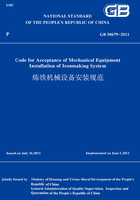
6.2 Welding
6.2.1 The welders and welding shall be in accordance with the following requirements:
1 The welders shall weld in accordance with the provisions of welding method statement or welding instructions.
2 The welders who have once local repair and have failure rates of more than 20% shall stop welding.
3 Each welding seam welded by the welder shall be marked and a welding record chart shall be filled in.The record chart shall comprise weather,date,conditions of joint,welding material,preheating temperature,welding position and other contents.
6.2.2 Welding equipment shall be in accordance with the following requirements:
1 Heating,temperature measurement and temperature control performances of baking and heat preservation equipment shall meet the requirements of application and quality of products.
2 Manual electric arc welding machine,electro-slag welding machine,submerged arc welding machine and other welding equipment shall be placed in a rain-proof and snow-proof electric welding machine room,in which ground wires shall be unified to lay and connected in a right manner.The shell of the equipment shall be grounded reliably.The welding machines and the cable should be subject to unified code.
3 A carbon dioxide cylinder for carbon dioxide arc welding shall be equipped with a preheating dryer.
4 The welding equipment and the baking and heat preservation equipment shall be checked regularly and their voltage and current shall be stable and normal.The welding equipment and the baking and heat preservation equipment shall go out of service and be repaired in case of discovering abnormal conditions.
5 The breakage of the cable for welding equipment shall be subject to insulation protection.
6.2.3 The management of welding materials shall be in accordance with the following requirements:
1 The welding materials shall be free of rust,deterioration,coating shedding,cracks and contaminations.
2 The welding materials shall be baked in compliance with the following requirements.
1)Managers shall bake the welding materials according to variety,specifications and quantities as required of welding electrodes,welding wires,welding flux,consumable nozzle and flux-cored wire and other welding materials as required for welding,as well as the provisions of product manual and relevant process documents.
2)The welding electrodes to be baked shall be put into a high temperature oven according to their variety and specifications and be heated up to specified temperature and time step by step.Low hydrogen type welding electrode shall be baked at a temperature of 350℃-380℃,be kept warm for 1h to 2h after reaching the temperature,and then be cooled to at a temperature of 100℃-150℃,and be placed into a constant temperature tank for storage.The welding electrodes shall be baked again when the storage temperature is lower than 100℃.
3)The baked low hydrogen type welding electrode shall be baked again if it is placed in air for more than 4h and it should not be baked above twice.
4)The acid welding electrode shall be baked according to its damped condition.In case it is required to be baked,its baking temperature shall be at 150℃to 200℃for 1 h to 2 h at a constant temperature.The acid welding electrode may not be baked any more if its storage time at a constant temperature is short and its packaging is in a good condition.
5)The welding flux may be recycled to bake again but it shall not be baked more than twice.
3 During drying,the welding materials must not be baked in bulk or in bundle and they shall be baked in a layered manner.In addition,1 layer to 3 layers of welding materials should be better.
4 The welding materials shall be issued according to the variety,specification,trade mark and quantities of the welding electrodes as stipulated by the welding position.In addition,the welding position,issued variety,specifications,trade mark,quantities,issuing time and receivers shall be kept a record.
5 The welder shall be equipped with the constant temperature tank for welding electrodes and take it along with himself.The issuing quantities of the welding electrodes shall be determined according to the volume of the constant temperature tank.During welding,the welding electrode shall not be placed on the ground or in the damp place.The welding electrodes received shall be exhausted on the same day.If there are welding electrodes remained,they shall be returned to the drying room on the same day and be stored in the baking oven at a constant temperature rather than in the open air.The welding electrodes with coating shedding or rusted core wire and rusted welding wires must not be used.
6 The selection of the welding materials shall meet the requirements of the design document.In case the design is not specified,the welding materials selected on the installation site shall be selected according to appendix A of this standard and comply with the following requirements:
1)The appropriate welding materials shall be selected according to chemical composition of base metal,mechanics and welding performance and in combination with form of welding seam joint,welding method and working conditions,etc.,and shall be determined by process test whenever necessary.
2)The welding materials special for steel plates of blast furnace shell shall be adopted according to the provisions of appendix A of this standard.
3)Low alloy steel should adopt the low hydrogen type welding electrode.
6.2.4 Welding conditions shall be in accordance with the following requirements:
1 When the ambient temperature of the welding region is lower than 0℃,the base metal with the thickness of double to three times of that of the steel plate in all directions of member welding region as well as within the range of no less than 100mm shall be heated up to above 20°C for welding.
2 Welding shall not be done when the relative humidity of the operating region is larger than 90%.
3 When the wind speed of manual arc welding installation site is larger than 8m/s and that of gas shielded welding and flux-cored wire arc welding installation site is larger than 2m/s,a windproof shed shall be provided and other windproof technical measures shall be taken.For the welding region in the fabrication plant,a wind shield shall also be provided if there is cross ventilation or air blast of a blower.Specific windproof plan shall be formulated by construction contractor and be put into effect till it has reported to and approved by supervision unit.
4 Heating and dehumidified measures shall be taken when the surface of the welding element is damp or snow-covered.
5 Weather,temperature,humidity and wind speed,etc.shall be made a record during welding.
6.2.5 The shell welding of process steel structure shall be in accordance with the following requirements:
1 Plant fabrication may adopt manual arc welding and gas shielded welding.The splicing of butt weld should adopt automatic submerged arc welding.
2 Installation site welding may adopt manual arc welding,gas shielded welding,electro-slag welding,self shielded welding,automatic submerged arc welding and electrogas welding,etc..
6.2.6 Welding procedure qualification shall comprise the following contents:
1 Type of steel used for the first time,type of welding material or changed welding material,welding method and weld heat treatment process.
2 Type of steel,welding material,welding method,joint type,welding position,post-weld heat treatment process as specified by design,as well as combination of welding procedure parameter and various parameters of preheating measure as adopted by the construction contractor.
3 Welding through electro-slag welding or electrogas welding.
6.2.7 Test pieces for welding procedure qualification must be submitted to statutory testing organizations with nationally approved test qualification for test detection,and welding operation shall be made till the detection is qualified.
6.2.8 Welding procedure instructionsor welding plan and process card shall comprise the following contents:
1 Welding method.
2 Trade mark,thickness and other relevant dimensions of base metal.
3 Type and specification of welding material.
4 Type of welded joint,shape of joint and allowable deviation of dimension.
5 Requirements of clamp,positioned welding and liner.
6 Welding current,welding voltage,weld heat input,welding sequence,welding speed,welding level,back chipping requirement and other welding procedure parameters.
7 Range of preheating temperature and interpass temperature.
8 Post-heating and post-welding stress relieving treatment process.
9 Test method and acceptable quality level.
6.2.9 Welding procedure qualification of shells of blast furnace,hot-blast stove and smelting reduction ironmaking furnace,as well as column and beams of frame structure shall meet the relevant requirements of the design document as well as the current national standard JB 4708 Welding Procedure Qualification for Steel Pressure Vessels or GB 50372 Code for Installation Acceptance of Metallurgical Machinery Ironmaking Equipment Engineering.
6.2.10 Before formally welding the blast furnace,hot-blast stove and smelting reduction ironmaking furnace,the welding equipment and its affiliated devices shall be conducted adjustment and commissioning,the welders and welding equipment shall take simulation test and meet the requirements of welding procedure.
6.2.11 Welding procedure shall be in accordance with the following requirements:
1 The type and dimension of the joint shall meet the relevant requirements of the design document as well as current national standards GB/T 985.1 Recommended Joint Preparation for Gas Welding,Manual Metal Arc Welding,Gas-shield Arc Welding and High Energy Beam Welding,GB/T 985.2 Recommended Joint Preparation for Submerged Arc Welding or JGJ 81 Technical Specification for Welding of Steel Structure of Building.Rust,oil,ponding,snows and other contaminations shall be eliminated within the range of 10mm-20mm of both sides of joint of manual arc welding seam,self shielded welding and submerged arc welds as well as within the range of 40mm-50mm of both sides of joint of electro-slag welding and automatic vertical welding seam.
2 The type and dimension of the joint of electro-slag welding and electrogas welding should be in accordance with those specified in Figure 6.2.11.
3 The butt welds of uptake duct,downcomer,T-branch pipe and other large-diameter coil-welded steel pipe as well as steel plates in longitudinal and transverse directions of dust removal shell shall adopt T-shaped intersection with a space of not less than 200mm.The steel plate of five-way ball equatorial zone should not be spliced.The butt welds of the equatorial zone and the upper and lower polar zones shall adopt T-shaped intersection with a space of not less than 100mm.

Figure.6.2.11 Type and dimension of joint of electro-slag welding and electrogas welding seam
4 After assembling the members,the shape,position,interface gas and alignment tolerance of joint of the assembled members shall be checked.The surface of the joint shall be free of cracks,interlayer,slag inclusion and other defects.The assembled gap of the joint shall be larger than 4mm and surfacing at one side or both sides of the joint shall be made.The alignment tolerance of more than 4mm shall be marked and gentle transition shall be done in the course of welding.
5 Positioned welding shall be welded by the welder in compliance with the provisions of Article 6.1.6 of this standard.The welding materials for positioned welding and welding quality shall be the same as those for formal welding.The length and space of positioned welding shall be determined according to the thickness,structural style and restraint intensity of the base metal.The thickness of thewelding seam should not exceed 2/3 of that of the designed weld.The positioned welding of the blast furnace shell shall be conducted at one side of the shallow joint.Its length shall be 200mm-500mm and its space shall be less than 1000mm.The positioned welding of the blast furnace shell should be conducted by many people symmetrically and simultaneously.The preheating temperature for positioned welding shall not be lower than that for formal welding.
6 Interpass temperature shall be controlled for welding the thick steel plate and must not be lower than the preheating temperature.In addition,welding shall be continuous.
7 The contact part in the need of planning flatly and supporting tightly shall not be welded until it has been approved by quality control division.
8 During assembling,workpiece to be welded shall be fixed reliably.
9 Before welding,the assembling quality,the positioned welding quality and cleaning condition of welding part shall be reviewed and meet the relevant requirements of current professional standard of the nation JGJ 81 Technical Specification for Welding of Steel Structure of Building.
10 Fire and arc must not be struck on the base metal excepting welding seam.A run-on plate and a run-off plate shall be arranged on both ends of the main welding seam of T-shaped joint,cross-shaped joint,fillet joint and butt joint.The material,welding procedure parameter and type of joint shall be the same as those of the welded piece.The other materials must not be used as the run-on plate and the run-off plate.The ground wire,the cable and electrode holder shall not be subject to arc striking with the welding element.Crater in electric arc abrasion part of the welding element shall be polished in smooth transition.The polished depth shall not be larger than 5% of the thickness of the welding element or 2mm.
11 The dimension of the run-on plate and the run-off plate and the run-off length of the welding seam shall meet the requirements of Table 6.2.11.
Table 6.2.11 Dimension of run-on plate and run-off plate and run-off length of welding seam(mm)

12 The multilayer welding shall be in accordance with the following requirements:
1)The joint of the thick steel plate shall be welded in a multilayer and multi-weld beads welding method with.The multilayer and multi-weld beads welded joint should be staggered more than 50mm.During manual welding with multilayer and multi-weld beads,subsection,layering,backward and reverse,and balanced welding methods shall be adopted.
2)Multilayer welding for thick steel plate shall be continuous.Welding slag and surface splash shall be cleared timely after the welding of each weld bead is completed.In case of discovering defects affecting welding quality,the welding shall be done after the defects are removed.
3)The temperature of the base metal of the welding zone shall be controlled in the continuous welding method.In case of breaking off welding,appropriate heat preservation measures shall be taken,and another preheating temperature shall not be lower than the specified one when rewelding.
4)When the weld bead at the bottom layer of the joint adopts manual arc welding,the welding electrode with diameter of no larger than 4mm should be used for welding,the minimum dimension of the weld bead at the root of the bottom layer shall be appropriate,and the maximum thickness should not exceed 6mm.
13 Box column and beam of frame shall be welded after general assembly.The welding seam between internal partition and wing plate and between internal partition and web shall be welded firstly,and then 4 main welding seams between the wing plate and the web shall be welded.4 main welding seams should be subject to manual arc welding or carbon dioxide arc welding,extending in the same direction from the middle to two ends respectively,and performing back-step welding and balanced welding.
14 For the furnace shell,inside welding seam and outside welding seam shall be welded in sequence.Vertical welding seam of each ring shall be firstly welded and then transverse welding seam shall be welded.A circle shall be uniformly distributed by many welders.Symmetric and reverse welding method,multilayer and multi-weld beads welding method and back-step welding method shall be used for welding.
15 The bottom plate of the furnace should be welded by extending from the centre of circle to circumference.The transverse welding seam shall be welded by many welders from the middle to the two ends in back-step skip sequence welding method,symmetric and reverse welding method and multilayer and multi-weld beads welding method.The bottom plate and ring plate of furnace shall be uniformly distributed by several welders in a circle manner and welded by symmetric and reverse welding method,multilayer and multi-weld beads welding method and back-step welding method.The bottom plate and the ring plate should be welded in sequence.
16 The butt weld of the box column of the frame at the lower part of the blast furnace and the smelting reduction ironmaking furnace should be welded from inside to outside in a symmetric manner.
17 Manhole temporarily opened on the blast furnace shell shall be recovered and welded for closing.The flange stub pipe on the blast furnace shell should be welded symmetrically.The long welding seam shall be subject back-step welding or skip sequence welding.
18 The opening of the shell member shall be welded with the pipe or the stub pipe by low hydrogen type welding electrode with the same or similar composition and performance of the body material.
6.2.12 Preheating for welding,post-heating and stress relieving treatment shall be in accordance with the following requirements:
1 Preheating temperature for welding shall be comprehensively determined according to the type and dimension of the joint of the welded joint,type of steel,thickness of steel plate,restraining condition of member,content of diffusible hydrogen of deposited metal,weld heat input,thermal conduction condition of joint,ambient temperature and other factors or by procedure qualification.The preheating temperature of carbon structural steel with manual arc welding plate of thicker than 50mm and low alloy structural steel with plate of thicker than 36mm should be at 100℃-150℃.The preheating temperature of the steel special for the blast furnace shell shall be determined by procedure qualification.
2 Preheating for welding should be accompanied with an electric heater.But under exceptional circumstances,gas,propane and other gas flames may be adopted for uniformly preheating.Preheating shall be implemented at the back of the welding part.Preheating zones shall be arranged at both sides of the welding joint.Its thickness at each side shall be double to three times of that of the welding part of the welding element and shall not be less than 100mm.The preheating temperature should be measured at the back of the preheating part.Temperature measuring points shall be 50mm to both sides of the weld bead.The temperature may be measured by a temperature chalk or far infrared thermometer and other thermometers.When a fired heater is used for preheating,temperature measurement at the front shall be conducted after stopping heating.
3 Preheating requirements for accessories on furnace shell,temporary tool and clamp before welding shall be in accordance with those specified in Item 1 and Item 2 of Article 6.2.12 of this standard.
4 The preheating temperature shall be selected according to the thermal conduction condition of the joint.In addition,T-shaped joint shall be 25℃-50℃higher than the preheating temperature of the butt joint.
5 The low alloy structural steel with manual arc welding plate of thicker than 36mm,the carbon structural steel with plate of thicker than 50mm and the blast furnace shell with plate of thicker than 50mm shall be subject to post-heating treatment after welding.The post-heating treatment may be conducted by electrical heating equipment.The post-heating treatment temperature shall be at 200℃-350℃.The holding time shall be determined according to the plate thickness of the workpiece and shall not be less than 0.5h per 25mm of plate thickness.The total holding time shall not be less than 1h.After the holding time is reached,slow cooling shall be performed to normal temperature.
6 The stress relieving treatment after welding high temperature section of the hot-blast stove shall meet the requirements of the design document.The stress relieving treatment shall be conducted after nondestructive testing is up to standard and all holes,lifting lugs,clamps and other accessories are welded.For local stress relieving treatment of the welding seam welded on the installation site,the stress may be relieved by thermal treatment and other effective methods.Thermal treatment shall meet the relevant requirements of the current national standards JB/T 6046 Welding assembly for carbon steel and low alloy steel Post-welding heat treatment method and JB/T 4709 Welding Specification for Steel Pressure Vessels.The shell after thermal treatment must not be welded and cut once again.
7 When the tuyere section of the blast furnace is manufactured in a blocking way according to circumference,the assembled and welded tuyere flange or tuyere shall be subject to the stress relieving treatment respectively and meet the requirements of the design document.The stress may be relieved by thermal treatment and other effective methods when there is no requirement in the design document.The thermal treatment shall be in accordance with those specified in Item 6 of this article.The tuyere section of the blast furnace shall be divided into a number of assembly parts and be subject to grouping and butt weld after being transported to the installation site.The butt weld may be welded by electro-slag welding method and manual arc welding method and may not be subject to stress relieving treatment after welding.
8 The vertical butt weld of the smelting reduction ironmaking furnace shall adopt thermal treatment and other effective methods for stress relieving.The thermal treatment shall be in accordance with those specified in Item 6 of this article.
6.2.13 The repair for surface defects of welding seam shall be in accordance with the following requirements:
1 Air hole,slag inclusion,weld flash,excess weld metal and other defects shall be removed by polishing of grinding wheel,spading and chiseling,and be subject to repair welding.
2 Undersize of welding seam,undercut,unfilled crater and other defects shall be subject to repair welding.
6.2.14 The repair for internal defects of welding seam shall be in accordance with the following requirements:
1 Defects shall be removed by polishing of grinding wheel or carbon arc gouging according to the location determined by nondestructive testing and depth of defects.
2 In case the defect is crack,the cause shall be made sure and the welding technician shall formulate a repair plan to treat it.
3 Before carbon arc gouging,holes shall be drilled at both ends of the crack,and the crack as well as the welding seam and the base metal respectively 50mm to its both ends shall be eliminated.
4 During removal of defects,gouging slot shall be machined as a joint with chamfered angles at four sides of larger than 10°,the surface shall be trimmed,and gouging carburized layer shall be grounded.In addition,penetration testing or magnetic particle testing method shall be used for determining whether removing thoroughly whenever necessary.
5 Arc strike in joint shall be performed for repair welding and the crater shall be filled when quenching of arc.Multilayer welding layers shall be staggered.The length of the welding seam shall not be less than 100mm.When the length of the weld exceeds 500mm,the back-step welding method shall be adopted.
6 Repaired part shall be welded continuously.Post-heating and heat preservation shall be conducted in case the welding is interrupted.The appearance shall be checked when welding again.Whenever necessary,magnetic particle or penetration testing method may be used for inspection,and welding shall be continued after confirming there is no crack.
7 Preheating temperature for repair welding shall be 10℃-20℃higher than that of normal welding in the same conditions.
8 Repair welding should be welded by ultra-low hydrogen welding electrode.Whenever necessary,post-heating treatment shall be taken.
9 The positive and negative sides of the welding seam are one part respectively.The same part should not be repaired more than twice.Another repair plan shall be formulated for the part that is not still qualified after repairing twice and may not be implemented until it has been accepted by the project leader and approved by supervision engineer.
6.2.15 Carbon arc air gouging shall be in accordance with the following requirements:
1 Carbon arc gouging planer shall be allowed to work after passing training.
2 In case of"carbon inclusion",re-gouging shall be performed at 5mm-10mm of its edges.The gouging depth shall be 2mm-3mm larger than"carbon inclusion"depth.The grinding wheel may be used for polishing in case of"bonding slag".
3 For low-alloy high-strength steel and steel special for blast furnace,the surface of the gouging slot shall be polished by the grinding wheel,and hardening layer shall be removed to weld.
6.2.16 Welding testing shall be in accordance with the following requirements:
1 Welding checker and nondestructive testing personnel shall be responsible for welding testing.The checker shall take complete inspection and supervision according to the current national standard GB 50372 Code for Installation Acceptance of Metallurgical Machinery Ironmaking Equipment Engineering,the design document and instructions for welding procedure.
2 The executive condition of the welding procedure shall be checked in the welding process and bias shall be corrected timely in case of discovering it.
3 All welding seams shall be cooled to ambient temperature and then taken appearance testing.For the welds of steel with yield strength of larger than or equal to 235MPa and less than 420MPa,inspection result after completing welding for 24h shall be taken as basis of inspection and acceptance.For the welds of steel with yield strength of larger than 420MPa,inspection result after completing welding for 48h shall be taken as basis of inspection and acceptance.
4 The shape of joint and polishing degree of finish shall be checked.In case of discovering cracks,they shall be treated and made a record well.
5 Visual inspection should be used for appearance testing of the welding seams.5-time magnifier shall be accompanied for inspection of the cracks under appropriate lights.Whenever necessary,magnetic particle testing or penetration testing shall be used.Magnetic particle testing method and quality assessment shall meet the requirements of the current national standard JB/T 6061Non-destructive Testing-Magnetic Particle Testing of Welds.Penetration testing method and quality assessment shall meet the relevant requirements of the current national standard JB/T 6062 Non-destructive testing-Penetrant testing of welds.When there are cracks in the welds through appearance testing,the same kind of welds in batch shall be checked totally.The appearance dimension of the welds shall be measured by measuring tool and caliper gauge,etc..
6 After the internal quality of the butt weld of the large-diameter coil-welded steel pipe passes through ultrasonic testing,kerosene leakage test may not be conducted any more.The kerosene leakage test should be conducted when adopting multilayer and multi-weld beads welding method.The leakage test shall comprise the following steps of cleaning up and coating with white powder slurry on one side of the welding seal capable of being checked,drying it,and coating with kerosene on the other side of the welding seam to fully soak the surface for 30min,and checking there is oil stain on the surface coated with while powder.As a result,the quality is qualified.After testing,the weld shall be repaired if the kerosene leakage phenomenon occurs.
7 When welding the fillet welds between the lifting lug for lifting the blast furnace shell is welded and the furnace shell,magnetic particle testing or penetration testing shall be taken and there shall be no cracks.
8 Ultrasonic testing part for internal quality of welding seam shall be in accordance with the following requirements:
1)T-shaped weld of joint.
2)Alternation part of cross section and intersection of pipes.
3)Part where there is objection during appearance testing or one appointed by testing personnel.
6.2.17 The quality of butt weld of process steel structure,such as frame and truss of blast furnace and melting reduction ironmaking furnace shall meet the requirements of the design document.The internal quality of butt weld shall meet the requirements of the current national standard GB 11345 Method for Manual Ultrasonic Testing and Classification of Testing Results for Ferritic Steel Welds related to ClassⅢor above of Category B when there is no requirement in the design document.The appearance quality shall meet the requirements of the current national standard GB 50205 Code for Acceptance of Construction Quality of Steel Structures related to Class B.
6.2.18 The internal quality of butt welds of process steel structure,including blast furnace,hot-blast stove,five-way ball and smelting reduction ironmaking blast furnace shell shall meet the requirements of the design document.The internal quality of butt weld shall meet the requirements of the current national standard GB 11345 Method for Manual Ultrasonic Testing and Classification of Testing Results for Ferritic Steel Welds related to ClassⅡof Category B when there is no requirement in the design document.The appearance quality shall meet the relevant requirements of the current national standard GB 50372 Code for Installation Acceptance of Metallurgical Machinery Ironmaking Equipment Engineering.
6.2.19 The internal quality of the other shell and the T-shaped butt-fillet composite welding seam shall meet the requirements of the current national standard GB 11345 Method for Manual Ultrasonic Testing and Classification of Testing Results for Ferritic Steel Welds related to ClassⅢof Category B.The appearance quality shall meet the relevant requirements of the current national standard GB 50372 Code for Installation Acceptance of Metallurgical Machinery Ironmaking Equipment Engineering.
6.2.20 The internal quality of the butt weld of the water cooling pipe at the furnace bottom shall meet the requirements of the design document.The internal quality of butt weld shall meet the requirements of the current national standard GB 3323 Radiographic Examination of Fusion Welded Joints in Metallic Materials related to ClassⅡof Category B when there is no requirement in the design document.The appearance quality shall meet the relevant requirements of the current national standard GB 50236 Code for Construction of Field Equipment,Industrial Pipe Welding Engineering related to ClassⅡof quality grading standard of welding seam.
6.2.21 The quality of the butt weld of the large-diameter coil-welded steel pipe shall meet the requirements of the design document.The internal quality of butt weld shall meet the requirements of the current national standard GB 3323 Radiographic Examination of Fusion Welded Joints in Metallic Materials related to ClassⅢof Category B when there is no requirement in the design document.The appearance quality shall meet the relevant requirements of the current national standard GB 50236 Code for Construction of Field Equipment,Industrial Pipe Welding Engineering related to ClassⅢof quality grading standard of welding seam.
6.2.22 The quality of welding seams of the large-diameter coil-welded steel pipe and the stub pipe flange of the cooling equipment for furnace body shall meet the requirements of the design document.The kerosene leakage testing should be taken when there is no requirement in the design document,and there shall be no leakage.The appearance quality shall meet the requirements of the current national standard GB 50236 Code for Construction of Field Equipment,Industrial Pipe Welding Engineering related to ClassⅢof quality grading standard of weld.