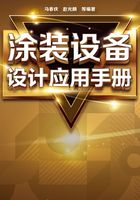
2.3 工艺设计程序
2.3.1 了解如下设计基础资料
① 生产纲领:××件/年。
② 工作制度:××天/年,××h/天。
③ 工件尺寸及重量。
④ 厂房尺寸及工件进出口的位置。
⑤ 能源的种类。
⑥ 涂装车间周边的环境。
⑦ 工程方对涂装线工艺水平的要求。
2.3.2 确定输送方式
涂装生产线的输送方式大体上分为两种,即连续式(通过式)及步进式(间歇式)。
生产量在100000辆/年(汽车车身)以上的涂装生产线应采用连续式;生产量在50000~80000辆/年(汽车车身)的涂装生产线可考虑采用步进式;生产量在50000辆/年(汽车车身)以下的的涂装生产线,资金又不足时,可考虑手动步进式。如果是小工件,如汽车车轮,则首先要确定每个挂具挂几个工件,然后再确定其输送方式。工件吊挂的方式也很重要,需根据工件的尺寸、结构、形状及工艺要求来确定。
2.3.3 计算生产节拍及输送速度
生产节拍(T):
式中 t——日时基数(16h即960min);
k——设备负荷(90%);
m——生产纲领,辆/天。
例:生产量为150000辆/年,1年生产300天,即500辆/天,则
根据上述生产节拍,不能采用步进式输送,必须选用连续式,因此需计算涂装线的输送速度v。
式中 L——工件间距,m;
T——生产节拍,min/辆。
挂具的节距应按工件长度、各工位的要求而定。
例:汽车车身长度4800mm,则前处理-电泳线的节距L=5515.2(153.2×36=5515.2),取5520即可。
注:153.2是积放输送链的链条节距,36是积放链的节数,此数根据工件长度来确定。
喷漆线是滑橇输送,考虑到喷涂方便,节距适当加大,取L=6000mm。
烘干室内的节距应,适当缩小,取L=5200mm。
所以,前处理-电泳线:
其他各工位速度的计算,依此类推。
500辆/天各工位的生产节拍及输送速度见表2-1。
表2-1 500辆/天各工位的生产节拍及输送速度

注:1.表中数据均为设计值。
2.持续运行时间,两班制,16h/天×60=960min/天。
3.设定车身长度为4.8m,滑橇长度为4.9m,在烘干室中工件间距≥5.2m。
4.喷涂间距为6.0m,换色装挂间距为7.0m,若5台车身换色1次,则平均装挂间距为6.2m。
2.3.4 工艺流程及技术参数
不同的产品对涂层的要求不同,自然涂装工艺流程也不同,下面列举一个典型的轿车车身涂装工艺流程,见表2-2。
表2-2 典型的轿车车身涂装工艺流程


工艺流程不能生搬硬套,应根据自己企业不同的产品、不同的生产纲领、不同的要求、不同的作业环境等条件而合理选定。
2.3.5 绘制工艺平面布置图的原则
具备了上述的设计基础资料后,就可着手构思工艺平面布置图,绘图时一定要遵循如下原则。
① 确定平面布置的方式。一般中小型涂装线平面布置为单层分区,大型涂装线宜采用多层立体分区布置。立体分区可将辅助设备分布在主体设备的上层或者下层,使工艺操作区与辅助系统操作区分开。可将洁净度要求高的喷漆室相对集中,高温区烘干室相对集中,既有利于涂层质量,又便于车间管理。这种布置造价较高,但合理先进。
② 确定非标设备的尺寸,主要配套设备的规格。
③ 物流、人流路线要畅通,同时要考虑设备维修通道和安全消防通道。
一般安全消防通道宽度为3~3.5m,物流运输通道宽度为2~2.5m,人流通道宽度为1.5m。
④ 前处理设备最好布置在一条直线上,不得已要转弯时,也要保证磷化处理前在一条直线上。在尽量防止串水的前提下,前处理工序间的过渡段应尽量缩短,时间不超过1min,迫不得已的情况下,为防止工件生锈,需在过渡段加喷雾段。前处理结束后需烘干时,立即进入水分烘干室,以防工件生锈。
⑤ 电泳结束后需尽快进入烘干室,以防涂层产生返溶现象。
⑥ 喷漆、流平及烘干工位也需要尽量布置在一条直线上。
⑦ 擦净室与喷漆室之间一定要加气封段(1.5~2m),以防灰尘污染涂层。
⑧ 平面图的定位基准线是轴线,标注必须准确。各设备的外形尺寸和定位尺寸也要标注清楚。
⑨ 要较合理、准确地预留各大型配套设备的位置与面积。
⑩ 如果涂装车间是新建厂房,应在可能的条件下,较准确地预留好各排风、进风的位置,避免破坏厂房。
⑪ 如果遇到厂房或者旧设备改造,则麻烦较多,一定要认真弄清楚原始资料,谨慎从事。