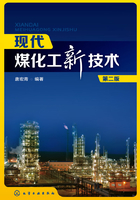
3.4 气化后续流程
3.4.1 后续流程的含义
正如前面所说,煤气化技术包括备煤、气化炉和后续流程三个部分。后续流程有激冷流程和废热锅炉流程两种形式,两者后面都可以有洗涤过程。
气化炉后面跟什么样的后续流程,与气化炉无关。在以前有一些讨论中,比较两者气化工艺时,把Shell气化炉与废热锅炉作为固定搭配,把水煤浆气化与激冷流程作为固定搭配,这是误解。国内就有水煤浆搭配废热锅炉的流程,也有下喷粉煤气化搭配激冷流程的。因此,我们应该将这件事作必要的解释:气化炉是气化炉,后续流程是后续流程。
这里用粉煤气化来解释这个问题。
3.4.2 后续流程介绍
(1)激冷流程简述 用N2或CO2输送的粉煤、高压氧气/水蒸气经过喷嘴混合,在1400℃高温及操作压力约3~6MPa的条件下自上而下地喷入气化炉,煤粉中的碳与氧发生部分氧化反应,生成以CO、H2、CO2为主要成分的粗煤气。见图3-3。

图3-3 下喷式煤气化激冷流程图
高温煤气夹带着未完全反应的碳粒及少量熔渣颗粒并流向下,经气化炉下部的出气口进入激冷器。在激冷器中高温煤气与激冷水充分接触,使煤气降温冷却并饱和,煤气降温、熔渣固化。固化后的熔渣和未反应的碳粒进入激冷器下部的渣罐定期减压排出。
冷却后的煤气和激冷水由激冷器流入气水分离器,分离器下部的灰水经减压后去沉淀池进行灰水处理,上部出来的煤气进入文丘里后进入洗涤塔,在塔中用逆流水洗涤,经洗涤脱除煤气中的灰后气体进入下游的变换工序,洗涤后的碳黑水除去碳颗粒后送入处理系统。见图3-3。
激冷流程中粗煤气的水蒸气含量约为50%~60%,适合于进入后续的变换工艺,因此激冷流程主要用于煤化工项目,作IGCC用是不合适的。
(2)废锅流程 用N2或CO2输送的粉煤、高压氧气/水蒸气经过喷嘴混合,在1400℃高温及操作压力约3~4MPa的条件下,自下平喷喷入气化炉,煤粉中的碳与氧发生部分氧化反应,生成以CO、H2、CO2为主要成分的粗煤气。
由反应室顶部出来的气体,被来自后续工序的合成气冷激至900℃左右,使其中飞灰固化。然后通过输气管、气体返回室和废热锅炉(合成气冷却器)内的膜式水冷壁冷却至330℃左右,同时产生高压或中压蒸汽。
上述粗合成气流中所夹带的灰分颗粒通过旋风分离器和陶瓷过滤器分离清除。分离后的气体中的一部分通过循环压缩机返回反应器顶部的输气管作冷激气源,另一部分进入文丘里除尘器和煤气洗涤塔,进一步除尘,送至后续变换工艺。
气化炉中的大部分渣以熔融状态从反应室锥形底部流入渣池,经灰水淬冷形成均匀的玻璃状颗粒,经破渣机借助一个锁斗系统送出界区。见图3-4。

图3-4 废热锅炉工艺流程图
气化炉原理与激冷流程采用的气化炉大体相同,区别在于煤粉喷射的位置,下喷式气化炉采用侧壁烧嘴,位于气化炉下部,并且可根据气化炉能力由4~8个烧嘴呈中心对称分布。
(3)后续流程比较
①投资。过去这个问题有许多比较并不在一个平台上,即一个是水煤浆气化,另一个是粉煤气化,比较的数据就不一定可靠。假如我们都在粉煤气化的基础上讨论问题,不同流程的投资差别比较明显,见表3-4。
表3-4 不同后续流程投资的比较(不含空分)

①GSP、HT-L、CROLIN中最低者。
②能耗。这是指整个装置的能耗,不是单独气化的能耗。单独比较气化的能耗是不够的。
气化后续流程是整个流程中的一部分,在气化得到或损失的能量,要看在后面全部工序中能否补充回来。在同样原料不同的设计中,动力系统(蒸汽平衡)十分重要,蒸汽平衡做得好,全系统的能耗就低。因此,单独讨论气化炉和废热锅炉能回收多少能量是没有意义的。
采用废锅流程可以回收干煤气显热,产生的蒸汽部分参与动力系统的蒸汽平衡,部分回到粗煤气中,用以保持一定的水汽比(H2O/干气),同时消耗一定量的蒸汽,用于循环压缩机。
这部分蒸汽约占废锅回收蒸汽的多少,视气化温度和产品的性质而定。对于制氢来说,大约只能多回收10%~20%。
这个问题就显得复杂了,在同样原料、同样产品和同样规模的情况下,如果作全流程的模拟计算,优化蒸汽平衡,废锅流程和激冷流程的吨产品能耗应该差别不大。
甲醇工艺和合成氨工艺有区别,甲醇工艺的低位能比较富裕,可以用这部分能量来节水,并没有浪费。
③运行周期。有关Shell废锅流程运行时间的问题,已经讨论很久。在这个问题上,质疑者和支持者的意见相左。近年来国内引进的Shell废锅流程,已经在线生产的有23台,按照投煤量分三个档次,1000t/d的有4台,2000t/d的有12台,2800t/d的有7台,在建的还有几台。
经过国内企业多年的努力,Shell废锅流程的技术日趋成熟。
从目前国内开车的情况来看,1000t/d档次的工艺运行得比较好,已经达到设计能力,主要表现在年运行时间在8000小时,年投煤负荷达到100%。从设计角度来说,可以说是达到设计要求。
2000t/d档次的运行逐步达到设计能力,表现在年运行时间在7000~8000小时左右,年投煤负荷在90%~100%。从化工设计角度来说,可以说是基本达到要求。
2800t/d档次的数据没有公布,或者说没有测定或不具备测定条件,因此不能认为已经达到设计能力。
不要把投煤量1000t/d工艺装置的数据强行推广到投煤量2800t/d的工艺装置上,装置规模越大,问题越多。整个流程运行周期短的原因是多方面的,这是煤气化后续流程太复杂造成的,规模越大,越容易出问题。这个规律在化工中是可以理解的,因为处理固体在化工中很麻烦,更何况是压力比较高。要提高运行周期,应该简化气化炉后续流程,走激冷流程是理想的选择。简化气化流程以后,发生运行问题的可能性就会下降,运转周期就会提高。
④后续流程的选用讨论。在作了上述讨论以后,我们认为最好采用下喷式激冷流程来实现化工上需要的煤气化。从上面的分析来看,在节能、运行周期上没有明显优势的情况下,花巨大的投资采用废热锅炉流程,没有多大的必要。
化工上由于H2/CO的客观需要,通常后续流程采用激冷流程,自然地在粗煤气中补充了水蒸气,水气比高一些,对变换也有利一些。这样的流程很简单,投资也比较低,设备制造也很容易,是化工上经典的流程。
发电上采用废热锅炉流程有其合理一面,它不需要在后面补充水蒸气,可以充分利用粗煤气中的热量,产生高中压水蒸气用于发电,合成气本身再用于发电。这就是IGCC想法,也是有道理的。
煤气化技术有两个用途:发电与化工。发电是发电,化工是化工,两者各自面向后续流程,应该各自取舍。煤气化的后续流程有激冷流程和废锅流程。这个问题极其重要,但是被人忽视。
废热锅炉流程主要用于发电,激冷流程主要用于化工。
发电用的是煤的能量,因此气化炉后煤的能量一部分直接转化为中压水蒸气,另一部分能量转化为可燃气体CO、H2、CH4,然后进行燃烧取得能量,最终产品为CO2和水蒸气。显然,发电用的煤气化后应该采用废热锅炉来达到这个目的。
化工煤气化的本质是获取化学物质,主要是以合成气CO、H2和水蒸气为主的化学物质形态。为了后续的化学反应需要,这三种物质要保持一定比例,在此基础上,适当利用这三种物质具有的能量。显然,煤气化后应该采用激冷流程来达到这个目的。
近期,国内业者在看到国外的新技术时,总希望把发电上用的流程移到国内的化工上来,这与国内从事电力的企业来扩展化工业务有关。在这里提醒一句:发电上需要的是能量,化工上需要的是物质,它们是有区别的,具体问题请具体对待。
⑤激冷流程的历史。最近,国外某公司散发材料,说激冷流程没有工业实践经验。这说明国外公司在推广废锅流程时,采用了商业化宣传的手法来误导国内业者。
了解激冷流程的历史,也许对我们发展煤化工有好处。激冷流程不是今天的新事物,在我国化工中的应用有悠久的历史。
在20世纪60年代,激冷流程已经在重油气化工艺中使用。典型代表是60年代从意大利蒙特卡提尼引进重油气化技术,在国内兴平、鲁南、刘家峡建设三个合成氨装置。后来气化用油变稠,成为渣油气化。90年代,鲁南和渭河从Texaco引进水煤浆气化技术,激冷流程亦在其中,水煤浆技术从此得到推广。
尽管在使用过程中发生各种问题,但是最终都让中方克服,成为今天成熟的技术。国内的煤化工行业对于激冷流程已经得心应手,特别是烧嘴的使用、维修、更换都已经轻车熟路。
激冷流程的工艺主要是气化炉(包括烧嘴)、激冷室、文丘里和洗涤塔四个部分组成。后三者造价低廉、操作简单,是这个技术得以推广的原因。近年来国内的研究在气化炉的形式上推陈出新,例如多喷嘴、两段氧化、内冷壁等,后续激冷流程没有也未必需要重大的革新。
国内在激冷流程上的丰富知识和经验,值得国外同行好好学习。
在化工上,从节省投资和提高运行率出发,气化后续流程采用激冷流程是合情合理的,激冷流程是成熟技术。