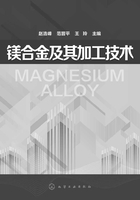
第1章 镁合金的特性及发展
1.1 镁及镁合金的特性
1.1.1 镁矿资源及生产方法
1.1.1.1 镁矿资源及开发
镁合金是最轻的商用金属工程材料,也是一种理想的现代结构材料。在世界范围内得到开发和应用的材料中,镁及其合金材料因具有密度小及可回收利用等优点而格外引人注目。它有许多优良的物理及力学性能,具有较高的比强度和比刚度,容易切削加工,易于铸造,减震性好,能够承受较大的冲击震动负荷,导电、导热性好,磁屏蔽性能优良。正是因这些符合“21世纪绿色结构材料”的一系列特征,使其特别适合在汽车、摩托车等交通工具和计算机、通信、仪器仪表、家电、轻工、军事等领域应用。此外,随着社会的快速发展,金属材料的消耗日益增多,对铁、铝、铜等金属的需求持续增长,常用的金属资源已经表现出逐年短缺的势态,而镁是世界上最丰富的矿产资源之一及地壳中分布较广的元素之一,其在地壳中的储量极其丰富,约占地壳总储藏量的2.77%,居第8位。与地壳中其他金属元素的含量相比,镁元素在地壳中的含量仅在铝、铁之后,位居第三。在大多数国家都能发现镁矿石,但最主要的资源还是海水。海水中含有丰富的镁,其含量为0.13%,也就是说每立方米海水中约含有0.13kg镁。因而湖水、海水成为人们取之不尽的镁资源。仅死海一处的镁,若能得到全部的开发,就可供人类使用22000年。可见,占地球表面积70%的海洋也是一个天然的镁资源宝库。表1-1为地壳中分布最广的化学元素的含量。镁以化合物形态存在的镁矿,在1500种矿物中占200多种,但能作为炼镁原料的镁矿并不多,如表1-2所示。
表1-1 地壳中分布最广的化学元素的含量

表1-2 炼镁用的镁矿及其特性

目前具有工业应用价值的镁矿资源有菱镁矿、白云石、水氯镁石(浓缩的海水、卤水或MgCl2·6H2O)、光卤石四种。
(1)菱镁矿 菱镁矿(MgCO3)是碳酸盐矿物,理论上含MgO 47.82%、CO252.18%,矿物有结晶形与无定形两种。结晶形菱镁矿属于六方晶系,有玻璃光泽,而无定形菱镁矿则没有光泽,并有角质断口。菱镁矿外观色泽为白色或淡黄色,由于常含有碳酸钙、碳酸铁、碳酸锰、二氧化硅等杂质,因此其颜色各种各样。菱镁矿许多国家都有,如中国、前苏联、印度、意大利等。世界上储量最大、质量最好的菱镁矿矿床在中国的辽宁省大石桥。中国山东掖县、河北邢台等地均有菱镁矿,其质量不如辽宁省大石桥的。能作为炼镁原料的菱镁矿,其品位为:MgO 45%~46%,CaO 0.8%~1.0%,SiO20.5%~1.0%。菱镁矿可作为电解法炼镁的原料,也可作为热法炼镁的原料。
(2)白云石 白云石(MgCO3·CaCO3)是碳酸镁与碳酸钙的复盐。理论上含MgO 21.8%、CaO 30.4%、CO247.68%。CaO与MgO的质量比为1.394,摩尔比为1.0。大多数天然白云石中CaO与MgO的质量比为1.4~1.7。白云石有结晶形与无定形两种。白云石因含有不同的杂质而具有不同的颜色。白云石分布很广,许多国家、地区都有。白云石主要作为硅热法炼镁的原料,也可以先提取MgO,再成球氯化为MgCl2,用电解法生产金属镁。能作为硅热法炼镁的白云石,其品位为:MgO 19%~21%,CaO 30%~33%,Fe2O3+Al2O3<1.0%,SiO2<0.5%,Na2O+K2O<0.01%,Mn<0.0005%,烧损率为46.5%~47.5%。
(3)水氯镁石及光卤石 水氯镁石(MgCl2·6H2O)与光卤石(KCl·MgCl2·6H2O)是两种含水的氯盐。这两种原料必须经过彻底脱水成为无水MgCl2或无水光卤石(KCl·MgCl2)后才能按电解法来生产金属镁。MgCl2·6H2O与KCl·MgCl2·6H2O在中国青海省盐湖中有极为丰富的资源,其组分为:MgCl230.75%,KCl 24.98%,NaCl 0.77%,H2O 34.55%。
正是由于镁及其合金材料表现出的这些优异特性和其具有的潜在价值,自1808年金属镁被发现以来,人们就从未停止过对镁的开发和应用。仅仅是在最初的一百多年里,由于镁价格和技术两大瓶颈问题,加之铝的使用而推迟了镁的广泛应用。镁较早作为工程结构材料使用较少,主要用于制备铝合金、钢铁脱硫等,也主要应用于航空、航天领域。但到20世纪80年代,随着两大瓶颈问题的突破,镁及其合金材料的开发应用高速增长,镁合金在工程领域的广泛应用越来越受到重视,在90年代之后得到迅猛发展。近几十年来,全世界的镁产量翻了一倍,世界各国纷纷把镁资源作为新时代的重要战略资源进行规划。美国、日本、欧洲等国家和地区为攻克镁合金对各个生产环节的关键技术进行了大量的综合性研究。中国具有丰富的镁资源,菱镁矿储量,原镁产能、产量和出口均居世界首位。中国是世界上镁资源最丰富的国家,菱镁矿探明储量约占世界的1/4,具有发展镁产业的先天性基础条件。此外,中国不但是一个摩托车生产、消费和出口大国,也是一个潜在的汽车生产和消费大国,镁及镁合金产品的市场应用前景广阔。但是在镁和镁合金的研究和应用方面我们有很大的空间待开发。因此,充分利用中国的镁资源优势,将镁的资源优势转变为技术、经济优势,促进国民经济发展,增强中国在镁行业的国际竞争力,是摆在我们面前的迫切任务。所以,大力发展镁及镁合金产业对于中国的可持续发展将具有非常重要的战略意义。虽然目前在铝合金领域所消费的镁最多,但近年来增长速度已减缓,而在压铸件中的用镁量(目前主要是汽车和IT行业)则呈快速增长之势。
1.1.1.2 镁的生产方法
镁的生产方法分为两大类,即氯化镁或光卤石熔盐电解法和热还原法。金属镁从发展到现在经历了200多年的历史(即1808~2016年),工业生产的年代已有130余年(1886~2016年)的历史。在这130年中,镁的发展可分为三个阶段。
19世纪初(1808年)英国科学家H.戴维从氧化镁中分离出了镁。1929年法国科学家A.布西用钾或钠的蒸气去作用熔融氯化镁得到了金属镁。到了19世纪60年代,英国和美国才开始用化学法得到多一点的镁。此阶段经历了78年(1808~1886年),但没有形成工业生产的规模。1830年英国科学家M.法拉第首先用电解熔融氯化镁的方法制得了纯镁。1852年P.本生在实验室范围内对此法进行了较详细的研究,直到1886年在德国开始镁的工业生产。1886年以后,镁的需求量增加,1909年由于“电子”镁基合金(作结构材料)的发明和使用,对镁生产的发展产生了重大的影响,奠定了电解氯化镁生产镁的方法。直到现在,电解法仍然是具有先进水平的工艺方法。无水光卤石熔体采用MgCl2-NaCl-KCl三元系电解质电解,电解温度为720℃。电解质中MgCl2含量为9%~12%,电流效率为75%。由于镁的需求量越来越大,仅靠电解法生产镁不能满足镁的需求,所以许多科学家在化学法的基础上,研究了热还原法炼镁。硅热法炼镁的特点是真空条件下的固相反应,反应速率与炉料的细度、还原温度及体系的剩余压力有关。氧化镁真空热还原法炼镁是1913年开始的,到现在已有100余年的历史。第一次用硅作还原剂还原氧化镁是1924年由Л.Χ.安吉平和A.Ф.阿拉贝舍夫实现的。1932年安吉平、阿拉贝舍夫用铝硅合金作还原剂还原氧化镁。1941年加拿大Toronto大学教授L.M.皮江在渥太华建立了一个以硅铁还原煅烧白云石炼镁的试验工厂,并获得了成功。1942年加拿大政府在哈雷白云石矿建立了一个年产5000t金属镁的硅热法炼镁厂。皮江法炼镁成为工业炼镁的第二大方法。第二次世界大战以后,1947年法国着手研究了连续生产的硅热法炼镁工艺流程,1950年建立了扩大试验炉,1959年第一台日产镁2t半工业炉投产,经过长期的研究试验,1969年建成年产4500t镁的半连续硅热法镁厂(半连续还原炉日产镁3.5t),1971年扩建到年产9000t镁(半连续还原炉日产镁6.5t)。半连续法炼镁(即熔渣导电半连续还原炉)成为镁工业生产中主要工艺方法之一。
1.1.1.3 世界镁产量及市场的变化
20世纪50年代以前,镁工业的发展主要依附于军事工业。60年代以后,由于金属镁在民用市场和空间技术的应用得到发展,推动了镁的增长。表1-3~表1-5所示为2000年前后世界总产镁量及镁的消耗量。美国、加拿大、挪威、前独联体、法国、意大利、前南斯拉夫、巴西、印度、朝鲜都生产金属镁,日本于1995年10月宣布永久性退出镁冶炼行业。从表1-3~表1-5可以看出,西方国家镁的供需在20世纪80年代后期及90年代初基本上是平衡的。由于世界经济衰退,镁的需求量及产量同时下降。随着西方经济逐步复苏,镁的需求量逐年增长。2000年,全球镁消费量为47.32万吨,增长了5.39%,其中西方世界为44.27万吨,增长了4.65%,西方世界的缺口为18.97万吨,其缺口的85%需要从中国进口,中国已是西方最大的镁供应国。尽管在2000年全球镁产量增长了6.5%,但中国增长率已达到21.7%,西方世界原镁产量几乎没有增长。2001年起,西方原镁产量已开始出现下降形势。到2002年需求量达到了48万吨,在这个大发展时期,西方国家也开始扩大生产能力。2004~2009年期间,世界镁消费量在增长,2007年达到最大。据中国有色金属工业协会镁业分会统计,2012年,中国原镁产量69.83万吨,占全球总产量的82%。2014年中国原镁产量87.39万吨,与2013同期相比增长13.53%。陕西省作为中国最大的金属镁产地,2014年累计生产40.46万吨,同比增长17.86%,占中国产量的46.30%。其中榆林地区累计生产39.63万吨,同比增长19.08%;府谷地区累计生产34.81万吨,同比增长29.89%,占中国总产量的39.83%。
表1-3 1998~2001年中国及全球镁产量

表1-4 1998~2000年中国及世界镁消费量

表1-5 2004~2009年世界镁消费量

镁具有丰富的资源,镁合金的应用研究和开发符合汽车工业、电子工业和航天工业等的发展要求,因而受到了各国政府、企业和科技界的高度重视。20世纪90年代以来,美国、德国、日本、加拿大等发达国家相继出台了各自的镁合金研究计划,将镁资源作为21世纪的重要战略物资,推动了镁合金在交通、计算机、通信、消费类电子、国防军工等诸多领域的应用。如德国政府制订了一个投资2500万德国马克的镁合金研究开发计划,主要研究压铸镁合金的生产工艺、快速原形化与工具制造技术、切削加工技术、连接技术和半固态成形工艺,以提高德国在镁合金应用方面的能力。国际企业界对镁合金的研发也不遗余力,如汽车业为了降低轿车自重以减少汽油消耗、减轻环境污染,同时使轿车的使用性能更加优良,各大汽车公司对镁合金的应用研究投入巨大的人力、物力,将镁合金制造零件作为重要发展方向。同时世界大牌汽车公司如美国通用公司与世界第二大镁业公司——挪威诺斯克·希德洛镁业公司达成协议,就增加镁合金在汽车上的应用进行长期合作,由希德洛公司长期向通用汽车公司供应所需的镁合金和镁合金零部件。大型的汽车厂家对镁资源开发进行控股,与镁金属生产厂家联合投资,共同参与,进行镁金属的大型生产项目的开发,以确保经济而稳定的镁的供应,满足汽车工业和其他行业对镁合金的日益增长的巨大需求。如美国福特(Ford)公司于1997年与Normandy矿产公司、澳大利亚联邦科学及工业研究院(CSIRO)合作组成澳大利亚镁业公司,在澳大利亚昆士兰(Gueesland)合股投资建设全球最大的镁生产基地。同时,联合开展低成本的镁冶炼工艺研究。德国大众汽车公司与以色列镁生产厂家合作,在镁资源丰富的死海地区合资兴建镁加工厂,其中大众公司占35%股份,以色列占65%。日本通过“家电回收法”限制工程塑料的使用,率先将镁合金用于制造笔记本电脑、移动电话、摄像机、数码相机等先进的电子装置壳体,并计划逐步推广到电视、投影仪、音响等大型家电中,目的是保持环境协调发展。许多大型项目的实施和完成,必将推动镁工业的低成本生产工艺的研究开发和应用,加上镁合金回收容易的因素,将使全球镁及镁合金的价格稳步下降。
首先应用镁合金压铸结构件的是德国VolksWagen汽车公司。之后,美国、前苏联、日本以及欧洲的一些国家相继在汽车制造行业采用镁合金压铸结构件,如曲轴箱、传动轴外壳、空调机外壳、变速箱壳体、驾驶舱仪表板、轮箍、气缸体、气缸盖、分配支架、油泵壳体、过滤器外壳等。这个阶段全世界的最高年产量曾经达到24000t。大众汽车公司是生产镁合金压铸件的最大厂家,在早期的比特(Beetle)型汽车中就开始使用镁合金。到1981年,该公司已生产2000多万辆这种型号的汽车,使用了40万吨镁。最初这些零件是用金属型铸造的,接着在1949年用压铸法生产小零件,1960年又有了进一步的发展,用压铸法生产了变速箱体和曲轴箱。20世纪70年代开始,空冷发动机的生产达到顶峰,1971年生产了200多万辆汽车,镁的使用量达42000t。20世纪70年代中期推销前轮驱动带液冷发动机的新车型,与此同时镁的价格与铝比较显著地上涨,面对这种形势,为保持灵活,公司规定变速箱体可用镁或铝压铸件,两套方案供生产选择,作为降低镁成本的措施,实际上扩大了除自产废料以外的其他废旧金属的回收使用。但到20世纪80年代中期,世界汽车制造镁合金压铸行业开始衰弱,以德国VolksWagen汽车公司所属Kassel变速箱厂为代表的世界汽车镁合金压铸骨干企业相继将镁合金压铸的生产资源转移至巴西、墨西哥、中国等发展中国家,而中断了自己的镁合金压铸生产。进入20世纪90年代后,以加拿大Meridian公司、美国Ltmt公司为代表的一批新兴的专业生产镁合金压铸汽车零件的企业重新出现在汽车制造业。近几年,镁合金汽车压铸零部件在欧美等发达国家汽车工业上的应用呈现出持续快速增长的态势。轿车的进气歧管材质主要为铝合金,近年来,应用镁合金材质的进气歧管有逐渐扩大之势(主要为AZ91D),通用(20世纪90年代初就在其北极星发动机中采用)、奔驰、大众等欧美汽车公司都在生产或积极研制。1997年,德国组织了44个企业(其中5个汽车公司)、5所大学及研究所投资2500万马克实施镁压铸计划(MADICA),计划实施为期3年,计划中的5个子项目为压铸研究与发展、快速成形、镁合金加工、镁合金装配及流变铸造。德国母线实施的SFB390项目投资5300万马克,历时15年研究镁合金。该项目共有17个子项目,其中7个项目涉及镁合金压铸生产,另外3个项目涉及新型镁材料。
1.1.1.4 中国原镁生产及产品的发展
中国原镁产能及产量主要分布于能源(煤、电)和资源(白云石、光卤石)较丰富的省区,其中山西、宁夏、河南是中国镁发展的优势地区,2000年分别占中国产量的67.64%、11.1%、6.7%。另有吉林、河北、青海、陕西、内蒙古、山东、云南等省区有部分产量。尽管世界范围内镁合金及制备技术发展较早,但是中国自己的镁工业只是在新中国成立后才开始建立。新中国成立前,中国的镁工业,仅1938年日本在中国抚顺建立了一个镁车间,以后这个镁车间未恢复生产。随着中国汽车工业、电子通信工业的飞速发展,对镁合金的需求与日俱增,镁行业发展很快。1957年在苏联专家的指导下,在原来的基础上,采用菱镁矿干团炉料氯化生产氯化镁熔体再电解生产金属镁的方法建成了年产3000t金属镁的车间(即抚顺铝厂镁分厂)。1963年后将菱镁矿干团炉料氯化改为菱镁矿颗粒氯化生产MgCl2,再电解MgCl2生产金属镁。1986年中国着手将青海民和镁厂的半连续硅热法炼镁工艺改造为年产4000t镁的电解法镁厂(生产工艺为菱镁矿颗粒氯化——电解法)。1992年后,利用青海盐湖资源,将天然光卤石脱水为无水光卤石,增加了电解无水光卤石制取金属镁的生产工艺,并解决了生产工艺中氯气的利用与平衡问题,使青海民和镁厂成为中国利用镁资源生产金属镁的重要基地。1987年起,皮江法炼镁在经过多年的研究及引进消化吸收的基础上,开始工业化生产。由于皮江法炼镁具有工艺流程相对简单、投资少,设计及生产规模灵活,所需原料白云石及煤炭资源丰富且分布较广等特点,符合当时的中国国情,得到了迅速发展。在经历了1988年、1992年两次皮江法建设高潮后,1995年起,中国皮江法在国际市场价格上涨的拉动下又形成了第三次建设高潮。1995~1996年中国共建有皮江法镁厂近500家,分布于20个省区,其中90%以上为1000t以下的小厂,又以300~500t的居多。1996年起,严重的供过于求导致价格大幅下跌,而发展条件的差异,又使大量镁厂停产倒闭。在短暂的市场繁荣之后,镁生产企业又在欧美反倾销及国内竞争加剧的双重压力下生存与发展,并在调整中仍保持着高速发展的势头,1999年起中国已成为世界最大的原镁生产国。
1.1.1.5 中国镁行业的发展条件及新材料研发
中国是镁的资源大国和生产大国,原镁产量居世界首位,但80%以上作为初级原料低价出口,镁深加工能力薄弱,镁合金应用领域的开拓更是严重滞后于发达国家。为适应21世纪高新技术产业发展的需求,扩大镁合金等轻质合金材料的应用,增强镁工业在国际上的竞争力,“十五”期间,特别是在西部大开发和加入世贸组织的历史机遇下,国家不仅组织实施了“镁合金开发应用及产业化”重大科技攻关专项,还在“863”计划中也安排了耐热、变形、高强、高韧等镁合金新材料、新工艺的研究内容。这些举措改善了中国镁合金的生产结构,扩展了镁合金的应用领域,推动了中国镁合金产业的健康快速发展。中国镁工业的发展,具备良好的资源条件、能源条件,具备劳动力便宜、投资成本低的优势,加之不断的技术创新、技术进步,因此,在国际竞争中显现出了后发优势。
①具有丰富的炼镁资源:目前世界上的炼镁原料主要有菱镁矿、白云石、光卤石、蛇尾石、海水和盐湖水等。这些资源在中国都十分丰富,且分布较广。中国是菱镁矿储量最多的国家,已探明储量27亿吨;白云石储量为40多亿吨;青海盐湖钾镁盐有16.55亿吨氯化镁和8.54亿吨光卤石,随着西部大开发中盐湖资源的综合利用,将副产更多的炼镁原料。中国的炼镁资源不仅丰富、分布广,而且易于开采,为镁工业提供了资源保证。
②具有良好的能源条件:炼镁是高耗能产业,其中皮江法煤耗为8~12t/t镁,硅铁消耗1.2~1.5t/t镁,电解法粗镁直流电耗15000~19000kW·h。因此,煤炭及电力资源较丰富的山西、宁夏、青海等省区具备发展镁的优势。煤炭采购价格成为皮江法企业竞争的最重要的因素。
③具有较低的投资成本:与国外电解法相比,中国皮江法具有投资少、建设周期短的特点,单位投资成本仅是国外电解法的几十分之一。
④生产工艺简单。正是由于这些发展条件,20世纪90年代以来,市场经济推动了中国镁工业的发展。目前,已有相当多的企业通过ISO质量认证,镁锭、镁合金、镁粉产品质量与产品标准已与国际接轨,镁行业已经出现了多个国际知名的品牌。现在中国镁产能与产量已居全球第一位。中国已成为世界上最大的镁生产国和镁出口国。中国镁企业为扩大出口,提高产品附加价值与市场占有率,积极按市场需要开发新产品,调整产品结构。中国镁工业的高速发展为全球镁的推广与应用做出了积极的贡献,也深刻地改变了全球镁工业的竞争格局。1992年以前,中国是镁的净进口国,1992年起,中国成为镁的净出口国。1995~2000年是中国镁出口高速增长的时期。2000年,镁产品出口量已达16.5万吨,是1995年的3.52倍,是1990年的258倍。中国已成为最大的镁产品出口国,西方世界供需缺口的85%以上需由中国供应。2000年,已有20家企业可以生产镁合金,其中专业镁合金厂家4个,总生产能力8万吨/年,产量4万吨,产品主要按美国和欧洲镁合金标准生产;有镁粉生产企业40余家,其中专业镁粉生产企业20家,总产能9万吨,总产量4.5万吨,产品包括镁粉(含钝化镁粉)、镁粒、镁屑等;镁的产量与出口量分别达到19.5万吨和16.53万吨,其中皮江法占98%。2001年,镁的产量为21.6万吨,出口量达到19.3万吨。出口企业主要集中在山西、宁夏、北京,出口商也在竞争中走向集中,并形成经营规模。加拿大、中国台湾、韩国等国家和地区成为中国镁的新兴市场。欧盟、美国、日本是中国镁产品三大出口市场,欧盟占到出口量的1/3,其他两家差不多。根据海关总署最新统计数据,2014年中国镁出口量共计43.50万吨,同比增长5.80%。其中,镁锭出口量22.73万吨,同比增长7.18%;镁合金出口量10.65万吨,同比增长4.42%;镁粉出口量8.80万吨,同比增长3.05%;镁废碎料出口量0.29万吨,同比增长87.66%;镁加工材出口量0.37万吨,同比下降16.83%;镁制品出口量0.66万吨,同比增长15.65%。2014年在全球经济复苏缓慢,中国经济转型升级的新常态下,中国镁出口增幅较上年回落,但整体仍呈现为增长态势。6种税号镁产品出口中,镁锭、镁合金、镁粉出口较上年同期为个位数的小幅增长,镁加工材出口量下降,镁制品出口量增长,尤以镁废碎料增长显著。
虽然目前中国的镁合金研究和应用还处于发展阶段,尤其是镁合金的应用落后于西方发达国家,但市场潜力非常诱人。首先,中国的个人汽车市场方兴未艾;其次,中国是笔记本电脑、手机等电子产品需求增长最快的市场;另外,中国的自行车市场面临全面的升级换代。这一切为中国的镁合金产业提供了巨大的发展空间和机遇。发展方向是通过调整现有成熟牌号镁合金的化学成分、冶炼工艺、成形工艺和热处理工艺等来提高合金的各项性能以满足不同场合的需求;进行新型镁合金(如快凝镁合金、非晶镁合金、镁合金生物、功能材料以及高强Mg-Li合金、Mg-RE合金、高温镁合金等)的开发与研制;进行镁合金腐蚀与防护技术的研发。通过这些举措,镁合金产业必将成为中国新的经济增长点,从而实现中国从“镁资源大国”向“镁生产强国”转变。
1.1.2 镁的物理性质
镁位于元素周期表第ⅡA族,原子序数12,属于活泼性碱金属,镁的自由原子的电子排列为1s22s22p63s2,所以镁通常为二价(Mg2+)。金属镁是一种很轻的金属,它的质量比铝还轻1/3。它不仅轻,而且化学性质很活泼,它是电与热的良好导体。镁是元素周期系第二族化学元素,其标准大气压下纯镁的晶格是密集的六方晶系,晶格常数a=0.321nm,c=0.521nm,c/a=1.623。镁的蒸气压相当高,在627℃时为215.95Pa,在727℃时为1037.1Pa,因此镁极易挥发。镁的蒸气压与温度的关系可用下式表示:
lgp=435.9-394.6×10-3T-1018.4×10-3T-1+116.5×10-6T2+333lgT(570-924)
lgp=1547.6-1014.4×103T-1-136lgT(924-1380) (1-1)
纯镁是柔软可锻的金属,镁的力学性能如表1-6及表1-7所示。纯镁的力学性能差,20℃时抗拉强度仅为90MPa,HB硬度为30。因此,纯镁很少用于工程用途,通常将某些金属(常用的有Al、Zn、Mn、稀土等)加入纯镁中,制成强度较高的系列镁合金,如Mg-Mn、Mg-Al-Mn、Mg-Al-Zn、Mg-Al-Zn-Mn等合金,以满足工程需要。镁与铝、铜、锰、锌、锆、钍等金属可构成合金,这些合金的力学性能比纯镁的优良。但镁与铁、铍、钾、钠等金属不构成使用的合金。镁中所含的杂质大多数对镁的力学性能有不良影响。MgO超过0.1%时会降低镁的力学性能。钠的含量超过0.01%或者钾的含量超过0.03%时也会大大降低镁的抗拉强度及其他力学性能。但同时含钠达0.07%和含钾达0.01%时,镁的强度并不降低,而只降低其塑性。但也有些元素的含量对镁的物理性能有所改善。如杂质硅能使镁的抗拉强度增大;钙能使镁的晶粒细化,含钙约为0.45%时,镁的塑性显著提高;含铝1%左右能增加镁的硬度和强度;铜在1%以下时不使镁的机械强度发生变化。铁与镁不能形成合金,但铁在镁中的溶解度随温度增高而增大,表1-8为铁在镁中的溶解度。
表1-6 20℃时镁的力学性能

表1-7 高温下镁的力学性能

注:1kgf=9.80665N。
表1-8 铁在镁中的溶解度

1.1.3 镁的化学性质
1.1.3.1 镁与氧的作用
镁与铝在化学、物理性质上存在较大的差别,主要表现在化学反应活性、金属液表面氧化物质致密性、凝固过程中的热效应及抗电化学腐蚀能力等方面。镁具有比铝强的化学反应活性,而且金属液表面不能形成如铝合金液一样致密的氧化物保护膜以阻止氧化反应的继续进行。镁被氧化后表面形成疏松的氧化膜,其致密系数α=0.79(Al2O3的α=1.28),这种不致密的表面膜不能阻碍反应物质的通过,使氧化得以不断进行。因此镁合金易燃烧甚至爆炸。由于镁液容易与氧、水蒸气等作用而发生燃烧,甚至发生爆炸,因此熔镁过程中的安全问题也是一个很突出的问题。镁合金还易溶解其他金属,包括严重降低镁合金抗电化学腐蚀能力的镍、铜等元素。另外,同样体积的铝合金及镁合金液在凝固过程中,镁合金释放的热量显著低于铝合金液。
另外,镁液很易与大气中的氧、水蒸气、氮反应而生成不溶于镁液的、难熔的MgO、Mg3N2等化合物。它们混入铸型后即成为“氧化夹杂”,在浇铸过程及在铸型流动中所产生的则称为“二次氧化夹杂”。镁与氧的化学亲和力要比铝与氧的大,通常金属与氧的亲和力大小可由它们的氧化物生成热和分解压来判断。氧化物的生成热越大、分解压越小,则与氧的亲和力就越强。它的氧化动力学曲线呈直线形式,氧化速率与时间无关,氧化过程完全由反应界面所控制。镁的氧化与温度关系密切:当温度较低时,镁的氧化速率不大;温度高于500℃时,氧化速率加快;当温度超过熔点650℃时,其氧化速率急剧增加,一遇氧即发生激烈氧化而燃烧,放出大量的热。反应生成的氧化镁绝热性很好,使反应界面所产生的热不能迅速向外散发,进而提高界面上的温度。这种恶性循环态势必然加速镁的氧化,燃烧反应更加激烈,反应界面的温度也越来越高,甚至可达2850℃,远高于镁的沸点(1107℃),引起镁熔体大量汽化,最终发生爆炸。
在镁中添加微量(0.002%~0.01%)的金属铍,可以提高镁熔体的抗氧化能力。由于铍是镁的表面活性元素,富集于镁熔液表面,致使表面含铍量约为合金中的10倍,并优先氧化。氧化铍的致密度系数α=1.71,所以氧化铍易于填入氧化镁膜的孔隙中,形成致密的复合氧化膜。但铍的加入量不宜过多,过多会引起晶粒粗化,恶化力学性能,并加大热裂倾向。当温度高于750℃时,铍对提高镁的抗氧化的作用大大降低,而镁合金的熔炼温度一般均高于750℃,因此用加铍防止镁熔体氧化仅是一种辅助措施。镁合金的熔铸必须采取有效措施,才能防止镁的氧化燃烧。
1.1.3.2 镁与水的作用
镁液不仅易燃烧,而且在遇水时引起剧烈爆炸。镁无论是处于固态还是液态均能与水发生反应,其反应方程式如下:
(1-2)
(1-3)
在室温下,反应速率缓慢;随着温度升高,反应速率加快,并且Mg(OH)2会分解为水及MgO,高温时只发生式(1-2)反应。在相同条件下,镁与水之间的反应,要比镁与氧之间的反应更激烈。
当熔融镁与水接触时,不仅因生成MgO放出大量的热,而且反应产物氢与周围大气中的氧迅速作用生成水,水又受热急剧汽化膨胀,结果导致猛烈的爆炸,引起镁熔体的剧烈燃烧与飞溅。熔炼镁合金时,与熔体相接触的炉料、工具、熔剂等均应干燥。当生产中坩埚泄漏时,镁液由于受热强烈蒸发(镁的沸点仅1100℃)并发生燃烧,以及在清理打磨时镁粉尘的自行燃烧,导致爆炸,所以在生产中应有专门的安全防火措施。
镁与水的反应也是镁熔体中氢的主要来源,它与镁合金铸件的主要缺陷——缩松的产生有密切联系。
1.1.3.3 镁与氮气的作用
固体镁在常温、干燥空气中一般是比较稳定的,不易燃烧,但在熔融状态时容易燃烧,并生成氧化镁(MgO)。在300℃时,镁与空气中的N2作用生成氮化镁(Mg3N2),使镁表面成为棕黄色。温度达600℃时,反应迅速。镁与氮气发生如下反应:
(1-4)
在室温下反应速率极慢,当镁处于液态时,反应速率加快。温度高于1000℃时,反应激烈。不过这种反应要比Mg与O2、Mg与H2O的反应缓慢得多。Mg3N2系粉状化合物,不能阻止式(1-4)的反应继续进行;同时Mg3N2膜亦不能防止镁的蒸发,所以氮气不能防止镁熔体的氧化和燃烧。
1.1.3.4 与其他物质的反应
镁在干燥大气、碳酸盐、氟化物、铬酸盐、氢氧化钠溶液、苯、四氯化碳、汽油、煤油及润滑油(不含水和酸)中稳定,所以镁合金常被用作齿轮箱和润滑油、燃油系统的零件。镁能溶解在无机酸(HCl、H2SO4、HNO3、H3PO4)中,但能耐氢氟酸和铬酸。盐卤、硫化物、氮化物、碳酸氢钠(NaHCO3)溶液对镁有侵蚀作用。镁在NaOH和Na2CO3溶液中是稳定的,但有机酸能侵蚀金属镁。利用镁在氢氟酸或氢氧化钠溶液中较玻璃及铝稳定的特点,镁铸件的细孔可用玻璃管或铝管镶铸,以后再用氢氟酸或氢氧化钠溶液把管子腐蚀掉,从而得到细孔铸件。
当熔镁使用熔剂时,如操作不当,熔剂随同镁液混入铸型即成为“熔剂夹杂”。这些非金属夹杂物的存在显著降低铸件的力学性能。氧化夹杂存在处亦常伴随着缩松、气孔的存在。熔剂夹杂的存在还将成为镁铸件腐蚀的发源地。因为熔剂中的MgCl2吸湿性很强,露出在铸件表面上的熔剂夹杂很易吸收大气中的水分,并发生反应,使镁不断被腐蚀而变成白色的Mg(OH)2,大大降低铸件的抗蚀性。因此,防止和去除上述两类非金属夹杂物将成为镁的熔炼工艺中最突出的问题。镁合金熔炼过程中另一重要工序是变质处理,它将对合金的晶粒大小和力学性能有很大的影响,且对镁液中的氧化夹杂亦有一定的影响,将在后面详细叙述。
(1-5)
(1-6)
1.1.4 镁合金的性能特点
镁合金是一种能够满足各种行业需求、发展前景可观的轻质材料,与铝和钢相比,镁合金材料具有以下特点。
(1)密度 镁的密度大约是1.7g/cm3,是铝的2/3,是铁的1/4,它是最轻的实用金属。在现有的工程用金属材料中,镁合金密度最小,通常为1.75~1.85g/cm3,约为铝的64%,钢的23%,是目前最轻的商用金属结构材料。
(2)比强度、比刚度 镁合金的比强度和疲劳强度均比铸铝合金高。与普通的塑料、铝合金及钢铁比,镁合金的比强度和比刚度更高,所以在实现同样强度和刚度零部件的情况下,镁合金的零部件能做得比塑料、铝合金和钢铁轻。因此,采用镁合金铸件可以减轻机器结构的重量,从而提高其效率,降低能量消耗和增大发动机功率以及运输机械的载重量和速度。在不降低零部件强度的前提下,镁合金零部件的质量比铝合金或钢的轻很多,而且镁合金的刚度随厚度的增加呈立方比增加,用镁合金制造刚性好的整体构件十分有利。
(3)机械加工性能 镁合金具有优良的切削加工性能,其切削速度可大大高于其他金属。因镁合金比其他金属的切削阻力小,若镁合金切削阻力为1,则铝合金的为118,黄铜的为213,铸铁的为315(切削阻力为铝合金的0.56、黄铜的0.43、铸铁的0.29);机械加工速度快,生产效率高,刀具使用寿命长。对刀具的消耗很小,切削功率很小。切削掉一定量金属所需的功率,如以镁合金为1,则铝合金为1.8,铸铁为3.5,低碳钢为6(镁合金、铝合金、铸铁、低合金钢切削同样零件消耗的功率比值为1:1.8:3.5:6.3)。另一个突出的特点是镁合金不需磨削和抛光,不使用切削液即可得到光洁的表面。此外,镁合金铸件在受冲击及摩擦时不会起火花。
(4)电磁屏蔽性能 镁合金是非磁性材料,电磁屏蔽性能好,抗电磁波干扰能力强,镁合金的电磁波屏蔽性能比在塑料上电镀屏蔽膜的效果还好,因此,使用镁合金可省去电磁波屏蔽膜的电镀工序,可以用于制作手机等通信产品的部件。
(5)传热性及导电性 镁合金的传热和热膨胀系数较大,弹性模量在常用金属中是最低的。镁合金的电导率大于铝和钢;传热系数比铝小,比塑料高出数十倍(如是工程塑料的300倍),比钢大。可以用于制造要求散热性能良好的电子产品。
(6)再生性能 镁合金与塑料不同,它可以简单地再生使用且不降低其力学性能。由于熔点低、比热容小,再生熔解时所消耗的能量较低。
(7)抗蠕变性能 镁随着时间和温度的变化在尺寸上蠕变少。
(8)对振动、冲击的吸收性 镁合金的比弹性模量与高强度铝合金、合金钢大致相同。铸件的截面刚度随其厚度的立方比而增加,所以当截面厚度增至2倍时,刚度将增大至8倍。因此用镁合金制造刚性好的整体构件十分有利。它除了能减轻重量外,还可以减少零件数目和大量的铆接、焊接和组合装配等工序。与弹性模量有关的另一特性,是铸造镁合金有高的振动阻尼容量,即高的减振性。在一定场合下,除有利于避免过高的应力集中外,在弹性范围内,当受冲击载荷时,所吸收的能量比铝大一半。镁合金具有极好的吸收能量的能力,可吸收震动和噪声。另外,镁合金的阻尼性比铝合金大数十倍,减震效果显著,适合制备抗震零部件。由于镁合金对振动能量的吸收性能好,使用在驱动和传动的部件上可减少振动。另外,冲击能量吸收性能好,比铝合金具有更好的伸长率,受到冲击后能吸收冲击能量而不会产生断裂,由冲撞而引起的凹陷小于其他金属。因此,镁合金适宜于铸造受猛烈碰撞的零件如轮毂和传送带轮等。魏光清采用不同的铸造工艺制备了机床减震用细晶AZ91Ce0.2镁合金,并对显微组织、力学性能、阻尼性能和耐磨损性能进行了测试与对比分析。结果表明,在试验条件下,获得的AZ91Ce0.2镁合金平均晶粒尺寸在90μm以内;铸造工艺对镁合金的性能影响较大,其中0℃抗拉强度增加了48MPa,室温抗拉强度增加了43MPa,-40℃冲击吸收功增加了23J,0℃冲击吸收功增加了20J,室温阻尼值提高了68.09%,0℃磨损体积减少了74.70%,室温磨损体积减少了78.67%。
镁合金在受外力作用时容易产生较大的变形,这一特性能使受力构件的应力分布更为均匀。镁合金的这个特性与其弹性模量较低有关,即弹性形变功与弹性模量成反比。
(9)无毒、易回收利用 镁及其化合物无毒,镁产品的使用不会造成环境污染。废旧镁合金铸件有可回收再熔化利用的特性,并可作为二次材料进行再铸造。镁合金的上述优点,使得其在航空航天、交通运输、电子仪器等领域有着广阔的应用前景。
但是镁合金也有一定的不足,主要体现在如下几个方面。
①熔化镁合金需要在保护条件下进行。镁的化学性质活泼,镁与氧的化学亲和力很大,在高温甚至在固态条件下,就很容易与空气中的氧气发生反应,放出大量热量。其生成的产物氧化镁不仅导热性差,热量不能及时发散,造成局部温度较高,引起燃烧和爆炸,而且生成的氧化镁致密度低,疏松多孔,不能有效隔绝空气中氧的侵入,使氧化反应继续进行。且表面生成的氧化镁膜是不致密的,镁在液态时氧化更为剧烈,很易燃烧。氧化膜致密与否由氧化物与生成它所消耗的金属两者体积之比(a)所决定,此a称为致密系数。由于体积比a<1,故镁氧化后生成氧化镁的体积缩小,因而氧化膜是疏松的。由于上述原因,镁的熔铸工艺需采用专门的防护措施,通常需在熔剂覆盖下进行熔炼,而在镁铸件中也易产生氧化夹杂和熔剂夹杂的缺陷。所以国内有单位在气体(SF6)保护下进行熔炼,可以改善这种情况。浇铸零件时,为了避免氧化燃烧以及与造型材料本身和造型材料中的水分相互作用,必须在型砂成分中添加保护剂。常用的保护剂有氟化物(氟硼酸铵、酸性氟化铵等)、硫黄、硼酸、菱镁矿、烷基磺酸钠等。芯砂中常用的阻化剂为硫黄和硼酸。
镁合金铸件的固溶热处理也需要在二氧化硫、二氧化碳或六氟化硫等气体保护下进行,扩散和分解过程缓慢是镁固溶体的特点。所以镁合金在固溶处理和时效时需要保持较长的时间。同样的原因,铸造镁合金的淬火一般只需要在空气或人造气流中进行。
②镁的平衡电位低,与不同类金属接触时易发生电偶腐蚀,并充当阳极。在空气、淡水及海水中镁合金的耐腐蚀性均不好,需要进行防护。
③镁属于HCP结构,在室温下只有1个滑移面和三个滑移系,因此它的塑性变形主要依赖于滑移与孪生的协调动作,但镁晶体中的滑移仅发生在滑移面与拉力方向倾斜的某些晶体内,因而滑移过程将会受到极大的限制。而且在这种取向下孪生很难发生,所以晶体很快就会出现脆性断裂。在温度超过225℃时,镁晶体中的附加滑移面开始起作用,塑性变形能力有所增强,因此其塑性加工只能在中高温下进行。
④在两次世界大战之间,镁合金铸件遇到了很多困难,因为它们容易产生不均匀的大晶粒,这常使力学性能恶化,还有显微疏松,而且变形部件的性能具有过大的方向性。特别是屈服应力相对于抗张强度总是偏低。
总的说来,铸镁合金虽有良好的使用性能,但其熔铸工艺较为复杂,废品较多,生产成本较高,而且铸镁车间有害气体多,劳动条件差,这些都限制了它的应用。但近年来,铸镁工艺日益发展,成本不断降低,在航空和导弹上应用较多,其他工业部门如仪表等也有应用。由于镁合金的压力加工性不足,约有1/4以上的镁用于铸造铸件。由于有上述的一些主要特点,镁合金被广泛应用于各个领域。
1.1.5 镁合金的牌号
一般来说,镁合金的分类依据主要有成形工艺、合金化学成分和是否含锆三种。镁合金的标记方法有很多种,各国标准不一,目前普遍使用的是美国材料试验协会(ASTM)的标记方法。根据ASTM标准,镁合金的牌号和品级由四部分组成,第一部分为字母,标记合金中主要的合金元素,代表合金中含量较高的元素的字母放在前面,如果两个主要合金元素的含量相等,两个字母就以字母顺序排列;第二部分为数字,标记合金中主要合金元素的质量分数,四舍五入取整数;第三部分为字母,表明合金的品级;第四部分表明状态,由一个字母和一个数字组成。在工业中应用较广泛的镁合金是压铸镁合金,主要4个系列,即AZ系列Mg-Al-Zn、AM系列Mg-Al-Mn、AS系列Mg-Al-Si和AE系列Mg-Al-RE。如AZ91E表示主要合金元素为Al和Zn,其名义含量分别为9%和1%,E表示AZ91E是含9%Al和1%Zn合金系列的第五位。如AZ91D-T6,表明该合金中含铝8.3%~9.7%,含锌0.35%~1.0%,D表明合金纯度要求,T6表明合金状态为固溶+时效。AZ91A、AM60A和AS41A是适用于压力铸造的合金,一般在铸态(F)下使用。AZ91B是最常用的压铸镁合金,AM60A适用于制造汽车轮毂和其他要求高伸长率、高韧度以及屈服强度和抗拉强度综合力学性能好的铸件。AS41A合金在175℃以下的抗蠕变性能优于AZ91B和AM60A合金,并有良好的抗拉强度、屈服强度和伸长率等综合力学性能。AZ91D、AM60B和AS41B是高耐蚀的高纯合金。
中国传统铸造镁合金牌号按照“ZM”编排。表1-9为两系列牌号的镁-铝系和镁-铝-锌系合金的物理性能。中国传统变形镁合金用“ZB”编排。为了使镁合金能够大量用作结构材料,开展变形镁合金的研制非常必要。镁合金的加工方式主要有挤压、轧制和锻造,由于镁合金通常为密排六方结构,常温下变形非常困难,为了得到较大变形量而不产生裂纹,镁合金通常采用热加工处理。经过变形后的镁合金缺陷减少,组织更加均匀细化,与铸造镁合金相比,可获得更高的强度、更好的延展性及更多样化的力学性能,而且变形镁合金的比强度也优于其他金属材料,如铝合金、钢材等,因此能够满足不同场合结构件的使用要求。最早的变形合金是Mg-1.5Mn,用于薄板、挤压件和锻件,但这种材料已在发展。常用的变形镁合金主要有Mg-Al、Mg-Li、Mg-Mn、Mg-Zn-Zr、Mg-RE等系列,而近年来开发的Mg-Gd-Y-Zr变形镁合金因具有优良的室温及高温性能而受到广泛关注。变形镁合金与普通铸造、压铸镁合金的典型力学性能对比,说明变形镁合金具有更大的优势。变形稀土镁合金比铸造镁合金具有更高的强度、更好的塑性。研究表明,镁合金在热变形后,组织得到了显著细化,铸造组织缺陷被消除,使得产品的综合力学性能大大提高。发展变形镁合金制品可使镁合金更大地应用于结构件上,如轧制的薄板或厚板、挤压材和锻件。但由于变形镁合金的开发与研究不够充分,有关稀土对其组织性能影响的研究远不如稀土在铸造镁合金中的研究那么深入和充分,相关的公开专题研究报道相对较少。中国变形镁合金材料的研制与开发处于发展阶段,因此,研究和开发性能优良、规格多样的变形镁合金材料显得十分重要。因为六方结构的Mg滑移系较少,变形加工度受到极大的限制。Mg在室温中的塑性变形主要靠基面{0001}沿密排方向<1120>的滑移和锥面的孪晶运动。当应力与基面平行时,只有压缩时才能产生孪晶变形,应力与基面垂直时,在拉伸条件下才能产生。当温度≥250℃,锥面{1011}也能参加滑移变形,塑性变形更加容易时,孪晶变形才退居次要地位。因此,镁合金的加工制品,一般多利用热变形。Mg的塑性低,很难用合金化的方法来改善。Al、Ag、Zn、Y、Nd、Mn等虽能在Mg中大量固溶,但只能增加固溶强化效应,不能改变晶体结构,高低温变形阻力反而增大。因此,变形用镁合金的合金化程度应比铸造合金低,以利于塑性变形。
表1-9 镁-铝系和镁-铝-锌系合金的物理性能

镁合金一般均在300~500℃进行挤压、轧制和模压加工。由于镁合金的上述变形特点,六方结构的Mg晶体弹性模量(E)各向异性不明显,织构对塑性加工产品的E值影响不大。挤压温度较低时,{0001}和{1010}倾向于与挤压方向平行;轧制时基面{0001}倾向于与板面平行,{1010}与轧向一致。压应力与基面{0001}平行时易生孪晶,所以镁合金受压应力时纵向屈服强度比受拉应力时低。两种屈服强度的比值为0.5~0.7,所以结构设计(包括抗弯性能设计在内)时要考虑抗压强度的影响。因此,这个比值是评价镁合金质量的一项重要指标,但该值因合金而异,并且随晶粒变细而增大;镁合金用卷筒卷取时,能产生交变的拉、压应变,在受压应变时则产生大量孪晶,使抗拉强度明显降低。生产各种塑性加工和作为抗蠕变(300~350℃)材料用的镁合金产品,其合金化程度一般要比铸造镁合金低,其目的就是要利于塑性变形。
通过变形可以生产尺寸多样的板、棒、管、型材及锻件产品,并且可以通过材料组织控制和热处理工艺的应用,获得比铸造镁合金更高的强度、延展性及力学性能,从而满足更多结构件的需要。2000年国际镁协会(International Magnesium Association,IMA)提出了发展镁合金材料的长远目标和计划,即研究与开发新型变形镁合金,开发变形镁合金生产新工艺,生产高质量的变形镁合金产品,这也代表了当今国际镁工业的发展趋势。美国、日本等发达国家十分重视变形镁合金的研究与开发,变形镁合金材料已开始向系列化发展,其中美国的变形镁合金材料体系较为完备,有Mg-Al、Mg-Zn、Mg-RE、Mg-Li、Mg-Th等。日本在1999年由教育部、科技部、体育部和文化部共同组织实施了“Platform Science and Technology for Advanced Magnesium Alloy”计划,着重研究镁的新合金、新工艺,开发超高强变形镁合金材料和可冷压加工的镁合金板材;2003年美国汽车材料联合体(The US Automotive Materials Partnership,USAMP)组织了多家公司进行汽车发动机、变速箱、油盘等部件的镁合金拉伸件研究;荷兰Delft科技大学对AZ31、AZ61、AZ80及含Ca、Sr元素的高温镁合金MRI153等的均匀化处理、等温挤压工艺及表面处理技术进行了全面研究,并开发出了一系列适合航空用的镁合金型材;法国和俄罗斯开发了鱼雷动力源用变形镁合金阳极薄板材料。
稀土元素的特性使其在耐热铸造镁合金中得到了广泛应用。但在变形镁合金中,由于稀土形成的晶界化合物不利于塑性加工,因此长期以来一直未被采用。近年来,稀土在变形镁合金中的应用逐渐得到重视,并取得了重要成果。MB8为在Mg-Mn系变形镁合金MB1基础上添加(0.15%~0.35%)Ce而得到的稀土变形镁合金,其常温拉伸屈服强度由100MPa提高到170MPa,伸长率则由4%提高到11%,同时可提高耐热性并减轻各向异性倾向;MB26为在Mg-Zn系变形镁合金MB15基础上添加富钇混合稀土开发出来的高强度变形镁合金,其最大延伸率达到1450%以上。余琨等通过在ZK60变形镁合金中添加0.8%Nd,得到了细小的热变形动态再结晶晶粒,并形成了含稀土的第二相,使合金具有较好的挤压变形能力和热处理强化能力。王斌等对添加Y和Nd的ZK60变形镁合金进行了热轧及热处理试验,结果表明,Y和Nd均能使其室温断裂强度大幅提高。
以稀土作为主合金元素的变形镁合金可获得高的力学性能和耐热性能。中国航空材料研究所开发了以Zn及Nd、Y为主合金元素的变形镁合金MB22、MB25,均具有较强的时效强化效果及较高的室温、高温性能。阎蕴琪等研究了不同变形条件对Mg-2.2Nd-0.5Zn-0.5Zr合金室温拉伸性能和组织的影响,发现弥散于晶界的Mg9Nd细化了晶粒,使合金的强度和延性都有不同程度的增加。随着更多稀土元素的特性被人们所认知,又相继开发出了一系列高性能稀土变形镁合金系,如Mg-Y、Mg-Gd、Mg-Sc、Mg-Dy等。1974年研究者发现,经过挤压、调质和时效处理的Mg-15Gd合金在高温及室温下具有较高的抗拉强度。而在Mg-Gd合金中加入Mn、Y、Zr、Sc等元素均能提高其室温性能。2001年,I.A.Anyanwu等研制出了具有优良耐热性能的Mg-9Gd-4Y-0.6Zr(质量分数,%)变形镁合金。有人研究了不同温度挤压对Mg-9Gd-4Y-0.6Zr镁合金组织及力学性能的影响,结果表明,随着挤压温度从500℃降低到400℃,晶粒也从126μm细化到7.4μm,抗拉强度和延伸率分别从200.1MPa和2.93%提高到312.4MPa和5.6%。肖阳等对挤压T5态的Mg-9Gd-4Y-0.6Zr进行了不同温度的性能测试,发现该合金具有优良的高温性能,400℃还可出现超塑性。S.M.He等研究发现,Mg-Gd-Y-Zr变形合金的时效析出顺序应为(S.S.S.S)→β″(DO19)→β'(cbco)→β1(fcc)→β(fcc),而不是T.Honma等研究发现的(S.S.S.S)→β″(DO19)→β'(cbco)→β(fcc),并指出当合金中析出β'相时,合金强度、硬度最高。
Mg-Zn-RE系准晶强化高性能镁合金材料的研发是近来研究的热点。Mg3 REZn6准晶为三维二十面体结构,其高温下很稳定,且具有高强度、硬度、低表面能等特性,是一种良好的强化相。中国开发的Mg-Zn-RE-Zr系MB25和MB26高强变形镁合金挤压后,晶粒尺寸为4~5μm,就是因为Mg3 YZn6准晶抑制了挤压变形时再结晶晶粒的长大。Bae等开发的Mg-4.3Zn-0.7Y(原子分数,%)合金,400℃热轧后晶粒尺寸约为14μm,0.5~2.0μm大小的准晶分布在α-Mg晶粒中,该合金的室温及高温性能优良。另外,Alok Singh等也在准晶方面做了工作。虽然利用准晶强化镁合金大有潜力,但还有许多问题未得到解决,如准晶的结构、形成机制、力学性能及加工方法等还有待进一步研究。