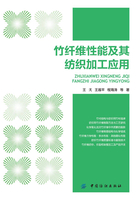
第二节 竹材的物理分离方法
按照物质受外加载荷的几种基本作用形式——拉伸、弯曲、压缩、剪切及扭转设计本实验。由于竹片极薄,厚度方向不考虑,将其看作二维的平面。其中弯曲作用因作用过程中易发生纤维断裂而未采用。本实验的目的是比较各种作用方式对竹材分离的效果。实验材料同第一节。
实验方法:对碱煮过的竹片(固定采用次外层竹片,竹片尺寸:厚1mm,宽10mm,足够长,以下同)施加正压力(图3-2),然后在LLY-06C/PC型单纤维强力仪上测试其勾拉强力(竹片内纤维与胶质间的分离力)(图3-3)。由于竹片经外载负荷作用后,纤维上还黏附着大量的胶质,无法进行准确的纤维细度、残胶率等指标的测试,因此以下实验均用勾拉强力的大小进行竹片分离程度的判定。

图3-2 施压过程

图3-3 勾拉过程
在施加压力过程中,改变了压力大小,分别施加0、0.2、0.4、0.6、0.8 MPa的压力,施压4次;改变施压次数,分别施压0、2、4、6、8次,压力选择0.6 MPa;更换轧辊材料,分别为1#、2#、3#材料,粗糙度依次增大。
实验结果见表3-3、图3-4、图3-5。
表3-3 不同压缩参数条件下的作用效果比较


图3-4 勾拉强力随施压次数的变化

图3-5 勾拉强力随压力大小的变化
压力负荷作用下的实验结果表明:在压力负荷作用下,竹片沿顺纹方向的勾拉强力下降了60%~70%,发生了显著的松弛分离效果。由于竹材的纵横向异性特点,在施加压力时所引起的横向张力和剪切力极易引发竹材沿顺纹方向出现裂纹并扩展,即使是垂直纹理的裂纹,也常常会发生偏转而改沿顺纹方向扩展。又由于竹材是纤维与基体弱界面结合材料,即使是基体裂纹也容易在界面处发生转折,从而使纤维保持完整,因此竹材在压力作用下横向很容易发生松弛而分离,而且由于压缩过程中竹片横向没有被限制其变形,因此会产生较大的横向膨胀,从而造成应力下降,而竹片中纤维纵向不会发生断裂。
竹片在受压过程中,压力的大小、施压次数以及轧棍材料对竹片的分离都有显著的作用。随施压次数的增多、压力增大,竹片沿顺纹方向的勾拉强力不断减小,竹片被分离的程度加剧。从图3-4、图3-5中看出,竹片在经受2~4次或0.4~0.6MPa的压力时,勾拉强力下降最快,以后下降减缓、效率逐渐降低。在反复受压或施加大压力过程中,竹片横向膨胀越来越小,这对于分离纤维与胶质已没有太大作用,反而会对纤维纵向强度造成破坏。从图中还可看出,在相同压力和受压次数时,表面粗糙的3#轧棍作用效果远优于光滑的1#、2#轧辊材料。3#轧辊材料被设计为高低起伏的点状凸起,这样可以产生竹片局部的高压区与低压区,高压区面积小压力大,只要该挤压分离临界压力小于纤维束的抗拉强度,竹片就会沿顺纹方向产生滑移和分离,而纤维不会被压断,同时由于湿态纤维在压力作用下有取向性,即纤维由压力高的区域向压力低的区域滑动,这样高低不平的挤压表面所产生的高压区与低压区,既保证了纤维的分离,又使纤维有足够的余地发生滑动,可有效避免纤维纵向压断现象的发生。最终加压条件设计为:0.6MPa压力、施压4次、3#轧辊材料。
总之,压缩外力的作用是在保证纤维束不断裂的前提下,使竹材天然复合材料的结构发生松弛、分离或重组,使纤维与胶质间的界面分离,甚至使纤维束发生部分分离,获得一定的尺寸形态以便继续施加另一载荷。
实验方法:碱煮后的竹片(实验材料条件同上)用夹持器将两端握持,沿轴向旋转180°,分别扭转5次、10次、20次、30次。
实验结果见表3-4。
表3-4 扭转外力对竹材分离的影响

扭转外力对竹材的分离有较明显的作用,扭转次数越多竹片越容易分离,但扭转次数超过20次,竹材分离效率下降,且次数过多会导致纤维断裂,次数过少则分离效果不明显,扭转20次的平均勾拉强力下降率在40%左右。表3-4结果还表明,扭转力也有利于竹片中纤维束与胶质的分离,但是没有压缩负荷作用显著,这是因为扭转力在径向的分力较小的缘故,而且由于竹片的2维平面体使扭转力在不同力矩点的力大小不等。
实验方法:沿竹片长度方向对碱煮后的竹片施加50g力的拉伸外力;将竹片沿与其轴向呈15°夹角的方向剪成平行四边形,如图3-6所示,握持两端,施加同样大小的拉伸外力,静置18h,然后在温水中浸泡1h后捞出测试其勾拉强力。由于竹片横向尺寸小(特别是一些小径竹横向尺寸更小),因此未施加横向拉伸负荷。
实验结果见表3-5、表3-6。
表3-5 拉伸外力对竹材分离的影响

通过对经受与未经受拉伸负荷竹片的勾拉强力值进行配对T检验表明:受拉伸与未受拉伸竹片的勾拉强力值无显著差异(相伴概率为0.645,大于0.05的显著性水平),表明纵向拉伸负荷对竹片的分离无显著作用,这与竹材的特性相吻合。
表3-6 斜向拉伸外力对竹材分离的影响


图3-6 对竹片施加斜向拉伸的取样方式
通过对经受与未经受斜向拉伸外力作用的竹片勾拉强力值做配对T检验,结果表明斜向拉伸对竹片的分离无显著作用(相伴概率为0.573,大于0.05的显著性水平)。这一方面说明斜向拉伸外力对竹片热软化效果要求较高,另一方面也是斜向制样角度较小的缘故。
以上研究表明,在物质的基本受力形式中,压缩外力对竹材界面分离效果最显著,扭转外力次之,顺纹方向拉伸与斜向拉伸作用不显著,这些结果与竹材特性是一致的。故竹材界面分离的最佳方式确定为:对竹片外载压缩负荷。
为了引发竹材的细观裂纹,采用了超声波法。超声波既是一种波动形式,又是一种能量形式,利用它的机械力学机制和空化机制等作用近年来应用在苎麻、大麻等纤维的脱胶上。在此希望利用超声波的物理机械效应和空化效应在竹材中引发微细裂纹。
仪器:KQ—100A型超声波清洗器,昆山市超声仪器有限公司。
实验方法:碱煮后的竹片在超声波仪中进行处理,振动频率:25kHz,处理时间:30min,温度:30~40℃。碱煮后的竹片先经加压(0.6MPa,施压4次,3#轧辊材料)后经超声波处理(30min,25kHz),然后在强力仪上测试经过处理与未经处理竹片的勾拉强力。
实验结果见表3-7。
表3-7 超声波对竹材分离的影响

表3-7的结果表明:采用超声波处理对竹片的分离效果有一定的作用,勾拉强力下降率接近30%。但从结果看,仅借助于超声波作用还不够显著,因为超声波的能量只能在局部微小区域起作用,因此对竹片的分离、对竹片宏观裂纹的产生作用不明显。
而经压力和超声波共同作用后,竹片的勾拉强力下降率达80%以上,两者组合作用效果优于单一方式作用之和。在处理过程中,竹片因压力先得以宏观分离,再利用超声波能量局部集中,促使物质局部做激烈的强迫机械振动,在一定频率的超声波振动过程中使竹片上的裂纹逐渐扩展。同时勾拉强力数据还表明:经过超声波和压力处理后勾拉强力数据波动较小,说明竹片的分离效果很均匀。
总之,对竹材先施加压力再实施超声波引发,压力使竹材横向分散,产生有效的分离作用,出现宏观裂纹;而超声波能量帮助纤维束内部进一步分离,也帮助纤维束与胶质分离,使竹材得以成纤。