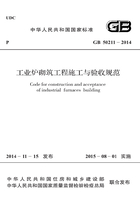
6.2 高炉
6.2.1 砌筑前应校核炉喉钢圈中心对炉底底基中心的位移。厚壁炉腰和炉身砌体的中心线应以炉喉钢圈中心为准。炉缸砌体的中心线应由测量确定,对炉身中心线的位移不应超过30mm。炉底、炉缸砌体的标高应以出铁口中心或风口中心平均标高为基准。
炉腰以上的砌体均以炉喉钢圈中心为基准砌筑。炉缸砌体的中心线则是参照炉身中心线由测量确定,若不校核两者之间的位移,则炉体上、下部的内衬有可能出现偏斜,影响高炉砌体的质量。为此,规定其位移不应超过30mm。超过此数值时,应重新调整炉缸砌体中心线的位置。国内很多高炉的风口采用组合砖砌筑,而组合砖直接砌筑在炉缸环形炭砖上,标高的调整余地较少。故在确定炉底、炉缸砌体的标高时,应以风口中心平均标高为基准,使风口组合砖能准确就位。风口不采用组合砖时,应以出铁口中心标高为基准砌筑炉底和炉缸。
6.2.2 冷却壁之间和冷却壁与出铁口框、风口和渣口大套之间的缝隙,应在砌砖前用填料填塞,其牌号和性能应符合设计规定。
国内外高炉在这些部位多采用炭质或碳化硅质材料作为填料,也可采用铁屑填料。故强调“其牌号和性能应由设计规定”。
6.2.3 高炉各部位炭素捣打料的施工应按本规范第4.5节的规定执行。当采用压缩比检查捣打料的捣实密度时,其压缩比为:炉底垫层不应小于45%,砌体与冷却壁(或炉壳)之间的缝隙不应小于40%。高炉热捣炭素料的加热温度不应超过120℃。
用于炉底垫层的炭素捣打料,要求料体结实致密,有较大的耐压强度和较高的导热系数。因此,捣打时压缩比不应小于45%。用于砌体与冷却壁(或炉壳)之间缝隙的炭素捣打料,主要作用是吸收炭砖砌体向四周的膨胀,但也应具有一定的密实度和导热性能,所以该部位的炭素捣打料的压缩比不应小于40%。高炉热捣炭素料的加热温度,参照其混炼温度规定为不应超过120℃。
6.2.4 设有冷却装置的炉底密封钢板表面,砌砖前应用炭素捣打料捣固或碳化硅质浇注料浇注并找平。其施工质量及表面平整偏差应记入验收记录中,并应附测量图。
随着新材料、新工艺的开发和应用,有些高炉的炉底找平层采用碳化硅质浇注料找平,故本次修订增加浇注料找平的内容。设有冷却装置的炉底密封钢板表面用炭素捣打料捣固或碳化硅质浇注料浇注是为了使整个炉底能较好地传热,以保护炉底,提高高炉的使用寿命。炉底钢板上炭素捣打料或碳化硅质浇注料的找平是道很重要的工序,关系到炭砖砌筑是否平整,强调应做好验收记录。
6.2.5 炉底炭素捣打料或碳化硅质浇注料找平层宜采用扁钢隔板控制标高。炉底炭砖湿砌时,扁钢上表面标高允许偏差应为-2mm~0;炉底炭砖干砌时,扁钢上表面标高允许偏差应为-1mm~0。
本次修订增加了碳化硅质浇注料找平的要求,同时还增加了炭砖干砌时对扁钢上表面标高允许偏差的要求。用扁钢隔板分块控制炭素捣打料或碳化硅质浇注料找平层标高的施工方法,具有结构简单、施工方便、找平质量高的优点,这种方法已在各地高炉的施工中广泛应用。炉底炭砖湿砌时,扁钢上表面的标高允许偏差应为-2mm~0;炉底炭砖干砌时,水平砖缝厚度小,没有用耐火泥浆调整厚度的可能,故要求扁钢上表面的标高允许偏差应为-1mm~0,是根据多座大型高炉的施工经验而定的。
Ⅰ 炭砖砌体
6.2.6 炭砖应在制造厂内预组装。预组装后的炭砖应按顺序编号,并应记入预组装图中。
炭砖是精度要求高的耐火材料,不易加工。高炉的各层炭砖应在制造厂内预组装,检验每块炭砖是否合乎砌筑质量的要求。预组装完毕应按实际绘制预组装图,记下每块砖的编号,便于砌筑时按图纸施工。
6.2.7 满铺炭砖炉底上、下两层炭砖列的纵向中心线应交错成30o~60o,并均应与出铁口中心线交错成30°~60°。
满铺炭砖炉底上、下两层炭砖列的纵向中心线交错成30°~60°,是为了防止铁水沿垂直贯通缝渗透到炉底下部。为了避免出铁时铁水沿砖缝冲刷破坏砌体,各层炭砖的砖列长缝均应与出铁口中心线交错成30°~60°。
6.2.8 砌筑满铺炭砖炉底时,炭砖列应保持平直,并应随时检查。炭砖湿砌时,炭砖列之间的垂直缝用千斤顶顶紧后,砖列端部应固定;炭砖干砌时,炭砖列之间的垂直缝用人工和木锤敲打顶紧后,砖列端部也应固定。
炭砖列如不平直,不仅会影响砖缝厚度,还会给最后一列砖的砌筑带来困难,因此应随时检查。炭砖湿砌时,炭砖列用千斤顶顶紧,砖列平直度、平面位置和垂直缝经检查合乎要求,应将两端用木楔予以固定。炭砖干砌时,仅需使用人工和木锤敲打即可顶紧,同时将两端用木楔予以固定。
6.2.9 砌筑炭砖时,炭砖应用真空吸盘吊或吊装孔专用吊具吊装就位。
真空吸盘吊作为砌筑高炉炭砖的机具,已普遍采用。炭砖上表面预留吊装孔,采用专用吊具起吊砌筑。实践证明,这两种方法简便省力、施工进度快、减少炭砖磨损、安全可靠。
6.2.10 炉底环状炭砖与其他耐火砖砌体之间的厚缝尺寸宜为40mm~120mm。
本条所指的厚缝实际上是一条工作缝,其下限尺寸需保证能用捣固锤将炭素捣打料捣实。常用的捣固锤锤头的最小锤面尺寸为30mm×60mm,故厚缝尺寸下限定为40mm。上限尺寸定为120mm也较合理。如果缝隙再大,则可加砌一块75mm宽的条子砖。
6.2.11 环状炭砖的放射缝应与半径方向一致。砌体内上、下层的砖缝应交错。
环状炭砖的放射缝与半径方向一致,能使砌体内受力均匀,且可避免出现错牙。
6.2.12 炭素泥浆需加热时,应隔水加热。
若用明火直接加热炭素泥浆,炭素泥浆内的某些易挥发物质容易因局部过热而挥发,降低炭素泥浆的和易性和粘接性,甚至还会出现安全事故,因此应隔水加热。
6.2.13 炭砖砌体砖缝内的炭素泥浆均应饱满。砌筑时应用千斤顶使炭砖彼此靠紧。
炭砖大且重,人工砌筑不能就位,砖缝内的炭素泥浆不易饱满,故应用千斤顶顶紧。
6.2.14 捣打炭素料前,炭砖砌体与冷却壁(或炉壳)、其他耐火砖之间的缝隙均应用木楔固定。环状炭砖砌体与冷却壁(或炉壳)之间的炭素料,应在该环炭砖砌完后捣打。
捣打炭素料之前用木楔固定炭砖,是为了防止炭砖在捣打过程中出现位移。环状炭砖砌体合门、调正前捣打炭素捣打料,会使炭砖产生位移,故应在环状炭砖砌完调正以后再开始捣打炭素捣打料。
6.2.15 炭砖砌体的上表面均应平整,并应按要求逐层检查,必要时应磨平。
炭砖砌体的上表面保持平整,并要求逐层检查,是碳砖砌筑的重要环节。
6.2.16 炉缸的炭砖应从出铁口开始砌筑,并应保证出铁口通道的宽度尺寸。渣口区的炭砖可从渣口开始砌筑。
炉缸环状炭砖从出铁口开始往两边砌筑,可保证出铁口通道的宽度尺寸、上下层炭砖不会出现错牙、铁口区其他耐火砖砌体与炭砖接触严密。
6.2.17 炭砖砌体的砖缝厚度应用塞尺检查。塞尺宽度应为30mm,厚度应等于被检查砖缝的规定厚度,其端部为直角形。当用塞尺插入砖缝的深度不超过100mm时,该砖缝可认为合格。
Ⅱ 其他耐火砖砌体
6.2.18 炉底、炉缸、炉腹、炉腰和炉身区域的砌体,当使用黏土质、高铝质和刚玉质耐火制品时,应采用相应的磷酸盐耐火泥浆砌筑。当使用铝碳质、碳化硅质或其他材质耐火制品时,应按设计规定采用相应的耐火泥浆砌筑。
磷酸盐耐火泥浆是一种耐高温胶结材料,它具有比普通耐火泥浆更优越的高温性能。采用这种泥浆后可以适当放宽砌体砖缝,从而取消粉尘严重、劳动强度大的磨砖工序。
6.2.19 炉底和炉缸的耐火砖(不包括保护层),施工前应认真选分与配层。
高炉炉底和炉缸耐火砖(不包括保护层),砖缝要求非常严格,应在施工前按厚度(竖砌时为高度)选分,做上标记。然后根据各级别砖的数量配层,必要时可研磨加工。
6.2.20 每层炉底均应从中心十字形开始砌筑,中心十字形炉底砖的纵向和横向砖列应相互垂直。
每层炉底只有从中心十字形开始砌筑,才能保证四周炉底砖的垂直偏差最小。中心十字形炉底砖的纵向和横向砖列如不互相垂直,其接触面会出现三角缝。因此,砌筑中心十字形砖列时,应随时检查。
6.2.21 炉底采用沾浆法砌筑时,应做到稳沾、低靠、短拉、重揉。
炉底竖砌砖用沾浆法砌筑,即将砖的大面和小面沾满耐火泥浆,放低靠上已砌好的砖,上下小幅度揉动,重力放在砖的下部,砖缝内的耐火泥浆则饱满而无“花脸”。
6.2.22 上、下两层炉底的砌筑中心线应交错成30°,并均应与出铁口中心线交错成30°~60°。通过上、下层中心点的垂直缝不应重合。
为了增强炉底砌体的整体性,避免铁水沿垂直贯通缝向下渗透,炉底砖上、下两层的砌筑中心线应交错成30°,通过上、下层中心点的垂直缝亦应错开。为避免出铁时铁水沿砖缝冲刷,各层炉底砖均应与出铁口中心线交错成30°~60°。
6.2.23 在炉底施工过程中,应随时检查砖缝厚度、耐火泥浆饱满程度、各砖层上表面的平整偏差和表面各点相对标高差。
炉底砌体是决定高炉寿命的关键部位,工程质量要求极严。砌筑炉底砖时,应随时检查砖缝厚度、耐火泥浆饱满程度、各砖层上表面的平整偏差和表面各点的相对标高差,确保炉底砌体的质量。
6.2.24 炉底砖层(除最上层外)上表面的错牙应磨平。磨平时不得将砖碰撞松动。
如果炉底砖层(除最上层外)上表面的错牙不磨平,其上一层砖砌筑后,会产生更多的错牙,而且越往上情况越严重。但是炉底最上层砖表面的错牙不会影响其他砖层的砌筑质量。在磨平炉底的错牙时,应仔细操作,不得将砌好的砖碰撞松动。
6.2.25 炉缸砌砖应从出铁口开始。砌出铁口时,出铁口框内的砌体应先砌。
出铁口砌体是炉缸的重要部位,砌筑技术复杂,质量要求严格。从出铁口开始往两边砌筑,可保证出铁口通道的宽度尺寸、出铁口中心线位置准确、出铁通道组合砖的砌筑质量。
6.2.26 在出铁口框和渣口大套外环宽500mm范围内的砌体以及风口带的砌体,均应紧靠冷却壁(或炉壳)砌筑。其间不严密处应用相应材质的稠耐火泥浆填充。
出铁口框和渣口大套外环宽500mm范围内的砌体以及风口带砌体均紧靠冷却壁(或炉壳)砌筑,其间不严密处填以相应材质的稠耐火泥浆是为了保证砌体的严密,防止铁水、渣或火焰从这些不严密处喷出,烧坏冷却壁(或炉壳)。
6.2.27 风口和渣口宜在水套安装完毕后砌筑。非组合砖砌体周围的砌体除顶部可侧砌外,其余部分应平砌,靠近水套的砖应加工。砌体与风口、渣口水套之间的缝隙不应小于15mm。
非组合砖砌体的风口和渣口两侧的砖平砌,便于加工水套周围的砖。既能保证风口、渣口区域的砌筑质量,又便于更换水套。风口、渣口的水套顶部砖若继续平砌封顶,则容易塌落,应用侧砌保证砌体的整体性和牢固性。砌体与风口、渣口水套之间的缝隙是为吸收砌体的受热膨胀,同时便于更换风口、渣口水套。故规定了缝隙的下限尺寸;至于上限尺寸,则应由设计规定。
6.2.28 炉底、炉缸采用陶瓷杯和环状炭砖混合结构时,对于大型预制块陶瓷杯,应先砌筑陶瓷杯,环状炭砖经现场预砌后再砌筑;对于小块砖陶瓷杯,应先砌筑炭砖,后砌筑陶瓷杯。
陶瓷杯由杯底垫和杯壁两部分组成。杯壁为多种形状的大型预制块结构时,陶瓷杯壁外侧一般为环状炭砖,当炉缸采用这种混合结构时,应先砌筑陶瓷杯,后砌筑环状炭砖。当杯壁砖不大时,应先砌筑炭砖,后砌筑陶瓷杯。
6.2.29 环形底垫砌筑前应先放好控制线。环形底垫由外向中心砌筑时,各环砖合门处应留成外大内小的喇叭口,待中心座砖砌完后,应再由内向外逐环合门。
杯底垫第二层为防止砖漂浮采取自锁结构,由外侧向炉中心砌筑。为此应逐环控制砌筑半径,避免中心座砖周围预留的填料缝过小,影响砌筑质量。合门处留成外大内小的喇叭口状,是由构造和砖型决定的。
6.2.30 陶瓷杯壁大型砌块宜采用专用器具吊装就位,经检查合格后,应及时用相应的耐火浇注料填充吊装孔。
陶瓷杯壁大型砌块形状多样,上表面一般较小,不宜使用真空吸盘和夹具吊装。利用砌块上表面预留的圆柱形吊装孔,采用专用器具吊装就位,既安全可靠,又方便施工。当一层陶瓷杯砌筑完成并经检查合格后,应及时用相应的耐火浇注料填充吊装孔。
6.2.31 砌筑陶瓷杯壁时,应严格控制砌块的水平度和垂直度,经常检查杯壁的砌筑半径,可利用干摆和微调砌筑半径的方法砌筑合门砖。
陶瓷杯壁每层砌块较高,上、下层多采取插入咬合。若不能保证砌块的垂直度和水平度,将给砌筑带来困难,并直接影响工程质量。因杯壁砌块难以加工,加工质量无法保证,故杯壁砌块合门时,每层最后几块砖应干摆,通过调整砖缝的办法合门,必要时可微调砌筑半径。
6.2.32 高炉圆形砌体不应同时有三层以上的退台。在同一层内,每环合门不应超过4处,并应均匀分布。
砌筑高炉圆形砌体时,不应同时留三层以上的退台是为了便于接槎砌筑,保持墙面平整。合门砖是砌体的薄弱环节,每环砖合门应愈少愈好。
6.2.33 砌筑厚壁炉腰和炉身时,应通过炉喉钢圈中心挂设中心线,并应随时检查砌体的半径尺寸。当厚壁炉腰和炉身的炉壳内表面有喷涂层时,应以炉壳为导面喷涂。喷涂层厚度的允许偏差应为±5mm。
高炉厚壁炉腰及炉身砌体的中心线,应以炉喉钢圈中心为准。通过炉喉钢圈中心挂设中心线,随时检查砌体的半径,将其控制在表6.1.2所规定的偏差范围内,能保证炉子的内型尺寸。炉壳内表面设计喷涂层既可防止炉内窜火烧红炉壳,又能隔热、减少热损失、节约能源,还可弥补炉壳凹凸不平给内衬造成的偏差。喷涂层应以炉壳为导面施工并及时修整,控制厚度的允许偏差为±5mm。
6.2.34 冷却板应在砌砖前安装。每层冷却板之间的砌体宜预加工。冷却板周围一块砖应紧靠炉壳砌筑,不应留填料缝。
炉身冷却板先安装,便于控制砖层高度、水平度以及填塞耐火填料。冷却板周围一块砖紧靠炉壳砌筑,不留填料缝,可防止隔热层内的填料在更换冷却板时流出。冷却板之间的间距固定、预加工耐火砖,能加快工程进度,提高工程质量。
6.2.35 高炉冷却壁与炉壳之间应压浆,其成分与配比应符合设计规定。
高炉冷却壁与炉壳之间压浆对提高炉衬的严密性、减少气体的窜漏、保护炉壳起着重要作用。炉身下部以下宜采用非水系压入泥浆,避免压浆料将大量水分带入炉衬内,给高炉的正常烘炉和顺利投产造成不利的影响。
6.2.36 炉身砌体与钢砖底部之间的缝隙应为50mm~120mm。当设计没有规定时,缝内应填以黏土质耐火填料。
高炉投产后,炉墙受热向上膨胀,需在钢砖底部留一定的间隙以吸收部分膨胀。