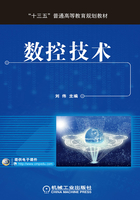
1.1.3 数控机床的发展趋势
以数字化为特征的数控机床是柔性化制造系统和敏捷化制造系统的基础装备,其总的发展趋势是高精化、高速化、高效化、柔性化、智能化和集成化,并注重工艺适用性和经济性。具体可归纳为下列方面:
1.持续地提高经济加工精度
1950—2000年的50年内加工精度提升了100倍左右,即加工精度平均每8年提高1倍,当前的普通加工精度已达到20世纪五六十年代的精密加工水平。
随着高新技术的发展和对机电产品性能与质量要求的提高,机床用户对机床加工精度的要求也越来越高。为了满足用户的需要,近十多年来,普通级数控机床的加工精度已由±10μm提高到±5μm。
2.推进全面高速化,实现高效制造
高速化机床向高速化方向发展,可充分发挥现代刀具材料的性能,不但可大幅度提高加工效率、降低加工成本,而且可提高零件的表面加工质量和精度。超高速加工技术对制造业实现高效、优质、低成本生产有广泛的适用性。20世纪90年代以来,随着超高速切削机理、超硬耐磨长寿命刀具材料和磨料磨具,大功率高速电主轴、高加/减速度直线电动机驱动进给部件以及高性能控制系统和防护装置等一系列领域中关键技术的解决,新一代高速数控机床加快了高速化发展的步伐。高速主轴单元(电主轴,转速为15000~100000r/min)、高速且高加/减速度的进给运动部件(快移速度为60~200m/min,切削进给速度高于60m/min)、高性能数控和伺服系统以及数控工具系统都出现了新的突破,达到了新的技术水平。高速化加工的另一个特点是大多从单一的高速切削发展至全面高速化,不仅要缩短切削时间,也要力求降低辅助时间和技术准备时间。
3.复合加工机床促进新一代高效机床的形成
复合加工机床的含义是实现或尽可能实现工件在一台机床上一次装夹完成大部分或全部加工工序,从而达到减少机床和夹具、免去工序间的搬运和储存、提高工件加工精度、缩短加工周期和节约作业面积的目的。复合加工机床根据其结构特点,分为工艺复合型和工序复合型两类。
工艺复合型为跨加工类别的复合加工机床,包括不同加工方法和工艺的复合,如车铣中心、铣车中心、激光铣削加工机床、冲压与激光切割复合、金属烧结与镜面切削复合等。
工序复合型应用刀具(铣头)自动交换装置、主轴立卧转换头、双摆铣头、多主轴头和多回转刀架等配置,增加工件在一次安装下的加工工序数,如多面多轴联动加工的复合加工机床和主副双主轴车削中心等。
4.工艺适用性的专门化数控机床正不断涌现
通过对机床布局和结构的创新,使其对不同类型的零件加工具有最佳的适用性,避免一方面出现不能发挥最佳性能,另一方面又存在功能冗余的现象。
要解决品种多样化与经济性的矛盾,就要对机床的模块化设计提出更高的要求。近年来,对并联机构机床和混联机构机床的研究以及对可重构机床(Reconfigurable Machine Tools,RMT)技术的探索,反映了对制造装备能更方便地实现个性化、多样化发展的追求。
5.智能化和集成化成为数字化制造的重要支撑技术
信息技术的发展及其与传统机床的相融合,使机床朝着数字化、集成化和智能化的方向发展。数字化制造装备、数字化生产线、数字化工厂的应用空间将越来越大;而采用智能技术来实现多信息融合下的重构优化的智能决策、过程适应控制、误差补偿智能控制、复杂曲面加工运动轨迹优化控制、故障自诊断和智能维护以及信息集成等功能,将大大提升成形和加工精度、提高制造效率。
6.发展适应敏捷制造和网络化分布式的制造系统
回顾制造系统的发展历程,基本上遵循以下两个方向:①增强制造系统的智能化和自治管理功能,以提高FMC/FMS的快速响应能力;②发展兼顾柔性、高效、低成本和高质量且便于重构的新型制造系统,以适应不确定性的市场环境。
这类制造系统称为快速重构制造系统(Rapidly Reconfigurable Manufacturing System,RRMS)或可重构制造系统(Reconfigurable Manufacturing System,RMS)。其原理为通过对制造系统中的设备配置的调整或更换设备上的功能模块来迅速构成适应新产品生产的制造系统。这就要求设备和系统不仅软件具有开放性,而且硬件也要有开放性,成为功能可重构的机床,即前面提到的可重构机床。
7.向大型化和微小化两极发展
能源装备的大型化及航空航天事业等的发展,需要重型立式卧式加工中心和铣车中心。从精密加工发展到超精密加工,是世界各工业强国致力发展的方向。其精度从微米级到亚微米级,乃至纳米级(<10nm),应用范围日趋广泛。超精密加工技术和微纳米技术是21世纪的战略高技术,正在形成一个产业。因此,需要发展能适应微小型尺寸结构和微纳米加工精度的新型制造工艺和装备。微型机床同时具有高速和精密的特点,最小的微型机床可以放在掌心之中,一个微型工厂可以放在手提箱中。操作者通过手柄和监视屏幕控制整个工厂的运作。
航空航天、信息技术和国防高新技术的需求推进了超精加工技术及设备的发展。20世纪60年代,美国开发出第一台商品化超精密机床,其加工尺寸精度为±0.8μm,20世纪70年代英国克兰菲尔德精密工程研究所批量生产的超精密车床加工的平面精度优于0.1μm,20世纪80年代美国LLL实验室和Y-12工厂合作生产的大型超精密金刚石车床加工的平面精度达0.0125μm,最大加工直径为2100mm。由于晶片和光学镜片等硬脆材料加工的需要,超精密磨削和研抛以及采用光、电、化学等能源的非机械能的特种加工方法使加工精度可达到纳米级(0.001μm)。通过机床结构设计优化,机床零部件的超精加工和精密装配,采用高精度的全闭环控制及温度、振动等动态误差补偿技术,提高了机床加工的几何精度,降低了几何误差和表面粗糙度值等,从而进入亚微米、纳米级超精加工时代。
8.配套装置和功能部件的品种质量日臻完善
功能部件不断向高速度、高精度、大功率和智能化方向发展,并取得成熟的应用。不仅数控系统(含数控装置和伺服驱动装置)有专业化生产厂,凡关键的通用性功能部件如高精度主轴单元、电主轴、力矩电动机、直线电动机、刀具自动交换系统、滚动导轨副、直线滚动丝杠驱动副、双摆主轴头、双摆回转台和自动转位刀塔等在国外均有一些著名的专业化生产厂,这对保证产品质量、提高整机的可靠性和降低成本起着重要的作用。
完善的高集成度的专用电路系统的研发,仍是数控系统可靠性继续提高和结构小型化的一项重要措施。
9.虚拟数控机床技术
虚拟数控机床实际上是虚拟环境中数控机床的模型。与真实机床相比,虚拟数控机床应具有以下功能:①应与真实机床的结构完全相同;②应比真实机床具有可观性;③强大的网络功能,为各种真正的制造资源服务,从而提高其与外界制造资源的相互操作性,快速地、并行地组织各部门、各集团成员将新产品从设计转入生产;④完善的图形和标准数据接口。
虚拟数控机床的应用将给制造业带来革命性的飞跃。由于虚拟数控机床是数字模型,所以容易实现对数字模型进行显示、分析、传递和迭代更新,为设计提供并行作业可能。虚拟数控机床和各设计软件的接口,为建模提供了方便,尤其是在特定的环境下,方便对产品的可靠性、产品的生产全过程、工艺规范以及产品方案的工艺计划进行性能评价。强化创新水平,用经济快捷的方式提高产品设计质量,缩短产品开发周期。虚拟数控机床的强大网络功能为真正实现远程合作提供了保证。
10.开放式数控系统
为适应数控机床普及、个性化、多品种、小批量、柔性化的要求,最重要的发展趋势是数控系统体系结构的开放性,设计生产出开放式的数控系统。美国、欧盟及日本等在研究开放式数控系统方面具有一定优势。由于个人计算机(Personal Computer,PC)所具有的开放性、低成本、软硬件资源丰富等特点,基于PC的开放式数控系统将成为一个主要趋势。
11.向标准化方向发展
数控标准是制造业信息化发展的一种趋势。数控技术诞生后的50多年间的信息交换都是基于ISO 6983标准,即采用G、M代码对加工过程进行描述,显然,这种面向过程的描述方法已越来越不能满足现代数控技术高速发展的需要。为此,国际上正在研究和制定一种新的CNC系统标准ISO 14649(STEP-NC),其目的是提供一种不依赖于具体系统的中性机制,能够描述产品整个生命周期内的统一数据模型,从而实现整个制造过程,乃至各个工业领域产品信息的标准化。
12.向高可靠性方向发展
数控机床的可靠性一直是用户最关心的主要指标,它主要取决于数控系统各伺服驱动单元的可靠性。为提高可靠性,目前主要采取以下措施:①采用更高集成度的电路芯片,采用大规模或超大规模的专用及混合式集成电路,以减少元器件的数量,提高可靠性;②通过硬件功能软件化,以适应各种控制功能的要求,同时通过硬件结构的模块化、标准化、通用化及系列化,提高硬件的生产批量和质量;③增强故障自诊断、自恢复和保护功能,对系统内硬件、软件和各种外部设备进行故障诊断、报警。当发生加工超程、刀损、干扰、断电等各种意外时,自动进行相应的保护。
13.绿色化
为了追求符合环保要求的机床,干式切削和微量润滑剂切削方法因其可大大减少润滑剂的挥发而得到越来越广泛的应用,同时,机床操作者在工作时的环境、位置会被考虑得非常舒适。此外,无污染的清洁加工技术也受到极大重视。