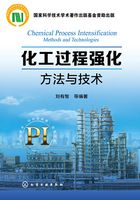
第2章 液-液过程超重力化工强化技术
2.1 概述
超重力技术是基于强化气-液两相接触过程而提出的,正像前一章所述,迄今强化气-液接触与反应方面的基础研究和应用研究取得很大的进展,其研究范畴涉及吸收与解吸、传热、气液反应等方面,研究成果在脱硫、除尘、脱氨、除湿、VOCs净化等领域得到了较广泛的应用[1]。但是,将超重力技术用于强化液-液相间传递过程和混合,也是近些年化工强化理论与实践的事情[2]。
基于多年的研究基础,山西省超重力化工工程技术研究中心提出了强化液-液混合与接触过程的新型超重力机制——撞击流-旋转填料床(Impinging Stream-Rotating Packed Bed,IS-RPB)[1],把超重力技术的研究领域从气-液相间的传递强化拓展到液-液相间的传递强化,并在液-液混合、萃取、液膜分离等化工过程强化和液-液反应合成纳米粒子等反应过程强化方面进行了大量的研究工作[3-6],部分工作已经形成工业规模的装置,并成功运行。
本章将从阐述撞击流的原理出发,介绍IS-RPB装置结构及液-液微观混合机制,阐述IS-RPB对化工过程强化和反应过程强化特性的基本理论、规律、性质和应用。
2.2 IS-RPB装备及技术
2.2.1 撞击流
撞击流的概念是由前苏联教授Elperin[7]在1961年提出并试验的,最早应用于气-固体系,其基本原理为等量的两股气体在加速管中将固体颗粒充分加速后形成气-固两相流,相向流动,在两加速管的中心区域同轴撞击,此时轴向速度迅速减小,转变为径向速度,并迅速增大,如图2-1所示。由于较大的撞击初速度(高达20m·s-1),在两加速管中心形成了一个强烈湍动的撞击区(Impingement Zone),极大地促进了动量、热量以及质量传递过程。

图2-1 撞击流反应器基本原理示意图
对于液体而言,虽然不像气体那样能够达到较大的撞击初速度,但是液体密度比气体大3个数量级,两液体间的动量传递要比气体间的强烈得多[8]。若两种撞击流装置加速管的截面积相等,即AL=AG=A,假定液体密度为气体密度的3个数量级,则
(2-1)
式中 、
——液体、气体的密度,kg·m-3;
u0L、u0G——以液体为连续相、气体为连续相的相向两流体撞击速度,kg·m-3;
根据Newton定律,液体为连续相的撞击流装置(LIS)中,单位时间内两股液体相向撞击的动量传递ML如式(2-2)所示:
(2-2)
式中 A——加速管截面积,m2;
ML——LIS中传递的动量,kg·m·s-1;
mL——LIS中液体液滴的质量,kg;
VL——LIS中液体体积,m3。
气体为连续相的撞击流装置(GIS)动量传递为:
(2-3)
根据式(2-1)~式(2-3)可得到GIS的动量传递与LIS动量传递之间的关系如式(2-4)所示:
(2-4)
即LIS传递的动量要比GIS中高10倍,如此高的动量传递再加上液体处于分子紧密聚集的状态,使得同轴相向撞击的液体间发生强烈的相互作用,例如:流团、分子间相互碰撞、挤压等,极大程度地促进了分子尺度的混合,达到理想的微观混合效果。
撞击流的分类很多,根据连续相的不同,可分为旋流型、平流型;根据射流在撞击流反应器的流动,可分为同轴逆流、偏心逆流、曲线同轴、曲线不同轴;根据撞击面的特征和数目,可分为固定型、移动型、多区型、平面径向流、平面环流;根据接触器的操作方式,可分为两侧进料连续式、单边进料连续式、半间歇式;根据撞击自由度不同,可分为受限式撞击流反应器(Confined Impinging Jets Reactors,CIJRs)和开放式撞击流反应器(Free Impinging Jets Reactors,FIJRs)。此外,研究较多的还有浸没式撞击流反应器、毛细撞击流反应器等。
(1)受限式撞击流反应器
CIJRs主要是指两股流体撞击空间受限,即两股流体经加速管2加速后,在一个很小的腔室内同轴相向撞击。由于CIJRs混合腔室空间较小,流体在撞击过程中是全部充满混合腔室1,系统为液-液单相流,在加速管2轴线上方的左右两侧各形成两个回流区,通过漩涡卷吸作用,卷吸周围流体从而促进混合过程。当流体到达出口处3时,出口直径缩小,腔室与出口的连接处呈现一定的角度,流体在此位置静压能最大,停留时间延长;流体在从腔室到出口的流动过程,类似于流体在由粗变细的变径管道中流动,静压能转换为动能,形成二次混合,提高了混合效率。常见结构如图2-2所示[9]。

图2-2 受限式撞击流反应器原理示意图
1—混合腔室;2—加速管; 3—液体出口
Gao等[10]采用粒子图像测速技术(Particle Image Velocimetry,PIV)技术对CIJRs内流场流动特性进行研究,结果表明撞击区中心湍动能最大,强化了动量传递过程,提高了混合效果;但是在加速管轴线上方,靠近混合腔壁面会形成死区,此区域流体保持较低的平均速度和瞬时速度,混合效果较差。
(2)开放式撞击流反应器
FIJRs用于液-液混合的研究最早是Savart[11]于1833年发现两股相等入口速度的流体在开放的环境或者是体积较大的腔室中相向撞击,撞击过程不受反应器壁的限制,原本稳定流动的液体被破碎。当两股流体在开放的环境中相向撞击,同轴撞击时产生圆形的撞击面,倾斜撞击时形成椭圆形或叶片形的撞击面,任意撞击角度的两股液体撞击流装置的结构如图2-3所示。在撞击过程中由于液体的不稳定性而产生强烈波动,促使其变形。当波动达到一定程度,液体破碎形成液滴;随着喷嘴出口速度的增大,液膜不稳定性的增强促进了破碎模式的转换,液体破碎形成更多、直径更小的液滴,最终形成较高程度的雾化。这个过程为气-液两相流系统,产生了高动能耗散和剧烈的湍动,促进动量传递和混合过程。

图2-3 开放式撞击流反应器原理示意图[12]
C1,C2—溶液1,2进料毛细管;J1,J2—溶液1,2入射口; y—垂直中心线或重力方向;x—水平轴向; S—流体碰撞后形成的x-y面;P—产物流体; V—视图方向
中北大学首次采用PIV技术,以去离子水为测试体系,加入8~12μm的空心玻璃珠为示踪粒子,研究了开放式撞击流反应器流场流动特性,建立了粒子图像测速系统、高速相机流场视频和酸催化水解平行竞争化学反应研究开放式撞击流流动特性的方法体系[13,14]。不同喷嘴出口雷诺数Re下,FIJRs内湍动能如图2-4所示[13]。从流线可以看出,在FIJRs中并没有回流区的形成,不会形成死区影响混合效果;从湍动能的分布可以看出,撞击区中心湍动仍然最剧烈,从而强化了动量传递过程,提高了混合效果;然而,在撞击面边缘湍动程度较弱且湍动程度分布不均匀,混合不均匀,相对于撞击中心,混合效果较差。由于这种边界效应的限制,使得FIJRs边缘混合或传递不够均匀。

图2-4 Re对湍动能分布的影响
综上所述,液-液体系的撞击流反应器极大程度地强化了两液体间的动量传递,提高了混合效果,同时开发了不同的撞击流的撞击方式,如单反射-环式喷嘴撞击流结构、川形撞击流结构、套管式撞击流结构等[15-17],其与旋转填料床的耦合技术IS-RPB能够消除撞击流混合边缘效应,为不同物系的物料混合提供均匀的环境,显示出了较强的微观混合性能、较高的传质强度、较短的停留时间等优势,在液-液混合、反应、乳化、萃取等方面具有广阔的应用前景。
2.2.2 IS-RPB装置
IS-RPB装置就是将撞击流装置设置在旋转填料床转子中心部位的填料空腔内,两个射流喷嘴同轴同心相向设置,与旋转填料床转子的转轴同心或平行。两喷嘴的轴向安装位置要求与填料的轴向厚度的中心线对称,如图2-5所示。

图2-5 撞击流-旋转填料床主体结构示意图
IS-RPB的工作流程是:两股加压的流体自两个液体进口分别进入后,自喷嘴以射流的形式喷出,两股射流相遇即刻发生撞击,形成一垂直于射流方向的圆(扇)形薄雾(膜)面,在其过程中两股流体进行了混合,该雾面边缘随即进入旋转填料床的内腔,流体在高速旋转填料作用下沿填料孔隙向外缘流动,并在此期间液体被多次切割、凝并及分散,从而得到进一步的混合。最终,液体在离心力的作用下从转鼓的外缘甩到外壳上,在重力的作用下汇集到出口处,经出口排出,完成液-液接触混合过程,从而实现均匀混合。
2.2.3 IS-RPB的设计原则
如图2-6所示,在进行IS-RPB设计时,需要首先确定的主要部件的几何尺寸包括:进液管直径Dl;喷嘴直径d0;喷嘴间距L;旋转床内径d1;旋转床外径d2;旋转床轴向厚度H。这些几何尺寸的设计,由如下的结构设计和操作设计来决定。

图2-6 IS-RPB主要设计参数示意图
结构设计原则:撞击流装置置于旋转填料床转子中心部位的空腔内,根据液体流量的大小,可以设置两股流体撞击或多股流体撞击,以确保经过流体撞击形成的雾面落在填料中心的空腔区域。
操作设计原则:经过对撞击流速和填料的旋转速度的协同调节,实现液体撞击形成的雾化面,落入结构设计要求的范围,达到撞击混合与填料旋转二次混合的耦合混合效果。
针对不同的物系及操作目的,以上参数之间有着不同的关系,同时不同结构的撞击流设计原则见参考文献[1,15-18]。
2.2.4 IS-RPB内流体流动及混合 (工作原理)
撞击流的基本原理是使两股很靠近的等量流体沿同轴相向流动,并在两股流体的中点处撞击。宏观上,两股射流相向撞击过程中,由于惯性,流体微元穿过撞击面渗入反向流。由于较大的动能作用,在撞击处动能转化为静压能,静压能的作用使得两股流体的流向发生改变,形成与原流体流动方向垂直的撞击(雾)面。微观上,相向流体撞击的结果产生一个较窄的高度湍动区,流体间碰撞产生的剪切力可导致滴粒破碎,增大其表面积并促进表面更新,从而增大传递速率。但是,在撞击面的外沿处其湍动程度明显减弱,其传递速率减小。
经过两股射流相向撞击后的液体在填料转子旋转的作用下进入旋转填料层内侧,混合较弱的撞击雾面边缘在旋转填料床作用下得到进一步混合。进入填料的液液混合流体被高速旋转的填料剧烈地微滴化,同时分布在旋转丝网填料的表面及填料空间。在此旋转填料床混合过程中,部分液体被第一层丝网捕获后,获得与丝网一致的周向速度;未被填料捕获的部分则保持原有的速度沿径向运动,由于填料丝网直径小(0.3mm)且缠绕密实,第二层丝网填料高速旋转所产生的巨大剪切力将未被捕获的流体进行部分捕获,依照这种运动方式,经过数层丝网后,未被捕获的液体均会被高速旋转的丝网填料所切割和捕获。捕获后的液滴依附在旋转的丝网填料上,由于流体的各个质点受力不均,部分液体被丝网甩出,甩出后的液滴周向速度小于半径处丝网的速度,所以液滴运动相对于丝网存在滞后。在周向上与初始入射角度相比,运动轨迹沿旋转方向的反方向有一定角度的偏移。角度的偏移会促进液滴在高速旋转填料中被切割成液丝、液滴和液膜等形态,旋转的填料对液体的作用有利于增大接触面积和促进丝网填料的表面更新,使得两种流体多次被捕获、雾化、凝并和分散,液体微元被高速旋转填料多次剪切为液丝、液膜和液滴等形式,使得液体被多次雾化,致使两种流体的强化接触与混合。旋转填料床内液体微元之间的聚并分散过程是瞬间完成的并且混合均匀,而在旋转填料床的填料主体内,由于液体微元进入之前就以高速进入,所以它们之间相对速度也较高,两个液体微元从相遇到再次相遇是个完全均匀的混合过程,能够使撞击以后没有完全混合的边缘部分进一步地混合。旋转填料床内径(内腔)尺寸与撞击雾面的大小“耦合”是这一机制的关键所在,也是消除撞击流混合边缘效应提高混合效果的根本原因。IS-RPB的最大混合特点是利用超重力装置内径处的端效应抵消了撞击流装置的边缘效应,从而使物料完成强化接触与混合过程。
在IS-RPB内,由于其独特的混合机理,使得其内部液体的总体对流扩散与湍流扩散得到极大的强化。一方面,液体是以极小的液滴、液丝、液线以及液膜的形式存在且高度湍动,从而使得湍流扩散造成的流体微团的尺度基本达到了分子尺度;另一方面,在IS-RPB内的液体混合在各处趋于均匀,从而不需要总体对流来实现混合设备内的均匀化。IS-RPB内对于湍流扩散的极大强化作用使得液体微团的尺度达到微米级水平,分子扩散的混合作用就变得非常明显,从而使流体微团消失,达到了设备内分子尺度的均匀微观混合。
2.3 IS-RPB微观混合性能
2.3.1 微观混合研究方法
微观混合[19]是指物料由湍流分散后的最小尺度到分子尺度的均匀化过程,它对燃烧、聚合、有机合成、沉淀、结晶等快速反应过程有着重要的影响。其原因在于快速反应体系需要短的停留时间和高强度的局部混合以避免分子尺度上的离集。微观混合不但影响这些化学反应的转化率和选择性,同时也影响产物的性质和质量。因此,对撞击流-旋转填料床混合性能的研究是十分重要和必需的。
采用平行竞争反应碘化物-碘酸盐反应体系评价撞击流-旋转填料床的混合性能[19,20]。
(2-5)
(2-6)
(2-7)
其中,反应(2-5)为中和反应,可以在瞬间完成;反应(2-6)为氧化还原反应,反应速率比反应(2-5)慢,反应程度取决于微观混合的好坏。如果达到最大混合均匀状态,则所加入的H+完全被反应(2-5)消耗,反应(2-6)不会进行;如果达到完全离集状态,则所加入的H+完全被反应(2-6)消耗;如果微观混合处于两种状态之间,则所加入的H+被两个反应竞争消耗;同时出现反应(2-6)和反应(2-7)。
由定义如下的离集指数XS来表征IS-RPB反应器微观混合效率:
(2-8)
(2-9)
(2-10)
式中,Y为参与反应(2-6)的H+的量与所加入的H+总量的比;YST为完全离集状况下XS的值。XS值在0~1之间,XS=1为完全离集,XS=0为最大微观混合。根据要求配置的溶液A和B分别加入两个贮槽1和7中,两股液体由泵打入IS-RPB反应器,如图2-7所示。在液体出口3处取样,然后用分光光度计(波长353nm)检测的浓度进而计算出I2的浓度,进而计算IS-RPB反应器的离集指数。

图2-7 实验工艺流程
1,7—贮槽;2—IS-RPB反应器;3—液体出口; 4—转子流量计;5—调节阀;6—计量泵
2.3.2 微观混合性能对比
在相近操作条件的情况下,对撞击流(IS)、旋转填料床(RPB)和撞击流-旋转填料床(IS-RPB)三种反应器的微观混合性能进行对比的结果见图2-8。从图2-8看出随着流量的增加,XS下降。IS(0.038<XS<0.115)与RPB(0.0201<XS<0.111)的离集指数相近,但明显高于IS-RPB(0.003<XS<0.018),表明IS-RPB具有良好的微观混合性能。

图2-8 三种反应器对离集指数的影响
同时,与其他反应器进行对比,气动搅拌槽[21]的离集指数为0.3~0.7,Liu等[22]对Couette Flow反应器进行了微观混合性能研究,其离集指数随旋转速度的增加由0.95降低至0.14;2000年,Monnier[23]采用超声测定连续流的微观混合性能,研究发现超声可以提高微观混合效率,在流量为9.53mL/s的条件下,离集指数从0.03变化到0.07。Yang[24]等对旋转填料床微观混合性能进行研究,在实验操作条件下,离集指数的变化范围为0.008~0.024。通过这些研究发现:在超重力和初始液体撞击的作用下,IS-RPB可以显著提高微观混合效率。同时,作为一个连续的混合器或反应器,将会在化学工业和其他工业中产生深远的影响。
2.3.3 黏性体系对微观混合性能的影响
通过甘油来配制不同黏性溶液,考察IS-RPB微观混合性能,固定氢离子浓度=0.1mol/L,撞击间距d=30mm,撞击角度α=180°和两股流体的体积流量比η=7,考察不同黏性流体微观混合性能的影响关系[19],实验结果如图2-9所示。

图2-9 离集指数随超重力因子的变化关系
从图2-9中看出,不同黏性流体微观混合性能的离集指数随超重力因子β的增加而减小并趋于定值;随着黏度的增加,微观混合效果变差,当黏度继续增加,微观混合效果相近。当超重力因子较小时,不同黏度的溶液微观混合差异较大;但当超重力因子较大时,高速旋转产生的剪切力强化了溶液中分子的扩散速率,导致不同黏度的溶液的微观混合的离集指数相近,特别是对于黏度为15mPa·s和20mPa·s的溶液更为明显;同时,从图中看出,黏度为1mPa·s的水体系在β>106.2离集指数趋于定值,而黏性流体在β>208.1时趋于定值,在高转速条件下(β>208.1)产生的剪切力将分子的扩散速率强化到较高的水平,此时超重力因子的增大对于混合效果的影响不显著,则离集指数下降不明显。
2.3.4 IS-RPB微观混合时间的确定及对比
由Villermaux等提出的团聚模型[25](Incorporation Model)逐渐受到了关注,该模型最初用于搅拌槽反应器的特征微观混合时间的计算。后来被扩展到连续式反应器特征微观混合时间的计算,如Coutte流反应器和静态混合器等反应器。通过实验测定XS随某一控制变量变化的曲线为渐近线。混合时间tm是了解微观混合真正具有实际价值的重要参数;而离集指数XS虽然可以作为了解微观混合的向导,却只能用于相对比较。因此,有必要计算出微观混合时间tm。
根据团聚模型及实验中所得的离集指数,求得IS的微观混合时间tm为0.05~1.6ms,RPB的微观混合时间tm为0.02~1.4ms,IS-RPB的微观混合时间tm为0.004~0.03ms,黏性体系的微观混合时间为0.05~0.1ms。与传统搅拌槽反应器tm=5~50ms和IS反应器tm=50~200ms[8],Y型微通道反应器[26]tm=0.1~1ms,定-转子反应器[27]tm=0.01~0.05ms以及旋转填料床[24]tm=0.01~0.1ms相比,微观混合时间远远小于以上几种反应器,表明IS-RPB反应器是一种高效的微观混合设备。
2.4 化工过程强化
IS-RPB实现了将气-液过程强化拓展到超重力液-液过程的强化,在此以液-液乳化、萃取、液膜分离等化工过程为例,阐述其过程强化特性和应用性能。
2.4.1 乳化
乳化操作是一类普遍的化工操作,在此以甲醇柴油乳化燃料的制备为例来介绍IS-RPB强化乳化的过程和特性。
甲醇柴油乳化燃料是一种可控污染排放的环境友好燃料、可部分代替柴油,在能源紧缺、环境日益严重的今天越来越受到科研工作者的重视。影响制备甲醇柴油乳化燃料性能的两个关键因素是乳化剂和乳化装置[4]。在乳化剂方面,国内外文献显示:采用单一乳化剂达不到乳化目的,采用含氮类乳化剂的燃料燃烧时会导致NOx污染物的增加,同时上述乳化剂含量高、用量大,显著增加了乳化柴油成本;在乳化装置方面,传统乳化装置主要有搅拌器、均质器和胶体磨等,存在流体质点受力不均、混合效果差、间歇操作、设备体积大和能耗高等缺点,致使乳化剂用量大、稳定性差。因此,开发新型乳化剂和连续操作的高效乳化装置势在必行。
2.4.1.1 IS-RPB强化甲醇-柴油乳化过程分析
IS-RPB制备甲醇柴油乳液的过程中,所有流体质点的运动途径是相同(近)和连续的过程,通过初始乳化、强化乳化、完善乳化等三个环节完成多级逐级强化甲醇柴油乳化的过程。同时采用计算流体力学的方法,首次研究了IS-RPB的流体形态,并且证实了其混合的三个过程的存在[4]。IS-RPB制备甲醇柴油乳液是一个连续的、流体质点受力均匀的稳定过程。高速分散器和IS-RPB两种乳化装置制备甲醇柴油乳液主要的区别在于甲醇和柴油在乳化装置中所受到力是不同的。在超重力场中,甲醇和柴油在乳化剂作用下的乳化是连续的,且所有甲醇和柴油流体质点在超重力环境下所受的力是一样的(所有流体质点经过撞击流乳化过程、旋转填料床乳化过程和壁面反溅乳化过程等);高速分散器制备甲醇柴油乳液是间歇操作,距离转子较近的甲醇和柴油有效乳化的频率是较高的,但距离较远的就不能达到有效乳化,在有些死角,甚至有的甲醇和柴油不能得到乳化,达不到乳化的能垒,也就谈不上有效乳化。基于所有甲醇和柴油流体质点所受的力不一样,也就使得油包水型甲醇柴油乳液的分散相大小不均,从而导致乳化效果的降低。因此,连续式超重力装置制备甲醇柴油乳液的混合效果优于间歇式高速分散器。
2.4.1.2 IS-RPB强化甲醇-柴油乳化工艺流程
按比例分别称取柴油、甲醇、亲水性乳化剂和亲油性乳化剂,甲醇和亲水性乳化剂混合制得水相,将其加入水相储槽1;柴油和亲油性乳化剂混合制得油相,将其加入至油相储槽3。在液泵的作用下经计量后进入撞击流-旋转填料床5。在此过程中,水相和油相在撞击流装置中发生撞击,水相和油相在乳化剂的作用下,降低油水界面张力,增强水相和油相混合,形成一垂直于射流方向的圆(扇)形薄膜(雾)面,实现了乳化柴油的初步乳化,混合较弱的撞击雾面边缘进入旋转填料床的内腔,流体沿填料孔隙向外缘流动,填料的高速旋转造成喷头喷出的液体与旋转填料的相对速度较大,对径向喷入的液体具有强烈的剪切作用,产生了强烈雾化作用,在此期间液体被多次切割、凝并及分散,从而得到进一步的混合。乳化柴油从液体出口排出,制得甲醇-柴油乳化燃料产品进行各种性能测试,其工艺流程见图2-10。

图2-10 超重力环境下甲醇柴油乳液制备工艺流程
1—水相储槽;2,4—离心泵;3—油相储槽;5—IS-RPB;6—产品储槽
2.4.1.3 稳定性能
稳定性作为乳化柴油最重要性质之一,其性能的好坏直接影响到乳化的效果,稳定性差的乳化柴油,就会出现分层,致使节能效率降低。通过考察甲醇含量、乳化剂含量、液体流量、超重力因子、HLB值、助溶剂类型和循环次数等对甲醇柴油乳液稳定时间的影响[4,28-31],得出如下规律:
①超重力因子和液体流量的增加提高了甲醇和柴油两股液体微元的湍动程度,有利于甲醇和柴油的乳化,延长了甲醇柴油乳液的稳定时间,采用非离子表面活性剂界面吸附拔河模型解释乳化剂的HLB值对甲醇柴油乳液稳定性的变化规律,得出最佳的HLB值为5.4,通过对撞击间距的考察,能够确定制备甲醇柴油乳液的旋转填料床内径与撞击面的“耦合”雾化切割半径;
②根据Prince混合膜理论,开发了新型复合乳化剂,得出不同助溶剂对甲醇柴油乳液稳定性的影响关系:正丁醇>正戊醇>异戊醇>正己醇>丙醇>无助溶剂;
③乳化剂含量的增加和乳状液循环次数的提高,有利于增强甲醇柴油乳液的稳定性,而甲醇含量的增加降低了甲醇柴油乳液的稳定性,甲醇含量为15%、乳化剂含量为3%、乳化剂HLB值为5.4,循环三次时,实验测得甲醇柴油乳液的稳定时间达30天以上。
2.4.1.4 流变性能
甲醇柴油乳液的流变性是发动机燃油的一个重要特性[30,32],对保证发动机的正常工作至关重要。它是衡量流体内部摩擦阻力大小的尺度,是流体内部阻碍其相对运动的一种特性,体现了流体抵抗剪切作用的能力。采用复合乳化剂条件下研究超重力环境下柴油-甲醇乳液的流变特性随油含量、乳化剂种类及含量等参数的影响规律[4]。研究表明:牛顿型复合乳化剂条件下,甲醇柴油乳液在各种组分配比下均近似牛顿流体,其黏度随着乳化剂含量及黏度的增加而增大;甲醇柴油乳液的黏度随着柴油含量的减少而增大。当其中乳化剂含量小于3%时,乳液黏度随乳化剂含量的增加而缓慢增大;当其中乳化剂含量高于3%时,乳液黏度随乳化剂含量而增大的幅度较大;当甲醇含量低于15%时,甲醇柴油乳液黏度为3.3~5.8mPa·s,满足压燃式发动机国家标准(GB/T 265)。
2.4.1.5 分散性能
乳化柴油中分散相的尺寸不仅关系到乳化柴油在柴油机中的燃烧效果,也关系到乳化柴油的稳定性和黏度,因此它是表征乳化柴油性能的一个重要的参数[33]。甲醇在柴油中分散得越均匀,分散的颗粒越微细,其在燃烧过程中的“微爆”效果则越佳,雾化效果越好。采用通过光学显微镜观察一定面积内甲醇柴油乳液中分散相-甲醇的个数和粒径大小,然后进行统计,用Sauter[34]平均直径D来表征分散度的概念,Sauter平均直径D是指乳化柴油中全部分散相液滴的体积与总表面积的比值,其值越小,表示相同体积的液体具有的表面积越大,分散度越高。
超重力制备甲醇柴油溶液分散特性[35]研究结果表明:甲醇乳化柴油分散相的平均粒径随超重力因子、柴油液体流量和乳化剂含量的增加而减小,但随甲醇含量的增加而增大;超重力环境下制备的甲醇柴油乳液分散相平均粒径为10~40μm,当超重力因子为208.1,柴油流量为70L/h和甲醇含量为15%时,甲醇乳化柴油中分散相甲醇的分散度为22μm,在实验操作条件下,应用MATLAB语言编制应用程序对实验数据的回归分析得出了超重力环境下甲醇乳化柴油分散相甲醇平均粒径的关联式(2-11),关联式的平均误差为4.2%,最小误差为0.2%,最大误差为8.9%,说明关联式拟合较好。
(2-11)
式中,D为分散相甲醇的平均粒径,μm;VA为甲醇的体积流量,L/h;θ为乳化剂的质量分数, %;c为甲醇的体积分数, %。
2.4.1.6 理化性质
焦纬洲等[36]在乳化剂的作用下,分别以质量分数为5%、10%、15%、20%、25%的甲醇与0#柴油在超重力环境下进行乳化制得甲醇柴油乳液。乳化剂以柴油和甲醇总质量的质量分数来计算,范围为1%~5%;超重力因子范围为26.5~373.2;液体流量为40~90L/h;甲醇含量为5%~25%。所得的甲醇柴油乳液按石油产品的国家标准分别进行密度、表面张力和腐蚀性等物化性质的检测,实验温度为(20±1)℃。
超重力场下制备甲醇柴油乳液的实验过程中测得甲醇乳化柴油的密度为0.825~0.851g/cm3,与柴油的密度0.835g/cm3相近,满足国家柴油标准;甲醇乳化柴油的表面张力随乳化剂和甲醇含量的增加而呈现不同程度的降低,有利于改善燃料的喷射雾化效果;采用新磨光的铜片浸泡在制备好的甲醇乳化柴油中(GB/T 5096),研究铜片表面的腐蚀性能。结果表明,超重力环境下制得的甲醇乳化柴油的铜片腐蚀性为中度变色,符合柴油腐蚀性要求;甲醇乳化柴油十六烷值随着甲醇含量的增加呈线性下降趋势,当甲醇含量增加至25%时,其十六烷值降至40以下,基于不改变内燃机结构考虑,当甲醇含量低于15%时,甲醇乳化柴油的十六烷值为43以上,满足柴油机对十六烷值的要求(GB/T 386)。
2.4.1.7 性能对比
(1)稳定性对比
对比高速分散器和超重机对甲醇乳化柴油的稳定性影响。当操作条件一致时,超重力技术和高速分散器分别制备甲醇柴油乳液的稳定时间为288h和220h,进一步证明超重力装置制备乳化柴油的稳定性优于高速分散器(参见图2-11)。主要是由于流体微元在超重力场中所受的力是均匀和连续的,而在高速分散器中流体微元所受的力是不均匀的,致使分散相-甲醇粒径分布很不均匀,所以稳定性较低[37]。

图2-11 相同操作条件下不同乳化装置稳定时间对比
(2)分散度对比
通过图2-12看出,随着甲醇含量的增加两种乳化装置制备甲醇柴油乳液分散相甲醇的粒径分布呈现递增的变化趋势,且分散相的平均粒径低于高速分散器,这主要与乳化装置的结构有关。对于超重力装置,甲醇和柴油流体在超重力环境下各个质点所受到的力是均匀的,而且在填料转子高速旋转所产生巨大剪切力的作用下使得甲醇和柴油有效乳化,致使制得的甲醇柴油乳液分散相粒径小且均匀;对于高速分散器,所有甲醇和柴油微元在烧杯中有效乳化的频率是不一致的,致使分散相粒径分布不均匀且平均粒径较大。这一点可以通过相同条件下两种乳化装置制备的甲醇柴油乳液分散相的显微摄影照片和分散相粒径分布得到论证(图2-12~图2-14)。图2-13为超重力装置制备甲醇柴油乳液的显微镜摄影照片,条件是甲醇含量为10%,乳化剂含量为4%,HLB值为5.4,液体流量为70L/h和超重力因子为208.1,其分散相平均粒径为14μm;图2-20为高速分散器制备甲醇柴油乳液的显微镜摄影照片,条件是甲醇含量为10%,乳化剂含量为4%,HLB值为5.4,转子转速为5×2800r/min和乳化时间为2min时,其分散相平均粒径为26μm。同时对比图2-13和图2-14可以看出,高速分散器制备的甲醇柴油乳液分散相粒径分布很不均匀。

图2-12 乳化装置对甲醇柴油乳液分散性的影响

图2-13 超重力装置甲醇柴油乳液分散相

图2-14 高速分散器制备甲醇柴油乳液分散相
图2-15为两种乳化装置制备甲醇柴油乳液分散相的粒径分布,操作参数是分别与图2-13和图2-14相对应。从图2-15中看出,在相近操作参数条件下,超重力装置制备的甲醇柴油乳液分散相的分布很窄,且呈现正态分布,分散相粒径范围为6~25μm,其平均粒径为14μm;对比高速分散器制备的醇乳化柴油中分散相的粒径分布较宽,且分布很不均匀,分散相粒径范围为1~58μm,其平均粒径为26μm,其主要原因分析同上。

图2-15 不同乳化装置分散相粒径分布
(3)运转功耗对比
间歇式高速分散器制备甲醇柴油乳液的适宜参数为:乳化时间2min,乳化甲醇柴油混合物的质量为50g,高速分散器的功率为360W;连续式超重力装置制备甲醇柴油乳液适宜参数为超重力因子208.1、柴油流量为70L/h,电机功率为750W。高速分散器制备甲醇柴油乳液单位时间生产每克甲醇柴油乳液的运转功耗为:360/(50×2)=3.6W/(g·min);超重力装置制备甲醇柴油乳液时,当甲醇含量为15%,乳化剂含量为3%时,甲醇柴油乳液换算成质量为70kg/h=1167g/min,则超重力装置(IS-RPB)生产甲醇柴油乳液的运转功耗为:750/1167=0.64W/(g·min),说明高速分散器的运转功耗要远远高于超重力乳化装置,即制备相同量的甲醇柴油乳液时,超重力装置的运转能耗仅为高速分散器的17.8%,且超重力装置具有连续操作、分散相粒径分布窄和平均粒径小等优点。
2.4.2 萃取
萃取是从稀溶液中提取物质的一种有效方法,广泛地应用于制药、湿法冶金、石油化工、工业废水、生物化工、核工业等领域。在液-液萃取过程中,两个液相的密度差小,而黏度和界面张力较大,两相的混合与分离比气-液传质过程(如吸收、精馏等)困难得多,为达到理想的萃取效果就需要萃取设备有很好的混合与萃取传质性能。IS-RPB在强化液-液混合方面十分有效,可作为萃取器应用于液-液萃取过程,本节主要介绍IS-RPB的萃取性能。
萃取操作是依靠不互溶的两液相间的混合与分相两个过程来实现,IS-RPB用于萃取过程实质上是将IS-RPB应用于萃取过程中的混合过程,利用其强化混合的特性来强化萃取传质过程。其操作示意图如图2-16所示。

图2-16 IS-RPB萃取操作示意图
由图2-16可以看出:IS-RPB完成萃取过程的混合操作是连续操作过程,而分相操作是间歇操作,由IS-RPB的混合与间歇分相操作组成了萃取单元操作。根据不同的分离目的及要求,可以用多个这样的萃取单元操作组成多级萃取,如多级错流萃取流程和多级逆流萃取流程。
刘有智、祁贵生等[38,39]以IS-RPB作为萃取器,进行了化学萃取传质性能和物理萃取传质性能的研究。
化学萃取传质性能的研究是以水-苯酚-磷酸三丁酯(煤油)为萃取体系,其中磷酸三丁酯(TBP)为萃取剂,煤油为稀释剂,苯酚为溶质;用级分配系数和萃取级效率来表征萃取效果。结果表明,级分配系数和萃取级效率随超重力因子、撞击初速、撞击角等操作参数值的增大而增大,其变化的趋势与IS-RPB混合效果增强的变化趋势相类似。在进行混合效果与级分配系数的关系研究中,已知10%TBP(煤油)萃取剂的平衡分配系数为48.8,则萃取级效率η=99.90%,接近于理论的平衡值,说明IS-RPB对萃取过程的传质强化效果。
物理萃取选用水-苯甲酸-煤油的萃取体系,其中水为萃取剂,0.15~0.2g/L的苯甲酸为溶质。水相中的苯甲酸浓度采用酸碱滴定法进行测定。由于苯甲酸在两相的分配比并不为一常数,故用萃取级效率来考察操作参数对萃取效果的影响。研究结果表明:随着IS-RPB撞击初速及超重力因子增加,萃取效果呈增加的趋势,可以得到99%以上的萃取传质级效率。
IS-RPB萃取的应用研究已在含酚废水的处理、醋酸萃取浓缩和湿法炼铜等方面取得较好的效果。祁贵生等用IS-RPB对实际的含酚废水(苯酚浓度4994mg/L)进行了萃取研究,采用磷酸三丁酯(TBP)为萃取剂,煤油作为稀释剂。萃取操作条件为:单级萃取处理,相比为1,撞击初速12.58m/s,超重力因子240,由于IS-RPB优良的萃取传质性能使得在单级萃取过程完成后,级分配系数已接近于平衡分配系数,得到了良好的萃取效果。
祁贵生等[39]以IS-RPB为萃取设备,20%TBP(煤油为稀释剂)为萃取剂,萃取醋酸稀溶液(浓度31.2g/L),撞击初速5.95~7.9m/s,超重力因子136~240,萃取级效率在95.5%~97.1%。再次验证了IS-RPB优良的萃取传质性能。另外,选用国内某大型湿法炼铜厂浸出的铜液,以LIX984N为萃取剂,煤油为稀释剂,以IS-RPB为萃取器和反萃取器的实验研究结果表明:在萃取剂体积分数为5%、相比为1∶1、超重力因子为135、流量为80L/h的情况下,萃取效率达到98.8%;在两相分离后,以IS-RPB为反萃取器和180g/L的H2SO4为反萃剂对富含铜的油相(LIX984N+煤油)进行反萃取操作,在相比为1∶1、超重力因子为135、流量为80L/h的工艺条件下,一级反萃取效果良好,反萃取率为95%。反萃取操作完成,分相后萃取剂相可循环使用。将IS-RPB用于铜液的萃取,能大大提高铜萃取率,节省运行成本,操作简便,该设备的投入使用,将大力促进湿法冶炼铜行业的发展,在我国铜资源不足问题日益突出的情况下显得尤为重要,对我国铜工业的可持续发展具有重要意义。
IS-RPB作为连续萃取器其处理能力比通用的萃取设备大得多,用比负荷(单位时间内通过单位设备截面的两相总流量)来对比有如下的结果,见表2-1。
表2-1 主要的几种萃取设备与IS-RPB的比负荷

从表2-1中可以看出,IS-RPB的处理能力很大,在处理能力相同的条件下,IS-RPB可以极大地减少萃取设备的体积。
总之,IS-RPB既可以作为连续萃取器,也可以作为连续反萃取器,液体在设备中的停留时间短,无返混,设备中的液体滞留量极少,对处理特殊物料及更换萃取剂等极为方便。设备体积小,处理能力大,萃取效率几乎达到平衡效率,这些特点必将引起萃取技术的发展。
2.4.3 液膜分离
液膜分离由于其液膜比表面积大、分离效率高、成本低等特点,成为分离、纯化与浓缩溶质等有效手段,在湿法冶金、废水处理、有机物分离、生物制品分离与生物医药分离等领域有着广泛的应用前景。而传统制备乳状液膜技术是在强烈搅拌混合器内完成,其设备庞大、效率不高、制膜时间长、消耗能量高,属于间歇制膜工艺,液膜尺寸和稳定性不宜保障,特别在后续使用过程中,长时间的滞留会造成膜的稳定性下降。
基于IS-RPB的高传质特性,中北大学首次提出了IS-RPB制乳工艺与技术,同时将IS-RPB也作为提取装置,开展了含酚、含苯胺废水的液膜分离研究。
液膜制备过程(即制乳过程)是将膜相溶液(Span80、液体石蜡、煤油)与内相溶液(氢氧化钠溶液等)以一定的比例进入IS-RPB,两种液流得到充分的接触,形成较均一的乳状液膜。其性能以制乳率(以氢氧化钠为示踪剂,通过测定未进入原始乳液外部的氢氧化钠的总量来计算制乳率)来衡量制乳过程的效果。
液膜分离过程(即提取过程)是把制得的液膜乳液和配制的含酚量为1000mg/L含酚溶液分别送入IS-RPB完成酚的提取过程。静置分层后,上层液为提取后的乳液,下层液为脱酚后的废水。
杨利锐等[40-43]分别采用IS-RPB和普通搅拌槽为制乳设备,进行了制乳率、膜稳定性、膜溶胀率的比较。实验采用由Span80、液体石蜡、煤油组成膜相,其质量分数分别为:4%、3%和93%;NaOH溶液的质量分数为5%,油水比为1∶1.5;IS-RPB的超重力因子(β)为346.7;制乳流量(油相)为60L/h;普通搅拌制乳使用JB90-D型强力电动搅拌机作为普通制乳设备,制乳转速为2800r/min;每次制乳量为40L。研究表明:利用IS-RPB作为制乳装置进行乳液的制备可以瞬间制乳且制乳效率可达99.90%。而传统高速搅拌器制乳效率也较高,最高达到99.77%,但其制乳时间较长,达到最高制乳率需要20min左右。
利用IS-RPB和高速搅拌器两种方法制得的液膜稳定性表明,通过IS-RPB制得的乳液破损率要明显低于高速搅拌器制得乳液的破损率。高速搅拌器制得的乳液的平均破损率是IS-RPB制得的乳液平均破损率的10倍左右。利用IS-RPB作为脱酚提取装置,可以瞬间完成且脱酚效率可达99.7%以上。而传统的高速搅拌方法脱酚效率不太高,最高只达89.57%,并且脱酚时间较长,达到最高脱酚率的提取时间需要25min左右。
李倩甜[44]采用IS-RPB乳状液膜法处理苯胺废水进行研究,考察IS-RPB操作条件对乳液稳定性和苯胺去除率的影响,得到最佳工艺条件为:Span-80用量4%、煤油96%、内相盐酸浓度1mol/L、油内比(油相和内相体积比)Roi=1∶1、乳水比(乳液和外相体积比)Rew=1∶20、初始外相pH=9、超重力因子65、撞击初速9.45m/s。在此工艺参数下,提取10min,苯胺去除率可达99.5%左右,剩余苯胺浓度降至5mg/L,达到国家规定的三级排放标准。最后比较IS-RPB和传统搅拌两种制乳方式制得的乳液性能,发现IS-RPB制乳时间大大缩短,乳液稳定性明显提高,苯胺去除效果明显,为液膜技术的进一步发展提供新的思路。
因此,IS-RPB作为高效的制乳、提取设备,具有操作时间短、效率高、易于放大、可连续化操作的优点,此技术适应任何形式(包括W/O型、O/W型)的乳液的制备和提取过程,有望在液膜分离技术的工业化生产中具有广阔的应用前景。
2.5 反应过程强化
当反应系统由两种互溶度较小的液体构成时,参与反应的反应物分别存在于两个液相中,这样的非均相反应即为液-液反应。液-液反应广泛应用于工业过程,常见的液-液反应有硝化、磺化、缩合、乳液聚合、烃化反应等[1]。对于这类反应,若将反应物置于溶剂相内,然后通过相界面的溶解和传质而进入反应相内,使反应物在反应相内的浓度受到分配系数和传质速度的控制,从而控制反应速率和反应释放热。
液-液非均相反应不但涉及反应器内两相间的反应速率,也关系到连续相和分散相间的相平衡、传质以及液滴分散、凝聚等过程。液-液反应过程中同时存在反应物在相界处的溶解、相间传质反应过程,如果反应在某液相内进行,也可根据相间传质速率和反应速率的相对大小,用双膜理论把液-液相反应划分为慢速、中速、快速、瞬间反应等几种。液-液非均相反应通常认为反应分别在液滴分散相内或连续相内进行,但实际反应速率往往取决于传质过程,并且与相界面面积,也就是液滴大小有关。在此以纳米氢氧化镁、重氮盐水解制酚、纳米Fe3O4、纳米零价铁、纳米2,4-二羟基苯甲酸铜等反应过程为例,阐述其过程强化特性和应用性能。
2.5.1 纳米氢氧化镁
随着人们安全和环境保护意识的逐渐增强,开发绿色环保型的阻燃剂成为阻燃领域的发展方向。氢氧化镁是一种无卤、绿色友好型阻燃剂,因其具有阻燃、抑烟、无毒、无腐蚀、热稳定性好和促基材成炭作用好等优点,在国内外受到广泛关注。
目前,工业上主要采用液相沉淀法制备氢氧化镁,该法操作简便,设备简单,原料易得,生产成本低,产物纯度高。但该法通常采用传统搅拌釜为反应器,由于反应器结构对反应物微观混合的局限性,导致产物存在粒径分布不均匀和批次重现性差等问题。同时氢氧化镁浆料的固液分离难以及氢氧化镁的表面有机化改性又是液相沉淀法制备纳米氢氧化镁工业化应用的关键技术问题。因此,研究开发一种制备高品质纳米氢氧化镁的高效混合反应器,且开发出一步合成形貌规则、高分散、表面有机化的纳米氢氧化镁的工艺路线,同时提高氢氧化镁浆料的沉降性能,是液相沉淀法制备纳米氢氧化镁工业化应用的关键技术[45,46]。
2.5.1.1 工艺流程
撞击流-旋转填料床(IS-RPB)制备纳米氢氧化镁的工艺流程如图2-17所示。在搅拌条件下,在储液槽1和2中分别配置一定浓度的氯化镁溶液和氢氧化钠溶液,开启加热器,待原料液温度上升到60℃以后,开启IS-RPB,控制转速,设备运行稳定后,同时开启氯化镁和氢氧化钠原料液输送泵4,调节流量为40L/h,使两股原料液在进液管的喷嘴处以8.47m/s的初速相向撞击,形成扇形液面。撞击后的溶液进入以超重力因子为55.31的转速旋转的环形填料中,形成氢氧化镁浆料,经板框压滤机过滤、洗涤、干燥、研磨后制得氢氧化镁粉体。

图2-17 撞击流-旋转填料床(IS-RPB)制备纳米氢氧化镁工艺流程
1,2—储液槽;3—搅拌器;4—泵;5—阀门; 6—流量计;7—撞击流-旋转填料床(IS-RPB); 8—收集槽
经过大量的实验研究发现,IS-RPB使成核过程可控,粒度分布窄化。但采用该反应器制备纳米氢氧化镁,并不能实质性地改变氢氧化镁表面的“亲水疏油”的结构。在线改性(又称沉淀改性)具有同时完成制备和改性的技术优势,可有效改变氢氧化镁表面的“亲水疏油”的结构,同时提高料浆的过滤性能,降低生产能耗,弥补IS-RPB所存在的不足。二者协同所形成的超重力在线改性技术可解决液相沉淀法工业化制备纳米氢氧化镁阻燃剂的关键性问题。
2.5.1.2 传统沉淀法与超重力沉淀法的对比
通过对传统沉淀法与超重力沉淀法进行对比发现,超重力沉淀法制备的氢氧化镁浆料沉降速度是正向沉淀法的4.7倍,是反向沉淀法的12.4倍,是双向沉淀法的2.1倍,见图2-18。因此,采用超重力沉淀法解决了传统沉淀法制备氢氧化镁存在的浆料分离难和产品粒径分布宽等问题,见图2-19。

图2-18 制备方法对氢氧化镁浆料沉降速度的影响

图2-19 制备方法对产物粒径分布的影响
2.5.1.3 氢氧化镁的性能表征
采用扫描电子显微镜和接触角测量仪对未改性Mg(OH)2和油酸改性Mg(OH)2的形貌、粒径和表面润湿性进行对比,如图2-20和图2-21所示。结果发现,未改性Mg(OH)2微晶界限模糊,氢氧化镁晶体的形状不规则,粒度分布不均匀,且出现许多片状交叉在一起形成大的团聚体。经油酸改性后的氢氧化镁呈规则的六方薄片状,粒径约为30nm,粒径分布均匀,分散性好,基本无团聚现象。且油酸改性后的氢氧化镁其接触角大于110°,远大于未改性氢氧化镁的接触角(小于10°),这说明改性后的氢氧化镁表面的亲水性降低,亲油性增大。

图2-20 Mg(OH)2和改性Mg(OH)2的FESEM图

图2-21 (a)Mg(OH)2、(b)油酸改性后的Mg(OH)2
2.5.1.4 氢氧化镁纯度检测
经改性后的氢氧化镁,氧化钙的含量均小于1.0%,盐酸不溶物的含量在0.02%~0.06%之间,水分含量大部分在0.93%~1.49%之间,Cl-含量在0.293%~0.325%之间,铁离子含量在7.03×10-5%~8.47×10-5%,筛分余物含量在0.463%~0.538%[45,46],氢氧化镁粉体的激光粒径在226~277nm,小于0.5μm,氢氧化镁粉体的灼烧失量[47]范围为9.41%~11.08%之间,优于未改性氢氧化镁。
2.5.1.5 纳米氢氧化镁阻燃聚丙烯的应用研究
聚丙烯(Polypropylene,PP)作为产量最大的高分子材料之一,由于其具有价格低廉、易于成型、无毒、耐化学腐蚀性好、综合力学性能优良及性价比高等特点,使其在包装业、纺织业、制造业、电子行业、制药行业等领域得到广泛应用。近年来,随着聚丙烯聚合技术的快速发展,其力学性能、表面光泽性、耐热性和电绝缘性等得到了更大的提高,使其成为家电、汽车、民用建筑等行业的主导材料。
由于聚丙烯的极限氧指数(LOI)仅为17.0%~17.5%,极易燃烧,且在燃烧过程中不易成炭,产生的熔滴又极易传播火焰,并产生大量的烟雾和有毒气体,这对于扩大聚丙烯的应用是个障碍,尤其是用作建筑、车辆和电绝缘材料时,对聚丙烯的阻燃要求很高。因此,为了保证人民的生命、财产安全,赋予聚丙烯阻燃性能显得极其重要。
经表面改性后的无机添加型阻燃剂Mg(OH)2的表面亲油性明显提高,进而使其与聚丙烯的相容性提高,采用其阻燃聚丙烯,在保证阻燃效果的同时不会影响聚丙烯的力学性能。经改性后的Mg(OH)2进行了阻燃聚丙烯的应用研究,通过燃烧性能(氧指数)和力学性能测试(拉伸性能)发现:
(1)氧指数分析
超重力沉淀法制备的纳米氢氧化镁添加到聚丙烯中,氧指数均有所增加,其值均大于添加市售氢氧化镁后复合材料的氧指数值,而超重力沉淀法制备的Mg(OH)2阻燃剂氧指数值与前两者相比有较为明显的增大。这证明添加型阻燃剂的粒度对其阻燃性能影响较为明显,粒度小且分布较窄会使得阻燃剂在材料聚丙烯中均匀分散,从而使阻燃性能得到较大的改善。而氢氧化镁改性前后,添加到PP中LOI值也有较大的改变,说明改性后的Mg(OH)2阻燃剂与聚丙烯的界面差减小,使二者相容性有明显的改善,从而使得阻燃性能得到进一步的加强。
(2)力学性能分析
添加Mg(OH)2阻燃剂后,材料的力学性能均有所下降。而采用传统沉淀法制备的氢氧化镁阻燃剂添加30%后,拉伸强度和断裂伸长率减小了15.23%和24.34%,相比市售Mg(OH)2阻燃剂减小39.28%和28.68%,对PP力学性能的影响相对较小。采用超重力沉淀法制备的Mg(OH)2阻燃剂添加30%后,拉伸强度和断裂伸长率则分别减小了11.76%和22.69%。由此证明超细氢氧化镁阻燃剂的粒径小和粒度分布窄能够尽量减少对材料力学性能的恶化。同时超重力沉淀法制备超细Mg(OH)2阻燃剂时,机械改性减弱了其亲水性,在聚丙烯中分散性和相容性更好,对材料的力学性能影响最小。
2.5.2 重氮盐水解制酚
2.5.2.1 研究背景
芳烃基重氮盐的水解反应是合成相应酚类产品的重要环节,在化学合成方面占据十分重要的地位,该路线制备对酚具有原料价廉、产物易分离、产品纯度高等优点,其产品大多是国民经济发展需要的重要精细化工中间体(如愈创木酚、间甲酚、对羟基苯甲醛等),广泛应用于医药、农药、香料、化妆品、液晶、电镀等领域。
重氮盐水解制酚时,主、副反应属平行连串反应,可用式(2-12)和(2-13)表示:
(2-12)
(2-13)
据文献[48]报道,耦合反应的活化能为59.36~71.89kJ·mol-1,水解反应的活化能为95.3~138.78kJ·mol-1,反应温度每升高10℃,耦合反应速率增加2~2.4倍,水解反应速率增加3.1~5.3倍,可见,从活化能的角度分析,升高温度有利于主反应对副反应的竞争。
目前芳烃基重氮盐的水解反应均采用传统釜式水解法,这种水解方式不可避免地存在如下问题:随着反应的进行,生成的酚在反应体系中的浓度越来越高,副反应生成偶氮化合物的概率越来越大;重氮盐的酸溶液采用滴加的方式同反应釜中的溶液接触,滴加速度太慢,降低工业生产的效率;另外,反应物料在釜内升温速度慢,由于副反应较主反应有较低的活化能,使得反应在升温阶段均处于对副反应有利的低温阶段。以上原因造成传统釜式水解法生产时间长、产物收率低、副产物多、能耗高等问题。
2.5.2.2 重氮盐水解动力学分析
(1)从活化能的角度分析
升高温度有利于主反应对副反应的竞争,一般来说,升高温度主要有两种途径,如图2-22所示[49]。

图2-22 两种升温方法的温度变化
曲线Ⅰ表示:先加热部分反应物料到反应温度,再滴加另一部分物料,这样才能保证整个水解过程都在最佳的温度条件下进行,以确保反应温度始终处于对水解反应有利的高温范围。曲线Ⅱ表示:反应物料一次性全部加入反应器后升温,在t<t0时间内均处于升温过程,此阶段有利于副反应,因此此种情况下产物选择性较低。如果反应物料一次性全部加入,通过采取特殊的升温措施,能够将t0缩短到可以忽略(缩短升温过程,实现瞬间升温),即如果将水解液和重氮盐溶液一次性加料,而且达到曲线Ⅰ的升温效果,这样既省去了滴加原料所用的长时间,又满足了瞬间升温的要求,这便是动力学要求的最佳效果。
(2)从加料方式与分布分析
化学反应是在分子尺度上进行的过程,无论对简单反应还是复杂反应,分子尺度上的混合(即微观混合)、相间传质、分散相在连续相中的分散均匀性都可以影响化学反应的转化率和选择性。
传统釜式水解法采取的滴加部分原料的方法可满足快速升温的条件。冷的重氮盐溶液滴入高速搅拌的高温水解液中,先分散后反应很重要,要保证重氮盐充分分散于水解液中,最佳的效果是每个重氮盐分子周围都是水分子。若重氮盐在水解液中不能快速、均匀分散,必然形成部分重氮盐小液滴,原料液滴表面水解生成的产物会迅速与原料液滴内部未反应的重氮盐发生耦合副反应,从而降低产物收率。
在水解过程中,随着水解反应的进行,体系内产物酚的浓度会逐渐增加,必然加大新滴入原料与反应器内高浓度酚发生副反应的概率。从产物的浓度考虑,必须采取措施将生成的产物酚及时移走,这样才能确保减少副反应,提高主产物收率。
上述分析总结出两点:一是将原料重氮盐均匀快速分散于水解液中,确保先分散后反应;二是采取适宜的措施将产物酚及时从体系中移出,降低体系中产物浓度,降低副反应发生的概率。理想的分散图如图2-23所示。

图2-23 理想的原料与产物分散图
(3)产物的移出方式
通常从体系中移出酚有两种方式,一是水蒸气蒸馏法[50,51]:将水解过程产生的酚与水蒸气一起蒸出,使体系中产物浓度降低,从而降低副反应发生的概率;二是相转移法,将重氮盐滴入水与有机溶剂的非均相混合物中,在水相生成的产物迅速转移至油相,相当于降低了水相中酚的浓度,减少了副产物的生成。该法一般适用于不易挥发、在水中溶解度远小于油中溶解度的酚类。
以上两种产物移出方式中,水蒸气蒸馏法对降低体系中酚的浓度效果显著,但该法温度高,时间长能耗高,大量水蒸气同产物一同蒸出后,经分离会产生更多的含酚废水;相转移法需要增加后续溶剂的分离与回收等工序。
由动力学分析可知,要同时提高水解反应的转化率和主产物的选择性,必须提高主反应对副反应的竞争,从动力学的角度出发必须解决以下几个关键问题:
①解决快速升温:将原料在最短的时间内升高到所需的水解温度,缩短升温过程,使反应始终处于对主反应有利的高温范围。解决此问题的传统法是将重氮盐滴加到高温的水解液中,但此法时间长、能耗高。
②解决快速分散:将滴入的重氮盐快速分散到水解液中,先分散后反应。滴加重氮盐的方式在一定程度上解决了分散问题,但在釜式反应器中仅靠搅拌的分散作用有限,一定程度的原料累积必然导致副反应的发生。
③及时移出产物酚:传统法是采用水蒸气蒸馏法将酚及时从体系中移出,该法采用高温蒸馏产生水蒸气,耗时长,必然带来能耗高,同时增加了后续分离等。
作为一种新的过程强化设备,撞击流旋转填料床具有微观混合特性和高效的传质传热特性,解决传统水解反应器存在的快速分散和快速升温问题;管式反应器具有平推流特点,可有效抑制物料返混,减少副反应发生的概率,同时控制物料在管式反应器中的停留时间使得水解反应更加完全。将撞击流旋转填料床和管式耦合反应器(IS-RPB/PFR)作为水解反应的核心反应器,具备加热速度快、分散效果好、返混程度小等特征,满足重氮盐水解动力学要求。
2.5.2.3 工艺流程
IS-RPB/PFR水解反应流程简图见图2-24。将一定配比的水解液放入储罐2,用空气压缩机1将水解液打入套管预热器5预热至85~90℃,经转子流量计以一定流速进入撞击流-旋转填料床6的液体分布器喷口A;冷的重氮盐水溶液放入储罐3,用空气压缩机输送,经转子流量计4以与水解液相同的流量直接进入液体分布器喷口B,两股液体以相同流量同轴对撞。进液前开启导热油炉,控制导热油温度到所需水解温度。两股液体对撞后迅速分散在填料中,并在此期间液体被多次切割、聚并及分散,从而得到进一步的混合,确保重氮盐均匀分散于水解液中。之后混合液在离心力的作用下被甩到填料床内壳,经旋转床套管进一步加热到所需的水解温度,在重力的作用下汇集到液体出口处,经出口排出进入长度为30m、内径为21mm的管式反应器7中继续将水解反应进行完全(管式反应器温度用油浴保温,与水解温度保持一致),反应完的混合液流出管式反应器7后趁热用活性炭过滤器8滤掉漂浮在上层的焦油副产物,再进入列管冷凝器9冷凝,收集冷凝后的产物混合液,并进行后处理得到纯品。

图2-24 重氮盐水解IS-RPB/PFR流程简图
1—空气压缩机;2—水解液存储压力罐;3—重氮液存储压力罐;4—液体转子流量计; 5—套管预热器;6—撞击流-旋转填料床;7—管式反应器(设有加热夹套);8—活性炭过滤器;9—列管冷凝器
2.5.2.4 实施效果
以重氮盐水解制备对苯二酚为例,采用IS-RPB/PFR水解反应器达到了缩短反应时间、提高收率和生产效率的目的[52]。与传统釜式反应器的对比结果见表2-2。
表2-2 釜式反应器与组合反应器水解工艺的比较

由表2-2可知,取0.53kg对氨基苯酚进行重氮盐水解制备对苯二酚,与釜式反应器相比,采用组合反应器具有一定的优势:收率相当,而反应时间由3~4h缩短到0.24h内,极大地缩短了水解时间,相应地也节约了能耗;设备体积显著减小,同样处理0.53kg原料,釜式反应器体积为35.333L,而组合反应器则为12.116L,约为釜式反应器体积的1/3;生产效率也得到了极大的提高,单位时间产量由0.11kg/h提高到了1.31kg/h,整整提高了约12倍。
2.5.3 磁性纳米Fe3O4
2.5.3.1 背景
磁性纳米粒子(如Fe3O4)既具有纳米材料的特性如表面效应、小尺寸效应、量子效应和宏观量子隧道效应,又具有良好的磁导向性、超顺磁性和生物相容性等特殊性质,使得其广泛应用于磁记录材料、磁流体、磁催化、巨磁电阻材料、磁成像、传感器、雷达吸波材料以及生物医药等领域,发展批量连续制备磁性纳米粒子并付诸应用受到人们的极大关注。目前,已经发展了许多种制备磁性纳米粒子的方法,如机械球磨法、水热法、溶胶-凝胶法、微乳液法和共沉淀法等。近年来,快速反应沉淀法已成为制备磁性Fe3O4纳米粒子的重要方法,被认为是一种低成本、可规模化制备Fe3O4纳米粒子的新技术。然而,在传统化学反应器中分子尺度上的传递和混合速率常慢于成核速率,导致成核和生长过程处在分子尺度上的不均匀性环境,因而存在粒径大、粒度分布宽、形貌难控、批次重复性差、过程放大效应大等工业性技术难题。
近十多年来,人们一直致力于研究和开发能够高度强化传质和混合的新型反应器。撞击流-旋转填料床(IS-RPB)是适用于液-液混合接触的过程强化的新型设备。其原理是利用两股高速射流相向撞击,经撞击混合形成的撞击雾面沿径向进入旋转填料床内侧,两股高速撞击的射流在强大离心力作用下,巨大的剪切力使液体撕裂为纳米级的膜、丝和滴,产生很大和快速更新的相界面,微观混合与传质过程得到极大强化。由前面可知,团聚模型初步估算的IS-RPB内微观混合均匀特征时间tm约在0.1~0.01ms,可见,超重力环境下微观混合均匀特征时间tm远小于成核诱导期特征时间tind。可以使反应系达到理想均匀成核环境,均一的成核速率,使颗粒呈现出较窄的粒径分布。
在制备Fe3O4的过程中,首先按照化学计量比配置一定浓度的铁盐混合溶液和碱液,然后等体积的两股反应物料通过液体分布器的喷嘴等速撞击后喷射到旋转填料床的内缘上,在任意一个时刻铁盐混合溶液和碱液都是按照设定的比例进行混合后反应生成Fe3O4沉淀,不存在传统的搅拌反应器中将碱液逐步加入到铁盐混合溶液的过程中产生的过饱和度稀释的问题,且生成的Fe3O4粒子在IS-RPB中无反混,不会对后续物料产生影响。因此,利用IS-RPB反应器强大的微观混合性能,可以使反应体系达到较高且分布均匀的过饱和度以及小于成核诱导时间的微观混合时间,由此可以制备出粒径小且分布均匀的Fe3O4纳米粒子,且具有反应时间短、制备成本低、易于工业化放大生产(与常规方法相比可提高4~20倍)等优点。
2.5.3.2 工艺流程
采用IS-RPB为反应器,以NaOH为沉淀剂,FeCl2·4H2O和FeCl3·6H2O为铁源采用共沉淀法制备Fe3O4纳米粒子,其反应原理为:
(2-14)
IS-RPB制备Fe3O4纳米粒子的工艺流程见图2-25,称取一定质量的FeCl3·6H2O和FeCl2·4H2O,按照Fe3+与Fe2+的摩尔比为1.8∶1配置一定浓度的铁盐混合溶液;按照OH-与Fe3+的摩尔比为6∶1配制一定浓度的NaOH溶液;将铁盐混合溶液和NaOH溶液分别加入到原料储槽5和6中,预热到80℃,启动离心泵将液体经流量计3输送入IS-RPB主体装置7中,等速的两股原料液通过两个液体分布器相向撞击,在两喷嘴的中间位置形成了撞击区,进行初步混合反应,撞击形成的扇形雾面进入旋转的填料床,液体在离心力的作用下沿填料孔隙由转子内缘向转子外缘流动,并在填料层中相互混合反应,反应物在填料外缘处甩出到外壳上,最后在重力作用下汇集到液体出口流出,反应在氮气保护下进行。反应结束后,磁性分离反应物,并用蒸馏水反复洗涤至中性,真空干燥,得磁性Fe3O4纳米粒子。

图2-25 IS-RPB制备Fe3O4纳米粒子的工艺流程
1—氮气瓶;2—减压阀;3—转子流量计;4—阀门;5—铁盐储槽;6—碱液储槽;7—IS-RPB;8—产物储槽
2.5.3.3 结果分析
通过考察超重力因子、撞击初速以及反应物的浓度对所制备的Fe3O4纳米粒子粒径及其分布的影响,结果表明Fe3O4纳米粒子的粒径随着超重力因子、撞击初速度以及反应物FeCl3·6H2O浓度的增大而减小。在Fe3O4晶核形成之前,较高的超重力因子和撞击初速度使液体微元之间的相对速度较大产生强大的微观混合效果,有利于生成较高且分布均匀的过饱和度。并且反应物FeCl3·6H2O浓度增大,这些变化都加快了成核速率,导致Fe3O4纳米粒子的粒径减小,这与反应沉淀法制备Fe3O4的热力学和动力学分析结果相吻合。根据所制备的Fe3O4纳米粒子的晶体组成、形貌、粒径及粒径分布得到IS-RPB制备Fe3O4纳米粒子的最佳操作条件为超重力因子为65.32、撞击初速为9.43m/s、反应物FeCl3·6H2O浓度为0.321mol/L。在此条件下,IS-RPB成功地制备出平均粒径约为9nm的Fe3O4纳米粒子。与传统的Fe3O4纳米粒子的制备方法不同(如水热法、球磨法等),在此最优参数下,IS-RPB能够以2.23kg/h的生产能力连续制备Fe3O4纳米粒子[53]。
采用IS-RPB在最佳工艺条件制备的Fe3O4纳米粒子的形貌及粒径分布如图2-26所示,所制备的Fe3O4纳米粒子主要为球形结构,粒子大小约为9nm,且分散性较好、粒径分布较窄[图2-26(b)]。此外,所制备的Fe3O4纳米粒子在室温下均表现为超顺磁性,且Fe3O4纳米粒子的饱和磁化强度为60.5emu/g(图2-27)。这一特性使得所制备的Fe3O4纳米粒子有较广泛的应用领域,如药物传递、生物分离以及磁共振成像等[54]。这一点也与当Fe3O4纳米粒子粒径小于临界尺寸25nm时具有超顺磁性的结论是一致的[55]。

图2-26 (a)Fe3O4纳米粒子的TEM图及(b)Fe3O4纳米粒子的粒径分布图

图2-27 Fe3O4纳米粒子的磁滞回线曲线图
2.5.3.4 应用
随着社会经济的发展和人民生活水平的提高,水中重金属离子的检测与去除问题备受关注。磁性纳米材料由于具有纳米材料和磁性能的双重特性,其纳米材料特性具有高比表面积和丰富的与重金属相互作用的活性位点;其磁性能可以在外加磁场吸引的作用下快速地实现回收分离。这个“双重特性”使其在水中重金属离子的检测和去除方面展现出广泛的应用前景。
中北大学将IS-RPB制备的Fe3O4纳米粒子作为纳米吸附剂材料用于对水中重金属Pb(Ⅱ)和Cd(Ⅱ)的去除,IS-RPB制备的Fe3O4纳米粒子对Pb(Ⅱ)和Cd(Ⅱ)的最大吸附容量分别为30.47mg/g和13.04mg/g。为了提高Fe3O4纳米粒子对重金属的吸附容量,利用壳聚糖的pH响应性,以IS-RPB为反应器,采用超重力反应沉淀法一步原位制备出粒径约为18nm的包埋结构的超顺磁性壳聚糖基磁性纳米粒子(Fe3O4/CS),其饱和磁化强度为33.5emu/g,制备效率为3.43kg/h。Fe3O4/CS纳米粒子对Pb(Ⅱ)和Cd(Ⅱ)的吸附过程属于单分子层吸附,最大吸附容量分别为79.24mg/g和36.42mg/g。
此外,将所制备的磁性Fe3O4和Fe3O4/CS纳米粒子作为电极修饰材料,采用阳极溶出伏安法实现了对Pb(Ⅱ)、Hg(Ⅱ)、Cu(Ⅱ)和Cd(Ⅱ)四种重金属离子的单独和同时检测,并且对Pb(Ⅱ)表现出较高的检测灵敏度和选择性[56]。
通过超重力过程强化技术可以连续制备、可重复利用的磁性纳米吸附剂材料和重金属检测的传感器,该方法具有制备工艺简单、成本低、制备时间短、可快速批量生产,是一种具有工业应用潜力的制备方法。
2.5.4 纳米零价铁
2.5.4.1 背景
针对传统搅拌式反应器在纳米零价铁制备过程中存在混合不均匀、颗粒粒径分布不均匀、滴加式进料难以大批量生产等问题,利用撞击流-旋转填料床(IS-RPB)能够强化微观混合、反应,实现连续进料的特点,在IS-RPB中批量、连续制备颗粒粒径均匀的纳米零价铁[57]。
利用IS-RPB能够实现纳米零价铁的批量、连续化生产,但制备出来的纳米零价铁在与废水反应之前仍需洗涤、分离、储存。而洗涤、分离、储存等过程仍需耗费巨大的水、电等人力、物力。为进一步简化纳米零价铁的制备及使用过程,提高纳米零价铁的利用率,采用撞击流-旋转填料床将纳米零价铁的生成反应与纳米零价铁还原硝基苯的反应耦合在一起,实现超重力制备纳米零价铁并同步处理含硝基苯废水。本方法变多步为一步,避免了常规处理方法纳米零价铁制备过程中的洗涤、分离、干燥、储存等繁杂操作,极大地简化了制备及使用步骤,有效降低废水处理成本。实验完成,可为含硝基苯废水的处理提供一种简便、高效、低成本的处理方法。
2.5.4.2 工艺流程
利用IS-RPB制备纳米零价铁并降解硝基苯废水的反应原理见式(2-15)和式(2-16),其工艺流程如图2-28所示。先将一定量的硫酸亚铁溶解于3.0L自来水中配制成0.1mol/L含铁离子溶液,调节溶液pH值至4.0后置于储液槽1中;将一定量的硼氢化钠溶解于3.0L水中配成0.2mol/L的还原剂溶液,置于储液槽5中。设置撞击流旋转填料床的转速为800r/min。储液槽1和5中的两股液体由泵打入撞击流-旋转填料床4中,两股液体体积流量相等,经液体流量计计量调至40L/h后由喷嘴喷出,在撞击区内进行初次快速碰撞、混合、反应;随后液体沿径向由内向外运动进入到高速旋转的填料层中,被旋转的填料高速碰撞、剪切,流体之间进行二次深度均匀混合、反应;混合反应后的液体最后被甩出,沿旋转填料床外壳内壁流至出液口,排入储液槽8[58]。
(2-15)

图2-28 超重力法制备纳米零价铁工艺流程
1,5,8—储液槽;2,6—泵;3,7—液体流量计;4—撞击流-旋转填料床;9—电机
纳米零价铁与硝基苯的反应式:
(2-16)
制备出来纳米零价铁,先用磁铁将其从反应液中分离出来,得到黑色纳米零价铁固体颗粒。随后,将黑色固体颗粒加入适量清水中,超声洗涤5min以去除颗粒间包覆的其他离子。超声之后,用磁铁将其与液体分离。如此,反复多次,直到洗涤溶液的pH值为中性。洗涤完成后,将纳米零价铁与液体分离开,浓缩成浆料转移到小口黑色样品瓶中,4℃下低温保存、备用。部分样品进行真空干燥,用以检测分析。
2.5.4.3 结果分析
图2-29为超重力法制备出来的纳米零价铁与常规搅拌法制备出来的纳米零价铁TEM图。对比两图可知,超重力法制备出来的纳米零价铁颗粒粒度分布均匀,颗粒粒径在10~20nm左右,颗粒间的团聚现象明显减少,颗粒分散性较好。硼氢化钠还原二价铁离子生成零价铁单质,是一个快速的反应沉淀过程。反应沉淀过程中,化学反应与晶粒成核、生长串联进行,而化学反应通常比较迅速,过程多为微观混合所控制。由结晶化学可知,晶粒的形成包括成核、生长、团聚等过程。成核时间称为成核特征时间(tN),其值约为1ms级。成核特征时间与反应器的微观混合均化特征时间(tm)的相对大小,影响着晶粒的粒径、均匀性。当tN<tm时,微观混合未完全,既已有晶核形成,成核和生长在非均匀微观环境中进行,易导致晶粒粒径较大、且粒径分布不均;而当tN>tm,微观混合完全后,晶核才开始形成,成核与生长在均匀微观环境中进行,晶粒粒径容易控制,且分布较窄。据估算,传统搅拌式反应器的tm在5~50ms之间[59],而超重力反应器的tm在0.01~0.1ms之间[19]。显然,传统搅拌式反应器中tN<tm,而超重力反应器中tN>tm。因此,超重力法能够制备出粒径更小、分布更均匀的纳米零价铁。

图2-29 纳米零价铁的TEM
从图2-29中可以看出,超重力法制备出来的纳米零价铁的颗粒球形性没有传统搅拌方法制备出来的好。其原因是在超重力场内,高速旋转的填料对纳米零价铁晶核具有强大的碰撞、剪切、撕裂作用,纳米零价铁晶粒在生长过程中生长环境受到了影响,晶粒生长被抑制。
2.5.4.4 应用
将制备的纳米零价铁用于含硝基苯废水的降解,硝基苯初始浓度为250mg/L,废水初始pH值为4.0,反应时间为30min。在特定停留时间内硝基苯去除率随着纳米零价铁剂量的增加而增加。当纳米零价铁剂量增加至4.0g/L时,废水中硝基苯去除率即可达到将近100%。与常规搅拌方法制备的纳米零价铁相比要达到接近100%的硝基苯去除率[57],纳米零价铁的剂量至少在5.0g/L以上。分析其原因可能是,超重力法制备出来的纳米零价铁颗粒尺寸比常规搅拌方法制备出来的要小,其在废水中的分散性良好,暴露给反应底物的表面积更加充分,纳米零价铁表面利用率更高,因而较小的剂量即可达到较高的硝基苯去除率。
在此基础上,用超重力技术对纳米零价铁的制备及其处理含硝基苯废水进行过程强化,进行了超重力制备纳米零价铁并同步处理含硝基苯废水实验。将纳米零价铁的制备与纳米零价铁还原硝基苯的反应耦合在一起,在纳米零价铁制备中同步实现含硝基苯废水的快速处理。纳米零价铁的生成环境在硝基苯废水中,纳米零价铁一经生成即被硝基苯分子包围住,纳米零价铁在成核初期及生长过程中即与硝基苯发生还原反应,纳米零价铁的利用率更加充分。考察了撞击流-旋转填料床转速、液体流量、硝基苯废水初始浓度、废水中铁(Fe2+)离子初始浓度、硼氢化钠溶液浓度、废水初始pH值等因素对硝基苯去除率的影响。实验结果表明:假设反应过程中铁(Fe2+)离子完全还原成纳米零价铁,按铁(Fe2+)离子初始浓度为0.05mol/L计,换算成纳米零价铁剂量约为2.79g/L。与前述处理方法对比,同步处理在纳米零价铁剂量上,比常规制备方法处理少用2g/L以上,比用超重力法制备出来后再进行处理少用1g/L以上。处理过程中,投加的铁离子适宜初始浓度约为硝基苯废水中硝基苯浓度的20~30倍,硼氢化钠还原剂溶液浓度范围为铁离子初始浓度的2.0~3.0倍。以含硝基苯废水直接配制硼氢化钠还原剂溶液,在原废水基础上实现含硝基苯废水的处理,处理后废水总体积不变,不增加后续处理负荷。本方法变多步为一步,避免了传统方法纳米零价铁制备过程中的洗涤、分离、干燥、储存等繁杂操作,极大地简化了制备及使用步骤,为含硝基苯废水的处理提供了一条简便、快速的新途径。
2.5.5 纳米2,4-二羟基苯甲酸铜
2.5.5.1 理论基础
以2,4-二羟基苯甲酸、氢氧化钠和硫酸铜为原料反应制备2,4-二羟基苯甲酸铜[60],其反应过程如下:
(2-17)
(2-18)
(2-19)
上述反应式(2-17)为酸碱中和,在STR反应器进行,式(2-18)为反应结晶过程,式(2-19)是副反应,由结晶理论可知,粒子形成过程是晶体生长过程,对于溶液中晶体的生长,可以分为晶核形成与晶体长大两个过程,该过程也是相变过程。式(2-18)反应结晶过程是均匀成核过程,生成2,4-二羟基苯甲酸铜的相变驱动力为自由能变化为:
(2-20)
式中,ΔG为吉布斯自由能变化;r为成核胚芽半径;Δg为摩尔相变吉布斯自由能变化;V为摩尔体积。
由Gibbs-Thomson关系式,临界晶核大小:
(2-21)
式中,R为气体常数;S为过饱和度。
成核过程可以看做是激活过程,成核所需的活化能为:
(2-22)
可见,提高溶液中2,4-二羟基苯甲酸铜的过饱和度S,可以大大降低ΔGc使rc减小。因此,溶液的2,4-二羟基苯甲酸铜过饱和度是纳米粒子形成的必要条件。
2.5.5.2 工艺说明
2,4-二羟基苯甲酸铜合成路线见图2-30,启动IS-RPB反应器,调节变频器控制IS-RPB装置转鼓的转速,稳定运转。启动反应液进料泵,调节阀门控制反应物流量,两股反应物液体同时进入IS-RPB装置,在IS-RPB装置内反应后反应液流回贮液槽,保温熟化一段时间,过滤后洗涤数次,洗涤直到不能检测到硫酸根离子为止。过滤后所得滤饼,分别在水或乙醇中超声波振荡分散,抽干后在80℃下真空干燥3h,得浅黄色粉末。

图2-30 燃烧铜催化剂合成工艺
2.5.5.3 应用
传统的反应器不能满足液相快速反应对混合的要求,所制备的粉末以粒度大,粒度分布宽为主要特征。采用撞击流旋转填料床制备的2,4-二羟基苯甲酸铜粒子,在转速1000r/min和撞击初速28m/s以及100℃真空干燥温度的操作条件下,粉体产品为形貌规则的片状结构,平均粒径610nm,大部分粒子分布在0.12~0.363μm,比表面积为11.6265m2/g。表明撞击流旋转填料床制备纳米颗粒具有生产能耗低、混合效率高等优点,可以为沉淀反应提供一个理想的反应环境[5,61,62]。
2.6 发展趋势与前景
液-液均相和非均相体系广泛地存在于精细化工、高聚物合成、制药工业、炸药生产、生物化工、燃料调制等工业过程中,良好的微观混合是这类过程得以进行的前提和必要条件,而IS-RPB对液-液强化的效果,显示出IS-RPB是迄今强化液-液相间传递最有效的方法之一,越来越被广大科技工作者广泛关注[63]。预计未来一个时期将会在以下方面加大研究力度,拓宽应用范围:
①提高反应的选择性。根据化学产品合成过程中,主反应与副反应动力学、热力学的原理,利用IS-RPB连续快速微观混合的特性来促进主反应,同时抑制副反应发生或减慢副反应的速率,提高反应的选择性,最大限度提高产品的收率,减少副产物,优化反应过程。
②乳化过程研究和乳化产品开发。这是今后IS-RPB研究的一个领域,包括乳化炸药生产过程、乳化食品生产、乳化涂料及其他乳化产品的生产等。
③提升高聚物合成技术。随着高聚物合成反应的进程,体系的黏度会不断增大,IS-RPB的强制混合和聚合效果,有利于保证聚合度的均一性,提升产品的质量。
④液膜分离技术不断完善。IS-RPB连续制备的液膜具有液膜滴径小、且分布范围窄、乳液稳定性好、溶胀率高、膜现制现用、不需存放等优点。同时IS-RPB作为提取装置,具有提取效率高、连续操作等优点,将仍然为十分活跃的研究领域,该技术将不断完善。在湿法冶金、废水处理、气体分离、有机物分离、生物制品分离与生物医药分离、化学传感器与离子选择性电极等领域有着广泛的应用前景。
⑤强化废水处理过程。随着科技的飞速发展,废水的排放量呈逐年上升趋势,废水中污染物的控制成为首要解决的问题,IS-RPB反应器可以实现连续制备的纳米金属或金属氧化物粒子,解决粒径大、粒度分布宽、形貌难控、间歇操作、批次重复性差、过程放大效应大等技术难题,实现有机废水、重金属废水中污染物的强化处理。同时,IS-RPB也可应用于废水中的萃取、吸附及纳米过渡金属制备及降解废水一体化等过程。
⑥拓宽应用领域。IS-RPB将在相关化学反应中的结晶、硝化、耦合、磺化和烷基化等领域具有更加广阔的应用前景。
总之,由IS-RPB强化传质特性,必将推进液-液接触与反应技术的新的发展,逐渐形成效率高、设备体积小、占地面积小、能耗低、稳定连续操作的符合提质降耗系列的液-液连续快速接触与反应的新工艺和新技术。
参考文献
[1] 刘有智.超重力化工过程与技术[M].北京:国防工业出版社,2009.
[2] Burns J R,Ramshaw C.Process intensification: Visual study of liquid maldistribution in rotating packed.beds[J].Chemical Engineering Science,1996,51:1347-1352.
[3] Liu Y Z,Jiao W Z,Qi G S.Preparation and properties of methanol-diesel oil emulsified fuel under high-gravity environment[J].Renewable Energy,2011,36(5):1463-1468.
[4] 焦纬洲.超重力强化甲醇柴油乳化燃料制备技术[M].北京:国防工业出版社,2013.
[5] Li Y,Liu Y Z.Synthesis and catalytic activity of copper (Ⅱ) resorcylic acid nanoparticles[J].Chemical Research in Chinese Universities,2007,23(2):217-220.
[6] Fan H L,Li L,Zhou S F,Liu Y Z.Continuous preparation of Fe3O4 nanoparticles combined with surface modification by L-cysteine and their application in heavy metal adsorption[J].Ceramics International,2016,42(3):4228-4237.
[7] (以色列) Tamir A.撞击流反应器——原理和应用[M].伍沅译.北京:化学工业出版社,1996.
[8] 伍沅.撞击流:原理·性质·应用[M].北京:化学工业出版社,2006.
[9] Johnson B K,Prud 'homme R K.Chemical processing and micromixing in confined impinging jets[J].AIChE Journal,2003,49(9):2264-2282.
[10] Gao Z M,Han J,Xu Y D,et al.Particle Image Velocimetry (PIV) Investigation of Flow Characteristics in Confined Impinging Jet Reactors[J].Industrial & Engineering Chemistry Research,2013,52(33):11779-11786.
[11] Savart F.Memoire sur le choc de deux veines liquides animees de mouvements directement opposes circulaire[J].Annali di Chimica,1833,54:56-87.
[12] Erni P,Elabbadi A.Free impinging jet microreactors:controlling reactive flows via surface tension and fluid viscoelasticity[J].Langmuir,2013,29(25):7812-7824.
[13] Zhang J,Liu Y Z,Qi G S.Investigation of Flow Characteristics in Free Impinging Jet Reactors by Particle Image Velocimetry (PIV)[J].Fluid Dynamics Research,2016,48(4):045505.
[14] Zhang J,Liu Y Z,Luo Y.The turbulent behavior of novel free triple-impinging jets with large jet spacing by means of particle image velocimetry[J].Chinese Journal of Chemical Engineering,2016,24(6):757-766.
[15] 刘有智,焦纬洲,祁贵生等.一种连续制备甲苯二异氰酸酯的单反射超重力装置及工艺[P].中国专利201410481252.0,2014-09-20.
[16] 刘有智,焦纬洲,祁贵生等.一种连续制备甲苯二异氰酸酯的装置及工艺[P].中国专利201410481281.7,2014-09-20.
[17] 刘有智,祁贵生,焦纬洲等.一种连续制备甲苯二异氰酸酯的川形超重力装置及工艺[P],中国专利201410481280.2,2014-09-20.
[18] 张珺,开放式撞击流反应器流场特性研究[D].太原:中北大学,2016.
[19] Jiao W Z,Liu Y Z,Qi G S.A new impinging stream-rotating packed bed reactor for improvement of micromixing iodide and iodate[J].Chemical Engineering Journal,2010,157(1):168-173.
[20] Jiao W,Liu Y,Qi G.Micromixing Efficiency of Viscous Media in Novel Impinging Stream-Rotating Packed Bed Reactor[J].Industrial & Engineering Chemistry Research,2012,51(20):7113-7118.
[21] Lin W W,Lee D J.Micromixing effects in aerated stirred tank[J].Chemical Engineering Science,1997,52(21-22):3837-3842.
[22] Liu C I,Lee D J.Micromixing effects in a couette flow reactor[J].Chemical Engineering Science,1999,54(13-14):2883-2888.
[23] Monnier H,Wilhelm A M,Delmas H.Effects of ultrasound on micromixing in flow cell[J].Chemical Engineering Science,2000,55(19):4009-4020.
[24] Yang H J,Chu G W,Zhang J W,et al.Micromixing Efficiency in a Rotating Packed Bed:Experiments and Simulation[J].Industrial & Engineering Chemistry Research,2005,44(20):7730-7737.
[25] Fournier M C,Falk L,Villermaux J.A new parallel competing reaction system for assessing micromixing efficiency-determination of micromixing time by a simple mixing model[J].Chemical Engineering Science,1996,51(23):5187-5192.
[26] Yang K,Chu G W,Shao L,et al.Micromixing Efficiency of Viscous Media in Micro-channel Reactor[J].Chinese Journal of Chemical Engineering,2009,17(4):546-551.
[27] Chu G W,Song Y H,Yang H J,et al.Micromixing efficiency of a novel rotor-stator reactor[J].Chemical Engineering Journal.2007,128 (2-3):191-196.
[28] 焦纬洲,李晓霞,李鹏等.超声制备甲醇柴油乳液及其稳定性研究[J].日用化学工业,2015,45(10):568-571.
[29] 李静,焦纬洲,刘有智等.甲醇柴油乳液稳定性研究[J].日用化学工业,2014,44(7):366-370.
[30] 焦纬洲,刘有智,祁贵生.柴油-甲醇-水三元乳化液W/O流变特性的研究[J].石油学报(石油加工),2010,26(2):214-218.
[31] Jiao W,Wang Y,Li X,e al.Qiaoling Zhang.Stabilization performance of methanol-diesel emulsified fuel prepared using an impinging stream-rotating packed bed[J].Renewable Energy,2016,85:573-579.
[32] 焦纬洲,李静,刘有智等.甲醇柴油乳液的黏度特性[J].石油学报(石油加工),2014,30(2):279-282.
[33] 焦纬洲,刘有智,上官民等.甲醇乳化柴油分散特性研究[J].燃料化学学报.2011,39(4):311-314.
[34] 童祜嵩.颗粒粒度与比表面测量原理[M].上海:上海科技文献出版社,1989.
[35] Jiao W,Li J,Liu Y,et al.Dispersion Performance of methanol-diesel oil emulsified fuel prepared by high gravity technology[J].China Petrol Proc & Petrochem Techn,2014,16(1):27-34.
[36] 焦纬洲,刘有智,祁贵生等.柴油-甲醇-乳化剂三组元乳化液的制备及其理化特性[J].石油学报(石油加工),2011,27(1):91-94.
[37] Cheng C H,Cheung C S,Chan T L.Comparison of emissions of a direct injection diesel engine operating on biodiesel with emulsified and fumigated methanol[J].Fuel,2008,87(10-11):1870-1879.
[38] 刘有智,祁贵生,杨利锐.撞击流-旋转填料床萃取传质性能研究[J].化工进展,2003,22(10):1108-1111.
[39] 祁贵生,刘有智,杨利锐.撞击流-旋转填料床处理含苯酚废水的单级试验研究[J].化学工业与工程技术,2004,25(1):9-12.
[40] 祁贵生,刘有智,杨利锐.撞击流旋转填料床内磷酸三丁酯对苯酚的络合萃取[J].化工生产与技术,2004,11(1):13-16.
[41] 杨利锐,刘有智,祁贵生等.撞击流-旋转填料床乳状液膜法处理含酚废水的研究[J].应用化工,2004,33(3):31-33.
[42] 杨利锐,刘有智,焦纬洲等.撞击流-旋转填料床乳状液膜法处理含酚废水的研究Ⅱ[J].化工科技,2004,1:40-43.
[43] 杨利锐,刘有智,祁贵生等.撞击流-旋转填料床制乳性能研究[J].化工科技,2003,11(5):36-39.
[44] 李倩甜.IS-RPB乳状液膜法处理苯胺废水的基础研究[D].太原:中北大学,2014.
[45] 冯霞,刘有智,申红艳等.超细氢氧化镁阻燃剂的研究现状[J].塑料工业,2013,(02):7-10.
[46] 白俊红,刘有智,申红艳等.表面改性对超细氢氧化镁过滤性能和沉降性能的影响[J].化工进展,2013,(06):1363-1366.
[47] 焦学瞬,贺明波.乳状液与乳化技术新应用[M].北京:化学工业出版社,2006.
[48] 蒋登高,章亚东,周彩荣.精细有机合成反应及工艺[M].北京:化学工业出版社,2003:148-158.
[49] 陈荣业.有机合成工艺优化[M].北京:化学工业出版社,2006:182-195.
[50] 张珍明.水蒸气蒸馏技术在精细化学品生产中的应用[J].化工时刊,2004,18(6):48-49.
[51] 张珍明.相转移催化合成邻乙氧基苯酚的研究[J].淮海工学院学报,1998,7(4):43-45.
[52] Zhang Q L,Liu Y Z,Li G M,et al.Preparation of p- Hydroxybenzaldehyde by Hydrolysis of Diazonium Salts Using Rotating Packed Bed[J].Chinese Journal of Chemical Engineering,2011,19(1):140-144.
[53] Fan H L,Zhou S F,Qi G S,et al.Continuous preparation of Fe3O4 nanoparticles using Impinging Stream-Rotating Packed Bed reactor and magnetic property thereof[J].Journal of Alloys and Compounds,2016,662:497-504.
[54] Akbarzadeh A,Samiei M,Davaran S.Magnetic nanoparticles:preparation,physical properties,and applications in biomedicine[J].Nanoscale Research Letters,2012,7(1):1-13.
[55] Qu J,Liu G,Wang Y,et al.Preparation of Fe3O4-chitosan nanoparticles used for hyperthermia[J].Advanced Powder Technology,2010,21(4):461-467.
[56] Fan H L,Zhou S F,Gao J,et al.Continuous preparation of Fe3O4 nanoparticles through Impinging Stream-Rotating Packed Bed reactor and their electrochemistry detection toward heavy metal ions[J].Journal of Alloys and Compounds,2016,671:354-359.
[57] Jiao W Z,Feng Z R,Liu Y Z,et al.Degradation of nitrobenzene-containing wastewater by carbon nanotubes immobilized nanoscale zerovalent iron[J].Journal of Nanoparticle Research,2016,18:198.
[58] 俸志荣.纳米零价铁处理含硝基苯废水实验研究[D].太原:中北大学,2016.
[59] 康荣灿,刘有智,郭雨等.撞击流-旋转填料床合成超细平台燃烧催化剂β-Cu[J].化工科技,2006,14(4):1-5.
[60] 陈建峰,邹海魁,刘润静等.超重力反应沉淀法合成纳米材料及其应用[J].现代化工,2001,21(9):9-12.
[61] 李裕,郭雨,刘有智等.纳米2,4-二羟基苯甲酸铜粉体的合成及表征[J].火炸药学报,2006,29(3):32-35.
[62] 刘有智,郭雨,李裕等.2,4-二羟基苯甲酸铜 (Ⅱ) 的合成[J].合成化学,2006,14(3):269-271.
[63] 刘有智.超重力撞击流-旋转填料床液-液接触过程强化技术的研究进展[J].化工进展,2009,28(7):1101-1108.