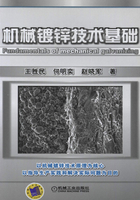
1.2 金属微粉涂镀工艺及特点
1.2.1 冷喷涂工艺
1.冷喷涂工艺的提出
冷喷涂(CS:cold spray)又称冷空气动力学喷涂(CGDSM:cold gas dynamic spray method或CGDS、CGSM)。20世纪80年代中期,前苏联科学院在用示踪粒子进行超音速风洞试验时,发现当粒子的速度超过某一临界速度时示踪粒子对靶材表面的作用从冲蚀转变为加速沉积,由此在1990年提出了冷喷涂的概念[6]。前苏联研究者Papyrin于1995年在美国召开的全美热喷涂会议上与美国学者开始联合发表相关研究结果[7],直到2000年在加拿大召开的国际热喷涂会议上才组织了专门的讨论会,由此在国际上引起了广泛的关注。近几年来美国与德国一部分研究机构也开展了冷喷涂技术的研究工作[8]。
2.冷喷涂的基本原理
冷喷涂是基于空气动力学原理的一种喷涂技术[9],其原理如图1-1所示。冷喷涂是利用高压气体通过缩放管产生超音速流动将粉末粒子从轴向送入高速气流中,经加速后,在完全固态下撞击基体,通过较大的塑性流动变形而沉积于基体表面上形成涂层的。为了增加气流的速度,从而提高粒子的速度,还可以将加速气体预热后送入喷枪,通常预热温度小于600℃。
图1-1 冷喷涂原理示意图[10]
冷喷涂过程中,高速粒子撞击基体后,是形成涂层还是对基体产生喷丸或冲蚀作用,或是对基体产生穿孔效应,取决于粒子撞击基体前的速度。对于一种材料存在着一定的临界速度υc,当粒子速度大于υc时粒子碰撞后将沉积于基体表面;当粒子速度小于υc时,将发生冲蚀现象。υc因粉末种类而异,一般为500~700m/s[10]。
影响冷喷涂过程中粒子沉积特性的主要因素包括气体的压力、温度、种类,粉末的种类与粒度,以及喷枪结构等。在其他条件一定的情况下,气体的种类、压力及温度主要决定了粒子的速度,粒子速度的大小决定了其沉积特性。如前所述,只有当粒子速度超过临界速度υc时,才能在碰撞基体后实现沉积;否则将对基体或涂层产生冲蚀效应。
3.冷喷涂层的结合机理
关于冷喷涂涂层的沉积过程行为,一般认为,高速粒子撞击基体时粒子的动能使粒子与已形成的涂层或基体产生较大的塑性变形,从而结合在一起实现粒子的沉积。冷喷涂镀层虽然是高能量冲击镀层,但镀层主要由金属颗粒组成,颗粒之间存在明显的界线,并且镀层中存在一定的空隙,镀层内金属颗粒之间为机械式物理结合。例如,文献[11-13]中观察到金属粒子撞击经抛光的基体后的扁平粒子和基体侧凹坑,这表明粒子和基体发生了明显的塑性变形。T.H.Van Steenkiste[14]利用铝粉、铜粉喷涂时发现镀层中存在明显的颗粒界面,同时还发现金属粉末的喷涂过程基本不发生氧化,即使是利用空气作为携带气体介质,金属粉末的氧化也非常少。Hamid Assadi[15]认为,冷喷涂形层过程中金属颗粒没有被明显加热,涂层中金属颗粒之间的结合仅仅是依靠冲击所产生的能量造成的机械锚合,结合牢固与否主要是由金属颗粒的冷喷涂临界速度决定的。然而也有人认为,粒子撞击到基体上时可能产生较大的冲击波,使被碰粒子与相邻粒子在界面处的局部温度达到材料的熔点以上而造成局部熔化,进而达到局部的冶金结合[8,16,17],并认为该过程与爆炸焊的过程类似。近两年来,人们通过大量的研究认为,冷喷涂涂层之间的粒子结合以机械咬合为主,同时有部分冶金结合[18-20]。
4.冷喷涂的应用
冷喷涂主要用于喷涂具有一定塑性的材料,比如纯金属、金属合金、塑料及复合材料等,特别是由于粒子加热温度低,基本无氧化,适用于对温度敏感(纳米、非晶等)、对氧化敏感(Cu、Ti等)和对相变敏感(金属、陶瓷)材料的涂层制备。由于高速粒子碰撞时对基体或涂层表面强烈的喷丸效应,涂层内一般处于压应力状态,有利于沉积厚涂层;而且由于粉末没有经历明显的热过程,基本不发生组织结构的变化,未沉积的粒子可以回收利用。为了获得高的粒子速度与沉积效率,要求粉末颗粒粒度及其分布范围要小,一般为1~50μm[21]。迄今的研究表明,冷喷涂多用于制备有一定塑性的纯金属与合金,如纯金属A1、Cu、Fe、Ni、Ti等,不锈钢、青铜等合金,也可以制备NiCr基高温合金等。通过控制气体预热温度也可以制备金属陶瓷(如Cr2C3-NiCr)等涂层,还可以制备有机高分子材料涂层及金属基复合材料涂层。随着冷喷涂技术的不断发展,人们也在尝试用冷喷涂制备纳米结构陶瓷涂层,实际上已有研究表明,在低压气氛下完全可以进行微纳米氧化物陶瓷颗粒的沉积,尽管对沉积机理尚不清楚[10]。但利用冷喷涂在低温下成功制备锌防护层的研究甚少[14,22]。
1.2.2 轧制镀工艺
1.轧制镀的提出
粉末轧制镀(plating powder and rolling method)全称为金属粉末—板带复合轧制镀,英文缩写为PPR法,是昆明理工大学在20世纪90年代研究开发的一项制备双金属复合薄板的新技术。该技术的主要工艺特点是:以一种金属为基材,在其表面覆上另一种金属粉末,通过将两者共同轧制和适当的后处理工艺,形成金属复合板带,板带表面金属轧制覆盖层的厚度可以控制在100~2000μm的范围内[23,24]。
2.轧制镀的工艺过程
(1)表面预复合 将选定的基材进行表面活化处理后,通过特殊工艺在其表面沉积一定厚度的金属粉末。
(2)复合轧制 将经表面预复合的板带进行复合轧制,其目的是进一步强化覆层与基材的结合,改善复合板带材的表面质量,实现产品规格所需的最终几何尺寸。
(3)扩散处理 对轧制后的板材进行扩散处理,确保覆层与基材实现冶金结合。
3.轧制镀的原理
粉末轧制镀与传统双金属带复合轧制相同,金属在轧制力作用下的变形可分为滑动变形和粘结变形,如图1-2所示[25]。在滑动变形区(Ⅰ区)内,粉末颗粒与轧辊、粉末颗粒与基材、粉末颗粒与颗粒之间均发生相对滑动,这种滑动促使金属粉末颗粒外表面包裹的氧化膜破裂甚至脱落。在轧制力作用下,较大直径的粉末颗粒开始发生延展变形,较小直径的粉末颗粒通过滑动填充到大直径颗粒的间隙中。在金属粉末颗粒尚未压紧变形之前,金属颗粒的变形是均匀向四周延展的。随变形量的增大,粉末颗粒逐渐变扁、展宽,彼此接近,间隙越来越小,最后相互焊合连接成一体。进入粘结变形区(Ⅱ区),已延展成一体的金属粉末与钢铁基体发生粘结,完成板带表面金属粉末镀层的轧制过程。
图1-2 PPR法复合过程金属变形示意图
用PPR法制备金属复合板带的轧制过程是一种不同于单一板材或板材叠轧的工件不对称轧制。在轧制力的作用下,粉末由疏松的颗粒状延展成致密的片状,并与金属基体结合成一体,粉末的变形与轧制力的大小有关,并直接影响复合板材的质量,而轧制压力又受粉末材料的特性、覆层厚度、颗粒大小的影响。另外,轧制过程中的摩擦力也对轧制压力有影响[25,26]。
4.轧制镀层的结合机理
在粉末轧制镀过程中,金属粉末颗粒在延展变形、连接成片的同时还对基材产生挤压作用,致使基材金属表面粗化,并与延展成片的粉末颗粒覆层紧密地“冷焊合”在一起完成复合过程,经过后续的扩散退火热处理,使镀层和基体之间达到扩散结合[27-28]。
5.轧制镀的应用
至今,利用粉末轧制镀已成功地开发出铜-钢、黄铜-钢、铝-钢、钛-钢、不锈钢-钢、银-钢等表面复合金属板带材,其中铝-钢粉末轧制复合材料已经用于卷帘门等领域的工业生产。
1.2.3 无机水性金属微粉涂层工艺
1.无机水性金属微粉涂层的提出
以富锌漆和达克罗涂层等为代表的技术直接利用非铁金属粉末参与形层,涂层防护功能强,形层过程无污染,逐渐引起人们的广泛关注。非铁金属粉末与有机或无机的粘结剂配制成涂料,刷涂或喷涂于工件表面,然后自然风干或加热烘干,形成涂层,例如有机富锌漆、无机富锌漆、达克罗涂层[29]、交美特涂层[30,31]等。这些涂层技术的共同特点是,金属粉末在各种粘结剂和添加剂的作用下,通过物理或化学的作用,金属粉末直接参与形层,而无重熔、再结晶过程。据此,何明奕等人[32,33]提出了金属微粉涂层的概念,即金属微粉涂层是采用非铁金属微粉,加入其他无机金属盐、有机或无机添加剂,以及表面活性剂和其他添加剂,采用喷涂、刷涂或其他机械力的形式,使金属微粉直接参与形成表面涂层的一种表面处理技术。
2.无机水性金属微粉涂层形成原理
水性金属微粉涂层制备工艺涉及种类多,如富锌漆涂层、水性锌-铝复合涂层、达克罗涂层(锌铬膜涂层)、交美特涂层等。但其形层原理有着共同的特点:采用片状(或微细颗粒状)锌粉或铝粉、无机金属盐水溶液、有机或无机还原剂混合成浆料,加入表面活性控制物质或其他添加剂,配置成水性金属微粉涂料,经过喷、涂、浸等工艺涂覆于工件表面,然后经过低温烧结或自然固化形成金属基涂层。水性金属微粉涂层的防护机理主要有三:其一是物理屏蔽作用,涂层阻止腐蚀介质渗透到基体表面;其二是涂层中部分添加剂起到缓蚀剂的作用,比如涂层中添加铬酸盐或铬酐,涂层固化或形成过程中溶出铬酸根离子,其强烈的氧化作用使金属表面钝化,从而产生优异的耐蚀性;其三就是涂层的阴极保护作用,大部分水性金属微粉涂层中的锌粉(或锌基合金粉、锌铝混合粉)的质量分数可高达80%以上,从而保证了锌粉/锌粉之间及锌粉/钢基材之间良好的导电性,当水分侵入到涂层内,锌粉和钢基材之间即形成微电池,由于锌的电化学电位比铁负得多,所以就从锌粉向钢铁流过防蚀电流,从而对钢铁起到阴极保护作用。
3.无机水性金属微粉涂层的结合机理
水性金属微粉涂层形成过程一般是在低温甚至室温下进行的,即使有的涂层制备工艺采用后烧结固化操作,但涂层和基体之间一般仍以物理结合为主,涂层/基体界面不存在冶金过程或扩散过程。在涂层内部,因为涂料中添加了粘结剂或烧结过程部分金属盐起到粘结剂作用,致使金属微粉颗粒相互之间结合在一起,构成涂层主体[34]。
4.无机水性金属微粉涂层的应用
水性金属微粉涂层因具有环境友好、高强度件不产生氢脆、耐蚀性好、涂覆渗透性好等优点,被广泛应用于大型钢结构、汽车制造、家用电器、小五金件等防腐领域,而且其应用已扩展到船舰等领域[35]。