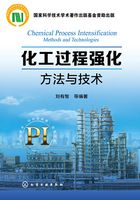
第1章 气液过程超重力化工强化技术
多相流之间的传递过程与反应是化学工业及许多相关领域中的一个基本过程,而对于气-液两相流体的相间传递过程,使用最为普遍的传质设备是塔器设备,包括板式塔、填料塔、喷淋塔等,这些操作均是液体流动靠着重力作用从塔顶向塔底流动,是在重力场下完成的,液相的流动主要是受重力作用的影响,由于重力加速度g是一个不能改变的有限值,这也就从宏观上决定了液体的流动基本行为。即在传质设备中液相流体以较厚的流体层缓慢流动,形成相间传递面积更新频率低和传递面积较小的状态,使相间的传递速率受到限制[1]。
利用离心力场强化传质过程的思路最早可追溯到20世纪初期。1925年,Myers和Jones制作了最早的带有转动体的锥形截板式蒸馏柱;1965年,Vivian等曾用试验研究离心力场对气体吸收的影响,试验利用由陶瓷鲍尔环填料构成的转子测试了CO2在水中的溶解情况,发现液相体积传质系数随着离心力呈0.41~0.48次方的变化关系;1976年,美国在太空进行的气-液两相间的传质试验表明,在完全失重的条件下,气液间传质无法实现;受此传质试验的启发,在20世纪70年代末,英国帝国化学工业公司(ICI)以Ramshaw教授为首的课题组[2]经过数年的研制,设计出了新型的传质设备——超重力装置亦叫旋转填料床(Rotating Packed Bed,RPB)或旋转床或超重机,并且在旋转填料床内做了一系列气液化工分离单元操作,并发表了名为“Higee”(High“g”)的许多技术专利,逐渐形成了“超重力强化传质”的概念。这一研究成果促成了超重力分离技术的诞生,随后引起了美、英、中、印等国的应用技术研究和开发热潮,相关的专利、文章和成果每年呈上升趋势。
自超重力概念提出以来,其研究领域主要集中在精馏、吸收、解吸等类似塔设备所涉及的化工单元过程中的气液接触方面,同时在其液相流体的流动形态、气相流体力学等基础理论方面的研究也取得明显的进展。特别是近十多年来,随着研究的深入,逐渐将研究领域拓展到气-液传热、液相高聚物脱挥、多相分离(除尘、除湿)、化学反应等化工单元过程的气液传递方面。
本章集中讨论超重力技术对于气-液化工过程的强化,从阐述超重力环境的液体流动形态和气相压降等有关流体力学性能开始,介绍超重力吸收、超重力解吸、超重力精馏、超重力气液反应和超重力气液直接换热的基本原理、超重力过程强化特性及研究进展情况。
1.1 气-液超重力技术简介
1.1.1 超重力技术概述
1.1.1.1 基本概念
超重力是指在比地球重力加速度大得多的环境下,物质所受的力(包括引力或排斥力)。研究超重力环境下的物理和化学变化过程的科学称为超重力科学。利用超重力科学原理而创制的应用技术称为超重力技术[1]。超重力技术作为过程强化的新型技术,在工业上有着广阔的应用前景。
气液两相流体在旋转的填料床中进行接触和反应,旋转填料床体系是一个非惯性体系,由于流体微元受到惯性力(也就是通常说的离心力),其大小与流体微元质量、旋转角速度和所处的半径位置有关系。由于气体微元质量小,所受的惯性力就小,气体在克服这种惯性力作用下,沿着惯性力的反方向通过旋转填料;而液体微元质量较大,所受的惯性力就大些。从这个意义上来讲,液体微元在通过填料时其形状和大小不仅在不断变化,而且在惯性力作用下,液体由转子的内圆沿直径方向通过旋转填料。
由于惯性力实际上并不存在,实际存在的只有原本将该物体加速的力,对填料旋转来说,就是由电机作用于转轴的力来加速其运转的。因此惯性力又称为假想力。概念的提出是因为在非惯性系中,牛顿运动定律并不适用。但是为了思维上的方便,可以假想在这个非惯性系中,除了相互作用所引起的力之外还受到一种由于非惯性系而引起的力——惯性力。
旋转填料床体系就是一个非惯性体系,在这个体系中,流体微元受到了惯性力(离心力)的作用。如果把任一瞬间物质在旋转体内各点所受的惯性力分布总和,称为惯性力(离心力)场的话,因为惯性力是不存在的,那么这个惯性力场就是模拟的力场。在这个惯性力场中的加速度,就是离心加速度G,即:G=rω2。式中,ω为转子旋转的角速度,1/s;r为转子的半径,m。
如果这个离心加速度(G)大于重力加速度(g),这个惯性力场也就称为超重力场。即:G=rω2>g,式中,g为重力加速度(9.8m/s2)。
从这里可以看出,惯性力加速度是可以靠调节角速度来改变其大小的;在相同角速度条件下,离转动圆心越远,惯性加速度就越大。只要将靠近转轴处的惯性加速度调节到大于重力加速度,就可以保证整个旋转填料床内的各处均处于超重力场的环境。
根据化学工程的研究方法,可以用无量纲参数(即无因次数)来表达超重力场的强度,以便于不同尺寸、不同转速的旋转填料床进行对比。把惯性加速度与重力加速度之比称为超重力因子,用β来表示。超重力因子的表达式为:
(1-1)
将有关数值代入,超重力因子可以简化为:
(1-2)
式中 ω——转子旋转的角速度,1/s;
r——转子的半径,m;
N——转子旋转的转速,r/min。
当转速一定时,超重力因子随转子的半径呈线性变化,表现为沿径向方向超重力因子呈线性增大,如图1-1所示。

图1-1 填料层内超重力场沿径向的分布
r1—旋转填料的内径;r2—旋转填料的外径
由于超重力场强度沿径向存在一定的分布,为使用方便,通常用平均超重力因子来描述超重力场的强度。实际上,超重力场具有立体结构分布场的性质,当转子中的填料在轴向均匀分布装填情况下,超重力场可以看成是一个平面的分布场。超重力场强度的平均值就是其面积平均值:
(1-3)
实际上,超重力因子就是表达模拟力场的加速度是β倍的重力加速度,为此,也可称为“超重力数”。这是一个无量纲数,可以使人们看到事物的本质,更便于分析比较在不同尺寸设备和不同转速条件下的数据。超重力因子也可理解为质量相同的流体微元受到的超重力(mG)与重力(mg)之比。
如此看来,超重力场是由旋转而产生的离心力场来进行模拟的,也可以看成流体微元处于超重力场的环境,受到了超重力的作用。流体在超重力场所受的力要远比重力场中大得多,流体的流动和形态发生了根本的变化,流体微元的形成速度更快,瞬间即逝,流体微元的尺度变得更小、更纤细,表面的更新速度更快。
1.1.1.2 超重力装置(旋转填料床)的技术特点
旋转填料床中气液两相的传质过程是在超重力场中进行的,与重力场中的填料塔、鼓泡塔以及筛板塔等传统塔设备相比,旋转填料床具有以下特点[1,3]:
①强化传递效果显著,传递系数提高了1~3个数量级;
②气相压降小,气相动力能耗少;
③持液量小,即生产过程在线物料存量少,提升生产的本质安全,适用于昂贵物料、有毒物料及易燃易爆物料的处理;
④物料停留时间短,适用于某些特殊的快速混合及反应过程,有利于用于控制某些反应的选择性;
⑤达到稳定时间短,便于开停车,便于更换物系,易于操作;
⑥设备体积小,成本低,占地面积小,安装维修方便;
⑦既易于微型化适用于特殊场合,又易于工业化放大;
⑧填料层具有自清洗作用,不易结垢和堵塞;
⑨应用范围广、通用性强、操作弹性大。
1.1.2 气-液超重力装置的结构与类型
超重力装置结构主要包括转子、液体分布器和外壳等[4]。超重力设备可分为单轴结构和双轴结构,其中单轴结构按气、液接触构件的结构形式可分为旋转填料床(逆流、错流和并流)和折流床,双轴结构分为SP-RPB和CAS-RPB。
1.1.2.1 单轴结构
(1)旋转填料床
旋转填料床(如图1-2所示)在转子内装载大量填料作为相间接触构件。填料由转子装载和固定,装填的填料可以是规整填料,或是随意堆积的散装填料,也可以是按某种结构设计的形状等,填料在动力驱动下进行高速旋转。液体从液体分布器均匀喷洒在填料内缘,在填料高速旋转产生的离心力作用下,以液滴、液丝和液膜的形式由填料内缘沿径向向外流动。气体在压力作用下穿过旋转的填料层,与液体在填料表面和内部进行密切接触。填料不仅为气液接触提供较大的传质表面[5],还通过高速旋转来改善气液分布、增强气液的分散及混合效果,为提高过程的传递效率、减小流动阻力及特殊产品的制备提供了重要支撑。

图1-2 超重力装置结构示意图
1—气体进口;2—转子;3—填料;4—超重力装置内腔;5—液体进口;6—气体出口;7,12—密封;8—喷嘴; 9—超重力装置外腔;10—外壳;11—中央分布器;13—转轴;14—液体出口
按照旋转填料床内气、液接触的流动方式,可以将旋转填料床分为逆流旋转填料床、错流旋转填料床和并流旋转填料床三类[6]。
a.逆流结构。逆流结构的旋转填料床如图1-3所示,在旋转填料内气、液两相呈逆流接触,即液体经液体分布器均匀喷淋到填料内缘,在离心力的作用下,沿填料的表面或间隙呈液滴、液丝或液膜的形式流向填料外缘,碰到静止的器壁后落下,从位于底部的液体出口排出。气体从气体进口进入,在压力的作用下,由填料外缘进入旋转填料床,与液体在填料内逆流接触后通过填料层进入填料内缘,后从位于填料中心气体出口排出。

图1-3 逆流结构旋转填料床示意图
逆流结构的旋转填料床以丝网填料和碟片填料旋转床[7]为代表,结构如图1-4和图1-5所示。在此过程中,由于强大的离心力的作用,液体在高分散、强混合及界面快速更新的环境下与气体充分接触,极大地强化了传递和反应过程。

图1-4 丝网填料逆流旋转床示意图

图1-5 同心环碟片填料逆流旋转床结构示意图
b.错流结构。错流结构的旋转填料床如图1-6所示,在旋转填料内气、液两相呈错流接触,即液体经液体分布器均匀喷淋到填料内缘,在离心力的作用下,沿填料的表面或间隙呈液滴、液丝或液膜的形式流向填料外缘,碰到静止的器壁后落下,从位于底部的液体出口排出。与逆流旋转填料床不同,气体由气体进口引入后,在压力作用下,由填料下端轴向穿过旋转填料床,其间与液体在填料内呈错流接触,后由填料上端穿出,再从位于壳体上端的气体出口排出。相比逆流旋转填料床,错流旋转填料床不存在液泛问题,而气体的液沫夹带问题很容易通过在液体喷淋段后面增设捕沫段得到解决。因此,错流床适合高气速下操作;除此之外,在正常通气情况下,床内液体无明显轴向分散,液体的轴向返混很小,因此,错流旋转填料床具有更广泛的工业应用价值。

图1-6 错流旋转填料床的结构简图
如图1-7所示是由北京化工大学[8]开发研制的一种卧式错流旋转填料床。液体由空心轴进入,在转子的喷淋段沿径向喷出与轴向流动的气体错流接触后被抛到外腔,然后由设备底部液体出口排出;气体由气体进口进入,经过叶轮增压后进入填料层与液体错流接触,然后沿轴向通过除雾段,最后从气体出口离开。

图1-7 卧式错流旋转填料床结构简图
如图1-8所示是由中北大学开发研制[9]的一种立式错流旋转填料床。其特点在于填料分上下两层设计,转子固定在与轴相连的中隔套上,在电机的带动下旋转。气体自气体进口进入,沿轴向自下而上通过下层填料后进入中隔套进行二次分布,再沿轴向通过上层填料,然后从旋转填料床的上部气体出口离开。液体从位于转子中心的液体分布器进入转子内缘,沿径向甩出,与沿轴向穿过填料层的气体错流接触,液体被甩到外壁后垂直落下,从液体出口排出。液体进料管共有四个,可通过单独使用或同时使用几个进料管来控制液体的最大进料量和进料位置。在仅仅使用下层的两个液体进料管时,上层填料可起到除雾的作用。

图1-8 两级轴向错流旋转填料床结构简图
c.并流结构。并流结构旋转填料床如图1-9所示[10]。气、液两相同时由填料内缘同向穿过填料层后到达填料外缘。填料在电机的带动下高速旋转,气体由气体入口管导入填料内腔,在压力作用下自填料内腔进入床层,经过填料进入外腔,从气体出口排出;液体由位于填料内腔的液体分布器喷洒在填料内缘进入床层,在高速旋转产生的离心力作用下,由填料内缘沿径向向外流动,碰到静止的机壳后落下,从位于底部的液体出口排出。在此过程中,由于强大的离心力的作用使得液体被雾化,液体在高分散、强混合及界面快速更新的环境下与气体并流接触。并流结构旋转填料床的操作虽然简单,但操作范围较小,分离效率不高,工业应用较少。

图1-9 并流旋转填料床的结构简图
应当指出,由于气相的流通路径的不同,气、液相的接触形式随之发生了变化,这会带来诸多流体力学、传质性能及工业应用上的差异。例如,在正常的操作条件下,由于气、液逆流接触,在相界面产生较大的相对滑移速度,提高了相际间表面更新速度,利于气液传质效果的提升,逆流旋转填料床具有明显的传质优势;与此同时,逆流接触会造成气体在流通过程中产生巨大的阻力,使得逆流旋转填料床的气相压降明显高于错流旋转填料床和并流旋转填料床,若将两相流接触形式由逆流改为错流,可以减轻液泛现象的发生,还可以使转子的直径减小到与气体管路的直径相当,达到减小设备体积、降低设备造价的目的。因此,错流旋转填料床在工业应用上表现出更广泛的应用价值。
(2)折流床
折流床(图1-10、图1-11)是在转子内设置一定数量规则排列的同心动、静折流圈,动、静折流圈之间的环隙空间提供了气液流动的曲折通道[11]。液体在动静圈之间经历了多次分散-聚集的过程,气体在折流通道内与液体呈逆流接触。折流式旋转床转子内气液的接触时间较长,因而单个转子的分离能力较旋转床有显著提高,且易于实现多层结构,从而成倍地增加单台设备的分离能力。折流床是一种气液接触效率较高、体积小的气液传质设备,有效地克服了旋转床中气液接触时间短的缺点,特别在精馏、吸收和化学反应等场合得到广泛应用。

图1-10 单层折流式旋转床的结构简图

图1-11 多层折流式旋转床的结构简图
1.1.2.2 双轴结构
旋转填料床作为一种新型高效的传质设备已有较多研究,普遍认为旋转填料床对传质过程中的液相传质系数的提高极为明显,但对于传质过程中的气相传质系数影响不大,基于强化气膜控制的传质过程,传统旋转填料床的结构研究者则提出了许多新型双轴结构旋转填料床以改善和强化对气膜控制的传质过程。
(1)分裂填料旋转床(SP-RPB)
在普通旋转填料床中的液相传质系数比传统塔有效地提高了数倍至数十倍,但对气相传质控制过程的传质系数与传统塔气相传质系数相当,这主要是由于旋转填料床中高比表面积填料对气体的曳力作用不足,造成气体与填料间的相对滑移速度较小,气体几乎随旋转填料床中的填料同步旋转,和传统塔一样以“整体”或“股”经过填料层,气体的湍动程度较小,相界面得不到快速更新,不能有效地强化气膜内的传质过程。而且传统单轴旋转填料床存在着液体分布不均的现象,使得气相传质过程得不到强化。为此,研究学者对普通旋转填料床转子结构进行改装以强化气相传质过程。其中最具代表性的为Chandra A等[12]提出一种新型双轴转子结构旋转填料床——分裂填料旋转床(Split Packing Rotating Packed Bed,SP-RPB),结构如图1-12所示。

图1-12 SP-RPB转子结构示意图
对SP-RPB机制进行分析可知,强化气膜控制传质过程是发生在相邻的两个填料环之间的环间隙内。当气体通过相邻填料环之间的环间隙时,会受到旋转填料对其产生的曳力作用而做切线运动,但由于其曳力作用十分有限,对气体切向流动的推动力不足,使得气体只能形成一定的扰动,在局部区域形成湍流,对气相传质过程强化起到一定的促进作用。但随着径向方向的气速不断增大,曳力作用引起的切向流速会明显降低,严重时将导致强化气相传质的机制逐渐失去作用。因此,仅靠填料的曳力作用促进气体湍动以及强化气相传质也是有限的;再者SP-RPB采用泡沫金属为填料,不易更换,机械强度不足,难以应用于大气、液通量的场合;靠近转子中心处的填料环半径较小,气体受到填料作用获得的切向速度较小,强化气膜控制传质过程的效果不明显。
(2)气流对向剪切旋转填料床(CAS-RPB)
中北大学刘有智教授[13]提出了另一种强化气膜控制传质过程的新型双轴结构——气流对向剪切旋转填料床(Counter Airflow Shear Rotating Packed Bed,CAS-RPB)[14]。其转子结构如图1-13所示。

图1-13 CAS-RPB转子结构及形体阻力件示意图
CAS-RPB的转子是由能独立旋转的上、下两个转盘组成。每个转盘上各固定若干个同心环状填料,每个同心环状填料的支撑框架为同心薄壁圆筒围成,周向密布开孔,作为流体的通道;这些支撑框架的薄壁圆筒外侧布局安装有流体力学的形体阻力件(凸出圆筒曲面),强化气体剪切作用;支撑框架的内部则是填料的装填区,可以装填不同的填料。当上、下转盘逆向旋转时,相邻的两个填料环呈相反方向转动,形体阻力件对气体产生巨大的剪切力,形成连续的涡流和强烈的湍动,以“整体”流动的气体被“破碎”,打破了传统旋转填料床中气体“股”的流动模式,使得气体与填料间的相对滑移速度增加,气体的湍动程度增强,气膜表面更新速率加快,传质阻力减小,从而有效地强化了气膜内的传质过程[15]。
旋转填料是由多个形体阻力件构成的圆环片组合而成,相邻的圆环片交替式分别安装在两个旋转盘上,圆环之间留有空隙,当两个旋转盘旋转时,相邻圆环片以相反的方向旋转。形体阻力件(图1-13)设置在圆环之间的空隙,旋转时将引起气体的剪切和边界层分离,强化气相的传质速率。形体阻力件是指多孔波纹圆环片型或两圆环间装入其他填料的圆环组件型,也可以是在圆环的圆周上安置类似风叶状的翅片型。填料边缘构建的形体阻力件,增大对气体的剪应力和形变速率,促进实现气体边界层分离,从而形成漩涡,实现气体的湍流,直至紊流运动,加速气体界面更新,达到强化气相传质的效果。CAS-RPB强化传质机制就是通过形体阻力件在填料环隙空间内创造气体边界层分离,形成漩涡,实现气体强扰动、高湍流,加速气体界面更新。改变形体阻力件的尺寸参数,增加气体曳力,在加速气体的切向速度的同时,加大气体剪应力和形变速率。
自CAS-RPB开发以来,研究者就对其基础性能及应用进行了研究:2013年,杨力等[16]对CAS-RPB内部气相流场进行了模拟计算,并与已有的分层式旋转填料床进行对比发现:CAS-RPB内气相湍动能较高,用扰流翅片作为形体阻力件能明显促进湍流,有利于相界面的快速更新,从而促进气相传质与微观混合过程。2015年,谷德银等[15]以CO2-NaOH体系考察了CAS-RPB的气相传质特性,研究结果发现CAS-RPB的气相体积传质系数比文献逆流结构的RPB提高36%,有效地强化了气相传质过程。2015年,张芳芳等[17]在CAS-RPB中以NaOH为吸收液脱除烟气中的SO2,考察了超重力因子、液气体积比、进气量等因素对脱硫率和气相传质系数的影响及循环次数对脱硫率和溶液pH值的影响,得到的最佳工艺条件为:超重力因子67,进气量55m3/h,液气体积比(1.1~1.3)×10-3。在该条件下,出口气体中SO2质量浓度低于100mg/m3,脱硫率稳定在约98.7%。CAS-RPB的开发,将超重力过程强化技术从原有的液膜控制的传质过程拓展到气膜控制的传质过程,有效弥补了超重力过程强化的局限性,丰富了超重力化工过程强化的理论与实践。
与SP-RPB相比,CAS-RPB具有以下特征:①转子的各个填料环外缘构建了多个形体阻力件。在各个填料环外缘上构建形体阻力件后,形体阻力件将会随着填料环同步旋转,增大对气体的剪应力和形变速率。与此同时,当气体进入CAS-RPB中的填料环间隙时,由于形体阻力件在填料环隙间的凸起,改变了原有的流体通道,气体在到达形体阻力件时因流通截面积变小而作加速减压运动,在流过形体阻力件之后就因流通截面积变大而作减速增压运动,这就产生了速度梯度和逆压梯度,使得形体阻力件附近产生了气体回流涡,从而促进实现气体边界层分离,形成气流漩涡,实现气体的湍流运动,直至紊流运动,加快气体界面的更新速率。此外,形体阻力件将电机所提供的动能传递给气体,除了弥补气体产生漩涡所消耗的能量外,还使得气体的湍动能增加,也使气液的流动轨迹更加蜿蜒曲折,停留时间也相应延长,气液两相得到充分的接触、混合和反应,从而达到强化气膜控制传质过程的效果。②采用填料支撑来固定填料,根据不同处理要求可以更换合适的填料,且机械强度增加,适用于大气液通量的场合。③填料环自由端采用迷宫式密封以此加强气体的密封效果。④在气体出口处构建了缓冲室,使其更容易解决液泛问题,运行更加稳定。
1.1.3 超重力技术强化气-液化工过程研究进展
超重力技术相比于其他常规技术具有成本和性能方面的显著优势,已经广泛应用于气体分离与净化、水处理、精馏和纳米材料制备等工业过程,在环境治理和资源回收方面发挥出重要作用。目前,世界上许多大的化学公司都在竞相对超重力技术进行开发研究,并进行了一定的中试或工业化运行,主要集中在以下几个方面:
1.1.3.1 超重力气体分离和净化技术
(1)超重力湿法脱除硫化氢
在河北某陶瓷企业实现工业化,采用中北大学超重力法脱除煤气中硫化氢,处理煤气量约为10000m3/h(标准状况),其中H2S含量1000mg/m3,工业化装置的转速仅为200~400r/min,处理后煤气中硫化氢可降低至15mg/m3以下,单级脱硫率可达到95%以上,替代天然气烧制陶瓷,年节约燃料费500万元。此技术同时在四川平武锰业、广西华银铝业等地实现工业应用,节能减排效果显著。
北京化工大学与中国海洋石油总公司等合作,成功将超重力脱硫技术应用于海洋平台天然气脱硫化氢工业过程,实现了油田天然气中H2S的深度脱除,效果显著。
超重力脱硫反应器设备体积仅约为传统塔的1/10或更小,体现出明显竞争优势。
(2)超重力脱除二氧化硫技术
火电厂排放的大气中含有大量的二氧化硫气体,传统湿法石灰石/石灰-石膏法烟气脱硫很难达标治理,且存在投资大、设备易结垢、堵塞、有二次污染等问题。
中北大学将湿法与超重力技术相结合,充分利用了湿法脱硫剂可循环使用、可回收二氧化硫资源与超重力技术投资小、脱硫率高的技术优势。采用超重力湿法脱除二氧化硫,强化吸收效果明显,在较低的液气比下,可获得99%以上的脱硫率,该技术具有脱硫效率高、液气比小、成本低、设备体积小、使用范围宽等优点。
北京化工大学与硫酸厂合作,采用亚胺吸收法进行了超重力脱硫的工业侧线实验,经过超重力设备吸收后尾气中二氧化硫含量降至100mg/L以下,若将单级超重力脱硫与喷射脱硫器相结合,可在设备投资、动力消耗、气相压降等方面较原有技术有较大优势。
(3)超重力净化硝烟技术
火炸药行业硝化过程中排放高浓度氮氧化物(俗称“硝烟”),污染严重、治理难度大。传统常压净化技术采用多级吸收但效果仍不理想,排放浓度5000mg/m3左右。
中北大学将超重力技术用于火炸药行业高浓度硝烟净化治理,创建了超重力常压净化高浓度NOx新工艺。采用该工艺后,当进口浓度为18000mg/m3时,通过两级深度净化吸收组合分解塔工艺,硝烟浓度可降到240mg/m3以下,NOx排放量削减了95%,达到了国家排放标准。相比现有塔设备成本可降低30%以上,节省投资75%,运行费用降低79%,为有效解决高浓度硝烟污染问题提供了新方法,具有良好的工业化应用前景。
与山西平朔煤矸石发电有限公司联合开发高效实用型(DN-A)CFB锅炉SNCR脱硝系统。此工艺采用超重力烟气气提方法,将质量浓度为20%~25%氨水中游离氨吹脱至气相中,含氨10%左右气体作为氮源加入到炉内脱硝,保证脱硝效率,减少危险源,实现本质安全。超重力吹氨设备处理氨水量为0.1~0.8m3/h,稀释空气用量为1000~2400m3/h,氨水吹脱率可达95%以上,NOx排放浓度小于100mg/m3,氨逃逸浓度小于8mg/m3。
(4)超重力湿法净化气体中细颗粒物技术
燃煤发电、化工、冶炼等固定污染源排放的工业废气中,含大量细颗粒物,难以被常规除尘器脱除。超重力湿法净化气体中细颗粒物技术复合了离心沉降、过滤、机械旋转碰撞、惯性碰撞捕获及扩散、水膜等多种细颗粒物捕集净化机制,切割粒径小、净化效率高、液气比小、压降低、能耗低,适于工业应用。
山西省超重力化工工程技术研究中心将超重力技术和湿法除尘技术耦合,应用于天脊兴化公司富铵钙尾气除尘,超重力除尘设备直径1.6m,高3.4m,气体处理量43000m3/h,液体循环量12m3/h,除尘效率达到了99.5%;在贵州开磷集团实现原料气的深度净化,处理后气体中尘含量低于10mg/m3;在新疆广汇新能源公司压缩机进口煤锁气除尘技术改造项目,2台超重力湿法除尘设备,单台处理气量21000m3/h,焦油煤尘去除率大于90%,年回收煤气2.3亿立方米,解决了煤锁气火炬燃烧排放造成的环境污染和资源浪费的行业难题。
(5)超重力脱氨除湿技术
硝酸磷肥行业排放的含氨含尘含湿尾气,气体成分复杂,氟化物易堵塞设备,难以治理。采用超重力旋转填料床实现了脱氨除湿一体化治理。在天脊集团实现工业应用,单台设备处理气量55000m3/h,脱氨率90%以上,除湿率56.4%,并推广应用于全球最大的缓控释肥生产基地——山东金正大公司,实现脱氨率92%以上,除湿率45.5%,两台超重力装置总处理气量达25000m3/h,温度降低到80℃,取得了良好的环境与社会效益。
(6)超重力脱除挥发性有机化合物
随着我国工业的快速发展,挥发性有机化合物(Volatile Organic Compounds,VOCs)排放到大气中,对人类健康和生态环境造成巨大的危害,随着人们环保意识增强,VOCs的治理也越来越受到重视。旋转填料床作为一种高效的传质设备,在治理挥发性有机化合物废气方面具有极大应用价值。
台湾工业技术研究院化学工业研究所开发的旋转脱气机,其液体处理量1m3/h,液体黏度小于0.01Pa·s,每米传质单元数大于25。研究表明,当气液比为25且转速为700r/min时,常温下脱除水中甲苯,脱除率可达95%以上;当气液比为63且转速为1200r/min时,液体预热至95℃则脱除水中丙酮物质,脱除率可达95%以上。
中北大学以旋转填料床为吸收装置,考察超重力参数对甲苯吸收率的影响,确定适宜的工艺操作参数。研究表明:旋转填料床用于吸收治理甲苯废气是可行的,且填料的润湿程度对甲苯吸收率有重要影响。在超重力因子为33.42,液气比为5~6.67L/m3,气体流量为6m3,在入口甲苯浓度为500ppm(1ppm=10-6)时,吸收率可达到74.2%左右。将旋转填料床应用于吸收治理挥发性有机化合物,可克服传统塔设备存在的压降大、设备体积庞大、开停车不方便等应用限制,具有灵活通用、使用成本低和占地面积小的优点,具有极为广阔的应用前景。
1.1.3.2 超重力水处理技术
工业废水存在危害大、难降解,成分复杂等问题,传统水处理方法很难使其达到排放标准。将超重力技术借助其高效传质的特点应用于废水处理,是一种既经济又有效的处理方法。
(1)氨氮废水处理
中北大学应用超重力技术在氨氮废水吹脱方面进行了研究,对某化肥厂铜洗工序的氨氮废水进行了处理,当进口氨氮废水pH值为10.5~11.5、处理量为20~50L/h、气流量为30~120m3/h时,氨的单程吹脱率高达85%。气液比为1200(是传统吹脱法气液比的1/4~1/3),由于床层压降较小,气体用量减少,能耗明显低于传统吹脱法。该项目被列入2002年度国家科技成果重点推广计划,科技部计划发展司授予“超重力法吹脱氨氮废水示范工程”的依托单位证书。
(2)超重力氧化技术
北京化工大学与中国石化石油化工研究院合作,以超重力机为氧化再生反应器,进行脱硫醇废碱液深度氧化反应与分离耦合的新工艺技术开发,并实现工程化,数月连续运行结果表明:新技术既能满足油品升级对高品质MTBE的生产要求,又实现了碱渣近零排放,为液化气深加工产业减轻环保压力,具有广阔的应用前景。
山西省超重力化工工程技术研究中心针对TNT红水具有成分复杂、毒性大、色度高、难降解,以及臭氧氧化技术受气液传质限制的特点,应用旋转填料床作为臭氧氧化气液反应装置,使臭氧溶于液相的效率极大提高,提升臭氧的利用率。该技术较传统臭氧氧化技术可缩短反应时间(减少约40%),节约臭氧消耗量(减少约30%),降低水处理成本(减少约45%)。
台湾工业技术研究院化学工业研究所采用超重力臭氧氧化技术去除水中COD,每小时处理量为300m3。试验将超重力装置与卷气式反应器进行了对比。结果表明,操作费用约减少48%,能源成本可减少37%。由此可见,超重力臭氧氧化系统除了具有高效率之外,其潜在经济效益亦非常可观。
1.1.3.3 超重力精馏技术
精馏是石油化工、炼油生产过程中一个重要环节,也是能耗最大的化工分离过程。对塔器精馏设备改进和研发,产生了明显的技术进步和经济效益。但化工行业仍面临着节能降耗、产业升级的需求,超重力精馏技术以其高效,低成本的特点逐渐成为一个新的研究热点。
浙江工业大学将超重力精馏技术应用于包括甲醇/水、乙醇/水、丙酮/水、DMSO/水、DMF/水、甲醇/甲缩醛/水、乙酸乙酯/水等的常规精馏过程,无水乙醇制备的萃取精馏过程,乙腈/水的共沸精馏过程,以及医药中间体分离、有机溶剂回收等过程,取得了很好的传质效果。
中北大学分别以乙醇-水和甲醇-水为体系进行了全回流精馏实验研究,得出了不同操作条件下的理论塔板高度。研究表明超重力装置的传质效率比传统填料塔高1~2个数量级,体积缩小为原来的1/10,而且操作稳定,不易液泛,具有广阔的应用潜力。
1.1.3.4 超重力强化气-液反应技术
(1)超重力纳米粉体制备技术
中北大学以CO2和NaAlO2为原料连续制备出粒径小于20nm的超细氢氧化铝,超重力技术的应用极大提高混合程度,缩短碳化时间,实现超细粒子的合成及改性一步工艺,该项目获得了山西省科技进步一等奖。
北京化工大学以CO2和Ca(OH)2为原料,采用超重力技术制备出平均粒径为15~30nm的纺锤形等多形态纳米碳酸钙,该项目已进行工业化推广。以四氯化钛和氯化钡为原料,以氢氧化钠溶液为沉淀剂,利用超重力反应器采用直接沉淀法制备了30~70nm纳米级立方相BaTiO3粉体。采用超重力反应器以NaAlO2溶液及CO2气体为原料,制备了平均直径1~5nm,长100~300nm的纤维状纳米拟薄水铝石。
(2)超重力卤化技术
溴化丁基橡胶(BIIR)广泛应用于轮胎、医用胶囊、防腐防化等领域,北京化工大学将超重力技术用于强化丁基橡胶溴化反应过程,研究结果表明,与搅拌釜反应器相比,反应时间可缩短至2min,用该技术制备的BIIR产品结构、性能指标均与市售的国际公司的BIIR产品指标相当,具有良好的工业应用前景。
1.2 超重力流体力学性能
流体力学性能是衡量超重力装置气液传递性能的重要指标之一,气液传质性能优劣、负荷的大小及操作的稳定性等很大程度取决于流体力学性能。流体在超重力场下的流体力学性能不能简单地用超重力场代替重力场而求取,超重力场下的流体力学性能比传统塔设备中更为复杂。超重力装置流体力学性能一般包括流体流动形态、压降、液泛及停留时间等。
1.2.1 液体流动形态
(1)液体在旋转填料中的流动状态
液体在超重力场中的流动状况十分复杂。国内外学者采用摄像机或高速频闪照相实验技术,直接观察液体的流动过程和流动状态。Burns和Ramshaw等[2,18]发现:在超重力场中填料的流动状态可以分为三种流动形态:孔流(Pore Flow)、液滴流动(Droplet Flow)、液膜流动(Film Flow),如图1-14所示。郭锴等发现液体在被加速时并非是一起被加速的,而是存在两种情况:一是当它们被填料捕获后,就达到与填料相同的速度;二是未被填料捕获的部分则保持原有的速度,大约经过10mm左右才全部被捕获,表明填料床存在端效应区。张军等[8]发现液体以液滴、液线和液膜三种形态存在于填料中,在填料内缘处,液体主要以液滴形态存在,在填料主体区,填料表面上液体主要以液膜形式存在。

图1-14 液体在填料中的三种流动形态
(2)液体在旋转填料中的分布状态
Burns采用高速频闪照相机对液体在填料中的不均匀分布问题进行了研究,结果如图1-15所示。液体在填料中的分布很不均匀,液体以放射状螺旋线沿填料的径向流动,向周向的分散很少。为考察液体在旋转填料中分布性,采用两个20mm的金属挡片垂直放置于液体分布器与填料内侧之间,将填料内圈一些部分用挡片挡住,使液体不能从此部分进入填料。结果发现:金属挡片沿填料外缘径向阻挡的这部分填料是干的,说明液体基本上是径向运动,而周向分散很小,见图1-16。

图1-15 液体在填料中的不均匀分布

图1-16 液体在填料中的不均匀流动
1—干填料;2—湿填料; 3—金属挡片;4—有机玻璃支架
1.2.2 气相压降性能
气相压降是衡量设备阻力大小和能量消耗的一项重要指标,是设备设计、填料选择等必须考虑的问题。超重力场下压降的产生依据受力的状态[19-21]可以分为:
①离心阻力即高速旋转的填料对气体形成剪切作用,对气体进行剪切变形,带动气体流动造成能量损失,这就是离心压降产生的主要原因。离心压降的大小与填料旋转的速度、填料形状、装填方式及空隙率等有关;
②摩擦阻力是指气体在流动过程中在填料表面和气液界面上产生的黏性曳力;
③形体阻力是由于气体通过的流道突然增大或缩小以及方向改变等造成的能量损失。
为便于对超重力场各种条件下的压降进行研究和比较,在此介绍几个有关压降的概念。超重力装置的气相压降特性有床层压降(Δps)、离心压降(Δpc)、干床压降(Δpd)及湿床压降(Δpw)、总压降(Δpt)等指标。
1.2.2.1 气液逆流操作的气相压降
以水-空气为研究体系,对逆流式超重力装置的气相压降进行实验测定研究,测压点分布如图1-17所示,点1设置在超重力装置气体入口处,点2设置在超重力装置气体出口处,点1-2所测的气相压降为总压降(Δpt);点3设置在超重力装置填料内侧,点4设置在填料外缘处,点3-4所测气相压降为床层压降(Δps)。在室温条件下,改变气体流量、液体流量及转子转速,待设备运转稳定后,测出对应段的气相压降。气相压降由U形管压差计测定,转速由光电转速测定仪测定,气液流量由转子流量计测定。

图1-17 逆流旋转填料床测压点分布测试图
研究者[22,23]对逆流旋转填料床气相压降性能进行了分段研究,研究发现进口压降和外腔压降均与液量无关,只与转速、气量有关,液体刚引进时,出口压降迅速增大,内腔压降明显减小,该床的干床压降大于湿床压降。科氏力引起的压降占总压降的12%~20%之间,摩擦力引起的压降占总压降的40%~70%之间,其中对科氏力及摩擦力引起的压降影响最为显著的是转速。
1.2.2.2 气-液错流操作的气相压降
错流式超重力装置[24,25]具有处理物料通量大、压降小和泛点高等优点,备受广大科技工作者的青睐。测试方法如下:
以水-空气为工作介质,对错流超重力装置的离心压降、干床压降和湿床压降进行了测量,测压点分布如图1-18所示,通过测定气体进出口点1-2为超重力装置总压降。气相压降由U形斜管压差计测定,超重力因子由变频器调节转轴的速度来测定,气液流量由转子流量计测定。

图1-18 错流旋转填料床测压点分布测试图
研究者们[26-30]研究了错流旋转填料床的气相压降特性,研究结果表明:错流旋转填料床湿床压降大于干床压降,其干床压降与湿床压降均与气速的平方成正比,处于阻力平方区;干床压降与转速无关;湿床压降与转速的平方成反比,与液体流量成正比;气相压降关联式与传统塔设备类似,但是不同于逆流旋转填料床;错流旋转填料床不会受到液泛气速的影响,气体流速可高达15m/s,甚至更高;与逆流旋转填料床相比,错流旋转填料床填料的直径可大大缩小。影响错流旋转填料床气相压降主要是转速和气量,液量影响较小,与逆流旋转填料床相比,错流旋转填料床的压降是它的1/10。床层气相压降与填料的空隙率及其厚度有关。
1.2.3 液泛现象
气液在超重力装置内接触的过程中,由于液相流体受到较大的超重力场的作用或者说流体质点受到较大的离心力作用,其流速远比在塔设备中的液体流速大得多。因此,在这种情况下,气体速度能在较高的速度情况下操作,气液接触一般不易发生液泛现象。但是,在操作不当的情况下,会发生气体中大量夹带液体的现象,甚至出现液泛现象,严重时会影响整个气液接触操作。
逆流旋转填料床的转子中心出现液雾状液滴,气体出口有大量液体喷出,压降有较大幅度波动时,可认为逆流旋转填料床[31,32]出现液泛现象。液泛现象首先出现在内缘(内腔)区,与气量、液量和转速有关,主要表现形式是气相夹带液滴,从正常操作到发生液泛的过程中气相压降、液相夹带量连续增加。相比之下,错流旋转填料床[21]不存在液泛问题,只有液沫夹带问题,可以在很高的气速下操作。而错流出口气体中的液沫夹带是很容易通过捕沫器设计解决的。在通气的情况下床内存在轻微轴向偏流,床内液体无明显轴向分散,因此液体轴向返混程度很小。
1.2.4 停留时间
液体在旋转填料床中的停留时间取决于填料径向深度、填料种类、转速以及液体本身的性质。衡量填料转子内液体量有两种基本方法:一个是转子内液体的平均停留时间;另一个是填料内的持液量。旋转填料床内的液体的停留时间可以通过示踪观察或者示踪电导传感的方法来测定,实验测得停留时间为0.2~1.8s,并且随着转速、液量和转子径向距离的增加而减小,而气量和液体黏度对停留时间影响不大。国内外研究者对旋转填料床持液量的研究并不多,仅有Basic和Burns的文献报道[1]。
1.2.5 小结
掌握气体和液体在旋转填料床内的流动特性对于理解其性能非常重要。例如,良好的液体分布特性有利于填料的均匀润湿,而且对于防止填料转子失衡非常重要;液体以液滴、液丝和液膜的形式存在于填料中,有助于传质和传热过程的强化;错流旋转填料床不受液泛的影响以及较低的压降导致了设备的处理能力提高。因此,旋转填料床的流体力学性能直接影响到填料床内的传质效果和设备的生产能力。通过对旋转填料床内部流体力学性能的研究,掌握设备结构及内构件对流体的作用机理,有助于设备性能的改善和提升,为超重力设备设计、操作参数的设置、设备放大及商业化应用提供重要的技术支持。
1.3 超重力吸收
吸收过程是最典型的传质过程,超重力装置作为一种新型的传质设备,可显著强化传质过程,因此超重力吸收技术在吸收过程占有极重要的地位。
1.3.1 超重力吸收原理
气体吸收过程是利用气体混合物中各组分在溶剂中溶解度的差异或与溶剂中活性组分化学反应的差异实现组分分离的过程,也是气体净化的常用单元操作,气体吸收过程实质是溶质由气相到液相的质量传递过程。工业上的气体吸收过程可分为物理吸收、化学吸收和物理化学吸收三大类。无论采用何种吸收形式,都要解决过程的极限和过程速率两个基本问题。
传统塔设备是利用重力作用达到气液两相在其中的充分接触实现物质传质,由于重力场较弱,液膜流动缓慢,在传质过程中体积系数较小,故这类设备通常体积庞大,空间利用率和生产强度低。超重力吸收设备,则是利用高速旋转的填料床,使液体产生强大的离心力,在几百至上千倍重力加速度时,液体流速可比重力场提高10倍,液体在巨大的剪切力作用下被拉伸或撕裂成微小的液滴、液丝和液膜,产生巨大的相间接触面积,流体的湍动程度大大增强,减小了相界面的传质阻力,大大强化了气液两相的传质。
因此,超重力吸收设备具有传统塔设备无法比拟的独特优势,越来越多的人们意识到它在过程强化领域的发展潜力以及应用前景。许多国家和地区(例如美国、中国、印度、英国、巴西和中国台湾等)的研究机构在不断地对旋转填料床进行开发应用研究,学者们采用不同吸收体系(CO2~NaOH[33]、CO2~H2O[34]),不同结构旋转填料床(错流床[35]、逆流床[36])研究了旋转填料床的气液吸收传质性能。结果表明,旋转填料床的传质效果明显高于传统塔设备,其液相体积传质系数比普通气液传质塔设备高1~2个数量级。试验结果均表明,超重力吸收装置可显著地强化吸收过程的传质速率。
1.3.2 超重力吸收工艺
采用超重力技术进行气液吸收实验,可采取类似以下工艺流程进行。在吸收实验工艺流程中,采用的旋转填料床可以是错流床、逆流床、多级轴向旋转床、SP-RPB、CAS-RPB等,采用的吸收体系可以是气膜控制,也可以是液膜控制。以Na2CO3溶液吸收H2S为例,采用错流旋转填料床描述超重力吸收工艺。实验流程如图1-19所示。

图1-19 超重力吸收H2S实验流程示意图
1—罗茨风机;2—H2S罐;3—U形压差计;4—旋转填料床;5—吸收槽; 6—液封装置;7—碱液槽;8—离心泵
贫液槽中的脱硫贫液在贫液泵的作用下,沿旋转填料床液体进口进入旋转填料床,经液体分布器分布后喷洒于高速旋转填料内缘,在离心力作用下向填料外缘甩出,在旋转的填料内,液体被分割为微小的液滴和液膜。含硫化氢原料气体经输气管路进入旋转填料床空腔,在压差推动下,气体沿填料外缘向内缘流动,与脱硫液逆流接触。气液两相在高湍动、强混合及相界面快速更新的情况下完成脱硫液对硫化氢气体的吸收过程。脱硫后的气体由旋转填料床中部的气体出口排出,接入下道工序。装置主要工艺参数见表1-1。
表1-1 装置主要工艺参数

1.3.3 超重力吸收应用
超重力技术极大地强化了气液间的传递过程,其体积传质系数比重力场条件下提高了一个数量级,这意味着完成同样的生产任务,超重力装置的体积将比普通的吸收设备缩小数十倍,不仅使系统设备体积和占地面积或空间体积大幅度减小,节省大量基建投资;而且设备重量轻,维修方便,可缩短检修周期,大大降低产品的生产成本。因此,在超重力场进行气体吸收操作是十分有利的,在这个方面已经实现了许多工程化应用,在这一节中,对几个典型实例进行简要说明。
1.3.3.1 超重力场中净化硝烟
在硝基苯、硝基炸药、硝基染料的生产过程,以及金属与非金属表面硝酸处理过程、硝基化合物分解等过程中会产生硝烟,其浓度达10000mg/m3以上。硝烟成分复杂,主要为N2O、NO、NO2、N2O4、N2O5的混合物,排放量较小、排放点集中、扩散速度快、危害严重、治理难度大。目前,氮氧化物的治理方法有干法和湿法两种,干法主要是针对低浓度的氮氧化物烟气,而高浓度的氮氧化物治理主要采用湿法进行。中北大学[37]率先提出采用超重力技术治理火炸药行业的硝烟,将超重力旋转填料床作为硝烟吸收器,通过其强大气-液传递速率的特性,提高硝烟控制步骤的吸收速率,进而加快整个吸收过程速率,达到深度净化的目的。该技术应用于太原某厂,通过现场试验表明,该技术对硝烟的处理有良好的预期效果,可以适用于不同场合硝烟气体的治理,易于操作,尾气排放达标。工艺参数见表1-2。
表1-2 工艺参数

1.3.3.2 超重力法脱除硫化氢气体
超重力法硫化氢吸收技术,其核心是将超重力技术应用于湿法脱硫工艺,采用超重力设备——超重力旋转填料床作为脱硫设备,利用其传质效率高、停留时间短的特性,使得脱硫过程得到强化,脱硫选择性得到提高,从而有望低耗、高效地实现选择性脱硫。超重力设备用于湿法脱硫的优势在于:脱硫效率高、脱硫液循环量小、填料具有自清洗作用、设备体积小、停留时间短、选择性好、设备可选用耐腐蚀材料。
该技术可推广应用于天然气、炼厂气、煤层气、合成气、煤气、半水煤气、焦炉煤气和变换气等气体中H2S的脱除。目前,江苏海基环保能源公司已经将该技术应用于炼油厂、化肥厂的尾气脱硫,年处理量达到7200万立方米/年,处理后H2S含量小于20mg/m3,实现达标排放的同时,还节省了脱硫成本。中北大学[38]将超重力脱硫技术成功地应用于山西某厂选择性脱除H2S、陶瓷行业的煤气脱硫、焦化行业的焦炉煤气脱硫、四川某集团的氨法低成本净化尾气、广西某厂的发生炉煤气等行业领域。以某行业超重力脱硫技术为例,其与常规方法对比的工艺技术参数如表1-3所示。
表1-3 工艺参数对比

实践证明,采用超重力技术脱硫能使脱硫液循环量和泵的扬程减小,整套脱硫装置的阻力降低,大大节省了能源。与传统技术相比,该技术脱硫率高,可达到90%以上,年减排H2S 700余吨。
1.3.3.3 超重力法脱除二氧化硫
由于我国经济的高速发展,能源的消耗量不断增加,二氧化硫的排放量也日趋增多。我国酸雨面积已占国土面积的40%,成为继欧洲和北美之后的第3大酸雨区。面对如此严重的防治酸雨的形势,国家强令关停小火力发电站、小型水泥厂、小型砖瓦窑,实现了一定程度的SO2减排;同时,对大型火力发电厂烟气开展深度治理,使排放烟气中SO2含量达到发达国家水平。为此必须通过经济和安全的手段使其达标排放,而现行的脱硫装置设备庞大,投资高,效率低,为了实现酸雨和二氧化硫污染控制目标,必须加快国产脱硫技术和设备的研究、开发、推广和应用。
现行的脱硫方法分为干法,半干法和湿法,而以湿法脱硫为主(85%以上)。湿法脱硫工艺的主体设备为吸收塔,有板式塔、填料塔和喷淋塔等。在此过程中,液膜流动缓慢,单位体积内有效接触面积小、液膜控制的传质过程的体积传质系数低,因此此类设备体积庞大,空间利用率和设备生产强度低。而在超重力旋转床中,液体被高度分散,气液界面高度湍动,形成了不断更新、极大的表面积,传质速度得到了极大的提高。正是基于这一特点,北京化工大学利用超重力旋转床对硫酸厂尾气气量为3000m3/h进行处理,可以使尾气中的二氧化硫含量降到100ppm。若将单级超重力脱硫与喷射脱硫器相结合,可在设备投资、动力消耗、气相压降等方面较原有技术有较大的优势。
1.3.3.4 超重力法吸收二氧化碳
近几十年来,由于CO2的过量排放造成地球表层的气温不断升高,给环境带来了很大的危害,各种自然灾害也愈演愈烈。但CO2也是一种非常宝贵的碳资源,可以被广泛用于多种领域,在工业生产中有非常重要的应用。对排放的CO2进行回收、固定、资源再利用,已成为世界各国特别是发达国家十分关注的问题。现阶段采用的吸收装置主要有:各种类型的吸收塔,文丘里洗涤器,鼓泡反应器等。但是这些反应器都存在明显的缺点,如传质效率不高、设备体积大、能耗高、安装维修不方便等。而超重力反应器由于其高效的传质效果,将其应用于二氧化碳的吸收过程,比传统的反应器传质效率更高、能耗减少、更经济。
中北大学的刘有智等对混合胺回收低分压二氧化碳的传质行为进行研究,认为超重力旋转填料床回收低分压CO2机理在于提高了气-液相接触总比表面积,强化了气液间的传质速率,提高了吸收效率:通过循环及时排走了反应生成热,有利于反应向吸收方向进行,最终使传质系数得以提高。工业生产中,CO2的吸收和再生是同时操作的,溶液再生的能耗决定了回收CO2的经济成本。在考察吸收状况的同时,进行溶液再生的研究是十分必要的。北京化工大学教育部超重力工程研究中心对二氧化碳的捕集和纯化进行了研究,并且这一研究计划得到了国家“十一五”科技支撑。
1.3.3.5 超重力法吸收VOCs
挥发性有机化合物(VOCs)是一种具有刺激性或臭味的气体,成分复杂、易挥发,可导致人体出现诸多不适,多数是由化工相关产业生产过程、产品消费行为以及机动车尾气造成的。我国针对石化、有机化工、合成材料、化学药品原药制造、塑料产品制造、装备制造等重点行业,完善VOCs的污染防治体系,以期达到改善空气质量和污染减排的目的。
传统VOCs控制方法主要以吸收法为主,利用液态吸收剂处理废气,气体溶解于液体中,从而达到控制大气污染的一种方法。该法适用于大气量、中等浓度的含VOCs废气的处理。采用常见的吸收设备如喷淋洗涤器、泡沫洗涤器、文丘里洗涤器等。传统设备存在传质效果差、体积庞大、装置阻力大等问题,采用旋转填料床取代传统吸收设备,可以有效解决以上问题。蒸汽汽提法被认为是从有机化工工业、塑料工业和合成纤维(OcPsF)工业产生的废水中去除VOCs的“最有利用价值的技术”。北京化工大学[39]采用超重力汽提技术去除VOCs,实验证明该技术能显著缩小反应器或分离设备的体积,简化工艺流程,实现了过程的高效节能,减少了污染排放,提高了产品质量。
1.3.3.6 超重力法吸收其他物质
合成氨、碳酸铵、硝酸铵、硫酸铵、纯碱、硝酸磷肥等化工生产过程中产生的含NH3类废气,气量大、浓度高,且含大量水汽和粉尘等杂质。在处理过程中,粉尘等杂质在水汽冷凝过程中会形成泥浆类物质,导致塔设备堵塞、NH3回收率低,难以稳定运行,是行业的难题。针对某厂气量为55000m3/h、含NH3的废气,其中含NH3为7960mg/m3,先前的吸收填料塔存在氟化物易堵塞,风机压头有限等难题,中北大学采用超重力技术进行脱氨除湿。结果表明,采用超重力技术脱氨率达到85%以上,年回收氨2800t,环境效益明显,经济效益每年可达420万元。该技术在山东某化肥公司也投入工业化,采用两台超重力装置,总气量可达25000m3/h,脱氨率可达92%以上,有效解决了行业难题。
此外,超重力气液吸收技术还应用于回收醋烟技术方面,中北大学将该技术引进到某厂进行现场中试,实验结果表明,针对气量为4500m3/h的醋烟,以水为吸收剂进行吸收,年可回收225t醋酸,回收率比原工艺提高了15%,年经济效益可达146万元。
超重力气液吸收技术不仅可以达到常规技术所不能比拟的高吸收率,而且超重力设备具有体积小、单位体积处理量大、设备和基建费用少、开停车短等特点。在创造可观经济效益的同时,也使得吸收装置自动化,取得了良好的社会效益。
1.4 超重力解吸
解吸是吸收的逆过程,又称气提或汽提,是将吸收的气体与吸收剂分开的操作。解吸的作用是回收溶质,同时再生吸收剂(恢复吸收溶质的能力)。工业上,解吸是构成吸收操作的重要环节。解吸分为物理解吸(无化学反应)和化学解吸(伴有化学反应)。采用传统的塔设备进行解吸,同样存在传质效果差、气液接触面小等缺点,采用超重力技术解吸,其优势在于解吸率高、气体用量小、不易结垢堵塞、设备体积小、气相压降小等。前面论述了超重力下的吸收操作,与吸收相反的过程,是超重力下的解吸过程,使溶质从液相中分离出来而转移到气相的过程。解吸与吸收的区别仅仅是物质传递的方向相反,它们所依据的原理是相似的。
1.4.1 超重力解吸原理
解吸是与吸收相反的过程,即溶质从液相中分离出来而转移到气相的过程(用惰性气流吹扫溶液或将溶液加热或将其送入减压容器中使溶质放出)。解吸和吸收的区别仅仅是过程中物质传递的方向相反,他们所依据的原理并无二致。超重力解吸技术同样如此,解吸液体在旋转填料床中被高速旋转的填料切割成尺寸很小的液丝、液滴和液膜,液体的湍动程度随转速的增大而增大,气液两相接触面积增大,液膜表面的更新速度加快,液相传质阻力减小,与惰性气体接触时,能更有效地进行解吸过程。
氨氮废水治理方法很多,主要有空气气提法、蒸汽汽提法、预氯化-活性炭吸附法、离子交换法、氧化池法、生物硝化-反硝化法等。其中空气气提法技术可靠,投资费用和运行费用相对较低,是应用最广泛、运行成本最低的一种方法。空气气提法是利用相间氨浓度差促使水中游离氨向空气中扩散的一种单元操作,即吸收操作的逆过程,又称为解吸或气(汽)提。在此单元操作中气提速率与气液接触方式及相间传质过程密切相关,利用超重力技术在强化传质方面的优势,可以使解吸设备体积小型化。这里以吹脱氨氮废水(即空气气提法处理氨氮废水)为例来介绍超重力场下的解吸过程。
水中的氨氮主要以铵根离子()和游离氨(NH3)的形式存在。常温常压下,它们与水中OH-保持化学平衡,其平衡关系式如下:
工业上通过加碱后,将铵根离子转变为游离氨,再采用空气吹脱(气提)或蒸汽汽提的方法,脱除液相中的游离氨。存在的问题主要是采用空气吹脱法时效率很低,吹脱率仅40%左右;且所需空气量大,风机能耗高。超重力技术单程吹脱率在85%以上,填料塔吹脱率只有40%~50%,出口气相氨浓度为平衡浓度的70.3%,理论推算的估计值为68%,本技术更接近理论平衡态,接近极限状态。超重力场中由于传质系数的大幅度提高,在气液比为传统方法1/4左右时即可达到同样的吹脱效果,减少了气液比,压降通常在200mmH2O(1mmH2O=9.80665Pa)左右,从而对风机全压的要求较低,减小了风机能耗,减少了设备投资及运行费用。
1.4.2 超重力解吸工艺
以吹脱氨氮废水为例说明超重力解吸过程,其工艺流程见图1-20。空气由罗茨鼓风机输送,空气首先经缓冲罐和转子流量计计量后,由气体进口管导入到转鼓外侧,在压力作用下气体自转鼓外侧进入床层,经过填料流至转鼓内腔并由气体出口管排出;调节好碱度的氨氮废水由输液泵自废水槽泵出,经流量计计量后送至位于转鼓内腔的静止液体分布器,均匀喷洒于转鼓内缘,进入床层的液体受到高速旋转填料的作用,由内向外径向流动。在此过程中,由于强大离心力的作用,液体在高分散、强混合及界面快速更新的环境下与气体充分接触并产生质量传递。为控制体系温度,在气体输入管路以及氨水槽均配有恒温加热器。本实验所用氨氮废水由某化肥厂提供,用NaOH做碱源调节氨氮废水的pH值。

图1-20 超重力吹脱氨氮废水工艺流程
1—风机;2—缓冲罐;3—变频器;4,7—流量计;5—旋转填料床;6—电机; 8—液体分布器;9—气体出口;10—液泵;11—氨氮废水
1.4.3 超重力解吸应用
超重力解吸技术与传统的解吸方法相比,具有处理效果好、设备体积小、成本低等优势,有利于解吸液中溶质的析出。目前,超重力解吸技术应用于氨氮废水、脲醛胶脱甲醛、提溴、吹碘等方面,下面分别介绍这几种工艺。
1.4.3.1 超重力法吹脱氨氮废水
氨氮污染可能引起江河水体藻类过度繁殖,形成富营养状态,大量消耗水中的溶解氧,致使鱼类和其他水生物窒息死亡,威胁生物的生长,破坏生态平衡。氨氮废水治理方法很多,主要有空气气提法、蒸汽汽提法、预氯化-活性炭吸附法、离子交换法、氧化池法、生物硝化-反硝化法等。其中空气气提法技术可靠,投资费用和运行费用相对较低,是应用最广泛、运行成本最低的一种方法。
超重力法吹脱氨氮废水技术[40,41]是采用旋转填料床作为吹脱设备,以空气为汽提剂,将水中的游离氨分子解吸到气相中的氨氮废水治理方法。在适宜工况下,单程吹脱率可达85%,采用两次逆流吹脱,总吹脱率可达98%,吹脱过程中气液比为传统吹脱法的1/4~1/3。整体来看,与传统吹脱法相比,超重力法吹脱氨氮废水具有气相动力消耗小;氨氮去除率高;设备体积小、运行稳定且操作弹性大;气液比小,利于氨回收;能增加水中溶解氧等特点。工程化应用效果显著,具有广泛的工业化应用前景。
中北大学与山西朔州某厂联合开发高效实用型(DN-A)CFB锅炉SNCR脱硝系统。将原先的氨气化工艺改为氨水吹脱,减少了能源消耗,降低了危险发生概率,实现了本质安全。采用超重力吹脱技术,使整个装置设备体积大大减小,节省了占地空间,并且改善了吹脱效果。实践证明,采用超重力烟气气提方法,将质量浓度为20%~25%氨水中游离氨吹脱至气相中,含氨10%左右气体作为氮源加入炉内脱硝,保证了脱硝效率。运行过程中的具体工艺参数如表1-4所示。
表1-4 工艺参数

1.4.3.2 超重力法吹碘
碘是制造无机和有机碘的基本原料,是重要的资源,一方面碘对人体健康有重要作用,也广泛用于医药、农药、化工、电子及军事工业;另一方面,含碘废液不加以处理直接排放会带来环境污染。目前,中国碘的年产量只有几百吨,与中国对碘的需求量形成巨大的反差,这直接导致国内市场碘的售价昂贵,而且中国每年都要花费大量的外汇从国外进口碘物资。在磷矿工业中伴生的碘一直作为“暂难利用”资源,在磷肥生产过程中耗散。因此,在磷化工企业中开展回收碘资源是一项利国利民的有意义的工作。
从稀磷酸中回收碘,碘的吹脱是稀酸提碘工艺中重要的一个环节。目前,工业中常用的方法为离子交换法和空气吹出法,离子交换法操作步骤比较繁琐,而空气吹出法工艺较简单,尤其是用于湿法磷酸中碘的回收对主产品稀磷酸的质量无任何影响。我国目前对碘的需求量还很大,碘的生产规模仍然较小,工艺技术水平低,旋转填料床既可用于传质分离过程,又可用于复相反应过程,采用超重力技术进行吹碘,具有良好的应用前景。
中北大学在贵州某集团进行了超重力吹碘实验,该集团拥有世界上第一个以磷矿伴生极低品位碘资源为原料的碘回收工业化装置,采用吹出吸收工艺从稀磷酸中回收碘。原料液中有5%左右的石膏、且本身也易结垢的特性,采用热空气吹脱、单层筛板塔仍只能连续运行5天。对于吹脱装置提出了抗腐蚀、强化气液接触、延缓结垢堵塞的要求。采用超重力吹碘技术后,将旋转填料床代替庞大的、滞留时间较长的填料塔,减少了工艺过程中的气液比、减少了空气用量、降低了碘资源及能源的消耗,简化了流程设备,强化了设备的生产能力,为工业化回收碘资源提供了新的技术方法。
由实验结果及分析可得:
①超重力技术应用于碘吹脱过程,可获得平均58%以上的吹脱率,最低出碘含量:8ppm。
②超重力吹脱过程,气液比由原工况的133减小到34左右时,空气用量减少2/3,吹脱率仍可保持在58%左右;减少热空气用量,增加吹脱后气体中碘浓度,有利于后续的碘吸收过程。
③采用超重力吹脱工艺,将热空气改为常温空气,吹脱工艺仍可正常运行,且吹脱效果无明显减小。
1.4.3.3 超重力法提溴
溴素是一种重要的基础性化工原料,在医药、农药、阻燃剂、灭火剂、制冷剂、感光材料、精细化工、油田开采等领域广泛应用。近年来,我国含溴卤水资源中溴浓度日益降低,而主流的空气吹出提溴工艺存在能耗高和温度适用范围窄的缺陷,当含溴卤水浓度较低时,空气吹出法提溴经济性变差,因此以降低能耗、提高效率为目标,离子交换树脂吸附法、气态膜法、乳化液膜法、鼓气膜吸收法和超重力法等提溴方法得以广泛研究。
空气吹出尾气封闭循环酸法制溴(简称酸法制溴)是国内卤水提溴领域的主流工艺。该工艺主要由酸化、氧化、吹出、吸收等工序组成。其中吹出工序是影响产品质量和成本的关键所在。其吹脱率的大小不仅关系着产品的最终得率,而且关系到吹后废液中残余的游离溴含量和影响着下游整个盐田生态系统。
提溴工序普遍是用空气在塔设备中将氧化液中游离溴吹出,通常吹脱率较低,即使在最适宜的条件下,吹脱率也仅有75%~85%;另外,塔设备存在阻力大和吹脱气液体积比大,风机的运行费用高的问题。超重力空气吹出氧化液中游离溴是利用超重力技术高度强化传质的特性,强化游离溴解吸至气相的传质过程。超重力场中氧化液在高速旋转的转子内填料的作用下被分散、破碎成极大的、不断更新的表面,在高分散、高湍动、强混合以及界面急速更新的情况下与空气以极大的相对速度在弯曲的孔道中逆向接触、传质,将氧化液中游离溴吹出,传质过程得到极大强化。
针对空气吹出提溴工艺吹出率低、能耗大的缺陷,中北大学利用旋转填料床,以不锈钢丝网为填料,在高转速条件下,利用离心力场取代重力场使含溴原料在填料表面分布,与吹溴空气错流接触进行解吸操作,其特点在于在高速离心作用下,一方面使得含溴料液内的传递阻力大为降低,另一方面,液体在气体中被分散为尺度极小的液膜、液丝和液滴等形式,极大地提高了传质比表面积。基于这两个特点,超重力法提溴在旋转填充床内实现了游离溴解吸过程的强化。
超重力技术的引入不仅使空气吹出酸液吸收法制溴工艺中氧化与吹出工序的配氯率与气液比降低,氧化率与吹脱率提高而且降低了气、液相动力消耗,尤其是超重力装置对气液变化不敏感,体积较小,维修方便的优点更为分散式卤水溴资源的开发利用提供了便利条件。我国西部大开发将伴随有大量油气田卤水的采出,为满足市场需求,提高产品质量,降低成本,超重力技术应用于我国卤水提溴工艺具有重要的历史意义和经济效益,为我国溴产品与国际化水平接轨提供了技术创新。
1.4.3.4 超重力法脱挥
在单体聚合成高分子物质的过程中,从反应器中出来的大多数聚合物都含有低相对分子质量的组分,如单体、溶剂、水及反应副产物,被统称为挥发分,是聚合物中不应含有的组分。这些单体或低聚物通常对于聚合物的品质有影响,或是对聚合物的物理化学特性有影响,或是对聚合物的应用性能有影响。从聚合物本体中脱除挥发分可以提高聚合物的性能、回收单体和溶剂、满足健康和环境要求、去除异味和提高聚合度;其脱除过程则称为挥发分脱除,简称脱挥。
聚合物系脱挥过程是将挥发性物质从液相移到气相并加以分离的过程。在聚合物制备过程中,脱挥过程所消耗的能量占全过程的60%~70%,因此脱挥过程的节能是一个重大的研究课题。聚合物生产及后处理过程的好坏,在很大程度上取决于所采用的聚合设备和脱挥设备的特性。聚合物脱挥是个受热力学、传质控制的分离过程,其单元操作具有很强的技术性,难点在于处理的是高黏性物料,操作过程中伴随发生的传热、传质及化学反应影响了聚合物的性能,使得过程更加复杂。由于这些限制,需要专门设计分离装置,使其中的流体流动方式更利于有效的分离。通常,高黏流体和超高黏流体的流动性极差,几乎无法在常规分离设备中操作。另外,高的黏度使得挥发物的传递速率大幅度下降,常规分离设备的效率大大下降。这就对分离设备提出了特殊的要求:要求能够在高黏度下操作时仍然保持较高的分离效率。因此,高速表面更新的新型高效传质设备的开发成为聚合物脱挥技术推广的关键。
超重力脱挥过程依靠超重力设备来实现。待处理的聚合物经过预热后,靠泵将其送入超重力装置内环处的分布器,进入旋转的填料内,在高速旋转的填料的剪切应力的作用下,使得液态的聚合物的流动形态成为极薄的液膜和极小的液滴,甚至形成雾滴状态,并且得到快速更新。在超重力设备内,一方面使低分子及易挥发的成分从高聚物中脱出的阻力降低,另一方面使得气液接触面积极大提高,从而促进挥发组分在聚合物中向气-液界面扩散,极大强化了相间传递过程。
一般来说,传质系数会随着黏度的增大而减小,对于非牛顿流体来说,在高剪切力的状况下其表观黏度也会相对减小,从而有利于传质的进行。超重力设备能够提供对液体强大的剪切力,不仅可以有效地迫使高黏度流体通过填料层,而且对于强化非牛顿流体的传质过程十分有效。超重力脱挥过程的优势有:
①巨大的剪应力克服了表面张力,将高黏度聚合物撕裂成液体薄膜,增加气液的接触面积;
②加快了液相聚合物表面更新速度;
③高剪切力使物系的表观黏度相对减小,利于传质的进行;
④高速旋转的填料有助于气泡的破裂;
⑤填料存在很大的表面积,使得气液接触面积增大;
⑥超重力场可强化微观混合和传递过程。
脲醛树脂胶黏剂是以甲醛和尿素为原料通过缩聚反应得到一种热固性树脂。因价格低廉、使用方便、有较高的胶合强度而广泛用于纤维板、胶合板等人造板的制造和木材加工工业。当前国内脲醛胶的主要缺陷是产品的游离甲醛含量较高,一般游离甲醛含量都在3%左右,使胶接产品在生产和使用过程中有较高的有毒气体甲醛逸出,严重地污染环境,损害了生产者和消费者的身心健康。目前,降低脲醛树脂中游离甲醛的主要方法除改进生产脲醛树脂的配方和合成工艺外,还使用甲醛捕捉剂、合理选用固化剂和脱水工艺等。虽然这些方法对降低游离甲醛起到很大作用,但也存在诸多不足,如树脂的胶接性能、水溶性能、初黏性等的降低。采用超重力常压空气吹脱的方法进行脱除脲醛树脂中游离甲醛单体,其处理量大,处理效果显著,处理后其中游离甲醛最低可达到0.1%以下。
中北大学[43]采用超重力技术对脱除脲醛树脂中游离甲醛进行了应用研究,研究结果表明超重力场脱除脲醛树脂中游离甲醛效率高,单程脱除效率在85%以上,脱除时间短,比常规的方法缩短70%左右的时间,适合间歇操作。处理后脲醛树脂中游离甲醛含量(质量比)不超过0.5%,其他性能指标按照《木材工业胶粘剂用脲醛、酚醛、三聚氰胺甲醛树脂》(GB/T 14732—2006)执行。超重力场脱除脲醛树脂中游离甲醛工艺简捷,配套设备少,只需在原有工艺中增加超重力装置和引风装置即可,以空气为介质脱除甲醛单体的同时,也降低了脲醛树脂的温度,省去采用冷却水降温过程。
静态型脱挥设备简单、可靠、经济,同时要求溶液黏度低且易于流动,但在静态型设备内,物料停留时间较长且分布宽,不适用于热力学不稳定的聚合物即最高操作温度较低的情况;薄膜更新型可以形成更小的薄膜厚度,但是为了获得巨大的气液传质面积,薄膜蒸发器一般都体积巨大,要形成更小的薄膜厚度就需要更高的设备精度要求,难度较大;排气挤出型设备的主体设备结构简单,工业应用成熟,但它是负压操作,在排气口处容易冒料,而且从经济角度评价,工业应用的大部分脱挥器中,双螺杆挤出机能耗最高,使得脱挥工段占据了聚合物制备工艺的大部分能耗;表面更新型脱挥器优化设备的结构使液膜变薄,提高传质传热面积,增加表面更新,强化传质过程,缩短物料停留时间,防止过热、避免发生再聚合。
超重力旋转填料床具有传质效率高、能耗低等优点,在聚合物脱挥工业中的应用必将越来越受到人们的重视。虽然该项技术在基础理论和应用方面取得的较大的进展,但在某些方面还有待于完善,如不同物系对填料结构的不同要求以及工业放大设备的动平衡与密封件的寿命问题。虽然如此,超重力技术显示出的极好性能,将会使其广泛应用于聚合物脱挥工业中。
1.5 超重力精馏
化工生产常需要将互溶液体混合物进行分离,以达到提纯或回收有用组分的目的。互溶液体混合物的分离按照混合物的物理化学特性有多种分离的方法,而蒸馏及精馏是最常用的方法。
精馏过程是利用混合液体中各组分的相对挥发度之间的差异,在精馏设备中根据多次部分汽化与冷凝的过程使得组分得以分离。常用的精馏设备有填料塔、板式塔等,在这些塔设备中,汽液的接触与流动都是在重力下进行的,因此液体流动缓慢,在填料表面形成的液膜面积小,且更新慢,进而导致了传质系数低,设备体积庞大,造价及运行费用高。针对这些问题,科学工作者对塔器设备结构、塔板结构及填料等方面进行了大量改进和研发工作,取得明显的技术进步和经济效益,推动了精馏技术的发展。随着经济的发展和节能降耗的要求,超重力精馏技术逐渐成为一个新的热点。
在超重力环境下,汽液实现高分散、高混合、强湍动,界面更新速度快,产生巨大相界面,混合物在短时间内得到分离提纯,大大强化了传递效率,设备体积相比传统精馏塔设备呈数十倍的比例减小,运行成本明显降低。超重力技术的这些优异特点,引起科技工作者的高度重视,使得人们在超重力精馏技术方面进行了不断的探索[43-49]。下面依据多年的研究工作和掌握的情况,对超重力场精馏原理、设备结构、传递特性等进行阐述。
1.5.1 超重力旋转填料床精馏
1.5.1.1 超重力旋转填料床精馏装置
超重力场精馏装置与流程可以依据气液流动形式、装置的结构、填料的设置情况、操作条件、流程结构等进行分类。
(1)依据填料设置情况分类
①单级超重力精馏装置 单级超重力精馏装置工作原理:蒸汽从气体进口管进入超重力精馏装置的外腔后,在压力的作用下自旋转填料的外侧沿径向通过填料层到达填料内侧,汇集于超重力精馏装置的内腔,然后从气体出口离开超重力精馏装置。液体从液体进口管进入超重力精馏装置的中央分布器,通过喷嘴均匀分散到填料的内侧,在超重力的作用下,液体自旋转填料内侧沿径向通过填料层向外侧甩出,经外壳收集后从液体出口流出。这种超重力精馏装置在工业中只能用于简单蒸馏,或用于精馏塔中的精馏段或提馏段。
②两级或多级超重力精馏装置 两级或多级超重力精馏装置指填料的设置分内外两(多)级和上下两(多)级填料。图1-21所示为内外两级超重力精馏装置,图1-22、图1-23所示为上下多级超重力精馏装置。两级或多级超重力精馏装置的不同级可作为精馏段和提馏段,因此,该装置可用于连续精馏操作。

图1-21 两级超重力精馏装置结构示意图
1—液体分布器;2—测压口;3—原料液进口; 4—气体出口;5—回流液进口;6,8—密封; 7—第一级填料;9—第二级填料;10—气体进口; 11—超重力精馏装置外壳;12—超重力精馏装置外腔; 13—转子;14—轴承;15—转轴;16—超重力精馏装置内腔;17—液体出口

图1-22 多层折流式超重力精馏装置
1—旋转折流盘;2—气体进口; 3-1,3-2—液体进口; 4—固定折流盘;5—气体出口; 6—引导管;7—液体进口; 8—支架;9—液体出口;10—转轴

图1-23 单层错流、总体逆流超重力精馏装置
1,12—原料进口;2—液体分布器;3—取样口; 4,9—回流液进口;5—气体出口;6—轴承轴; 7—转轴;8—转子固定楔;10—受液盘;11—转子; 13—降液管;14—介质进口;15—液体出口;16—旋转床外壳;17—填料下支撑盘片;18—填料上支撑盘片
(2)依据流程结构情况分类
①单台超重力精馏装置流程 图1-24所示为常压、全回流间歇操作精馏工艺流程。待分离的液体混合物,由再沸器汽化后,经气体流量计控制流量、压力表测压和温度计测温后,从气体进口管进入超重力精馏装置的外腔,在气体压力作用下自外向内强制性流过填料层,汇集于超重力精馏装置的中心管,然后在超重力精馏装置的气体出口经测压后进入冷凝器。冷凝液体通过液体转子流量计计量和温度计测温后进入超重力精馏装置的中央分布器,经喷嘴喷入旋转填料内侧,填料在电机的带动下高速旋转,形成超重力场,液体受超重力作用被甩向外侧,经超重力精馏装置的外壳收集后,从液体出口流回再沸器进行循环。

图1-24 单台超重力精馏工艺流程
1—再沸器;2—填料;3—机壳;4—液体入口; 5,18—取样口;6—温度计;7—阀门; 8—流量计;9—冷凝器;10—U形差压计; 11—气体出口;12—液体分布器;13—中心管; 14—喷嘴;15—外腔;16—液体出口; 17—转轴;19—气体进口
②双台超重力精馏装置流程 图1-25所示为双台超重力精馏工艺流程。原料在泵的作用下,经转子流量计计量后进入超重力精馏装置(RPB2),在填料中,受离心力的作用由填料内侧向外侧甩出,经液体出口流入再沸器。再沸器中的液体部分引出,部分经程序控温加热产生蒸气,减压阀控制蒸气量后进入超重力精馏装置(RPB2),蒸气在压力作用下由旋转填料外侧向内侧流动,由超重力精馏装置(RPB2)气体出口进入超重力精馏装置(RPB1)。从超重力精馏装置(RPB1)气体出口进入冷凝器的蒸气,经冷凝后部分作为回流液回流到超重力精馏装置(RPB1),其余作为产品贮存。

图1-25 双台超重力连续精馏工艺流程
1—原料贮槽;2—泵;3,7,8,11—转子流量计;4—RPB1;5—分凝器;6—全凝器; 9—废液贮槽;10—再沸器;12—RPB2
1.5.1.2 超重力旋转填料床精馏研究进展
超重力精馏作为一种可能带来巨大社会和经济效益的新兴化工分离工程技术,如今正吸引了世界各处的科研工作者对其进行研究,如表1-5所示。目前,在化学工业上已经成功地应用了超重力精馏技术,并显示出超重力设备相对传统塔设备的极大优越性。基于此,包括Glitsehteeh、Akzonobel在内的著名化工企业都开设了专门研究超重力精馏技术及设备的部门。今后超重力精馏的发展方向将主要是实现超重力精馏设备向中试和工业化的迈进以及对超重力精馏设备的转子、液体分布器以及填料的选择进行更加科学系统的研究;同时如何将超重力精馏技术与其他特殊精馏技术,如反应精馏、减压精馏、热偶精馏等结合起来,拓展超重力精馏技术的应用领域,也将是今后超重力精馏技术的发展重点。
表1-5 各研究机构关于超重力精馏研究一览表

1.5.2 超重力折流板精馏
1.5.2.1 超重力折流板精馏装置
一般而言,精馏过程需要的理论塔板数较多,单个转子具有的理论塔板数难以满足精馏的要求,而在一台超重力设备内同轴串联多个转子,又存在转子之间的密封问题。一种转子由动静部件相结合的旋转床[50],可以方便地解决转子之间的密封问题,在一台超重力床内同轴串联两个以上的转子[51,52],满足一般精馏所需要的理论塔板数,并可在一台超重力床内实现连续精馏所必须的中间进料。由于气液在转子内折流流动,故称为折流式超重力床(Rotating Zigzag Bed,RZB),其结构如图1-26所示。RZB的核心部件为动静部件相结合的转子,转子是由一个动盘1(下)和一个静盘5(上)构成,动盘和转轴11相连,静盘和壳体9固定进行密封。动盘1上表面固定有一组同心的圆形圈2(称为动折流圈),圈的上部开有小孔(图中未画出),动折流圈随动盘一起绕转轴旋转。静盘5下表面固定有另一组同心的圆形圈4(称为静折流圈),转子转动过程中静折流圈保持静止。动静两组折流圈相对且交错嵌套布置,动静折流圈之间的环隙空间与动折流圈和静盘以及静折流圈和动盘之间的缝隙,提供了流动的通道。

图1-26 折流式超重力床结构简图
1—动盘;2—动折流圈;3—气体进口管;4—静折流圈;5—静盘;6—气体出口管;7—液体进口管; 8—中间进料管;9—壳体;10—液体出口管;11—转轴
多层折流式超重力床的结构如图1-27所示(以三层为例),每层转子与单层旋转床相比,其中心处增加了导流管8,将来自上层转子外缘的液体引入到下层转子的中心,实现液体在各层转子之间的依次流动。另外,由于多层转子结构较单层转子的重量成倍增加,考虑到轴和壳体的机械强度以及设备的动平衡问题,因此多层结构通常采用中心悬垂式结构,即转轴完全穿过壳体,因此需要上下两处轴密封。另外多层结构还设置有多个进料口4,进料位置既可以在转子之间(4-1,4-2),也可以在某层转子上(4-3),这样可以在一台多层超重力床中实现带有多股进料、侧线采出、中间换热的复杂精馏以及萃取精馏、共沸精馏等过程。

图1-27 三层折流式超重力床结构简图
1—动盘;2—动折流圈;3—气体进口管;4-1,4-2,4-3—液体进口管;5—静盘;6—静折流圈;7—气体出口管; 8—导流管;9—回流管;10—壳体;11—液体出口管;12—转轴
1.5.2.2 超重力折流板精馏装置流体力学和传质特性
(1)流体力学性能[53-56]
折流式超重力床的结构以及气液流动方式均与其他旋转床不同,结构和流动形式的差异必然会引起旋转床内流体力学特性的变化。旋转床内流体力学特性的研究,对旋转床的操作有重要的指导意义,也是进一步研究旋转床传质性能的基础。
实验是在壳体直径和高度均为800mm的单层折流式超重力床内进行,实验装置流程如图1-28所示,转子外径为600mm,内径为150mm,高度为80mm,内含7个动折流圈和6个静折流圈,转速为600~1400r/min,离心加速度约为75g~410g(以转子的平均半径计)。实验采用空气-水作为测试物系,压降采用U形管压差计进行测量,主要研究了气体流量、液体流量和转速对气相压降的影响。

图1-28 折流式超重力床流体力学性能测试实验流程示意图
1—三相电度表;2—调频器;3—液体出口;4—传动皮带;5—调速电机;6—旋涡气泵; 7—温度计;8—孔板流量计;9—气体进口;10—U形压差计;11—高位槽;12—气体出口; 13—液体进口;14—折流式超重力床;15—转子流量计
研究结果表明:干床压降随着转速的增加而单调增加,与周向速度的平方成正比,即与转速的平方成正比,因此这部分压降可以称为离心压降;在气流存在的情况下,干床压降随着转速和气量的增加而增大,此时干床压降除了来自于离心力之外,还来自于气体通过转子的摩擦阻力和局部阻力;气量增大,干床压降增大,这主要是由于气体的径向运动时的局部阻力所引起的,气速的增加会加大局部阻力,从而使得通过旋转床的压降随气量的增加而增大。湿床压降随着气量的增加而增大,这主要是因为气体通过转子时径向运动时所造成的阻力损失增大,与气量影响干床压降的机理相类似;湿床压降均随着液量的增加而减小,减小的趋势随着气速的增加更为明显,当液量继续增大到一定值(约为600L/h)时,湿压降随着液量的变化不大;湿压降随转速的增大而增加,湿床的气相压降随转速的变化较为缓慢。
(2)传质性能[53,56]
传质性能测定实验在双层折流式超重力床内进行,实验装置流程如图1-29所示。旋转床壳体直径为800mm,高度为550mm,壳体内包含两个相同的转子,外径为630mm,内径为200mm,高度为80mm。壳体内上层转子作为精馏段,有9个静折流圈和8个动折流圈,下层转子作为提馏段,有9个静折流圈和8个动折流圈。实验测试物系为乙醇-水。

图1-29 折流式超重力床传质性能测试实验流程示意图
1—再沸器;2—产品储槽;3—产品转子流量计;4—回流转子流量计;5—冷凝器;6—原料高位槽; 7—U形压差计;8—原料转子流量计;9—调速电机;10—调频器;11—双层折流式超重力床
研究结果表明:理论板数随着回流流量的增加而降低,但当回流流量超过300L/h时,理论板数几乎不再变化。这是因为一方面回流流量的增加减小了气液之间的接触时间,削弱了传质,另一方面回流流量的增加会加大气液之间的相对速度,从而加剧湍动程度和液相表面的更新,强化了传质过程。通常来说,尤其是回流流量较小的情况下,转速对传质效率的影响比较大。实验发现传质效率随着转速增大而增加,且增加的幅度较大。在回流流量大于300L/h的情况下,理论板数随转速增加的变化不再明显,表明此时气液已经达到了完全的接触。这种变化趋势可归因于转速的双重效应,一方面转速增加会使得液膜变薄,有利于液相分散和传质过程;另一方面,转速增加会减小气液的接触时间,会导致传质效率的降低。因此折流式超重力床操作转速宜在1000r/min左右,此时单台旋转床的理论板数可以达到14块。
1.5.2.3 折流式超重力床的工业应用
折流式超重力床是一种通用的气液接触设备,其新颖的结构及独特优点决定了该设备在化学工业的诸多领域内具有广泛的应用前景。经过十多年的反复试验及改进,目前折流式超重力床已成功地应用于工业生产中连续精馏过程。现已产业化应用的设备有近600套,而且推广应用的范围和地域在不断地扩大,其中部分装置已连续运行近十年,设备操作稳定,性能良好,并为企业带来了可观的经济效益和社会效益。
(1)常规精馏——甲/乙醇回收[57]
折流式超重力床可以在单台设备内方便地实现中间进料和多转子同轴串联,而连续精馏是工业中应用最广泛且分离要求较高的单元操作,因此折流式超重力床是化学工业中的连续精馏过程最佳选择。折流式超重力床用于连续精馏过程的流程如图1-30所示。在目前已实现工业应用的折流式超重力床中,浙江某制药厂用于乙醇-水物系精馏的旋转床,其转子直径为630mm,两层转子,外壳直径为800mm、高为550mm。连续精馏,进料乙醇体积分数为40%,回流比2.5。所得产品乙醇体积分数为95%,再沸器残液中乙醇体积分数为0.5%,产品出料量4.5t/d。嘉兴某化工有限公司用于甲醇-水溶液精馏的旋转床,其转子直径为750mm、厚度为80mm,三层转子,外壳直径830mm、高800mm。连续精馏,进料甲醇质量分数为70%,回流比为1.5。所得产品中甲醇质量分数大于99.7%,再沸器残液中甲醇质量分数小于0.5%,产品出料量为12t/d。在工艺条件相同的情况下,表1-6给了折流式超重力床与传统填料塔高度和体积比较的结果,从表中可以看出折流式超重力场旋转床可极大地降低设备高度,缩小设备体积,是一种资源节约型的小型化气液传质设备,为超重力技术用于连续精馏过程提供了一个很好的范例。
表1-6 相同任务下折流式超重力床和传统填料塔的尺寸对比


图1-30 折流式超重力旋转床应用于连续精馏过程的流程
(2)汽提过程——高黏度热敏产品脱溶剂[57,58]
折流式超重力床作为通用的气液传质设备亦可以应用到工业中的汽提过程。浙江某生化股份有限公司在某产品合成过程中会引入甲醇作为溶剂,而最终要将含量约为10%的甲醇溶剂脱除。该脱除过程通常采用精馏操作在填料塔中进行,流程如图1-31(a)所示。由于产品脱除甲醇后水溶液呈浆状,黏度很高,易堵塞填料,因此原料只能直接加入再沸器,水蒸气直接通入再沸器进行加热。同时,由于物料在塔釜中停留时间较长,所以为防止产品水解而须采用真空操作以降低塔釜温度,而这又会导致塔顶甲醇蒸气温度过低,往往需要采用冷冻盐水来进行冷凝。在正常操作中为了减少进出料的次数,采用庞大的再沸器,而且最终产品中甲醇的含量也仅能降至0.3%,影响了产品的质量和产品的市场。该流程较复杂,操作繁琐,设备投资费用和操作费用也较高。

图1-31 填料塔(a)和折流式超重力床(b)应用于高黏度热敏产品脱甲醇过程的流程
现利用折流式超重力床对原工艺进行了改造,改造后的流程如图1-31(b)所示。新工艺中水蒸气和物料直接进入旋转床内进行常压汽提操作。该工艺具有以下特点:①旋转床具有较强的防堵塞能力,因此原料可以直接加入到旋转床中,从而省掉了造价较高的再沸器;②旋转床内物料的停留时间短,在较高操作温度下也不会发生显著的分解,因此操作可在常压下进行,从而省去了真空系统,节约了设备的投资和能源的消耗;③由于有效地减少了物料的分解,产品收率得到了提高;④采用常压操作,甲醇蒸气可以采用廉价的自来水进行冷凝,省去了冷冻盐水系统;⑤由于折流式超重力床传质速率高,产品中的甲醇质量分数可降至0.1%以下,显著地提高了产品的质量。由此可见,利用折流式超重力床改造后的新工艺大大地减少了设备投资费用和能耗,形成了独具特色的技术,带来了可观的经济效益和社会效益。表1-7给出了新工艺中折流式超重力床和原工艺中填料塔主要技术指标的对比。
表1-7 折流式超重力床和原工艺中填料塔主要技术指标的对比

1.6 超重力气-液反应
气-液反应是气相组分进入液相进行的反应,反应组分可以是气体和液体,也可以都是气体,但参与反应的气体组分需进入含有催化剂的液相才能进行反应。
气-液反应按反应类型主要有两类:一类是气体和液体间进行的气液相反应,以制取产品为目的。其中,化学吸收通常用于除去气相中某一组分以及从各种尾气中回收有用组分或除去有害组分等也属于这类反应。另一类是在液体催化剂存在下进行气相反应,例如乙烯和氧气通入氯化钯-氯化铜的盐酸水溶液生成乙醛。在这里主要介绍以制取产品为目的的第一类气液反应。
气-液传质设备类型有很多,主要应用板式塔和填料塔,其他亦可用喷淋塔、卧式塔、鼓泡塔、湿壁塔等。在选择气-液设备过程中要满足以下基本要求:相际面积大和气-液两相充分接触;生产能力大,可以保证正常的有效操作;操作稳定,操作弹性大;阻力小,节省能耗;结构简单,制造、安装方便;不堵塞、易检修。旋转填料床作为一种新型的气-液反应设备,可以有效满足以上基本要求,在气-液反应方面具有很大的应用前景。
1.6.1 超重力气-液反应机理
同传统塔器传质设备相比,超重力旋转床中的气-液两相间传质过程更为复杂。国内外的研究者们对不同结构的旋转填料床的传质性能进行了大量的实验研究,分别考察了设备结构参数、操作参数以及所选物系参数等对旋转填料床传质性能的影响情况,证明旋转填料床对传质的强化优于传统塔设备。这是由于超重力场的存在,使旋转填料床具有比塔设备更高的有效传质比表面积和气-液相的传质系数,从而使得气-液相传质的总传质系数得到大幅度的提高。
超重力旋转床中,液体在高分散、高湍动、强混合以及界面急速更新的情况下与气体以极大的相对速度在弯曲孔道中逆向接触。虽然这一过程极大地强化了传质过程,但也致使气-液间的传质过程变得较为复杂。为此,很多学者根据研究体系的不同,在3种典型气-液传质理论(Whitman提出的双膜理论、Higbie提出的溶质渗透理论和Danckwerts所提出的表面更新理论)基础上进行相应的合理简化和假设,提出了不同的超重力旋转床运行过程中的气-液传质理论及相应的气-液传质模型。到目前为止,在超重力旋转床中并没有普适性的气-液传质机理理论和传质模型式,从而难以为超重力旋转床的工业应用提供相应的设计基础数据。
1.6.2 超重力气-液反应工艺
以超重力气-液反应器制备纳米氢氧化铝为例,说明超重力气-液反应过程。深度脱硅脱钙除铁后的铝酸钠溶液放入循环贮液槽,经泵送至超重力反应器内部液体分布器,均匀喷射到旋转填料的内侧,二氧化碳/空气按比例混合后经过缓冲罐后送至旋转填料层外腔。气-液两相在旋转填料中逆向接触,发生沉淀反应,反应后液体流回循环槽中,在充分搅拌下,进行循环反应,当pH达到规定程度引入粒度控制剂,继续循环一段时间,终止反应。纳米氢氧化铝制备工艺如图1-32所示。

图1-32 纳米氢氧化铝制备工艺
1.6.3 超重力气-液反应应用
1.6.3.1 超重力气-液反应器制备纳米氢氧化铝
纤维状氢氧化铝是一种胶态的结晶不够完整的假水软石,晶相纯度高,成型性能好,具有触变性凝胶的特点。纤维状氢氧化铝主要用作生产催化剂载体、活性氧化铝原料等。由拟薄水铝石制得的活性氧化铝的比表面积、吸附性能较高,表面化学特性较好,具有一定的孔隙率和孔径分布,常用于催化剂及载体,大孔容的超细活性氧化铝用于加氢催化剂和重整催化剂载体。纳米级活性氢氧化铝阻燃剂是合成材料无卤阻燃剂之一,它具有阻燃、消烟、填充功能,在燃烧时无二次污染,并且其比表面积更大,表面能更高,阻燃效果更好,作为添加剂不影响材料的力学性能和加工特性,而且具有补偿性能。氢氧化铝的超细化及开发高性能的增效剂和高效的表面处理剂,是氢氧化铝阻燃剂的发展方向之一。
超重力技术制造的纳米粉体,具有颗粒小、粒径分布窄的优点,而且容易大量生产,是目前生产纳米粉体成本最低的方法之一。螺旋通道型旋转床超重力反应器,就是利用强大的离心力,使气-液流速提高,此装置可极大地强化传质反应过程并使微观混合均匀。碳分反应沉淀过程中,CO2与偏铝酸钠溶液反应是一气-液反应过程,螺旋通道型旋转床超重力反应强化其传质反应过程,并使其微观混合均匀。干燥过程中加入辅助分散剂异丁醇进行共沸蒸馏干燥,从而制备出粒径小且分布均匀的氢氧化铝纳米粉末。北京化工大学采用超重力反应水热耦合法得到的纳米氢氧化铝,形态单一、分布均匀,这是由于旋转填料床具有强化传质和微观混合的作用,相比搅拌槽,可以得到性能更为优异的氢氧化铝凝胶。
1.6.3.2 超重力臭氧氧化废水
目前,超重力处理含硝基苯废水、TNT红水、黑索金(也称黑索今,一般指环三亚甲基三硝胺)废水已达到了很好的效果。臭氧单独氧化过程中,虽然臭氧具有较高的氧化还原电位(2.07V),但其在水中溶解性差,存在臭氧利用率低等缺点;而双氧水单独作用氧化能力差。当两者以适当的比例混合协同处理废水时,可大幅提高废水的去除率。因为在臭氧和双氧水反应过程中生成了更多氧化性更高的羟基自由基,进而提高了废水的去除率[59]。
中北大学[60]采用RPB-O3/H2O2法处理黑索金废水,黑索金去除率达到98%以上,处理后废水中黑索金质量浓度为0.056mg/L,COD为21mg/L,达国家一级排放标准。超重力臭氧双氧水处理含硝基苯废水去除率可以达到96.7%;处理含黑索金废水去除率可以达到98.6%。中北大学同样采用RPB-O3/H2O2法处理硝基苯废水,循环处理35min硝基苯去除率可达96.7%,处理时间60min后,废水中硝基苯含量1.4mg/L,COD为39mg/L,达国家一级排放标准。这是由于在旋转填料床中用O3-H2O2法来进行氧化反应。一方面通过将强氧化剂臭氧与双氧水组合,产生氧化性更强的羟基自由基·OH来降解有机物,是一种高效、无二次污染的高级氧化技术;另一方面超重力技术使得气-液传质速率比传统的气-液反应装置提高了1~3个数量级,极大地强化了气-液传质过程,提高了臭氧利用率。
1.7 超重力直接换热
传热是化工重要的单元操作之一。基于以提高传热速率、减少热损失和缩小传热设备结构尺寸的目的,一些学者对超重力技术应用于气液两相之间的强化传热进行了探索性的研究。
1.7.1 超重力换热器
超重力场中的热交换是属于冷、热流体直接接触混合的热交换,该换热方式属于直接接触式换热,把完成这种直接接触式换热的超重力装置称为超重力换热器[61,62]。在旋转填料床中,由于超重力的作用,填料对液体的高剪切作用把液体分割成具有一定线速度的极薄的液膜和细小的液滴,气体通过高速旋转的、弯曲狭窄且多变的、充满着极薄的液膜和细小的液滴的填料层中的空隙时,气体和液体都与填料形成了急速的碰撞接触,可能使得液膜厚度减小,提高了传热系数,强化了传热过程。因而,超重力直接换热器换热机理主要是通过增强流体湍动程度,减小传热边界层中滞留内层的厚度,提高了对流传热系数,减小了对流传热的热阻,从而实现介质在设备中的快速换热,强化传热效果。
因气-液逆流接触状况是平均温度差Δt最大的情况,因而逆流型是主要的超重力换热器,其结构如图1-33所示。以水与空气为冷、热介质,其在超重力换热器中的热交换过程为:热气流通过超重力换热器的进气口进入,在压力作用下自转鼓周边进入填料层,经过填料进入外腔,从出口排出;冷流体通过液体分布器后进入填料层,液相流体被强大超重力强制沿径向做雾化分散。这样被高速旋转的填料分散成的极微小液滴、雾滴在填料层与热流体经过充分的接触,完成气-液两相间的传热传质过程。液相流体经壳内壁汇集到装置底部的排液口排出,气流则由装置上部排出。在填料层内既发生气相向液相的热量传递,也发生水的汽化或冷凝,即传质过程。

图1-33 逆流型超重力换热器的结构
1.7.2 超重力场中传热过程
在超重力换热器中的换热属于直接接触式传热,由于传热、传质同时进行,传热和传质的方向可能不同。旋转填料床内部实际过程的传递方向应由各处两相的温度和分压的实际情况确定。本节将以气液逆流接触的旋转填料床中热气体的直接水冷和热水的直接空气冷却为例进行讨论,定性分析其在超重力换热器中的热质传递过程。
1.7.2.1 过程传递的方向
在超重力换热器中进行的传热过程,传热和传质的方向都可能会发生逆转,在任何情况下,温度是传热方向的判据,分压(浓度)是传质方向的判据。以空气与水为例分析其在旋转填料床中的热质传递过程。气体中水汽分压的最大值为同温度下水的饱和蒸气压值,此时的空气称为饱和湿空气。显而易见,只要空气中含水汽未达饱和时(不饱和空气),该空气与同温度的水接触其传质方向必由水到空气。
在热、质同时进行传递的过程中,造成传递方向逆转的根本原因在于:液体的平衡分压(即水的饱和蒸气压ps)是由液体温度唯一决定的,而未饱和气体的温度t与水蒸气分压p水汽则是两个独立的变量。因此,当气体温度t等于液体温度θ而使传递过程达到瞬时平衡时,则未饱和气体中的水汽分压必低于同温度下水的饱和蒸气压,此时必然发生传质,即水的汽化。同理,当气体中的水汽分压等于水温θ下的饱和蒸气压时,传质过程达到瞬时平衡,但不饱和气体的温度必高于水温θ,此时必有传热发生,水温将会上升。由此可见,传热与传质同时进行时,一个过程的继续进行必定打破另一过程的瞬时平衡,并使其传递方向发生逆转。
1.7.2.2 冷热流体换热过程分析
(1)逆流旋转填料床中热气体的直接水冷
气、液两相沿填料径向的温度变化和水蒸气蒸气压的变化如图1-34所示。宏观上,气相和液相沿填料径向(自填料内部向填料层外部)的温度变化是单调下降的,而液相的水蒸气平衡分压pe与液相温度有关,因而也相应地单调下降。可是,气相中的水蒸气分压p水汽则可能出现非单调变化。气、液两相的分压曲线在填料层中某处相交,可以依据其交点(虚拟点)将填料层分成内、外两个部分(这个划分不是物理划分,而是热力学划分)。

图1-34 逆流超重力换热器中热气体的直接水冷过程
①内层:指靠近填料内腔的填料层。从热量传递过程看,在此区域,气体温度高于液体温度,热量由气相向液相传递,液相自气相获得显热又以潜热的形式随汽化的水分返回气相,液相温度变化缓和;从质量传递过程看,在此区域,由于气相温度变化急剧,同时,气相中的水汽分压p水汽低于液相的水汽平衡分压(水的饱和蒸气压ps),此时p水汽<ps,质量由液相向气相传递。因此,填料层内层的过程特点是:热、质反向传递,水汽分压自下而上急剧上升,但气体的热焓变化较小。
②外层:指靠近填料外沿部分的填料层。从热量传递过程看,在此区域,气体温度高于液体温度,气体传热给液体;从质量传递过程看,在此区域由于水温较低,气相中的水汽分压p水汽高于液相的水汽平衡分压(水的饱和蒸气压ps),相应的水的饱和蒸气压ps也低,气相水汽分压p水汽转而高于液相平衡分压pe,水汽将由气相转向液相,即发生水汽的冷凝。因此,填料层外层过程的特点是:热、质传递同向进行,水温急剧变化。
(2)逆流旋转填料床中热水的直接空气冷却
图1-35表示气、液两相沿径向填料高度方向的温度变化和水蒸气压的变化。类似地,宏观上,液相温度从填料层外沿向填料层内腔方向流动时呈现单调下降的趋势;液相的水蒸气平衡分压pe也相应地单调下降;而气相中的水汽分压p水汽则可能出现非单调变化。依据气液两相的分压曲线交点(虚拟点)将填料层分成内、外两个部分(这个划分不是物理划分,而是热力学划分)。

图1-35 逆流超重力换热器中热水的直接空气冷却
①外层:指靠近填料外沿部分的填料层。从热量传递过程看,在此区域,热水与温度较低的空气接触,水传热给空气;从质量传递过程看,在此区域由于水温高于气温,液相的水汽平衡分压必高于气相的水汽分压p水汽<ps,水汽化转为气相。此时,液体既给气体以显热,又给汽化的水分以潜热,因而水温自上而下较快地下降,该区域内热、质同时传递,都是液相转向气相。
②内层:指靠近填料内腔的填料层。从热量传递过程看,在此区域,水与进入的较干燥的空气相遇,发生剧烈的汽化过程,虽然水温低于气温,气体传热给液体;但对液相来说,由气相获得的显热不足以补偿水分汽化所带走的潜热,从质量传递过程看,在此区域,质量由液体转向气体。因此,填料层内层的过程特点是:热、质反向传递,液相温度自上而下地逐渐下降。
1.7.3 超重力换热器特点
超重力换热器通过快速而均匀的微观混合使得换热面更新加快,增大了传热面积;填料的高速旋转增强了流体湍动程度,使传热边界层中滞留内层的厚度减小,提高了对流传热系数,即减小了对流传热的热阻,从而强化了换热效果,其换热特点如下:
①超重力旋转填料床总传热、传质面积等于填料面积与液滴表面积之和;
②用超重力旋转填料床代替传统的换热塔,放大倍数显示其传热效果比传统填料塔提高了1~2个数量级,传热单元高度为0.08~0.23cm;
③逆流超重力旋转填料床中热气体的直接水冷,在填料层内层的过程的特点是热、质反向传递;填料层外层过程的特点是热、质同向进行;
④逆流超重力旋转填料床中热水的直接空气冷却,在填料外层热、质同时传递,都是液相转向气相;填料层内层的过程的特点是热、质反向传递,液相温度自上而下地逐渐下降;
⑤超重力旋转填料床用作换热设备,强化传热的最大影响因素是转速;其他的影响因素(如冷热介质的流量、温度等)和传统塔设备的影响趋势相同,但趋势的变化加剧,充分说明传热强化主要因素是超重力旋转填料床产生的超重力场。
参考文献
[1] 刘有智.超重力化工过程与技术[M].北京:国防工业出版社,2009.
[2] Burns J R,Ramshaw C.Process intensification:visual study of liquid maldistribution in rotating packed beds[J].Chem Eng Sci,1995,51:1347-1352.
[3] Weizhou Jiao,Youzhi Liu,Guisheng Qi.Gas pressure drop and mass transfer characteristics in cross-flow rotating packed bed with porous plate packing[J].Industrial & Engineering Chemistry Research,2010,49(8):3732-3740.
[4] 陈建峰.超重力技术及应用[M].北京:化学工业出版社,2002.
[5] 欧阳朝斌,刘有智,祁贵生等.一种新型反应设备——旋转填料床技术及其应用[J].化工科技,2002,10(4):50-53.
[6] 刘有智,刘振河,康荣灿等.错流旋转填料床气相压降特性[J].化工学报,2007,58(4):869-874.
[7] 简弃非,邓先和,邓颂九.碟片旋转床流体力学实验研究[J].化学工程,1998,26(2):6-9.
[8] 郭奋.错流旋转床内流体力学与传质特性的研究[D].北京:北京化工大学,1996.
[9] 焦纬洲,刘有智,刁金祥等.多孔波纹板错流旋转床的传质性能[J].化工进展,2006,25(2):209-212.
[10] 袁志国,刘有智,宋卫等.并流旋转填料床中磷酸钠法脱除烟气中SO2[J].化工进展,2014,(5):1327-1331.
[11] 隋立堂,徐之超.折流式超重力旋转床转子结构对气相压降的影响.高校化学工程学报,2008,22(1):28-33.
[12] Chandra A,Goswami P S,Rao D P.Characteristics of flow in a rotating packed bed(HIGEE)with split packing[J].Ind Eng Chem Res,2005,44(11):4051-4060.
[13] 杨力,刘有智,邵凡.气相剪切旋转填料床流场特性的数值模拟[J].计算机与应用化学,2013,30(3):286-290.
[14] Youzhi Liu,Deyin Gu,Chengcheng Xu,Guisheng Qi,Weizhou Jiao.Mass transfer characteristics in a rotating packed bed with split packing.Chinese Journal of Chemical Engineering,2015,23(5),:868-872.
[15] 谷德银,刘有智,祁贵生等.新型旋转填料床强化气膜控制传质过程[J].化工进展,2014,(9):2315-2320.
[16] 杨力,刘有智,邵凡等.气相剪切旋转填料床流场特性的数值模拟[J].计算机与应用化学,2013,(3):286-290.
[17] 张芳芳,刘有智,祁贵生等.新型旋转填料床脱除烟气中SO2的实验研究[J].过程工程学报,2015,15(4):589-593.
[18] J R Burns,J N Jamil,C Ramshaw.Process intensification:operating characteristics of rotating packed beds determination of liquid hold-up for a high-voidage structured packing[J].Chemical Engineering Science,2000,55:2401-2415.
[19] 陈建峰.超重力技术及应用[M].北京:化学工业出版社,2002.
[20] 王焕,祁贵生,刘有智等.错流旋转填料床气相压降特性实验研究[J].天然气化工(C1化学与化工),2013,(06):38-41.
[21] 赵海红,刘有智等.错流旋转填料床气相压降特性研究[J].化工科技.2004,12(2):12-15.
[22] 谢国勇,柳来栓等.旋转填料床气相压降研究进展[J].煤化工,2001,1:24-26.
[23] 李振虎,郭锴,陈建铭等.旋转填充床气相压降特性研究[J].北京化工大学学报,1999,26(4):5-10.
[24] 计建炳,王良华,徐之超.旋转填料床流体力学性能研究[J].石油化工设备,2001,30(5):20-23.
[25] 焦纬洲,刘有智等.多孔板错流旋转床流体力学性能研究[J].化工进展,2005,24(10):1162-1164.
[26] 焦纬洲,刘有智等.塑料孔板旋转填料床吸收性能研究[J].天然气工业,2005,25(12):125-127.
[27] 郭奋.错流旋转床内流体力学与传质特性的研究[D].北京:北京化工大学,1996.
[28] 赵海红,刘有智,石国亮等.错流旋转填料床气相压降特性研究[J].化工科技,2004,12(2):12-15.
[29] 刘有智,刘振河,康荣灿等.错流旋转填料床气相压降特性[J].化工学报,2007,58(4):869-874.
[30] 王焕.错流与逆流旋转填料床气相压降性能研究[D].太原:中北大学,2014.
[31] Munjal S,Dudukovic M P,Ramachandran P A.Mass-Transfer in Rotating Packed Beds with Countercurrent Gas-Liquid Flow[C].Chicago,Illinois:77th Annul AICHE Meeting,1985,11:10-15.
[32] 陈海辉等.逆流型旋转填料床的液泛实验研究[J].青岛科技大学学报.2004,25(3):228-231.
[33] 焦纬洲,刘有智等.多孔板错流旋转床流体力学性能研究[J].化工进展,2005,24(10):1162-1164.
[34] 焦纬洲,刘有智等.塑料孔板旋转填料床吸收性能研究[J].天然气工业,2005,25(12):125-127.
[35] 康荣灿,刘有智等.填料结构对错流旋转填料床传质性能的影响[J].青岛科技大学学报,2007,28(5):406-409.
[36] 杨平,胡孝勇.超重力反应器有效传质比相界面积的测定[J].闽江学院学报,2004,25(2):83-86.
[37] 李鹏,刘有智等.超重力技术治理火炸药行业氮氧化物的初步研究[J].环境污染与防治,2007,29(7):545-547.
[38] 祁贵生,刘有智,潘红霞,焦纬洲.错流旋转填料床中湿式氧化法脱除气体中硫化氢[J].石油学报(石油加工),2012,(02):195-199.
[39] Chen Y S,Liu H S.Absorption of VOCs in arotating packed bed[J].Ind Eng Chem Res,2002,41(6):1583-1588.
[40] 焦纬洲,刘有智,刘建伟等.超重力旋转床处理焦化氨氮废水中试研究[J].现代化工,2005,25(7):257-259.
[41] 刘有智,柳来栓,谢国勇,霍红,赵海红,张艳辉,贾建芳,李裕,任永成.超重力法吹脱氨氮废水技术研究[Z].太原:中北大学,2001.
[42] 刘有智,刘会雪.超重力旋转填料床在聚合物脱挥中的应用研究[J].高分子材料研究,2007,10:15-16.
[43] 栗秀萍,刘有智,张振翀.多级翅片导流板旋转填料床精馏性能研究[J].化学工程,2012,(06):28-31.
[44] 栗秀萍,王新成,李俊妮,刘有智.超重机内多孔板填料上气液流场的计算流体动力学模拟[J].石油化工,2013,(12):1361-1366.
[45] 徐之超,俞云良等.折流式超重力场旋转床及其在精馏中的应用[J].石油化工,2005,34(8):778-781.
[46] 计建炳,徐之超等.多层折流式超重力旋转床装置[P].ZL200510049145,2005.
[47] 俞云良,计建炳等.折流式旋转床电功率消耗特性[J].石油化工设备,2004,33(4):4-7.
[48] 陈文炳,金光海等.新型离心传质设备的研究[J].化工学报,1989,5:635-639.
[49] 徐欧官,计建炳等.折流式旋转床精馏研究[J].浙江化工,2003,34(3):3-5.
[50] 计建炳,王良华,徐之超等.折流式超重力场旋转床装置[P].ZL01134321.4,2001.
[51] 计建炳,徐之超,俞云良.Equipment of multi-rotors zigzag high-gravity rotating beds[P].US7344126B2,2005.
[52] Wang Guangquan,Xu Zhichao,Yu Yunliang,Ji Jianbing.Performance of a Rotating Zigzag Bed-A New HIGEE[J].Chemical Engineering Processing,2008,47(12):2131-2139.
[53] 计建炳,俞云良,徐之超.折流式旋转床——超重力场中的湿壁群[J].现代化工,2005,25(5):52-54,58.
[54] Todd,David B.Multistage vapor-liquid contactor[P].US3486743,1969.
[55] 俞云良.折流式旋转床性能的研究[D].杭州:浙江工业大学,2004.
[56] Wang Guangquan,Xu Zhichao,Ji Jianbing.Progress on Higee distillation—Introduction to a new device and its industrial applications[J].Chemical Engineering Research and Design,2011,89(8):1434-1442.
[57] 王广全,徐之超,俞云良等.超重力精馏技术及其产业化应用[J].现代化工,2010,30(S1):55-59.
[58] 焦纬洲,刘有智,祁贵生,杨森,李孟委.超重力氨法制备超细氧化锌[J].化学反应工程与工艺,2012,(04):341-345.
[59] 刘有智,张琳娜,李裕等.卤水提溴工艺中超重力空气吹出技术研究[J].现代化工,2009,29(8):78-81.
[60] 梁晓贤,刘有智,焦纬洲等.RPB-O3/H2O2法处理含黑索今废水的实验研究[J].现代化工,2012,32(9):89-92.
[61] 栗秀萍,刘有智,王晓莉.超重力精馏过程传热传质机理研究[J].化学工业与工程技术,2010,(02):1-5.
[62] 王新成,栗秀萍,刘有智,宋子彬.管壳式换热器的简捷设计与HTRI设计对比及分析[J].计算机与应用化学,2014,(03):303-306.