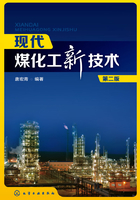
2.6 煤化工发展的六次热潮
可以说,每一轮煤化工发展的热潮来源就是产品的选择。从21世纪初到现在,先后有甲醇、煤制甲烷(合成天然气)、煤制烯烃、煤制油、煤制乙二醇和煤炭分质利用共六次热潮。
2.6.1 甲醇
甲醇是碳一化工的基础产品,以甲醇为原料生产众多化工产品的行业就是甲醇化工行业。它的发展在很大程度上取决于甲醇工业应用领域的开拓和深加工产品的开发。
20世纪末,甲醇被认为是碳一化工的主要发展方向[13],从此,甲醇的产量迅速上升,10年期间增长了7倍。
国内外甲醇制烯烃(MTO、MTP)的进展,以及甲醇制二甲醚、醋酸、碳酸二甲酯等下游产品的开发,为甲醇工业的大发展、技术的进步开辟了广阔的前景。国内单套甲醇装置的建设从10×104t级迅速达到180×104t级。很快,甲醇热遍布全国,2010年产能达到3840×104t,产量1574×104t;2013年产量达到2858×104t,产能达到6400×104t[27],产能过剩50%以上。由于国外甲醇价格便宜,沿海地区还从国外购进约485×104t。
过剩的甲醇往何处去?这是一个难题。现代煤化工的大项目都是新建甲醇装置,没有缓解甲醇过剩的意图。
尽管发改委对甲醇装置的建设规模有一定的限制,甲醇热依然不退,每年投入的产能在几百万吨左右。部分人士明确反对甲醇汽油的使用[28],而有的部门继续大力推广甲醇汽油[29]。这个问题争论了二十多年,显然没有结论。
“甲醇热”在争论中继续。
2.6.2 甲烷
被称为煤制天然气的工艺,实际上是合成甲烷。
作为13亿人口的大国,居民饮食和生活燃料问题是十分重要的。随着人民生活水平的提高,对环保、生活的舒适性要求越来越高,天然气肯定供不应求。让13亿人民的饮食和生活燃料都用上甲烷(约需180×108m3/a),实行全国居民用燃料的管道化,前景是相当诱人的!
“十一五”期间,我国共有四个装置151×108m3/a在建,实际上一期仅46×108m3/a。这些装置的建设基本上是引进鲁奇和David的甲烷化技术,个别项目在气化技术上有所变化。
各地对煤制甲烷的热情非常高,到2013年10月底为止,已经开建和获得国家批准进行可行性研究的项目有14个,总能力达到671×108m3。一旦天然气的价格上调,煤制天然气的项目很难控制住了。
2014年,第一个煤制甲烷的装置开车过程中出现一些问题,主要是设备腐蚀和环境污染问题,煤制甲烷的热情受到一定程度的打击,反对之声油然而起,新的项目没有再批准。实际上腐蚀问题是容易解决的,污染问题要从根本上解决比较困难。
煤制甲烷在狂热后受到打击。
2.6.3 煤制烯烃
煤制甲醇,甲醇再制烯烃工艺的主要产品是乙烯(C2H4)、丙烯(C3H6),和少量的碳四产品。传统上乙烯和丙烯的来源主要是石油烃类蒸汽裂解,其原料主要是石脑油。中东地区主要是靠天然气中的乙烷裂解来得到,因此成本很低。2013年中国进口聚乙烯880×104t,聚丙烯359×104t,可见缺口比较大。在此背景下,促使人们去寻求进一步开发非石油资源的新途径,甲醇制取烯烃成为备受关注的生产路线。
在世界上,我国甲醇转化烯烃的技术是领先的。在20世纪80年代初中科院大连化物所开始研究甲醇制烯烃工艺,2007年神华包头公司建设600kt/a甲醇制烯烃项目,2010年6月通过考核,技术上取得成功。
同年7月18日,国家发改委产业司对其作出结论[15]:“在当前油煤比价下,煤制烯烃经济效益较好,但现有发展方式的资源占用和二氧化碳及污染物排放明显高于石油制烯烃。面临十二五日益严峻的资源和环境双重约束,不宜大规模推广,应进一步优化建设方案,开展升级示范。”
与此同时,国内引进两套鲁奇公司甲醇制丙烯的装置,刚刚投产,运行情况尚未正常。
煤制烯烃可以代替石脑油,但是媒体宣传中称可以代替石油,一个‘脑’字的遗漏,隐藏着对石油工业的误解。
在这种形势下、一场大规模推广煤制烯烃的浪潮正在全国兴起,各地规划的项目大约有2800×104t[30]。新建的煤制烯烃工厂,都是新建大型甲醇装置,又怎样来缓解甲醇过剩的初衷?
聚烯烃的主要使用地在沿海,煤制聚烯烃的主要生产地在西北,这个矛盾很难克服,因此,沿海进口甲醇制聚烯烃的热情高涨,其实,这还不如直接进口聚烯烃。到2020年,石油烯烃的产量大约可以做到2000×104t/a,全国需求大约3000×104t/a,如果留给沿海地区进口200×104t/a,煤制烯烃的总容量也就是800×104t/a。由此可见,煤制烯烃的浪潮难免不与石油烯烃相互火拼。
尽管有许多不解的问题,但是这个浪潮还很热。
2.6.4 煤制油
中国是一个贫油的国家,需要煤制柴油技术作为一种补充。
煤制油产业实际上有F-T合成、直接液化和甲醇制汽油三个类型,煤焦油加氢不属于煤制油,它是“油制油”。
我国有400多万公里的公路,三千万台柴油机车,担负着运输重任。国内柴油产量是远远不够的,何况强大的国防需要高性能的柴油支撑。因此,把煤化工的重点指向柴油,特别是高性能柴油,作为石油化工的补充,这是国之所望,民之所期。
煤制油产业起步于20世纪30年代。2000年中科院山西煤化所建立了一套700t/a规模的浆态床合成油中间试验装置,2005年9月通过了国家科技部验收。其后为伊泰、潞安、神华提供技术,建设160~180kt的装置。
2010年7月伊泰合成油装置在稳定运行5000小时后,由国家有关部门对这套装置进行了考核,满负荷稳定运行72小时的数据为吨油能耗110GJ,折合标煤3.75t,催化剂的生产能力为1200~1500t油品/t,能量转化率为40.53%,比2010年全国煤电能量转化率36.67%高3.94个百分点。该厂2013年产量为18.16万吨油品,超过设计能力13.5%,实现了“安稳长满”运行。
至此,中国费托合成油的知识产权和技术成果已经确立,其成果涵盖了国际先进的煤间接液化所有核心技术,中国科学院至少有三代科学家为此奋斗了三十年。煤制油间接液化的所有单元技术,国内均已经成熟和掌握,技术水平已经超过南非,可以自行建设成套的煤制柴油装置,不必引进。
直接液化一直是和间接液化一样受到行业的普遍关注的,年产108万吨的装置已经运行6年,产率已经超过80%。
甲醇制汽油有的装置虽然运行几年,但是开工率没有达标。
由于发改委对煤制油装置的建设规模设定下限,限制了这个技术的发展,实际上批准在建的项目只有3个,因此许多地方不具备满足条件,真正动手的寥寥无几。
煤制油想热还没有热起来。
2.6.5 煤制乙二醇
乙二醇(EG)是一种重要的石油化工基础有机原料,从它可以衍生出100多种化工产品和化学品,主要用于生产聚酯纤维等。目前,化学工业中合成乙二醇的主要方法是先经石油路线合成乙烯,再氧化乙烯生产环氧乙烷,最后由环氧乙烷非催化水合反应得到乙二醇(简称乙烯路线)。
近年来,国内外开发了从煤制得合成气再进一步合成乙二醇的工艺。
国内合成乙二醇的科研十分活跃,其中最早进入工业化的是中科院福建物构所,经过几十年的研究,在实现300t/a和10000t/a的实验后,由丹化集团在内蒙古通辽建立年产乙二醇20×104t的示范装置,其中有8条2.5×104t乙二醇合成的生产线。该项目于2009年12月建成试车,目前偏离设计负荷较远,2014年生产12.6×104t,特别是其煤气化技术采用常压恩德炉气化,能耗高污染严重;加氢催化剂的活性衰减比较快,其原因没有定论。作为示范装置,单线规模太小,数量太多,不能反映大型化的本质。在这个示范厂还没有取得成功和考核的前提下,许多地方翻版这样的装置,显然没有道理。
2013年以来,各地对乙二醇的研究兴趣很浓,大约有10个单位在开发这个技术,还有引进的技术,中科院福建物构所开发了第二代技术,中试装置很多,最大规模为5万吨,2013年生产4.4万吨,基本算是成功。于是,2014年有了突飞猛进的发展,在建拟建的装置有二十多套,总能力约为560万吨/年。
煤制乙二醇“热”得提前了。
2.6.6 分质利用
大家都知道,应积极探求煤炭的高效利用办法。几十年来,科学家提出的分质利用,就是为了达到提高能量转化率的目的。
煤的分质利用包括三部分内容:中低温热解(500~650℃)后分解成气体(荒煤气)、液体(焦油)、固体(半焦)三种形态产品,然后分别利用。
对于荒煤气,可按照碳一化工的办法,得到CH4,CO和H2,分别或综合利用它们,这是非常成熟的技术。
焦油可先提取酚,然后再加氢制成轻质芳烃,石脑油等油品。
半焦作为清洁能源,可用于高炉喷吹和气化原料。
实际上,这个思维在20世纪三四十年代已经实现,只不过水平不如现在。
由此可见,分质转化工艺路线符合物质流和能量流的合理配置,有利于实现能耗和排放的最小化。几十年来被理论界认为是能耗、物耗最低的煤炭转化方式。
但是,既然大家早已经明白这个道理,为什么没有实现呢?问题出在整个运转过程中,没有完整和独立的示范厂、更没有完整的商业化装置。
在这种情况下,各地普遍误认为煤炭分质利用问题已经解决,把半焦磨成浆以后就可以气化,因此,近期立项的报告,集中在这个题目上,几十套装置建设的可研报告已经上报有关部门。
实际上,情况并非如此,分质利用的困难很大,污染严重,气化等许多工程问题没有解决。
煤炭分质利用热的太早了。