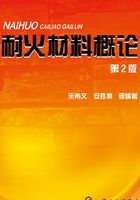
3.6 高铝质耐火材料
由Al2O3-SiO2二元相图中的高铝区可以看出高铝质耐火材料的基本相关系。以Al2O3/SiO2等于2.55为分界线。当Al2O3/SiO2比值大于2.55时,组分处于刚玉-莫来石区,高温稳定相为刚玉和莫来石。这是特级(Al2O3含量大于90%)、Ⅰ级(Al2O3含量大于75%)和高Ⅱ级(Al2O3含量72%~75%)高铝砖的组成区域。在这类制品中,由于Al2O3含量高,莫来石呈连续连锁网络状而构成骨架。刚玉分布在莫来石骨架间,这种结构给这类材料以较好的高温力学性能。当Al2O3/SiO2比值等于2.55时,组分处于莫来石固溶区,这是纯莫来石制品的组成区。这种制品的物相组成是莫来石。高的莫来石含量给这种制品带来了特有的高热稳定性能。当Al2O3/SiO2比值小于2.55时,组分处于SiO2-3Al2O3·2SiO2区,这类制品的基本物相组成是石英和莫来石。这是低Ⅱ级(Al2O3含量65%~72%)和Ⅲ级(Al2O3含量48%~65%)高铝砖的组成区。在这类制品中,高温稳定相莫来石的含量随Al2O3含量的增加而增加。莫来石含量的增加可以改善这类制品的高温力学性能。
3.6.1 高铝制品的生产工艺要点
高铝制品的生产工艺与多熟料黏土制品的生产工艺基本相同,但比黏土制品工序增加了破碎前的熟料捡选和筛分后除铁的工序。原料的严格分级、颗粒料分级贮存和除铁、部分熟料和结合黏土的混合细磨等措施,对提高和稳定高铝制品的质量具有重要意义。
矾土熟料在使用时,首先要按不同等级原料的外观拣选标准进行严格的分级拣选,分级堆放,以避免掺杂、混合。根据不同等级高铝制品的质量要求选用不同等级的矾土原料,有利于合理使用,精料精配,尽可能不使用混级严重的原料。熟料的质量取决于煅烧温度,通常煅烧温度应达到或略高于矾土的烧结温度,以保证熟料充分烧结和尽可能高的体积密度,并使二次莫来石化和烧结收缩作用在煅烧过程中完成。
矾土熟料的质量控制,除了要求一定的化学组成外,还用体积密度值衡量,特级品≥3.00g/cm3,Ⅰ级品≥2.80g/cm3,Ⅱ级品≥2.55g/cm3,Ⅲ级品为≥2.45g/cm3。
采用软质黏土或半软质黏土作结合剂,同时还加入少量有机结合剂(如纸浆废液等),以改善坯料的成型性能,提高坯体的强度。在确定黏土使用量时,应考虑在制品烧成时,结合黏土和熟料反应生成二次莫来石所产生的体积效应。对Ⅰ、Ⅱ级高铝制品的配料中,结合黏土不宜多加,一般波动于5%~10%;对Ⅲ级高铝制品,黏土基本上不和Ⅲ级矾土熟料反应生成二次莫来石,故可根据成型及烧成工艺要求以及制品的质量要求而适当多加,常用量为15%~20%。若用生矾土细粉代替黏土作结合剂,可以彻底解决二次莫来石效应的影响,但工艺复杂,给生产带来困难。
高铝砖料的颗粒组成与多熟料黏土砖料相似,采用粗、中、细三级配合。颗粒范围一般为3.0~0.5mm(粗)、0.5~0.088mm(中)、<0.088mm(细)。三级配合应符合“两头大、中间小”的原则,减少中间颗粒,增加细粉,并适当增大临界颗粒尺寸,可以获得气孔率低、荷重软化温度和热震稳定性高以及结构强度大的制品。
提高成型压力是降低气孔率的重要因素。生产实践表明,普通高铝砖的成型压力应达到137MPa,高密度高铝砖的成型压力应为176~215MPa。也就是说,只有采用250t的摩擦压砖机成型,才能取得这样的效果。成型时对砖坯有适当的放尺,放尺率的大小,主要与泥料性质、成型方法和装窑方向有关,其精确数值要通过试验来确定。
制品的烧成温度,主要取决于矾土原料的烧结性。用特级及Ⅰ级矾土熟料时,由于原料的组织结构均匀致密,杂质Fe2O3、TiO2含量偏离,使坯体容易烧结,安全烧成温度范围较窄,容易引起过烧或欠烧。采用Ⅱ级矾土熟料制砖时,由于二次莫来石化造成的膨胀和松散效应,使坯体不易烧结,故烧成温度略高。至于Ⅲ级矾土熟料,组织致密,Al2O3含量低,烧成温度较低,一般略高于多熟料黏土制品的烧成温度约30~50℃。
但是,在高铝耐火材料中,往往含有R2O、RO、Fe2O3等杂质氧化物。它们与Al2O3及SiO2在高温下反应生成液相。在Al2O3-SiO2-R2O系统中,在高温下液相量的增长速度随着温度的提高而加快。这样,由于提高烧成温度而带来液相量的大量增加、液相黏度的降低都会导致制品的变形及制品高温性能的降低。故在以液相烧结为主的烧结过程中,宜采用较低的烧成温度和较长的保温时间。生产实践表明,Ⅰ、Ⅱ级高铝制品可采用同一烧成温度。用倒焰窑烧成时,一般为1430~1450℃,保温40h;Ⅲ等高铝砖为1390~1420℃。用隧道窑烧成时,分别为1550~1560℃及1450~1500℃。高铝砖一般采用平码装窑,有时为避免产生黑心,也可采用侧码,码垛高度应小于1000mm。烧成在氧化焰中进行。
3.6.2 高铝制品的种类、性能与应用
3.6.2.1 普通高铝砖
高铝砖的主要矿物组成为莫来石、刚玉和玻璃相。随着制品中Al2O3含量的增加,莫来石和刚玉相的数量也增加,玻璃相相应减少,制品的耐火度和高温性能随之提高。玻璃相的数量增加和黏度降低均会破坏高铝砖的结构,尤其是K2O、Na2O的存在不仅使生成液相的温度降低,而且使液相黏度下降,导致制品的高温强度迅速下降。对于Al2O3含量低于72%的高铝制品,唯一的高温稳定相是莫来石,它随Al2O3含量增加而增多;对于Al2O3含量在72%以上的高铝制品,高温稳定晶相是莫来石和刚玉,随着Al2O3含量增加,刚玉量增多,莫来石量减少,相应地提高了制品的高温强度。
Ⅲ级高铝制品和黏土制品的性能相近,其主晶相为莫来石和玻璃相。由于其高温性能较黏土砖的好,能用黏土砖的场合均可使用Ⅲ级高铝制品。Ⅱ级高铝制品的Al2O3含量范围为65%~75%,相当于莫来石矿物的组成。但因原料的组成分布不均匀,部分Al2O3未与SiO2化合,而以刚玉形态单独存在。该类制品的高温性能要明显优于黏土制品。Ⅰ级高铝制品的主晶相是莫来石和刚玉。由于刚玉的化学稳定性和耐火性比莫来石高,因此制品中刚玉含量越多,制品的耐火性和抗侵蚀性越高。但刚玉的热膨胀系数远远大于莫来石,其线膨胀系数α0~1000℃分别为(0.8~0.85)×10-6℃及(0.5~0.55)×10-6℃,因而刚玉含量增多时,会使制品的抗热震性能降低。
高铝制品的重要工作性能是荷重软化温度和高温蠕变性。荷重软化温度随制品中的Al2O3含量的增加而提高,如图3-8所示。Al2O3含量在70%以下制品,荷重软化温度取决于莫来石晶相与液相间的数量比例。Al2O3含量在70%~90%间的莫来石-刚玉制品,随Al2O3含量增加,荷重软化温度提高不明显,这是由于原料中Fe2O3、TiO2成分随Al2O3含量的增加而稍有增多,改变了高温液相的数量和性质。高温下莫来石晶相部分软化,刚玉数量虽有增加,但不能形成骨架,因而导致荷重软化温度无明显的提高。只有当制品中Al2O3含量>90%,甚至达到95%以上时,制品中的主晶相是刚玉,晶粒之间直接结合率明显提高,液相只是存在于晶粒间的空隙中,其荷重软化温度才显著提高。

图3-8 高铝砖中Al2O3含量和荷重软化温度的关系
高铝制品的高温蠕变性用蠕变速率来表示。Ⅰ、Ⅱ级高铝砖的扭转蠕变速率相近,在1200℃下,其蠕变速率为0.25~0.29×10-5rad·h-1;而Ⅲ级高铝砖在相同温度下则为3.5×10-5rad·h-1,比Ⅰ、Ⅲ级高铝砖高10倍。物相分析表明,Ⅰ、Ⅱ级高铝砖中玻璃相量7%~9%,Ⅲ级高铝砖为20%。蠕变速率不仅与玻璃相含量有关,而且与玻璃相的组成及其高温黏度有关。Ⅲ级高铝砖在1200℃时液相的表现黏度为0.49×1014Pa·s,只相当于Ⅰ级高铝砖一半(0.9×1014Pa·s);为Ⅱ级高铝砖的26%(1.9×1014Pa·s)。由此看出,Ⅲ级高铝砖的蠕变行为,玻璃相起主导作用,而Ⅰ、Ⅱ级高铝砖,除玻璃效应外,晶界蠕变起重要作用。晶相间的直接结合率越高,晶界蠕变作用越明显。显然,在生产中提高原料纯度,改变基质的化学、矿物组成,减少玻璃相数量及调整玻璃相组成,是提高高温蠕变性的关键。同时也能改善高温体积稳定性和抗渣性能。
高铝制品的热震稳定性差,这与制品的物相组成密切相关。在生产中,通常采用调整泥料的颗粒组成,改善制品的颗粒结构特征等措施来适当提高其热震稳定性。近年来,在配料中加入适量的合成堇青石(2MgO·2Al2O3·5SiO2),锆英石微粉等,制造高热震稳定性高铝制品,取得一定成效。
高铝制品广泛应用于冶金、机械制造、石油化工、动力以及轻工等工业生产领域所用的热工设备的内衬材料。
3.6.2.2 改性高铝砖
(1)高荷软高铝砖。高荷软高铝砖和普通高铝砖相比,所不同的是基质部分和结合剂部分。①基质部分除添加三石精矿外,按照烧后化学组成接近莫来石的理论组成,合理引入高铝物料(磨细的高铝矾土、工业氧化铝或α-Al2O3微粉、刚玉粉、高铝刚玉粉);②结合剂选择优质球黏土等,视品种不同采用黏土复合结合剂,或莫来石质结合剂。通过采用以上办法,使高铝砖的荷重软化温度提高50~70℃。
(2)微膨胀高铝砖。微膨胀高铝砖是以高铝矾土为主体原料,添加三石精矿,按照高铝砖生产工艺流程制成。为使高铝砖在使用过程中适量膨胀,关键选择好三石矿物和其粒度,控制好烧成温度,使所选的三石矿物部分莫来石化,残留部分三石矿物。残留的三石矿物在使用过程中进一步莫来石化(一次或二次莫来石化),伴着膨胀反应。选择的三石矿物以复合材料为好。因三石矿物的分解温度各不相同。莫来石化产生的膨胀也各有差异,利用此特征,高铝砖因工作温度不同而有相应的膨胀效应,挤紧砖缝,提高砖的整体密实性,从而提高了砖的抗熔渣渗透能力。
(3)低蠕变高铝砖。我国长期在热风炉中使用的黏土砖、高铝砖的考核指标中,主要是荷重软化温度,未提出蠕变率的指标要求。经过长年使用,出现了砖的变形、开裂、下沉等问题,如果热风炉风温提高,此类问题更加突出。随着炼铁高炉大容积、高风温技术及长寿化的发展,对热风炉用耐火材料提出了更高的要求,要求材料能承受长期热应力和高风温等的作用而不易损坏。因此,要求热风炉用高铝砖具有低的蠕变率。近几年,通过生产实践,明确并规范了热风炉用砖的蠕变率的要求,这对热风炉的长寿起着重要的作用。对低蠕变高铝砖的性能指标要求见表3-16。
表3-16 低蠕变高铝砖的性能指标要求

为了解决高铝耐火材料的抗蠕变性,采用添加有益矿物的办法,利用所谓的未平衡反应来解决。当蠕变温度为1550℃、1500℃时添加物为石英、三石矿物;蠕变温度为1450℃、1400℃、1350℃时,添加物为三石矿物,相应引入刚玉、α-Al2O3等;蠕变温度为1300℃、1270℃、1250℃时,添加物为三石矿物。其中,三石矿物、活性氧化铝等主要以基质形式加入,基质的完全或近于完全莫来石化是关键。因为基质的莫来石化,必将提高材料的莫来石含量,降低玻璃相含量,而莫来石优异的力学、热学性能有利于材料高温性能的改善或提高。为使基质完全莫来石化,控制Al2O3/SiO2比是关键。
有研究表明,在Ⅰ级高铝砖的生产中,加入15%~35%的硅线石精矿,可制得蠕变温度为1400~1450℃的高炉热风炉用高荷软、低蠕变高铝砖。对于蠕变温度为1500~1550℃的低蠕变高铝砖,除添加适量的硅线石外,还需加入一定量的莫来石;或采用部分电熔刚玉和硅石原料。
(4)磷酸盐结合高铝砖。磷酸盐结合高铝砖是以致密的特级或一级高铝矾土熟料为主要原料,磷酸溶液或磷酸铝溶液为结合剂,经半干法机压成型后,于400~600℃热处理而制成的化学结合耐火制品。它属于免烧砖,为避免在高温使用过程中制品收缩较大,配料中一般需要引入加热膨胀性原料,如蓝晶石、硅线石、叶蜡石、硅石等。与陶瓷结合的烧成高铝砖相比,其抗剥落性更好,但其荷重软化温度较低,抗侵蚀性较差,因此需加入少量的电熔刚玉、莫来石等,以强化基质。磷酸盐结合高铝砖适用于水泥窑、电炉顶、钢包等。
3.6.2.3 以硅线石族矿物为主原料的高铝质耐火制品
以硅线石族矿物为主原料生产的高铝质耐火制品,其最大特点是制品在使用过程中具有持续的抗蠕变性能。这与硅线石族原料的纯度高、抗蠕变性强以及其持续的莫来石转化因素相关,有的制品还与硅线石族原料的二次莫来石化相关。
以硅线石族矿物为主原料生产的高铝质耐火制品,由于原料本身的SiO2和Al2O3分布均匀,杂质含量低,故制品的组织结构均匀、致密,加热后的相组成比较接近于热平衡状态时的组成,因此,制品的性能优良。硅线石族精矿的Al2O3含量直接影响其应用效果。Al2O3含量越接近于其理论值,表明原料的纯度越高,则其应用效果越好,制品在烧成时的收缩越小或无收缩,其荷重软化温度也高。与相应组成的高铝砖相比较,用硅线石族原料所制产品的荷重软化温度能提高100~150℃。国内生产的几种硅线石砖和红柱石砖的典型性能指标列于表3-17中。
表3-17 几种硅线石砖和红柱石砖的典型指标

以天然硅线石族原料为主原料生产的高铝质耐火制品具有较高的荷重软化温度、热震稳定性好、耐磨性和抗侵蚀性优良,因此适用于钢铁、化工、玻璃、陶瓷等行业,如用作烟道、燃烧室、炉门、炉柱、炉墙及滑板等。在高炉上,为确保内衬结构的稳定性、密封性,避免碱性物的侵入和析出,或风口漏风,在出铁口、风口部位,选择内衬大块型组合砖结构的硅线石族耐火材料,延长了使用寿命。
3.6.2.4 莫来石质耐火材料
莫来石质耐火材料是以人工合成莫来石(或天然提纯莫来石)为原料制成的以莫来石为主晶相的耐火制品,属Al2O3-SiO2系列产品。当制品的Al2O3含量低于莫来石理论组成时,还含有少量方石英;当Al2O3含量高于莫来石理论组成时,含有少量刚玉。莫来石制品的抗高温蠕变能力远远优于包括特级高铝砖在内的其他普通高铝砖,它的高温性能可与硅质、镁质、刚玉质制品的某些性能相媲美,抗热震性远优于这些制品。对酸性及低碱度熔渣的侵蚀抵抗能力则优于镁质制品,但不及刚玉制品。莫来石质耐火材料从矿相组成上可分为莫来石、莫来石-刚玉、刚玉-莫来石三类。其Al2O3含量在68%~95%范围内变化,相组成分别为:莫来石制品为莫来石单相结合,莫来石-刚玉制品为莫来石和刚玉复相结合,主晶相为莫来石,次晶相为刚玉,刚玉-莫来石制品结合相主要为莫来石,主晶相为刚玉,也属复相结合范畴。从生产工艺分有烧结莫来石制品和熔铸莫来石制品两大类。
(1)烧结莫来石制品
烧结莫来石制品的生产工艺与高铝制品的生产工艺相似。采用合成莫来石熟料为颗粒料,细粉为合成莫来石熟料,或采用白刚玉、石英粉以及纯净黏土配制成相当于莫来石组成的混合细粉。将颗粒料和细粉按比例配合,常用配比为:颗粒料45%~55%,细粉(<0.088mm)55%~45%。均匀混合后,高压成型。烧成温度为1550~1600℃。当采用电熔合成莫来石熟料为颗粒料时,其烧成温度应大于1700℃。
配料可根据使用条件所确定的Al2O3含量而定,目前最常见的配料方法为:
①合成莫来石(烧结的或电熔的)为骨料+合成莫来石细粉;②合成莫来石(烧结或电熔)为骨料+合成莫来石细粉+Al2O3细粉+高纯黏土粉;③合成莫来石(烧结或电熔)与电熔白刚玉为骨料+合成莫来石细粉+Al2O3细粉+高纯黏土粉。
粒度配比应根据“两头大、中间小”的配料原则进行配制。用亚硫酸纸浆废液或聚合氯化铝或多聚磷酸盐作结合剂,经混炼均匀后,高压成型,于高温窑内烧成,烧成温度根据制品中Al2O3含量而定,一般在1600~1700℃。
莫来石质耐火材料中通常含有TiO2、Fe2O3、CaO、MgO、K2O和Na2O等杂质氧化物,天然原料生产的莫来石中的杂质含量要比人工合成原料高。这些杂质氧化物在莫来石中起熔剂作用,降低熔液的形成温度和黏度,增大液相的生成量,提高熔液对固相的溶解速率和溶解数量,但各杂质氧化物所起的作用强弱程度不同,其中以K2O和Na2O对液相形成温度影响最大,K2O和Na2O分别使其无变量点温度降低513~724℃,同时还起分解莫来石的作用。在这些杂质氧化物中,TiO2的影响最小,仅使无变量点温度降低101~107℃。当TiO2含量较少时,除了部分固溶于莫来石中形成有限固溶体,促进莫来石生成和晶体发育长大外,还有部分在高温下进入液相形成玻璃体。高温下Fe2O3在莫来石和刚玉中有一定固溶度,形成有限固溶体。它在刚玉中的固溶度较在莫来石中的高,由于固溶体的形成,使莫来石和刚玉的晶格格长大。Fe2O3对Al2O3-SiO2系材料的始熔温度与系统中的Al2O3含量或者说与Al2O3/SiO2比值有关,当Al2O3/SiO2<2.55时,始熔温度为1380℃,若Al2O3/SiO2>2.55时,始熔温度提高到1460℃,并随其Al2O3含量提高而逐渐提高。在还原气氛下,Fe2O3被还原成FeO而脱溶进入玻璃相,并使系统的始熔温度下降,分别下降至1240℃和1380℃。
总之,随着莫来石质制品中Al2O3含量的提高,其高温性能提高;而熔剂量增多,高温性能降低。据此,严格控制杂质氧化物含量,尤其K2O、Na2O和Fe2O3的含量,是获得高性能莫来石质耐火材料的重要措施。在含有碱类成分熔渣或气体环境中使用,对莫来石质耐火材料均具有严重的侵蚀作用。
(2)熔铸莫来石砖
熔铸莫来石砖主要由高铝矾土或工业氧化铝、黏土或硅石进行配料,在电弧炉内熔融,再浇注成型及退火制成,其主要矿物成分是莫来石。
由于莫来石组成高温熔液冷却析晶时会产生粗大、不均匀的结晶倾向,易使熔铸制品产生裂缝。根据Al2O3-SiO2二元系相图,系统的低共熔点组成靠近莫来石固溶体的临界组成。考虑到低共熔混合物具有良好的流动性和能够促使莫来石析晶过程中生成均匀且细小的结晶,使铸件产生裂缝的可能性大大降低。因此,对于熔铸莫来石制品的组成,从理论上分析,应该位于Al2O3 79%和SiO2 21%左右较合适。但在生产中还必须考虑到原料中存在着一定数量的杂质成分,它们在高温下会与Al2O3、SiO2反应而改变Al2O3/SiO2的比值,因而实际所取的Al2O3/SiO2比应稍低一些。
原料中的杂质对熔铸莫来石制品产生不利影响,主要表现在以下几方面。
①铁的氧化物和Al2O3、TiO2一样,可以部分地进入莫来石固溶体中,对制品的熔点影响不大。但铁的氧化物容易促进玻璃相形成,增加玻璃相含量,使铸件的玻璃部分染成深色,降低制品的耐火性能。
②碱金属氧化物对莫来石结晶的影响更大,它起助熔剂作用,会促使莫来石熔融分解并析出刚玉,同时产生较多的玻璃相。
③CaO对于莫来石的结晶过程也有影响,加入11.5%石灰时,会阻碍莫来石析晶。
④MgO对于莫来石结晶的影响次于CaO,少量存在时,会生成莫来石、镁尖晶石、堇青石和刚玉等,相应地降低莫来石数量。
⑤原料中的Fe2O3可以靠加入木炭或焦炭等还原剂,在熔融过程中还原除去,反应式为:
(3-12)
(3-13)
(3-14)
最终生成硅铁(FeSi)沉于炉底。因此,对于铁、硅氧化物含量较高的原料要注意处理好硅铁问题,否则,硅铁穿透炉底会造成漏炉事故。
熔化过程中原料中的TiO2、CaO、MgO、R2O等杂质不能被还原除去,除少量的TiO2能固溶于莫来石中以外,其他主要是存在于玻璃相中。因此,杂质成分增多,会使制品中的玻璃相和刚玉含量增多,并促使莫来石形成粗晶结构,从而使熔铸制品的气孔率增高,抗热震性和抗侵蚀性能降低,铸件易出现裂纹。
莫来石从熔融状态直接凝固析晶,并不预先析出刚玉。但实际生产中由于加入了一定量的助熔剂(含R2O),熔融物冷却时首先析出的是刚玉晶体,而莫来石晶体要在1750~1800℃以下才开始稳定地析出。所以应保证在熔体开始析晶至1750℃之间的温度范围内迅速冷却,而在低于莫来石开始析晶的温度,要有适当的保温时间,或充分地缓慢冷却,以便早期析出的刚玉晶粒有足够时间与熔液作用形成莫来石,从而使制品中莫来石有最大的含量。
为了促使在铸件中形成微晶结构,在配料中加入适量的ZrO2,可提高熔液的黏度,抑制莫来石晶体长大的速度,有利于均匀地析出细晶。而且ZrO2还可充当玻璃相中的骨架,促进形成微晶结构,减少裂纹,在一定程度上减弱了助熔剂的不良影响。通常加入5%~7%的ZrO2,就能改善熔铸莫来石砖的性能。
典型的莫来石制品的主要性能示于表3-18中。
表3-18 典型的莫来石制品的主要性能

莫来石质耐火材料广泛应用于冶金工业的热风炉、加热炉、钢包,建材工业的玻璃窑焰顶、玻璃液流槽盖、蓄热室,机械工业的加热炉,石化工业的炭黑反应炉,耐火材料和陶瓷工业的高温烧成窑及其推板、承烧板等窑具。