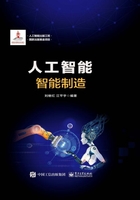
1.1 制造模式
1.1.1 产品全生命周期
制造业是指利用一定的资源(物料、能源、设备、工具、资金、技术、信息和人力等),按照市场要求,产出工业产品和生活消费产品的行业。类比人类,产品也具有生命周期,对应产品的“生”到“亡”。产品生命周期是指从产品的市场需求、设计方案等无形的产品描述到生产出实物产品,再到产品的使用,最终报废回收的整个周期,以汽车为例,其生命周期如图1-1所示。

图1-1 产品生命周期
尽管产品生命周期的阶段划分因产品而异,但一般可以分为产品规划、产品设计(概念设计、详细设计)、产品生产(工艺设计、生产加工)、产品销售、产品使用和维护(产品使用、维护服务)、报废回收6个阶段。
① 产品规划阶段通过分析市场或用户的需求,制订新产品开发计划或者已有产品的更新换代计划,确定产品的主要技术特征。
② 产品设计阶段又可以细分为概念设计和详细设计两个阶段,根据对应市场需求的技术要求和约束条件,完成产品技术方案由粗到细、由抽象到具体、由总体到局部的逐步完善,开展设计方案评价,确定产品的各类信息,产生设计模型或文档。简而言之,该阶段是将新思想、新构思转变为新产品原型或样品的过程。
③ 产品生产阶段则根据产品的设计结果,统筹安排各种制造资源,从而实现由原材料到产品实物的转变。这是将无形的产品描述转变成实物产品的阶段。
④ 产品销售阶段则完成产品的买卖和运送等。
⑤ 产品使用和维护阶段指产品在最终用户处发挥其功能作用,包括产品使用和维护服务等内容。
⑥ 报废回收阶段包括两方面的工作:一是作为产品个体生命周期的终点,报废已无法正常发挥作用(失去使用价值)的产品或产品的零部件;二是作为新个体的组成部分加以回收,使其回到产品生产阶段,实现再利用。
事实上,产品生命周期阶段的划分也与制造企业的组织划分有密切关系。例如,制造企业有设计部门、生产部门、销售部门、服务部门及管理部门。各部门各自完成相应的业务活动,同时相互衔接协同工作,促进产品全生命周期的开展。另外,所谓的制造模式,可以针对产品生命周期的某个环节(阶段)来考虑,也可以针对产品全生命周期来考虑。
1.1.2 制造模式的发展
制造模式可以理解为基于某种思想和技术的制造企业的制造业务组织与实施方式。制造模式可以具体体现在制造战略上,也可以对应具体的制造系统。从人类创造工具、改造自然开始,可以说就有了相应的制造模式,即使在制造业(或工业)形成之前,个体手工劳动也具有一定的制造模式,也就是手工作坊单件生产的制造模式。制造模式更多是指在工业革命之后所形成的生产组织方式。200多年来的工业发展见证了诸多制造模式的形成与变迁。推动或牵引制造模式发展的因素包括社会发展、科技进步。
制造模式可以根据生产产品种类和批量加以分类。18世纪中叶到19世纪中叶,蒸汽机和制造设备的发明促进了手工作坊单件生产的制造模式向机械化的生产模式(单件小批量)转换。19世纪中叶到20世纪前期的电力电气技术的发展则进一步促进了大规模(少品种大批量)自动化生产制造模式的实现,促进了社会大生产。社会经济的发展和市场需求的多样化,结合诞生在20世纪40年代的计算机技术等信息技术的发展,催生了数控加工技术、计算机辅助设计技术等制造技术,使得制造模式进入了由信息技术驱动的所谓的先进制造模式时代——多品种小批量生产。针对不同的实际需求,涌现出了众多各具特色的制造模式和制造系统。当然,由于产品不同,实际上某种变型的大规模生产方式,如大规模定制生产制造模式与个性化定制生产制造模式存在于不同的制造行业。汽车、工程机械、家电、工业控制器、电子产品等采用大规模定制生产制造模式,而燃气轮机、海洋装备、航天器等则采用个性化定制生产制造模式。
先进制造模式是根据适用的产品生命周期阶段和技术内涵予以分类的[1]。自20世纪40年代以来,信息技术一直处于高速发展时期。20世纪80年代到90年代直至当今时代,先进制造模式可谓层出不穷。无论什么样的先进制造模式,客观而言,最终都是要让制造企业能够实现缩短周期、降低成本、提高质量、提高企业和产品竞争力的目的。典型的先进制造模式包括柔性制造、计算机集成制造、并行工程、精益生产、敏捷制造、智能制造、虚拟制造、网络化制造等。本节简单介绍其中的计算机集成制造、并行工程、精益生产和智能制造。
(1)计算机集成制造[2]。计算机集成制造概念最早由美国Joseph Harrington博士于1973年提出,认为从系统论角度出发,企业的各种生产经营活动之间是不可分割的,需要统筹考虑;从信息论角度出发,整个生产制造过程实质上是信息的采集、传递和加工处理的过程。美国制造工程师学会计算机与自动化系统协会(SME/CASA)于1985年提出计算机集成制造系统论图,认为计算机集成制造融合了新的管理理念,使其业务信息系统能够无缝集成整个制造企业的业务,为推动计算机集成制造模式的推广,设立了企业领先奖和大学领先奖。中国从国家863计划开初就设立了计算机集成制造主题,开展计算机集成制造系统应用示范工程,按照信息集成、过程集成、企业集成的阶段不断深化。计算机集成制造模式关注企业研发设计、生产制造和经营管理全业务,在单元信息系统,例如计算机辅助设计、计算机辅助工艺设计、计算机辅助制造系统的基础上,通过产品数据管理、制造执行管理和企业资源管理平台实现信息系统集成,实现企业信息化。实际上,计算机集成制造模式是当今智能制造模式的基础。
(2)并行工程。并行工程是在20世纪80年代中期,针对传统的产品研发制造串行模式存在的弊端提出的先进制造模式。它重点关注产品研发与制造的并行集成,强化产品研发环节信息的及早下发和产品制造环节评价的及早反馈,甚至达到两个环节的同步进行。并行工程的三大支柱是流程、技术和团队:流程再造实现了研发设计与制造等下游环节的更好、更有效的集成;面向产品生命周期的设计技术(Design for X)支持将下游信息反馈给设计环节,使下游环节中可能出现的问题在设计阶段及时被发现并得以解决,最大限度地减少设计反复;团队则是要求组织进行变革,采用多学科工作组的形式实现各组间的有效协同工作。
(3)精益生产。丰田生产模式即精益生产模式,于20世纪70年代盛行于日本,并最早在日本制造企业中被广泛采用。这一生产模式主要以生产环节为对象,瞄准买方市场,实现拉动式生产。精益生产模式将销售(买方市场)的需求作为生产起点,自后向前拉动整个生产环节,消除无效劳动、多余库存和浪费。技术方面主要包括准时制作业、全面质量管理、成组技术等。
(4)智能制造。Paul K.Wright等人于1988年提出制造智能(Manufacturing Intelligence)的概念,希望综合运用知识工程、软件、机器人等人工智能技术,实现经验技能知识的表达应用和智能机器人的应用[3]。事实上,此时,专家系统已经应用于计算机的设计,而定性推理技术已经尝试用于电路、机械机构、大型设备的设计和诊断中。智能制造(Intelligent Manufacturing,IM)概念于1989年由时任日本东京大学校长的吉川弘之(也是一般设计理论的提出者)首次提出。1995年4月,由日本倡导发起的、多国参与产业引领的、为期10年的国际智能制造系统(Intelligent Manufacturing System,IMS)联合计划正式启动。该计划关注生产活动全球化、地球环境问题、生产知识继承、消费者需求等方面的制造业环境的变化,致力于有机融合贯穿从订货、研发设计、生产制造到市场销售全制造过程的智能活动和智能机器,提升生产力。该联合计划的提出恰逢人工智能第二个高潮(知识工程),学术界和产业界充分意识到人工智能技术成果可能对制造模式和制造技术的影响。因此,智能制造实际上是要通过模拟人类专家的制造智能行为,替代或延伸制造环境中的部分脑力劳动,实现制造运行的智能化。智能制造技术是人工智能技术与制造技术的融合。其研究方向包括未来制造系统(敏捷制造、分形工厂、生物制造、全企业集成等)、制造信息处理智能通信网络、绿色制造、快速原型制造、无人化制造系统、开放分布式制造系统、扩展企业、虚拟企业、企业技术知识管理等。2003年度的10个主要技术领域包括可持续设计产品及过程、可持续职场设计、数字化制造的基于知识的价值创造、智能组织、动态协同价值创造网络、扩展企业、移动泛在电子商务、虚拟工程与数字化工厂、数字化定制制造、纳米技术与生物技术。