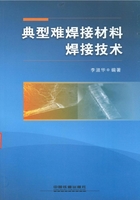
六、如何解决AZ31镁合金CO2激光焊焊缝下塌问题?
目前的镁合金激光焊接中,大部分研究和应用集中在无填丝的薄板焊接上,即通过母材的自熔化将两块金属连接在一起。焊接过程中,由于镁的表面张力较小(比铝还小),焊件受热时很容易使焊缝金属产生下塌现象,特别是焊接功率越大,工件的热输入量大越大,下塌现象越严重。为解决焊缝下塌问题,拓宽激光焊接的应用领域和提高焊缝的质量,一些科研工作者在激光填丝焊方面进行了较多的研究,提出了激光填丝焊接的新方法。激光填丝焊接与自熔焊接相比,具有很多优点:第一,激光填丝焊接对母材的加工和装配精度要求降低,可以降低加工成本;第二,激光填丝焊接过程中可以通过填加有用的合金成分方便改变和控制焊缝的组分,提高焊接接头质量;第三,激光填丝焊接可以焊接更厚的材料,而且容易实现多层焊。
例如,某院校的研究人员采用CO2激光焊接方法研究了AZ31镁合金的填丝焊接工艺,实现了镁合金的激光填丝焊接。试验选取的AZ31镁合金板材化学成分见表2-13,板材厚度为2.6mm。板材首先被加工成了80mm×245mm的试件,焊接前样品用丙酮清洗以去除表面的油脂。试验是在如图2-31所示的具有自动填丝功能的CO2激光焊接试验系统上进行的,该系统由一个最大输出功率为2.0kW的CO2激光器、具有特殊保护功能的焊枪、特制的焊接夹具、自动送丝机构和数控工作台等组成。焊接过程中,氩气从焊枪轴向、侧向和焊接夹具三路同时加入,如图2-31所示。轴向气体沿激光束轴线加入,用于保护激光的聚焦镜头不受熔滴的沾污;第二路气从焊枪侧面加入,以旁轴形式吹出,用于保护熔池表面和压缩由于激光激励产生的等离子体;第三路气从夹具背面加入到焊接夹具的气室中,可直接保护焊缝背面。
表2-13 AZ31镁合金的化学成分(一)


图2-31 CO2激光填丝焊接试验系统示意图
焊接采用平板对接方式,焊接过程中选取ERAZ31焊丝作为填充金属,焊丝直径为2.0mm,焊丝材料的组分与AZ31镁合金母材基本相同,焊丝由自动送丝机构通过送丝嘴送入到激光束中,焊丝与激光焦斑相交于工件的表面。焊接过程中,送丝角度(填充焊丝与工件表面之间的夹角,如图2-31中的α角)是影响焊接质量的一个重要参数。如果角度较小,送丝嘴靠近工件,则焊丝必须伸出较长的一段,导致焊丝的指向性下降,严重时焊丝会偏离光束,从而影响到激光对焊丝的加热效果。
实践证明,焊丝伸出送丝嘴的长度以不大于8mm为宜。反之,如果角度加大,就给调整填充焊丝带来问题,因为很小的位置偏差就会使光束与焊丝的接触点在垂直方向上发生很大的变化。送丝角度的大小还会影响到填充焊丝对激光的反射,送丝角度越大,焊丝对激光的反射越弱。通过工艺试验得到最佳送丝角度范围为20°~35°。研究者在工艺试验中都采用28°的送丝角度,获得的效果较好。
由于激光光束焦斑直径只有ф0.3mm,焊丝的直径为ф2mm,所以焊丝进入熔池较困难,选择合理的送丝方式对焊缝成型起着重要作用。送丝可分为“前送丝”和“后送丝”两种方式(如图2-32所示)。“前送丝”是指焊丝以一定倾角从熔池前方送入,焊丝端部对准激光聚焦光斑,焊丝先受到光斑加热,熔化后进入熔池并进一步受热熔化混合。“后送丝”是指焊丝以一定倾角从熔池后侧送入,并指向光斑,熔化后即混入尾部熔池并迅速凝固。

图2-32 两种送丝方式示意图
在相同焊接条件下,采用不同送丝方式得到的焊缝表面成型如图2-33所示。由图可见,采用“后送丝”方式填充的焊丝熔化但未与母材金属熔合,而采用“前送丝”方式填充的焊丝得到的焊缝成型较好。“后送丝”与“前送丝”方式得到的焊缝表面成型不同是因为不同的送丝方式对焊丝的加热机制不同,前者焊丝通过等离子体和熔池热辐射及热传导加热,这部分能量不足以使焊丝与母材金属完全熔合;而后者焊丝是激光直接照射和等离子体加热,使得焊丝熔化更充分。因此焊接时建议选择“前送丝”方式。

图2-33 不同送丝方式的焊缝表面成型
获得好的焊接质量除与送丝角度和送丝方式有关外,还与激光功率参数有关。激光工艺参数包括激光功率、焊接速度和送丝速度。根据有关镁合金CO2激光焊接经验,要获得较好的焊缝表面保护效果,正面和背面保护气体的流量需要达到20L/min以上。因此试验过程中,轴向气体压力保持为0.2MPa,正面和背面的保护气体流量都固定在20L/min。研究者试验中选择了L25(53)正交试验,焊接试验参数水平见表2-14。
表2-14 焊接试验参数水平表

正交试验结果表明,激光功率要达到1200W以上,焊丝才能获得较好的加热并熔化,否则焊丝熔化较差,焊缝成型不好。同样,焊接速度不能太快,否则焊缝中焊丝和母材熔合不好,较好的焊接速度范围为600~900mm/min。而送丝速度亦不能太快,否则焊丝来不及熔化,可用的送丝速度范围为400~800mm/min。上述就是2.6mm厚AZ31镁合金板材的激光填丝焊较优化的工艺参数。
从大量工艺试验中,选取了两个典型工艺条件下获得的焊缝进行了接头性能分析,两个典型接头的焊接工艺条件见表2-15。
表2-15 A、B两个典型焊缝的焊接工艺条件

两个焊接接头的断面形貌如图2-34所示。从图中可见,两个焊缝都完全熔透,背面也形成了凸出的焊缝形貌,实现了单面焊双面成型。由于焊接过程中填充了焊丝,使得两条焊缝的上表面都有明显的凸起,这样就克服了原来的激光自熔焊(无填丝)存在的上表面下塌问题。两个不同工艺条件下获得的焊缝断面有较大差别,焊接速度较小的焊缝B背面熔宽较大,背面下塌也较多。

图2-34 典型镁合金激光填丝焊接焊缝的横断面形貌
两个典型焊缝在母材、热影响区和焊缝三个不同区域的显微硬度如图2-35所示。从图中可见,典型试样A和B的焊缝区域的显微硬度值都与母材区域差不多,只是在热影响区域稍微高一点,但三个区域的显微硬度值都处于同一水平。因此填丝后的焊缝区域的硬度值与母材相比并没有大的改变。
抗拉强度的测量结果如图2-36所示。从图中可见,典型试样A和B的焊接接头抗拉强度与母材的抗拉强度相差不大,说明AZ31镁合金激光填丝焊焊接接头的力学性能良好,达到了母材的水平。

图2-35 典型镁合金焊缝的显微硬度

图2-36 典型试件A和B焊接接头与母材的抗拉强度对比
试样A焊接接头熔合线附近的微观组织结构如图2-37所示。从图中可见,母材金属区域为典型的变形镁合金的粗大等轴晶组织。同时,在熔合线附近没有发现明显的粗大晶粒组织形成,热影响区不明显。当采用激光焊接方法时,激光束能量非常集中,焊后冷却速度又很快,所以形成的热影响区很小。在焊缝区域是明显的枝状晶结构,而且枝状晶的伸长方向是指向焊缝中心的,这主要是由于激光焊接的快速冷却造成的,而且焊缝中心位置通过母材的传热比焊缝边缘更慢,冷却和凝固也最慢,从而使得枝状晶的生长方向指向了焊缝的中心。从图中还可发现,与母材区域相比,焊缝区域晶粒明显细化,这也为焊接接头具有良好力学性能提供了保证。

图2-37 试样A焊接接头的微观组织
由此可见,建立具有自动送丝功能的CO2激光焊接试验系统,通过填加AZ31镁合金焊丝,可以进行AZ31镁合金板材的激光填丝焊接。用填丝焊工艺形成的焊缝成型更加美观,克服了不填丝焊接情况下焊缝的严重下塌问题。填丝焊工艺形成的焊缝显微硬度和抗拉强度都与母材相当,达到了母材的力学性能。