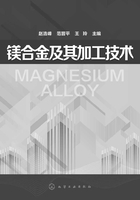
2.2 镁合金的重力铸造技术
2.2.1 砂型铸造
2.2.1.1 镁合金砂型铸造工艺性能
砂型铸造特别适合于生产大型、复杂、多品种、小批量的镁合金零件。镁合金砂型铸造虽然已经发展了数十年,也积累了十分丰富的经验,但仍有许多工作尚待完善。目前砂型铸造生产工艺复杂,生产成本高,多应用于小批量、多品种的军工产品;产品合格率较低,常见的质量问题包括熔剂夹杂、氧化夹杂、疏松、疏孔、浇不足、裂纹、晶粒粗大等。用砂型铸造来生产民用品也有一个技术适应性的问题,例如,用于生产飞机轮毂的工艺并不完全适合生产轿车的轮毂。
液态镁合金在型腔中流动属于黏性流体流动,特别是在结晶及有氧化膜出现时有黏度增大的现象。液态镁合金在型腔中流动属于黏性流体,流动属于非稳态流动。随着液流温度的降低,液体黏度增加,流动阻力增大。资料表明,液态镁合金在砂型型腔中的流动属于多孔管的流动,有可能将外界气体卷入。液态镁合金在型腔中流动属于紊流流动。镁合金对铸型的充填能力和合金本身的流动性、液态金属的过热度、金属本身的氧化倾向有关。镁合金凝固收缩大,铸件易产生缩孔及疏松。因此,工艺上要求顺序凝固。生产中,常选用合适的铸型材料来实现这种凝固制度。各铸型材料的热物理性能见表2-39。
表2-39 铸型材料的热物理性能

2.2.1.2 浇冒系统
ZM-6是铸造镁合金中一种重要的合金,工业生产中以砂型铸造为主。镁-铝合金具有较宽的凝固区间,因此在浇铸时易形成缩孔,降低合金的组织完善性。王狂飞等根据镁合金铸造的特点和工艺要求,采用开放-封闭式浇铸系统以及设置冒口等,成功地试制生产出该类零件。同时,也确定了合理实用的镁合金砂型铸造工艺。在铸件浇冒系统设计时,应该注意合理设计浇铸系统:浇铸系统设计要防止金属液体的飞溅和冲击,并要加强铸件的顺序凝固。浇铸系统的比例推荐为:对大型铸件,F直:F横:F内取1:(3~5):(3~8);对中型铸件,F直:F横:F内取1:(2~4):(3~6);对小型铸件,F直:F横:F内取1:(2~3):(1.5~1.4)。直浇道截面积可按式∑F直=G/[0.0443γμτ(H均)1/2]设计。其中F直为总面积,cm2;μ为系数,取0.35~0.5,阻力大时取上限;G为直浇道流过的总金属液质量,kg;τ为浇铸时间;γ为液态金属的密度;H均为液态金属的平均计算静压头。采取底注方式,也可采用缝隙式。采取底注式可以形成补缩的通道,采用缝隙侧注也可获得良好的力学性能。采取合适的横浇道及内浇口:使用椭圆截面的横浇道以减少吸气倾向;内浇口设计成薄而宽的形状,以避免热节的出现。浇口截面要允许液体有足够大的充型率,减小金属进入铸型的流动速度,否则会造成冲砂或充型不足。表2-40为内浇口的厚度。采取分层浇铸:分层浇铸是指逐层浇入合金液。待第一层液体快凝固时再浇入第二层合金液,这样可实现第二层合金液对第一层液体凝固收缩进行补充。采用明冒口:采用尺寸足够大的明冒口,使其能在铸件凝固时发挥补缩作用,要在近于内浇口及被补缩的部位放置。ZA-27合金凝固范围很宽,而且对凝固收缩十分敏感。因此,铸件的设计(不同厚度的分布)和冒口的安放应能保证准确的定向凝固。冒口可用补充加热的方法来保温,也可采用浇铸后向冒口补注金属的方法来保温。铸件冒口尺寸设计一般采用模数法,其比例为:M件:M冒颈:M冒=1:(1.1~1.5):(1.2~1.8)。多采用池型浇口杯。
表2-40 内浇口的厚度

2.2.1.3 重力铸造中的其他注意事项
砂型铸件是镁合金用得最多的方面,铸造时应遵循某些由镁的物理性质和化学活性所决定的一般原则。在型砂中必须加入适当的抑制剂以避免熔融的镁和汽之间的反应而放出氢,对生砂或充二氧化碳提高结合力的砂用硫作抑制剂,而对合成砂也加入化合物如KBF和KSiF6。对某些砂也用硼酸,它既有助于成形又由于能包覆砂粒而作为可能的抑制剂。金属的流动要尽可能平滑以减少氧化。由于镁的密度低,浇口和冒口辅助填充模子的压头较小,砂子要有渗透性,模子必须很好地开排气孔以排出空气。镁的体积热容量较低,所以需要有大的冒口以维持较热金属的熔池,因此需要为这些冒口和进料系统供应合金,浇铸的金属对实际铸件的体积比对镁合金来说可能平均高达4:1。
硬模铸造过程和砂型铸造相同,但是较快的凝固速率会得到较细的晶粒以及较高的力学性能。压铸件既用热室法也用冷室法生产。在这里镁的体积热容量小是一个优点。因为与锌或铝相比,镁从金属模具吸收的热较少,因而有可能提高生产率。锌、铝和镁冷室压铸相对速率各为1.0:1.6:1.9。
由于凝固过程中生成的氧化皮具有一定的抗氧化作用,尤其是添加了微量铍的合金表面的保护性能更好,所以合金锭在后处理时不能打磨,只需用铁刷子将锭表面的毛刺去掉就可以。
2.2.1.4 镁合金型砂性能控制
镁合金的型砂要求与铝合金基本相同,但是由于镁的易氧化性,因此必须提高型砂的防燃能力。资料表明,镁合金铸造生产中使用的辅助材料有硫黄、硼酸(HBO3)、氟附加物(NH4BF4·NH4HF·NH4F)、烷基磺酸钠(RSONa)等,用以防止镁熔体在浇铸及充填铸型时发生氧化、燃烧。常在型砂中加入燃烧保护剂烷基磺酸钠3%~4%和1.5%~2.5%硼酸。型砂中也可加入2%~4%的RSONa和1.5%~2.5%的HBO3,保证在充填铸型过程中防止镁的燃烧。RSONa为开链结构化合物,加热到270℃时链会断裂分解出SO2、CO2等防护性气体。另外,能和镁熔体反应生成MgS等致密膜(致密度系数a=0.95),代替疏松的MgO膜,减缓镁熔体的氧化。HBO3受热后即脱水生成硼酐(B2O3),它与镁反应还原出硼,与镁形成致密的Mg3B2保护膜,B2O3还可与熔体表面的MgO反应,生成MgO·B2O3,它是致密的釉质保护膜,能防止镁熔体的燃烧。针对镁合金SLS覆膜砂型铸造过程中存在的局部燃烧及大量烧蚀等问题,李偲偲等提出了在SLS覆膜砂材料中添加含硼酸、碳粉及硫铁矿粉等的复合阻燃剂,并采用SLS覆膜砂型进行了镁合金铸件的快速铸造,研究了镁合金与SLS覆膜砂型砂芯之间的界面反应,并对SLS覆膜砂型的阻燃机理进行了分析。结果表明,添加复合阻燃剂SLS覆膜砂型镁合金铸件表面光滑,有金属光泽;金属液与SO2/CO2气体之间起皱后体系能量增加,变形不能够自发进行,氧化膜不易起皱破裂,表面组织致密。
氟附加物与镁熔体接触后即分解出HF、NH3等防护性气体,并在镁熔体表面形成致密的MgF2及Mg3B2保护膜,具有良好的防护作用,但由于产生大量的氟化物气体,这些有害气体严重损害人们的身体健康,腐蚀厂房设备,污染环境,近年来已基本被烷基磺酸钠所取代。
镁合金熔体一般不用石墨坩埚或耐火材料炉衬(坩埚),因为SiO2与镁生成不溶于镁熔体的Mg2Si,是镁合金中最有害的杂质,降低合金的塑性及抗腐蚀性,故炉料中的砂料必须清理干净,以防止硅进入镁熔体中,生产上一般使用铸钢或钢板焊接坩埚,因为铁在镁熔体中的溶解度极小。表2-41为两种典型湿型砂的成分及性能。
表2-41 两种典型湿型砂的成分及性能

2.2.2 永久型铸造
2.2.2.1 镁合金永久型的概念及技术标准
永久型铸造是将液态金属浇铸到金属铸型或石墨型中并依靠重力充型的一种铸造方法。这种方法用来生产具有良好表面质量的精密铸件,可制尺寸小到25mm大到1.3m的铸件。美国镁合金永久模铸件标准的说明定义了永久模铸造,它是将熔化金属在重力作用或低压作用下注入用耐用材料如铁或钢制成的模具,凝固得到金属制品的过程。在轻合金永久型的铸造中,镁合金的铸造难度较大,这是由于镁合金的结晶温度范围较宽、热容小、容易氧化等导致铸件质量很难控制。而且镁合金一般是密排六方晶体结构,冷加工困难,因而铸造镁合金在工业生产中占有很大的比重。另外,镁合金铸造中,晶粒细化的措施很少,更有必要通过金属型铸造来细化组织,提高性能。陈健美研究了热管在轻合金永久型铸造中的行为、作用、利用潜力和应用的基本形式,特别提出了一种新颖的采用热管技术制备镁合金铸管的方法以及一种轻金属半固态铸锭制备的改进方法,阐明了高温热管技术在永久型铸造冷却控制中的应用价值。
(1)取样及对合金的成分要求 铸件应具有均匀的质量和条件,避免裂纹和其他有害的缺陷,在检测前铸件应用吹砂或其他可行的方法清理干净。若在铸件浇铸时取样,在每907kg的金属液中至少取一个试样。当从铸件或测试棒上取样时,除了要求的每个铸件取一个试样外,在船运的产品中还应该每907kg取一个代表试样。决定化学成分的试样的取法应与下面的方法中的一种保持一致,即化学分析试样应该通过钻、锯、磨、车削或刨削等方式从材料中取下来,通过上述方式取得的试样质量不少于75g。在对光谱化学分析法或其他分析法取样时,应采用适合于材料分析形式和类型的方法。
材料的化学成分应与表2-42所列合金化学成分保持一致。当铸件浇铸时,通过分析试样决定其化学成分的一致性,或分析从完成的产品中取得的试样决定化学成分的一致性。如果在制造的过程中已经决定了产品的化学成分,那么就没有必要对成品取样和分析了。
表2-42 永久型铸件的合金化学成分的上下限

(2)合金的力学性能要求 拉伸要求试样的个数为每907kg浇包中至少取一个拉伸试样来代表同一浇包浇出的铸件。如果铸件要求热处理,试样应随相同合金的成品铸件进行同样的回火热处理,然后,测试试样,判断试样的热处理是否与相应的浇包中的金属热处理特性相一致。每一热处理炉燃烧室内至少包括一个与产品同时浇铸的拉伸试样,这样的试样应与铸件有相同的合金和相同的回火热处理。最后,通过测试这些试样来判断给定炉内热处理工件的质量。如果从铸件上取测试棒,取测试棒的数量和位置应事先在供应商和用户之间达成一致意见。表2-43中的性能极限是基于对每个测试棒的铸造张力数据的分析基础上的,并且建立在至少有99%的数据基础上。拉伸试样应用永久模独立铸出,测试前试样不应机加工,除了给测试机的夹具留夹紧末端,用这种方式以确保轴向载荷。假如,一些拉伸试样不适合拉伸机或出现了缺陷,应该报废这些试样,用另外的试样来代替,而这些另外试样与报废的试样是经过同样的热处理或是从同一包中浇出来的。
表2-43 永久型铸件的拉伸要求

注:c为不要求。
表2-44中给出了不同合金的最小屈服强度值,同时给出了根据弹性模量的“加载拉伸法”的相应单元变形,E=44800MPa。表2-45所示的典型布氏硬度数值可以通过使用10mm球和500kgf的砝码来得到,表中数据仅供参考。在铸件的船运和储存过程中,铬酸洗可提供适当的保护,防止腐蚀和生锈。酸洗后,铸件将变为灰色或黄色,这些取决于合金和条件。含有金属添加剂的铸件不推荐用铬酸洗,这样的铸件装船前不应表面处理或涂润滑化合物来保护。
表2-44 加载拉伸法实验数据和典型布氏硬度

表2-45 镁合金的性能和特性

2.2.2.2 镁合金永久型铸造工艺的特点
镁合金所用的金属型材料可采用铸铁或铸钢。在金属型铸造的合金中,沿铸型散热方向生长的枝晶具有合适的生长速率。因此,铸件的力学性能良好(尤其是伸长率)。金属型的类型很多,按分型面的位置划分有整体金属型、水平分型金属型、垂直分型金属型及多面金属型。整体金属型无分型面,适用于外形简单、有较大斜度的中小铸件。水平分型金属型由两半型扣合而成。这种铸型在生产中用的较为广泛。垂直分型金属型由垂直的两半型组成。这种铸型排气容易,散热性好,开闭方便,适用于轴线对称形状的铸件。
金属型铸造时,根据所用涂料,预热铸型至一定温度;给铸型涂刷涂料(最好用喷枪);铸型加热至230℃(有时到300℃),若低于该温度,就不能保证枝晶的正常生长;根据铸件种类,在高于液相线100~150℃的温度下浇铸;浇铸完后,向冒口中注入高温金属使冒口和补缩通道最后凝固。这样就可以得到较好的顺序凝固。必要时,还可以重新加热冒口;冒口凝固后即可脱模。在上述铸造过程中,特别要注意以下几个方面。
(1)涂料 镁合金涂料的配制方法:将硼酸溶解于沸腾的水中,然后将耐火粉料用热水搅拌成糊状,再将硼酸水加入,仔细搅拌均匀,冷却到30℃,再加入水玻璃。
(2)金属型预热 金属型预热的目的是避免液态金属因冷却速度过快而造成的气孔、冷隔、浇不足及缩孔等缺陷,另外也有保护铸型、延长使用寿命的作用。对于一般铸件,铸型预热温度为200~350℃,工作温度为200~350℃;对于薄壁复杂件,预热温度为300~400℃,工作温度为300~400℃;对于金属芯,预热温度为300~400℃,工作温度为300~400℃。
(3)充型时间及浇铸温度 镁合金的充填时间通常与铝的充填时间基本相同。镁合金的浇铸温度为720~780℃,在个别情况下可低于720℃。
(4)铸件脱型温度及时间 由于金属型无退让性及大量吸热,因而铸件可早些从铸型中取出。如果停留时间过长,铸件会因产生的铸造应力而开裂。镁合金在浇冒口基本凝固完毕,即可抽芯开型。
镁合金金属型铸造斜度对外表面为不小于1°,对内表面不小于2°。镁合金金属型可采用蛇形浇铸系统,其浇道截面尺寸与直浇道高度见表2-46。镁合金金属型铸件的最小壁厚为25mm。铸件的内孔尺寸为6~8mm,不穿透孔的深度为9~12mm,穿孔深度为12~20mm。镁合金的冒口尽量使用明冒口,高度不小于60mm。
表2-46 镁合金金属型蛇形浇铸系统的直浇道高度

2.2.3 镁-铝合金的石墨型铸造
在石墨型铸造的合金中,石墨型铸型预热温度不像金属型那样高,因此铸造锌-铝合金中组织的枝晶并不很大。采用石墨砂型铸造镁合金,可在不加防燃保护剂的条件下获得质量优良的铸件。有人为了探讨石墨砂型铸造镁合金的防燃保护机理,对石墨砂型铸造镁合金ZM-5的表面保护膜进行了研究。试验设备为英国Kratos公司生产的XSAM800型X射线光电子能谱仪,光电子激发源是MgKa X射线,光电子能量为1253.6eV。试验中考虑到氧化态镁峰在金属态镁峰所在处的贡献比较小,可以根据金属态镁峰位置处总的镁的谱峰的高度,将镁的谱峰中金属态镁原子和氧化态镁原子的贡献解叠开来。为此用基体得到的镁峰作为标准的金属态镁峰并求出它的面积(即积分强度)与峰高之比。将镁的总谱峰中金属态峰所在处的高度乘以上述标准金属态镁的面积与峰高比,即得总的镁2P谱峰中金属态镁峰的贡献,总的镁2P峰减去求得的金属态镁峰的贡献,余下的即为氧化态镁的贡献。试验结果表明,镁合金的表面氧化膜的组成结构划分为表面层、中间层和过渡层,表面层是Mg(OH)2及MgO,中间层主要是MgO,而过渡层含有大量的金属Mg和少量的MgO。表面层和中间层氧化得较为完全,统称为氧化膜的阻挡层。这一层的厚度可看作保护膜的实际厚度。石墨砂型铸造镁合金时,表面氧化膜中由于C原子的渗入而形成MgO+C复合膜,其致密度较好,具有良好的防燃保护性能。
石墨型的设计原则与金属型基本相同。石墨型材料的质量对石墨型铸造极为重要,因此要求石墨型的材质应具有高的力学性能及耐磨损性;密度要高、气孔要少,从而使铸型具有良好的导热性,表面状态良好(通常铸型表面要抛磨)。
浇铸温度应高于液相线50℃,但是不应超过液相线150℃。铸型上涂一层湿石墨粉,以免金属向显微孔隙中渗入。用涂料涂覆浇道和冒口,以保证铸件的顺序凝固。这种铸造工艺适用于生产中型铸件。石墨型的密度较小,可在小型自动浇铸机上应用,生产效率明显高于非自动化金属型铸造。
2.2.4 铸型净化技术
镁合金的复合净化技术是发展的方向。有人在溶剂和吹氩气的基础上增加了合金液的过滤环节。使用的过滤元件为铁丝网和多孔陶瓷块。合金的浇铸温度在720~730℃范围。试验表明,经过复合净化处理,AZ91的抗拉强度和伸长率分别为206MPa和5.21%。他们分析认为,对金属熔体进行过滤有三方面的作用:一是过滤器上的空隙能阻挡夹杂物颗粒;二是能使细小的颗粒沉淀于过滤器内部的边角处;三是过滤器骨架具有较大的比表面积,能够吸附微细的杂质。