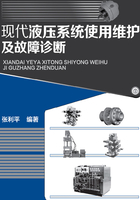
2.4 液压油液选用要点
正确选用液压油液,对液压系统适应各种工作环境条件和工作状况的能力、延长系统和元件的寿命、提高主机设备的可靠性、防止事故发生等方面都有重要意义。液压油液选用原则见表2-3。
表2-3 液压油液选用原则

2.4.1 品种的选择
目前各类液压设备使用的液压介质中,液压油达85%,具体选用时可从以下三方面入手。
①按工作环境和使用工况(液压系统的工作压力及温度)选择液压油液(表2-4)。
表2-4 根据工作环境和使用工况选择液压油液

②按泵的结构类型选择液压油液。液压泵对抗磨性要求的高低顺序为叶片泵>柱塞泵>齿轮泵。对于以叶片泵为主泵的液压系统,无论压力高低,都应选用HM油;对于以柱塞泵为主泵的液压系统,一般应选用HM油,低压时可选用HL油。
③检查液压油液与材料的相容性。初选液压油液品种后,应仔细检查所选油液及其中的添加剂对液压元件构件中的所有金属材料、非金属材料、密封材料、过滤材料及涂料的相容性。如发现有与油液不相容的材料,则应改变材料或改选油液品种。例如HM抗磨液压油除了与青铜、天然橡胶、丁基橡胶、乙丙橡胶不相容外,与大多数材料都相容。液压油液与常用材料的相容性可从手册(参考文献[3])查得。
2.4.2 黏度等级(牌号)的选择
黏度等级(牌号)是液压油液选用中最重要的考虑因素,因黏度过大,将增大液压系统的压力损失和发热,降低系统效率,反之,将会使泄漏增大也使系统效率下降。尽管各种液压元件产品都指定了应使用的液压油液牌号,但考虑到液压泵是整个系统中工作条件最严峻的部分,故通常可根据泵的要求(类型、额定压力和系统工作温度范围),确定液压油液黏度等级(牌号)(表2-5),按照泵的要求选择的油液黏度,一般对液压阀和其他元件也适用(伺服阀和高性能比例阀等除外)。
表2-5 按液压泵选用液压油液的黏度等级

2.4.3 难燃液压液的选用
对于高温或明火附近及煤矿井下的液压设备,不能用矿物油,而应采用难燃液,以保证人身设备安全。一般而言,可按表2-4进行初选,然后再从环境条件、工作条件、使用成本及废液处理几方面进行综合分析,最终得出最佳选择。
①液压设备的环境条件。若环境温度低(达0℃以下),用水-乙二醇较好,磷酸酯也可用。若环境温度高,则用磷酸酯较好。对于工作环境较为恶劣的液压设备,最好选用价廉、污染小的液压介质(如一部分牌号的高水基液体),以免因管道爆裂等原因导致外漏或排放时对环境造成污染。
②液压设备的工作条件。除了考虑液压介质与各类材料的相容性外,最主要应考虑液压泵的适应性与介质的润滑性。例如阀配流卧式柱塞泵,与所有水基难燃液均适应,但对于齿轮泵、叶片泵和轴向柱塞泵,因水基难燃液的润滑性较差,对泵的轴承寿命及摩擦副的磨损均有很大影响。从减少磨损、延长使用寿命考虑,对高压系统采用磷酸酯(其润滑性能接近矿物油)较好;对中高压及低压系统,采用油包水、水-乙二醇及高水基液体(其润滑性次于磷酸酯)为宜。通常,原有液压泵改用耐燃液压液时,应降低使用压力及转速。
③使用成本。主要应考虑设备改造、介质成本、维护监测及系统效率等因素。因油包水、水-乙二醇及磷酸酯的黏度较大,原有油压设备改用这些介质时,除了要更换不相容的材料及轴承外,其他变化不大。但对于高水基介质,则因黏度低,可能导致泄漏增大,原有元件应降压使用。关于介质的价格:磷酸酯价格最高,其次是水-乙二醇、油包水,高水基介质价格最低(是油包水的1/20)。关于系统的维护与检测:油包水要求最严,其次是磷酸酯和高水基介质,相对而言,水-乙二醇要求要低些。关于系统效率,高水基介质引起黏性阻力很小,系统效率最高;其他几种介质基本接近。
④废液处理。难燃液污染性强烈,不经处理不能排放。水-乙二醇对水中生物危害很大,故其废液必须单独收集并进行氧化或分解处理后才能排放。磷酸酯(比水重)或油包水(比水轻)可轻易地从废液池底部或顶部分离出来进行处理。高水基液较易处理,有可能直接排放而不会造成污染。