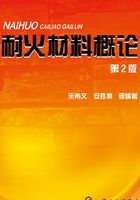
1.2 耐火材料的性能
1.2.1 结构性能
本书只表述耐火材料的宏观结构性能,它包括气孔率、吸水率、体积密度和透气度等,是影响耐火材料使用性能的重要因素。这些性能之间是相互关联的,耐火材料中的气孔率直接决定它的吸水率、体积密度和透气度等性能指标。
1.2.1.1 气孔率
气孔是影响耐火制品常温与高温性能的重要因素,特别是在高温条件下,它会使制品对外界侵蚀的抵抗能力大大降低。形成气孔的原因有:制品成型时物料中的空气未完全排出;物料水分排出后留下的空间;原料煅烧不充分,有些应分解的盐类未完全分解,应灼烧的成分未完全灼烧;物料成分不均匀,高温烧成时收缩不均匀等。但在有些轻质隔热制品中,还需特意引入一些分布较均匀的气孔。
耐火材料中的气孔大致分为三类(见图1-4):(1)闭口气孔,封闭在制品中不与外界相通;(2)开口气孔,一端封闭,另一端与外界相通,能被流体填充;(3)贯通气孔,贯通制品的两面,流体能通过。

图1-4 耐火材料中的气孔类型
1—闭口气孔;2—开口气孔;3—贯通气孔
由于开口气孔和贯通气孔占总气孔体积的绝大部分,而且对制品的使用性能影响最大,又较易测定,因此在耐火制品的检测标准中,以显气孔率P a,即开口气孔和贯通气孔的体积之和占制品总体积的百分率来表示气孔率指标。
气孔率是耐火材料的基本技术指标,它几乎影响耐火制品的所有性能,尤其是强度、热导率、抗侵蚀性、抗热震性等。一般来说,气孔率增加,强度降低,热导率降低,抗侵蚀性降低。但气孔率对抗热震性的影响比较复杂。
耐火材料的气孔率受所用原料、工艺条件等多种因素的影响。一般来说,选用致密的原料,按照最紧密堆积原理来采用合理的颗粒级配,选用合适的结合剂,物料混炼充分,高压成型,提高烧成温度和延长保温时间均有利于降低材料的气孔率。
显气孔率的测定方法为:使用50~200cm3的立方体或圆柱体试样,先称干燥试样的质量,然后让试样在容器中抽真空,再加入液体充分饱和试样,称量饱和试样在空气中的质量和饱和试样的表观质量(饱和试样完全淹没在液体中,饱和试样的质量减去完全被排出液体的质量)。计算显气孔率的公式为:
(1-1)
式中,Pa为耐火制品的显气孔率, %;m1为干燥试样的质量,g;m2为饱和试样的表观质量,g;m3为饱和试样在空气中的质量,g。
1.2.1.2 吸水率
吸水率是制品中全部开口气孔所吸收的水的质量与其干燥试样的质量之比。它实质上反映了耐火材料中开口气孔的数量。由于吸水率测定方法简便,在耐火材料生产实际中常常用来鉴定原料煅烧的质量。原料煅烧的越好,吸水率越低。
吸水率的测定方法与显气孔率的测定方法相同,计算公式为:
(1-2)
式中,Wa为吸水率, %;m1为干燥试样的质量,g;m3为饱和试样在空气中的质量,g。
1.2.1.3 体积密度
体积密度是指耐火材料的干燥质量与其总体积之比,单位为g·cm-3。体积密度直观地反映了耐火制品的致密程度,它是耐火原料、致密耐火制品质量水平的重要衡量指标。但在轻质隔热制品的生产中,为降低热容和热导率,常采用各种手段降低制品的体积密度。
耐火材料的体积密度对其他许多性质都有显著的影响,如气孔率、强度、抗侵蚀性、荷重软化温度、耐磨性和抗热震性等。对于轻质隔热耐火材料,如隔热砖、轻质浇注料等,体积密度与其导热性和热容量也有密切的关系。一般来说,体积密度越高,对耐火材料的强度、抗侵蚀性、耐磨性、荷重软化温度越有利。
耐火材料的体积密度受所用原料、生产工艺等因素的影响,控制所用原料的体积密度、压制砖坯的压力和烧成制度,均能有效地控制最终制品的体积密度。
对于致密定形耐火制品来说,体积密度和显气孔率是同时测定的,计算公式为:
(1-3)
式中,ρb为耐火材料的体积密度,g·cm-3;ρL为在试验温度下,浸渍液体的密度,g·cm-3;m1为干燥试样的质量,g;m2为饱和试样的表观质量,g;m3为饱和试样在空气中的质量,g。
对于定形隔热耐火制品来说,直接测量试样的质量和尺寸,体积密度按下式计算:
(1-4)
式中,ρb为定形隔热耐火制品的体积密度,g·cm-3;m为干燥试样的质量,g;Vb为试样的总体积,cm。
1.2.1.4 真密度
真密度是指多孔体材料的质量与其真体积之比。真体积是指多孔体中固体材料的体积。它可以反映材质成分的纯度以及晶型转变的程度、比例等,由此可以推知在使用中可能发生的变化。
真密度的测定方法为:将试样磨细到尽可能无封闭气孔存在的粉末试样,称量比重瓶的质量和装有试样的比重瓶的质量,两者之差即为干燥试样的质量。选用蒸馏水或已知密度的液体装满装有试样的比重瓶,称量其质量。选用同一液体装满已倒空试样和洗净的同一比重瓶,称量质量。真密度的计算公式为:
(1-5)
式中,ρ为试样的真密度,g·cm-3;ρ L为所选用液体在试验温度下的密度,g·cm-3;m1为干燥试样的质量,g;m2为装有试样和比重瓶的质量,g;m3为装有选用液体的比重瓶的质量,g。
1.2.1.5 透气度
透气度是指耐火制品允许气体在压差下通过的性能。透气度与贯通气孔的数量、大小、结构和状态有关,并随着制品成型时的加压方向而异。
制品的透气度高,提高了具有侵蚀性流体的通过能力,极大地加快了砌体的侵蚀速率,缩短了砌体的使用寿命。另外,透气度高也使热工窑炉的热损失增大,因此在一般情况下,希望制品的透气度越小越好。
耐火材料的透气度直接受生产工艺的影响,通过控制颗粒级配、成型压力和烧成制度可控制材料的透气度。
对于致密定形耐火制品的透气度的测定方法为:检测在三个不同的压差下,干燥空气或氮气流过规定尺寸试样两端面的流量,计算公式为:
(1-6)
式中,μ为试样的透气度,m2;η为试验温度下气体的动力黏度,Pa·s;h为试样的高度,mm;d为试样的直径,mm;Q为气体的体积流量,L·min-1;Δp为试样两端气体的压差,Pa,Δp=p1-p2;p1,p2分别为气体进入试样端和逸出试样端的绝对压力,Pa。
1.2.2 力学性能
耐火材料的力学性能是指制品在多种条件作用下的强度等力学性能指标,该指标表征制品抵抗因外力作用而产生的各种应力变形而不被破坏的能力。无论是在常温或是在使用条件下,耐火材料都会因受到各种外界作用力如压缩力、拉伸力、弯曲力、剪切力、摩擦力或撞击力的作用而变形乃至破坏,因此检验不同温度条件下的耐火材料的力学性质,对于了解它抵抗破坏的能力,探讨它的损坏机理,寻求提高制品质量的途径、办法具有极其重要的意义。
1.2.2.1 耐压强度
耐压强度是指耐火材料在一定的温度下单位面积所能承受而不被破坏的极限载荷。耐火材料的耐压强度分为常温耐压强度和高温耐压强度。它是衡量耐火材料质量的重要性能指标之一,间接地反映出制品的组织结构,如致密度、均匀性和烧结性等。
耐火材料的常温耐压强度是指在室温下,耐火制品试样单位面积上所能承受而不被破坏的极限载荷。耐火材料的常温耐压强度对于该制品的生产、运输、使用性能均有极大的影响,而且在多数情况下,也直接影响到使用寿命,由此我们希望制品达到较高的耐压强度值。
耐火材料的高温耐压强度是指耐火材料在指定的高温条件下,规定尺寸的立方体试样单位面积上所能承受而不被破坏的极限载荷。耐火材料的高温耐压强度决定了该制品的使用范围,它是耐火材料选择的重要依据之一。对于不烧耐火制品和不定形耐火材料来说,由于在材料中加入了一定数量的结合剂或外加剂,其结合方式和强度会随着温度的升高而产生变化,因此其高温耐压强度具有更为重要的意义。
在室温下测得的耐压强度为材料的常温耐压强度。将试样按规定的速率升温到指定的温度,保温一定时间后测定的耐压强度为该温度下的高温耐压强度。耐压强度的计算公式为:
(1-7)
式中,S为耐火制品试样的耐压强度,MPa;P为试样破碎时的最大载荷,N;A为试样的面积,mm2。
1.2.2.2 抗折强度
抗折强度是指具有一定尺寸的耐火材料条形试样,在三点弯曲装置上所能承受的最大弯曲应力,又称抗弯强度。耐火材料的抗折强度亦分为常温抗折强度和高温抗折强度。常温抗折强度是指在室温下,规定尺寸的长方体试样在三点弯曲装置上受弯时所能承受的最大应力。一般说来,常温耐压强度较高的样品其常温抗折强度也较好。其计算公式为:
(1-8)
式中,Rr为耐火材料的常温抗折强度,MPa;F为试样断裂时的最大载荷,N;L为下刀口间的距离,mm;b为试样中部的宽度,mm;h为试样中部的高度,mm。
耐火材料高温抗折强度(Re)是指耐火制品在规定的高温条件下,规定尺寸的长方体试样在三点弯曲装置上受弯时所能承受的最大应力。计算公式同式(1-8)。
高温抗折强度高的制品,在高温使用条件下,对于物料的冲击、磨损、液态渣的冲刷等,均具有较好的抵抗能力。
1.2.2.3 耐磨性
耐磨性是指耐火材料抵抗坚硬的物体或气流的摩擦、磨损、冲刷的能力。耐火材料的耐磨性取决于其矿物组成、组织结构和颗粒结合的牢固性以及材料本身的密度、强度等。
常温耐磨性用磨损体积来表示,其测试方法为:将磨损介质垂直喷吹到试样表面上,测量试样的磨损体积。按下式计算磨损量:
(1-9)
式中,A为磨损量,cm3;ρ b为试样的体积密度,g·cm-3;m1,m2分别为试验前后试样的质量,g。
1.2.3 热学性能
由于耐火材料经常在加热情况下使用,因此耐火材料的热学性能也是其性能的重要方面。耐火材料的热学性能主要包括热容、热膨胀性和导热性。
1.2.3.1 热容
热容是指温度升高1K时材料所吸收的热量,比热容是单位质量的材料温度升高1K所吸收的热量。在不同的温度下,材料的热容是不同的,在温度T时材料的恒压热容C p可以表示为:
(1-10)
工程上通常使用平均热容,它是指将材料从T0温度加热到T1温度所吸收热量的平均值:
(1-11)
式中,Q为试样温度由T0加热到T1所吸收的热量,J;m为试样的质量,g;T0,T1为试样加热前后的温度,K。
耐火材料的热容指标,在设计和控制炉体升温、冷却,特别是计算蓄热能力时具有重要意义。
1.2.3.2 热膨胀性
耐火材料的热膨胀性是指制品在加热过程中长度或体积随温度的升高而增大的现象。耐火材料在使用的过程中常伴有巨大的温度变化,随之而来的长度和体积的变化,会严重影响热工设备砌体的尺寸,甚至导致砌体破坏。此外,耐火材料的热膨胀情况还能反映出受热后的热应力分布和大小,晶型转变及相变,微裂纹的产生及抗热震稳定性等。
热膨胀的表示方法有线膨胀率和线膨胀系数两种,也可以用体积膨胀率和体积膨胀系数来表示。线膨胀率ρ是指由室温到试验温度之间试样长度的相对变化率(%)。线膨胀系数α是指由室温到试验温度之间,每升高1K,试样长度的相对变化率,单位为1×10-6K-1。相应地,体积膨胀用体积膨胀率()和体积膨胀系数β来表示,
。若线膨胀系数很小,则体积膨胀系数约等于线膨胀系数的3倍,即β=3α。
热膨胀系数实际上并不是一个恒定值,它随着温度的变化而变化,通常所说的热膨胀系数都是指在一定的温度范围内的平均值。
耐火材料热膨胀性的测试方法有两种,顶杆法和望远镜法。其基本原理是以规定的升温速率将试样加热到指定试验温度,测量随温度的升高试样温度的变化值,计算出随温度升高试样的线膨胀率和指定温度范围内的平均线膨胀系数。
(1)顶杆法。试样由室温至试验温度各温度间隔的线膨胀率按下式计算:
(1-12)
式中,L0为试样在室温时的长度,mm;L T为试样在试验温度T时的长度,mm;Ak为在试验温度T时仪器的校正值,mm。
试样由室温至试验温度线膨胀系数的计算公式为:
(1-13)
式中,ρ为试样的线膨胀率;T0为室温;T为试验温度。
(2)望远镜法。望远镜直读法是用望远镜直接观察炉内高温下试样的膨胀值。试样由室温至试验温度的线膨胀率按下式计算:
(1-14)
式中,L0为试样在室温时的长度,mm;L T为试样在试验温度T时刻时的长度,mm;,
分别为试验温度T时,左右镜筒中观测点的长度变化,mm。
1.2.3.3 导热性
导热性的衡量指标为材料的热导率。热导率(或导热系数)是指在单位温度梯度下,通过材料单位面积的热流速率。它是表征材料导热特性的一个物理量,它与材料的种类、组织结构及使用温度等因素有关,可以表示为:
(1-15)
式中,λ为热导率,W·(m·K)-1;q为单位时间内的热流密度,W·m-2;∂T/∂x为温度梯度,K·m-1。
材料热导率的测定方法分为稳态法和非稳态法两种。在稳态法测试中,待测试样处于一个稳定的温度场中,测定试样通过单位面积上的热流密度、试样在热流方向上的温度梯度及试样的几何尺寸,然后根据式(1-16)来计算材料的热导率。最常用的为平板热导法,平板法测定耐火材料热导率的计算公式为:
(1-16)
式中,λ为热导率,W·(m·K)-1;Q为通过的热量,J;δ为试样的厚度,m;F为有效面积,m2;T1为试样冷表面的温度,K;T2为试样热表面的温度,K;t为传热时间,min。
稳态法是经典方法,但它的缺点是测试时间长、影响因素多。非稳态法的优点是测量简便、快速。耐火材料热导率测定中采用非稳态法中的十字热线法。利用热线法(非稳态法)测定耐火材料的热导率的表达式为:
(1-17)
式中,λ为热导率,W·(m·K)-1;I为加热电流,A;V为热线两端的电压,V;L为热线长度,m;t1,t2为加热电流接通后测量的时间,min,T1,T2为热线在t1,t2时对应的温度, ℃。
热导率是耐火材料最重要的热物理性能之一,是在热工设备的设计中不可缺少的重要数据,也是选用耐火材料很重要的一个参考因素。
1.2.3.4 温度传导性
温度传导性是材料在加热或冷却的过程中,各部分温度倾向一致的能力,即温度的传递能力。温度传导性用热扩散率来表示:
(1-18)
式中,α为热扩散率,m2·s-1;λ为热导率,W·(m·K)-1;ρ为材料的表观密度,g·cm-3;C p为耐火材料的恒压热容,J·(g·K)-1。
耐火材料的α值越高,则在相同的外部加热或冷却条件下,材料内部的温度传播速度越快,各处的温差也就越小,因此它决定材料急冷急热时内部温度梯度的大小。α是非稳态传热过程热分析、计算的重要参数。间歇式窑炉炉墙温度分布和蓄热量计算、隧道窑的窑车蓄热量计算都用到耐火材料的热扩散率。热扩散率的测量采用非稳态法,常用的是激光脉冲法。
1.2.4 使用性能
耐火材料的使用性能是指耐火材料在高温下使用时所具有的性能。包括耐火度、荷重软化温度、高温蠕变性、体积稳定性、抗热震性、抗侵蚀性等。
1.2.4.1 耐火度
耐火度指耐火材料在无荷重时抵抗高温作用而不熔融和软化的性能。耐火度的意义与熔点不同。熔点是指纯物质的结晶相与其液相处于平衡状态下的温度。而一般耐火材料是由多种矿物组成的多相固体混合物,无统一的熔点,而是在一定温度下开始产生液相,随温度升高液相比例不断增大,到某一固定温度时固相才能全部熔融为液相,在这两个固定温度之间的一段温度范围内,都是液固两相同时存在。
决定耐火度的基本因素是材料的化学矿物组成及其分布情况。各种杂质,特别是具有强熔剂作用的杂质成分,会严重降低制品的耐火度。成分分布不均匀,以致不能形成理想的高熔点矿物,将使制品的耐火度降低。值得注意的是耐火度并不代表制品的使用温度,因为耐火材料在使用的过程中经常在经受高温作用的同时,还伴随着荷重和外物的熔剂作用,因此使用温度往往比耐火度低得多。
耐火度通常都用标准测温锥的锥号表示。测定耐火材料耐火度试验方法的要点是:将由被测耐火原料或制品制成的试锥与已知耐火度的标准温锥一起置于锥台上,在规定的条件下加热并比较试锥与标准温锥的弯倒情况,直到试锥顶部弯倒接触底盘,此时与试锥弯倒的标准温锥可代表的温度即为该试锥的耐火度。试锥在不同阶段的熔融弯倒情况见图1-5。

图1-5 试锥在不同阶段的熔融弯倒情况
a—熔融开始以前;b—在相当于耐火度的情况下;c—在高于耐火度的情况下
1.2.4.2 荷重软化温度
耐火材料的荷重软化温度是指材料承受恒定压负荷并在一定升温速度的加热条件下产生变形的温度。它表示了耐火材料对高温和荷重同时作用的抵抗能力,也表示耐火材料呈现明显塑性变形的软化范围。在设计高温窑炉时,根据耐火材料的荷重软化试验和残存收缩率,在一定程度上可以推测耐火材料的高温体积稳定性。
影响耐火材料荷重软化温度的因素不仅包括材料的化学、矿物组成和显微结构等内在因素,而且包括原料的纯度、配料及烧成温度等外在工艺条件。
测量耐火制品荷重软化温度的方法有示差-升温法和非示差-升温法两种。示差-升温法的基本原理是:在规定的恒定压负荷和升温速率下,加热圆柱体试样,直至试样产生规定的压缩变形,测量在产生规定压缩变形量时相应温度。所采用的试样为直径50mm,高度50mm的圆柱体,中心钻一直径为ϕ12~13mm的贯通圆孔,上、下底面平坦并互相平行。将试样置于电阻炉内支撑体与加压柱之间,对致密耐火制品加压0.2MPa,对定形隔热制品加压0.05MPa,升温速率4.5~5.5℃·min-1。记录试样中心温度及变形量,得温度-变形曲线。再用事先已测得相当于试样通常高度的氧化铝管温度-膨胀曲线对所测曲线进行校正。分别记录自试样最高点压缩试样原始高度的变形量0.5%、1%、2%和5%时相应的温度,即为荷重软化T0.5、T1、T2、T5的温度。
非示差-升温法的测试方法为:将直径36mm、高度50mm的圆柱体试样以恒定的负荷0.2MPa在电阻炉内加热,升温速率在低于最高膨胀点的150~200℃以前为10~15℃·min-1,以后为5~6℃·min-1。测定试样温度-变形曲线。记录试样从膨胀的最高点被压缩0.3mm时的温度为软化开始温度(或称0.6%变形温度),试样自膨胀最大点被压缩2mm的温度为软化变形温度(或称试样的4%变形温度)。
1.2.4.3 高温蠕变性
当耐火材料在高温下承受小于其极限强度的某一定荷重时,产生塑性变形,变形量会随时间的延长而逐渐增加,甚至会使耐火材料破坏,这种现象叫蠕变。耐火材料的高温蠕变性是指制品在恒定的高温条件下受应力作用随着时间的变化而发生的等温形变。
高温蠕变的检测方法为:恒压下,以一定速率升温,到达指定温度后长时间保温,记录随时间的变化试样在高度方向的变形量,计算蠕变率。计算公式为:
(1-19)
式中,P为耐火制品试样的高温压缩蠕变率, %;L n为试样恒温n小时后的高度,mm;L0为试样恒温开始时的高度,mm;Li为试样原始高度,mm。
由于耐火材料在高温、荷重条件的变形量及时间-形变曲线,是随着材质、升温速率、恒温温度、荷载大小等诸多因素的变化而变化的,而且差异极大。因此,对于不同材质的制品,应根据其使用条件单独规定高温蠕变试验温度等条件。
1.2.4.4 高温体积稳定性(重烧线变化)
耐火材料在高温下长期使用时,其外形尺寸保持稳定不发生变化(收缩或膨胀)的性能称为高温体积稳定性。通常用重烧线变化来判断制品的高温体积稳定性。
重烧线变化是指耐火制品试样加热到规定温度,保持一定时间,冷却到室温后所产生的残余膨胀或收缩。计算公式为:
(1-20)
式中,LC为试样重烧线变化率, %;L1为加热后试样的长度,mm;L0为加热前试样的长度,mm。
1.2.4.5 抗热震性
抗热震性是指耐火制品对温度迅速变化所产生损伤的抵抗性能。耐火材料在使用的过程中,经常受到环境温度的急剧变化作用,例如,盛钢桶衬砖在浇注过程中,冶金炉(转炉、平炉或转炉)的加料、出钢或操作中炉温变化等,导致制品产生裂纹、剥落,甚至崩溃。此种破坏作用不仅限制了制品和炉窑的加热和冷却速率,限制了炉窑操作的强化,而且也是制品、炉窑损坏较快的主要原因之一。
影响耐火材料抗热震性的因素非常复杂。一般来说,材料的线膨胀系数小,抗热震性就好;材料的热导率高,抗热震性也好。另外,材料的颗粒度组成、致密度、气孔大小和分布、制品形状等均对其抗热震性有影响。
对于不同的耐火材料,其抗热震性的检测方法也不同,主要包括水急冷法和空气急冷法两种。
1.2.4.6 抗渣性
抗渣性是指耐火材料在高温下抵抗炉渣的侵蚀和冲刷作用的能力。抗渣性是耐火材料重要的使用性能,对于改善耐火材料的生产工艺、指导其正确使用具有重要意义。
影响耐火材料抗渣性的因素有耐火材料的物理化学性质及组织结构、熔渣的性质以及熔渣与耐火材料的相互作用条件等。在实际生产中,应根据熔渣的特点和性质,结合使用条件,选择与熔渣相适应的耐火原料和适宜的生产方法,以保证获得组织致密、结构均匀的耐火材料。
抗渣性的测定方法主要包括静态法和动态法两大类。
1.2.4.7 抗氧化性
抗氧化性是指含碳耐火材料在高温氧化气氛下抵抗氧化的能力。含碳耐火材料具有优良的抗渣性和抗热震性能,因此在冶金行业中具有广泛的用途。但是,碳容易被氧化,一旦碳氧化,则制品的性能将不复存在。提高含碳制品的抗氧化能力,特别是高温条件下的抗氧化能力,是含碳耐火材料的重要研究内容。
抗氧化性的测试方法如下。
对于含氧化抑制剂的含碳耐火材料,将试样置于加热炉内,在氧化气氛中按规定的加热速率加热到试验温度,并在该温度下保温一定时间,冷却到室温后切成两半,测量其脱碳层厚度。试样为边长50mm的正方体或直径与高度均为50mm的圆柱体。升温速率为从室温到1000℃为8~10℃·min-1,从1000~1400℃为4~5℃·min-1。以4L·min-1的流量向炉内通空气。保温时间为2h。
对于不含氧化抑制剂的含碳耐火材料,将边长为50mm的试样首先进行碳化,测定残存碳含量,称量碳化后的质量。然后置于炉内,在氧化气氛中以8~10℃·min-1的速率升温至1000℃,在该温度下保温5h。冷却至室温后,称量氧化后的质量。利用所测数据,计算失碳率。
关于其他非含碳耐火材料,如Sialon、AlON及氮化物耐火材料,目前还没有统一的测试抗氧化性能的标准。
1.2.4.8 抗水化能力
碱性耐火材料,如CaO、MgO等,在生产、保存及使用的过程中,都有与环境中的水发生反应而丧失强度甚至粉化的现象,称为水化反应。水化反应严重影响了某些耐火材料的生产与应用。表示水化反应程度的方法有以下三种。
(1)在规定时间内,制品发生水化反应的量占试样总量之比例。计算公式为:
(1-21)
式中,L S为水化程度, %;m1为试样原始质量,g;m2为除去已水化疏松部分的质量,g。
(2)测量试样截面的水化层厚度,即水化深度,用mm或μm表示。
(3)水化质量增加百分率。计算公式为:
(1-22)
式中,M S为水化质量增加率, %;m1为试样原始质量,g;m2为试样水化后质量,g。
当前普遍采用的抗水化措施:一是提高原料的煅烧温度,降低其化学反应活性。如白云石的煅烧温度在900~1000℃,在大气中极易水化,当煅烧温度提高到1600℃时,置于大气中2~3个星期后才开始发生水化疏松现象。镁砂也是利用提高煅烧温度的方法来提高抗水化能力的。也可加入少量添加剂促进烧结来防止水化。
另一种方法是在材料的表面包覆一层有机物(或无机物)以隔绝空气中的水与制品接触。如在活性石灰的表面包覆一层硅油。通过高温浸煮,在制品的表面包覆一层沥青或石蜡。另外,提高制品的致密度,降低气孔率,也是提高材料抗水化能力的措施之一。
本章小结
作为高温结构材料,耐火材料在使用过程中受到多种物理、化学因素的综合作用,为了满足各种使用条件的需要,对不同用途的耐火材料的使用性能要求是不一样的。而耐火材料的使用性能是由其化学矿物组成、结构性能、力学性能和热学性能来决定的。因此,本章从耐火材料的化学矿物组成及显微结构入手,介绍了以上几方面的内容。本章的内容是耐火材料的共性问题,是学习、理解耐火材料的基础。
思考题
1.请说明耐火材料的化学、矿物组成及其显微结构特征。
2.耐火材料的结构性能包括哪些?并说明其含义。
3.耐火材料的力学性能有哪些?
4.耐火材料的热学性能分别为什么?
5.何为耐火材料的主要使用性能?并分析各自的意义。