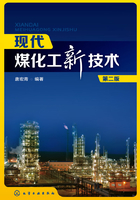
2.3 煤化工的效率
2.3.1 煤化工的效率高低
煤化工的效率高低和有序发展问题,已经引起国内高层学者的深切关注[17]。这个问题的实质是用煤作原料来生产化工产品是否合适。
这个问题的重要性在于,许多投资者认为,从能量转化率出发,应该投资能量转化率高的产品作为煤化工的发展方向。
但是,事实上不完全如此,我们应该研究能量转化率的问题,也要兼顾别的因素。同时,我们应该看到,一个化工装置的能量转化率没有理论值,它是一个工业技术的转化值,随着化工科研的继续,特别是催化剂的更新、节能技术的运用,某一种化工装置的能量转化率在不断提高。
以合成氨为例,20世纪70年代的天然气制合成氨的吨氨能耗为42GJ,到20世纪末是29GJ,现在可以低于28GJ。三十多年来合成氨工业的进步,主要就体现在能耗的降低上,也就是能量转化率的提高。现在再要这样大幅度地提高是比较困难的了,再进步的步伐就很小了,甲醇也一样。
目前,一些新兴的化工工艺正如三十多年前的合成氨工业一样,例如费托合成柴油,正在步入快速提高能量转化率的黄金时代。深入地进行科学研究,促使催化剂更新换代,工艺流程的优化,有可能大幅度提高能量转化率。因此完全立足于这些工艺今天的能量转化率来判断是否需要发展,是有失公允的。
让我们来看看煤电工业的情况,更能说明这一点。我国的煤电工业,单位电量的煤耗在逐步下降,体现了能量转化率数据随技术进步而变化,见表2-15。
表2-15 我国历年供电标准煤耗与能量转化率

2.3.2 吨产品的能耗
从工程设计的角度看来,吨产品的能耗是一个描述方法,是整个工程的宏观数据,以目前各种先进技术为依据的数据见表2-16。
表2-16 煤化工产品的能耗

①表中数据是预测值,实际的装置可能会有出入。
②2010年伊泰合成油厂考核值。
③包括其他液态烃。
煤制甲烷和甲醇的产业链比较短,后加工的工艺比较简单,导致它们的能量转化效率比较高。特别是甲醇,有几十年发展的历史和大型化的经验,现在的能量转化率已经是比较高了,再提高是可能的,但是幅度不会很大。
不难看出,改进煤化工的效率是所有的煤化工工艺的发展良策。
图2-2说明,同样的能量,通过不同的途径为不同的目的提供的能效是不同的,因此,能量转化率与用途有关。它们之间有高低的区别,但是没有先进与落后的区别,也就是说,应该按需使用而不是择高使用。

图2-2 煤制液体燃料能量转化图
2.3.3 煤气化的方法与能量转化效率有关
(1)不同的气化方法能耗也不同 现实告诉我们,煤化工的特点是气化方法与数据息息相关,煤气化的能耗随气化方法的不同而有差异。
以水煤浆气化为龙头技术的煤化工产品,与以粉煤气化为龙头技术的煤化工产品,吨产品的能耗会有一定的差别。这个差别反映在气化出口气体的成分上,但是这个差别的大小是要从整个流程来考虑的。
粉煤气化的能耗比水煤浆气化的能耗低,这是肯定的,但是低多少,却是要认真研究的。
前面已经提到,在Shell炉大举进军中国市场时,外商利用对比平台不一致的手法,故意夸大了这个数据。说是粉煤气化比水煤浆气化能耗可以节能15%,氧耗量能够节省25%等。经过研究,粉煤气化比水煤浆气化效率高6%。这个结论推广到甲醇,就是说大型水煤浆制甲醇装置的吨醇能耗约为42GJ,粉煤气化可以做到40GJ,再低的数据只是商家的宣传而已。
(2)对比平台不一致 这里要解释什么叫“对比平台不一致”的问题。在传统的化肥工业计算中,都是以1000m3的CO+H2的合成气来作为计算基础的,这是基于以下原因。
①化肥工业是以气体干基作为计算基础,忽略水蒸气,认为水蒸气是可以除去的无关组分。
②认为CO可以全部转化为H2,实际上是以100%的氢气为计算基准。
长期以来这个问题并没有引起人们的注意,没有从能量的角度考虑同一个“1000m3的CO+H2”会具有不同的能量。这里有两个不同:a.CO和H2各自的能量是不同的;b.CO+H2的能量随着它伴生的水蒸气含量不同而有所区别。
在比较Shell和Texaco气化工艺时,它们的差别就很明显了,用1000m3的CO+H2作为分母来计算的。实际上,Shell气化产生的合成气中的水蒸气含量很低(14%),CO的干基含量很高(66%),Texaco气化产生的合成气中的水蒸气含量很高(62%),CO的干基含量较低(46%),这两种气体所含的能量是不同的,是不能作为同一个分母来对比的。见表2-17。
表2-17 含有1000m3的CO+H2的合成气的实际湿气体的低热值

注:上述数据是根据同一种煤的62t/h投煤量,在两种气化方式下的计算结果[11]。
还要进一步说明的是,气化单元出口进入后续可利用能量的温度不是气化炉出口的温度,而是经过水洗塔的温度。这个时候的合成气湿气才有可能利用。比较这两个情况下的能量(低热值),才有意义。
计算必须采用同一煤种,这也是同一对比平台的基础。
表2-17数据表明,在同煤种、同投煤量条件下,水煤浆生成的1000m3的CO+H2的低热值,比粉煤气化的值要高得多,所以,这就叫“对比平台不一致”。利用1000m3的CO+H2进行比较,有的方法是吃了亏了,比较的数据就不可信了。
在一部分文献的论述中,两种气化炉的原料煤种都不一样,比较的数据就更没有代表性了。
近期国内一位著名学者经过多年研究[18],对于几种气化技术作了经济上的比较,值得参考,见表2-18。但就吨氨或吨醇成本和投资来说,仍要考虑全系统的能量问题。
表2-18 几种气化技术的经济比较[18]

2.3.4 煤化工是高能耗工业
煤化工的能耗比较大,因此不主张大规模发展煤化工的学者认为煤化工不合算,能量浪费大,这个意见是有道理的。例如,合成氨的能耗就说明这个问题,见表2-19。数据表明,以煤为原料的工艺比以天然气为原料的工艺能耗至少高40%,足以说明煤化工是高能耗的工业。
表2-19 煤与天然气制氨能耗比较

但是,反过来想一下,不发展煤化工行吗?
目前,我国的能源消耗主要是靠煤,我国的能源产量是以煤为主。表2-20是近年中国能源产量的统计,从能量形式来讲,我国消耗的能量中70%靠的是煤。
表2-20 近年中国能源产量

随着近年来国民经济的快速发展,我国石油消费一直呈上涨趋势,从1993年起我国已成为石油净进口国。据海关公布,2013年进口原油2.82亿吨。
与天然气化工和石油化工来比,煤化工的吨产品能耗无疑是比较大的。以甲醇为例,在都是最先进的技术条件下,天然气制甲醇合理流程的吨醇能耗为30GJ,煤制甲醇合理流程的吨醇能耗为42GJ。相比之下,煤化工的能耗约高出40%左右。
这就是煤化工的代价,这个代价是很大的,不仅能量的回收率很低,煤中大约70%的C生成的CO2后直接排放到大气中(见表2-21),从而引起环境的问题,这也就决定了煤化工不可能没有控制地发展。
表2-21 排入大气中碳的比例

我们在呼唤发展煤化工的时候,冷静地想一想,不要走到另一个极端上去,时刻记住煤化工是高能耗工业。
2.3.5 能量转化率不是煤化工发展的主要判据
能量转化率是重要的数据,是我们选择产品的要素之一。但是,从总体上来说,这个能量转化率应该是全过程的,不是局部的,我们不能把它作为唯一的判据。也就是说,我们不能将一个产品的能量转化率最高的产品来作为我们首选发展的唯一目标。
能量转化率的具体数据是否重要呢?在有些情况下是重要的,在有些情况下是不重要的,主要表现在以下方面。
①对同一种原料、同一种产品、不同的工艺作比较是重要的。
这个问题在设计工作中经常体现,设计院要做工艺比较,其中最重要的指标就是能耗。不同工艺路线的能耗比较,往往决定了一种工艺路线的取舍。
这个问题还体现在已经生产的企业中,节能改造极其重要。例如,山西有个企业,在十年期间将原有的300kt/a合成氨装置,进行节能扩产50%的改造,并不增加总体系列,使合成氨的能耗从61GJ/t降至46GJ/t,总投资仅为新建全套系列的48%。这个实例说明,对同一种原料、同一种产品、不同的工艺作比较,提高能量转化率是何等重要。
②对不同原料、同一种产品,不同的工艺作比较是不重要的。
如果我们想得到甲醇,用天然气来做原料,明显比用煤来做原料的能耗低,这个结论已经是一个人所共知的常识,再作比较已经没有什么意义。但在一个只有煤资源的地方,去强调天然气化工的能量转化率如何高,不正是脱离实际吗?在这种地方只有强调节能改造、降低能耗。
然而事实是多么无情,由于我国天然气资源不足,有一些用天然气生产甲醇和合成氨的工厂,现在改用煤作原料。按照现在的说法是主动降低能量转化率,与理论界的想法背道而驰。
③对不同产品的不同工艺作比较是没有意义的。
近年来,这个问题非常热门,热心学者试图证明煤制甲醇、煤制三烃等比煤制柴油的能量转化率高[5],执意不希望建设煤制柴油的工厂。这个比较有必要吗?
这里以煤制不同产品为例来研究这个问题。图2-2说明同样的标煤可以得到不同的产品,提供的能量是不同的。我们能否得到将煤生产甲烷和甲醇是最合理的结论呢?不能!因为我们还要看这个产品是否是国家需要的,是否能够替代别的产品。
现在热门的甲醇汽油,代替的是汽油而不是柴油。在世界上,汽油是过剩的物资,柴油是缺额的物资,在当前的中国,也是这个局面。甲醇、乙醇、天然气、电动车、MTG等代替汽油,代来代去,越代汽油越过剩。
因此,甲醇汽油与煤制柴油不要混为一谈,将它们来比较能量转化率是毫无意义的。
近年来,也有人提出甲醇柴油,也有人提出用DMM3-8(聚甲氧基二甲醚)作为柴油成分,这些建议也很难推行。柴油的国标指标有二十多项,替代产品要全面达到国标是很困难的,要经过严格的测试,有一项没有达标,就是不合格。
④在煤化工领域内,不同煤种、同样产品的能量转化率的比较意义也不大。
对不同品质的煤,同一规模、同样的产品也会有不同的结果,能量转化率的出入在5%左右是正常的。
出现这个现象,在于煤的品质不同。加工过程中的能耗自然不同,高品质的煤,可以采用效率较高的煤气化方法,反应温度低一些,氧耗也低一些,物耗能耗都可以下降,能量转化率当然就可能高一些。低品质的煤中有大量的水和灰渣,脱除这些物质,自然需要消耗一定的能量,能量转化率就可能低一些。源头在煤上,工艺过程没有受到责备的必要。
因此,用作煤化工原料的煤,尽量用品质好一点的煤。
近期出现一个没有道理的事情,有关部门居然把每一种煤化工工艺的装置能量转化率规定了先进值和一般值,这有点脱离实际。如果一个企业采用优质原料煤,它永远当先进,采用劣质原料煤,它永远当落后,这太不公平了。
⑤对同一种原料、同一装置中有多种不同性质的产品,能量转化率的数据本身意义就不大,没有与其他工艺比较的必要性。
近期发生了新的情况,煤的分质利用及低品质煤的提质已经开始受人高度关注。有人将其能量转化率可以达到75%~80%作为理由,说全国有多少褐煤可以提炼出多少油,从而说这个煤制油的工艺版本比F-T制油有效得多,从而来推动新一轮煤化工热。这真是奇迹吗?非也,煤的分质利用是个比较好的主意,应该认真研究它,但是它同时有大量的副产品半焦,这个半焦还没有利用就算在产品油品中,往后利用时消耗的能量就可以为零了,变成了永动机。显然,这是一个明显的理论错误。
总之,我们没有必要过分认真地用能量转化率作不同产品的横向比较。我国目前最大的煤化工产品是煤制合成氨,几十年来,它的建设从来都是根据国民经济中农业的需求来决定的,而非取决于氨和甲醇等产品的能耗差别。
现在有不少煤化工装置是由电力部门来运作的,电力部门非常看重能量转化率在不同装置上的比较,这是十分正确的。但是这个指标在化工上,横向看不见得有多么重要,道理已经叙述得很清楚了。
做好每一个化工装置设计本身的节能降耗,才是正道。