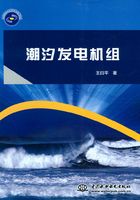
3.8 灯泡贯流机组CFD分析
3.8.1CFD定常流动分析模型
近年来,计算流体动力学(ComputationalFluik Dynamics,CFD)得到迅速发展,
利用CFD技术可以优化转轮叶片设计,以减少制作模型转轮叶片数量和上模型试验台做试验的次数;在老电站技术改造中,利用CFD技术可分析原水轮机的不足,然后提出优化措施,这可大大提高水轮机设计的质量和效率。
水轮机工作介质是水,水在流动分析中被视为不可压缩的流体,因此,水轮机内部的流动分析属于不可压三维湍流问题。全三维湍流N—S方程是目前描述流体运动比较准确的数学模型。求解N—S方程的方法主要包括雷诺时均方程(RANS)法和大涡模拟(LES)法。
由于大涡模拟对网格尺度要求高,特别在湍流活跃的剪切区、逆压梯度区和近壁区,要求计算域内的网格足够密,湍流的多尺度特性所要求的网格密度是目前计算机无法承受的,因此,在对真机的模拟中,采用大涡模拟进行大量工况的计算在现阶段还不现实。而雷诺平均方程为统计模型,对计算资源的要求远远小于大涡模拟,因此,在目前的条件下,宜采用以雷诺平均方程为基础的湍流模型,计算中采用了SSTκ—ω模型。
其中,静止坐标系中雷诺平均N—S方程如下:
∂∂xi(u→i)=0
∂∂uit+∂∂xj(uiuj)=-ρ∂∂pxi+∂∂xj[(μ+ρμt)(∂∂xuij+∂∂uxji)]+fi
由于要计算旋转转轮内的流动,在旋转坐标系下,雷诺平均N—S方程如下:
∂∂xi(wi)=0
∂∂wti+∂∂xj(wiwj)=-ρ∂∂pxi+∂∂xj [(μ+ρμt)(∂∂xwji+∂∂wxij)]+f′i
u→=w→+ω→×r→
F→′=-2ω→×w→-ω→×(ω→×r→)+f→
式中:p为压力;fi为体积力分量;ρ为水的密度;ω→为转轮旋转角速度;ui、wi分别为绝对速度和相对速度分量;μ为黏性系数;μt为湍流黏性系数。
由SSTk—ε湍流模型加以封闭。
由于是不可压缩流场计算,在RANS的求解中,采用了SIMPLEC实现速度场与压力场的耦合。
定常计算条件包括以下几方面。
(1)进口条件。采用压力进口条件,在进水段进口处,根据水轮机的水头给定相对总压力,速度方向垂直进口断面。
(2)出口条件。采用压力出口条件,在尾水管出口处,给定平均静水压力为0。(3)转轮转速。根据水轮机转速给出。
(4)壁面条件。固壁面采用无滑移边界条件。
(5)交界面。计算中采用了滑移网络模型模拟动静干扰流场,转轮部件的网格相对活动导叶和尾水管部件的网格转动,各部件的计算同时进行。交界面处保证插值后速度分量和湍流量一致;同时保证积分后压力和流动通量一致。进口段与活动导叶的交界面采用Stage类型的交界面,活动导叶与转轮的交界面、转轮和尾水管的交界面为滑移交界面。
3.8.2 离散方法
灯泡贯流式水轮机的活动导叶和转轮区域采用六面体结构网格,进口段、灯泡体段和尾水管段采用非结构化四面体同位网格,在动量方程中,扩散项采用中心差分格式,对流项采用二阶迎风格式,在速度修正方程中,压力项采用动量插值形式,以防止出现不合理的波形压力场。
取整体流道作为计算域,将计算域分为进口和灯泡体段、活动导叶段、转轮区以及尾水管段。交界面在计算过程中通过插值进行信息交换。
图328所示分别为活动导叶单流道区域的网格划分和转轮室的网格划分情况。采用结构化网格对叶片附近局部加密。

图328 灯泡贯流式水轮机的流道计算域
(a)活动导叶单流道计算域;(b)转轮室计算域
3.8.3 模型机组CFD计算结果分析
为便于与模型试验值相比较,计算模型按模型φ350mm转轮直径进行全流道三维造型,包括进水流道、固定导叶、活动导叶、
转轮和尾水管等在内的整体流道,如图3
29所示。
代入原模型机组的导叶、转轮叶片,作灯泡贯流式水轮机模型机组计算,其最大试验水头由电站给定。调节导叶开度和桨叶角度,计算水轮机不同工况的协联点。选取6个典型工况计算水轮机的能量特性,并与试验值对比分析。对比6个典型工况的计算结果和试验数据,如表312所示。

图329 灯泡贯流式水轮机模型机组流道图
表3 12
模型水轮机6个典型工况的能量特性

对比计算结果与试验值,6个工况的单位转速和单位流量的计算结果与试验值基本一致。工况1、2与试验值较吻合;计算结果2为工况3、5调整导叶角度后和工况4、6调整桨叶角度后得到协联点的数据。计算的效率较低可能是由于三维建模尺寸与模型试验的尾水管尺寸不一致引起的。
计算结果显示的流线分布和速度矢量分布合理,导叶区和转轮区流动状态良好,效率较高,说明所选的各项计算参数合理。
选取最优工况、小流量工况和大流量工况三个典型工况,对应表312中的典型工况1、工况3和工况6,对灯泡贯流式水轮机模型机组整体流道进行数值模拟分析,显示整体流道的流动状态,通过导叶和桨叶进出口的流动状态,分析导叶和桨叶的能量性能。计算结果分析如图330~图338所示。

图330 模型机组整体流道流线分布(最优工况)

图331 模型机组活动导叶不同柱面展开面流线分布(最优工况)

图332 模型机组转轮叶片不同柱面展开面流线分布(最优工况)
(1)最优工况流动显示。模型机组整体流道的相对流线分布如图330所示,最优工况下,整体流道的流动状态良好,尾水管内的流线旋转前行,出口附近形成回流,这与尾水管内部的水力损失相对较大相对应。
图331和图332,分别显示了活动导叶和转轮叶片在不同柱面展开图上的流线分布,图示span(测量间隔)的数值表示:所取柱面到轮毂的距离与轮缘到轮毂距离的比
值。因此,span=0.1和span=0.9分别代表了靠近轮毂和轮缘的位置,span=0.5表示
相对居中的位置。通过柱面展开图上的流线分布,可以看出流线均比较平顺,叶片进口冲角不大,流线分布合理。这与导叶和转轮区的水力损失情况相对应。

图333 模型机组整体流道流线分布(小流量工况)

图334 模型机组活动导叶不同柱面展开面流线分布(小流量工况)
(2)小流量工况流动显示。图333~图335,进行了小流量工况下的流动显示,整体流道的流线分布图显示出尾水管内的流线旋转前行,出口段出现明显回流,对应水力损失增大。导叶和转轮叶片区的流线图,同样验证了较为理想的流动特性。
(3)大流量工况流动显示。图336~图338,进行了大流量工况下的流动显示,尾水管内的流线光顺,转轮出口环量较小,这与转轮叶片的开度较大相关,导叶和转轮区的流动状态较好。

图335 模型机组转轮叶片不同柱面展开面流线分布(小流量工况)

图336 模型机组整体流道流线分布(大流量工况)

图337 模型机组活动导叶不同柱面展开面流线分布(大流量工况)

图338 模型机组转轮叶片不同柱面展开面流线分布(大流量工况)
典型工况的流动显示,均说明了所选用的活动导叶和转轮叶片具有良好的水力性能。
3.8.4 灯泡贯流式水轮机增容改造的计算结果
根据模型机组所选计算参数,在原流道中代入新设计的导叶、转轮叶片,结果水轮机出力达不到电站要求增容20%的要求。
为此将流道直径由φ5500mm增至φ6000mm。修改后的流道三维模型如图339所示,重新计算结果如表313所示。

图339 修改后灯泡贯流式水轮机流道三维图(单位:mm)
表3 13
灯泡贯流式水轮机流道改造后12个典型工况的能量特性

续表

在流道改造后和代入新设计的导叶、转轮叶片的灯泡式水轮机,通过计算结果表明,在额定水头Hr=4.9m(工况8)时,水轮机出力可到2.48MW,超过电站增容要求
2.258MW;最小水头Hmin=3.0m(工况3)出力可到1.23MW;最大水头Hmax=5.5m(工况12),出力可达到2.92MW,超过电站增容要求值2.58MW。
对灯泡贯流式水轮机改造流道后进行数值模拟分析,显示整体流道的流动状态。分别选取最小水头、额定水头和最大水头下的较优工况,对应表3 13中的工况2(最小水头)、工况6(额定水头)和工况10(最大水头),通过导叶和桨叶进出口的流动状态显示,分析导叶和桨叶的能量性能。流动显示如图340~图348所示。

图340 水轮机改造流道最小水头工况流线分布

图341 水轮机改造流道活动导叶不同柱面展开面流线分布(最小水头工况)

图342 水轮机改造流道转轮叶片不同柱面展开面流线分布(最小水头工况)

图343 水轮机改造流道额定水头工况流线分布

图344 水轮机改造流道活动导叶不同柱面展开面流线分布(额定水头工况)

图345 水轮机改造流道转轮叶片不同柱面展开面流线分布(额定水头工况)

图346 水轮机改造流道最大水头工况流线分布

图347 水轮机改造流道活动导叶不同柱面展开面流线分布(最大水头工况)

图348 水轮机改造流道转轮叶片不同柱面展开面流线分布(最大水头工况)
(1)最小水头工况流动显示。最小水头工况的流动显示,整体流道的相对流线分布如图340所示,整体流动状态良好,尾水管的流线分布不光顺,靠近出口段流线旋转前行。图341和图342分别显示了活动导叶和转轮叶片在不同柱面展开面上的流线分布,可以看出流动均匀,叶片进口冲角不大,流线分布合理。
(2)额定水头工况流动显示。额定水头工况的流动显示图343~图345,整体流道的流线分布于图343中,尾水管内部的流动相对不均匀,活动导叶和转轮叶片在不同柱面展开面上的流线,显示整体流态合理,导叶区和桨叶区的能量特性较好。
(3)最大水头工况流动显示。最大水头工况的流动显示图346、图347、图3 49,尾水管内部流线旋转前行,出口段附近存在回流,导叶区和桨叶区流动状态良好,叶片进口冲角不大,能量特性较好。
流动显示总体说明,改造流道后的流动状态较好,能量特性得以保证,且达到了电站要求的增容值。
3.8.5 水轮机流道改造后典型工况空化性能分析
分析流道的空化性能,需要将流道内点的绝对压力与空化压力比较,若绝对压力低于空化压力,则该区域易发生空化。一般取空化压力约为3500Pa。数值模拟计算中,可以读取流道内点的相对静压力,记为读数p,流道内点的绝对压力记为p′,p′可由p换算而得。
由于计算中考虑了重力的影响,给定边界条件时,设尾水管出口中心静压力为0,尾水管中心处的绝对压力pdt可表示为
pdt=pa+ρg*(尾水位高程-尾水管出口中心高程)
式中:pa为大气压力,取值101325Pa,尾水位高程取下游最低水位194.7m,尾水管出口
中心高程为191.27m。

图3 49(一)水轮机改造流道叶片部分低压易空化区域

图3 49(二)水轮机改造流道叶片部分低压易空化区域
流道内各点的绝对压力p′可表示为
p′=p+pdt
式中:p代表流道内点的相对静压力,通过数值模拟计算结果可以读取。由此获得流道内点的绝对压力p′,当其低于空化压力时发生空化。用流道内点的相对静压力分布图表示出可能出现空化的区域。
图349中蓝色线区域表示较低压力区。由图3 49可见,在大流量大开度工况下,
如工况4、工况8和工况12,低压易空化区域范围较大,空化性能较差,但已属于超功率的非运行工况,其他工况空化性能良好。
电站实测表明,在毛水头4.9m,机组出力2000kW,各部瓦温均低于规程要求值,空化情况良好,基本达到了用户的要求。
上述表明,用CFD技术可以揭示水轮机流道内各部分的流态状况,为优化水轮机设计提供了良好的条件。但是,CFD技术是在不同假设条件下计算分析的,这与水轮机内部真实的流动状态还是有差距的。
为便于比较,在新转轮设计或老电站改造中,尽量模拟已定的流道(包括进口、引水段、蜗壳、固定导叶、活动导叶、转轮、尾水锥管、尾水管、尾水出口),并输入已有的好转轮或原老转轮的参数,并与原模型试验特性相比较,以确定CFD公式中的各系数值,在各系数相同的条件下输入新设计转轮参数,并得到预估模拟的综合特性曲线,这样的对比可信度较高。
尽管目前已开展了水轮机能量与气蚀性能的CFD预估,但最终还是应由模型试验结果来做判断。