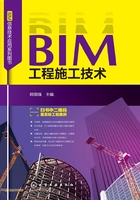
第四节 BIM钢结构工程深化设计及数字化加工
一、BIM钢结构工程深化设计
钢结构BIM三维实体建模出图深化设计的过程,其本质就是进行电脑预拼装、实现“所见即所得”的过程。首先,所有的杆件、节点连接、螺栓焊缝、混凝土梁柱等信息都通过三维实体建模进入整体模型,该三维实体模型与以后实际建造的建筑完全一致;其次,所有加工详图(包括布置图、构件图、零件图等)均是利用三视图原理投影生成,图纸中所有尺寸,包括杆件长度、断面尺寸、杆件相交角度等均是从三维实体模型上直接投影产生的。
三维实体建模出图深化设计的过程,基本可分为四个阶段,具体流程如图2-33所示,每一个深化设计阶段都将有校对人员参与,实施过程控制,由校对人员审核通过后才能出图,并进行下一阶段的工作。

图2-33 钢结构深化设计流程示意图
①根据结构施工图建立轴线布置和搭建杆件实体模型。导入AutoCAD中的单线布置,并进行相应的校核和检查,保证两套软件设计出来的构件数据理论上完全吻合,从而确保了构件定位和拼装的精度。创建轴线系统及创建、选定工程中所要用到的截面类型、几何参数。
②根据设计院图纸对模型中的杆件连接节点、构造、加工和安装工艺细节进行安装和处理。在整体模型建立后,需要对每个节点进行装配,结合工厂制作条件、运输条件,考虑现场拼装、安装方案及土建条件。
③对搭建的模型进行“碰撞校核”,并由审核人员进行整体校核、审查。所有连接节点装配完成之后,运用“碰撞校核”功能进行所有细微的碰撞校核。
④BIM模型出图。
某工程BIM钢结构深化设计如图2-34~图2-36所示。

图2-34 耳板族

图2-35 某体育场结构剖面图

图2-36 复杂节点图
又如上海世博会,某展馆的垂直承重结构由钢材制成。正面由窄体元件组成,在现场进行组装。
水平结构由木质框架元件组成,地板则由小板块拼成。内部使用木板铺面。外部正面使用富有现代气息的鳞状花纹纸塑复合板,这是一种工业再生产品。
中庭墙壁以及二层的一些墙壁由织物覆盖,并用透明织物覆盖中庭。楼梯和电梯为独立元件。全部建筑元件在进行制造的时候,就必须保证建筑建成后能被分解和再组装。
此工程采用了三维深化设计软件,把复杂纷乱的连接节点以三维的形式呈现出来,显示出所有构件之间的相互关系,通过这样的设计手段,保证了异型空间结构的三维设计,提高了工作效率和空间定位的准确性,如图2-37和图2-38所示。
又如某工程钢网架支座节点深化设计BIM模型如图2-39所示,基于BIM模型自动生成的施工图纸如图2-40所示。

图2-37 梁柱节点

图2-38 结构系统

图2-39 网架支座节点深化设计模型

图2-40 BIM模型生成网架支座深化设计施工图
完成的钢结构深化图在理论上是没有误差的,可以保证钢构件精度达到理想状态。统计选定构件的用钢量,并按照构件类别、材质、构件长度进行归并和排序,同时还输出构件数量、单重、总重及表面积等统计信息。
通过3D建模的前三个阶段,我们可以清楚地看到钢结构深化设计的过程就是参数化建模的过程,输入的参数作为函数自变量(包括杆件的尺寸、材质、坐标点、螺栓、焊缝形式、成本等)及通过一系列函数计算而成的信息和模型一起被存储起来,形成了模型数据库集,而第四个阶段正是通过数据库集输出形成的结果。可视化的模型和可结构化的参数数据库,构成了钢结构BIM,我们可以通过变更参数的方式方便地修改杆件的属性,也可以通过输出一系列标准格式(如IFC、XML、IGS、DSTV等),与其他专业的BIM进行协同,更为重要的是成为钢结构制作企业的生产和管理数据源。
采用BIM技术对钢网架复杂节点进行深化设计,提前对重要部位的安装进行动态展示、施工方案预演和比选,实现三维指导施工,从而更加直观化地传递施工意图,避免二次返工。
深化设计的数据需要为后续加工和虚拟拼装服务,包括的内容见表2-1。
表2-1 深化设计内容


图2-41 节点编号示意
二、BIM钢结构工程数字化加工
1.铸钢节点
首先,将各不相同的铸钢节点按一定的截面规格分解成标准模块,然后将标准模块按最终形状组合成模,再加以浇铸成型。这种方式创造性地改变了对应不同形式节点需加工不同模型的思路,可大大节省模型制作时间及费用,非常适合类似地下空间自然采光结构这种具有一定量化且又不尽一致的铸钢节点。
其次,采用高密度泡沫塑料压铸成标准模块,利用机器人技术进行数控切割和数控定位组合成模,大大提高了模型的制作加工精度及效率,如图2-42和图2-43所示。

图2-42 泡沫塑料块

图2-43 机器人数控切割
最后,采用熔模精铸工艺(消失模技术),提高铸件尺寸精度和表面质量。一般的砂型铸造工艺无论尺寸精度还是表面质量都达不到地下空间自然采光结构要求,且节点形状复杂,难于进行全面机械加工,选择熔模精密铸造工艺铸造节点示例,如图2-44和图2-45所示。

图2-44 节点泡沫塑料模型

图2-45 铸钢节点
钢结构实心铸钢节点各不相同,如采用传统的模型制作工艺,需加工相同数量的模型,每个模型都先需要制作一副铝模再压制成蜡模或塑料模型,通常每副铝模制作周期大约为2个星期,且只能使用一次,光模型制作时间对工程进度来说就是相当大的制约,无法满足施工要求。如采用组合成模技术,按不同截面划分12种形式,则可节省模具数量和费用,时间上也会大大节约。
2.焊接节点
焊接节点按照加工工艺主要分为两类:散板拼接焊接节点和整板弯扭组合焊接节点。
散板拼接焊接节点主要是将节点分散为中心柱体和四周牛腿两大部分,如图2-46所示,分别加工,最后组拼并焊接形成整体。首先将节点的每个牛腿按照截面特性做成矩形空心块体,然后利用机器人进行精确切割,形成基础组拼件。

图2-46 散板拼接焊接节点
在完成了节点所有基础组拼件的加工后,即需要组拼并焊接,形成完整节点。如图2-47所示,焊接主要分为两个步骤:打底焊以及后期填焊。整个过程必须保证焊接的连续性和均匀性。整板弯扭组合焊接主要是将节点的上下翼缘板分别作为一个整体,利用有关机械进行弯扭以保证端部能够达到设计要求的位置,之后再将节点的腹板和构造板件组合进行整体焊接。

图2-47 节点焊缝示意图
在完成节点的制作过程以后需要对节点的端面进行机加工处理。地下空间自然采光结构作为曲面、异型精细钢结构,其加工精度较之常规钢结构来说要求更高,尤其是节点牛腿各端面,其精度将直接影响到安装的精确性。这一指标需要作为重点内容控制。
(1)节点在组装、焊接、机加工与三坐标检测时采用统一基准孔和面,在加工过程中应保护基准面与孔不损坏。
(2)节点端面机加工在专用机床进行,在加工前仔细对节点编号与加工数据编号进行校核,核对准确后按节点加工顺序示意图规定加工。如采用五轴数控机床,其经济性和加工周期难以保证,因而采用设计的专用机床,既保证了加工精度,加工周期也得到了保障,如图2-48所示。
钢结构工程中,加工过程实现数字化精密加工,成本会逐渐下降,以后BIM与数字化加工的整合也将普及。

图2-48 端面加工专用机床