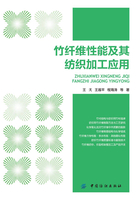
第三节 竹纤维的化学制取方法
物理法使竹材初步成纤,宏观裂纹使竹纤维与胶质脱粘分离、而细观裂纹也已初步产生,但由于物理法无法使胶质脱除干净,因此必须配合化学脱胶方法对竹材上的胶质进行分离。
一、研究对象与方法
实验材料同前,经第二节物理法处理后的竹材作为本节的实验材料。
目前,国内外麻的化学脱胶发展趋势是快速、高效、短流程和连续化,为了缩短工艺流程、加速脱胶工序进程以及节省能源,方法之一是取消传统的浸酸、高温高压煮练等工艺,其作用由碱煮工序增加功能作用来代替,即在碱液中添加有效的脱胶助剂,为加速胶质的溶出速度和效率创造条件。借鉴麻脱胶的研究基础,本节对竹纤维的化学脱胶工艺进行了设计,其宗旨是短工序、低能耗、低污染、低成本。本节的化学处理采用有效的脱胶助剂并进行复配,不采取传统的浸酸工序,煮练也在常压沸煮的条件下进行。本章中所制取的是生竹纤维,在后道工序中再对竹纤维做进一步的精细化处理。如漂白、多道煮练等。
实验方法:采用化学脱胶法,即利用竹材中的纤维素和胶质成分对碱液稳定性的不同,在不损伤或尽量少损伤纤维原有机械性能的原则下,去除其中的胶质成分。在此采用正交实验方法进行实验设计,利用正交表安排实验方案。
化学处理用药品:氢氧化钠,亚硫酸钠,焦磷酸四钠,表面活性剂ZF。
经化学脱胶后,将竹纤维的细度、强度及残胶率等指标作为竹纤维制取成功的主要评判依据进行测试,这些指标决定了纤维的可纺性和应用价值。普通的化学脱胶主要脱除半纤维素为主的胶质,木质素脱除效果往往不好,故在此以残胶率而不是剩余木质素含量为指标进行工艺效果的评定。
(1)纤维细度。参照国标GB 6100—85,采用中段切断称重法测试。
仪器:中段切断器(Y171型),宁波纺织仪器厂;电子分析天平(AR2140型),奥豪斯国际贸易有限公司;电脑式恒温恒湿箱(YG751B型),宁波纺织仪器厂。
测试条件:纤维在温度(20±3)℃,相对湿度为(65±5)%的环境下调湿24h。
纤维细度计算:Tt= 1000m /(L×N)
式中:Tt为线密度(tex); m为中段纤维质量(mg);N为纤维根数(>300根);L为切断纤维长度(20mm)。
(2)纤维残胶率。参照国标GB 5889—86苎麻残胶率测试方法进行测试。
仪器:八篮恒温烘箱(Y802L型),莱州电子仪器有限公司;电子分析天平(AR2140型),奥豪斯国际贸易有限公司;恒温水浴锅(HH·S21-8型),上海树立仪器仪表有限公司。
测试条件:NaOH溶液浓度20g/L,沸煮时间3h,烘干温度105~110℃(直至恒重)。
残胶率计算:W c =(G0-G1)/ G0×100
式中:Wc为试样残胶率(%);G0为试样提取残胶前的干重(g);G1为试样提取残胶后的干重(g)。
(3)纤维断裂强度。参照国标GB 5886—86苎麻单纤维断裂强力试验方法进行测试。
仪器:单纤维强力仪(LLY-06C/PC型),莱州电子仪器有限公司;电脑式恒温恒湿箱(YG751B型),宁波纺织仪器厂。
测试条件:预加张力0.05cN/dtex,夹持距离20mm,下夹头下降速度20mm/min;
试样在温度(20±3)℃,相对湿度为(65±5)%的环境下调湿24h。
测试指标:断裂强度(cN/dtex)。
纤维制成率在此仅作为参照指标,非限定性指标,故未列出。
二、竹纤维制取用助剂的选择与复配
在化学脱胶的过程中,若只用烧碱溶液(不含其他化学助剂)作用于竹材,由于烧碱溶液对竹材的界面张力大于水对竹材的界面张力,会导致脱胶速度慢、脱胶时间长,甚至消耗更多的烧碱。随着人们对麻化学脱胶工艺的改进研究,特别是20世纪70年代末到80年代初,湖南株洲苎麻纺织厂、武汉市纺织科学研究所等单位先后选用磷酸盐类助剂,成功实现了以磷酸三钠和亚硫酸钠、三聚磷酸钠、焦磷酸四钠和亚硫酸钠三种为代表的无机助剂化学快速脱胶工艺。该工艺大大缩短了碱煮时间,提高了工效和脱胶效率,因此很快在全国范围内得到了应用和推广。
亚硫酸钠具有还原作用,能夺取其他物质中的氧,防止这些物质在高温和强碱性介质中对纤维的损伤,尤其在碱煮过程中,亚硫酸钠能使木质素变成木质素磺酸盐而易溶于碱液中。
磷酸三钠有溶解果胶、蜡脂质的作用,同时具有渗透、乳化和很强的分散性能。分散性能的产生,使它对多价金属离子有较强的络合能力,可促使胶质分解、溶出。此外,磷酸三钠本身对胶质有吸附能力,使胶质不断与煮练液作用,而又不断地分散在煮练液中。
三聚磷酸钠是一种多电荷并具有胶束结构的电解质,正是这个原因,煮练一开始就大大增加了胶质上的负电势,加快了钠离子对胶质作用的反应速度,使果胶、木质素、半纤维素胶质分散成微小的胶溶粒子而悬浮于碱液中,同时由于它的高势垒可以阻止、延缓溶解了的胶质重新吸附到竹材表面的现象,这是三聚磷酸钠优于磷酸三钠的一个重要原因。且它也是一种很强的螯合剂。
焦磷酸四钠具备三聚磷酸钠所有的优点,并且更优于三聚磷酸钠的是,它在高温、高浓度碱液条件下的水解性小,有利于保持和发挥效能,故能以较小的用量达到较好的快速脱胶效果,很好地适应了实际生产条件。
除上述无机化学助剂外,表面活性剂也是一种应用较多的脱胶助剂,它可以大大降低液面的表面张力,提高反应的活化能。若将表面活性剂与几种无机化学助剂复配,将会综合低表面张力、高渗透效果、扩散和多价电荷胶束的强电解质等多方面优势,而发挥出较佳的快速脱胶效果。
根据以上分析,最终选定焦磷酸四钠和亚硫酸钠两种无机化学试剂,并选用纺织印染助剂公司提供的表面活性剂(ZF),利用正交实验方法进行实验设计,确定这三种助剂的最佳用量并按比例进行复配。
由于竹材结构紧密,而且其中的半纤维素、木质素等胶质含量远远大于常规麻的胶质含量,因此三种脱胶助剂(亚硫酸钠、焦磷酸四钠、表面活性剂ZF)的最大用量范围都比麻脱胶用量增加一倍。为了确定它们的最佳值,选择L9(34)正交表进行实验设计(表3-8)。另外,助剂用量单位均为对竹材重(%),碱煮NaOH浓度为10g/L,碱煮时间为1h。
表3-8 脱胶用助剂正交实验设计方案

表3-9是竹纤维制取用助剂的正交实验结果,表3-10是各测试指标的直观分析结果。其中,K表示各个水平的均值,R表示极差。
表3-9 脱胶用助剂正交实验结果

表3-10 脱胶用助剂正交实验直观分析结果

首先利用表3-10确定各助剂的最佳用量。对于纤维细度来说,该指标越小越好,最佳方案为A2B2C3;对于纤维强度来说,该指标越大越好,最佳方案为A3B2C3;对于纤维残胶率来说,该指标越小越好,最佳方案为A3B2C2。综合得出三种助剂的最优用量方案是A3B2C3,即亚硫酸钠6%,焦磷酸四钠3%,表面活性剂(ZF)6%。这种组合方案没有安排在表3-9的九个实验中,按照最优方案重新制取竹纤维,得到纤维性能指标列于表 3-11。
表3-11 助剂最优方案下的纤维性能指标

表3-11中各项纤维性能指标相对较优,因此竹纤维制取用助剂的最优方案为:A3B2C3。并在此基础上,按照亚硫酸钠:焦磷酸四钠:表面活性剂(ZF)=2:1:2的比例将三种助剂复配成一种新的助剂,称为复合助剂。
方差分析表明,对于脱胶效果来说,三种助剂的作用大小各不相同,基本趋势是:表面活性剂(ZF)>焦磷酸四钠≥亚硫酸钠。但就助剂作用的显著性来说,只有表面活性剂(ZF)对纤维细度的影响作用显著,其他二者的作用都不明显;而对于纤维强度和残胶率来说,三者均没有显著作用。这可能是由于单纯靠脱胶助剂的作用还不够强,还需要与碱浓度、碱煮时间等工艺条件相结合才能发挥出最佳效果。需要进一步研究竹纤维化学制取工艺。
三、竹纤维化学制取工艺的研究
在竹纤维化学制取工艺中,氢氧化钠浓度、碱煮时间及复合助剂的用量对脱胶效果产生很大影响,需要进行单因素影响分析,通过对所制取纤维性能指标(纤维细度、纤维强度、残胶率)的测试,根据各个因素的变化范围进行正交实验设计,优化工艺参数,得到竹纤维制取的最佳化学工艺条件。
(1)碱浓度对脱胶效果的影响。氢氧化钠是碱煮过程中的主要化工原料,其用量大小不仅影响脱胶的质量,也影响化工原料的消耗和成本。用量过少,脱胶程度不足;反之,用量过多,既浪费了化工原料,还会导致脱胶过头,形成竹单根纤维,无法进行纺纱。因此,氢氧化钠的用量非常重要。在复合助剂用量为10%(对竹材重),碱煮时间为90min的条件下,改变NaOH的浓度,进行一系列实验,实验结果见图3-7。
从图3-7中可以看出,随着碱浓度的增加,纤维的细度、强度和残胶率都呈下降趋势。这是由于在相同助剂用量及碱煮时间的条件下,NaOH浓度越高,便有更多的Na+离子进入竹材内部与胶质进行反应,这样,纤维与胶质的分离程度也更大,因此纤维变细、残胶率下降,但与此同时,也有更多的Na+离子进入竹材内部破坏纤维细胞间质的连接,同时也对纤维造成一定损伤,因而纤维强度有所降低。

图3-7 碱浓度对竹纤维性能的影响
当NaOH浓度增加到16g/L时,纤维细度、残胶率值基本达到稳定,而纤维强度仍在下降。事实上,在14g/L时,各项指标变化速率显著减慢,即使再增加NaOH浓度到20g/L,纤维细度、残胶率也没有太大改善,反而使纤维强度进一步下降,说明此残留在竹纤维上的胶质很难在碱作用下去除。因而再增加NaOH浓度无法起到应有的作用,故选择NaOH浓度范围为11~15g/L。
(2)碱煮时间对脱胶效果的影响。碱煮时间是煮练过程的重要工艺参数之一。在NaOH浓度为14g/L,复合助剂用量为10%的条件下,研究碱煮时间对脱胶效果的影响,实验结果见图3-8。

图3-8 碱煮时间对竹纤维性能的影响
从图3-8中可以看出,随着碱煮时间的延长,纤维强度呈下降趋势,纤维的细度和残胶率先下降,而后随着时间的延长(120min后)有所上升;而且碱煮时间到90min后,下降的趋势较平缓。这是因为,一方面,随着时间的增加,溶液中的碱浓度在不断减小,反应的速度逐渐变慢。碱煮时间从30min延长到60min时,纤维细度、强度、残胶率的下降幅度都较大,时间从60min再延长到90min时,下降速度减慢;另一方面,随着碱煮时间的延长,竹材表面开始形成多糖高分子物凝胶,即溶解了的胶质又重新吸附在竹材表面,阻止了Na+离子及复合助剂离子对胶质的进一步反应,因此脱胶程度开始稳定,以至于时间再延长到120min,重新吸附的胶质使竹纤维的细度和残胶率又有所回升。但是纤维强度则不同,时间越长,只会使纤维表面受到的损伤越大,降低强度。因而选择碱煮时间范围为60~100min。
(3)复合助剂用量对脱胶效果的影响。将上述三种助剂按一定比例复配形成复合助剂。在NaOH浓度为14g/L,碱煮时间为90min的条件下,摸索该复合助剂用量对脱胶效果的影响,实验结果见图3-9。

图3-9 复合助剂用量对竹纤维性能的影响
从图3-9中可以看出,随着复合助剂用量的增加,纤维的细度、强度和残胶率都呈下降趋势。该复合助剂具有低表面张力、高渗透效果、多价电荷胶束的强电解质和高势垒等多方面特点。复合助剂用量越多,越有利于Na+离子与胶质进行反应。另外,由于它的高势垒作用,可以阻止、延缓溶解了的胶质重新吸附到竹材表面,加快了脱胶的进行,同时也使更多Na+离子进入竹材内部。因而,复合助剂用量增加后,纤维得到细化,残胶率有所下降,当然也由于更多Na+离子的作用造成纤维一定的损伤。
当复合助剂用量由10%增加到12%时,纤维的细度趋于稳定,这是因为余下的胶质是难以溶解的抗碱性物质,由于Na+离子进入竹材内部,也会造成纤维强度的下降,但对纤维细度的改善不大。因而,确定复合助剂的用量范围为6%~10%。
通过对碱煮过程中NaOH浓度、碱煮时间及复合助剂用量的单因素影响分析,确定了三个因素的工艺参数范围。为了最终得到它们的最佳值,选择L9(34)正交表进行实验设计(表3-12)。
表3-12 竹纤维化学制取工艺的正交实验设计

竹纤维化学制取工艺的正交实验结果见表3-13,分析结果见表3-14。
表3-13 竹纤维化学制取工艺的正交实验结果

表3-14 竹纤维化学制取工艺的正交实验直观分析结果


通过该正交实验,可以确定竹纤维制取的最优工艺条件。首先分析在不同测试指标下的最佳方案,列于表3-15中。
表3-15 不同测试指标下的最佳方案

从表3-14可以看出:碱浓度和复合助剂用量从1水平到3水平,纤维细度越来越细,残胶率越来越低,纤维强度也越来越低,这与前面的单因素分析结果是一致的。但纤维强度的下降幅度并不大,可以满足加工与服用要求。因此,通过表3-15,可以得出碱浓度和复合助剂用量的最佳水平为3水平。对于时间因素的各水平来说,一方面时间对纤维各指标的影响较小,另一方面纤维细度作为本工艺的重要测试指标,也为了节约能耗,选择碱煮时间为2水平。因此,综合得出竹纤维制取工艺的优化方案为A3B2C3:即NaOH浓度为15g/L,碱煮时间为80min,复合助剂用量为10%。该组合方案没有安排在表3-13的九个实验中,按照优化方案重新制取竹纤维,得到纤维性能指标如表3-16。
表3-16 竹纤维制取工艺优化方案下的纤维性能指标

另外,通过方差分析可以得出不同工艺条件对于脱胶效果的作用大小,其基本趋势是:NaOH浓度>复合助剂用量>碱煮时间。就作用的显著性来说,NaOH浓度和复合助剂用量对纤维细度分别有很显著和显著的影响,而对于纤维强度和残胶率来说,三者均没有显著影响。分析其原因,对纤维强度来说,由于所制取的竹工艺纤维细度相对较粗,本实验中碱用量并不大,虽然碱处理会在一定程度上破坏纤维间的结合,但对纤维强度影响较小;对残胶率来说,主要是因为竹材中含有部分抗碱性的顽固胶质,经碱处理到一定程度后,其残胶率基本达到稳定。
综上所述,通过对竹纤维制取工艺的单因素实验及正交实验,得到毛竹纤维的最佳细度为4.15tex,残胶率为14.16%,纤维强度为3.13 cN/dtex。同时利用相同工艺处理慈竹,得到慈竹纤维细度3.71tex,残胶率13.15%,纤维强度3.23 cN/dtex。
尽管通过物理化学制取工艺获得的竹纤维还较粗,残胶率还很高,但其纤维已初步具备纺织用纤维的雏形,因此,物理化学联合的制取工艺是可行的。当然,从纤维可纺性来说还存在一定的差距,尤其是顽固性胶质的存在,很难仅仅通过煮练方式使纤维的细度和残胶率得到显著改善,有待于选择更有效的木质素脱除手段做进一步研究。