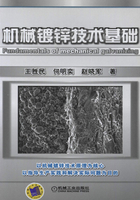
1.3 机械镀工艺
1.3.1 机械镀的提出
19世纪40年代末50年代初,美国Tainton公司的Erith Clayton在利用颗粒状金属粉生产片状金属粉末的过程中,发现球磨机内金属粉和钢球一起滚动时,钢球表面经常覆盖有金属粉末。于是,他选择合适的化学药剂在不通过电流的情况下,采用金属锌粉在另外一种金属表面获得锌覆盖层,并称其为锤击镀(peen plating)[36]。当时的这种镀锌工艺镀覆一批工件要用几个小时,甚至达8h才能达到预定的厚度,且金属锌粉的有效利用率仅为30%,故未能进入生产应用。之后,人们逐渐优化化学添加剂,设计新型设备,选择更合适的冲击介质,一直到20世纪70年代末,金属锌粉的有效使用率提高到90%左右,锤击镀也逐渐在全世界进入工业应用,这种工艺并被广泛称为机械镀锌(mechanical plating或mechanical galvanizing或peen plating或impact plating)。
从严格意义来讲,机械镀分为干性机械镀(dry impact plating)和湿性机械镀(wet impact plating)。干性机械镀在日本发展较快,现在在太平洋沿岸各国和欧洲许多国家得到开发利用。该工艺是利用类似喷丸的设备,将金属粉末高速喷打到工件表面上,使机械能在瞬间转化为结合能而形成镀层。它具有防腐、不产生氢脆、无污染、无废水处理的优点。
机械镀借助于机械能形成镀层的这一过程,就可以使得欲镀金属仅发生固态转移且在工件表面形成致密的金属镀层,施镀过程中的能量转换为:电网电能→电动机→机械能→变形能和热能→形成镀层。按机械镀过程冲击介质获得能量的高低,将其分为传统机械镀和高能机械镀。
1.3.2 高能机械镀
1.高能机械镀工艺的基本原理
高能机械镀是把欲镀金属(颗粒状或细片状)、冲击介质和经过预处理的零件放入容器中,容器通常具有真空环境或有惰性气体保护,装置运动使冲击介质产生强烈机械能,欲镀金属和工件在机械能的作用下牢固结合在一起形成镀层,经后续热处理增加镀层结合强度而获得最终镀层。
高能机械镀过程介质获得高机械能是依靠加速度,这不同于传统的机械镀。因此,介质往往选用硬质耐磨的球状物质作为冲击介质。
高能机械镀后续热处理的作用是:释放镀层中部分能量,使镀层趋于稳定;产生烧结效果,增加镀层的强度[37]。
高能机械镀与传统机械镀的区别在于:高能机械镀过程冲击介质具有较高的机械能,是传统机械镀过程介质能量的几十到几百倍,并且介质能量可根据需要人为在一个较大的范围内变动。高能冲击介质可使金属粉末扁化,还能完全摧毁工件表面的氧化膜使工件表面保持洁净[37,38]。
高能机械镀的工艺流程为:工件→预处理(脱脂、除锈)→建立施镀环境(小件采用密封性容器,大件利用装夹使施镀环境密封)→选择是否保护性气氛→开启装置形成镀层→卸料→分离→热处理→贮运。
2.高能机械镀设备
高能机械镀设备的主要功能是通过机械运动(搅拌、振动、喷射、球磨、摩擦等)使冲击介质获得较大的机械能,促使欲镀金属在工件表面变形并形成金属镀层。
图1-3 搅拌型高能机械镀装置原理图
1—容器 2—转动轴 3—真空泵 4—冷却套 5—密封盖 6—密封圈 7—冲击介质 8—金属粉末 9—叶片 10—工件
图1-4 振动型高能机械镀装置原理图
1—容器 2—振动台 3—工件 4—真空泵 5—弹簧 6—密封圈 7—冲击介质 8—金属粉末 9—振动器
高能机械镀设备因产生高机械能的方法不同,所以出现多种类型的设备。根据机械能产生的方式大致分为四类:搅拌型(见图1-3)、振动型(见图1-4)、球磨机型(见图1-5)、喷射型(见图1-6)。搅拌型、振动型、球磨机型的设备通常包括三部分:动力部分(如图1-3中的转动轴及叶片、图1-4中的振动发生器及弹簧等)、容器部分(存放冲击介质、欲镀金属、工件)、保护气氛装置(真空泵或惰性气体的导入和排出部分,如图1-3、图1-4中的真空泵等)。搅拌型和振动型装置都采用了真空环境防止金属表面的氧化(欲镀金属粉末表面和工件表面)[37]。球磨机型设备类似于行星高能球磨机,冲击介质选用钢球或金刚砂,在施镀过程中需要添加专用的活化剂,如铝粉、氯化锌、氯化铵等[39]。喷射型设备类似于喷丸装置,冲击介质和欲镀金属粉末混合在一起,经输料系统传输到喷射器,然后快速喷射到工件表面上,使高机械能在瞬间转化为结合能而形成镀层[40,41]。高能机械镀的辅助设备主要是热处理炉,热处理炉及工艺参数(温度、时间、气氛)的选择不仅要考虑工件的尺寸,还要注意欲镀金属的熔点温度、镀层中各化合物的熔点温度。例如,当采用高能机械镀获得Al的合金化镀层时,镀层中若形成Ni3Al、Fe3Al、TiAl等金属间化合物,比较各化合物、工件基体、欲镀金属铝的熔点温度,发现铝的熔点温度最低,故设置热处理温度为800~1300K[37]。
图1-5 球磨机型高能机械镀装置原理图
1—工件 2—筒子 3—金属粉末 4—冲击介质
图1-6 喷射型高能机械镀装置原理图
1—金属粉末 2—冲击介质3—工件 4—喷射器
3.高能机械镀工艺的特点及应用
(1)高能机械镀工艺的特点
1)镀层不产生氢脆,可实现清洁生产。
2)易获得合金化镀层WC、TiAl、TiC、SiAl等,实现镀层的复合化。
3)可以获得硬质金属镀层,如Fe、Ti、W、Zr等。
4)选择合适的设备可以施镀大尺寸工件。
5)不需要废水处理。
6)镀层厚度和均匀性难以控制。
(2)高能机械镀的应用 高能机械镀因产生高机械能的方式不同,工艺操作过程和设备也各有所异。与传统的机械镀相比,高能机械镀工艺的研究及应用发展缓慢,应用也不是很成熟。其中,喷射型高能机械镀工艺在太平洋沿岸各国和欧洲部分国家获得了应用,其发展核心是喷射物料,美国专利4714622[42]和美国专利5548488[43]中提到的喷射物料为钢丸和金属粉末的混合物,锌粉要求杂质(如铅等)的质量分数不超过0.2%,钢丸直径为0.4~0.8mm;日本专利[44]提到的喷射物料是将金属粉末(如锌粉)用有机粘结剂粘结在钢丸表面,钢丸与被镀工件表面碰撞时金属粉末转移到工件表面逐渐形成镀层。但由于此工艺不易控制镀层的厚度和均匀性,喷射物料的制备比较复杂,于是在大批量的生产应用中还存在一些问题。
1.3.3 机械镀锌工艺及特点
1.机械镀锌工艺
传统的机械镀锌也就是通常所指的机械镀锌,其定义为:在常温常压下利用物理、化学吸附沉积和机械碰撞使金属锌粉在工件表面形成镀层的表面处理工艺。20世纪80年代在发达国家,20世纪90年代在我国,机械镀锌工艺进入工业生产。常见的工艺流程为:工件脱脂、除锈,预镀铜后与玻璃丸和水装入镀筒,然后根据预定的镀锌层厚度加入保持性活化剂、锌粉和沉积性活化剂,随着镀筒的转动,锌粉在工件表面上沉积并逐渐形成镀层。工艺中一般是采用柠檬酸、柠檬酸铵、酒石酸等有机酸和它们的盐作为保持性活化剂的主原料;亚锡盐作为沉积活化剂促进锌粉在工件表面上沉积[45]。在镀锌过程中适当的加入硫酸保持镀液的pH值为1~2,形成一个酸性的活性环境。上述工艺在生产中往往出现上锌速度慢,锌粉使用率低,镀液pH值易随锌粉的加入而升高,镀层表面粗糙,镀层厚时(>40μm)会出现镀层片状脱落等不正常的现象,严重时无论加入多少锌粉都难以得到厚镀层。主要原因可能为:①保持性活化剂的活性和稳定性较差,在镀锌过程中不能始终保持一定的活化力度;②亚锡盐水解形成的锡离子促使锌粉在溶液中聚团,当这种作用过强时锌粉团在工件上沉积出较粗糙的镀层,镀层的锡含量高,造成镀锌成本明显增加;③预镀铜处理对镀层结合强度影响的作用机理尚不清楚,厚镀层时(40μm以上)易脱落。后来,随着机械镀锌的发展,国内外的机械镀锌工艺经不断完善出现了柠檬酸(或柠檬酸盐)系列和少锡盐沉积系列。
2.镀层形成原理
关于传统机械镀锌的形层机理国内外都没有深入的研究,国外学者认为机械镀锌的机理是“冷焊”(Cold welding),而对于机械镀锌过程的冷焊研究及描述并未给出详细的解释[46]。经文献检索,有关双金属冷焊结合的理论假设或解释有七八种之多[47-49]。本书在长期的研究中发现机械镀锌层的形成过程发生着复杂的化学反应[50],但因为机械镀锌镀筒内物料环境的复杂性导致镀层形成过程化学反应的研究难度较大,关于此部分的研究分析也正是本书的主要内容之一。
3.机械镀锌设备
机械镀锌所用设备包括主设备和辅助设备(见图1-7),主设备以完成金属粉末在工件基体表面上沉积成层为主要功能,在工作过程中提供机械碰撞力和使混合料液形成合理的流态。
图1-7 机械镀典型设备原理图
注:选自http://www.mechanicalplating.com.
辅助设备用来完成工件和玻璃丸的装卸,锌粉和药剂的加入,工件、玻璃丸和浆液的分离,镀后工件的干燥和镀前、镀后处理,以及工件、玻璃丸的输送。它们可以与主设备连为一条全自动生产线,也可以从投资考虑用人工代替。
典型的机械镀锌工艺是把经过预处理的工件放入机械转动的镀筒中,加入水和冲击介质(玻璃丸),转动镀筒形成一个具有碰撞和搓碾作用的流态环境,根据预定的镀层厚度加入金属粉和药剂,在化学药剂和机械碰撞的共同作用下使工件的表面获得镀层,所以转动的镀筒是机械镀锌设备的主要组成。机械镀锌发展至今,镀锌设备先后出现了简易“跷跷板”型、半自动化型、PLC控制自动化型、机械式主机型、机械-液压复合式主机型,但镀筒的形状变化不大,均为六角或八角的开口橄榄球形(见图1-8)。
图1-8 典型机械镀设备镀筒模型图
4.机械镀锌工艺特点及应用
(1)机械镀锌工艺的特点
1)镀层不产生氢脆 机械镀锌可以完全消除氢脆或把氢脆的危险性降到最低程度。机械镀锌过程不需要电流,虽然在镀层形成过程中也有氢气产生,但因为镀层中存在有微孔,氢气不会在镀层中长时间滞留。
2)镀层厚度容易调控 机械镀锌层的厚度可以根据需要通过加料量控制,生产中可依工件的防腐蚀要求选择适合的厚度,实现防腐功能与生产成本的合理控制。
3)可实现清洁生产 机械镀锌所用原料无毒性,全过程在室温下进行操作;工艺用水可以做到全部循环使用,无溅洒和溢、漏的情况;生产中不会产生热浸镀时因高温造成的燃烧烟尘、有害气体、金属蒸气和助镀剂挥发出的氯化氢、氨气等,也没有电镀时电解槽上方有害气体的挥发,操作环境较好。因此,机械镀锌是切实可行的清洁生产技术[51]。
4)成本低 机械镀锌操作方便,设备简单,投资少,见效快。在加工成本上与电镀锌相比,当镀层厚度小于12.5μm时,电镀比机械镀稍占优势,但相差不大;随着镀层厚度的增加,机械镀锌的优势逐渐表现出来,当厚度达30μm时,电镀与机械镀的成本之比约为1.8∶1[52]。
(2)机械镀锌工艺的应用 一般长度小于300mm,质量小于0.5kg的工件适合于机械镀锌,再大些的工件虽然也可以加工,但会因装载量少而增加生产成本。带有盲孔和深凹槽的工件不适合于机械镀锌。适用于机械镀锌的金属制件包括射钉、环链、螺栓、螺母、垫片、装载机械五金、通信线路五金、航空五金、汽车五金等。另外,还有一些用热浸镀锌难以加工的小件也正在逐渐采用机械镀锌。
适用于机械镀锌的金属基体包括:碳素结构钢、低合金高强度钢、合金结构钢、弹簧钢、可锻铸铁、灰铸铁、粉末冶金件、黄铜铸件、青铜铸件、烧结铜件等。
本书所阐述的机械镀锌即为传统的机械镀锌,即前面提及的湿法机械镀锌,在本书各章节中均以机械镀锌提及。