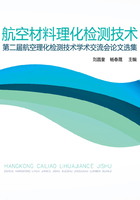
7075铝合金端面晶粒坑蚀试验研究
肖文,胡建雄,韩金军
(中航飞机起落架有限责任公司,陕西汉中 723200)
摘要:7075铝合金是铝-锌-镁-铜系超硬铝合金,经固溶处理和人工时效后具有很高的强度和硬度,但耐蚀性较差。铝合金表面处理过程中可使用碱清洗和酸清洗两种工艺,而两种工艺过程控制不当会造成铝合金表面产生坑蚀现象。必须对铝合金的碱清洗或酸清洗工艺过程进行控制,通过检测铝合金试样的坑蚀来评定碱及酸的清洗工艺。本文就试样的制备、检测方法、铝合金端面晶粒坑蚀的特征几个方面进行研究。
关键词:超硬铝合金;耐蚀性;碱清洗;酸清洗;端晶坑蚀
1 引言
铝合金质轻,比强度高,同时也具有优异的耐腐蚀性能、机械性能等,广泛应用于军工、民用、航空航天等多个领域,尤其在航空航天领域更加占据着不可替代的位置。然而其服役的环境变化无常,比如自然条件(大气腐蚀)、太空极端条件(宇宙风暴)、海洋苛刻条件(高温冲刷腐蚀),导致其使用寿命受到了巨大的挑战。
7000系铝合金是现代航空航天、武器装备等领域发展必不可少的关键结构材料,正向着高强、高韧、耐腐蚀、高淬透性方向发展。7075铝合金属于Al-Zn-Mg-Cu系,系热处理强化型合金,是在Al-Zn-Mg系铝合金基础上发展起来的,经固溶处理和人工时效后具有很高的强度和硬度,但耐蚀性较差,使该合金的推广应用受到制约。铝合金表面处理过程中可使用碱清洗和酸清洗两种工艺,而两种工艺过程控制不当会造成铝合金表面产生坑蚀现象。必须对铝合金的碱清洗或酸清洗工艺过程进行控制,通过检测铝合金试样的坑蚀来评定碱及酸的清洗工艺。
2 试验与方法
2.1 试验试件要求
7075铝合金要从7075-T6511或7178-T6511的型材上切取试样,以便使晶端暴露出来。也可以从余料或边角料上切取试样。所用的试样应与被处理的合金、成型工艺和热处理状态相同,试件尺寸为40mm×30mm×5mm,见图1和图2。切割试样时需要冷却,以避免试样过烧。

图1 端晶坑蚀和晶间腐蚀试样方位

图2 未经表面处理的试样(0号试样)
7075铝合金试样浸入溶液中达到要求的时间,以去除参考规范中规定的金属数量,如果参考规范中没有规定时间,将试样浸入溶液30min或所必要的时间,浸蚀的程度以每个面被去除0.0010in(0.0245mm)为准。为保证试件和零件一致的浸蚀效果,试样和零件一起经过全部操作(包括预先清洗及以后的清洗)之后,在规定的时间内,去除金属的金属量应满足图纸要求或达到规定的清洁度。晶间腐蚀和坑腐蚀的程度应满足参考规范中试验零件所规定的极限。
2.2 试样的镶嵌
对试样应进行镶嵌,镶嵌试样是为了更好地对试样进行磨抛,见图3。金相试样在镶嵌机中用环氧树脂或酚醛塑料制成镶嵌试样,当用环氧树脂或酚醛塑料镶嵌试样时,加热温度为160℃±5℃,压力≥1.5MPa,固化时间≥1h。选择不同的镶嵌材料时,应选用与之相符合的温度和时间。磨抛后再将试样的镶嵌料部分去除,与零件一同进行表面处理。

图3 镶嵌后的试样
2.3 试样的磨抛
用磨光机磨出检查面,然后用砂纸由粗到细进行磨光,磨光和抛光时每次磨削方向应相互垂直(互成90°角),且每次磨削时应将前一次的磨痕全部去除,最后抛光应用润滑油或氧化铝悬浊液,以得到良好的检查表面。磨抛后的试样用水、酒精依次清洗并吹干。
2.4 试样的粗糙度要求
用于试验的试样粗糙度至少达到Ra0.08μm。最终用于试验的试样状态见表1。
表1 用于试验的试样状态

2.5 端面晶粒坑蚀及晶间腐蚀的测定方法
磨抛好的试样放在100倍及以上倍数的显微镜下观察整个观察面,找出最深的凹坑并测量测出坑蚀深度,观察晶间腐蚀情况并测量晶间氧化深度。端晶坑蚀及晶间腐蚀测量方法见图4。

图4 端晶坑蚀的测定
利用激光共聚焦显微镜,不仅能检测B面边缘一条线上的凹坑分布情况,还可以看到A面上凹坑的形状及凹坑的分布情况,并通过激光共聚焦扫描的2.5D、3D等图像功能观察凹坑的形貌特征及测量凹坑的深度。
3 试验结果
3.1 未进行表面处理试样的表面形貌
为了分析试样表面处理前后的变化,首先对未进行表面处理的0号试样表面形貌进行观察,图5、图6分别给出了0号试样A面激光扫描图像和B面激光扫描3D图像,用于和表面处理后的试样表面形貌进行比较。

图5 0号试样A面激光扫描形貌图像

图6 0号试样B面激光扫描3D图像
3.2 碱清洗试样端面晶粒坑蚀检测
碱清洗工艺使用turco4090清洗液,溶液浓度37.5g/L~55g/L,温度71.1℃~87.8℃,腐蚀时间10min。在正常的工艺过程中,7075铝合金断面晶粒未发生端面晶粒坑蚀和晶间腐蚀,见图7;在超出工艺要求温度达到99℃,腐蚀时间仍为10min,7075铝合金发生了端晶坑蚀,见图8;在99℃温度下,延长腐蚀时间至30min,7075铝合金发生端晶坑蚀,见图9。端晶坑蚀的形貌特征为圆形坑和环形坑,经测量端晶坑蚀的坑直径在20μm~60μm,坑深度在40μm~60μm之间,见图10。

图7 1号试样B面激光扫描2.5D图像

图8 2号试样B面激光扫描2.5D图像

图9 3号试样B面激光扫描2.5D图像

图10 4号试样A面激光扫描2.5D图像
3.3 酸清洗试样端面晶粒坑蚀检测
酸清洗工艺过程中使用硝酸清洗液,溶液浓度300g/L~400g/L,温度为室温(25℃),腐蚀时间10min。在正常的酸清洗工艺下,5号试样的A面没有发生坑蚀现象,与未表面处理的0号试样(图5)相比较,A面未发生变化,见图11;在超出标准规定的溶液硝酸浓度的情况下,6号试样的A面有微孔出现,见图12;在超出标准规定的清洗时间30min的情况下,7号试样的A面有明显孔洞出现,见图13;在超出标准规定的温度下,8号试样A面出现了较大孔洞,见图14。

图11 5号试样A面激光扫描形貌图像

图12 6号试样A面激光扫描形貌图像

图13 7号试样A面激光扫描形貌图像

图14 8号试样A面激光扫描形貌图像
8号试样B面激光扫描3D图像与未表面处理的0号试样B面激光扫描3D图像(图6)相比较,可以看出原本平直的表面出现了孔洞,见图15。

图15 8号试样B面激光扫描3D图像
4 结论
在使用turco4090清洗液进行清洗的过程中,要注意溶液的浓度、清洗的温度、时间工艺条件,超出了工艺条件范围会引起端面晶粒坑蚀现象。
对7075铝合金的酸洗工艺过程,应严格控制酸洗的溶液浓度、酸洗溶液温度及酸洗的时间,超出了标准规定的酸洗工艺条件就会造成铝合金表面的坑蚀现象。
参考文献
[1]胡勇杰,周晓丽,任晓霞,等.发动机波纹管破裂原因分析[J].失效分析与预防,2013,8(3):178-182.
[2]王梅丰,李光东,杜楠.表面粗糙度对304不锈钢早期点蚀行为影响的电化学方法[J].失效分析与预防,2012,7(2):86-90.
[3]陈勃,刘建中,王浩伟,等.含点蚀铝合金的疲劳寿命预测技术研究进展[J].失效分析与预防,2012,7(1):50-56.
[4]罗勇,许晓静,张允康,等.强化固溶处理对7075铝合金晶间腐蚀和剥落腐蚀性能的影响[J].热加工工艺,2012,41(14):203-208.
[5]陈素晶,袁庆铭,何建平,等.7075铝合金瞬时腐蚀速率的计算和试验验证[J].材料工程,2014(12):43-46.
[6]李晓丹,翟玉春,纳邱峰,等.纳米SiC颗粒强化7075铝合金在NaCl溶液中的电化学腐蚀行为[J].腐蚀科学与防护技术,2012,24(2):139-143.
Investigation on End Grain Pitting Corrosion of 7075 Aluminium Alloy
Xiao Wen, Hu Jian-xiong and Han Jin-jun
(The aircraft landing gear Co., Ltd., Shaanxi, Hanzhong 723200,China)
Abstract:7075 aluminum alloy is Al-Zn-Mg-Cu super duralumin alloy with very high strength and hardness as well as poor corrosion resistance after solution treatment and artificial aging. Aluminum alloys can be treated use two kinds of surface treatment technology, alkali cleaning and acid cleaning, and the improper process methods will result in surface pitting corrosion phenomena for aluminum alloy, so the cleaning process must be controlled, which can be evaluated by pitting corrosion test. The preparation of samples, testing methods and characteristics of end grain pitting corrosion for 7075 aluminum alloy have been studied.
Keywords:Super duralumin aluminum alloy; Corrosion resistance; Alkali cleaning; Acid cleaning; End grain pitting corrosion