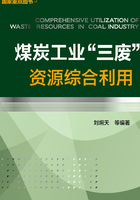
2.2 煤矸石生产含铝化合物
煤矸石作为化工原料,主要是用于生产无机盐类化工产品。例如南票矿务局用洗矸作原料,建成了一座年产1万吨的化工厂,生产氯化铝、聚合氯化铝和硫酸铝,并从提取氯化铝的残渣中制出氧化钛和二氧化硅;太原选煤厂利用煤矸石中含碳酸铁、硫酸铝和硫酸镁较高的特点制取铵明矾等。
选择合适的煤矸石为原料,能制备多种化工产品。
2.2.1 结晶氯化铝的生产工艺
结晶氯化铝呈浅黄色粉末,分子式为AlCl3·6H2O,代号BAC。它是新型净水剂、造纸施胶沉淀剂和精密铸造型壳硬化剂。氯化铝的生产原料包括金属铝、氢氧化铝、三氧化二铝或各种含铝矿物。一些煤矸石含有较高水平的铝,也是生产结晶氯化铝的优良原料。
一般煤矸石的硅铝比小于3,常用酸法生产。煤矸石中的铝主要以高岭石的形式存在,煤矸石受热分解可形成具有活性的Al2O3,加酸后形成AlCl3溶液,再经固液分离、浓缩、结晶,就可生产出结晶氯化铝。结晶氯化铝生产的原则流程见图2-29,生产过程主要包括矸石准备、焙烧、酸浸和浓缩结晶等主要环节[27]。

图2-29 结晶氯化铝生产原则流程
2.2.1.1 原料的选择和准备
实践证明,用煤矸石提取铝盐产品时,选择的原料一般应满足以下3个条件。a.矸石中杂质含量要低。尤其是含铁量应低于1.5%,钙、镁含量在0.5%左右。b.矸石中氧化铝含量要高。实际生产中氧化铝含量应在30%以上,以降低原料和盐酸的单耗。c.浸出率要高。一般Al2O3酸浸出率应大于60%。
由于原料焙烧速度和粒度大小有关,因此要先将原料破碎至8mm以下,然后加入沸腾炉中焙烧。
2.2.1.2 焙烧
焙烧的作用主要是使原料脱水、脱碳,破坏其内部分子结构,形成游离态的Al2O3和SiO2无定形混合物。焙烧后的熟料失去结晶水和有机物,形成无数的微孔,具有很大的活性表面,有利于提高浸出率。
焙烧温度对氧化铝浸取率有很大的影响。焙烧温度控制在600~700℃之间最佳。当温度高于850℃后,铝硅二次结合,重新重结晶成新相,非晶质Al2O3和SiO2不断减少,Al2O3与酸的反应性急剧减弱,浸出率降低。
由图2-30可以看出,煤矸石在400~700℃区间脱除H2O,其间逐步形成在酸中具有一定化学活性的偏高岭石,因而,浸取率随焙烧温度的提高而增加。当温度为700~800℃时,氧化铝转变为在酸中具有化学活性的γ-Al2O3,故浸取率较大。但随着温度的继续升高,γ-Al2O3逐步过渡为α-Al2O3,失去反应活性,导致氧化铝在酸中的浸取率急剧降低。

图2-30 焙烧温度对氧化铝浸取率的影响
2.2.1.3 酸浸
(1)酸浸反应
酸浸制取结晶氯化铝工艺的主要环节。浸出过程有连续和间歇法两种。因沸渣中除含活性Al2O3外,尚含有SiO2、Fe2O3、CaO、Ga2O3等,酸浸的主要反应有:
(2)影响酸浸反应的因素及控制
由于铁的金属性比铝更强,优先转入溶液,给浓缩、结晶和分离作业带来困难,影响质量和外观色泽。CaO和MgO很容易和HCl反应,增加了单位成品HCl的消耗量。因此这些杂质含量要严格控制。Ga2O3富集于滤液中,可用低碳脂肪酸萃取,回收镓。
从酸浸的主要反应看到,矸石和盐酸反应属于固-液多相反应,影响浸出率和速度的因素较多,生产中控制的主要因素如下。
①矸石的成分和性质 要求原料中Al2O3含量高,结构不复杂,杂质少。焙烧后形成活性Al2O3含量越高,越有利于浸出。反应时熟料的粒度越小,反应总表面积越大,浸出速度越快。粒度过细,由60目减小到100目时,浸出率略有增加,但粒度太细,使溶液浓度增加,造成渣液分离困难,因此粒度以小于60目为宜。
②反应温度 提高反应温度,在其他条件相同时,每增加反应温度10℃,则可提高浸出率1/5~1/2。但考虑到系统压力不宜太大,要保持良好的操作条件。因此反应温度一般控制在100~110℃之间。
③溶剂浓度 从理论上分析,用高浓度的盐酸浸取,化学反应激烈,浸出速度能提高一些,但酸的浓度过高,在反应中容易挥发造成单耗过高,污染环境。因盐酸浓度在20%时沸点最高,浸出效果亦较理想,所以选用20%浓度的盐酸作溶剂为宜。
④搅拌强度 增加搅拌强度,有利浸出反应进行,但增加到一定值后,对浸出速度影响不大。为了避免机械搅拌的腐蚀,一般采用压缩空气搅拌。
⑤反应时间 浸出时间与原料的内部结构有很大关系。一般反应时间增长,浸出率增加,但时间过长反应速率逐渐下降,同时设备生产能力降低,因此反应时间一般控制在1~1.5h。
2.2.1.4 渣液分离
氧化硅不与盐酸反应,在料浆中以硅渣固相的形式存在。我国多数生产厂均采用自然沉降工艺,使三氯化铝母液与硅渣分离。一般硅渣微粒(1~5μm)在料浆中沉降速度要受到渣粒大小、料浆密度、料浆的pH值和溶剂黏度的影响。为了加快沉降速度,在溶剂中可加入万分之五的聚丙烯酰胺溶液絮凝剂。
2.2.1.5 浓缩结晶
由沉降分离出来的三氯化铝液体,入浓缩器加热蒸发。为了提高浓缩效率,可采用负压蒸发。
当母液蒸发后达到过饱和状态时,出现新的固相,开始结晶过程,改变影响晶核生长速率和晶粒成长速率的因素,就可以控制晶粒的大小。
经渣液分离后的氯化铝浸出液,送入搪瓷浓缩罐中进行浓缩结晶。罐体夹套通入120~130℃的蒸汽加热,蒸汽压力保持在300~400kPa。为加快浓缩和结晶的速率,采用负压浓缩,真空度控制在665kPa以上。在加热和负压条件下,浓缩液内有大量结晶生成,当固液比达到1:1时,便可停止加热,打开底阀,将浓缩好的浓缩液放入缓冲冷却罐,使浓缩液冷却到50~60℃,晶粒进一步长大,以利于真空吸滤和单罐产量。
浓缩液脱水采用真空吸滤,将冷却后的浓缩液中的结晶氯化铝与饱和溶液用吸真空的方式进行分离。真空吸滤采用普通砖砌真空吸滤池,其内壁及池底衬三层玻璃钢及两层瓷板以加强防腐。池底向滤出液出口方向倾斜,池底上用小瓷砖砌成支撑柱,支撑上部的玻璃钢穿孔滤板,滤板上铺耐酸尼龙筛网。浓缩液放入池内,开启真空泵,滤出液通过尼龙筛网流入池底,筛网上剩余的黄色结晶便是结晶氯化铝的成品。
浓缩结晶后的料浆放入过滤器中,使晶体和滤液分离,得到的晶体即为结晶氯化铝成品。滤液加工成品,滤液循环,当滤液中铁含量超过控制指标时,就不再循环,而将其浓缩加工成3#混凝剂,供净化工业污水使用。
2.2.2 聚合氯化铝的生产工艺
聚合氯化铝的通式为[Al2(OH)nCl6-n·xH2O]m,简称PAC,属于阳离子型无机高分子电解质,相对分子质量为1000~2000。它是由碱式铝盐经缩聚而成的羟基铝聚合物,因此也称为碱式铝、羟基铝、络合铝和聚合铝等,可视为AlCl3水解成Al(OH)3的中间产物。聚合氯化铝分子结构中羟基化程度称为碱化度。碱化度高,说明聚合物的聚合度高,相对分子质量大,电荷量低,凝聚效能高。碱化度常用羟基铝当量比即B=[OH]/3[Al]×100%来表示。
聚合氯化铝是一种无机高分子化合物,其组成随原料及制作条件的不同而异,非单一固定的分子结构,而由各种络合物混合而成,属可水解阳离子的无机盐类,具有使胶粒脱稳和吸附架桥作用,是水质的混凝处理中首选混凝剂。
聚合氯化铝有液体和固体产品,氧化铝的含量:固体中为43%~46%,液体中为8%~10%,与硫酸铝比较,Al2O3成分含量高、投量少、药耗省、成本低;pH值在5.0~9.0范围内均适用,投加时最低配制浓度为5%,其絮凝体致密且大、形成快、易于沉降。聚合氯化铝在投加使用中操作方便,腐蚀性较小;处理水碱度降低少,对低温低浊和污染原水的处理效果较好,在众多混凝剂中应用最为广泛和普遍。
聚合氯化铝作为一种新型无机凝聚剂,同传统硫酸铝、氯化铝等相比,有一系列的优点,它不但在各种用水和工业废水处理技术中应用日益广泛,而且在造纸、制药、制糖、精密铸造、油井防砂、混凝土、高级鞣皮和耐火硅铝纤维的黏结等方面也有研究和应用。
用煤矸石生产聚合氯化铝,有热分解、喷雾选粒和溶液干燥三种工艺。其中喷雾选粒工艺具有工艺短、质量好、易控制、整个工艺能连续化、自动化等优点。喷雾选粒工艺是将矸石与盐酸反应,得到氯化铝母液,母液通过雾化器的作用,喷洒成极细小的雾状液滴,这些液滴同载热体均匀混合,在瞬间进行热交换,使水分解时蒸发形成固体,然后在同一装置内进行热分解,得到单体,单体加水聚合产生固体聚合氯化铝。
结晶氯化铝水解也可得到聚合氯化铝。
2.2.2.1 聚合氯化铝生产的基本原理
首先用含铝矿物生产出结晶氯化铝,在一定温度下加热,分解析出一定量的氯化氢和水分,变成粉末状的碱式氯化铝,称为聚合铝单体,如把单体聚合,即可得到溶于水、凝聚效果好的固体聚合氯化铝。
反应式:
2.2.2.2 生产工艺
(1)聚合氯化铝的生产工艺
固体聚合氯化铝生产工艺流程见图2-31。将结晶氯化铝加入热解塔内,由塔底导入400~500℃的热风,经密孔板进入炉内使结晶氯化铝进行热解,沸腾段的热解温度应严格控制在170~200℃之间。分解出来的氯化氢和水分经冷水洗涤塔回收盐酸复用。得到的聚合铝单体再进行熟化聚合。聚合反应可在一个带搅拌的罐中进行。先把水加入罐内,再陆续加入单体,达到单体和水按质量比1:1.5配合。由于单体和水发生放热反应,温度可上升到60℃以上,反应约10min,料浆由淡黄色逐渐变成深褐色的稠状液体时,即放入冷凝池内,形成树脂状胶体产物,即固体聚合铝。再进一步烘干后便可长期保存。

图2-31 固体聚合氯化铝生产工艺流程
1—鼓风机;2—加热炉;3—列管式换热器;4—沸腾热解炉;5—电磁振荡;6—单体料桶;7—熟化聚合罐;8—吸收塔;9—循环洗涤水池;10—引风机;11—循环耐酸泵;12—压差计;13—热电偶
(2)影响氯化铝生产的主要因素
①加酸摩尔比、盐酸起始质量分数的影响 加酸摩尔比即反应时加入的盐酸与矸粉中氧化铝的摩尔比。加酸摩尔比、盐酸起始质量分数对氧化铝浸取率的影响如图2-32所示。从图2-32可知,盐酸起始质量分数一定,浸取率随加酸摩尔比的增加而增加。当加酸摩尔比小于1.25时,增幅较大;大于1.25时,增幅较小。加酸摩尔比一定,浸取率随盐酸起始质量分数的增大而增大。盐酸质量分数大于18%时,浸取率增加的速度减慢。

图2-32 加酸摩尔比和盐酸起始质量分数对氧化铝浸取率的影响
②矸粉投加比A对碱化度B的影响 矸粉投加比A(A=新加入的矸粉中的Al2O3质量/一次酸浸液中的Al2O3质量)对碱化度B的影响如图2-33所示。可以看出,碱化度B值随A值的增加而增加。当A小于1.5时,由于在一次酸浸液中含有过量的盐酸,随着矸粉的加入,过量的盐酸逐步被反应消耗掉,酸浸液中Al3+逐步增多,[Al(H2O)6]3+中的配位水水解机会增多,使溶液中OH-浓度增加,从而使B值增加的幅度较大。当A大于1.5时,过量的盐酸已基本反应完,酸浸液中Al3+就不会增多,因而B值趋于稳定。

图2-33 矸粉投加比A与碱化度B的关系
③聚合率与碱化度B的关系 聚合率是指PACS中聚合态铝与总铝的百分比。图2-34表明,聚合率随B的增加而增加。聚合开始时,铝是以络合离子[Al(H2O)6]3+的形式存在的。当溶液中pH值升高时,络合离子内配位水发生水解,从而引起质子迁移过程,单体间的两个OH-产生架桥而逐步缩聚为二聚体、三聚体。因此,开始时随B值增加而聚合率增大。但当聚合到一定程度时,因Al3+越来越少,聚合机会就减小,因而B值大于70%后,聚合率趋于稳定。

图2-34 聚合率与碱化度B的关系
2.2.2.3 产品质量规格
结晶氯化铝、聚合铝单体和固体聚合氯化铝的质量要求见表2-9和表2-10。
表2-9 结晶氯化铝的质量指标

表2-10 聚合铝单体和固体聚合氯化铝质量指标

2.2.3 煤矸石生产氢氧化铝和氧化铝
2.2.3.1 氢氧化铝和氧化铝的用途
氢氧化铝[Al(OH)3],又称水合氧化铝,为白色单斜晶体,相对密度2.42,不溶于水;氧化铝为白色晶体,熔点2050℃,沸点980℃。氧化铝及水合氧化铝是冶金炼铝的重要基本原料。冶金级氧化铝(熔盐电解生产金属铝)应符合行业标准YS/T 274—2006要求。化学成分见表2-11。
表2-11 Al2O3化学成分行业标准

氢氧化铝为含铝矿物制取氧化铝的中间产物,它本身也是一种商品。水合氧化铝加热至260℃以上时脱水吸热,具有良好的消烟阻燃性能,可广泛用于环氧聚氯乙烯、制备橡胶制品的无烟阻燃剂。高纯超细α-Al2O3具有特殊优良的物理、化学性能,在精细陶瓷、微电子集成电路、轻工纺织等行业亦有很高的应用价值。我国非冶炼行业用(多用途)氢氧化铝数量占炼铝用量的15%左右。“九五”期间,非冶炼用氢氧化铝的数量每年要达到45万吨左右才能满足电子、石油、化工、陶瓷、造纸、耐火材料、磨料、油墨等行业对氢氧化铝和氧化铝的需要。
世界上绝大多数氢氧化铝、氧化铝均采用铝土矿碱法生产,要求原料有较高的铝硅比。我国铝土矿主要分布在山西、河南、贵州、广西等地。如果铝土矿的铝硅比低于4.5,则采用烧结法生产,能耗高、成本高。随着铝土矿的长期开采,所生产的矿石产量及性能将无法满足日益发展的铝业要求。与此同时,我国煤系地层中的共生高岭岩(土)资源丰富,现已探明的储量为16.73亿吨,远景储量为55.29亿吨,以高铝矸石为原料制取多用途氢氧化铝,不仅可以扩展煤矸石的综合利用途径,也可为铝业生产开拓一种取之不尽、用之不竭的矿物资源[31]。
2.2.3.2 氢氧化铝生产的基本原理及工艺流程
(1)生产氢氧化铝的工艺流程
高铝矸石生产氢氧化铝和氧化铝的工艺流程如图2-35所示。

图2-35 高铝矸石制取多用途氢氧化铝工艺流程
(2)氢氧化铝的生产原理
氢氧化铝和氧化铝生产过程中各主要环节及发生的化学反应如下。
①烧结 对铝矿物进行烧结的目的在于使矸石中的Al2O3成为可溶于纯碱溶液的化合物,而使铝与硅、铁等杂质分离。由于高铝矸石含铝较低而含硅高(铝硅比<1),只能采用石灰烧结法。
在石灰烧结过程中发生的主要化学反应如下:
CaCO3=CaO+CO2
3(Al2O3·2SiO2)=3Al2O3·2SiO2+4SiO2
SiO2+2CaO=(2CaO·SiO2)(C2S)
3Al2O3·2SiO2+7CaO=3(CaO·Al2O3)+2(2CaO·SiO2)(CA)
7(3Al2O3·2SiO2)+64CaO=14(2CaO·SiO2)+3(12CaO·7Al2O3)(C12A7)
2CaO+Fe2O3=2CaO·Fe2O3(C2F)
CaO+TiO2=CaO·TiO2(CT)
上述反应的结果,生成了可被碱液分解出铝酸钠的铝酸钙(C12A7、CA)及不易与碱液反应的C2S、C2F和CT等。
②浸出 浸出的目的在于通过用纯碱溶液处理烧结熟料,使其中的铝化合物以铝酸钠形态进入溶液而与绝大部分杂质分离。
在浸出过程中发生的主要反应有:
第一个反应是生产的主反应,余下的几个反应称为副反应(二次连串副反应)。副反应的发生,导致Al2O3和碱的损失。
③脱硅 碱浸液除含有铝、钠等元素外,还含有硅等杂质。当用此种溶液制取阻燃剂氢氧化铝时,必须加以净化才能制得合格产品。碱浸液含SiO2约1g·L-1,可采用加石灰常压除硅。
除硅过程中发生的主要反应为:
④碳分 碳分过程发生的主要反应有:
当溶液含硅较高时,还有下列反应发生:
在碳分后期,当NaAl(OH)4浓度不高时,有下列反应进行:
2NaAl(OH)4+2CO2+aq=Na2O·Al2O3·2CO2·nH2O+aq
在生产过程中,可以通过控制碳分工艺条件(CO2浓度、碳分温度、原液的Al2O3浓度、碳分率和碳分速度等)及洗涤来实现对产物质量的控制[28]。
2.2.3.3 氧化铝的生产
(1)生产原理与工艺
高铝煤矸石经煅烧,所含的高岭土活化,其中的Al2O3再经酸溶、水解、碱溶、碳化及焙烧,就可得到纯净的Al2O3。
生产过程中发生的主要反应有
酸溶:Al2O3+6HCl=2AlCl3+3H2O
水解:2AlCl3+6H2O+3CaCO3=2Al(OH)3↓+3CaCl2+3CO2↑+3H2O
2FeCl3+6H2O+3CaCO3=2Fe(OH)3↓+3CaCl2+3CO2↑+3H2O
碱溶:Al(OH)3+NaOH=NaAlO2+2H2O
碳化:2NaAlO2+CO2+3H2O=2Al(OH)3↓+Na2CO3
焙烧:2Al(OH)3=3Al2O3+3H2O
以煤矸石为原料生产氧化铝的工艺流程如图2-36所示。

图2-36 煤矸石生产氧化铝的工艺流程
(2)影响氧化铝生产的主要因素
①酸浸条件 煤矸石粒度通过100~120目筛,焙烧时温度控制在(700±50)℃,焙烧时间1h。盐酸浓度为20%,酸浸温度为100℃,酸浸时间为1.5h,固液比为1:3.5,Al2O3溶出率可达85%以上。
②水解温度影响 碳酸钙作为AlCl3和FeCl3的水解促进剂,其反应机理为:
CaCO3+2H+=Ca2++H2O+CO2↑
该反应在室温下能够顺利进行,反应60min后FeCl3的水解率达91.3%,AlCl3的水解率达87.7%,并且在80℃以前随着水解温度升高,水解率也随之增大(见图2-37)。固液比为1:10;反应时间60min。

图2-37 Al(OH)3和Fe(OH)3转化率与反应温度之间关系
③碳酸钙用量的影响 从图2-38可以看出,当反应温度为60℃时,固液比为1:10,碳酸钙过量100%(按化学反应方程式计量)。反应时间为60min后,它们已达到足够高的转化率,若再增加碳酸钙用量显然是不合理的。

图2-38 Al(OH)3和Fe(OH)3转化率与CaCO3过量系数之间关系
固液比1:10,反应时间60min,反应温度60℃
④反应时间的影响 从图2-39可以看出,在反应温度为60℃,固液比为1:10,碳酸钙过量100%的条件下,反应时间为80~100min,氢氧化铝和氢氧化铁转化率为最大。

图2-39 Al(OH)3和Fe(OH)3转化率与反应时间之间的关系
固液比1:10,反应温度60℃,CaCO3过量100%
⑤固液比的影响 溶液中的水不仅作为溶剂,而且还参与Fe3+和Al3+的水解反应而生成Fe(OH)3和Al(OH)3,因此将随着固液比的降低,FeCl3和AlCl3的水解率大为提高(图2-40)。当固液比为1:1时,Al(OH)3=85.5%,Fe(OH)3=80%,而当固液比为1:10时,Fe(OH)3=100%,Al(OH)3=98.2%[29]。

图2-40 Al(OH)3和Fe(OH)3转化率与固液比之间的关系
反应时间80min,反应温度60℃
2.2.3.4 生产氢氧化铝和氧化铝的新工艺
(1)生产氢氧化铝和氧化铝新工艺的工艺流程
从煤矸石中制备Al2O3及Al(OH)3产品的研究一直是煤矸石化工利用的一个热点。从煤矸石中提取氧化铝并用残渣直接煅烧硅酸盐水泥熟料,同时作废气、废液循环利用是煤矸石高附加值、低污染资源化综合利用的新工艺。在这一工艺过程中,氧化铝提取是至关重要的步骤。既要通过粉料制备、烧结和浸取工序,完成一系列的物理、化学变化,尽可能多地提取煤矸石中的氧化铝,又要使得残渣具有合适的化学和矿物组成,以实现其直接利用。
工艺流程如图2-41所示。

图2-41 生产氢氧化铝和氧化铝新工艺的工艺流程
(2)新工艺的主要影响因素及控制
对影响氧化铝提取过程的诸多因素进行研究和分析,寻求合理的工艺配方和工艺条件,是提高煤矸石中氧化铝的提取率的关键。
①反应原料的配料 煤矸石-石灰石-纯碱混合粒化物料烧结过程的目的是使煤矸石中的Al2O3与纯碱中的Na2O结合,生成易溶于水的铝酸钠。考虑到提取氧化铝的残渣中保留适量的Al2O3,故物料中Al2O3与Na2O的分子比可采用1:1,并由此确定煤矸石与纯碱之间的配比。
物料中CaO与SiO2的分子比(钙硅比),对煤矸石-石灰石-纯碱烧结过程中的固相反应,特别是对铝酸钠的生成反应影响较大。图2-42描述了维持Al2O3与Na2O分子比为1时,混合物料在1000℃下烧结80min后,氧化铝的提取率随CaO与SiO2分子比变化而变化的情况。当钙硅分子比较小,烧结过程中只有少量的SiO2与CaO生成2CaO·SiO2,大量游离的SiO2一方面阻碍煤矸石中高岭石的分解,另一方面也可能消耗一部分Na2O并生成Na2SiO3,从而影响铝酸钠的生成,使Al2O3的提取率降低。随着钙硅分子比的增大,氧化铝的提取率提高,当钙硅分子比约为2时,提取率达到最大值,这显然与烧结物料中物质的结合状态有关。

图2-42 氧化铝提取率随钙硅比的变化关系
进一步提高钙硅分子比虽然能使烧结物料中的2CaO·SiO2含量达到最大值,但同时也将使游离的CaO含量增加,从而促进CaO与Al2O3之间的反应,生成更多的CaO·Al2O3,消耗掉一部分Al2O3,使氧化铝的提取率明显下降。所以烧结物料配方的钙硅分子比以2为适宜。
②物料粒径 物料的比表面积与粒径大小和级配有关。对粉料颗粒群的粒径描述方法有很多,其中在筛分分析的基础上计算颗粒群的体积平均粒径DV,是一种较为常见的粉料粒径表示形式。
图2-43为烧结时间80min和烧结温度1000℃不变的条件下,煤矸石、石灰石粉料体积平均粒径与物料烧结后氧化铝提取率之间的关系。可以看到,随着物料颗粒体积平均粒径的增大,煤矸石中氧化铝的提取率下降。物料的体积平均粒径越小,则其比表面积越大,烧结过程中固相反应的接触界面增大,反应的完全程度增加,因而氧化铝的提取率增大。此外,物料的体积平均粒径降低后,反应物Na2CO3在固相反应过程中扩散迁移的距离缩短,也使得烧结过程的固相反应加快,有利于提高氧化铝的提取率。

图2-43 粉料体积平均粒径与氧化铝提取率的关系
物料的体积平均粒径下降,加速烧结过程固相反应另一个不容忽视的原因是,物料在机械加工过程中增大了颗粒的表面能,同时也造成了煤矸石、石灰石等物料颗粒晶格或内部结构的缺陷,不仅增大了颗粒表面与其他物质的反应倾向和反应速率,而且也提高了晶体本身的反应活性,降低了固相反应的开始温度。
由图2-43可知,要使氧化铝的提取率在80%~85%之间,煤矸石、石灰石粉料的体积平均粒径应在0.06~0.07mm(即200~270目)范围内。
③烧结温度及时间 烧结温度的变化对煤矸石中氧化铝提取率的影响十分明显。从图2-44中可见,固定烧结时间为80min时,煤矸石中氧化铝的提取率随烧结温度的升高呈上升状态,并在大约1040℃温度下达到极大值。这是因为烧结温度升高,煤矸石中高岭石的分解趋向完全、铝酸钠的生成反应加快,氧化铝的提取率增大。但当烧结温度超过1040℃时,由于煤矸石中部分Al2O3与石灰石分解产生的CaO生成难溶的铝酸钙(CaO·Al2O3)数量增大,使得氧化铝的提取率反而呈下降趋势。

图2-44 烧结温度与氧化铝提取率的关系
保持烧结温度为1040℃不变,测定不同烧结时间下煤矸石中氧化铝的提取率,得到图2-45所示的关系曲线。当烧结时间较短时,随着烧结时间的延长,煤矸石中的高岭石分解趋向完全,铝酸钠的生成量也逐渐增多,因而氧化铝的提取率不断上升。经过一定的烧结时间(约80min)后,氧化铝的提取率随时间变化十分缓慢。这说明烧结过程的各种固相反应已经基本完成,铝酸钠的生成量不再增加,延长烧结时间只是使烧结过程中的一些新生矿物的晶体长大,而不能提高氧化铝的提取率。

图2-45 烧结时间与氧化铝提取率的关系
值得指出的是,以水溶液的形式向物料中引入纯碱,不但提高了纯碱分散的均匀性,而且对烧结过程的固相反应有着重要的促进作用。因为,煤矸石中的高岭石分解并与Na2CO3反应生成铝酸钠,这一反应是在基本没有液相参与的情况下进行的,因而反应的速度和完全程度取决于反应物Na2CO3在固相中的传质扩散迁移。以水溶液的形式引入Na2CO3,煤矸石颗粒被Na2CO3溶液润湿并均匀包裹,且溶液还能沿着煤矸石颗粒本身的毛细孔、相界面及内部缺陷进一步渗透到其内部,水分蒸发后,Na2CO3便均匀分布于粉体中,使得其扩散传质的距离缩短,速度加快,从而加速了烧结过程的固相反应,有利于提高氧化铝的提取率[18]。