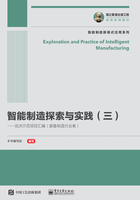
02 顶驱装置智能制造试点示范
——北京石油机械有限公司
一、项目实施背景与状况
(一)项目实施背景
石油装备制造属于典型的离散型制造,其产品生产具有单件小批量、多品种等典型特点。随着智能控制技术的不断发展和日趋成熟,石油装备的自动化发展进程成功进入智能控制的崭新阶段。“十三五”新时期的到来、制造强国战略的实施和“一带一路”倡议的推进,将加快智能制造、绿色制造、服务型制造的发展,提升制造业的层次和核心竞争力。与此同时,美国页岩气革命对国际天然气市场及世界能源格局产生重大影响,世界主要资源国都加大了页岩气勘探开发力度。尤其是近年来,我国天然气对外依存度快速攀升,页岩气进入我国国家能源战略视野。
顶部驱动钻井装置(简称“顶驱”)作为近代钻井装备的革命性成果之一,实现了钻机自动化过程的阶段性跨越,代表着 21 世纪石油钻井领域重大技术装备的最高水平和发展方向。针对页岩气开采的地质特点,结合顶驱的技术优势,开发页岩气专用智能顶驱,成为行业发展和企业生存趋势所向。北京石油机械有限公司智能顶驱产业化项目拥有一套具有自主特色的顶驱智能制造新模式,通过开发页岩气专用智能顶驱,不仅能够为页岩气低成本规模化开采提供装备和技术,更有助于企业占领科技制高点,引领和推动行业发展。
(二)项目实施的主要思路和目标
北京石油机械有限公司(简称“北石”)是中石油高端石油钻采技术装备研发、制造和服务的重点企业,是中石油唯一在京的钻采技术装备研发、制造水平展示基地,肩负着为我国石油工业提供高、精、尖石油钻采装备的重任。企业基于十余年的顶驱装置研发、制造及产业化经验,围绕页岩气顶驱产品从立项、数字化设计、关键件制造到试验装配全过程的智能化协同制造,借助信息化的高效研发手段,以及核心智能制造装备特别是数控设备、产品试验台、智能物流系统等一系列设备应用及技术手段,提升最新一代页岩气专用智能顶驱生命周期内各环节的智能产业化程度,实现产品研制周期缩短 30%~40%,有效控制产品不良率,能量回收率最高可达 89%,运营成本降低 20%以上。
二、项目主要实施内容
(一)项目实施的主要内容
北石新区智能工厂规划以“智能制造、智能管理、智能决策”为核心,以面向“无人化”的智能装备及物流装备为基础,改变原来离散制造业相对固化的生产线及生产体系,使企业在营销、设计、研发、工艺、制造、仓储、服务全环节更加紧密、柔性和智能,着力打造数字化的聚合平台(见图 2-1)。
(1)基于 BIM/PIM 技术的智能工厂建设,实现工厂总体建设技术手段的创新,对工厂的设施设备实施全生命周期管理,为智能工厂的可视化运营管理搭建基础信息模型平台。
(2)以 PDM、ANSYS 为核心,结合 PDM/3D/2D/CAPP/CAE/ANSYS 的集成与协同,搭建研发设计平台,助推企业智能产品科技创新。
(3)以 MES 和 DNC 系统为核心,结合先进的数控加工设备、检验试验手段,以及 PDM/CAM/UG/设备管理系统的集成应用,打造智能化生产制造平台,提升智能产品的加工精度和生产效率。
图 2-1 智能工厂建设总体架构
(4)以远程监控系统为核心,结合备件系统、产品全生命周期管理系统搭建智能化服务平台,全面提高服务质量,加快服务响应速度。
(5)以 ERP 为核心,结合 OA/AM/QM/HSE 技术文件管理系统的集成,以及 BYOD(Bring Your Own Device)应用模式,打造智能化管理平台,提升过程管控能力和数据分析能力,为领导决策提供快速和可靠的依据。
(6)通过 ERP 与 PDM 集成、ERP 与 OA 集成、ERP 与 WMS 集成、ERP/OA与 AM 集成等多系统综合集成,打通数据和业务流通环节,提升智能产品全生命周期信息化管控效率。
(二)采取的主要措施
1.应用 PIM 解决方案对智能制造车间整体工艺流程及布局模型进行仿真
项目采用了基于 BIM(Building Information Modeling)技术并结合工厂工程建设项目特点的贯穿于整个工厂工程建设项目生命周期的 PIM(PlantInformation Modeling)解决方案,实施内容包括项目建模及设计验证、管线综合深化设计、施工安装优化模型设计、竣工模型设计、现场技术服务及技术培训。在项目实施过程中,组建专业 PIM 设计团队,建立全过程 2D、3D信息同步及协同设计流程,并制定了 PIM 设计质量管理制度、施工阶段信息同步机制、竣工阶段信息核对机制等一系列保障措施。
2.通过数字化设计技术及产品数据管理系统对产品设计研发过程进行管理
页岩气顶驱的产业化依托北石 PDM 数据管理平台,进行产品生命周期前端需求分析及研发设计环节中的数字化设计建模、仿真验证及数据管理。该平台以标准产品库、标准工艺体系库为基础,支持设计人员在三维 CAD环境中将抽象的产品设计方案快速可视化和产品模型快速编辑,由 CAE 软件承接三维 CAD 数据进行产品可靠性验证;支持工艺人员快速编制产品零部件工艺,CAM 软件承接三维 CAD 数据模拟仿真零件加工过程,从而形成贯穿设计、仿真分析、工艺及生产模拟的数字化设计平台体系,其上的产品设计研发流程如图 2-2 所示。企业通过产品零部件标准库的建设及设计工艺数据的深度集成实现了设计工艺的数字化、智能化;采用 PDM 数据管理平台做技术数据管理,在做好数据管理的同时,也给其他信息系统提供了数据支撑,能够方便及时地向 ERP、MES、DNC 等系统提供物料信息、BOM 信息、工艺路线、代码信息等,实现数据在企业内部的贯通。
3.将自动化生产线及先进技术装备应用于产品智能制造
基于数年的顶驱装置研发、制造及产业化经验,北石建立了页岩气专用顶驱产品的智能制造生产线及工艺流程(见图 2-3),依靠引进、联合开发、自主研制等技术手段,提升最新一代页岩气专用智能顶驱生命周期内各环节的智能产业化程度。
图 2-2 基于 PDM 数据管理平台的顶驱产品设计研发流程
(1)生产制造环节:投用先进数控机床及加工中心,完成页岩气顶驱包括主轴在内的高精度螺纹加工;投用具有网络化监控和管理功能的热处理生产线及数字化、网络化的表面处理装备,供最新一代页岩气顶驱产品完成磷化、防硫化等处理工艺。
(2) 试验检验环节:自主研制顶驱全自动智能试验平台,供最新一代页岩气顶驱产品完成出厂前整机联调及性能试验,为最新的顶驱配套技术提供联调测试验证平台。
(3) 产品可追溯管理环节:定制研发北石产品技术支持服务系统,建立顶驱产品在产品生命周期内的可追溯信息的电子档案,为技术支持提供全面的档案跟踪集成管理平台。
(4) 仓储管理环节:联合开发基于 RFID 的智能仓储系统,彻底改变原来的库房人工管理方式,从仓储物资层面提升了顶驱装置的生产智能化水平。
(5) 现场技术服务环节:搭建顶驱远程监控系统及资源调度中心、产品备件订购平台等面向客户的远程技术支持系统,助力北石“制造+服务”发展进程。
图 2-3 页岩气专用顶驱产品工艺流程
4.生产环节关键技术装备智能物联,搭建数字化在线监控平台
(1) 采用了先进数控车床、车削中心、卧式镗铣加工中心、立式加工中心、摇臂钻床、数控高精度平面磨床等数字化机加工设备,并将这些生产车间级的底层设备进行物联,实现代码管理、数据采集、统计分析以及集中监控,建设了具备网络化监控和管理的机加工生产线(见图 2-4)。
图 2-4 具备网络化监控和管理的机加工生产线
(2)采用可碳氮共渗、可调制的箱式炉生产线及保护气氛的调制用井式炉生产线,对全生产线进行网络化监控和管理(见图 2-5),工艺参数、实时加工情况可远程监控,热处理工艺可远程上传,配套天车具备定点停车功能,实现真正的无人值守车间。
图 2-5 具备网络化监控和管理的热处理生产线
(3) 结合自身近三十余年的喷丸经验,吸收、借鉴并创新地对江苏昆山生产的先进数控喷丸机进行个性化定制,实现了参数设定、工艺管理、加工监控等的全数字化、网络化,以及喷丸工艺曲线的自动生成和保存(见图 2-6)。
图 2-6 具备网络化监控和管理的表面处理生
5.研制顶驱装置全自动智能试验平台,实现产品在线质量检测
北石借助多年顶驱研制经验,发挥机械制造优势,以网络化、智能化、绿色节能为出发点,采用直驱加载方式,结合智能传感器及数据采集模块、视频监控技术,基于 PROFINET、PROFIBUS 先进工业通信协议,完全自主研制了顶驱装置全自动智能试验平台(见图 2-7),完成了试验台架的设计、加工制造及试验台控制系统的软硬件设计与实现。
图 2-7 顶驱智能试验
6.搭建北石产品技术支持服务系统,实现生产过程数据的可追溯性管理
企业将传统业务需求与先进信息化技术手段相结合,定制研发了北石产品技术支持服务系统(见图2-8、图2-9),通过顶驱产品在装配、检验、试验、现场安装调试、现场技术服务响应、现场大修等产品生命周期环节的数据集成与异地共享,实现了检验过程记录电子档案库、呼叫中心技术支持和顶驱运行服务动态知识库三大核心功能。
图 2-8 北石产品技术支持服务系统总体架构
图 2-9 北石产品技术支持服务系统界面
7.通过信息化与工业化融合的手段,构建产品远程技术支持系统,实现“制造+服务”远程技术支持
将智能制造向产品生命周期末端持续扩展,推进“制造+服务”,搭建了顶驱远程监控系统及资源调度中心、产品备件订购平台(见图 2-10)等面向客户的远程技术支持系统,通过产品服务智能化实现按需、主动服务,通过微信及移动 App 主动给用户提供精准、高效的服务。
图 2-10 产品备件订购平台应用客
8.建立 MES,并与企业资源管理 ERP 系统进行集成,实现生产执行过程管控
北石MES在构建时按照规划主要涵盖与ERP集成的企业生产计划调度;与DNC集成的现场设备监控、信息采集、质量控制;基于ERP/MES/WMS/PDM的多源现场信息可视化展示等流程。作为企业生产过程监控和实现自动化、智能化制造的数据管理和信息共享的平台,MES的实施可以实现顶驱产品从设计、工艺管理到生产制造执行的一体化,从而打造以PLM/ERP/DNC/MES为软件核心的高效智能顶驱生产工厂。
三、实施成效
(1)研发了更加贴合石油装备制造行业应用特点的国产软件系统和应用模式。在北石顶驱智能制造数字化工厂建设过程中,在利用现有成熟技术的基础上,梳理石油装备制造在生产过程、业务流程等方面的行业特点,联合数码大方等国内知名软件解决方案供应商,创新研发出更加贴合行业应用特点的国产软件,并结合自身应用实践进行优化,最终形成了一套基于“两化融合”框架以及“制造+服务”理念的石油装备制造信息系统示范应用模式。
(2)建立了离散型石油装备制造智能工厂标准化模板。2014 年,北石以新区搬迁为契机,启动了数字化工厂建设,并于 2016 年正式投入使用。2017年,成功完成工信部两化融合管理体系建设。在两化融合实践中,北石不断优化智能化建设、总结应用及管理经验,形成了多业务领域、多系统之间的数据互联互通,构建了基于产品全生命周期的跨平台数据管理模式,并对智能决策进行初步尝试。
(3) 以获取管理智能化、生产智能化、服务智能化等优势为持续关注焦点,在信息化环境下打造企业精细化自动仓储管理能力、生产全流程管控能力、透明化生产现场管理能力、动态服务管理能力,助力企业可持续提升和绿色发展。
四、实施经验
(1)更加关注离散型石油装备制造业的产品研发、制造、服务一体化协同制造平台建设,深化以 PDM 为核心的 CAD/CAE/CAPP/CAM 集成协同,同时将研发设计一体化集成协同向生产制造端扩展,重点实现 PDM 与 ERP集成,积极探索 PDM、ERP 和 MES 的深入集成,努力打破设计、工艺、制造环节各执行层系统的数据壁垒,实现产品生命周期数据的互联互通和一致性管理,促进设计生产一体化。
(2)更加关注离散型石油装备制造业的生产现场的数字化改造,依托DNC 设备管理、设备物联及数据采集系统建设,将 ERP/DNC/MES/WMS 有效集成,建立基于各应用系统的统一的工业数据中心,实现企业研发、生产、经营、质量管理中各类人、财、物等对象数据的透明展现,为企业领导层快速决策提供丰富的信息和数据支持,最终实现生产制造车间数据透明化管理。
(3)更加关注离散型石油装备制造业的产品智能化升级,开发产品远程监控系统、备件系统、产品运行服务动态平台,推进传统制造业与计算机、互联网等先进信息技术的深度融合,以及“制造+服务”融合发展的新型产业形态。
(4)更加关注离散型石油装备制造实施两化融合以及构建智能工厂过程中的工业信息安全,从资金、管理、人员、设备、技术等维度出发,建立长效的工业网络安全防护机制,为工业控制系统及关键基础设施全生命周期的信息安全提供有效保障。
(沈克、徐文 供稿)