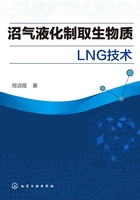
1.3.2 沼气净化研究现状
(1)脱除二氧化碳
沼气中存在以二氧化碳为主的杂质气体,二氧化碳降低了沼气热值并影响沼气燃烧性能,研究表明二氧化碳体积分数降到一定的比例后,沼气的热值有明显提高。沼气分离回收二氧化碳的方法有溶剂吸收法、变压吸附法、膜分离法及低温液化法。
①溶剂吸收法。热钾碱法是溶剂吸收法的一种,以热碳酸钾作活化剂,去除二氧化碳。吸收和再生反应式如下:
吸收过程: (1-4)
加入活化剂DEA的吸收反应: (1-5)
再生过程: (1-6)
加入活化剂DEA的再生反应: (1-7)
由于反应为可逆反应,其吸收二氧化碳效率相对较低。
氨水法是溶剂吸收法的另一种,既能除掉二氧化碳,又能除掉硫化氢。氨处理设备包括氨吸收塔、萃取塔、重沸器、低压蒸发缸、溶剂冷却器、泵、回流系统。
②变压吸附法。当气体分子运动到固体表面上时,由于固体表面分子(具有一定极性的分子)的引力作用,固体表面的一些分子会暂时停留在固体表面上,这些分子在固体表面上不断积累,这种现象称为气体分子在固体表面上的吸附。相反,由于分子力的不稳定性,固体表面上被吸附的分子返回气相的过程称为脱附或解吸。
当气体是混合物时,由于固体表面对不同气体分子的分子力差异,使吸附相的组成与气相组成不同,这种气相与吸附相在密度和组成上的差别构成了气体吸附分离技术的基础。
变压吸附技术是近30多年来发展起来的一项气体分离技术。20世纪60年代初,美国联合碳化物公司首次实现了变压吸附四床工艺技术的工业化应用。由于变压吸附相对于其他分离技术,产品纯度高,启停灵活方便,而且运行费用低,故该技术已成为现代工业中较为重要的气体分离及净化方法。目前变压吸附技术在各类气体的分离、提纯和工业气体净化领域已得到了广泛的应用。
吸附剂是变压吸附技术的基础,吸附剂的性能直接影响分离效果。因此,在变压吸附技术领域对吸附剂的研究极为活跃,既有对原有吸附剂的改性,又有新型高性能吸附剂的合成。
变压吸附法利用吸附剂对不同气体的吸附力不同,选择性地将气体混合物中某种组分吸附下来,使之和其他气体得到分离。吸附剂有天然沸石、分子筛、活性氧化铝、硅胶和活性炭等。
硅胶(SiO2·nH2O)是一种坚硬、无定形链状和网状结构的硅酸聚合物颗粒,为一种亲水性的极性吸附剂。用硫酸处理硅酸钠的水溶液,生成凝胶,将其水洗除去硫酸钠后经干燥,便得到玻璃状的硅胶。它主要用于干燥、气体混合物及石油组分的分离等。
活性氧化铝(activated alumina,分子式为Al2O3·nH2O)是由铝的水合物经加热脱水制成,活性氧化铝一般都不是纯Al2O3,而是部分水合无定形的多孔结构物质,其中不仅有无定形的凝胶,还有氢氧化铝晶体。由于它的毛细孔通道表面具有较高的活性,故又称活性氧化铝。它对水具有较强的亲和力,是一种对微量水深度干燥的吸附剂。在一定操作条件下,它的干燥深度可达露点-70℃。
活性炭是将木炭、果壳、煤等含碳原料经炭化、活化后制成的。活化方法可分为两大类,即药剂活化法和气体活化法。药剂活化法就是在原料里加入氯化锌、硫化钾等化学药品,在非活性气氛中加热进行炭化和活化。气体活化法是把活性炭原料在非活性气氛中加热,通入水蒸气、二氧化碳、烟气、空气等,并在700~1200℃范围内进行反应使其活化。活性炭含有很多毛细孔构造,具有优异的吸附能力,可用于水处理、脱色、气体吸附等方面。
分子筛吸附剂根据原料和生产工艺分为沸石分子筛、碳分子筛和锂分子筛等,这些分子筛大多应用于某些特定组分的分离。
Cavenati等采用真空变压吸附仪去除天然气中的二氧化碳,得到燃料级甲烷;Zhao等研究了磷酸铝分子筛对二氧化碳的吸附作用,在273K温度下,二氧化碳/甲烷的可选择性高达21.77;Dong等研究了二氧化碳/甲烷/N2三元混合气体的变压吸附热偶精馏过程;Warmuzinski等研究了在变压吸附分离甲烷、氮气混合物的过程中吸附压力对甲烷纯度的影响。变压吸附具有产品纯度高、环境效益好、工艺流程简单、自动化程度高等许多优点,但是变压吸附法能耗高,成本偏高,一般要求选择合适的吸附剂,而且需要多台吸附器并联使用。
③膜分离法。气体膜分离技术是20世纪70年代开发的气体分离技术,其原理是在压力驱动下,借助气体中各组分在高分子膜表面上的吸附能力以及在膜内溶解扩散上的差异,即渗透速率差来进行分离。膜分离的驱动力是压力差,当膜两边存在压力差时,渗透率高的气体组分以很高的渗透速率透过薄膜,形成渗透气,渗透率低的气体则绝大部分在薄膜进气侧形成渗余气,两股气流分别引出,从而达到分离的目的。
二氧化碳分离膜大部分由高分子材料制成,目前应用较为普遍的膜材料有聚砜树脂(PS)、聚酰亚胺(PI)、聚硅氧烷(PDMS)、含氟聚乙胺、聚酰胺等。
聚砜树脂膜是一种力学性能优良、耐热性好、耐微生物降解、价廉易得的膜材料。由聚砜树脂制成的膜具有膜薄、内层孔隙率高且微孔规则等特点,因而常用作气体分离膜的基本材料。如某公司采用聚砜树脂非对称中空纤维膜,并采用硅橡胶涂覆,以消除聚砜树脂中空纤维皮层的微孔,将其用于从合成氨厂弛放气、炼厂气中回收氢气,H2-N2的分离系数可达到30~60。一些研究者通过调整聚砜制膜液配方,降低了制膜液的湿度敏感性。研究表明,在聚砜的分子结构上引入其他基团,可以制成性能更好、应用范围更广的膜材料,聚砜树脂在今后一段时间内将是重要的气体分离膜材料。
聚酰亚胺(PI)膜具有良好的强度和化学稳定性,耐高温。由于PI玻璃态聚合物的僵硬主链对不同分子的筛分作用,PI膜对CO2-CH4、CO2-N2具有很高的分离性能。但PI作为膜材料的最大缺陷是CO2的透过性差。因此,人们通过合成新的PI和化学改性来改善PI的链结构,减弱或消除链之间相互吸引力,增加CO2溶解性,以期提高CO2透过性和分离性。
聚硅氧烷有机硅膜材料的研究和开发一直是一个热点。聚二甲基硅氧烷从结构上看属半无机、半有机结构的高分子,具有许多独特性能,是目前发现的气体渗透性能较好的高分子膜材料之一。我国的一些膜材料研究者已经成功地用它及其改性材料制成富氧膜,普遍用于二氧化碳的分离。
以聚乙胺为代表的芳香族复环状高分子膜,对气体分子的扩散选择性极大。特别是由于聚乙胺高分子的主链结构兼有电子的提供和接受部分,根据高分子链间电子移动的相互作用,形成了独特的柱管结构。气体沿着柱管结构被分离,特别对于分子直径不同的CO2-N2、CO-CH4体系而言,其分离效果尤为突出。
膜分离法是利用一种高分子聚合物薄膜材料,依靠气体在膜中的溶解度不同和扩散速率差异,达到分离的目的。Harasimowicz等研究表明:使用聚酰亚胺膜的毛细管模块可将沼气中甲烷的体积分数从55%~85%提高到91%~94.4%。Makaruk等指出膜渗透法将沼气热值提升至天然气质量等级是可行的,膜系统在运行前需要将气体预处理以保护薄膜。膜渗透法具有工艺复杂、造价昂贵、性能不稳定的特点,存在需要经常更换介质的问题。
④低温液化法。低温液化分离技术依据气体液化温度(沸点)的差异,将气体冷却降温,使气体变成液态时某些组分产生冷凝或冻结,达到分离的目的。与甲烷相比,二氧化碳液化点较高。二氧化碳的焓温值如图1-3所示。

图1-3 二氧化碳的焓温值
高压液化法如图1-3所示的“1-2-3-4”过程,二氧化碳气体经压缩机压缩到较高压力后,冷却到常温下即可液化。常温高压液化采用提高压力的方法使气体二氧化碳在常温下变为液体。当温度为31.1℃、压力为7.38MPa即可开始液化,气体压缩后由冷却器冷却,经气液分离后,液态二氧化碳储存于高压钢瓶内。高压法虽不需要低温制冷设备,工艺简单,但由于压力高和采用钢瓶储存,带来能耗与储运成本增加的问题。
低压液化法工作压力约为2MPa,对应的饱和温度大约为-20℃。低温液化法如图1-3所示的“2'-3'-4'”。二氧化碳气体经压缩机压缩到2MPa左右,冷凝放热,蒸发器里的工质蒸发吸热。二氧化碳气体则在-25~35℃的饱和温度下凝结成液体,储存在液体储罐中。
(2)其他气体的脱除
硫化氢气体是一种无色、高毒性、恶臭、易燃的酸性气体。硫化氢对人体有较大危害,在正常情况下,空气中硫化氢浓度不能超过20mg/m3。慢性硫化氢中毒时会导致头晕恶心,甚至可能神志不清;急性硫化氢中毒时会导致流泪眼痛、咳嗽胸闷,甚至可能导致死亡。在湿热环境下,硫化氢气体会对接触沼气的管道、金属设备等器具造成腐蚀,有可能使其产生氢脆和应力开裂的现象。硫化氢气体对生态环境有较大影响,硫化氢在燃烧时会形成二氧化硫(SO2),与水反应会生成硫酸、亚硫酸等,对大气和水体造成污染。在沼气的生产过程中,硫化氢是在厌氧环境下由蛋白质和其他含硫化合物转化生成。所以,硫化氢的脱除成为沼气等清洁能源在安全生产和综合利用之前所面临的重大挑战。
沼气的水蒸气需要去除,一方面是因为管路中温度和压力变化时,水蒸气增加了管道的压力;另一方面,水蒸气与硫化氢反应,加速了金属管道、阀门及流量计的腐蚀与堵塞。我国环保标准严格规定,利用沼气能源时,沼气中硫化氢含量不得超过0.02g/m3。
①硫化氢脱除技术。脱硫化氢方法有干法脱硫、湿法脱硫及生物法脱硫等。
干法脱硫方法有铁法、活性炭法、活性炭纤维法、氧化锌法、分子筛法、固定吸收谱法等。固体氧化铁(Fe2O3·H2O)法是常用方法之一,生成硫化铁、硫化亚铁,沼气的流速与接触时间对反应影响较大。
干法脱硫是指在脱硫吸收过程和产物处理过程都处于干燥状态的脱硫技术。主要包括氧化锌脱硫法、吸附脱硫法、氧化铁脱硫法等。这种技术是先利用固体脱硫剂和硫化氢气体反应生成硫化物,然后再利用氧气与生成的硫化物反应生成单质硫,同时实现固体脱硫剂的再生。干式脱硫法是气固直接反应的方法,常被用于去除浓度较低的硫化氢气体。干式脱硫技术具有工艺简单、成熟可靠、成本较低等特点,并能够实现较高的净化程度。但这种方法存在工艺设备笨重、更换固体脱硫剂时需消耗大量人力物力、对环境造成污染以及废弃的脱硫剂难以再利用等难题。
固体脱硫剂种类很多,其中金属氧化剂是较好的固体脱硫剂,例如氧化铜、氧化铁、氧化镁等。以三氧化二铁(Fe2O3)作为脱硫剂的金属氧化物干法脱硫是常用的干式脱硫法。在脱硫过程中脱硫剂Fe2O3与硫化氢发生化学反应生成三硫化二铁(Fe2S3)、硫化亚铁(FeS)、单质S,硫化氢被吸收,当脱硫剂吸收硫化氢处于饱和状态时,与氧气反应使脱硫剂实现还原再生。
吸附脱硫法可分为物理吸附脱硫和化学吸附脱硫。物理吸附脱硫法是通过物理作用力将硫化物吸附在吸附剂上实现脱除的技术,在吸附的过程中无化学反应发生。物理吸附剂的种类很多,主要包括多孔碳材料、分子筛、金属有机骨架化合物(MOFs)材料等。化学吸附脱硫法是先将硫在吸附剂表面转化成其他形式的硫化物,然后再将其选择性地吸附在吸附剂上,从而实现硫脱除的方法。根据脱硫反应的类型,可将化学吸附脱硫法分为还原型反应吸附脱硫法和氧化型反应吸附脱硫法。常用的还原型反应吸附剂包括Ni/ZnO、Ni/MnO、Ni/分子筛、Ni/Al2O3等复合材料。
湿法脱硫用于处理燃气量大、含硫量高的气体。湿法脱硫技术主要是使待处理的气体与溶剂逆向接触进行脱硫,可分为吸收和氧化两类,具有溶剂可再生利用、自动化程度高、脱硫效率高、适应范围广等特点。但湿法脱硫也存在消耗药剂量巨大、初期投资大、运行成本高,在脱硫过程中会造成资源浪费等问题。常用湿式脱硫法有氧化钙石灰-石膏脱硫法(碱法)、氢氧化钠(NaOH)脱硫法、胺法、海水脱硫法等。
氢氧化钠脱硫法通常分为两个步骤。第一步使用NaOH溶液对混合气体进行洗涤,脱除约80%的硫化氢气体。第二步使用次氯酸钠(NaClO)和NaOH的混合溶液再次洗涤混合气体,进一步脱除剩余的硫化氢气体。
氢氧化钠脱硫法采用较高浓度的碱液吸收硫化氢,但碱液在循环使用中容易发生结垢的现象,使循环泵发生堵塞。同时,脱硫过程中使用的化学原料无法循环使用,运行成本较高,所以现在基本不再使用氢氧化钠法脱硫。
胺法脱硫是指使用胺液吸收硫化氢的方法,主要分为两步。第一步:碱性的胺液在常温高压环境下与混合气体中的硫化氢发生反应,硫化氢气体被转移到液相中,达到脱硫的效果。第二步:在低压高温环境中,酸性组分从吸收液中分离出来,胺液被再次利用。根据脱除对象的不同,胺法脱硫被分为两类:常规胺法与选择性胺法。常规胺法不仅脱除硫化氢,同时也会脱除二氧化碳。选择性胺法仅对硫化氢进行专一脱除。李坚等人将PDS法应用于某沼气脱硫的研究与试验,脱硫效率高达90%。胡明成等人采用三氯化铁吸收-电化学再生方法研究表明:硫化氢的吸收效率可以达到85%~92%。
采用复合型甲基二乙醇胺(MDEA)作为脱硫剂对硫化氢进行脱除,效果比较显著。但这种方法的缺点是吸收液容易受到酸性杂质的污染,导致工艺中对吸收液的维护比较复杂。催化氧化法脱硫技术也是一种常见的脱硫技术。它是借助一种或多种氧化剂和硫化物反应,再通过萃取等方法脱除硫化物的技术。这种技术的核心是氧化剂和催化剂的选择。常用的氧化剂主要有H2O2、过氧化物、无机强氧化剂等;常用的催化剂主要有有机酸、无机酸和金属杂多酸等酸性催化剂。PDS(双核酞菁钴磺酸)脱硫法、克劳斯脱硫法是典型的两种催化氧化脱硫法。
PDS脱硫法是以酞菁钴磺酸盐为催化剂,将沼气中的硫化氢在液相中氧化的方法。该工艺主要由硫吸收、氧化再生、硫分离三个阶段构成。PDS脱硫液在硫化氢吸收塔中将气体吸收转化成为硫氢化钠(NaHS),然后进入再生系统,NaHS被氧化得到硫单质并离开系统,富液变为贫液,实现循环使用。
克劳斯脱硫法主要分为三个阶段。第一阶段为热反应阶段,部分硫化氢气体在高温炉内与氧气发生反应转变为SO2。第二阶段是克劳斯反应阶段,高浓度的硫化氢在催化剂的作用下和SO2继续反应转化成单质硫,从而回收高纯度的硫黄。第三阶段为尾气处理阶段,经第二阶段处理后还会有一定量二氧化碳、SO2、硫化氢剩余,所以需要进一步的处理。
生物法脱硫通过微生物去除硫。黄兵等用生物膜填料塔进行了去除硫化氢废气的研究,生物法脱硫存在效率低、微生物生长周期长以及工业化程度不高的缺陷,仍有待于深入研究。
生物法脱硫又被叫作生物催化脱硫(biocatalytic desulfurizaton,简称BDS),是一种常温常压下利用脱硫细菌将硫化物转化为单质硫或硫酸盐的脱硫方法。生物法脱硫的基本原理是:硫化氢气体被吸收液吸收转化为硫化物,然后被脱硫细菌吸收至体内,作为营养物质被脱硫细菌分解、氧化、利用,在脱硫的同时为脱硫细菌的生长繁衍提供能量。生物法脱硫的过程主要分为3个阶段:
a.硫化氢气体的吸收过程:硫化氢气体由气相转移至液相,被吸收液吸收转变为硫化物;
b.硫化物的吸附吸收过程:溶解至水溶液中的硫化物被脱硫细菌吸收吸附,从水溶液中转移至脱硫细菌的体内;
c.生物氧化的过程:进入脱硫细菌体内的硫化物被用作能源或养分在细菌体内酶作用下氧化分解和利用,从而达到去除硫化氢的目的。
生物法脱硫可分为酸法生物脱硫和碱法生物脱硫。
酸法生物脱硫通常采用氧化硫硫杆菌和氧化亚铁硫杆菌进行硫化物的氧化,这些细菌具有嗜酸性,生物反应器中的溶液环境呈酸性,pH值通常为2~6,氧化产物主要是。
发生的化学反应为:



奥地利英环(EnvironTec)生物滤池脱硫工艺和Bio-SR工艺就是两种典型的酸法生物脱硫。但酸法生物脱硫过程中,吸收液对硫化氢吸收效率较慢,需要较长的气体停留时间,吸收塔的体积大,建设成本高。
碱法生物脱硫是指采用排硫硫杆菌作为脱硫细菌进行生物脱硫的方法,生物反应的环境呈中性或碱性。生物反应器中溶液呈碱性,氧化产物主要是单质S,对硫化氢的吸收效率高,停留时间短,吸收塔体积小。
荷兰帕克公司的壳牌-帕克工艺(shell-PAQ工艺)是一种碱法生物脱硫工艺,其脱硫基本原理主要由两部分组成:第一部分为硫化氢的吸收,将硫化氢气体和洗涤塔里含硫细菌的碱性溶液进行接触,硫化氢溶解在碱液中并随碱液进入生物反应器中;第二部分是脱硫细菌氧化硫化物,主要是生物反应器在曝气环境下,硫化物被脱硫细菌(硫杆菌属)氧化成单质S,硫黄以料浆的形式通过沉降槽和硫渣分离器从生物反应器中析出,通过进一步干燥成硫黄粉末或经熔融生成商品硫黄。
1993年,荷兰帕克(Paques)公司开发出基于排硫硫杆菌的沼气生物脱硫工艺。1997年,英荷皇家壳牌公司与帕克公司合作,进一步推广生物脱硫技术,2002年生物脱硫技术成功应用于天然气脱硫。2004年,英荷皇家壳牌、帕克、美国UOP公司合作,把生物脱硫技术应用于炼油厂尾气处理。2008年,美国NATCO公司与帕克公司合作推广生物脱硫技术。生物脱硫技术逐渐应用于沼气、合成气(煤制氢、煤制甲醇)、炼油厂尾气、造纸业等不同领域。2011年,鉴于生物脱硫技术广阔的应用前景,英荷皇家壳牌公司与帕克公司各出资50%成立新的合资公司,致力于生物脱硫技术在石油和天然气领域的推广应用。
荷兰帕克公司自1993年开发沼气碱法生物脱硫工艺,现今已成功把碱法生物脱硫技术应用于多个领域,但对于如何提高单质硫的生成率,出于技术保密原因,没有相关的论文发表。San-Valerop等人研制了一种全好氧生物脱硫装置,采用吸收塔和鼓泡塔生物反应器耦合的方法,使硫化氢去除率稳定在80%以上。Song等设计了上流式内循环缺氧反应器,硫化物的去除率约为95.2%。陆慧锋等人在某中试项目中对一体式沼气安全脱硫反应器的操作进行优化,沼气脱硫率为93.8%。刘卫国等人建立了碱法生物脱硫技术的中试项目,硫化氢含量在3000~4000mg/m3之间,硫去除率可达95%。由于难以控制单质硫的生成率,除帕克公司外,近几年生物脱硫技术研究仍然集中在实验室小试和现场中试阶段。
②H2O脱除技术。沼气中H2O的脱除方法,主要有冷凝法、吸收法、吸附法。冷凝法用于大量水分子的脱除。吸收用的脱水剂有氯化钙、氯化锂及甘醇类。
天然气脱水采用甘醇胺、二甘醇水溶液(DEG)和三甘醇水溶液(TEG)。三甘醇脱水工艺属于溶剂吸收法,是目前天然气工业中应用最普遍的方法之一。其利用吸收原理,采用甘醇类物质作为吸收剂与天然气充分接触,使水传递到溶剂中从而达到脱水的目的。
在甘醇的分子结构中含有羟基和醚键,能与水形成氢键,对水有极强的亲和力,具有较高的脱水深度。三甘醇属甘醇类,再生容易,其贫液质量分数可达98%~99%,具有更大的露点降,且运行成本较低。实践证明DEG和TEG法是有效的。吸附法用于少量的水分子脱水,此方法对气温、流速、压力变化不敏感。