强度高,尺寸稳定性好,耐热、耐溶剂和化学品的优良性能,广泛用作分离膜的支撑增强材料[34]。聚酯类树脂主要有涤纶、聚对苯二甲酸丁二醇酯和聚碳酸酯等。另外,聚四溴碳酸酯由于其良好的氧氮渗透选择性,可作为性能优越的富氧膜材料使用。
聚烯烃类主要包括聚乙烯、聚丙烯、聚氯乙烯、聚偏氯乙烯和聚4-甲基-1-戊烯等。聚乙烯和聚丙烯难以用溶剂溶解,通常采用熔融拉伸法制作多孔膜,因疏水性比较强,可用在膜吸收过程。聚4-甲基-1-戊烯的O2和CO2渗透系数分别为32.2Barrer和92.6Barrer,O2/N2 分离系数为4左右,渗透系数次于硅橡胶,但选择性远高于硅橡胶,且可制成皮层约1μm非对称中空纤维膜,是比较理想的空气分离膜和脱湿膜材料,是目前ECMO膜的首选材料。聚4-甲基-1-戊烯经表面氟化后氧氮选择性高达7~8[35]。PVA(聚乙烯醇)常用于和其他成膜性能不好的聚合物或无机物共混制膜[36]。
含硅聚合物主要包括聚二甲基硅氧烷(PDMS,化学结构式见图12-4)和聚三甲硅基丙炔(PTMSP)[37]。PDMS是现有的通用橡胶态聚合物材料中渗透速率最高的,但是机械强度差。该类材料常用于复合膜中作为底膜材料的堵孔剂,消除底膜表皮层的缺陷,使膜的选择性提高至材料的本征性能[12,13,38]。

图12-4 PDMS的化学结构式
该类材料还可以被涂覆在多孔的超滤底膜上作为功能层用于氧氮分离或有机蒸气分离[39]。
PTMSP是一种高自由体积的玻璃态聚合物,其结构特征为:主链为聚乙炔,每条链上的碳原子共平面,因而易形成长程刚性片段;侧链带有体积较大的官能团,阻碍了其长程刚性片段的密实堆积,进而形成了微孔。PTMSP透气速率比PDMS还高一个数量级,对大分子的烃类气体的渗透速率大于小分子永久性气体如氢气等,对烃类/H2具有很好的选择性。但PTMSP链刚性不强,形成的微孔不规则,分布较宽,分离永久性气体混合物的分离系数很低,如O2/N2的分离系数为1.5,且其他的应用由于化学稳定性和热稳定性以及抗老化性能较差而受到限制[40]。
含氟聚合物具有优异的高温稳定性和化学惰性、良好的耐候性、独特的气体渗透性和吸附性能,被广泛地应用于气体分离和有机蒸气渗透等领域。全氟聚合物可以由全氟单体均聚或共聚而得,聚四氟乙烯疏水性强,是膜吸收过程的理想膜材料。
表12-5列出了一些常用玻璃态和无定形态含氟聚合物的气体渗透性能。通常在含氟聚合物中引入含侧链基团的单体(如六氟丙烯、全氟丁烯基醚)或体积庞大的环状单体单元(如二氧环戊烯)来降低其结晶度,增加自由体积。其中,Teflon AF2400具有极高的气体渗透系数,其对O2的渗透系数为1600Barrer(25℃),对N2的渗透系数为780Barrer(25℃),但其对有机蒸气进行传输时易发生塑化[41]。2017年,Fang[42]等报道了一系列无定形全氟二氧戊环共聚物膜,其对He/CH4、H2/CH4、N2/CH4等的渗透选择性超过2008年Robeson上限。通过改变共聚单体的比例,聚合物膜显示出可调的传输性质,而且这些共聚物可溶于氟化溶剂中,使用现有的工业方法即可使其放大生产。然而含氟单体种类少、价格昂贵、共聚反应时单体之间的竞聚率限制了其发展。由通用高分子材料氟化也可以得到含氟聚合物,如对聚4-甲基-1-戊烯(PMP)表面氟化处理,可提高其氧氮分离系数。
表12-5 玻璃态和无定形态含氟聚合物的气体渗透性能[3]

聚酰亚胺(PI)是主链上含有酰亚胺环的一类聚合物,由芳香族或脂肪族环四酸二酐和二元胺经缩聚得到的芳杂环高聚物,具有耐高温、优良机械稳定性的优点,最早是由Bogert和Renshaw在1906年合成的。
PI的刚性主链对不同分子具备筛分作用,对H2/N2、CO2/CH4和O2/N2等具有很高的分离性能,是气体分离膜的理想材料之一。聚酰亚胺用于气体分离始于20世纪80年代,UBE首先实现了PI中空纤维膜商业化,展示了PI作为膜材料的广阔前景。目前各公司广泛采用PI作为高性能膜材料,杜邦公司在20世纪80年代末期开发了用于空气富氮的聚酰亚胺膜分离器,美国Monsanto公司开发的第二代Prism分离器也是采用聚酰亚胺膜,Medal、Parker-Hannifin和德国Evonik Industries AG公司等均采用聚酰亚胺作为气体分离膜材料,已成功应用于各种工业气体混合物的分离,如氢回收、空气分离、气体除湿和乙醇气相脱水等工业分离过程。
聚酰亚胺一般的结构式见图12-5,具有以下优势:①很高的热稳定性,可以使分离系统在较高的温度下操作;②良好的机械性能,便于制造膜组件,也使组件可以在很高的压力下操作;③优异的化学稳定性,有利于膜结构和性能的稳定;④良好的成膜性,可以选择多种成膜体系;⑤结构多样可调变,针对不同的目标分离体系,可通过选择不同的二酐或者二胺单体调整材料的分子结构,合成不同种类聚酰亚胺。聚酰亚胺主要有芳香族二酸聚酰亚胺、全芳香聚酰亚胺及全氟聚酰亚胺等。

图12-5 聚酰亚胺的一般结构
图12-6列出了四种已经商业化的聚酰亚胺材料分子式。聚酰亚胺分子链刚性强、分子链间作用力大,使聚酰亚胺具有较高的气体渗透性和选择性,例如商用聚酰亚胺Matrimide5218的气体渗透系数和分离系数均优于聚砜。表12-6列出了一些常用聚酰亚胺的气体渗透分离性能。

图12-6 四种商业化聚酰亚胺膜材料分子式
表12-6 常用聚酰亚胺的气体渗透分离性能[26]

聚酰亚胺作为气体分离膜材料具有优异综合性能,但聚酰亚胺分子链刚性强、分子链间作用力大引起聚酰亚胺分子链紧密堆砌,使得大部分聚酰亚胺的气体渗透系数仍有待进一步改善,而在一些分离体系上的选择性也需提高。设计、合成具有高渗透性和良好渗透选择性的聚酰亚胺一直是膜科学工作者追求的目标。
兼顾高透气性和良好透气选择性的理想聚酰亚胺材料结构应具有如下特征:
①刚性分子骨架,低链段活动性;
②较差的链段堆砌,即大的自由体积;
③链段相互作用要尽可能弱。
为得到理想的聚酰亚胺气体分离膜材料,可以在分子水平上对聚酰亚胺结构进行改性。通常采用以下方法:
①引入柔性结构单元;
②引入庞大的侧基;
③引入扭曲的非平面结构;
④通过共聚破坏分子的对称性和重复规整度;
⑤交联;
⑥自聚微孔聚酰亚胺膜、聚酰亚胺炭膜、热重排聚酰亚胺等;
⑦促进传递膜、混合基质聚酰亚胺膜等。
(1)共聚
共聚是在聚合物主链中引入特定链段或特定侧基,对聚合物化学结构及其组成进行调控,调节和改善材料对气体的渗透分离性能[43];或者在昂贵的材料中引入廉价单体,在基本保持膜渗透性能前提下,降低材料成本。
在刚性聚合物中引入柔性链段,形成硬段-软段共聚物,玻璃态的硬段主要提供材料的热性能和机械性能,橡胶态的软段主要提供气体渗透的微结构(图12-7)。硬段-软段聚合物能够综合两种不同性质的聚合物的特点,从而得到性能更优异的膜材料,在许多膜过程材料中受到广泛重视。常用的硬段主要有聚酰亚胺、聚酰胺和聚氨酯等,常用的软段主要有聚醚、聚硅氧烷类等[44,45]。

图12-7 硬段-软段共聚物膜材料示意图
(2)交联
聚合物交联形成网络后,减小链段活动性,可以改善聚合物膜机械性能和热性能,也可以改变聚合物结构,使渗透性能下降、渗透选择性升高[46]。常用的交联方法有[47]热处理、化学交联和光辐照交联等。
聚酰亚胺也可被二端氨基化合物交联,这种交联反应可在常温下发生。如将硬段6FDA聚酰亚胺膜在对苯二甲胺的甲醇溶液中浸泡,聚酰亚胺的酰亚胺环被打开,羰基与交联剂的氨基反应生成酰胺基,产生交联反应。图12-8模拟了交联反应发生的过程。交联也可以改善聚酰亚胺膜的抗CO2塑化性能[48]。

图12-8 聚酰亚胺膜化学交联[49]
12.2.2.2 无机材料
除有机聚合物膜外,近年来无机膜的研究得到了很大的发展。无机膜包括金属、金属氧化物、陶瓷、多孔玻璃和沸石等材料制成的膜。多孔无机膜孔径分布窄、耐高温、化学稳定性以及机械强度好[50]。
但是无机膜也存在一些缺点,例如:制造成本较高;质地脆,需要特殊的形状和支撑系统;制造大面积的膜比较困难;高温条件下膜分离器的安装和密封比较困难[42,45]。在气体分离应用上,多孔膜因孔径控制比较难,重复性不好,除了铀同位素的分离已经工业化外,其他过程均处于基础研究中,许多问题有待于深入研究和探讨,离工业化还有一段距离。
无机膜目前应用主要集中于脱氢、加氢和氧化反应。关于无机膜研究最多的方向是将金属钯用于制备氢气选择性分离膜,这主要是由于金属钯具有优良的氢气吸附和解离能力,同时具有很高的选择透过性。理论上可以将氢气与其他杂质分子完全分离,得到的氢气纯度可达到99.9995%[51,52]。为了提高机械稳定性,金属钯管厚度在100μm左右,这会导致氢气透量相对较低,制造成本相对较高。将金属钯负载在多孔基质表面,可有效将膜厚度降低到几个微米,成本降低20~40倍,透氢量提高一个数量级[53]。
目前存在的主要问题是钯膜氢脆影响使用寿命。在氢气氛下,钯膜在573K温度下存在相变(α-PdH与β-PdH),由于α-PdH与β-PdH晶相具有不同的晶胞参数,金属钯在长时间氢的溶解析出过程中导致钯反复地收缩膨胀,最终导致钯结构发生破坏[54-58]。
另外,钯膜的化学稳定性问题也是阻碍钯复合膜实现工业化的主要障碍之一[59],杂质气体如CO、CO2、CxHy及H2S等在膜表面发生化学反应,生成金属碳化物或者硫化物,明显降低了膜透氢性能,或其与体相金属的晶格参数存在差异,晶格发生膨胀,导致膜结构发生不可逆的破坏[59-62]。目前研究方向之一是把其他金属(例如Ag、Cu、Ni、Fe、Au、Pt)掺入钯中构成合金膜或者膜表面增加保护层来提升钯膜化学稳定性。
12.2.2.3 有机微孔聚合物材料
至今工业应用的膜材料都采用工程塑料或经过物理/化学改性的工程塑料。气体渗透系数和分离系数间的trade-off关系使其分离性能很难超越Robeson上限。受PTMSP高自由体积启发,2004年,P.M.Budd和N.B.McKeown合成出第一个自具微孔聚合物材料(polymers of intrinsic microporosity, PIMs),并将其命名为PIM-1[63],PIM-1是由含有螺环的四羟基单体和含有四氟基单体通过缩聚反应而制备,其CO2渗透系数达8000Barrer以上,对氮气和甲烷的选择性分别约为16和10。PIMs的衍生物多由刚性强的多卤代物与含有多个羟基的化合物发生双亲核取代反应制得。它具有刚性、扭曲的分子结构,其链段不能自由内转动,阻碍了大分子链的有效堆积,促使在膜内部形成连续的微孔结构,再加上其良好的热稳定性、溶解性成型和优良的力学性能。按照刚性扭曲单元的不同,自具微孔聚合物可分为螺环单元类(Spiro)、三蝶烯单元类(Trip)、特格勒碱单元类(Tröger Base)等[64-68]。
热致重排过程是聚合物前驱体在固态下经热处理发生原位分子内重排,羟基等官能团与亚胺环发生固态热转变,伴随着分子链结构和构型的变化,转变为另一种刚性芳杂环结构的反应,所得聚合物称为热致重排聚合物(thermally rearranged polymers,TR-polymer)。热致重排聚合物是一种具有高自由体积和特殊孔径分布的刚性微孔聚合物材料[69],2007年Freeman课题组和Lee课题组提出了“热重排”的概念[70],将聚酰亚胺进行热处理以获得更高的自由体积以及更窄的微孔尺寸分布,材料具有较大的比表面积,有利于气体分子的渗透。
热致重排反应是在相对高温下进行的,原本的柔性分子链发生原位化学反应以及分子链段的运动,形成刚性硬质共轭的片层结构,这种硬质棒状结构在三维空间中堆砌和排列,在聚合物基体中留下小分子气体可以透过的连通型微孔,实现气体快速输送。同时,较小的自由体积单元融合形成较大的连通型自由体积单元,其细颈作为可调整尺寸的“分子窗口”,减少选择性的损失[71,72]。热致重排聚合物膜表现出优异的气体渗透选择性能,超出传统聚合物膜材料。
热致重排聚合物可以通过设计前驱体的分子结构和优化热致重排过程来调控膜孔尺寸和分布,设计制备具有目标气体分离性能的热重排聚合物。其前驱体多为邻位官能化的聚酰亚胺或聚酰胺等。由于在高温处理过程聚合物分子链易降解,大大降低膜的机械性能。近年来研究主要集中在机械性能的改善、气体分离性能的进一步优化、中空纤维膜的纺制等[73],调控措施有:引入特殊官能团[74,75];共聚[76,77];通过分子链间的交联,抑制分子重排过程中膜孔的坍塌和分子链间的滑移[78-80];掺杂无机粒子[81,82]。
12.2.2.4 有机无机杂化膜
有机膜易于加工,可用于制备非对称膜,但气体渗透系数和分离系数间的trade-off关系使其分离性能很难超越Robeson上限。无机膜最大的优势就是高气体渗透分离性能,但是无机膜材料柔韧性差,制备工艺复杂。有机无机杂化膜(mixed matrix membrane)[83]是指将无机固体颗粒混入有机高分子中结合而成的膜,它通过在有机膜中引入无机粒子来提高有机膜的气体渗透分离性能,它兼具有机膜易成形、韧性好等优点和无机膜气体渗透分离性能好的特点,实现有机膜与无机膜的优势互补。无机颗粒的作用主要是:一方面通过其微孔结构的分子筛分效应促进气体分离,另一方面打破高分子链间结构堆砌促进气体分子在聚合物相中的传递,两方面的共同作用影响气体的渗透和分离性能。
被引入聚合物中制备混合基质膜的无机材料主要包括:分子筛(沸石分子筛和碳分子筛)、碳纳米管(CNTs)、二氧化硅、二氧化钛、氧化石墨烯以及新型金属-有机骨架材料(MOFs)等[84-92]。目前,混合基质膜研究面临的挑战主要有两类:分散相粒子的团聚(表层或底层团聚),有机-无机相界面缺陷。如何抑制或消除这些缺陷是混合基质膜制备过程需要解决的主要问题。
12.2.2.5 促进传递膜
用接枝或聚合方式将活性载体基团以共价键的形式连接在聚合物链上,活性载体基团能主动选择与膜上游侧的特定气体如CO2发生可逆反应,通过载体摆动来实现分子促进传递。固定载体膜材料柔韧,结晶性低,具有高渗透性能;活性基团能与特定气体进行可逆反应,因此一般都具有较高的分离选择性。固定载体膜中最常见的载体包括吡啶基、氨基和羧酸根等碱性基团[93,94]。
12.2.3 气体分离膜材料(按分离过程分类)
不同的分离体系,所需要的膜材料不同。下面将针对不同的分离体系对常见的膜材料进行介绍。
12.2.3.1 H2回收
美国Monsanto公司、Ube公司等,以聚砜/硅橡胶、聚酰亚胺、醋酸纤维素为膜材料,研制了第一代商业应用的氢气分离膜。表12-7列出了第一代用于氢气回收的膜材料及其分离性能。
表12-7 第一代用于氢气回收的膜材料

12.2.3.2 天然气中He回收
工业上通常采用低温冷凝法获得He,但是耗能较大。随着膜技术的发展,膜分离法提纯氦气展现出越来越好的应用前景。工业上应用的膜应具有高渗透选择性和良好的化学、机械和热稳定性。
(1)传统聚合物膜材料
表12-8列出了目前常用于天然气中He回收的传统聚合物膜材料,其中醋酸纤维素膜用于分离纯化He已经初步实现了商业化,Cynara(Cameron的子公司)和UOP Separex(Honeywell的子公司)可提供醋酸纤维素膜组件。聚酰亚胺及其共聚物膜在其结构中具有交替平坦且体积庞大的链段,是最具商业化前景的膜材料。
表12-8 用于天然气中He回收的传统聚合物膜材料

(2)其他膜材料
其他材料制备的分离膜在天然气中纯化He中显示出了极大的优势(表12-9、表12-10),但是由于制造成本及生产工艺不成熟等原因,其研究仍处于实验室阶段。
表12-9 用于天然气中He回收的其他聚合物膜材料

表12-10 用于天然气中He回收的混合基质膜材料

12.2.3.3 O2/N2分离
(1)聚合物膜材料
目前,用于O2/N2分离的高分子膜材料主要有聚砜、聚二甲基硅氧烷、聚酰亚胺、醋酸纤维素、聚丁二烯等。表12-11中列出了某些高分子膜材料的O2和N2渗透系数以及O2/N2的分离因子。
表12-11 用于O2/N2分离的致密聚合物膜材料

O2/N2分离膜主要用于空气的分离,可分为富氧分离膜和富氮分离膜,现在大多数的高分子膜都优先透氧,为富氧分离膜。实现膜材料的工业应用,不仅要求膜材料具有高的气体渗透性和分离因子,膜材料的化学稳定性、机械强度和长期稳定性也要满足要求。目前,硅橡胶、聚-4-甲基-1-戊烯、三醋酸纤维素和聚三甲基硅炔等高分子材料均已实现O2/N2分离膜的工业应用。
为提高分离膜的气体渗透性能,PIMs膜、热重排膜等有机微孔聚合物材料也用于O2/N2分离性能的研究。表12-12中列出了部分有机微孔聚合物膜材料的O2和N2渗透系数以及O2/N2的分离系数α。
表12-12 用于O2/N2分离的多孔聚合物膜材料

(2)无机膜材料
20世纪40年代以来,随着无机膜的发展,其在化学稳定性、机械性和耐高温方面的优势使无机膜在某些工业上开始取代高分子膜并具有工业大规模应用趋势。炭膜以其孔径均匀、孔径分布范围小、孔径范围可调且对气体的选择分离性好等优点吸引着大批的研究者。美国的Foley等[115]采用平均孔径为0.2μm的商业化多孔不锈钢板管为支撑体,通过超声喷涂的方法制备复合炭膜,以烧结的不锈钢管和多孔不锈钢板为支撑体制备的复合炭膜,氧气通量分别为43Barrer和3.3Barrer,氧氮分离因子分别达到了3.7和30.4。尽管炭膜的氧氮分离性能在现有的富氧膜材料中处于绝对领先地位,但其工业应用却受到很大的限制,其主要原因在于非支撑炭膜如中空纤维炭膜与炭薄膜,质地呈脆性,在储存、运输和使用过程易于破损;而力学性能较高的复合炭膜相对于有机聚合物膜而言制作成本又很高,难以大规模推广应用。鉴于此,对炭膜的共混改性研究受到越来越多学者的关注。将炭材料和有机聚合物共混,使炭材料的高选择性和聚合物的柔顺性、易加工性结合起来,从而在降低炭材料高制作成本的同时提高共混膜的氧氮分离性能。
Vu等[116]研究了以聚酰亚胺为前驱体在800℃裂解而成的CMS膜分散在两种商品名为Matrimid 5218和Ultem 1000的聚酰亚胺高聚物基质中形成的聚合物基质共混改性膜,O2渗透系数为6Barrer,O2/N2分离因子为8。常见的共混氧氮分离膜分离性能见表12-13。
表12-13 用于O2/N2分离的炭膜材料前驱体及膜性能

除炭膜外,陶瓷透氧膜的研究和开发引起了人们越来越普遍的关注。钙钛矿陶瓷透氧膜是一种混合氧离子电子传导膜,该类陶瓷材料不仅具有传导离子而且具有传导电子的能力,具有良好的耐溶剂腐蚀性和稳定性,由于其管径小、管壁薄及比表面积比较大,通过相转化共烧结技术制备出的陶瓷中空纤维膜的非对称结构非常适合透氧膜。常见的钙钛矿陶瓷透氧膜材料主要包括(La,Sr)(Co,Fe)O3钙钛矿型、(La,Sr)(Fe,B)O3钙钛矿型、(Ba,Sr)(Fe,B)O3钙钛矿型等[121],氧气渗透通量约为1~2mL/(min·cm2)。
迄今为止,炭膜和钙钛矿陶瓷膜还没有实现大规模工业化,还存在一些亟待解决的问题:如何增加渗透性不牺牲气体的选择性,如何实现自动化生产增强涂覆过程的均匀性,如何降低复合膜的成本,等。
12.2.3.4 CO2分离
烟道气中CO2捕集、天然气或沼气净化以及合成气脱碳制氢等实际工业过程均需分离CO2。CO2/N2、CO2/CH4和CO2/H2是三种主要的含CO2混合物体系。
(1)普通高分子膜材料
CO2分离膜材料是分离CO2膜技术的核心。目前,商品的CO2分离膜大多数是普通高分子膜,例如醋酸纤维素(CA)膜、聚砜(PSF)膜、聚醚砜(PES)膜、聚苯醚(PPO)及聚酰亚胺(PI)膜等,其选择透过机制都为扩散选择机制,CO2渗透系数为5~10Barrer,相应的CO2/CH4分离因子为20~40,已经成功用于天然气脱碳过程[122]。但是由于其渗透选择性能不高,仍需要进一步构建合适的分子结构以及聚合物堆积程度,提高CO2的扩散系数,降低CH4的扩散系数,提高膜的渗透选择性能。
酰胺基与CO2具有良好的亲和性,但聚酰胺和聚酰亚胺材料由于刚性比较强,所以膜的渗透性较差。目前较多使用的聚醚与聚酰胺嵌段共聚所制备的聚醚共聚酰胺——PEBA材料,已经商业化的最著名的就是Arkema公司生产的一系列以Pebax为商标的产品,如Pebax-1657、Pebax-2533等。由于聚酰亚胺是用二元酸酐和二元胺单体缩聚反应而来,采用不同的二元酸酐和不同的二元胺单体进行组合能制备出一系列化学结构不同的聚酰亚胺材料。大多数的聚酰亚胺都具有足够高的分子量使其能够加工成坚韧的极薄膜,具有良好的气体分离性能。
目前商品膜的渗透选择性能还远不能满足多种CO2分离过程的要求。为此,不少研究者们通过对膜材料进行分子设计及后处理,开发了很多性能优异的新型高分子膜材料。用于CO2分离研究的普通高分子膜材料主要有天然高分子材料,含氟、硫、磷的高聚物膜材料,含硅高聚物膜材料,聚酰胺和聚酰亚胺类膜材料和聚醚氧类膜材料。
研究者们发现醚氧类基团对CO2具有强的亲和作用,为此开发了一系列富含醚氧基团的聚氧乙烯型膜。聚氧乙烯型膜是指富含聚氧乙烯(PEO)链段或醚氧(EO)基团的一类膜的总称,是一类典型的CO2分离膜[123]。然而,使用纯PEO作为膜材料难以制得具有优异渗透选择性能的CO2分离膜。交联和共聚可实现膜内具有高PEO含量的同时保持膜处于橡胶态。Freeman课题组以聚乙二醇双丙烯酸酯、聚乙二醇丙烯酸酯、聚乙二醇甲醚丙烯酸酯、聚乙二醇二甲基丙烯酸酯以及它们的混合物作为聚合单体,利用光引发聚合制备了一系列交联的聚氧乙烯型膜[124-126]。研究较多的PEO型嵌段共聚物有聚氧乙烯-聚酰胺(PEO-PA)、聚氧乙烯-聚酰亚胺(PEO-PI)、聚氧乙烯-聚氨酯(PEO-PU)等[127-130]。性能较好的PEO型嵌段共聚物膜最大的优势在于它可以通过简单的涂覆法制备成具有超薄分离层的复合膜。德国GKSS研究中心用Polyactive共聚物膜材料成功制备了平方米规模的分离层厚度小于100nm的聚氧乙烯型嵌段共聚物复合膜[131]。此外,美国膜技术研究中心(MTR)利用富含EO基团的聚合物膜材料研制了PolarisTM复合膜,第二代PolarisTM复合膜的气体分离性能达到了国际领先的水准[132]。
(2)有机微孔聚合物膜材料
有机微孔聚合物是指具有较大比表面积且所含有的绝大多数孔属于微孔的聚合物的总称。根据孔结构形成机理的不同,有机微孔聚合物可大致分为共价有机骨架、共轭微孔聚合物、超交联聚合物、热重排(TR)聚合物和自聚微孔聚合物(PIMs)。其中,TR聚合物和PIMs为膜材料的CO2分离膜研究较为广泛。
通过热重排处理得到的TR聚合物的气体渗透系数通常比聚合物前驱体的气体渗透系数至少高两个数量级。但是,由于受到制备条件的限制(高温热处理),TR聚合物骨架上难以引入CO2亲和的功能基团,TR聚合物膜的分离性能普遍较低。
PIMs是依据自身的刚性骨架以及分子的非平面性质而获得微孔结构的。2005年由Mckeown课题组设计并合成的PIM-1是最具代表性的PIMs[133]。为了提高PIMs膜对CO2的溶解性以及调控聚合物的骨架结构,通过多种化学反应在PIM-1的氰基反应位点处引入了不同的极性基团,如伯氨基、酰胺基、脒基、羧基以及四唑基等。Guiver课题组利用“点击化学”的方法将PIM-1中的氰基转变为CO2亲和的四唑基团,所制膜具有良好的分离性能[134]。
(3)促进传递膜材料
促进传递膜是向分离膜中引入载体,通过待分离组分与载体之间发生可逆化学反应,促进某种物质通过膜的传递,能很好地改善膜的分离性能。促进传递膜可分为液膜、离子交换膜和固定载体膜。
促进传递的研究最早就起源于液膜。虽然液膜分离性能非常优异,但膜液是靠毛细管虹吸作用固定在液膜中,为了使膜液稳定,很难制得很薄的膜,所以渗透速率不是太高,且在压差作用下载体会随着膜液流失,膜性能不稳定,所以液膜一般寿命较短,不利于大规模应用[135]。
离子交换膜中由于载体仍然具有移动性,能主动选择与膜上游侧的CO2进行可逆反应,因此一般都具有较高的分离选择性。Quinn等[136]以聚苯乙烯三甲基氟化季铵盐制备的CO2分离膜,F-作为CO2载体可以主动与进料侧的CO2选择性地形成配合物,并在聚合物链间扩散传递,所以具有很高的分离选择性,CO2/CH4的分离因子达到1000。
固定载体膜是通过接枝或聚合的方式,将活性载体基团以共价键的形式连接在聚合物链上,所以载体非常稳定,但载体不能自由移动,是通过在所在位置的平衡摆动来实现促进传递的,其选择性比起含有可移动载体的液膜和离子交换膜略低。但是,固定载体膜其膜材料柔韧,成膜性好,结晶性低,因而更容易得到高渗透性能的膜,而且固定载体膜材料大多价廉易得,也易于进行物理或化学改性,因此广受青睐。固定载体膜中最常见的载体包括吡啶基、氨基和羧酸根等碱性基团。目前各种含氨基的材料是最常见以及研究最为深入的载体,如聚乙烯基胺(PVAm)、聚丙烯基胺、季戊四乙二胺、含叔氨基的聚酰胺等。乔志华等[93]选用小分子哌嗪(PIP)交联改性PVAm制备了PVAm-PIP/PSF膜。李诗纯等[94]以均苯三甲酰氯为有机相单体,以N,N'-双(3-氨丙基)甲胺和4,7,10-三氧-1,13-癸烷二胺的混合物为水相单体,在涂覆了改性硅橡胶中间层的聚砜支撑膜上进行界面聚合制备了聚酰胺复合膜。表12-14列举了一些代表性的用于二氧化碳分离的聚合物膜材料。
表12-14 用于二氧化碳分离的聚合物膜性能

(4)无机膜材料
常见分离CO2的无机膜有多孔陶瓷膜(Al2O3和TiO2)、多孔玻璃膜(SiO2)、多孔金属膜、碳分子筛膜(简称炭膜)及沸石分子筛膜等。多孔陶瓷膜中以Al2O3陶瓷膜最为常见,通过条件控制可制备出孔径为1~100nm的陶瓷膜,而多孔玻璃膜的孔径结构则通过调节玻璃组成和处理条件来控制。上述两种无机膜通常采用溶胶-凝胶方法或化学气相沉积(CVD)方法进行表面修饰,进一步减少膜表面孔尺寸,从而提高分离性能目前,用于CO2分离的无机膜材料研究较多的有炭膜、分子筛膜、MOF膜等。
炭膜是指由炭素材料构成的分离膜,是碳分子筛膜(CMSM)的简称,主要由含碳物质的有机聚合物作为前驱体热解而成,如聚酰亚胺(PI)、聚糠醇、酚醛树脂、聚丙烯腈、聚偏二氯乙烯、纤维素和聚醚砜酮等。炭膜具有近似气体分子尺寸的超细微孔结构,不仅对气体分离表现出极高的选择性和渗透能力,而且具有耐高温、耐高压、耐有机溶剂及耐酸碱腐蚀性等优点[138,139]。通过掺杂无机纳米粒子对炭膜进行修饰是一种简单有效的方法[140]。研究发现,将杂原子物质(如沸石、碳分子筛、聚乙烯醇、聚乙烯吡咯烷酮、金属及金属氧化物等)引入到炭膜前驱体中制备炭膜,可显著提高炭膜的气体分离性质[141]。在分离CO2中研究较多的炭膜材料及其性能如表12-15所示。
表12-15 用于分离CO2的炭膜前驱体及膜性能

分子筛膜是一类具有亚纳米孔的无机膜,自身具有抵御CO2塑化的化学抗性和高选择性。沸石膜通常是将硅酸盐多晶体薄片负载到多孔支撑体上,膜内部孔径的尺寸大小决定何种气体组分优先通过,具有较高的内表面和较大的孔容。分子筛孔壁通过TO4有序连接,骨架组成可变,具有负电性、离子交换性质和固体酸性质。分子筛膜主要分为MFI型、A型、NaY型和SAPO型四大类,在分离CO2中研究较多的分子筛材料及其性能如表12-16所示。
表12-16 用于分离CO2的分子筛膜材料

MOF是由金属离子和有机配体通过配位形成的具有晶格结构的材料,通过选择不同的金属、配体以及配位条件可合成具有不同孔径和孔结构的MOF,同时也为MOF的功能化改性提供了条件。研究表明,MOF具有较高的CO2吸附量,化学稳定性良好,同时部分MOF还具有优异的水热稳定性,孔径大小与一些气体分子的动力学直径相似。因此,MOF是一种应用前景较大的捕集CO2膜材料[155]。
ZIF(沸石咪唑酯材料)合成制备工艺简单、孔径较小,因此ZIF是研究较多的用来分离CO2的MOF膜材料。ZIF的金属中心原子如锌、钴和铜等与咪唑酯(Im)或是功能化咪唑酯上的氮原子链接形成中性框架结构同时具有由四元环或六元环的ZnN4、CoN4和CuN4形成的可调节的纳米尺寸孔道结构。ZIF化合物同分子筛的框架结构相似,比如分子筛中的T-O-T(T代表Si、Al、P)键被M-Im-M(M代表Zn、Cu、Co等)键取代。杨维慎等用热涂覆法在Al2O3表面制备一层纳米级超薄ZIF膜,利用纯气测试可知H2的渗透速率为3800GPU,H2/CO2分离因子可达300[156]。
目前已经制备出多种MOF膜用来研究在不同体系下的分离性能,在CO2/N2分离领域的膜材料有ZIF-69、HKUST-1[157]等;在CO2/CH4分离领域的膜材料有ZIF-8[158]、HKUST-1[157]、MOF-5[159]、MIL-53[160]、SIM-1[161]、ZIF-7[162]、ZIF-22[163]、ZIF-69、ZIF-95[164]、ZIF-90等;在CO2/H2分离领域,大多数的MOF材料都是H2优先透过膜,H2优先透过膜具有较高的分离因子和氢气渗透速率,而CO2选择性膜更具有较大的工业应用价值,但目前研究较少。大多数的MOF膜相比于其他无机膜表现出较高的CO2渗透通量和分离因子。几种典型的MOF膜材料的性能如表12-17所示。
表12-17 用于分离H2/CO2的MOF膜性能

无机膜目前仍处于实验室阶段,以下几个原因限制了无机膜的大规模应用:一是目前大多数无机膜的性能是在纯气条件下测试,缺乏真实环境下(如烟道气、天然气等)的膜性能数据;二是无机膜的重现性较差,难以重复制备;三是制备无机膜成本较高。因此,突破上述几个问题将有助于进一步推动无机膜在CO2分离领域的应用。
(5)混合基质膜材料
混合基质膜主要由无机或有机纳米材料作为分散相,聚合物材料作为连续相。常见的聚合物材料有聚酰亚胺、聚醚酰亚胺、聚醚砜、醋酸纤维素、磺化聚醚醚酮、聚醚共聚酰胺以及PVAm等。常见的纳米填料有二氧化硅、二氧化钛、碳分子筛、氧化石墨烯以及MOF等。
目前混合基质膜的研究依旧处于实验室阶段,表12-18列举了几种具有代表性的用于二氧化碳分离的混合基质膜材料。
表12-18 用于二氧化碳分离的混合基质膜材料

12.2.3.5 空气及天然气脱湿
通常人们采用分子筛脱除空气中的水,但存在能耗较大、压降较大等问题。膜技术以其高效、低能耗、压力损失小等优点引起了人们的关注。用于空气及天然气脱湿过程的膜主要有聚砜(PSF)膜、聚酰亚胺(PI)膜、聚二甲氧基硅烷(PDMS)膜以及醋酸纤维素(CA)膜[177]。目前美国的Permea公司和UOP公司、日本的UBE公司以及我国的长春应用化学研究所和大连化学物理研究所均已经开发出用于气体脱湿过程的分离膜及膜分离工艺,实现了空气及天然气脱湿的工业化应用。表12-19列出了两种用于空气脱湿的膜材料及脱湿性能。
表12-19 用于空气脱湿的膜材料及脱湿性能

美国Separex公司开发了醋酸纤维素螺旋式膜组件用于海上开发平台天然气脱水,其H2O/CH4分离因子为500,在7.8MPa、38℃下脱水后的天然气的水蒸气露点温度可达-48℃,水蒸气含量<10-4时,可以除去97%的水分,这对天然气的输送,避免管道腐蚀十分有利[180]。中国科学院大连化学物理研究所于1994年研制出中空纤维膜天然气脱水装置,并在长庆气田进行了天然气膜法脱水先导性试验,在此基础上开发出天然气膜法脱水工业试验装置,脱湿膜采用了复合膜结构,其致密层是聚砜材料,涂层是硅橡胶;膜组件的构造是中空纤维式。试验结果表明:在输气压力4.6MPa下,净化气水蒸气露点达到-13~-8℃,甲烷回收率不低于98%[181]。
12.2.3.6 VOCs回收
采用膜分离技术处理废气中的VOCs,不受浓度限制,且无二次污染,具有很高的经济效益和良好的社会效益。常用的处理废气中VOCs的膜分离工艺包括:蒸汽渗透(vapor permeation,VP)、气体膜分离(gas/vapor membrane separation,GMS/VMP)和膜接触器(membrane contactor)等。随着膜材料和膜技术的进一步发展,国外已有许多成功应用的范例。GKSS[182]、日东电工以及MTR公司[15]已经开发出多套用于VOCs回收的气体分离膜装置。表12-20归纳了针对不同化合物的VOCs回收应用的复合硅橡胶膜的有效选择性范围。
表12-20 用于VOCs回收应用的各种化合物的复合硅橡胶膜有效选择性范围

近年来,德国的GKSS公司、美国的MTR公司和日本的日东电工都成功地实现了采用膜技术回收废气中VOCs的工业化生产,其主要工业应用列于表12-21。
表12-21 采用膜技术回收废气中VOCs的工业应用

12.2.3.7 C4~C8同分异构体的分离
C4~C8同分异构体繁多,且各个同分异构体之间的性质相近,以C5的馏分分离为例,工业上通常采用萃取精馏或恒沸精馏分离,由膜法涉及的分离过程较少,其研究目前停留在实验室阶段。表12-22列出了一些用于C4~C8同分异构体分离的分子筛膜性能报道。
表12-22 用于C4~C8同分异构体分离的分子筛膜性能

12.2.3.8 烯烃/烷烃分离
膜法分离丙烯/丙烷,通常采用促进传递机制。使用具有优先溶解、透过丙烯的载体,达到分离丙烯/丙烷的目的。目前,固体膜以及液体膜均可用来分离丙烯/丙烷,但其分离效果仍有待提高,现阶段膜法分离丙烯/丙烷仍处于实验室阶段。表12-23列出了常用于烯烃/烷烃分离的膜材料渗透系数和分离因子。
表12-23 用于烯烃/烷烃分离的膜材料

12.2.4 气体膜分离原理
膜法气体分离的基本原理是根据混合气体中各个组分在压力的推动下透过膜的传递速率不同,从而达到分离目的。对不同结构的膜,气体通过膜的传递扩散方式不同,因而分离机理也各异。多孔膜是利用不同气体通过膜孔的速率差进行分离的,其分离性能与气体的种类、膜孔径等有关。其传递机理可分为分子流(即Knudsen扩散)、黏性流、表面扩散流、分子筛筛分、毛细管凝聚等。气体透过非多孔膜按传递机理可分为溶解-扩散、双吸附双迁移机理和促进传递机理等。图12-9列出分离膜按分离机理分类。

图12-9 分离膜按分离机理分类
12.2.4.1 分子流及黏性流
气体在多孔膜中的传递主要为Knudsen扩散流和黏性流,它们所占的比率由膜孔孔径(r)和气体分子平均自由程(λ)决定。分子平均自由程λ由式(12-1)计算,如果孔径很小或气体压力很低时,r/λ≪1,孔内分子流动受分子与孔壁之间碰撞作用支配,气体通过膜孔流量与其分子量M成反比,称分子流或Knudsen扩散,如图12-10所示。

图12-10 Knudsen扩散
(12-1)
根据Kundsen理论,气体透过单位面积流量q为
(12-2)
进一步可简化为
(12-3)
式中:
(12-4)
式中,η为气体的黏度;R为普适气体常数;T为温度;M为分子量;p为压力;p1、p2分别为进料侧和渗透侧的气体分压;L为膜孔的长度;r为孔径。
从式(12-2)可见,q与分子量平方根成反比,因此不同气体分离效果与它们分子量比值的平方根成反比(如表12-24)。显然只有对分子量相差大的气体有明显的透过速率差,这时分子流才有分离效果。从式(12-4)可知,渗透速率J与压力差无关。
表12-24 双组分Knudsen扩散的分离系数

如果膜孔径r与分子平均自由程比值r/λ≫1,孔内分子流动受分子之间碰撞作用支配,为黏性流,见图12-11。根据Hargen-Poiseuille定律,对黏性流动,气体透过单位面积流量q为

图12-11 黏性流
(12-5)
进一步可简化为
(12-6)
式中
(12-7)
可见,q取决于被分离气体黏度比。由于气体黏度一般差别不大,因此气体处于黏性流状态是没有分离性能的。
从式(12-7)可知,渗透速率J与膜两侧压力的平均值(p1+p2)/2成正比。
一般膜孔都有一定的孔径分布,气体平均自由程处于最小孔径和最大孔径之间,因此气体透过膜的渗透性是分子流和黏性流共同作用的结果。这时,气体透过大孔速率与黏度成反比,而透过小孔的速率与分子量平方根成反比。因此,气体透过整张膜的流量是黏性流和分子流共同贡献的结果(如图12-12)。例如,PM-10膜的公称平均孔径为1nm,按照式(12-4),透过速率应与压力无关,而事实上则表现出与压力的依存关系,这表明该膜具有孔径分布,存在着比1nm孔径更大的孔[186]。

图12-12 Kundsen扩散流与黏性流对渗透量的贡献(温度298K,氮气)
12.2.4.2 表面扩散流
如果分子吸附在孔壁上,那么浓度梯度使分子沿固体表面移动,产生表面扩散流,如图12-13。吸附气体沿孔壁的表面扩散可以用Fick第一定律来描述:

图12-13 表面扩散流
(12-8)
式中,qs是表面扩散流所产生的流量,Ds是表面扩散系数。室温下,Ds一般处在1×10-4~1×10-3cm2/s范围内,介于分子在气体介质和液体介质中的扩散系数之间。尽管吸附分子的扩散系数小于非吸附气体,表面扩散流对总的气体流量具有不可忽略的贡献[187]。
通常沸点低或临界温度高的气体易被孔壁吸附,表面扩散显著,见图12-14[187];而且操作温度越低,孔径越小,表面扩散贡献越明显[188]。例如对平均孔径4nm的玻璃膜,如用CO2、H2纯气测量分离系数,测试温度为583K时,测得H2/CO2分离系数为4.42;但当测试温度下降到273K时,H2/CO2分离系数下降到2.54,表明当温度下降时,CO2在膜孔上产生表面扩散[189]。

图12-14 气体临界温度对表面扩散的影响
在表面扩散流存在的情况下,气体流过膜孔流量由气相流(一般为Knudsen扩散)和表面扩散流叠加,见图12-14。对于非凝聚性气体,P基本恒定,对于凝聚性气体,随着气体临界温度的增大,表面扩散流对总的气体流量的贡献加大,如图12-14。
图12-15是温度对表面扩散的影响,在图中,气体流过膜孔流量先是随着温度升高而减少,达到最小值后,又随温度升高而增大。这是因为低温下表面扩散流动很大,占主导因素,而表面扩散流是随着温度升高而减少的。当达到一定温度后,表面扩散流可忽略,这时Knudsen扩散占主导因素,流量又随温度升高而增大。因此,气体流过膜孔流量随温度变化曲线表现出最小值[189]。

图12-15 气体在不同温度下透过Vycor玻璃微孔膜的渗透速率[189]
12.2.4.3 毛细管凝聚机理
对孔径比分子筛孔大1nm左右的膜孔,凝聚性气体将在孔内产生毛细管凝聚,可以阻碍其他非凝聚性气体分子通过,从而产生分离作用,如图12-16所示[190]。

图12-16 毛细管凝聚
12.2.4.4 分子筛分机理
如果膜孔径介于不同分子动力学直径之间,那么直径小的分子可以通过膜孔,而直径大的分子被挡住,实现气体分离,即具有筛分效果,如图12-17。一般具有分子筛分作用的膜孔较小且分布较均匀,利用分子筛分原理可以得到很好的分离效果。

图12-17 分子筛分
由于分子筛分是基于气体分子大小(见表12-25)而实现分离的,以分子筛分为机理的多孔膜在保持较好的气体渗透通量的同时表现出较高的选择性,是一个较为理想的分离过程。无机膜分离过程多遵循分子筛分机理,如文献报道的硅膜、炭膜以及分子筛膜等无机多孔膜[191-195]都表现出了超高的气体渗透分离性能。另外,一种新型的膜材料——自聚微孔聚合物材料也展现出了以分子筛分为机理进行气体分离的潜力[196]。
表12-25 气体分子动力学直径

综上所述,Knudsen扩散分离过程的选择性较低;常见分离气体(O2、N2、H2和CH4等)的沸点高、与膜材料的相互作用较差,通常不容易发生表面扩散流或毛细管凝聚现象;分子筛分机理可以有效地将不同尺寸的气体分子分离,具有很高的分离性能,是气体分离膜研究的一个重点。
12.2.4.5 溶解-扩散机理
气体渗透通过非多孔膜(致密膜)的机理与多孔膜存在差异。其中,溶解-扩散机理是公认的、应用最多的有机致密膜气体渗透机理,如图12-18所示。

图12-18 气体渗透通过膜的溶解-扩散机理
1—气体分子;2—浓度梯度(非稳态);3—浓度梯度(稳态)
溶解-扩散机理认为气体渗透通过致密膜过程分三步[197]:①气体分子在膜上游表面吸附溶解;②气体分子在膜内扩散;③气体分子在膜下游表面解吸。通常认为气体在膜上游表面的吸附溶解和下游表面的解吸过程很快,而气体在膜内的扩散过程相对较慢,气体在膜内的渗透是速率控制步骤。
刚开始时,溶解-扩散过程处于非稳态,气体在膜内浓度呈非线性分布,当达到稳态时,气体在膜内浓度线性分布,气体在膜内的扩散流量q为
(12-9)
式中,p1为膜高压侧压力;p2为膜低压渗透侧压力;A为膜有效渗透面积;δ为膜的厚度;P为渗透系数:
(12-10)
式(12-10)中渗透系数P等于扩散系数D和溶解度系数S的乘积,表明气体通过非多孔膜渗透是根据溶解-扩散机制进行的。
气体A和B的理想分离系数可以表达为:
(12-11)
式中,DA/DB为扩散选择性;SA/SB为溶解选择性。理想分离系数反映了膜材料本身对不同气体渗透能力的差异。
分离因子反映膜对不同气体(A/B)分离能力的大小。根据下式定义:
(12-12)
式中,x、y分别为原料气、渗透气浓度。
分离因子既可以通过实测原料气和渗透气中组成计算,也可以根据理论进行估算。
假定混合气独立透过膜,且在膜两侧为全混流,则
(12-13)
由于原料侧混合气的浓度比等于分压比,因此,
(12-14)
可见,分离因子不仅与膜材料性能(PA/PB)有关,而且还随操作条件改变。如果渗透侧压力很低,与原料侧相比可忽略不计
(12-15)
即为式(12-11)的理想分离系数,它反映了膜材料对不同气体的分离能力。通常,分离因子比理想分离系数低。
(1)影响溶解度的主要因素
①温度的影响 一般而言,气体在膜中的溶解度S与温度T呈Arrhenius型关系:
(12-16)
式中,S0为溶质在极稀情况下的溶解度;ΔHs为溶解热,是摩尔冷凝热(ΔHC)和摩尔混合热(ΔHM)之和。对于非凝聚性气体(H2、O2等),ΔHs主要取决于摩尔混合热ΔHM,为正值,溶解度随温度增加而增大;而对于可凝性蒸气如碳氢化物,ΔHs主要取决于冷凝热ΔHC,为负值,故其溶解度随温度的上升而减小。
②气体的性质 影响溶解度的主要因素是冷凝的难易程度,即临界温度、正常沸点和Lennard-Jones常数。图12-19列出了典型的玻璃态聚合物(聚砜)、橡胶态聚合物(硅橡胶)以及理想液体中气体的溶解度与其临界温度的关系。

图12-19 气体在玻璃态聚合物(聚砜)、橡胶态聚合物(硅橡胶)以及理想液体的溶解度和其临界温度的关系[198]
③膜材料性质 表12-26列出了一些聚合物对CO2/CH4的扩散与溶解选择性,不凝聚性气体在膜中溶解度取决于亨利系数或Flory-Huggins分子间相互作用引力参数。对玻璃态聚合物,由于各种不凝聚性气体与无定形高分子膜间的相互作用参数差异较小,因此溶解选择性小于扩散选择性。
表12-26 一些聚合物对CO2/CH4的扩散与溶解选择性[198]

(2)影响扩散系数的主要因素
橡胶态聚合物和玻璃态聚合物均可用于气体分离,橡胶态聚合物在玻璃化转变温度以上使用,链段具有较强的运动能力。而玻璃态聚合物在低于其玻璃化转变温度下使用,聚合物链段的运动处于被冻结的状态,无法实现构象的转变,分子链段热运动过程形成的链段间距是气体扩散的主要通道[199]。
Vrentas和Duda[200,201]提出了气体在玻璃态聚合物中扩散的自由体积理论,认为在部分聚合物链段间存在孔洞即自由体积。如图12-20所示,气体分子通过由一个自由体积单元跳跃至下一个自由体积单元完成气体扩散过程。气体分子要实现这一过程需要满足两个条件:相邻位置有足够大的自由体积单元;气体分子有足够的能量克服跳跃阻力。理论指出气体扩散过程受温度影响,温度升高,链段的灵活性加强,并且分子热运动加剧,气体扩散过程增强。

图12-20 气体通过分子链段热运动形成的链段空穴扩散跃迁
数字1~5表示聚合物的分子链段。A、B、C表示溶解于膜内正在进行扩散的气体分子,在进行纯气渗透实验时它们是同一种气体分子,而在进行分离实验时它们则可能为不同的气体分子。这些分子的位置随着链段运动而在膜内不断发生变迁
扩散系数通常是由扩散分子大小、聚合物的自由体积决定的。图12-21列出了不同气体在水、天然橡胶和聚氯乙烯中的扩散系数(D)与摩尔体积的关系,气体分子尺寸越大,扩散性能越差。

图12-21 不同气体在水、天然橡胶和聚氯乙烯中的扩散系数(D)与摩尔体积的关系[198]
通常扩散系数与自由体积的关系可以表示为:
(12-17)
在式(12-17)中,AD是指前因子,与气体分子大小及温度相关;B是与渗透气体分子大小成比例的参数;FFV是聚合物的自由体积分数。
自由体积与构成聚合物结构单元有关,可由基团贡献法估算[202,203]。根据Paul等提出的基团贡献法,可以预测某一材料对各种气体渗透性的本征值[203],计算公式如下:
(12-18)
(12-19)
(12-20)
式中,V代表聚合物的实际体积,可以用1/ρ(ρ为聚合物的密度)表示;V0代表聚合物链占据的体积;Vw代表基团的范德华体积;k代表基团个数;A、B的数值可以根据表12-27选取。
表12-27 由Bondi方法修订数据库后估算出的A和B的数值

①在35℃,10个大气压条件下;
②在35℃,2个大气压条件下。
从许多文献中的P-(1/FFV)关系图看,上述公式尚不能很好地描述P与FFV的关系,存在一些问题,例如:渗透系数的影响因素不仅仅只有FFV;文献中的(Vw)k可能会有偏差;Bondi基团贡献法中给出的修正因子1.3是比较粗略的。
为了更准确地预测P值,Paul课题组对式(12-19)做了修正,V0由式(12-21)计算。
(12-21)
式中,γnk是经验值,可由基团贡献法[203]得到。
(3)气体渗透性与选择性关系——Robeson上限(Robeson upper bound)
通常聚合物膜的渗透系数和分离系数是一对矛盾的性能,即对不同气体间选择性的增加会同时降低气体的渗透系数,反之亦然。Robeson在1991年提出了聚合物膜对气体的透气性和选择性存在的关系式,即Robeson上限[22],如图12-22所示,其经验公式为:

图12-22 气体渗透性与选择性关系——Robeson上限
(12-22)
式中,PA为两气体组分中渗透快的气体A的渗透系数;αA/B是两组分的分离系数;k和n为相关的参数。n与气体分子的大小相关,-1/n与dA-dB成线性关系(其中dA和dB为气体A与B的分子动力学直径),k是与气体的冷凝能力和聚合物的结构相关的参数。
随着气体膜分离的发展和新材料的涌现,在2008年Robeson对其上限进行了修改[204]。表12-28给出了不同分离体系的k和n的数值。新的上限对与聚合物结构有关联的k进行了大的改动,而与气体分子大小相关联的参数n没有大的变化。
表12-28 不同气体分离体系Robeson上限的截距值k和斜率[204]

1999年,Freeman[205]对Robeson上限经验公式进行了理论推导,得到如下公式:
(12-23)
此公式与Robeson上限式(12-22)表达方式不同,实质上是一致的。
式中,
(12-24)
(12-25)
对于λA/B,其仅由气体分子的大小决定;而在βA/B的表达式中,仅有一个可变参数f,它是温度的函数,a=0.64,b=9.2(橡胶态)或11.5(玻璃态),当气体分子与聚合物之间无强相互作用时,溶解度系数仅与气体分子的冷凝性有关。
在式(12-23)的推导过程中,认为在致密膜中的传递遵循溶解-扩散机理,扩散是控速步骤。另外,要求分子链间距接近或小于动力学直径,气体分子在聚合物链中的扩散需要克服一定的势垒,可以看作是一个活化过程。当气体分子为He、H2、N2、O2、CH4以及CO2等轻质分子时,聚合物中的可渗透空穴尺寸可以用这些气体分子的动力学直径来表示。
刚性玻璃态聚合物的气体渗透性质决定了Robeson上限的位置,Robeson上限的斜率值是刚性玻璃态聚合物分子筛分效应的自然结果。由式(12-25),对于给定的气体对,λA/B不变,而聚合物链的刚性的增大(分子链间距增大)或者溶解选择性的提高能够增大βA/B。影响气体渗透性能的聚合物结构因素包括聚合物的玻璃化转变温度(Tg)、结晶度、极性及其与气体分子的相互作用等,这些因素都可由对聚合物的化学结构的设计来实现。
Haiqing Lin等[206]引入一个可调参数,修正了自由体积理论来解释聚合物膜中CO2/CH4的分离性能,可以满意地预测各种纯气体分离上限,且上界的斜率和截距与Robeson上限经验方程和Freeman活化能理论的值一致。引入塑化对自由体积影响,该模型还可以预测CO2/CH4混合气体在CO2和非甲烷烃类高分压存在下的分离上限;应用到醋酸纤维素膜(CA)材料,可以解释在高CO2分压原料气下CO2/CH4的分离特性。
12.2.4.6 双吸附-双迁移机理
(1)纯气在聚合物膜上渗透
根据溶解-扩散机制,气体渗透速率与压力无关,通常橡胶态聚合物都符合这一规律。但对玻璃态聚合物,气体渗透速率往往表现出与压力有关的现象。对于一些与聚合物有很强相互作用的渗透物(如有机蒸气),溶解度系数与浓度有关,压力升高溶解度系数增大,如图12-23(a)所示呈现高度的非线性。特别是在高压下,这种非理想吸附行为通常使用Flory-Huggins模型方程(12-26)进行描述[207,208]:
(12-26)
式中,psat为气体在实验温度下的饱和蒸气压;χ为Flory-Huggins相互作用参数;ϕg为气体溶解在聚合物中的体积分数。
另外,对于有些聚合物,压力升高会使得溶解度系数减小然后趋于平衡,如图12-23(b)。Koros等[209]对PET-CO2体系测定吸附等温线(见图12-24),当温度低于PET玻璃化转变温度(85℃)时,CO2在PET膜内溶解度随压力呈现出非线性变化,偏离亨利定律,表明存在双吸附现象。

图12-23 非理想体系的等温吸附线

图12-24 CO2在PET中吸附等温线
Meares首先提出玻璃态高分子膜中由于分子链运动冻结,存在着微腔不均匀结构[210,211]。Barrer、Vieth等提出膜内存在气体分子溶解(亨利吸附)和微腔壁上吸附(朗格缪尔吸附)两种机制,如图12-25(a)所示;基于这两种吸附机理,膜内气体浓度如图12-25(b)所示,表达为亨利溶解CD和朗格缪尔吸附CH的叠加[212,213]。

图12-25 气体分子在玻璃态致密膜中的双吸附机理
(12-27)
式中,kD为亨利系数;b为亲和参数;C'H为饱和参数。其中,kD和b与温度有关,随温度的升高而减少。
研究结果表明,式(12-27)可以很好地描述简单气体在玻璃态聚合物上的吸附现象。
显然,当bp≫1或bp≪1时,浓度随压力p呈线性。实际上,从式(12-27)可得
(12-28a)
(12-28b)
从等温吸附曲线高压处的斜率可求出kD,再改变式(12-27)形式,以1/(C-kDp)与1/p作图,由直线截距和斜率分别可求出C'H和b值。表12-29~表12-31列出一些聚合物双吸附模型参数。
表12-29 CO2在玻璃态聚合物中双吸附模型参数(35℃)[214]

TMPC:四甲基双酚A聚碳酸酯;6FDA-BAPHF和6FDA-pp'ODA:聚酰亚胺。
表12-30 6FDA-1,5-NDA聚酰亚胺双吸附模型参数[215]

①由压力计算的数值;
②由逸度计算的数值。
表12-31 部分聚合物双吸附模型参数[216]

除实验测得双吸附模型参数外,模型参数还可以采用Lennard-Jones势参数、Flory-Huggins理论中聚合物与气体相互作用参数或基团贡献法进行估算。
b与气体分子的Lennard-Jones势参数(ε/k)有关,可由式(12-29)表示[217]:
(12-29)
式中,θ是被气体分子占据的自由体积的表面积分数;I'是系统常数,依赖于气体-聚合物体系所选择的参考状态。
kD可由气体分子的Lennard-Jones势参数进行估算。
(12-30)
式中,χ是Flory-Huggins理论中聚合物与气体相互作用参数,可以由下式估算,V是气体在聚合物中的摩尔体积。
(12-31)
这里,δp和δg分别为聚合物与气体的溶解度参数。
饱和参数C'H与聚合物在玻璃态时的过剩体积有关,即C'H与任意温度下的玻璃态比体积(Vg)和假想的液体体积的比体积(Vl)的差(Vg-Vl)成比例:
(12-32)
如图12-26,当温度降低至玻璃化转变温度以下时,由于聚合物链的松弛不充分,一部分自由体积以微腔形式冻结在聚合物链中,这部分自由体积处于热力学不平衡状态,称为过剩自由体积,即(Vg-Vl)。过剩自由体积(Vg-Vl)用热膨胀系数差(al-ag)表示,即

图12-26 非晶型聚合物中自由体积分数和温度的关系
(12-33)
代入式(12-32),得
(12-34)
双吸附-双迁移模型中各参数与气体渗透性、气体扩散率和气体溶解度等多种因素有关,Kanehashi等[218]基于对文献中约250种玻璃态聚合物进行统计分析,试图建立模型参数与聚合物玻璃化转变温度、自由体积分数和气体溶解度等关系,对同系列玻璃态聚合物模型参数相关性较好;但很难定量地比较不同系列玻璃态聚合物参数值。Saberi等[214]使用基团贡献法预测双吸附(DMS)模型参数,先把82种不同聚合物拆解成37个基团单元,建立了基团双吸附参数数据库,然后采用基团双吸附参数预测了数据库外其他6种不同聚合物CO2双吸附模型参数值,与测试值一致。
Paul和Koros[219]认为Langmuir吸附分子只有部分可以迁移,其迁移率与亨利溶解分子一样,可得到:
(12-35)
式中,K=C'Hb/kD。
可以得到透过系数:
(12-36)
式中,F=DH/DD,表示固定化程度,一般F<1;与bp理论曲线如图12-27所示。对不同F值,
均随压力增加而减少。玻璃态聚合物通常都有这种趋势[218,220-222]。

图12-27 双吸附-部分迁移模型的渗透系数与bp理论曲线
用对(1+bp)-1作图,从图上直线的截距和斜率,再结合由吸附实验得到的kD、b、C'H,可算出DH、DD。
Wang等用N2、O2、CH4和CO2气体测定6FDA-1,5-NDA聚酰亚胺膜渗透系数,根据式(12-36)计算了双吸附-双迁移模型参数,列于表12-32。
表12-32 6FDA-1,5-NDA聚合物双吸附-部分迁移模型参数[215]

(2)混合气在聚合物膜上渗透
混合气在玻璃态聚合物中渗透时,在总压一定条件下,某一组分的渗透往往受其他组分存在的影响,有时变大,有时变小。
M.P.McCandless研究CO-H2混合气在Kapton聚酰亚胺膜上渗透时发现,不但混合气透过膜的总透量仅为按相同分压下由纯组分算得的透量的70%~80%,而且表观分离系数也比按纯组分计算的值小,压力越高,这种差别越大。这表明混合气中组分之间相互作用影响混合气渗透过程。
考虑到玻璃态聚合物存在着Langmuir吸附,Koros等借助于气体分子在催化剂活性中心和分子筛吸附中心发生竞争吸附概念,将纯气公式扩散到混合气渗透。双组分混合气,得到[223,224]:
(12-37)
(12-38)
并得到各组分的稳态渗透系数
(12-39)
(12-40)
该模型揭示出混合气组分A和B互为竞争组分,即对Langmuir吸附中心发生竞争,从而影响渗透行为。用式(12-39)、式(12-40)可以较好地预测混合气的渗透系数。
由于混合气在膜中相互竞争吸附效应,对双组分混合气渗透,在总压一定下,“慢气”(指渗透速率小的气体)使“快气”(指渗透速率大的气体)变慢,“快气”使“慢气”变快。
由于双吸附-双迁移模型忽略渗透组分之间的平衡和动力学相互作用,对多组分渗透过程预测误差还是比较大。Ghoreyshi[225]等提出基于Maxwell-Stefan传质模型,考虑了渗透组分在吸附和扩散方面产生的耦合效应。用双吸附模型来描述吸附平衡,基于二元扩散系数的Maxwell-Stefan传质模型描述多组分扩散行为,预测结果对CH4/CO2和C3H6/C3H8分离实验数据吻合较好,而传统的双吸附-双迁移模型的结果较差。由于气体分离膜通常采用基于扩散选择性的玻璃态聚合物膜,因此,考虑传质动力学耦合效应尤其重要。该模型的一个主要优点是它可采用纯组分在膜中的吸附和渗透数据来预测真实的混合气选择性。
12.2.4.7 复合膜传质机理
实际应用的气体分离膜绝大多数是非对称膜,因分离皮层很薄,当皮层有缺陷时,常在膜外层包覆一层高渗透系数的材料(如硅橡胶等),硅橡胶的作用是填补表面孔和缺陷,这时,复合膜的阻力主要集中于底膜。传质采用阻力模型分析,如图12-28所示[226,227]。溶解的气体依次流经涂层、致密皮层、充填涂层聚合物的致密层有孔部分和支撑层扩散。

图12-28 复合膜结构示意图及模拟电路模型
将渗透过程类比为电路,将气体流经膜的过程与电流类比,可得描述流量的渗透方程。各层阻力分别为:
(12-41)
式中,A为气体渗透的有效膜面积;P为气体在膜内的渗透系数;L为气体渗透通过的膜厚度。
整个渗透过程的总阻力为:
(12-42)
式中,i=1,2,3,4;1表示涂层,2表示致密层,3表示充满涂层聚合物的致密层针孔,4表示支撑层。
非对称膜的总渗透速率J可表示为:
(12-43)
式中,Rt为气体渗透通过膜的总阻力;A为气体渗透的有效膜面积。
12.2.4.8 混合基质膜气体渗透机理
混合基质膜中引入无机粒子,其气体渗透性能兼具有机膜和无机膜气体渗透特性。假如无机粒子均匀分散在聚合物基质中,无相界面缺陷、无粒子团聚等问题,气体渗透通过分散相和连续相而实现,其渗透性能可采用Maxwell模型计算预测[228,229]:
(12-44)
式中 Peff——混合基质膜有效渗透系数;
Pc——连续相的气体渗透系数;
Pd——分散相的气体渗透系数;
ϕd——分散相的体积分数。
当Pd≫Pc时,Maxwell方程可以简化为式(12-45):
(12-45)
Maxwell方程假定气体扩散通过粒子边界层时不受相邻粒子干扰,适用于分散相含量较低的混合基质膜(如<20%)。Bruggeman等考虑了分散粒子间相互作用对气体渗透影响,对Maxwell模型进行了修正[230]:
(12-46)
当Pd≫Pc时,公式(12-46)可简化为公式(12-47):
(12-47)
12.2.4.9 促进传递机理
为实现气体分离膜同时具有高透过性和高选择性的目标,研究者们尝试在膜内引入可以促进某种物质在膜内传递过程的载体,从而改善膜的分离性能,这就是促进传递膜[231]。促进传递膜内的载体能够与待分离气体中的某种透过组分发生特异性的可逆反应形成中间化合物,并在膜内从高化学势侧向低化学势侧扩散。中间化合物在低化学势侧分解为原透过组分及载体,载体在膜内可继续发挥促进传递作用。因而该类型气体分离膜可以具有很高的选择性和渗透性,从而突破Robeson上限的限制[22,204]。根据载体在膜中的移动性,促进传递气体分离膜可以分为移动载体膜和固定载体膜两大类。
促进传递膜最早起源于移动载体膜,主要指液膜,在液膜内活性载体是流动的。液膜一般可以分成两类:乳化液膜和支撑液膜。液膜的易挥发性和载体的易流失性导致了膜难以长期保持高活性,大大缩短了其使用寿命,限制了该类型膜的应用。为克服上述缺陷,研究者们后续又开发出固定载体膜这类将活性载体固定化的促进传递膜。在固定载体膜内,载体通过接枝或共聚等手段,以共价键的形式固定在膜材料分子骨架上,使载体能够在一定的范围内振动而不能自由扩散。这种方法实现了载体的固载化,比较彻底地解决了载体流失的问题。
一般认为,无论是在移动载体膜还是在固定载体膜中,促进传递作用与溶解扩散作用并存。在液膜等移动载体膜中,未反应的载体和特定组分,以及载体与特定组分反应产生的配合物均可以在膜内扩散传递[232-234]。而在固定载体膜中,未参加反应的组分以扩散的方式通过膜,参加反应的特定组分以某种“跳跃”方式在膜内载体之间传递,特定组分与载体形成的配合物不能自由移动[235,236]。此外,在促进传递膜内传递机理的研究中,一般使用促进因子F(facilitated factor)来表征载体的促进作用[237],其定义如下:
(12-48)
描述被促进传递组分与载体之间可逆反应的最简单反应式为[237,238]:
(12-49)
式中,A、X和AX分别为被促进传递组分、载体和组分-载体配合物;kf和kr分别为正反应和逆反应的速率常数。
对于移动载体膜,在一维稳态下,组分A的总通量可表示为:
(12-50)
式中,JA为组分A的总通量;JSD为没有参加反应的组分A的通量;DA和DAX分别为未反应组分A和组分-载体配合物AX在膜内扩散系数;CA和CAX分别为膜内未反应组分A和组分-载体配合物AX的浓度;z为膜进料侧表面开始的膜内传递距离。
为了定量表征膜的性能,需求解如下的反应扩散方程:
(12-51)
(12-52)
(12-53)
式中,R'A、R'X和R'AX分别为被促进传递组分、载体和组分-载体配合物的反应速率; DX为载体X在膜内扩散系数;CX为膜内载体X的浓度。
边界条件:
式中,CA,0为组分A在进料侧气相与膜界面处膜中溶解的气体浓度;CA,l为组分A在渗透侧气相与膜界面处膜中溶解的气体浓度;CT为膜内载体总浓度。
式(12-51)~式(12-53)为二阶微分方程组,研究者们[232-234]通过不同方式对该方程组进行求解,得到移动载体膜中气体通量或促进因子的表达式。
Cussler认为,当传递过程达到稳态时,膜内未反应组分A以及组分A和载体X所生成配合物AX的浓度都呈线性分布[234,239]。此时,式(12-50)可推导为:
(12-54)
式中,CAX,0为配合物AC在进料侧气相与膜界面处膜中浓度;CAX,l为配合物AX在渗透侧气相与膜界面处膜中浓度。
在进料侧膜表面可逆反应的平衡常数K可表示为:
(12-55)
式中,CX,0为未反应载体C在进料侧气相与膜界面处膜中浓度。
膜进料侧载体总浓度CT等于未反应载体浓度CX,0和已反应载体浓度CAX,0之和,即:
(12-56)
当渗透侧浓度CA,l可忽略时,通过式(12-54)~式(12-56)得到组分A的总通量为:
(12-57)
Noble[240]通过另外一种方法计算出F的表达式。在计算过程中,Noble定义了以下的无量纲参数:
(12-58)
(12-59)
(12-60)
ε为Damkoler数的倒数,反映了逆反应速率与扩散速率之比,ε越大表明反应越接近平衡即过程为反应控制,ε越小则表明反应为扩散控制;ω为迁移因子(载体X与组分A迁移能力之比);K'为无量纲反应平衡常数。
若膜内载体X大量过剩,其浓度可视为常数,则反应可按照拟一级反应处理,得到如下解析解:
(12-61)
式中λ为:
(12-62)
当ε很小(ε≪1)时,膜内传递过程为扩散控制,,促进因子可表示为:
(12-63)
实际上,当未反应组分A的通量JSD可以表示为(忽略渗透侧浓度)时,将式(12-63)代入式(12-50),可以得到与式(12-57)相同的形式。
Noble进一步考察了外扩散阻力的影响[241],得到了如下的解析解:
(12-64)
式中,Sh0和Shl分为进料侧表面和渗透侧表面的Sherwood数。当外扩散阻力可忽略时,Sh0→∞且Shl→∞,式(12-64)可变为式(12-61)。
然而,目前对固定载体膜促进传递机理的研究还不充分,仅有少数研究者深入描述组分在膜内促进传递机理。
Cussler等[242]认为载体只能在平衡位置上振动,气体分子必须通过载体的摆动才能从进料侧传递到渗透侧(如图12-29所示),不参加反应的气体分子很少,自由扩散可以忽略。因此,只有当载体之间距离小于载体摆动的距离时才有气体分子的传递。他们据此预测载体浓度存在一个临界值,低于此值不发生促进传递现象。然而,Tsuchida等[243]报道,当载体浓度很低时也观测到了促进传递现象。

图12-29 Cussler摆动模型示意图[244]
Noble[235,236]认为气体分子能够沿着高分子链在配合物分子之间迁移。如图12-30所示,组分A的一部分分子沿着浓度梯度不断向膜渗透侧传递,同时,另一部分分子与载体X发生可逆反应,形成载体配合物AX,这部分分子在不同配合物Xj-1、Xj和Xj+1之间迁移,向渗透侧进行促进传递。两种传递方式之间也发生质量交换,即载体配合物分解产生的组分A的分子可能转为以溶解-扩散方式进行传递,而进行溶解-扩散方式传递的A组分分子也可能与载体结合形成载体配合物,转为以促进传递方式进行传递。

图12-30 Noble模型中溶质与相邻三个载体间的相互作用示意图[235]
Noble[235]通过位置j处配合物AXj的质量守恒,得到了稳态下的反应-扩散微分方程,发现此方程和式(12-61)在形式上是相同的。Noble利用式(12-61),对O2在固定载体膜中的渗透系数进行了分析,发现预测值与实验值相符较好。Noble的研究结果表明,对于移动载体膜和固定载体膜,尽管在微观上膜内传递机理可能不同,但描述两者促进传递机理的模型在数学上是等价的。
Noble[235,236]进一步指出,尽管描述移动载体膜和固定载体膜的反应-扩散微分方程在数学上是等价的,但方程中配合物扩散系数(DAX)的物理意义是不同的,固定载体膜中的扩散系数是有效扩散系数,与载体之间的相互作用有关。Noble[245]通过串联阻力模型,求出了有效扩散系数的表达式。
基于酸性气体CO2,王志等[246-252]开发了多种氨基促进传递膜,并对膜内的促进传递机理进行了深入研究[253-257],建立了可定量描述促进传递膜气体渗透速率3种不同反应形式的数学模型[式(12-65)~式(12-67)][253],同时首次将Henry系数表达式(12-68)[258]引入模型中,对文献中已报道的促进传递液膜和促进传递固定载体膜实验数据进行拟合分析后发现:对于常见的含伯氨基或仲氨基的支撑液膜,采用由无水参与的反应式推导的表达式[式(12-66)],可以得到与实验值接近的扩散系数和可逆反应平衡常数;对于含伯氨基或仲氨基的固定载体膜,膜中一部分氨基可能同时发生了无水参与的氨基与CO2反应和有水参与的氨基与CO2反应,因此使用由式(12-65)表达式描述CO2渗透速率比较合适。
[由简单反应式(12-49)推导获得] (12-65)
(由无水参与的反应式推导获得) (12-66)
(由有水参与的反应式推导获得) (12-67)
(当温度为298K时, HA=3.04×103MPa·cm3/mol)(12-68)
然而,促进传递机理十分复杂,目前人们对该传递机理仅有初步认识,多数已提出的数学模型均难以通过实验数据获得验证。因此,气体分离膜内的深层次促进传递机理仍待人们在后续研究过程中进一步探索与完善。