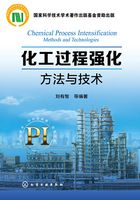
第5章 静态混合器
5.1 概述
静态混合器(Static Mixer)是20世纪70年代才得到工业性开发的一种先进的单元设备。最早的静态混合器由荷兰的研究者发明(荷兰专利号185539),其设计的思路为:利用特殊管路结构实现流体的“分割-位置移动-重新汇合”过程。此后,静态混合器的开发、研究都继承了这一基本思路。1970年,欧洲的Achema化学工程展览会展出了第一台Kenics型静态混合器[1]。1973年,工业化的Sulzer型静态混合器的问世标志着静态混合器的研究、发展进入了新纪元。我国从80年代起逐步对静态混合器进行了研究,并研发了SK、SX、SV等系列静态混合器,在液-液、液-气、液-固、气-气的混合、乳化、中和、吸收、萃取、反应和强化传热等单元操作中得到了研究和应用。
①液-液混合 从层流至湍流,黏度在106mPa·s的范围内的流体都能达到良好的混合。分散液滴最小径可达到1~2μm,而且大小分布均匀。
②液-气混合 静态混合器可以使液-气两相组分的相界面连续更新和充分接触,在一定条件下可以代替鼓泡塔和筛板塔。
③液-固混合 当少量固体颗粒或粉末(固体占液体体积的5%左右)与液体在湍流条件下混合,使用静态混合器,可强制固体颗粒或粉末充分分散,能达到使液体萃取或脱色的要求。
④气-气混合 可用于冷、热气体的混合以及不同气体组分的混合。
⑤强化传热 由于静态混合器增大了流体的接触面积,即提高了给热系数,一般来说对气体的冷却或加热,如果使用静态混合器,气体的给热系数可提高8倍;对于黏性液体的加热,给热系数可提高5倍;对于有大量不凝性气体存在的气体冷凝时,给热系数可提高8.5倍;对于高分子熔融体的换热可以减少管截面上的温度和黏度梯度。
5.2 静态混合器的类型
静态混合器是相对于搅拌器而言的,经过长期的发展,搅拌装置已经有了很大的改进,但仍存在着一定的缺陷,如轴封部件泄漏、存在死区、混合均匀度不高、不能连续化生产以及装置的动力消耗太大等。静态混合器是一种没有任何机械运转部件的新型高效传质设备,它是由具有一定的几何形状的混合元件有规则地排列组合并静置于管道内构成的。因其结构紧凑、维护较易、混合效率高、能耗较低而且能实现连续操作,被誉为一种“虽然非常简单,却能发挥巧妙作用”的工业设备。
随着研究的深入和应用的普及,目前静态混合器达50余种,国内最常用的有上海化工研究院开发的SV、SX、SL、SK和SH型5种,国外常用的有美国的凯尼斯型Kenics、瑞士苏尔寿公司的SMV型、SMX型、SMXL型,以及日本的东丽型(HI)等。静态混合器的种类很多,可以针对不同的物料条件以及工艺要求进行选用。表5-1列出了几种具有代表性的结构。
表5-1 静态混合器的类型


5.3 静态混合器的工作原理
当欲混合的物料流沿着管道进入静态混合器时,物料流在其自身功能的作用下,依次通过交替排列的一组左、右旋螺旋元件构成的特殊通道,被切割成很多层,而且每层都十分薄;再者,物料流在其中将彻底地连续不断地翻动,由于物料流的连续性,物料流中的任何粒子均被迫挤向管壁,而在两个螺旋元件的连接面上被迫改变旋转方向,又迫使它暂时离开管壁,随后它又会挤向管壁,这就是彻底的径向混合作用,流体自身的旋转作用在相邻组件连接处的接口上亦会发生,这种完善的径向环流混合作用,使物料获得混合均匀的目的。正由于这种作用的结果,消除了物料流在径向上的温度、密度、黏度和组分上的差异。
静态混合器的工作原理,就是让流体借助自身动能,在管线中流动冲击各种类型板元件,增加流体层流运动的速度梯度或形成湍流,层流时是“分割-位置移动-重新汇合”,湍流时,流体除上述三种情况外,还会在断面方向产生剧烈的涡流,有很强的剪切力作用于流体,流体在管路中受到流道形状和截面变化等约束,不断进行分流切割、合流剪切以及旋转搅动等运动,最终达到流体的充分混合[2]。
5.4 静态混合器流体力学特性
静态混合器的流体力学特性,主要包括流体速度场、湍动能分布以及压降,分析方法有实验研究和数值模拟,本节将从上述两方面分析其流体力学特性。
5.4.1 静态混合器流体力学实验研究
静态混合器的流体力学测试主要采用热线热膜风速(HWA)技术和激光测量技术。其中,激光测量技术又包括激光多普勒(LDA)技术、相位激光多普勒(PDA)技术、激光粒子成像(PIV)技术以及激光诱导荧光(LIF)技术等。科研工作者采用不同技术对静态混合器进行了流体力学实验研究。
Shaffiq[3]应用LDA技术测得了L/D=0.8、1.0、1.5的Kenics混合器在低雷诺数条件下的流场数据,并给出了轴向速度和周向速度侧形。结果表明:进入混合器的流动侧形为稳定的、抛物线速度场,进口效应不可能导致涡旋。Byrde和Sawley[4]在雷诺数Re=100的条件下从混合元件的扭转角度对混合效率的影响出发利用CFD进行优化,数值模拟实验表明螺旋混合元件的扭曲角度180°时较优。费维扬等利用LDA技术研究了50mm内径的Kenics型混合器的流场、压力降和液滴平均直径。结果显示:Kenics型混合器在中心部位切向速度较大,而在靠近管壁处,切向速度迅速下降;当流量较低时,出口轴向速度脉动值随流量增加得很快,而当流量大于7.7m3/h后增加的速度变慢。转折点处的流速约为1m/s;当混合单元数大于4时,静态混合器出口速度脉动值基本上不再随混合单元数的增加而增加,静态混合器的设计流速对混合和液滴粉碎情况都有重要影响。对于水-油体系来讲,1m/s左右的流速(相当于约7m3/h)既能提供良好的混合,又能使液滴得到良好的粉碎,压力降也不至于太大。
Ujhidy等[5]采用PDA技术研究了卷绕通道的流体流动模式。证实了在流体层流状态下,静态混合元件中的二次流的存在。对于Ar=1.0和Ar=1.5的螺旋元件,发生二次流时,Re分别为20和50。螺旋的表面影响了速度的空间分布,而元件的扭转主要影响二次流的结构。
肖世新等[6]用PIV方法测量了改进的Ross型静态混合器轴截面混合单元出口流体轴向速度侧形,验证了模拟结果的正确性。赵建华等利用PIV技术获得了静态混合器出口处的流场分布,同时与计算流体力学计算结果进行了比较。
Wadley等[7]用LIF测量了Kenics、HEV和SMX三种尺寸相同的混合器的流场,用标准化偏差量化混合效果。得到的结论是:混合质量是一个与进料位置、混合长度、流形、混合器种类相关的参数;当混合器很短时,进料对混合质量有显著的影响;总的来说,增加混合长度会提高混合质量,一般1~2个混合元件后,混合已经很充分了;在过渡区,Re增加混合质量提高,直到混合质量达到一个定值为止。
5.4.2 流体力学数值模拟
Kenics静态混合器是数值模拟中研究最多的一类混合器,其数值模拟早期是在螺旋坐标中求解N-S方程,以此获得流场分布。Arimond和Erwin[8,9]求解了控制方程,主要通过示踪剂粒子来获得模拟粒子在混合器内的流动轨迹,并且通过优化混合元件的扭转角来获得较合理的结果,但由于条件的限制,他们只计算了二维的简单情况。1993年,Bakker[10]将静态混合器的流场计算发展为三维模拟。同时,随着计算机硬件的发展和CFD方法的不断进步,静态混合器的流场模拟结果更加合理,在这方面研究最多的是Hobbs和Muzzio等[11-14]。模拟将混合器分成三段:进口段由空管和前两个元件组成,出口段由后两个元件及其后的空管组成,中间段由第三和第四个元件组成。结果显示:流场与混合器的结构相类似呈周期性变化,任意长度的混合器都可以看成是由这样的三段组成,只不过是把中间段的两个元件任意重复而已。
Vimal和Vaibhav等[15]采用CFD模拟方法模拟研究了Kenics静态混合器在较宽的Re(1~25000)条件下的流动模式和混合行为。结果显示:混合元件的中心处形成强制涡旋,在接近壁面处形成自由涡旋;在元件与元件交接的地方,流动受到影响的区域占整个元件长度的30%,其余的范围内流动充分发展。Byrde和Sawley[16,4]应用对流欧拉法求解雷诺平均方程,在Re=100条件下模拟了SK型静态混合器(L/D=1.5,6个单元结构)流动。结果显示:标准的Kenics静态混合器在扭转角为180°时性能最优。当以第四个混合元件的出口为研究对象,他们指出流体的旋转方向与混合元件的局部螺旋方向相反,同时在每个元件的进料口发现有二次涡。
除了对Kenics型静态混合器的研究外,Fourcade等[17]利用数值模拟的方法对比研究了SMX型和Kenics型静态混合器在层流流动时的混合情况,相同的能量输入,SMX型比Kenics型的混合效果更好。Lang和Drtina[18]对SMV型静态混合器中流体流动和混合过程进行CFD模拟,认为混合器结构形成的旋涡是流体混合的主要推动力。Regner等[19]应用CFD软件Fluent 6.1描述两种商业用的静态混合器。认为:混合元件的曲率引起了混合元件交叉口的二次流,容易产生二次流的地方存在于流体改变方向的位置;由于Lightnin型的中间有边界,所以旋涡强度高于KM型;对于长径比为1.5的混合器,发现涡旋形成时的Re数为10。张晓露等采用Fluent分别计算了Kenics型静态混合器和GK型静态混合器内的流场,GK型静态混合器的湍流强度低于SK型,压力降是SK型的55.4%~57.9%,但两者的传热膜系数相近,从而得出GK型具有较高的综合性能的结论。
5.4.3 静态混合器的压降
张春梅等在湍流流体不可压缩的假设前提下,利用实验数据对理论关联式进行修正得出流动摩擦系数与Re-0.25呈线性关系。Kumar等[15]对直径为0.0254m、长径比为1.5的Kenics静态混合器进行数值模拟,回归得到适用于Re=1~25000压力降经验关联式;对比实验结果,发现混合器特征元件的压力降随着流体雷诺数的增加而增加;在低雷诺数下(1≤Re≤1000),CFD模拟得到的压力降数值与Joshia等[20]的实验结果相吻合;在更高的雷诺数下,采用k-ω湍流模型得出的压力降数值介于Berkman和Calabrese[21]的实验结果与上述实验结果之间。Etchells[22]和禹言芳等[23]综述了近几年Kenics型静态混合器的特点和工作原理,总结出了压力降的计算公式(见表5-2)。
表5-2 Kenics型静态混合器压降经验公式

考虑到摩擦因素的影响,Song和Han[24]运用CFD软件标准k-ε湍流模型对SK静态混合器(结构类似Kenics型)内的流场进行数值模拟,并将混合器流动阻力影响因素之间的联系简化为摩擦系数(f)与雷诺数(Re)和混合元件长径比(Ar=L/D)之间的关系(表5-3)与文献提供特定长径比Ar和操作条件的摩擦系数f相比吻合较好,同时将适用范围推广到Re=0.1~1×105。费维扬等曾研究了混合元件数对SK型静态混合器出口速度脉动值的影响。SK型静态混合器压降公式如表5-3所示。
表5-3 SK型静态混合器压降公式

5.5 静态混合器强化混合-反应性能
静态混合器内流体的混合包括层流混合和湍流混合。混合过程具体表现为流团/颗粒破碎、条纹厚度变化和组分界面面积改变。层流混合主要靠流体的“分割-位移-汇合”过程,层流过程中,流体不断被分割,流体厚度不断变小,同时在流动过程受到剪切、拉伸以及旋转作用,汇合后进行扩散传质;而湍流混合比较复杂,按照混合理论可以分为宏观混合(Macromixing)、介观混合(Mesomixing)以及微观混合(Micromixing),如图5-1所示[15]。微观混合是分子尺度的混合,直接影响反应结果。对于液相快速反应过程往往对应较短的反应时间,混合时间要求达到毫秒级甚至更低才能实现均相反应过程,提高产物的质量。特别是对沉淀反应、聚合反应等过程,提高混合效率能够实现均相成核,不仅避免了副产物的产生,而且所得产品粒径分布以及纯度都会极大地提升。因此,研究静态混合器的混合过程有助于发展高效的反应过程强化设备。

图5-1 混合过程示意图
国内外研究者对于静态混合器的混合-反应过程做了大量的研究。例如,Fourcade等[17]在层流条件下基于Ottino微混合理论,提出一种计算Kenics型静态混合器内条纹平均稀释速率的新方法,其数值计算结果与LIF实验数据吻合较好。除了采用物理方法研究混合外,许多研究者还采用化学探针来研究静态混合器的微观混合。Fang等[25]在含有6对L/D=1.03、D=0.08m的Kenics静态混合器内,通过碘化物-碘酸盐平行竞争反应体系(图5-2),在Re=66~1020范围内,定量评价混合器内的微观混合效率,研究发现无论是层流还是湍流,Kenics静态混合器相对于空管都可以显著地提高混合效果;在相同的功率输出条件下,Kenics静态混合器相对连续流搅拌釜反应器能够达到更高的混合效率。

图5-2 碘化物-碘酸盐平行竞争反应分析微观混合效率
相对于实验研究来说,对静态混合器的数值计算方面的研究方向要广泛得多。Hobbs等[12]通过研究相邻混合元件结合处流体横截面的示踪粒子的轨迹线,定性地描述了其混合过程特征,同时建立了流体混合状态与流经混合器的轴向距离之间的方程,定量描述了混合性能。研究结果说明Kenics静态混合器的混合过程是一种无序混合。Elizabeth和Mickaily-Huber等[26]对SMRX型静态混合器进行了数值模拟,发现混合效果是一个关于管道内交叉角的函数,认为交叉角为90°时混合效果较优,压力损失与速度成正比,而且随着交叉角的增长而增长。
5.6 静态混合器强化传热性能
在空管管壳式换热器中,管内流体流动的速度沿径向非均匀分布,靠近管壁处的速度很小,可形成层流层,而在对流传热时,热阻集中在层流层。流体的黏度越大,在相同的流速情况下,层流层越厚。流体在含有静态混合器的换热器管内与在空管内的流动情况大不相同。混合元件对流体的分割和转向作用,使流动边界层沿轴向处于不断形成和不断破坏之中,从而导致边界层厚度变薄,传热、传质性能得以强化。此外,由于静态混合元件的径向混合作用,大大减小了管内层流层的厚度,甚至破坏层流层的形成。流体由静态混合元件的导向不断从管中心流向管壁,又从管壁流向管中心。由于相邻的静态混合件可轴向错开一定的角度,使管内流体充分混合,消除了管内流体的温度梯度。同时,对于非拆卸式静态混合元件,由于静态混合元件的边缘与管壁直接接触,静态混合元件就起到翅片的作用,这样大大增加了传热面积,从而强化传热,其传热系数是空管传热系数的3~7倍以上。
5.6.1 传热因子Nu
通常,对于换热器来说,最关键的参数是Nusselt数(Nu),静态混合器的Nu关联式见式(5-1):
(5-1)
式中,Pr是平均温度下的普朗特数;Prw是壁面温度下的普朗特数。
对于不同的静态混合器,由于内部元件的差异,传热因子的关联式也有不同,表5-4中列出了部分静态混合器的Nu关联式。
表5-4 常见静态混合器的Nu关联式

表中所示的关联式中都考虑到长径比L/D这一项,表明流体在壁面的更新是有限的,温度边界层在静态混合器处没有得到充分发展。根据经验,采用Kenics静态混合器,传热系数增大2~3倍,采用SMX静态混合器后,传热系数约增大5倍。另外,Cybulski和Werner[27]给出了预测加入静态混合器管路的Nu数的普遍关联式如式(5-2):
(5-2)
式中,Nu0是纯导热因子;Pr为Prandtl数,定义式如下:
(5-3)
Azer和Lin[28]定义了一个新的参数H,同时考虑加入静态混合器后传热和压降的变化,其定义式如下:
(5-4)
式中,Qheat指的是热通量;Aq是传热面积。结果表明,H值随Re的增加而降低,主要原因是在湍流情况下,压降随Re的增加急剧增大。静态混合器在强制对流,单相流动或过冷(欠热)沸腾,泡核沸腾场合的应用非常有效,因为加入静态混合器后传热得到强化,而压降增加得较少。在低Re下,单位压降所带来的热通量是随着Re数增大而增加的。
还有学者提出了一种表面更新理论来表征管内出现的冷凝或汽化现象,Nu关联式如式(5-5)所示:
(5-5)
式中,下标m,w分别代表气-液混合物和壁面特性;Hf为潜热;Hs为显热;x为冷凝器出口的气相分率;cp为比热容;Tb为管壁温度;D、L分别表示管径、管长。
5.6.2 传质系数Ka
通常,传质系数Ka可以用下式计算:
(5-6)
式中,N为传质速率,mol/h;V为萃取器的体积,L;Δ是平均推动力,mol/L;Ka是传质系数。
静态混合器的传质性能往往与流体线速度、混合元件数目、液滴尺寸等相关。许多研究者将静态混合器的空管线速度与传质系数关联。叶楚宝[29]指出:D0=19mm时,KNS型静态混合器传质系数Ka的关联式:
(5-7)
与空管比较,表观线速度ω=0.3~0.9m/s时,传质系数大约有2~10倍的强化;但随着线速度的降低,传质系数逐渐接近空管。他们以蒸馏水为萃取剂,从苯甲酸煤油溶液里萃取苯甲酸,通过分析流体线速度u对传质系数的影响,得到以下几种静态混合器的Ka经验关联式(见表5-5)。
表5-5 静态混合器Ka经验关联式

F.Steriff将传质系数Ka与扩散系数Dc,液滴平均直径Ds,表观线速度ω和黏度μ联系起来:
连续相一侧的传质分系数为:
(5-8)
分散相一侧的传质分系数为:
(5-9)
对于甲苯/苯甲酸/水体系,用SMV型静态混合器进行试验,测得k1=0.32,k2=2.98×10-4。井田惠三等对Hi型静态混合器进行试验,用水作为萃取剂,从煤油溶液中萃取安息香酸,测定结果表明,在单元数3~10的范围内,Ka∝n0.18(n是单元数)。使用5个单元的Hi型,Ka约是空管的7倍。
5.7 静态混合器的应用
5.7.1 静态混合器在制备纳米药物载体中的应用
Dong等采用静态混合器连续制备纳米壳聚糖(CS),实验流程以及静态混合器结构如图5-3所示。CS纳米颗粒受到CS浓度、流量、CS与TPP的体积比等过程参数的影响。结果表明:增大CS∶TPP溶液的流量,降低CS浓度或者降低CS∶TPP的体积比都能够减小产物粒径;通过静态混合技术可以实现CS纳米颗粒的可控制备,所得产物粒径范围为152~376nm。此外,Dong等还利用上述的静态混合器成功合成固态脂质体。通过控制脂质体溶液浓度以及负载药的输入量可以实现药物的可控制备;在流量为25~100mL/min,脂质体浓度为25mg/mL条件下,该工艺的产量可达37.5~150g/h,所得产物粒径为200nm。

图5-3 静态混合器制备纳米壳聚糖
5.7.2 静态混合器在超细粉体制备中的应用
钱刚等将静态混合器应用于ZrO2纳米晶微粉的制备,流程如图5-4所示。物料流的流动状态、静态混合器单元数、反应物浓度、流量等都会对粉末性能造成影响。由于静态混合器可消除反应器内物料在径向上的浓度、温度等差别,物料在其中的流动状态近似于活塞流;反应物浓度越大,越能够减小粉末的一次粒径,但团聚粒径变大;而增大反应物流量则有利于生成粒径较小的粒子。另外,Douroumis等[30]利用静态混合器实现流体的快速微观混合以合成超细OXC微粉,产品平均粒径大约为2μm,与搅拌槽混合器相比粒径分布更窄。

图5-4 静态混合器制备ZrO2装置流程
5.7.3 静态混合器在硝化反应中的应用
沈阳化工大学与辽宁庆阳化工有限公司合作开发了一种绝热硝化工艺,即采用静态混合器的管道式绝热硝化工艺。管道式绝热硝化工艺与有搅拌装置的釜式串联绝热硝化工艺相比,具有很明显的节能特点。管道式生产装置不需要搅拌设备,流体在混合元件间流动受到的流体阻力也很小,而釜式反应器内要设置搅拌设施,生产时要额外消耗部分电能,所以管道式绝热硝化工艺与釜式串联绝热硝化工艺相比更节能。另外,管道式绝热硝化工艺物料混合均匀、反应进行彻底、原料利用率高、反应热容易移走,消除了因物料混合不均而导致温度上升的危险,而有搅拌装置的釜式绝热硝化工艺硝化反应不连续,物料要在反应釜中停留一段时间,一旦搅拌器发生故障,反应器内物料温度便会急剧上升,容易发生危险。在不扩建厂房的条件下,使硝化系统的生产能力由原来的6000t/a提高到12000t/a。
王阳等[31]利用静态混合管式绝热反应器制备硝基甲苯,此工艺与传统硝化工艺相比,静态混合管式绝热硝化工艺具有反应时间短、反应条件温和、安全性高、全密闭无污染的特点,反应热可以用来提浓混酸,分离产品,使能量得到有效利用。
5.7.4 静态混合器在环保领域的应用[32]
(1)絮凝剂与废水的混合
上海怡中纺织实业公司纺织废水与无机絮凝剂(碱式氯化铝)的混合过程采用SVL型静态混合器,取得了预期的效果。为了确保出水水质,经生化处理的废水需要加入碱式氯化铝后再一次去沉淀池进行沉降。废水与絮凝剂混合均匀与否,直接影响到凝聚过程,从而影响沉淀后排放出的水质。该公司沉淀后的排放水达到工业废水排放标准,即化学需氧量COD≤100mg/L,生物需氧量BOD≤30mg/L,悬浮物质SS≤70mg/L,pH=6~9。
上海普林电路板公司采用SVL型静态混合器进行有机絮凝剂和电路板废水的混合。废水流量为40m3/h,聚丙烯酰胺水溶液的流量为23L/h,用计量泵加入,两者流量比为1739∶1。流量相差如此之大的流体混合一般都比较困难,采用了静态混合器作为混合设备,混合效果很好,与未采用静态混合器相比,颗粒沉降速度明显加快,确保了沉淀池排放水的水质。
(2)含酚废水的处理
上海染化二厂生产碳酸二苯酯(OPC)过程中产生大量的含酚污水,平均每天有27t含酚量在2000~5000mg/L的废水产生,需用N-503萃取废水中的酚。原采用脉冲萃取塔,但处理效果差,特别是运转一定时间后塔内阻力增大,严重影响处理能力,致使操作不稳定。在原脉冲塔污水进口区接装SVL-50型静态混合器后,排出污水的含酚量大大下降,达到工业排放标准,处理能力也得到提高,二者对比见表5-6。
表5-6 静态混合器和脉冲萃取塔的对比

相同工艺在河南四通精细化工有限公司、上海高桥石化公司化工厂、上海中华化工厂、浙江建德更楼化工厂等得到了应用。
(3)含粗胺废水的处理
某农药化工有限公司在甲胺磷生产过程中产生粗胺废水,废水中粗胺含量2.5%~5%,用纯苯作萃取剂进行处理。原来使用脉冲萃取塔,操作中发现顶部分不清,后来增加一个分离槽后效果仍不理想,且噪声大。采用SVL型静态混合器后,问题得到解决,噪声消除,操作稳定。
(4)用作中和反应器
九江化工厂盐水中和过程采用SVL-200型静态混合器。原来用曲径槽,由于两种液体的流量相差较大,所以难以达到混合均匀,往往因混合不均匀而造成中和不均匀,致使反应器出口各点的pH值相差较大。采用静态混合器作混合设备后情况大大改变,比较见表5-7。
表5-7 曲径槽出口处与静态混合器出口处pH值比较

(5)用作曝气装置
北京焦化厂在废水的生化处理脱酚中,原来采用穿孔管鼓风曝气,实践证明穿孔管的最大缺点是布气孔易堵、操作不稳定,此外能耗较大、效率较低。改用静态混合式曝气器后,不仅解决了穿孔管布气孔堵塞造成的操作不稳定,而且可以节约一台30kW的鼓风机,动力消耗降低15%~25%。
(6)用于废气处理
兰州炼油化工总厂引进的硫化烷基酚钙装置,原采用填料塔二级串联吸收流程处理尾气中硫化氢,使用氢氧化钠水溶液作为吸收剂。第一级吸收塔处理的是高浓度硫化氢气体,塔内填料在硫化氢和碱的腐蚀下很快粉化,不仅半年左右就需更换填料,而且粉化物随碱液循环造成机泵磨损。后采用SVL-300型静态混合器替代原来的1000mm×10000mm第一级吸收填料塔。静态混合器的实际吸收率超过了设计值,达到99%以上。有关数据参见表5-8。
表5-8 静态混合器的吸收效率

5.7.5 静态混合器在混合油精炼工艺中的应用
在混合油精炼工艺中,油-酸混合、油-碱混合采用静态混合反应器,由于酸碱在混合油中分散效果好于动态反应器,混合反应时间可比动态搅拌反应器节省反应时间75%。以600t/d混合油精炼生产线作为研究对象,生产线可节省动力67.5kW,每天减少电耗907.2kW·h,以每年生产300d计,每年可减少电耗27.2×104kW·h,运行成本大大降低。由于减少了电机动力,相应的电气配置费用减少约4万元,每年可节省维修费用约2万元,维修简单、使用寿命长。静态混合反应器使用前后的生产运行指标见表5-9。
表5-9 静态混合反应和动态混合反应的对比

南充炼油厂在异丁醇脱沥青装置上使用静态混合器后,装置加工能力由原来的62t/d提高到85t/d,脱沥青油回收率也提高了2.9%,产品合格率由原来的95.4%提高到99.7%,溶剂比下降了0.7~0.8。
5.7.6 静态混合器在酮还原反应中的应用
德国Merck公司在生产某种精细化学品过程中把Grignard试剂用于酮还原反应。此反应为强放热反应,生产过程中需要导出反应热,反应时间较长。Merck公司建成了一套全自动连续生产中试装置,由五个小型混合器并联操作,中试生产的产率高于实际间歇式生产产率20%,反应时间由原来的5h缩短至10s内。
5.7.7 静态混合器在气液混合中的应用
Dow Corning公司采用填料塔进行气液反应来生产一种关键化工产品,由于气体在填料塔中分散不均,导致填料塔的有些部位过热,反应过程中生成一种胶状的副产物,这种副产物严重影响催化剂的性能。因此,2~3周必须关闭一次设备来进行催化剂更换。并且,当气体流量超过272kg/h后,反应设备不能稳定操作,限制了设备生产能力。该公司与BHR有限公司合作经过技术改造后,仅投资2万美元,使反应的气体和液体首先经过一个静态混合器,然后再进入填料塔进行反应,设备生产能力提高了42%,同时彻底消除了胶状副产物,明显地增加了催化剂的寿命。
5.7.8 静态混合器在脱硫中的应用
齐鲁石化炼油厂原采用填料塔来脱除硫醇,但处理能力低、压力降大,抽提率不高,硫醇含量一般在15mg/kg左右,甚至能达到30~50mg/kg,该厂使用SK型静态混合器对填料塔进行技术改造,改造后精制油的硫醇含量降至5.98mg/kg,满足了生产要求;塔河油田在外输首站原有输油流程上安装静态混合器,对加注脱硫剂和原油进行强制混合,外输油的H2S含量由原来的25~30mg/kg下降到15mg/kg以内,脱硫剂的配比度也由原来的1.5‰~2‰下降到1‰以内,极大地降低了脱硫剂的成本。
5.8 新型静态混合器
到目前为止,包括Kenics、SMX、SMV、SMXL、SH等典型的静态混合器在内,世界上已有上百种静态混合器的专利,其中有相当一部分已实现商业化。
实验方法与数值模拟的发展不断促进静态混合器的研发,研究的尺度也由原来的宏观尺度过渡到微观尺度。通过对静态混合器混合机理的不断深入研究,人们发展了各种各样的新型静态混合器,能够适用于各类实际生产活动。同时,随着化工生产要求的提高,单一的结构形式的静态混合器已经不能满足需求,这进一步促进了各类新型设备的发展,特别是开发复合型静态反应器,将会是静态混合器的发展趋势。
5.8.1 微型静态混合器
随着微加工技术的发展与应用,微型化成为了化工发展的新方向。与常规静态混合器相比,微型静态混合器主要用作生物化学分析仪器的微传感器,以及用于生物芯片和微量化学分析与检测系统中的不同检体、不同试剂之间的混合;还用于药物的快速混合和微量注射;在第二代能源系统中的微燃烧器和微燃气透平等方面,微混合器也有着广阔的应用前景。Bertsch等[33]通过微加工技术构造了3D型微型静态混合器,如图5-5所示。两种微混合器分别采用了交叉和螺旋的内部结构,研究表明:交叉型微结构(Re=12)在连接处形成了复杂的梯度分布,而螺旋型微结构则出现了明显的入口和出口效应;通过粒子轨迹可以判断出交叉型结构能够促进流体分割/重新汇合的过程,因此末端流体分散性明显提高;相反螺旋型结构使流体不断伸长折叠,导致混合效率降低。

图5-5 微型静态混合器及其流动轨迹
针对微尺度混合的特点,傅新等提出了一种以玻璃湿法刻蚀加工技术为交叉导流式微型静态混合器。利用周期排列的导流块,在流场内产生剪切流和延伸流,增加不同流体间的界面面积,同时加强分子扩散作用,通过在微管道内设置周期交替的导流块,利用轴向的压力梯度产生的横向的速度分量诱发混沌对流达到实现快速而高效混合的目的。王瑞金等设计了一种新型的螺旋式微混合器。通过与直通道和蛇形通道比较发现螺旋式混合通道是一种新的加快混合效果的有效方法,在小Re数下由于流体分层而增加了流体接触面积,螺旋式混合通道显著加快了流体混合速度,其混合效果不仅比直通道有明显提高,甚至比蛇形通道还好。
5.8.2 立交盘式静态混合器
施景云等[34]提出了一种立交盘式静态混合器,该混合器由管体或筒体或塔体和至少两层立交盘组成,立交盘盘底为圆锥面,均布至少两个缺口或孔,各连接一异型短管,相邻短管间设置拱形顶盖,诸异形短管上口及拱形顶盖外缘组成的空间曲线在管体或筒体或塔体横截面的投影为直径等于管体或筒体或塔体的内径的完整圆周。该静态混合器结构简单,无流动死角,有效地消除流体状态径向差异。经过进一步发展,他们又提出了多种结构的立交盘式静态混合器,由于管内构件立交盘和螺旋片或交叉条带型等周向混合能力较强的静态混合元件,强化管壁传热,保证任意截面径向和周向流体状态均匀。图5-6为单个立交盘与一对螺旋片式静态混合元件交替排列的管道反应器。

图5-6 立交盘式静态混合/反应器
5.8.3 内循环静态反应器
内循环静态混合二甲醚流化床反应器是一种新型的内循环静态混合反应器,它属于对现有二甲醚三相浆状床反应器从结构上的改进。主要是通过在流化床反应器中下部设置带有静态混合元件的内套筒,在顶部设置轴流气液旋分器和除沫器;在环形区和反应器底部各设置一个气体分布器形成内循环导流,从而提高了液相中催化剂含量、含气率和设备单位体积处理能力,实现了气液混合均匀、气固接触充分。它主要由流化床反应器、带有静态混合元件的内套筒、轴流气液旋分器、除沫器和气体分布器等构成,具有以下突出的优点:①液相中催化剂固体含量高,有利于提高单位体积的处理能力;②气液混合均匀,液相含气率高,气固接触充分,反应效率高,同时避免了节涌和沟流;③气动内循环,浆液流动速度快,有利于取热;④静态强制混合,无运动内件,密封性要求降低,保证了设备长周期运行;⑤浆状床内带轴流分液器和除沫器,反应器高度大大降低。
5.8.4 静态催化反应器
K.A.韦尔普和A.R.卡托兰奥发明了一种由整块催化反应器和静态混合器构成的改进型设备,反应器和混合器均有入口和出口,静态混合器的出口与整块催化反应器的入口相通。他们还对整块催化反应器中实施反应的方法进行改进,其中将反应气和反应液导入整块催化反应器的入口,并使其反应,然后反应产物经整块催化反应器的出口排出。此外,可以在静态反应器中加入红外发生装置,同时结合原位FTIR、XRD、XPS、BET、质谱和连续微量反应等手段。王琳等[35]采用该静态反应器对大气颗粒物及氧化物对CS2进行多相催化,结果表明,CS2在大气颗粒物表面同样可以发生多相催化反应,生成氧硫化碳(COS)及单质硫(S),进一步深度氧化会生成CO2,并在大气颗粒物表面形成硫酸根(S),揭示城市大气中COS的来源,对CS2和COS的污染控制研究具有一定的指导意义。
5.8.5 生物静态发酵器
目前,在微生物发酵领域中,高黏度微生物发酵是一个难题。为了解决这一难题,许平和江伯英[36]设计发明了一种新型高黏度生物静态发酵器。该高黏度生物反应器由静态混合器、螺杆泵、循环管组成的外循环装置组成,并在反应罐内的底部有一个挡气板。它以静态混合代替动态混合,较好地解决了高黏度液罐内气-液混合问题。该装置具有结构简单、易拆洗、操作方便等优点,并且提高了氧传递效率、降低了能耗,提高了发酵生产率,对菌无任何生理不利影响。
5.8.6 复合型静态反应器
黄卫等[37]采用搅拌釜与静态混合器组合的高效化学反应器[图5-7(a)],主要构成部分包括搅拌釜、物料循环泵、静态混合器以及构成回路的连接管道;其中,搅拌釜、物料循环泵和静态混合器由连接管道形成闭合的回路,反应釜的上部为进料口,下部为出料口,反应釜中设有搅拌桨。该设备通过釜内搅拌和外循环两种措施强化了传质和传热,静态混合器则进一步加速了传质和传热过程,提高了设备的利用率,在最大程度上削弱了放大效应,提高了产品质量;结构简单,性能稳定可靠,经济适用。

图5-7 复合型静态反应器
1—搅拌釜;2—静态混合器;3—物料循环泵;4—Y形三通;5—静态混合器;6—螺杆
王峥等[38]开发了实用新型Y形管式反应器[图5-7(b)],具体涉及一种将两种能够发生反应液体分别快速从上部两进料口通入,并从下部出料口排出的反应容器,属于反应容器技术领域。所要解决的问题是:提供一种Y形管式反应器,在不使用电能的情况下,使液体在流过反应器的过程中能够较充分地发生反应。采用的方案为:Y形管式反应器,由正向放置Y形二通和位于Y形二通下方的管式静态混合器组成,管式静态混合器为桶形容器,其内部至少设置有一组可以分别绕顺时针和逆时针旋转的螺杆。这种新型Y形管式反应器可广泛应用到各种化工反应容器中。
参考文献
[1] John R Bourne,Eros Crivelli,Paul Rys.Chemical selectivity disguised by mass diffusion V:Mixing-disguised azo coupling reactions [J].Helvetica Chimica Acta,1977,60(8):2944-2957.
[2] Pahl M H,Mtlshelknuatz E.Static mixers and their applications [J].International Chemical Engineering,1982,22(2):197-204.
[3] Shaffiq A Jaffer.Experimental studies of static mixers and twin screw extruders[D]Hamilton:McMaster University,1998.
[4] Byrde O,Sawley M L.Optimization of a Kenics static mixer for non-creeping flow conditions[J].Chemical Engineering Journal,1999,72(2):163-169.
[5] Ujhidy A,Németh J,Szépvölgyi J.Fluid flow in tubes with helical elements[J].Chemical Engineering and Processing,2003,42(1):1-7.
[6] 肖世新,高正明,黄雄斌.牛顿流体流动的实验与数值模拟[J].过程工程学报,2006,6(1):6-10.
[7] Wadley R,Dawson M K.LIF measurement of blending in static mixers in the turbulent and transitional flow regimes[J].Chemical Engineering Science,2005,60(8):2469-2478.
[8] Arimond J,Erwin L.A simulation of a motionless mixer[J].Chemical Engineering Communication,1985,37(2):105-126.
[9] Arimond J,Erwin L.Modeling of continuous mixers in polymer processing[J].EngngInd-Trans ASME,1985,107(1):70-76.
[10] Bakker A,LaRoche R.Flow and mixing with Kenics static mixer[J].Cray Channels,1993,15(3):25-28.
[11] Hobbs D M,Muzzio F J.The Kenics static mixer:a three-dimensional chaotic flow[J].Chemical Engineering Journal,1997,67(3):53-166.
[12] Hobbs D M,Muzzio F J.Effects of injection location flow ratio and geometry on Kenics mixer Performance[J].Chemical Engineering Journal,1997,43(12):3121-3132.
[13] Hobbs D M,Muzzio F J.Reynolds number effects on laminar mixing in the Kenics static mixer[J].Chemical Engineering Journal,1998,70(2):93-104.
[14] Hobbs D M,Muzzio F J.Optimization of a static mixer using dynamical systems techniques[J].Chemical Engineering Science,1998,53(8):3199-3213.
[15] Vimal Kumar,Vaibhav Shirke,Nigam K D P.Performance of Kenics static mixer over a wide range of Reynolds number[J].Chemical Engineering Journal,2008,139(2):284-295.
[16] Byrde O,Sawley M L.Parallel computation and analysis of the flow in a static mixer[J].Computor and Fluids,1999,28(1):1-18.
[17] Eric Fourcade,Rob Wadley,Hubb C J,et al.CFD calculation of laminar striation thinning in static mixer reactor[J].Chemical Engineering Science,2001,56(23):6729-6741.
[18] Lang E,Drtina P.Numerical simulation of the fluid flow and the mixing process in a static mixer[J].Internatoinal Journal of Heat Mass Transfer,1995,38(12):2239-2250.
[19] Mårten Regner,Karin Östergren,Christian Trägårdh.Effects of geometry and flow rate on secondary flow and the mixing process in static mixers—A numerical study[J].Chemical Engineering Science,2006,61(18):6133-6141.
[20] Joshia P,Nigama K D P,Naumanb E B.The Kenics static mixer:New data and proposed correlations[J].Chem Eng J,1995,59(3):265-271.
[21] Berkman P D,Calabrese R V.Dispersion of viscous liquids by turbulent flow in a static mixer [J].AIChE J, 1988,34(4):602-609.
[22] Etchells A W,Meyer C F.mixing in pipelines:Science and practice [M] .Hoboken:John Wiley Sons Inc,2004:391.
[23] 禹言芳,王丰,孟辉波等.旋流静态混合器内瞬态流动特性研究进展[J].化工进展,2013(32):255-262.
[24] Hyun-Seob Song,Sang Phil Han.A general correlation for pressure drop in a Kenics static mixer [J].Chemical Engineering Science,2005,60(21):5696-5704.
[25] Fang J Z,Lee D J.Micromixing efficiency in static mixer [J].Chemical Engineering Science,2001,56(12):3797-3802.
[26] Elizabeth S,Mickaily-Huber T,Meyer,et al.Numerical simulations of mixing in an SMRX static mixer [J].The Chemical Engineering Journal,1996,63(2):117-126.
[27] Cybulski A,Werner K.Static mixers-criteria for applications and selection [J].International Chemical Engineering,1986,26(1):171-180.
[28] Azer N Z,Lin S T.Augmentation of forced boiling heat transfer with Kenics motionless mixers.Industrial & Engineering Chemistry [J].Process Design and Development,1980,19:246-250.
[29] 叶楚宝.五种静态混合器传质性能比较[J].化学工程,1985,1:21-26.
[30] Douroumis D,Fahr A.Enhanced dissolution of Oxcarbazepine microcrystals using a static mixer process[J].Colloids and Surfaces B:Biointerfaces,2007,59(2):208-214.
[31] 王阳,裴世红,郭瓦力等.静态混合管式绝热硝化制备——硝基甲苯工艺研究[J].精细石油化工,2014,31(1):33-38.
[32] 宋忠俊.静态混合器在环保领域的应用[J].化工装备技术,2003,5(24):9-12.
[33] Bertsch A,et al.Static micromixers based on large-scale industrial mixer geometry [J].Lab on a Chip,2001,1:56-60.
[34] 施景云,刘兆彦.新型静态混合器[P].CN 00109872.1,2001-01-03.
[35] 王琳,张峰,陈建民.CS2与大气颗粒物的多相催化反应研究[J].高等学校化学学报,2002,23(5):866-870.
[36] 许平,江伯英.一种高粘度生物反应器[P].CN 90105299.X,1991-12-11.
[37] 黄卫,陈志明,邵利等.搅拌釜与静态混合器组合的高效化学反应器[P].CN 200820036463.3,2008-06-06.
[38] 王峥,王兆华,田计青.Y型管式反应器[P].CN 200820077390.2,2008-05-28.