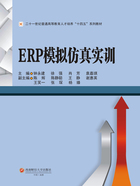
1.2 ERP的发展历程
自18世纪工业革命以来,新技术的不断创新推动了手工作坊向工厂生产的转变,从而催生了制造业的诞生。然而,日趋激烈的市场环境导致企业在生产过程中面临的问题也越来越突出,诸如不能保证原材料的及时供应、产品生产所需零部件的匹配协同性差、人力资源浪费严重、货物积压以及客户订单供应不精准等问题。通过研究发现,这些问题的根本原因在于原料采购控制问题。为解决这一问题,研究人员提出了订货点法。订货点法是指企业对某一物料库存设定一个订货点和安全库存点,当物料库存减少到订货点时即发出采购单;当该批物料到达时,库存中原料刚好下降到安全库存点,从而能及时弥补前期减少量。订货点法能在一定程度上解决材料采购的问题,但是其不足在于将产品生产所需各项材料割裂开了,未考虑到产品生产所需材料的匹配关系,因此对提高企业运营生产效率的作用效果不够显著。然而,我们也要清晰地认识到,订货点法产生的时代背景,在当时没有计算机进行辅助处理数据的情况下,能够用数学公式去规范企业原材料采购,对比从前已经有了很大的进步。
随着计算机的诞生,及时处理生产中产生的庞大数据成为可能。同时,计算机技术也推动了企业原材料管理更为先进的思想及方法。
其中最典型的是物料需求计划(material requirement planning,MRP)。相较于订货点法,MRP的贡献在于从产品的材料结构去考虑库存,而不是将不同材料单独地割裂开来,从而有利于从整体上来优化库存,实现原料之间的有效配比,降低库存,减少积压,提升原材料的利用效率,进而增强企业竞争力。此外,MRP在物料管理过程中还引入了时间坐标。具体而言,MRP在管理物料过程中不仅考虑了物料之间的配比关系,同时也追踪物料的状态,即何时到达、何时发出、分批次还是一次性到达等问题。企业引入MRP能在很大程度上实现了优化库存的目标。
MRP作为一种新的物料管理系统,对于提升企业物料管理具有十分重要作用。但是随着经济社会的发展,以及企业认知的不断提升,其局限性也越发明显。企业物料管理还会涉及企业的生产计划和采购计划,于是具有创新意识的企业便在MRP系统中加入了生产计划和采购计划,便形成了较为完善的闭环MRP。该系统在实际运用中遵循“计划—反馈—修正—再计划”的循环模式,使物料管理的体系更为完善。
闭环MRP使得企业生产计划各子系统实现了有机整合,提升了企业物料管理水平。但随着闭环MRP的深入实施,人们在实践中发现企业物流与资金流信息之间常出现矛盾的现象,而且事后溯源的工作量也非常大,因此企业强烈要求二者能实现有效的结合。由此,MRPⅡ便应运而生。
MRPⅡ将企业各系统有机结合起来,实现了对企业整体运营的模拟仿真。它犹如作战时的沙盘,使我们能够从整体上去把握企业各项资源情况,成为企业领导者决策的重要工具。MRPⅡ的先进之处不仅仅是将各系统有机整合,更为重要的是,它能够借助计算机强大的运算功能,快速准确地对企业复杂的数据进行分析,让各子系统在统一的数据环境下工作,实现整个企业的精准生产。因此,有人评价MRPⅡ恰如“靠仪表来驾驶的飞机”。
自20世纪90年代以来,经济全球化的趋势越来越明显,市场环境也变得更加扑朔迷离。因此要使企业在激烈的竞争环境中脱颖而出并取得胜利,我们就必须审时度势地分析企业内外环境,以客户为中心,以市场为导向,根据需求的变化及时有效地作出战略调整。因此,人们对于能够反映企业内外环境的管理系统的呼声越来越高。在此背景下,ERP顺势而生。图1.1为ERP的发展历程。

图1.1 ERP的发展历程