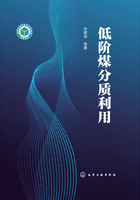
2.1 低阶煤中低温热解基本原理
低阶煤中低温热解的自由基理论、基本反应、热力学原理已经在第1章有所涉及,以下主要对反应动力学、影响因素进行论述。
2.1.1 热解反应动力学
利用热解反应动力学可以研究低阶煤在热解过程中的反应历程、反应速度、反应控制因素和反应动力学参数,是认识低阶煤的中低温热解机理的前提和基础,也是获得影响转化因素的重要方法。目前,煤热解反应动力学的研究主要包括两方面的内容:胶质体反应动力学和脱挥发分动力学。
2.1.1.1 胶质体反应动力学
Krevelen等根据煤的热解阶段的划分,提出了胶质体理论,对大量的实验结果进行了定量描述。该理论首先假设焦炭的形成是由三个串联反应形成的:
(2-1)
(2-2)
(2-3)
式中,k为反应速率常数,s-1;E为活化能,J/mol。
其中,式(2-1)是解聚反应,该反应生成不稳定的中间相,即所谓胶质体。式(2-2)为裂解缩聚反应,在该过程中焦油挥发,非芳香基团脱落,最后形成半焦。式(2-3)是缩聚脱气反应,在该反应过程中,半焦体积收缩产生裂纹。解聚裂解反应一般都是一级反应,因此可以假定式(2-1)和式(2-2)都是一级反应,而式(2-3)比式(2-1)和式(2-2)要复杂得多,但仍然假定它也是一级反应。这样上面的三个反应可用以下三个动力学方程式描述:
(2-4)
(2-5)
(2-6)
式中,t为反应时间,s。
在炼焦过程中k1和k2几乎相等,故可以认为k1=k2=k3。在引入t=0时的边界条件和一些经验性的近似条件后,上述微分方程可以得到如下解:
[P]=[P]0e-kt (2-7)
(2-8)
(2-9)
式中,为经过修正后的反应速率常数,s-1。
相关的实验结果表明,该动力学理论与结焦性煤在加热时所观察到的一些现象相当吻合,说明其具有一定的合理性。此外,利用Arrhenius公式,还可以求得反应活化能E:
(2-10)
式中,R为理想气体常数,J/(mol·K);T为热力学温度,K;b为常数。
结果显示,所求得的煤热解活化能为209~251kJ/mol,与聚丙烯和聚苯乙烯等聚合物裂解的活化能相近,大致相当于—CH2—CH2—的键能。一般来说,煤开始热解阶段E值小而k值大;随着温度的升高,热解逐渐加深,则E值增大,k值减小。式(2-1)~式(2-3)三个依次相连的反应,其反应速率常数k1>k2>k3。另外,不同煤化程度的煤其热解的平均表观活化能不一,会随煤化度的提高而增高。一般气煤和焦煤的活化能分别为148kJ/mol和224kJ/mol。
2.1.1.2 脱挥发分动力学
通常认为,煤热解是一个自由基反应,主要包括自由基碎片的生成及其稳定形成挥发产物和热解半焦,一般称为一次反应;此外,热解产生的挥发物在逸出过程中还会发生反应,包含挥发物二次裂解产生的自由基碎片以及由其再结合形成其他产物的反应,一般称为二次反应。在热解过程中,挥发分的逸出导致热解样品质量变化,而且挥发物会随热解气氛的带出而减少二次反应的发生,因此可以借助热重法测定在一定的加热速率样品质量的变化情况,从而实现煤热解脱挥发分动力学的研究。根据热解升温速率的不同,可分为等温和非等温(程序升温)法。
(1)等温热解
一般地,将煤加热至预定温度T、保持恒温、测量样品质量随时间的变化、建立失重曲线,从失重曲线在各点的切线可以求出-dW/t。恒重时,-dW/t=0。在测定温度T下的最终失重(-ΔWe),一般要在失重趋于平稳后数小时后才能测得。其反应速率常数可通过下式计算:
(2-11)
式中,x为对应于反应时间t时的失重量与最大失重量的比值。
按照一级反应来求算得到的表观活化能只有20kJ/mol左右。这可能与以下几个因素有关:①初始阶段,煤颗粒温度低于热源温度,煤粒内部微孔系统内产生了暂时的温度和压力梯度(挥发分浓度梯度),此时热解过程是扩散控制而不是反应速度控制,测得的活化能实际上是挥发分扩散活化能。所以,热解速率(反应速率)和挥发速率(反应与扩散的总速率)是两个不完全相同的概念。②在等温热解过程中,煤的一次热解和二次缩聚反应会发生部分重叠,但是又很难通过样品质量变化体现出来,所以计算结果与真实值有偏差。至于等温脱挥发分过程究竟是由扩散控制还是由挥发物的生成过程控制还尚未有定论。由于环境的不同,两种过程都有可能是主要的析出机理。
(2)非等温(程序升温)热解
等温热解中,所测得的活化能是所选温度范围内的平均值,并不能准确反映热解反应过程的情况。与等温热解法相比,非等温热解法具有以下优点:①由于记录的是整个升温过程的质量变化,因此可以反映整个测定温度范围内的热解情况,在计算活化能的温度范围时可避免因温度范围选择不当而造成的实验数据的不可比性;②可消除因取样差异而引起的实验误差;③可避免将样品在一瞬间升到考察温度时所发生的崩裂等问题;④原则上讲,程序升温法可从一条失重速率曲线得到整个温度范围内的动力学参数,因此极大方便和简化了测定方法,并且在可靠性上能够达到与等温法相一致的结果。对于某一反应来说,气体析出速率与浓度的关系为:
(2-12)
(2-13)
式中,η为煤热解转化率,%;n为反应级数;A为指前因子,s-1;M0为试样起始质量,g;M,ΔM分别为试样在热解过程中某一时刻的质量和失重量,g;Mf,ΔMf分别为试样在热解终点的剩余质量和失重量,g。
关于反应级数n有许多不尽相同的讨论。由于煤的热失重或脱挥发分速率与煤种、煤阶、升温速率、反应压力和反应气氛等密切相关,所以还没有统一的动力学方程可以描述。对应线性升温过程,Coats-Redfern方法较为简明。
设温度T与时间t有线性关系
T=T0+λt (2-14)
式中,λ为升温速率,K/s。
联立两式可以得到如下近似解:
(2-15)
(2-16)
对于一般的反应和大部分的E来说,2RT/E远小于1,因此式(2-15)和式(2-16)可以进一步简化。通过选择合适的反应级数(n值),可以得到一条直线,利用直线的斜率和截距,便可求得活化能E和指前因子A。
众多研究发现,活化能E较大的情况下,其指前因子A也较大,这一对参数之间存在线性互补性,可以用式(2-17)进行表述:
lnA=aE+b (2-17)
式中,a、b为补偿参数。Zsakó认为,参数a是由反应中化学键断裂的能量决定的,而参数b与反应的某些特性有关。此外煤的热解、燃烧、挥发分的释出、气化反应等过程均存在补偿效应。
上述的热解动力学模型属于单一反应模型,并没有涉及挥发分的具体成分,得到的活化能为测定温度范围内的平均值。此外,为了获得煤热解动力学参数,其他反应模型,如双竞争反应模型、有限多平行反应模型和无限多平行反应模型被开发。其中,双竞争反应模型由于需要参数较多(6个),所以其应用受到限制较大;而有限多平行反应模型是把煤热解过程看成一种或多种物质热裂解的平行反应,所以对于平行反应的个数确定需要经验。Anthony等认为,煤是复杂的高分子化合物,其热解过程是由无限多个平行一级反应组成,且反应数目足够大以至于可以用高斯分布连续函数来表示反应的活化能,以此为基础建立了分布活化能模型(distributed activation energy model,DAEM)或多重反应模型(multiple reaction model,MRM)。该模型认为,煤热解是由无数个平行的一级化学反应的组合,并且反应可以用相似化学方程式来表示:
(2-18)
式中,i代表某个独立的化学反应或者某个反应物;ki为i组分的化学反应速率常数;V为某时刻析出的挥发分量;V*为当t→∞时挥发分量。
ki由Arrhenius公式给出:
(2-19)
式中,k0为活化能的频率因子。
由于所假设的反应数目足够大,所以活化能的分布可以由一个分布函数f*(E)来表示。那么V*f*(E)dE则表示活化能在E至E+dE区间内的潜在挥发分部分,活化能分布函数应满足。因此某时刻挥发分量为:
(2-20)
通常f*(E)用高斯分布来表示,平均活化能为E0,活化能的频率因子为k0,标准方差为σ。将式(2-19)代入式(2-20)得到:
(2-21)
但是分布活化能模型仍存在一些缺点,例如双重积分的计算量大,不能预先估计积分误差。Donskoi等采用一种优化方法对分布活化能模型进行简化。该方法计算量减少,节省时间,并实现了误差的直接估计。优化模型方法建立在Gauss-Hermite Quadrature基础上:
(2-22)
式中,xi是埃尔米特多项式的零点;wi是高斯-埃尔米特积分中的重量;),活化能用公式
进行表示;m为缩放系数。
将式(2-22)代入式(2-21):
(2-23)
其中,式(2-23)看似复杂,但
在给定的模型形态中只需计算一次,相比较来说大大减少了计算量。
经过长期的发展,DAEM模型在利用热重法进行煤热解动力学研究方面取得了很大的进展,一系列处理方法相继被建立。例如,Miura等通过阶跃近似函数理论,建立了更简单、精确的求解DAEM中的活化能及频率因子的方法,即Miura积分法:
(2-24)
式中,h为恒定升温速率。由式(2-24)可知,要想求得反应活化能,需要以下几个步骤:
①测得同一样品在不同升温速率下(至少3个)的热失重曲线。
②计算不同升温速率失重曲线上,同一失重率xi下对应的h/T2值,然后将几条失重曲线上处于同一失重率水平的点连接起来,按照对于1/T作图,根据斜率求出该失重率xi下的Ei。
③重复上述步骤,最后得到不同的失重率xi下的活化能Ei,并将失重率对活化能作图,即可得到热解过程中活化能随反应转化率变化曲线;将失重率对于活化能进行微分,就得到活化能的分布曲线f(E)。Miura等人的研究结果表明,该方法获得的活化能更加精确。
杨景标等利用程序升温热重技术比较了单一反应模型与DAEM对宝日希勒褐煤和包头烟煤热解动力学分析的适应性。认为单一反应模型需要对一条失重曲线进行分段处理,只能得到某一温度范围内活化能的平均值;Miura积分法可以直接得到热解的活化能分布及频率因子;DAEM能够描述非等温热解逐渐升温的全过程,对于煤种变化和升温速率变化有更好的适应性。
除上述常用的处理方法,还有其他方法,如Friedman法。与DAEM法类似,Friedman法也需要利用不同升温速率下的失重曲线来求出活化能,但区别在于后者并不需要假设反应机理函数而直接求得活化能,从而可避免由于不同的反应机理函数的假设而可能带来的误差,常被用来检验其他方法求得活化能值的精确性。
上述方法尽管认为煤热解是由无数个平行的一级化学反应组合的过程,但是这些模型仍难以区分煤的不同热解阶段,尤其是挥发分的二次反应。为了完善DAEM模型,Caprariis等提出了2-DAEM模型(double distributed activation energy model,2-DAEM)。该模型假设热解过程发生两步反应:首先是初级热解过程中焦油和烃类气体的形成,然后是热解过程半焦的缩聚、交联等二次反应以及气体的进一步形成。通常,2-DAEM模型的数学表述如下:
(2-25)
其中,fi(E)与热解的两个步骤相关,符合高斯函数,可以定义为:
(2-26)
其中,w权衡了两个热解反应的程度,其范围是0到1,代表了在初级和二次热解反应中挥发分释放量的多少。w的值为0,表示所有的挥发分是在二次热解反应中生成;w的值为1,所有的挥发分在初级热解中释放。
在这种情况下,五个参数需要估算:两个平均活化能E01和E02,两个标准差σE1和σE2以及w。
双分布活化能结构模型由于考虑到煤热解过程的初级反应及二次反应,所以能够较好地描述煤的热解过程,再现煤热解过程中两个不同的步骤,计算值与实验数据相符,因此可以很好地解决传统单分布活化能模型描述煤热解过程中不够准确的问题。
2.1.2 煤热解影响因素
煤的热解过程不仅与煤本身的物理和化学性质(内因)有关,还与热解发生的条件(外因)密切相关。其中,内因主要包括煤化程度、煤样粒度、岩相组成和矿物质组成与含量等;外因包括热解温度、热解气氛、热解压力、加热速率、停留时间等。因此,深入认识各种因素对热解影响的规律对开发新工艺、确定工艺条件非常必要。
2.1.2.1 煤化程度
煤化程度可以用煤阶来反映,它是影响煤热解最重要的因素之一,直接影响着煤的热解特性、产物分布及性质。从表2-1可见,随煤化程度增加,初始热解温度逐渐增加,通常褐煤的初始热解温度最低,而无烟煤最高。
表2-1 不同煤阶的初始热解温度比较

在相同热解条件下,煤化程度不同,其热解产物也不同。表2-2给出了在550℃热解温度下几种典型煤的热解产物分布。可以看出,对于煤化程度较低的煤(如褐煤)热解时,由于其煤阶较低、氧含量和水含量较高,所以煤气、焦油和热解水产率高。对于像烟煤等中等变质的煤热解时,煤气与焦油产率较高,而热解水产率少;但是对于煤化程度较高的煤(如贫煤)热解时,焦油与煤气产率都很低,容易产生大量焦粉(脱气干煤粉)。总体来说,随着煤化程度的增加,煤的热解反应活性降低。但是从黏结性和结焦性来看,年轻的褐煤或越年老的煤黏结性几乎没有,只有中等变质程度的烟煤具有良好的黏结性和结焦性,是生产高强度焦炭的优质原料。
表2-2 煤化程度与热解产物分布间的关系(550℃)

2.1.2.2 热解温度
温度是除煤自身性质外,影响煤热解最重要的因素,它不但影响煤的一次热解反应,而且还影响初次热解产物的二次反应。
从理论上讲,当无二次反应发生的情况下,煤一次热解产生的挥发性产率会随热解温度升高而增加;但是由于二次反应的发生,导致一次热解产生的焦油在高温下再次发生裂解反应和缩聚反应,焦油产率减少、气体产率增加,同时半焦会发生再聚合反应,使得气体产率增加而半焦产率减少。Hayashi等发现,热解温度对二次反应的影响超过预期。他利用流化床反应器,通过控制密相区、稀相区温度作为变量对次烟煤进行热解研究。研究显示,当密相区温度(500~700℃)一定时,焦油产率随着稀相区温度(500~800℃)升高而降低,这可能是同样煤在不同反应器上热解产物不一样的主要原因;而当稀相区温度一定时,焦油产率在600℃时反而达到最大。李海滨等利用流化床反应器对神木煤进行热解,为了抑制稀相区二次反应,控制初始热解产物在密相区停留时间<0.5s,到取样口的时间约0.05~0.1s。研究发现,随着密相区温度(400~900℃)的提高,液相产物产率呈现出先增加后降低趋势,在600~650℃左右达到最大。提高密相区温度有利于H2、CO、CH4及C2H4的生成。
对于不同的煤种,即使是在同一种反应器,最高热解焦油产率对应的温度也不同。例如,Shen和Zhang在流化床中对澳大利亚褐煤的研究表明,其焦油产率在550℃时达到最大值。而Tyler等使用流化床反应器对维多利亚褐煤进行热解,发现其焦油产率在580℃时达到最大值。这种差异与煤性质、粒径大小、热解停留时间长短等密切相关。
2.1.2.3 热解压力
煤热解通常在常压下进行,一方面可以降低运行成本,另一方面较高的反应压力会增加二次反应的概率,但是近年来加压气化技术的迅速发展,使得对于加压热解的研究必要性日益凸显。究其原因在于,尽管整个气化过程中加压热解反应很短,但几乎所有的挥发物(气态烃类和焦油)均来自此热解,因此加压热解的研究对于降低焦油的形成和提高气体热值具有重要意义。研究发现,增加热解压力,热解挥发物停留时间增加,有助于煤的黏结性改善,但同样会促使热解焦油的二次反应发生,形成热解气体和半焦。但是部分研究者正是利用二次反应的发生来改善热解焦油的产率和品质。例如在加氢热解过程中,尽管氢压增加同样使热解焦油进一步发生裂解或聚合,但是同时也活化了分子氢,更多的活性氢参与焦油的生成,抑制了煤热解产生的大分子自由基间的聚合,提高了液相产率。
2.1.2.4 加热速率
由于煤的导热性差,加热速率的提高使得传至煤层内部的温度滞后,从而煤热解的各个阶段在更高的温度区间内发生。根据加热速率的不同,一般可以将煤热解分为慢速热解(<1℃/s)、中速热解(5~100℃/s)、快速热解(500~106℃/s)和闪裂解(>106℃/s)。升温速率对煤热解的影响如表2-3所示。
表2-3 升温速率对煤热解的影响

由表2-3可见,挥发物的析出温度受加热速率影响显著。众所周知,热解为吸热反应,而煤的导热性差,提高加热速率时,颗粒表面和内部温度滞后更加显著,所以宏观表现出来的是热解气体开始析出温度和最大析出的温度都随升温速率的增加而向高温移动。然而,提高升温速率,加快了热解挥发物的溢出速率,相应地降低了挥发物在热解区的停留时间,使得热解初次产物发生二次反应的概率大大减小,从而提高了热解焦油产率。因此,在实际应用中,为了提高热解过程焦油的产率,通常会采用煤的快速热解,但是所得焦油重质组分含量高、品质相对较差。
此外,研究人员还发现,升温速率对煤的黏结性和结焦性有明显的影响。由表2-4和表2-5可见,随着升温速率的增加,气煤的胶质体温度范围由76℃增加到96℃,鲁尔膨胀度也增加,说明煤的黏结性提高;但是收缩度却大幅度下降。这种变化一方面与煤的较差的导热性有关。煤的热解是吸热反应,在较高的升温速率下,温度滞后更加明显,颗粒内部温度明显低于热解区温度,因此部分结构来不及分解,而生成的产物来不及挥发,使得胶质体的开始软化温度和固化的温度都向高温侧偏移。固化温度的提高,增加了胶质体的停留时间,其黏结性得以改善。另一方面,在较高的升温速率条件下,焦油的生成速率显著地高于其挥发和分解的速率,所以胶质层厚度增加,膨胀度增加,收缩度减小,有利于黏结。对于焦炉来说,若提高升温速率,煤的黏结性会有明显的改善。
表2-4 升温速率对气煤胶质体温度范围的影响

表2-5 升温速率对膨胀度和收缩率的影响

加热速率的提高也导致了热解焦油产率的增加。究其原因,主要是两方面作用的结果:其一,在较高的加热速率下,煤结构受到较强的热作用,一些化学键断裂伴随着气相产物的溢出,使得内部的压力迅速累积,迫使焦油前驱体的析出量增加;其二,在高加热速率下,氢的析出和共价键的断裂共同抑制了热解产物再聚合反应的发生,产物析出速率加快,减少了二次反应的概率。Gibbins等认为,较高的加热速率将有效降低二次反应的发生,这与Gavalas等发现的流化床条件下热解焦油的产率远高于固定床中的结果相一致。
2.1.2.5 停留时间
无论是热解时气相挥发物(气体和焦油蒸气)的停留时间还是固体颗粒(半焦颗粒)的停留时间,它们都会显著影响最终气体、焦油和半焦的组成与分布。气相产物的停留时间包括热解挥发分在煤颗粒内的停留及在反应器内的停留时间。通常情况下,热解产生的一次焦油会随着挥发分停留时间的增加进一步发生裂解反应,进而生成气体或者发生缩聚反应生成重油或焦炭,使得热解焦油的产量下降;同时,初始热解气体产物中的烃类(如甲烷、乙烷等)也会发生热/催化裂解,改变了热解气体组成和收率。热解挥发物在热解区的停留时间对二次反应的影响也与裂解温度相关。当反应属于动力控制区,温度影响占主要地位;当反应属于扩散控制区,反应时间影响较大。对于为了获得较高焦油产率的热解工艺来说,应该尽可能降低挥发物在热解区的停留时间,而对提高焦油品质、降低重质组分含量的热解工艺来说,可以考虑通过延长停留时间来促进二次反应的进行。停留时间对于固体(半焦)的影响主要是煤中挥发分的逸出程度,延长固体停留时间能促进煤内挥发分的充分逸出,热解进行更加充分。
2.1.2.6 热解气氛
热解气氛是影响热解过程和产物形成的另外一个重要因素,主要通过与煤热解产生的自由基相互作用而体现。煤热解是一个自由基反应,在较高温度下,煤中弱共价键会发生断裂,产生大量的自由基,并从煤颗粒内部逐渐扩散至热解区。由于这些自由基具有极高的反应活性,在扩散过程中通过相互结合生成了气体、焦油或者半焦等产物。一般来说,当小分子自由基相互聚合时会形成气体;小分子自由基与大分子自由基结合形成焦油;但大分子自由基间聚合往往生成半焦,因此研究者希望通过对热解过程自由基的控制来调控热解过程产物的分布和产率。例如,在加氢热解过程中,由于氢自由基具有较小的自由程和反应活性,所以易和煤裂解产生的自由基结合,降低了大分子自由基间聚合反应的可能性,提高生成芳香族化合物等的概率,因此氢(氢气或其他供氢溶剂)可作为自由基的稳定剂。此外,利用氧与煤之间的氧化作用,可以实现工业上煤的破黏或者提高煤热解的转化率等。
除氢气和氮气外,其他气体如CH4、CO2、氧气(空气)、焦炉气、水蒸气、热解煤气等都可用于煤的热解气氛。众多研究表明,热解气氛对热解产物的产率和质量均有重要的影响。例如,当煤在富氢气氛(纯H2气氛以及焦炉气、热解气等含H2气氛)下热解时,能够大幅度地提高焦油的收率和改善焦油质量及半焦品质,因而受到广泛重视。但是如何降低制氢成本是其工业化应用的一个需要考虑的因素。
2.1.2.7 颗粒粒径
煤的粒径主要影响传热、传质过程和热解初始产物的二次反应,因此对于热解的影响相对比较复杂。现有的关于颗粒粒径影响的研究大都是针对粉煤级别的。随着工业生产中煤的粒径的增大,对于毫米级颗粒煤热解来说,颗粒粒径对热解过程的影响也越来越受到人们的重视。总体来讲,随着煤的粒度减小,其比表面积增加,传热、传质速度加快,胶质体厚度减少,而黏度增加。但是粒径的减小不利于煤的黏结性提高。一方面,煤开始软化温度和胶质体固化温度降低,胶质体温度间隔缩小,故使黏结性降低;另一方面,较小的粒径使得挥发物脱除速度提高,膨胀压力降低,不利于煤的黏结。
2.1.2.8 煤预处理
热解前煤的预处理是提高热解转化率和调控热解产物分布的一种重要途径,主要通过提高煤中氢含量或者改变煤中大分子间的作用力等方式,提高热解过程中产生的自由基数量和种类,达到提高热解焦油的产率和改善焦油品质的目的。
目前采用的预处理方式多种多样,有溶剂溶胀预处理、热预处理、离子液体萃取等。其中,溶剂溶胀预处理研究相对较多,主要是利用溶剂的作用,弱化煤的大分子结构与小分子之间的缔合作用,降低其交联程度,促使煤中氢键及一些弱非共价键断裂来提高煤的反应性。单一溶剂如甲醇、丙酮、N-甲基吡咯烷酮(NMP)、四氢呋喃、吡啶、四氢萘,混合极性溶剂(如CS2/NMP)甚至超临界二氧化碳、甲苯、水等都可以用于煤的溶剂预处理。经过溶剂溶胀预处理煤的热解焦油产率提高的主要原因可归结于三个方面:①从煤的结构来看,溶胀处理降低了煤的交联程度,弱化了煤中大分子相与小分子相之间的作用力,煤分子内部流动性增强,在热作用下煤中一些化学键更加容易断裂,能够产生更多的自由基碎片;②从传质角度来看,由于溶剂分子可以进入煤的微孔,网络结构变得疏松,缩短了热解气相产物在煤中的滞留时间,减小了焦油发生二次反应的概率,提高了焦油产率;③从自由基的反应过程来看,溶胀过程有助于一些小分子自由基(如·H和·CH3)的生成,降低了焦油前驱体之间的聚合概率,提高了焦油产率。热预处理是采用不同的气氛(如水蒸气)、处理温度和时间等对煤进行低温处理,然后再进行煤的中低温热解。不同预处理气氛对煤热解产物分布影响规律尚无定论。
2.1.2.9 催化剂
使用催化剂的热解称为催化热解。催化剂的主要作用是降低煤热解温度、提高热解转化率或目标产物产率。从催化剂的作用过程来看,可以催化煤的一次热解反应,也可以催化热解挥发物的二次反应。碱金属、碱土金属、过渡金属化合物、天然矿石、沸石分子筛,甚至热解半焦、活性炭等均可用于催化热解。
催化剂的添加方式也有多种多样,具体将在2.4.3部分进行详细介绍。
2.1.2.10 热解反应器结构形式
为了提高煤的传热传质效率、降低热解产物的二次反应概率和解决热解系统堵塞等问题,研究者对反应器的结构进行了多方面的探索,设计建立的反应器结构多种多样,但按煤颗粒在反应器内的相对运动状态可分为固定床、流化床、气流床、输送床等;按加热方式分为外热式、内热式和内外混合式。
反应器的结构形式会显著影响焦油的产率和品质。其中,煤颗粒的传热速率、返混程度、生成的热解挥发物在反应器内停留时间等直接影响煤焦油的产率;气体在床层内的扰动程度、热解挥发物的停留时间等会影响焦油的品质,主要表现为焦油中的含尘量、含水量及重质组分含量。这些反应器各有优缺,相对来说,外热式固定床反应器结构简单、操作方便、返混小,但由于煤导热性差导致传热速率较差,生成的挥发物在反应器内停留时间较长,所以焦油收率低,但是焦油含尘量少、品质较好。对于内热式固定床、流化床、气流床等反应器来说,由于气体的扰动可以实现热载体与煤颗粒的快速、充分混合,传热效率大大提高,并且由于气体的带动作用,降低了热解挥发物在反应器内的停留时间,部分抑制了焦油的二次热解,所以焦油收率较高。缺点是,焦油蒸气中会夹带大量粉尘进入除尘系统,部分灰尘甚至会作为重质组分聚合的载体,导致后续焦油除尘困难甚至堵塞除尘系统;存在焦油中灰分高、品质较差等问题。
综上可见,煤热解是一个复杂的传热、传质和反应过程,受煤本身性质和众多操作参数的相互影响,这就需要在具体热解工艺开发过程中给予综合性考虑。