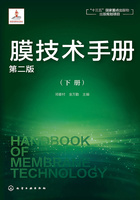
12.1 引言
12.1.1 气体膜分离特点
气体膜分离是气体分离方法的一种。目前可用于气体分离的方法主要有:深冷分离、吸附分离、溶剂吸收分离、膜分离等。
深冷法是把气体经压缩、冷凝后,利用气体的沸点差进行蒸馏而使不同气体分开的,其特点是产品气纯度高;但由于压缩、冷凝能耗高,深冷分离更适用于大规模气体分离过程。
吸附分离法基本原理是利用吸附剂对不同气体在吸附量、吸附速率等方面的差异进行分离的。根据对吸附气体的解吸方式不同,吸附分离又分为变温吸附(TSA)和变压吸附(PSA)。其中变压吸附根据吸附剂的吸附容量随压力而变化的特性,在加压时完成气体的吸附分离,在降压条件下完成吸附剂的再生,从而实现气体分离及吸附剂循环使用。变压吸附-解吸循环周期短,装置可以小型化,而且操作能耗也不高,适用分离对象广(如O2、N2、H2、CO2、CO、水蒸气等),近年来发展迅速,已成为一种强有力的分离方法。
溶剂吸收法是利用气体混合物中各组分在液体吸收剂中溶解度的不同,将其中目标组分分离,可分为物理吸收法和化学吸收法。如CO2吸收分离,物理吸收法通过交替改变CO2和吸收剂的操作压力或操作温度实现CO2吸收和解吸,从而达到分离CO2的目的。化学吸收法利用CO2与吸收剂的化学反应将CO2从混合气中分离出来。物理吸收法在吸收和解吸过程中不发生化学反应,消耗的能量比化学吸收法少。化学吸收法具有选择性高、应用广泛等优势,缺点是再生时耗能较大,同时胺吸收剂会腐蚀设备。
膜分离是根据膜对不同气体的渗透速率差而对气体进行分离的。气体膜渗透是气体与特殊制造膜相接触,在膜两侧压力差驱动下,气体分子透过膜的现象。对于不同气体组成的混合气体,由于不同气体分子透过膜的速率不同,渗透速率快的气体在渗透侧富集,而渗透速率慢的气体则在原料侧富集。膜分离的主要特点是能耗低、设备简单和系统紧凑、操作方便、运行可靠性高、成本和操作费用均较低等。表12-1比较了各种气体分离方法的原理、技术成熟程度、规模、气体种类、浓度、形态、能耗、用途等特点。
表12-1 各种气体分离方法比较[1-3]

12.1.2 气体膜分离现状
12.1.2.1 主要气体膜分离过程
早在1831年J.K.Mitchell用膜进行氢气和二氧化碳混合气渗透实验,发现了不同种类气体分子透过膜的速率不同的现象,首次揭示了用膜实现气体分离的可能性[4]。1866年,T.Graham研究了橡胶膜对气体的渗透性能,发现用膜可以将空气中氧气富集,并提出了溶解-扩散机理[5],即气体分子首先在膜表面溶解,使膜两侧表面产生浓度梯度,在此浓度梯度驱动下,气体分子在膜内扩散,最后在膜另一侧表面解析。同时他还发现如增加膜的厚度,膜对气体的渗透速率减少,但对气体选择性保持不变。
虽然在一百多年前科学家就已经发现利用膜实现气体分离的可能性,但由于当时没有找到合适的膜结构,膜渗透速率很低,膜分离难以与传统的分离技术如深冷、吸收等竞争,故未能引起产业界的足够重视。
气体膜分离应用研究始于20世纪50年代初,1950年S.Weller和W.A.Steiner用25μm厚乙基纤维素平板膜进行空气分离,得到氧浓度为32%~36%的富氧空气[6]。稍后1954年D.W.Brubaker和K.Kammermeyer发现硅橡胶膜对气体的渗透速率比乙基纤维素高出约500倍,具有优越的渗透性[7]。1965年S.A.Stern等用厚25μm的聚四氟乙烯膜,采用三级膜分离从天然气中浓缩氦气[8]。同年DuPont公司发表了从混合气中分离氢气、氦气的专利。
20世纪60年代初,Loeb和Sourirajan用相转化法制造出醋酸纤维素非对称膜,并成功地应用于反渗透过程[9]。但由于膜在干燥过程中,水的表面张力作用致使膜表面产生孔缺陷,而无法用于气体分离。1969年Kenneth和Burris发明了加入表面活性剂以减少界面张力的方法,避免了膜在干燥过程产生缺陷,但这研究没有继续下去[10]。直到1977年DuPont公司用熔融法制造出内径为36μm的均质聚酯中空纤维膜,并用于氢回收,这标志了气体膜技术开始走向工业应用[11]。由于均质膜对气体渗透速率太低,DuPout公司通过减少丝径增加膜分离器的填充密度(10000ft2/ft3膜分离器)来增加其对气体处理量。
气体膜分离技术的真正突破是在20世纪70年代末,1979年美国的Monsanto公司研制出Prism膜分离装置,成功应用在合成氨驰放气中回收氢气。Prism装置采用聚砜-硅橡胶复合膜,以聚砜非对称膜作为底膜,在其表面真空涂布一层硅橡胶膜。底膜起分离作用,硅橡胶涂层是为了修补底膜皮层上的孔缺陷,以保证高选择性[12,13]。非对称底膜由于皮层仅有0.2μm左右厚,远比均质膜薄,因此其渗透速率大大提高,自商业应用以来,目前已广泛应用在合成氨驰放气中和甲醇尾气中氢回收以及石油炼厂气中氢回收。
除氢氮分离膜外,20世纪70年代以来,富氮膜、富氧膜、二氧化碳分离膜及VOC膜等也取得长足进展。1976年美国GE公司把硅橡胶-聚碳酸酯共聚物用水面展开法得到0.015μm厚超薄膜,数张膜重叠,作为医疗用富氧膜,翌年把装置推向市场。1982年日本帝人公司开发的聚4-甲基-1-戊烯膜,富氧浓度达到40%。但由于聚4-甲基-1-戊烯膜氧氮分离系数只有4,用于富氮的经济浓度只有95%。1986年Permea公司(Monsanto子公司)推出Prism-α富氮装置,所用的膜也是硅橡胶/聚砜复合膜,但由于改进了制膜工艺,使其对气体渗透性能比Prism提高约3~5倍[14,15]。1990年前后,Generon、Praxair和Medal公司也相继采用定制聚合物使氧氮分离系数达到6~8,富氮浓度高于99%,用于小规格制氮系统,经济性优于空气深冷工艺。
1994年Medal公司推出聚酰亚胺(PI)中空纤维膜,用于CO2/CH4分离,但由于高压CO2和烃类气氛下PI抗塑化能力弱,分离系数衰减明显;此外PI作为膜材料,对CO2的透气性差,所以很多研究人员通过合成新的PI和化学改性来改善PI的链结构,阻止PI分子链段的紧密堆砌,减弱链间分子相互吸引力,增加CO2的溶解性,以期得到高选择性和高透过性的膜材料。目前,天然气脱碳市场仍以UOP公司的醋酸纤维素膜为主。UOP在巴基斯坦建成了迄今为止最大规模的天然气脱碳装置,处理量为5.1×106m3/d。此外,Cynara(现在的Natco公司)、GMS(现在的Kvaerner公司)也有醋酸纤维素膜可用于天然气脱碳。
水蒸气是可凝性气体,在聚合物膜中渗透速率非常高,因此,常用聚合物膜材料如聚砜(PSF)膜、聚酰亚胺(PI)膜、硅橡胶(PDMS)膜以及醋酸纤维素(CA)膜等均可以用于制造水蒸气透过膜。1987年Permea公司推出CactusTM膜法脱湿分离器,随后日本UBE公司推出聚酰亚胺中空纤维膜脱湿组件。目前美国Permea公司和UOP公司、日本UBE公司等均有气体脱湿过程用的分离膜产品,实现了空气及天然气脱湿的工业化应用。
有机蒸气膜法回收VOCs研究始于20世纪80年代,膜材料多为功能性硅橡胶,用于从聚合原料气、驰放气以及汽油储罐等中回收有经济价值的VOCs。目前国外膜分离法回收VOCs的生产厂家主要包括[16]:美国MTR、德国GKSS等。1998年,中国科学院大连化学物理研究所和吉化公司合作进行了现场实验,采用螺旋卷式膜分离器回收聚乙烯生产过程中排放的乙烯和丁烯单体,取得了较好的效果。国内主要生产厂家有中国科学院大连化学物理研究所、天邦膜技术国家工程研究中心有限责任公司和大连欧科膜技术工程有限公司等。
12.1.2.2 多种分离工艺集成过程
低温分离、吸附分离、溶剂吸收分离和膜分离等均可用于气体分离,各种过程均有局限性和应用范围。集成膜技术就是把膜技术与其他工艺优化组合,根据各技术自身特点,发挥协同作用,达到高效、低成本、低能耗及污染少的目标。举例如下。
①膜分离以分压差为推动力,适用于高浓度气体分离;变压吸附适用于低浓度气体分离,吸附可较长时间内操作,再生周期长。如把膜分离与变压吸附组合可以高效地从空气中制取99.5%氧气。
②VOC膜分离过程通常采用膜分离、变压吸附、吸收和冷凝分离等集成,实现单独工艺过程很难做到的高回收率和低能耗,油气浓度可降至排放标准。将膜分离氢回收与氨蒸馏集成,可以回收成氨驰放气中氢气与氨气,使过程更具有经济性。
③炼厂气中含有大量轻烃,采用压缩冷凝、变压吸附、氢气膜分离和有机蒸气膜分离等梯级耦合膜分离工艺,按照最合理的工序将合适的分离技术有机整合,实现不同分离单元的无隙匹配和高附加值物质的分离回收。
④胺吸收法更适合低浓度二氧化碳分离,将膜法-胺吸收法联合工艺用于从天然气脱二氧化碳,可以提高天然气脱二氧化碳的经济性。
⑤膜接触器吸收技术是膜技术与吸收过程进行耦合的新型吸收过程,膜起着分隔气体与吸收剂作用,同时为气体提供扩散通道,吸收剂根据气体各组分溶解度差提供选择性。膜接触器既具有中空纤维膜高装填面积,传质效率高,又具有吸收分离法的高选择性,同时避免在传统吸收塔中常常出现的不良现象,如液泛、漏液、夹带和鼓泡等。可以应用于天然气和沼气脱酸性气体、人工肺中体外膜肺氧合器(extra corporeal membrane oxygenation,ECMO)等。
膜分离技术具有能耗低、操作简单、装置紧凑、占地面积少等优点,因此氢分离膜、富氧膜、富氮膜相继研制成功,并应用于市场,有力地促进了气体膜分离技术的发展。其应用越来越广泛,对它的研究也日益深入。表12-2列出工业化的气体膜分离技术和目前正在研究开发的新技术,表12-3列出目前世界上气体分离膜主要生产厂家。
表12-2 目前已工业化气体膜分离技术和正研发的新技术[3,17,18]

表12-3 世界上气体分离膜主要生产厂家[19,20]

成熟的膜分离过程包括空气分离、H2回收、天然气处理、VOCs/气体、空气除湿等,正在发展的膜分离应用集中在石油精炼和化工行业的烃类回收,如天然气中、H2S、N2的脱除等。至今工业应用分离膜的材料大多采用工程塑料或经过物理/化学改性的商业材料。由于气体渗透系数和分离系数间存在trade-off效应,使得膜性能很难超越Robeson上限(在气体分离膜中,气体的渗透性和选择性成反比,而理想的结果是既要高的渗透性,又要高的选择性,在一定程度上两者会有一个相对最大值,这个就是Robeson上限);另外,膜分离技术仍需要和其他工业化分离手段相竞争。因此,需要开发出高分离系数和高通量的气体膜,目前气体分离膜发展研究热点主要集中在:
聚合物材料分子设计;
规模化生产的无缺陷、超薄皮层(<0.1μm)中空纤维分离膜;
CO2/H2和CH4/N2分离膜及过程;
有机微孔聚合物材料(如PIMs、TR膜等);
有机-无机杂化膜(如MMMs);
促进传递膜(含醚氧键、胺类化合物等);
无机分离膜材料(如SAPO-34等);
新过程(如膜吸收等集成过程等)。