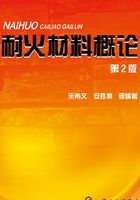
2.1 原料的选取和制备
随着耐火原料工艺技术的进步,耐火材料工业所用的原料从最初的天然原料,发展到经过精选加工的天然原料,再到按人们预定的要求而合成的耐火原料,从而使耐火材料的性能与寿命得以大幅度提高。耐火原料总的发展趋势一是高纯化,二是合成原料,三是发展耐火原料粉体。为适应使用要求,提高制品质量和试制新品种,对耐火原料的质量要求日益提高。天然优质耐火原料储量不多,且用量不断增加。天然耐火原料一般都是从矿体上取下的大块矿石,同时矿石中含有不同的杂质。因此,对天然耐火原料都需要进行选矿,煅烧以及破粉碎等加工工序,才能用于耐火材料。
2.1.1 选矿
选矿是用物理或化学方法将矿物原料中的有用矿物和无用矿物(通常称脉石)以及有害矿物分开,或将多种有用矿物分开的工艺过程,又称矿物加工。产品中有用成分富集的称精矿;无用成分富集的称尾矿;有用成分含量介于精矿和尾矿之间,需进一步处理的称中矿。
选矿过程包括选前矿物原料的准备作业,选别作业(选矿方法)及选矿后的处理作业。
2.1.1.1 选前矿物原料准备
选前矿物原料准备包括粉碎(含破碎和磨碎)、筛分和分级,有时还包括洗矿。
破碎:将矿山采出的粒度为500~1500mm的矿块破裂到粒度为5~25mm的过程,方式有压碎、击碎、劈碎等。一般分三个阶段:粗碎从300mm破碎到50~75mm,中碎从50~75mm破碎到3~5mm,细碎从5~10mm破碎到小于或等于0.088mm。
磨碎:以研磨和冲击为主,将破碎产品磨碎到10~300μm大小,常用的磨矿设备有棒磨机、球磨机、自磨机和半自磨机等。
筛分和分级:筛分是指破粉碎后的物料,通过一定尺寸的筛孔,使不同粒度的物料进行分离的过程。筛分过程中,通常将通过筛孔的物料称为筛下料,残留在筛上的物料为筛上料。按颗粒在介质(通常为水)中沉降速度的不同,将物料分为不同的等级称为分级。筛分和分级是在粉碎过程中分出适合粒度的物料,或把物料分成不同粒度级别分别入选。
2.1.1.2 选别作业
选别作业有重选、浮选、磁选、电选和化学选等。
对于耐火矿物原矿采用哪种选矿方法,首先取决于矿物中各种矿物的物理性质,例如矿物的颗粒大小和形状、密度、润湿性、电磁性质、溶解度、加热时的性状等。对于同一类矿物原料,由于产地差异使其伴生矿物和杂质含量可能存在较大差异,因而选矿工艺流程和方法也存在差异。
重选为在介质(主要是水)流中利用矿物原料密度不同进行选别。浮选是利用各种矿物原料颗粒表面对水的湿润性(或水性或亲水性)的差异进行选别。磁选是利用矿物颗粒磁性的不同,在不均匀磁场中进行选别。电选为利用矿物颗粒电性的差别,在高压电场中进行选别。拣选包括手选和机械拣选。化学选是利用矿物化学性质的不同,采用化学方法或化学与物理相结合的方法分离和回收有用成分,得到化学精矿。
2.1.2 原料煅烧与预合成
2.1.2.1 原料的煅烧
原料煅烧目的是在高温下除去结晶水、碳酸根及易挥发物,使耐火材料在制品的烧成时或直接在高温下使用时的体积能基本稳定。原料煅烧过程中主要发生两大变化。其一是物理化学变化,根据原料不同可能涉及吸附水、结晶水以及有机物的排出、分解反应、相变、固相反应等。其二是烧结,烧结是使原料的气孔率降低,从而提高了原料的体积密度。作为耐火材料,不但天然原料需要煅烧,合成原料也需要煅烧,不同原料的煅烧存在很多共性。
有的耐火材料很难烧结,因为它具有较大的晶格能和较稳定的结构,质点迁移需要较高的活化能,即活性较低之故。例如,高纯天然白云石真正烧结需要1750℃以上的高温,而提纯的高纯镁砂,需1900~2000℃以上才能烧结。这对高温设备,燃料消耗等方面都带来了一系列问题。所以,根据原料特点和工艺要求,提出了原料的活化烧结、轻烧活化、二步煅烧及死烧等概念。
(1)活化烧结 早期的活化烧结是通过降低物料密度,提高比表面积和增加缺陷的办法实现的,把物料充分细磨(一般小于10μm),在较低的温度下烧结制备熟料。
(2)轻烧活化 用化学法提高物料活性,研制降低烧结温度促进烧结的工艺方法。
(3)二步煅烧 即轻烧-压球-死烧工艺。轻烧的目的在于活化。例如菱镁矿加热后,在600℃出现等轴晶系方镁石,650℃出现非等轴晶系方镁石,等轴晶系方镁石逐渐消失,850℃完全消失。这些MgO晶格,由于结构松弛且具有较多的晶格缺陷,因此其活性高。死烧的目的在于使物料达到完全烧结。
二次煅烧与一次烧结相比,工艺过程复杂,燃耗较大,所以对纯度不高的物料,如杂质总量达到4%的镁砂,可不必采用二步煅烧工艺。
2.1.2.2 原料的预合成
(1)传统耐火原料的合成
自然界中存在但不具有开采价值而又十分重要的耐火原料也可以通过人工合成而得到。原料合成可按照使用目的人为地控制原料的化学组成和矿物组成,具有优于天然原料的多种性能。合成耐火原料是以两种或两种以上的天然原料或工业原料经过细磨、均化和高温处理(烧结或熔融)形成预期的矿物相。
合成耐火原料的工艺中配料、均化与高温处理特别重要。合成原料不可避免地有杂质存在,因而其实际成分和性能都低于理论值。为了得到性能良好的合成原料,配料时一般都偏离其理论组成点,如合成堇青石时Al2O3提高到38%以上;合成镁铝尖晶石时,通常将MgO提高到32%以上或将Al2O3提高到77%以上而形成富镁或富铝尖晶石。
均化对烧结法合成耐火原料尤其重要。要想得到物相均匀的合成原料,应把所使用的天然原料、工业原料和添加物严格计量,充分混合细磨,使其组分高度分散。
物料配料后经高温处理才能形成预期的矿物。高温处理的方法有高温烧结法与熔融法(电熔法)。烧结法合成原料实际上是配合料在高温下的反应烧结,它的过程易于控制,常用的烧结设备有倒焰窑、梭式窑、竖窑、回转窑和隧道窑。电熔法较烧结法工艺过程简化,熔化温度高,合成的原料纯度较高且晶体发育良好,因此性能比烧结法好,是十分有发展前途的耐火原料合成方法。
(2)高技术耐火原料粉体的合成
现代高技术耐火材料已成为高技术陶瓷的一部分。当物质细到一定程度下,它表现出与传统材料不同的奇异性能。要获得高技术的耐火材料,应该采用高纯、超细,组分均匀和少团聚或软团聚的均一球型粒子活性粉末。同时将这些耐火原料粉体添加到传统的耐火材料中,对其烧结性能、微观结构和使用性能都会产生重要影响。高技术耐火原料粉体的合成以及其对传统耐火材料性能的影响是现在和将来耐火材料领域研究的重点。粉体可分为粉粒体、微粉体和超微粉体,并可进一步细分。常用的粉体划分标准见表2-1。
表2-1 粉体的划分及粒径范围

目前应用较多的耐火原料粉体有SiO2、Si3N4、SiC、ZrO2和Al2O3。Si3N4和SiC高温强度大、抗热冲击、抗氧化,是理想的高温工程材料;加入部分稳定剂(Y2O3,CaO,MgO)后材料强度与韧性极高;Al2O3是用量最大的材料,可做为耐磨耐高温的机械部件。