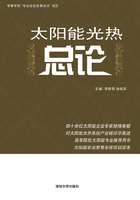
第1章 高硼硅玻璃3.3
——全玻璃真空管用毛坯管
一、引言
全玻璃真空管用毛坯管又称高硼硅玻璃3.3,是以氧化钠(Na2O)、氧化硼(B2O3)、二氧化硅(SiO2)为基本成分的一种玻璃,因热膨胀系数为(3.3±0.1)×10-6/K,故也称为“硼硅玻璃3.3”。它是制造太阳能热水器的重要原材料,占真空管生产成本的一半以上。
它是一种低膨胀率、耐高温、高强度、高硬度、高透光率和高化学稳定性的特殊玻璃材料。因其优异的性能,被广泛应用于太阳能、化工、医药包装、压制器皿、电光源、工艺饰品等行业,可制成灯具、餐具、标盘、望远镜片、洗衣机观察孔、微波炉盘、太阳能热水器等多种产品。
它的良好性能已得到世界各界的广泛认可,特别是在太阳能领域应用更为广泛,多个国家已进行了较为广泛的推广,该种玻璃在我国出现是基础材料工业的又一次新革命。
二、全玻璃真空管用毛坯管的生产发展历程
全玻璃真空管用毛坯管是利用高硼硅窑炉生产出来的,它的生产发展经历了四个关键阶段。
1.火焰炉的应用
火焰炉是以天然气燃烧的火焰为热源的。火焰炉炉膛内的火焰通常与物料直接接触,火焰直接给物料加热。炉子内壁既辐射热量,也部分地反射投射来的热量,在热交换过程中起重要作用。
玻璃原材料由外向内逐渐熔化,顶部温度较高,容易造成氧化硼等气体挥发,挥发率高达25%~30%,除对环境造成一定的污染外,还造成了原材料的巨大浪费。
2.全电熔炉技术的应用和普及
全电熔炉技术是20世纪国际上发展起来的一种新技术,取代传统火焰炉,采用全部电加热方式熔制玻璃产品。虽然玻璃在低温下几乎是绝缘体,但在高温熔融状态下的玻璃却是一种良导体,在熔融的玻璃里插入电极,利用玻璃液自身的电阻发热,使电能转化为热能,转换效率高达90%。
因为全电熔炉采用的是电极加热,玻璃液从内部加热,顶部温度接近室温,气体挥发率低于3%,在保证玻璃液熔制质量的基础上,使原材料能得到充分的利用。
3.维罗平拉技术的推广和应用
毛坯管生产初期,行业均采用的是垂拉的方式。垂拉成型,火焰炉出料量小,成型制造非常适合垂拉成型,垂拉型由供料机和垂拉机组成。垂拉机上部摆放一小车,小车上分层按纵横两向在玻璃管两边各摆放石墨砖,用来调节玻璃的椭圆度,垂拉机主要通过拉引量控制外径、壁厚、弯度等,电助窑炉的出现使垂拉成型出料量开始增大,垂拉成型的缺点开始显现,所需成型人员多尤其突出。
随着窑炉熔化量的逐渐提高,迫使各公司找到新的方式来替代垂拉成型,这时维罗生产线被引进中国。经过几年消化吸收,维罗生产技术成熟起来,并得到大量推广。维罗生产线比垂拉生产工艺复杂,设备多,但生产用人少,设备维护方便,产品质量稳定,有外径自动分拣系统。维罗线主要设备有搅拌机、供料机、真空跑道、冷却跑道、负压风机、牵引机、三脚架降温冷却梳理机等组成,真空跑道、负压机、牵引机使用调整玻璃管的椭圆外径。
4.大型全电熔窑炉的推广和应用
全电熔技术与维罗技术在共同发展中,逐步成熟,使全电熔炉制造的毛坯管单位能耗达到新的低点。经过近几年发展,太阳能毛坯管行业经过一次次大的洗牌,把全电熔技术应用与维罗生产技术完美结合使用。提高产品质量、提高窑炉熔化率、提高单线产能、降低产品单耗、减低人工费用等方面,山东龙光天旭太阳能有限公司走在了全国前前列,在行业创新领域中处于领先位置。
山东龙光天旭太阳能有限公司自行研发并投产,且正在运行的21m2高硼硅全电熔炉,采用一炉两线维罗平拉生产技术,以品质高、节能、环保的优势受到业内好评,目前单台窑炉日产量在35t以上,成品毛坯管单耗控制在1210kW·h/t以下,处于行业领先水平。其生产的毛坯主要供应国内知名企业,部分产品直接运销国外(图1)。

图1 山东龙光天旭太阳能有限公司21m2全电熔窑炉及生产现场

图1(续)
三、全电熔炉的介绍
玻璃电熔窑的技术经济分析应从玻璃制品的质量、窑炉的能耗、节约的挥发性原料、基建投资、电力和燃料的价格、配合料成本、操作成本、粉尘或废气净化设备、冷修成本等方面出发,对产品和电熔工艺过程做比较。
表面上看玻璃电熔不过是欧姆定律、焦耳定理和其他一些基本电工原理的简单应用,但实际上复杂得多。电熔窑设计考虑包括:冷顶还是热顶,单个熔化池还是多个熔化池,单相、两相还是三相供电,六角形截面还是矩形截面,垂直电极还是水平电极,加料方式等。
从热顶的矩形窑到冷顶的圆形窑,有着大量的设计方案可供选择,是采用单层电极还是多层电极。当使用水平电极时,应不断推进电极,电极在使用中的不断耗蚀、损坏,其浸入量是不断减少的。使用垂直电极则电极弯曲损坏的可能性减少了,也减少了由于浸入量变得太短引起池墙损坏的事故。但只要留意钼的选择,维护好电极及其水冷套,电极的弯曲及损坏是可以避免的。
电熔窑的熔化率不会因设计方案的不同而有显著变化,因为控制熔化率的主要因素是玻璃成分和碎玻璃用量。
现今电熔窑的一个倾向是熔化池较深,目前运转的大量电熔窑其深度都超过了2.5m。这一点再次确定了电熔窑应该选取优质耐火材料,其砖缝应尽可能地小,以免炉底砖块间玻璃液的挤出。
1.全电熔窑炉主要尺寸的确定
在确定电熔窑主要尺寸之前,首先要知道所熔制的玻璃成分和窑的日熔化量,电熔窑的熔化率取决于玻璃的种类、电熔窑的大小。玻璃电熔窑的热量是通过所熔化的玻璃的整个体积引入的,应以每天、每立方米的体积熔化量来确定电熔窑的结构。但是,人们常常习惯于采用面积熔化率来表示。可利用表1确定全电熔炉的熔化面积。
表1 面积熔化率

2.全电熔窑各部位耐火材料的合理选用和窑的保温
2.1 耐火材料的选用
合理选用全电熔窑各部位耐火材料,以满足熔制工艺上的要求,直接关系到电熔窑的产量、玻璃的质量、电熔窑的寿命、投资的成本。因此必须充分重视。
全电熔窑对耐火材料的要求:
(1)对玻璃无污染或污染程度很小。
(2)在正常使用温度下,必须具有很高的化学稳定性,能抗配合料和玻璃液的侵蚀,相邻耐火材料之间无接触反应。
(3)必须具有很高的高温机械强度。
(4)必须具有很高的耐火度。
(5)必须具有很高的抗热冲击性能。
(6)在正常使用温度下,体积的固定性要好,重烧收缩率和膨胀率应尽可能小。
(7)在正常使用温度下,必须具有很高的电阻率。
(8)尺寸要准确。
此外,选择耐火材料时要全盘考虑,不要由于局部薄弱环节而对整座电熔窑的寿命造成不良影响。
2.2 电熔窑的保温
电熔窑的保温十分重要,直接关系所设计的电熔窑的电耗和运行成本,考虑保温部位时坚持“能保即保”和“既保温又耐用”的原则。包括保温层设计、施工、烘烤、保温效果的研究和评定、保温后窑炉的结构和操作等。
(1)池底保温:池底先用标准黏土砖做好基底,上面再铺设黏土大砖,在黏土大砖上覆盖一层锆质捣打料,其上再铺一层电熔锆刚玉砖。
(2)池壁保温:液面线附近因侵蚀比较严重,不需保温。保温后,玻璃液有可能从砖缝漏出,为防止漏料,相邻的两块池壁砖面要磨平贴紧,并外贴锆质捣打料层。尽量消除水平砖缝,也可以把砖缝留出,并吹冷风。一般采用在池壁砖外贴锆质捣打料,再砌黏土大砖。
3.电熔窑的热平衡计算
电熔窑内所产生的电热效应,根据焦耳定律其热量Q与通过玻璃液的电流I的平方成正比,与电极间玻璃液电阻R成反比,Q=I2Rt=U2t/R,在全电熔窑内配合料熔化所需的化学反应热Q1,窑体的热损失Q2(包括池底、池壁、料毯),电极及冷却水所带走的热量Q3,以及其他热损失Q4,均来自电热效应所产生的热量。因此,电热平衡方程为:Q=Q1+Q2+Q3+Q4,若以单位耗电量[kW·h/kg(玻璃)]来表示,所消耗的电功率是电熔窑的经济性和完善性指标,与电熔窑的尺寸、熔化率、玻璃品种、保温条件等因素有关。
4.电源供电的介绍
对于小型的电熔窑,通常采用单相电源,容量较大者则采用两相或三相电源。多相供电电熔窑的形状和电气特性上可以是对称的,也可以是不对称的。对称系统有利于垂直熔化均匀的能量释放,用加料机使得整个熔化池的表面产生均匀的配比料覆盖层。
全电熔炉所用的电源系统取决于电熔炉的形状与尺寸。反过来,电熔炉的形状又由所用电源系统决定。形状与尺寸同时还取决于许多其他的变量。它们有玻璃成分、电阻率、所用电极的类型与数量、与人身安全有关电压的限制、可接受的电极电流密度以及加料的方式。
四、全玻璃真空管用毛坯管的常见质量缺陷、形成原因及控制措施
1.结石(主要分为以下3类)
配合料结石、耐火材料结石、析晶结石。
1.1 配合料结石产生原因(主因)
(1)石英砂中有大颗粒。
(2)氢氧化铝有时也有可能生成玻璃结石。
(3)碎玻璃中有异类物质。
配合料结石产生的原因较多,这些原因与原料的选择加工、配合料制备工艺、加料方法、熔化温度等因素有关,例如配合料中有大颗粒石英砂、混料不均等。
控制措施:
(1)原料一定符合原料质量标准。
(2)严格按照料方要求称料。
(3)严格按照倒料顺序倒料。
(4)控制混料时间,按要求更换混料机铲片,尽可能地提高配料均匀度。
(5)制定合理、稳定的大炉温度。
1.2 耐火材料结石产生的原因
(1)耐火材料质量不好。
(2)熔化温度太高导致耐火材料熔化。
(3)玻璃液的侵蚀,尤其是液面线附近。
(4)耐火砖掉入料道及料盆内。
(5)液面波动大忽高忽低。
(6)助溶剂用量过大。
控制措施:
(1)选用优质耐火材料。
(2)大炉温度合理。
(3)控制好液面。
(4)防止一些意外出现(如掉砖)。
1.3 析晶结石
析晶结石是由于玻璃在一定温度范围内自身的析晶而造成的。
控制措施:
(1)增加组分,以降低析晶温度。
(2)提高成型速度。
(3)更换护管时,要仔细烘烤至高温,使护管烤透。
(4)制定合理的成型温度。
2.条纹和节瘤
产生的原因:①熔化不均;②耐火材料被侵蚀;③结石熔化;④成型搅拌机构不合适;⑤成型工装使用时间过长。
另外,大炉温度的稳定与否与条纹和节瘤的产生密切有关,当温度不稳定时,破坏了均化澄清工艺,同时引起死料参与液流,导致条纹和节瘤的产生。
3.气泡(气线)
产生的原因:①石英砂中的尾粉超标;②大炉温度偏低;③澄清均化的时间不够;④大炉红顶;⑤成型温度搭配不合理;⑥挥发物、异类物质等掉入料盆。
4.弓弯
产生的原因:
①偏壁;②牵引机、跑道与出口料中心不在同一直线上;③跑道弯曲;④石墨块磨损严重。
整改措施:
(1)调整壁厚至均匀。
(2)安装生产线时务必做到三点一线(牵引机、跑道出料口中心)。
(3)调整跑道。
(4)更换石墨块。
5.蛇弯
产生的原因:
(1)料温过高。
(2)牵引机偏转过快。
(3)端头与所产玻璃管规格不符。
整改措施:
(1)降低料温。
(2)减少偏转。
(3)更换合适端头。
6.椭圆
产生的原因:
(1)料温不合适。
(2)负压过低。
(3)牵引机偏转小,玻璃管未转动。
整改措施:
(1)调整料温(换合适端头)。
(2)更换大功率负压风机,若风机无问题则需更换负压跑道。正常生产时负压变小,查看封跑道用的纸片有无脱落。
(3)调整牵引机偏转。
7.偏壁
产生的原因:
(1)料碗椭圆。
(2)护管椭圆过大。
(3)料温不均。
整改措施:更换合适的护管或料碗。
8.对偏
产生的原因:
(1)玻璃液分层。
(2)料碗椭圆或护管筒椭圆。
整改措施:
(1)加快搅拌桨转速。
(2)转护管90°,若调不好换护管筒料碗。
9.壁厚不稳,压帽不紧,料温不均
整改措施:
(1)换护管时一定要压好压帽。
(2)调整料道温度。
10.外径不稳
此项为成型过程最难控制的一项,产生的原因:
(1)端头不合适。
(2)料碗不合适。
(3)料过大。
(4)吹气大小不当。
(5)料温不均。
(6)各料道温度调整不到位。
(7)大炉功率不稳定。
(8)保温罩大小不合适。
(9)投料不匀。
(10)吹杆氧化堵塞。
整改措施:
(1)用合适的端头拉合适的管。
(2)换合适的料碗。
(3)调整吹气至正常。
(4)调整料道各区温度。
(5)稳定出料,稳定配合料从而稳定大炉功率。
(6)用合适保温罩,使用时间长。
五、全玻璃真空管用毛坯管的生产过程
1.毛坯管的生产工艺流程

1.1 配料
高硼硅玻璃3.3的生产需要以下六种原材料:石英砂、硼砂、硼酸、氢氧化铝、熟料、食盐。配料前,首先对各原材料进行检验,达到要求方可使用。
1.1.1 石英砂
外观要求:白色结晶体,色泽洁白、颗粒度均匀,无混合物杂质。
颗粒度要求:60目以上为零,60~140目之间大于85%,200目以上的细粉不允许有。
成分要求:SiO2≥99.30%,Fe2O3≤0.03%。
1.1.2 硼砂
外观要求:白色结晶体,色泽洁白,颗粒度均匀,无混合物杂质。
成分要求:Na2O≥21%,B2O3≥47%,Fe2O3≤0.01%。
1.1.3 硼酸
外观要求:颜色雪白,具有合适的流动性,看不到机械杂质,粒度细且手捻能更细腻或者手捻即碎。
成分要求:B2O3≥56(±1)%,Fe2O3≤0.01%。
1.1.4 氢氧化铝
外观要求:包装完好无破损、无杂质、不能有潮解结块现象。
成分要求:Al2O3≥21%,Fe2O3≤0.03%。
1.1.5 熟料
外观要求:片状玻璃。
成分要求:与高硼硅玻璃3.3成分符合。
1.1.6 食盐
外观要求:包装完好无破损,无杂质,不能有潮解结块现象。
成分要求:NaCl≥95%,Fe2O3≤0.05%。
将符合要求的材料按一定的比例先后倒入混料机内,并搅拌均匀,配合料均匀度要在95%以上,保证玻璃熔制和成形作业稳定。
1.2 投料
目前,行业内的投料方式有两种:人工投料、自动投料。
自动加料机应符合下列要求:上部结构紧凑,当电熔窑表面未被配合料覆盖时,对此温度必须适应;防尘简易可靠,至少能良好地密闭,粉尘要少;配合料的播散要与能量、温度和电流的分配相适应;操作要方便;在遇故障的情况下,整个电熔窑表面应能迅速地用配合料覆盖住。加料机把配合料撒播到整个熔化池的玻璃液面上,提供了一种真正的垂直熔化。
将配好的混合料,根据窑炉运行设定的投料量,定量均匀的投入窑炉内部。每30分钟测量一次液面,保持液面稳定。
1.3 熔化
熔化工序是窑炉生产控制的核心工序,该工序要求熔化功率稳定。在投料稳定和配料稳定的前提下,稳定熔化电流,根据窑炉玻璃液电阻显示,控制合理的电流、电压,将原料充分熔化,达到成型要求。熔化工根据电阻不定时调节熔化功率,将电阻控制在控制范围之内,经常检查各窑炉电极水套是否通水,各窑炉附属设备的使用是否正常,并每隔一小时记录各层电流、电压、电阻、出料量等各项关键指标,记录必须真实、准确,若发现异常情况,要及时处理并上报。
目前行业内较为普遍的全电熔窑截面采用十二边形的结构,电极采用炉体斜插式和底面垂直插入式结构,使原料垂直熔化,在垂直方向上依次形成冷顶层、硅酸盐形成层、玻璃形成层、澄清层和冷却层。
窑炉上半部分为熔化区和澄清区;下面为均化区。均化区的玻璃液有所冷却,玻璃液经过上升道进入料道,在经过供料机及成型装置,进入成型工序。
1.4 成型
成型是毛坯管生产过程的关键工序。过程中要做好窑炉牵引量稳。成型好坏关系毛坯质量等各方面因素,熔化好的原料经过料道和端头,模具成型,通过调节空气压力,达到毛坯的圆度要求,通过调节原料流速,控制毛坯壁厚,在前面三大稳的基础上,控制合理的牵引速度,调整好控制外径的大小的激光,最终生产出合格的产品。
1.5 包装入库
成型后的毛坯,按要求切割成一定的长度,由专业质量检验员,将合格产品逐支挑拣出,然后由专业包装人员按客户要求入库存放。
六、全玻璃真空管用毛坯管的质量要求
1.材质要求
玻璃管应采用平均线热膨胀系数α=(3.3±0.1)×10-6K-1的硼硅玻璃,其基本成分应符合表2要求。
表2 高硼硅玻璃3.3基本化学组成

注:R2O为一价金属氧化物。
2.玻璃管的规格尺寸及偏差(表3)
表3 玻璃管规格尺寸及偏差

3.理化性能
3.1 平均线热膨胀系数α(50~300℃)=(3.3±0.1)×10-6K-1。
3.2 密度ρ(20℃)=2.23±0.02g/cm3。
3.3 太阳透射比τ(AM 1.5)≥0.89。
3.4 抗冲击检测
玻璃管的撞击破损能量应不小于2.5J,通过率不低于95%。
3.5 环切等级
环切等级不大于HQ-8,具体等级分类参照表4。
表4 按玻璃制品使用要求的环切分类表

4.外观
(1)玻璃管上不得有石棉印、铁锈、铁屑、泥土和油污,不得有目测可见的光学变形,不得有裂纹划伤。
(2)气线:宽度不得大于0.5mm,在玻璃管上长度大于40mm的不允许存在;长度在20~40mm范围内的气线不允许超过两条;管长方向150mm范围内,5~20mm的不允许超过两条,5mm以下的气线不允许超过5条;距管口端200mm范围内不允许有气线存在。
(3)节瘤:玻璃管上大于2.0mm的节瘤不允许存在;1.5~2.0mm的节瘤不得多于5个;管长150mm范围内:1mm以下的节瘤不得密集,即10mm×10mm范围内不得多于2个。
(4)结石:玻璃管上大于1.0mm的结石不允许存在;1.0mm以下的结石不得密集,即10mm×10mm范围内不得多于1个;整支管子上结石不得多于5个;结石周围不得有裂纹。
(5)目视玻璃管不得有可见析晶物。
(6)不允许有严重的直楞线,必要时可封实物标准样。
(7)擦伤:单支轻微擦伤长度不超过100mm,累计长度不超过200mm。
作者简介

邢作新:山东龙光天旭太阳能有限公司董事长。从事玻璃行业30余年,对日用玻璃、药用玻管、高硼硅玻璃、钠钙玻璃、真空管、太阳能等多种产品都有深入了解,对行业的生产和销售均有很深的研究。2007年,他亲手创建了山东瑞光新能源科技有限公司,并在短短的几年时间里,取得了骄人的成绩。2013年起,在他的带领下,山东龙光天旭太阳能有限公司迎来了新的发展机遇,在整个行业发展速度减缓的大环境下,公司实现了发展和进步的几大跨越,为下一步的飞速提升奠定了坚实的基础,目前作为全国最大的毛坯管、真空管生产基地,在行业内起着举足轻重的作用。山东龙光天旭太阳能有限公司立志与行业有志之士一起,共同做好、做大、做强太阳能及相关产品这项伟大的事业,为推动新能源发展进步尽一份微薄之力。