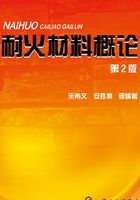
3.3 硅质耐火材料
硅质耐火材料是以二氧化硅为主要成分的耐火材料,包括硅砖、特种硅砖、石英玻璃及其制品。硅砖是以硅石为原料,以石灰乳、铁磷、纸浆废液为结合剂和矿化剂,在高温下烧成的酸性耐火材料。对酸性炉渣抵抗能力强,但受碱性渣强烈侵蚀,易被Al2O3、K2O、Na2O等氧化物作用而破坏,对CaO、FeO、Fe2O3等氧化物有良好的抵抗性。其荷重软化温度高、体积膨胀小、有良好的导热性。残余膨胀性保证了砌筑体有良好的气密性和结构强度,目前仍然是焦炉、玻璃熔窑、高炉热风炉、硅砖倒焰窑和隧道窑、有色冶炼和酸性炼钢炉及其他一些热工设备的良好筑炉材料。但其最大缺点是抗热震稳定性低,耐火度不高,这限制了它的广泛应用。
3.3.1 硅质耐火材料生产的物理化学原理
纯SiO2的熔点为1713℃。SiO2存在的晶型较多,外界条件改变时,会发生由一种晶型向另一种晶型的转变,并伴随着一定的体积变化。SiO2晶型转变、转变温度及伴随的体积变化如图3-2所示,各变体的性质见表3-8。SiO2的晶型转变可分为两大类:位移型转变和重建型转变。位移型转变不必打开结合键,只是原子的位置发生位移和Si-O-Si键角的稍微变化;转变时体积效应不大,到了一定温度突然发生,而且在整个晶体内同时发生骤然转变;转变是不可逆的。石英、鳞石英和方石英的不同晶型之间的转变均为位移型转变。重建型转变要打开旧键,建立新键,故转变活化能较高,转变速度较慢,往往是从晶体表面开始逐渐向内部推进,转变时伴随着较大的体积效应。石英、鳞石英和方石英之间的转变便属此类转变。

图3-2 SiO2的晶型转变与体积变化
表3-8 SiO2各变体的性质

①由于非均质体内部结构的影响,光的折射率值随方向的改变而发生有规律的变化,当一束平行光射入非均质体时,除光轴方向外,都要发生双折射,即分解成两束振动方向相互垂直,传播速度和折射率不等的偏振光。一轴晶只有两个折射率(常光o,非常光e),当常光小于非常光时为正光性,当常光大于非常光时为负光性。
由表3-8及图3-2可以看出,SiO2在常压下有多个变体,且硅砖的组成决定其性能,所以硅砖中鳞石英、方石英、残余石英与玻璃相的相对含量对硅砖的性质有很大影响。虽然鳞石英的耐火度不如方石英高,但由于鳞石英晶体具有矛头状双晶结构,其在制品中能够形成相互交错的网络结构,有利于提高制品的荷重软化温度与高温强度。另外从膨胀率及热导率来看,高的鳞石英含量有利于提高制品的抗热震性、体积稳定性与热导率。
在硅砖生产中,由于鳞石英不能由石英转变而来,为了在硅砖组成中获得大量的对性能有利的鳞石英,必须添加合适的矿化剂。添加的矿化剂必须满足三个条件:首先,促进石英转化为密度较低的鳞石英;其次不显著降低硅砖的耐火度等高温性能;再次,防止在烧成过程中因相变过快导致制品的松散与开裂。在有足够数量的矿化剂存在时,β-石英在573℃转变为α-石英;在1200~1470℃范围内,α-石英不断地转变成亚稳方石英,同时,α-石英、亚稳方石英和矿化剂及杂质等相互作用形成液相,并侵入由石英颗粒转变为亚稳方石英时出现的裂纹中,促进α-石英和亚稳方石英不断溶解在所形成的液相中,使之成为过饱和熔液,然后以鳞石英的形式不断地从熔液中结晶出来。如液相量过少,而且主要是以CaO和FeO组成时,则析晶主要为方石英。在起矿化作用的氧化物中,碱金属氧化物最强,MnO、FeO次之。生产中常用矿化剂为CaO,对硅质耐火原料的耐火度降低不大,并有足够的矿化作用,同时使泥料具有足够的结合性和可塑性,使砖坯干燥后有一定的强度。矿化剂石灰乳和铁鳞(Fe2O3+FeO)平均粒径<0.088mm,加入量一般不超过3%~4%。也可以用硅酸盐水泥代替。另外也可采用非氧化物作为矿化剂,如用含氟的化合物作为矿化剂,可得到高的鳞石英转化率。
3.3.2 硅砖的生产工艺要点
(1)配料与成型。将主原料硅石粗颗粒(1~3mm)、中颗粒(0.088~1mm)和细颗粒(<0.088mm)按4∶2∶4的比例配料。为了促进石英的转化,在配料中加入少量矿化剂(通常为FeO,CaO或MnO)。将硅石、矿化剂与适量的石灰乳或纸浆废液等结合剂充分混合后制成砖坯。
(2)干燥。砖坯的干燥速率视结合剂的性质而定。一般来说,用石灰乳作结合剂时,干燥速率可快些;用亚硫酸纸浆废液作结合剂,干燥速率应小一些,否则会导致硅砖龟裂。
(3)烧成。烧成是制造硅砖最为关键的一道工序,是前面数道工序质量的综合反映和检验。在烧成过程中,既要保证砖坯中石英向着所需要的方向转变,又要最大限度地防止石英转变而产生裂纹。因此,要根据砖坯特性、产品品种、窑炉结构、装出料方式等具体情况制定合理的烧成制度。
3.3.3 硅砖的种类、特性及应用
3.3.3.1 普通硅砖
(1)化学成分和矿物组成。硅砖的化学成分随硅石原料的不同而异。一般SiO2含量为93%~98%,Al2O3+Fe2O3+CaO为2.0%~0.7%。普通硅砖的矿物组成以磷石英为主,约占30~70%;高硅质高密度硅砖以方石英为主,约为20%~80%;残存石英和非晶态石英均为少量。
(2)耐火度和荷重软化温度。硅砖的耐火度主要决定于SiO2与杂质的含量及性质。SiO2含量越高、杂质含量越低,耐火度越接近于SiO2的熔点;反之,耐火度越低。硅砖的耐火度一般在1690~1730℃。
硅砖的荷重软化温度较高,约为1650℃。这主要是因为构成硅砖的主晶相为具有矛头双晶的鳞石英,其形成网络结构,且基质为黏度较大的玻璃相。硅砖的荷重软化温度和耐火度接近,这是硅砖的一个显著特点。
(3)热震稳定性。硅砖的抗热震稳定性差,在850℃下水冷仅为1~2次。原因在于硅砖在高温急冷过程中,将发生晶型转变,从而引起较大的体积变化。这是硅砖的一大弱点。
(4)抗渣性。硅砖是酸性耐火材料,对酸性及弱酸性炉渣和含腐蚀性炉气的侵蚀有很强的抵抗能力。
(5)高温体积稳定性。在加热过程中,硅砖除存在一定的热膨胀外,还发生晶型转变并伴有体积膨胀。如果砖内存在未转变的残存石英,高温下将继续变成鳞石英或方石英,产生较大的体积膨胀。
根据硅砖的特点,目前主要用于砌筑玻璃熔窑和焦炉的炉衬材料。在加热烘烤过程中,应缓慢升温,以免因膨胀过激而使砌体破坏。
3.3.3.2 特种硅砖
随着炼焦工业的发展,对焦炉硅砖的质量要求日益提高,特别是碳化室用硅砖要求具有高密度、高导热性及较高的高温耐压强度等性能,因此制造高密度、高导热硅砖引起了人们的重视。
(1)高密度硅砖
高密度硅砖与普通焦炉硅砖的性能比较见表3-9。
表3-9 高密度硅砖与普通焦炉硅砖的性能比较

(2)高密度高纯硅砖
高密度高纯硅砖是用纯石英岩(含SiO2>98%)作原料,加入少量矿化剂和结合剂(CaO+FeO<1.5%)制成的硅质耐火制品。高密度高纯硅砖的一般性质见表3-10。
表3-10 高密度高纯硅砖的理化指标

(3)高密度高导热性硅砖
目前提高硅砖热导率的途径主要是靠增加磷石英含量(见图3-3),降低制品的气孔率(见图3-4)或加入一些高导热性的金属氧化物,如CuO、Cu2O、TiO2、Fe2O3等。

图3-3 硅砖的磷石英含量与热导率的关系

图3-4 硅砖的显气孔率与热导率的关系
高导热硅砖首先应具有较低的气孔率和较高的体积密度。如前所述,通过采取纯净的硅石原料,调整颗粒组成,选择适宜的矿化剂和高压成型等工艺措施,可以制得砖坯密度大于2.33g·cm-3、气孔率低于16%的硅砖。
选择特殊硅石原料和可转化成SiO2的添加物,严格控制烧成制度,控制烧成气氛,对于开发高密度、高热导率硅砖是有益的。选择的硅石原料中含其他的矿物量要少且分布均匀,特别是Al2O3和碱的含量要少,要保证生成最大量的鳞石英。而选择SiO2组成添加物对提高热导率和降低气孔率也是非常重要的,因为生成的SiO2沉积在砖的气孔中,从而减少了总的气孔率。常用的添加剂有SiC,Si3N4和金属硅等,其中加入2%~3%的金属硅可以得到最佳性能的高密度硅砖。
加入CuO、Cu2O、TiO2、Fe2O3等金属氧化物可以有效地提高硅砖的热导率,其中以CuO效果较好。例如,加入CuO的高密度、高导热性硅砖,热导率至少提高20%。各种金属氧化物对硅砖导热性能的影响有如下顺序:CuO>Fe2O3>TiO2。随着配料中金属氧化物加入量的增加,制品的热导率有所提高,但会影响制品的耐火性能(如耐火度、荷重软化点等)。在现有原料条件下,在保证制品中SiO2大于93%时,为提高热导率,实际加入金属氧化物的数量一般不超过2%。否则其他性能将达不到标准要求。提高加入物的粉碎细度,改善其分散性,使其在坯料中均匀分布,可使制品热导率显著提高。加入物可以采用轧钢皮、轧铜皮、天然金红石、钛精矿等。CuO或Cu2O资源少,价格较贵,不能大量采用。含铁硅砖中加入轧钢皮,价格低廉,且易获得,但在使用过程中是否会产生碳素沉积作用,影响焦炉的使用寿命,尚有待进一步研究。我国TiO2矿资源较丰富。研究工作表明,采用天然金红石或精矿作为加入物,也取得较好效果。
高密度、高导热性硅砖的理化性能示于表3-11。
表3-11 高密度高导热性硅砖的理化性能

注:热导率为1000℃条件下的热导率。
3.3.3.3 熔融石英陶瓷制品
熔融石英制品是以熔融二氧化硅(石英)为原料经成型、烧结等工序制得的特种耐火材料,也称为石英玻璃陶瓷。熔融石英陶瓷制品分为两类:一类是熔融石英玻璃制品,另一类是熔融石英陶瓷制品(再烧结制品)。熔融石英陶瓷的制造方法很多,有模压法、捣打法、热压法、等静压法、泥浆浇注法等。其中采用较为普遍的是泥浆浇注法。
熔融石英陶瓷具有以下优良性能。
①低的线膨胀系数,与石英玻璃相同,为0.54×10-6/℃。由于膨胀系数小,所以其体积稳定性好,在砌筑时可以不留膨胀缝。②特别低的热导率,为2.09W·(m·K)-1,且在1100℃以下的温度范围内几乎不变,是一种理想的隔热材料。③优良的抗热震性,在1000℃与冷水的热交换循环次数大于20次。④它的常温电阻为105Ω,是很好的绝缘材料。⑤良好的化学稳定性,除氢氟酸及300℃以上的浓磷酸对其有侵蚀外,盐酸、硫酸、硝酸等对它几乎没有作用,与锂、钠、钾、铀、铯、锌、镉、铟、碲、硅、锡、铅、砷、锑、铋等金属熔体也不发生作用,能耐玻璃熔渣的侵蚀。
它的缺点如下。
①机械强度较低,浇铸制品的常温耐压强度约45MPa,但其强度随温度升高而增加,这是不同于其他几种氧化物陶瓷的特点。例如,氧化铝陶瓷从室温升到1000℃时,其强度值降低60%~70%,而石英玻璃陶瓷却提高了33%,这是因为熔融石英陶瓷随温度升高而发生局部软化,起到了黏结作用而减小脆性之故。②荷重软化点较低为1250℃。但由于其热导率低,在没有接触高温的部位仍可维持使用到该温度以上。③在过高温度下烧成或使用时会发生析晶,由玻璃相转变为晶相。由于熔融石英陶瓷的这个性质,限制了烧成温度的提高,从而难以制得致密、高强的制品,也就影响了制品的使用性能。但在使用时,由于析晶是在石英玻璃陶瓷表面开始的,初生的晶体牢固地附着在没有转化的石英玻璃相上,加之石英陶瓷的热传导慢,在表面析晶后,里层玻璃相的继续析晶就很缓慢,所以即使表面有结晶,但制品仍可以在较高温度下使用而不会很快破坏。
由于熔融石英陶瓷所具有的优良性能,其成本比石英玻璃制品低得多,又可制造出用石英玻璃难以制造的大型厚度制品,所以作为特种耐火材料和其他功能材料而得到广泛应用。在化工、轻工工业中,用石英玻璃陶瓷作耐酸、耐蚀容器、化学反应器的内衬、玻璃熔池砖、拱石、流环、柱塞以及垫板、隔热材料等。在金属冶炼中,石英玻璃陶瓷作为盛放金属熔体的容器、浇铸口、高炉热风管内衬等。尤其在炼钢中用作连续铸锭保护浇铸用长水口和浸入式长水口砖,对防止连铸板坯表面裂纹的产生、提高铸坯质量、改善劳动条件等都有显著效果。