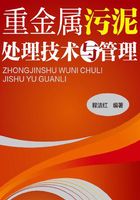
2.2 固化法制作建筑材料技术
将有害的重金属通过化学、物理方法包裹在固化体中,从而不再对环境造成污染,就是固化法。利用电镀污泥为原料或辅料生产建筑材料,也属于固化法。生产的建筑材料产品就是固化体。这些建筑材料产品包括用电镀污泥制作砖瓦、陶瓷、水泥等。近年来,随着经济发展,我国对建筑材料的需求量日益增大,导致砖瓦、水泥等行业对黏土都有大量的需求。随着黏土资源的大量开采,农田的数量和质量已受到严重影响。因此,利用污泥代替黏土生产建筑材料,在烧制过程中将有害物质去除或包裹在固化体中不能浸出,不仅能解决污泥带来的二次污染问题,而且能减少土地资源消耗,缓解建筑材料工业对黏土的大量需求,缓解我国人均耕地面积少,破坏大量土地资源的问题。特别是在目前国家加大了保护农村耕地的力度,限制黏土砖的生产使用的现状下,利用污泥建材化具有广阔的应用市场。这是污泥处理处置可持续发展的最佳方式,也是污泥处理较理想的出路之一。
2.2.1 电镀污泥制砖
制砖是真正大量消纳污泥并进行污泥综合利用的有效方法之一,也是将重金属污泥中有害物质固化在砖石中。经过多年探索证明,只要掌握适当的工艺条件,由电镀污泥烧出的砖不会造成二次污染,所有重金属可以固化在砖石中。这些重金属在一般的天然水、自来水中基本不溶出。利用重金属污泥可制造建筑用砖。由于重金属污泥中含有各种重金属离子,在高温下会呈现不同的颜色变化,因此还可以用于制造彩色陶瓷砖。如含锌污泥就可经干燥焙烧处理形成氧化锌和氧化铁。可代替彩色瓷砖釉的主要原料氧化锌,其表面光泽和釉层质量均符合标准,可制成黄色釉和棕红色釉,可用于制造当前大量使用的彩色陶瓷砖。
2.2.1.1 普通烧结制砖的原理
烧结砖制备工艺有干法制备和湿法制备之分。通常以制备物料的含水率为分界线,物料含水率在12%(干基)以下时,称为干法制备。大于这一值时称为湿法制备。污泥制砖工艺主要分为三个阶段:砖坯成型、自然干燥和高温焙烧。
烧结砖的砖坯成型工艺有塑性成型和半干压成型之分。塑性成型是使可塑状态的泥料在外力作用下成为一定形状、尺寸、密度和必需强度的湿坯成型方法。塑性成型时,成坯含水率决定了砖坯成型的优劣,成坯含水率通常为12%~30%(干基)。半干压成型是指采用含水率低于10%的潮湿粉料,在较高压力(700~1500MPa)下压制成型坯的方法。半干压成型结构致密、规格准确,但对原料的颗粒级配和含水率要求严格,需要庞大的制备和黏土或页岩干燥设备,成本较高。
干燥工艺按干燥方式可分为自然干燥和人工干燥。主要是脱除砖坯中的自由水以达到临界含水率,干燥后砖坯的含水率越大,干燥线收缩率越大,严重影响砖的尺寸,一般干燥线收缩率控制在3%以内。按干燥时间长短可分为慢速干燥和快速干燥。按干燥介质的操作时间可分为节律干燥和连续干燥,按干燥介质的流动方式可分为逆流干燥、同流干燥或混流干燥。在砖的实际生产中一般采用轮窑或隧道窑的余热人工干燥砖坯。
焙烧工艺也可以按燃料来源、操作方式、焙烧气氛等分为内燃焙烧及外燃焙烧等不同工艺。黏土砖坯在加热到一定温度后开始收缩。在450~850℃之间,黏土矿物质脱去结晶水,有机物逐渐氧化燃烧并完全分解。在继续升温至900~950℃的过程中,黏土中的杂质与黏土矿物质形成易熔物质,出现玻璃态液相,填塞于未熔颗粒孔隙中,液相表面张力的作用使未熔颗粒紧密黏结,从而使坯体孔隙率下降、体积收缩,强度也相应增大,最后变得密实。高温焙烧是烧结砖的最重要阶段,砖体因排出结合水而产生微小的线收缩率,烧结线收缩率应小于1%,否则砖体会产生裂纹;由于污泥有机物的燃烧,烧失量会随着污泥掺加量的增加而增大,烧失量应控制在50%以内,较大的烧失量会影响砖体的力学性能。
当焙烧窑中为氧化气氛时,黏土中所含铁的低价氧化物被氧化,生成红色的高价氧化铁(Fe2O3),烧得的砖颜色呈红色,若窑内为还原气氛,高价的氧化铁还原为青灰色的低价氧化铁(FeO),即得到青砖。
制砖工业中砖块的主要原料为黏土。国外有研究者曾对污泥灰与黏土的化学成分进行了比较,结果见表2-1。
表2-1 污泥灰与黏土的成分比较

从表2-1中可知,污泥灰和黏土的主要成分均为SiO2,这一特性成为污泥可作为制砖材料的基础。另外,污泥灰中除了Fe2O3和P2O5含量远高于黏土,而且重金属含量明显高于黏土,其他成分都比较接近,这说明使用污泥制砖是可行的。
2.2.1.2 重金属污泥制砖工艺
用污泥制普通砖主要采用的方法有两类:一是用干污泥直接制砖;二是用污泥焚烧灰渣制砖。用干污泥直接制砖时,需对污泥进行预处理,使其成分与制砖黏土的化学成分相当。先投加化学药剂进行反应使重金属稳定,使重金属发生形态转化转变为无害物质,对其进行去除处理,同时进行破胶处理(防止污泥胶结,影响后续脱水),再进行重力式真空分离产生污泥颗粒,这样可作为生产用的制砖原料。由于重金属污泥中有机成分含量低,对烧制工序有利,因此只要稳定化重金属,可以加大污泥掺和比。日本、美国以及欧洲国家等污泥大多采用焚烧处理方法,焚烧灰较多,因此多采用污泥焚烧灰渣制砖,这也是国外研究的热点,研究发现,焚烧灰渣与黏土化学成分接近,比较适于制砖。采用焚烧灰或者干污泥制砖的工艺流程基本相同,分别如图2-2和图2-3所示。

图2-2 污泥焚烧灰制砖工艺流程

图2-3 干污泥制砖工艺流程
由图2-2和图2-3可知,两种制砖的工艺流程基本相同。使用污泥灰作为添加剂或者完全替代黏土的技术可行性已被证实,在美国、新加坡、英国、德国和其他一些国家都有应用实例。用干污泥直接制砖时,应对污泥的成分进行适当的调整,使其成分与制砖黏土的化学成分相当。用干污泥制砖相对于污泥焚烧灰制砖成本要低,只需将污泥干燥粉碎即可直接混入制砖原料进行生产。
在污泥制砖生产过程中,为了获得成型性能良好的坯料,除了选择适当的单一黏土外,还可以选择几种性能不同的原料进行合理混配,以达到就地取材、减少生产成本和运输成本的目的。因地制宜地采用各种原材料来制备污泥砖是国内污泥建材化制砖行业发展的新方向,这些原材料除重金属污泥外,还包括粉煤灰、煤矸石、河道淤泥、工业废渣、生活污泥等,作为添加剂的材料主要有泥砾土、黄土及砂等。烧结工艺中,原料配比、烧结温度、保温时间和冷却方式是主要的工艺条件,应根据原料的性质和成分,经试验确定。
2.2.1.3 重金属污泥制砖实例
(1)重金属污泥直接制砖
① 制青砖 石灰中和法所产生的以铬为主的污泥与黏土、红陵土混合制成砖坯(污泥20%,黏土40%,红陵土40%),经自然风干,在40~180℃下焙烘,最后于950℃下烧结成砖。对成品砖进行机械强度和浸出试验,结果发现,机械强度比普通标准砖好,但浸出液中发现有六价铬的存在。在国内研究者将电镀污泥与黏土按15%~30%制红砖,20%~40%制青砖,并且对样品进行浸出试验。结果表明,在不同pH值条件下,红砖溶出Cr6+较多,而青砖溶出Cr6+极少,而且温度对Cr6+的溶出无影响,表明在采用合适的配比的条件下,青砖是安全可行的。这主要是烧红砖时用单一的氧化火焰,污泥中的三价铬有部分会被氧化成六价铬。如果烧制的是青砖,开始用氧化火焰,最后用还原火焰,窑内充满CO,而且用水冷却时,水因高温蒸发并与CO反应生成含H2、CH4的水煤气,这样CO、H2、CH4等还原气氛阻止三价铬的氧化,使铬以Cr2O3形式固定在砖块中,因此烧制的青砖浸出试验很少发现六价铬。因此采用较小的污泥掺入比、用机制法制取青砖,是能制出对铬固化效果好且符合质量要求的青砖。
对含铬重金属污泥进行手工制砖试验。重金属污泥中含铬约3%,以污泥含量为15%、20%、30%制红砖和20%、30%、40%制青砖,结果如下。
a.制成的红砖及其碎块在pH值为1、3、5、7、9的水中浸泡,六价铬的溶出量很大。
b.制成的青砖及其碎块在pH值为1、3、5、7的水中浸泡,铬的溶出量极小,检不出;在0.5mol/L硫酸中浸泡,三价铬有微量浸出。温度对青砖中铬的溶出量影响极小。
c.当污泥掺和量大于20%时,手工砖的强度达不到要求。
② 煤渣砖 含多种重金属的污泥可与煤渣混合制煤渣砖,在掺入量适宜和蒸汽养护的条件下,效果良好。重金属在砖中能稳定地固化,从而有效地防止重金属离子的二次污染。上海轻工业研究所与多家单位合作,进行了利用电镀污泥烧制煤渣砖的研究,结果表明,在煤渣蒸养法制砖的过程中,原料中掺入具有一定含水量的电镀污泥,可使重金属固定在煤渣砖中,砖的性能完全符合建材标准,是一种可靠的固化方法。而且电镀污泥不需要烘干、粉碎、过筛等预处理,甚至可直接利用不经脱水的电镀污泥,工序简单经济,容易推广应用。直接用电镀污泥和煤渣混合制成煤渣砖,其配比为:煤渣75%,电镀污泥15%,石灰8%,磷石膏2%(见图2-4)。煤渣砖的原料呈碱性,电镀混合污泥中的重金属大多以氢氧化物形式存在,因此这些重金属污泥在砖中可以稳定固化。

图2-4 电镀污泥制煤渣砖工艺流程
掺入电镀污泥的煤渣砖采用中性水、pH=2.3的酸性水、pH=11.8的碱性水进行浸出试验,结果表明,铜、镍、铬、铁、锌、铅和镉等重金属的浸出浓度符合国家工业废水排放标准,重金属的溶出率很低,约为十万分之一。
采用下述配方制备的煤渣砖的强度可达200号砖标准。
按下述配方配料:
生石灰8%~12%,石膏1%~3%,煤渣85%,电镀污泥3%。
其工艺流程如下。
a.混合配料后加水,用轮碾机破碎。
b.进行陈化处理。
c.用八孔制砖机制砖。
d.送入蒸汽窑中通蒸汽养护。
e.冷却后即得成品。
(2)焚烧灰渣制砖 另外,也可用重金属污泥的焚烧灰制砖。利用污泥焚烧灰渣制砖时,灰渣的化学成分与制砖黏土的比较接近。因此可以通过两种途径实现烧结砖制造:其一为与黏土等掺和料混合烧砖;其二为不加掺和料单独烧砖。
污泥焚烧灰制造非建筑承重用的地砖,是一种基本利用焚烧灰单一原料的污泥建材利用方法,该法无须掺和大量黏土,因此有符合相关建材技术政策的优势,但其工艺与一般黏土砖制作工艺有很大的差异。
其主要工艺如下。
① 原料 原料为污泥焚烧灰。原料特性对烧制质量的主要影响因素有以下三点。
a.灰渣的平均粒径。灰渣粒径应小于30μm,否则成品会出现丝状裂痕,流化床污泥焚烧炉的灰渣要好于炉排炉。
b.灰渣残余有机物质和水分的含量。灰渣中残余有机物质和水分的含量均控制在10%以下为宜,而据日本研究者报道,灰渣此两项成分的含量均控制在1%左右,以避免由原料有机物质和水分引起的成品开裂现象。
c.严格控制灰渣的CaO含量。灰渣中CaO含量应小于15%,如果含量过高,会使烧制成品出现丝状裂痕,影响产品质量,因此,污泥前处理时不宜采用石灰作为脱水调节剂。
② 制坯 制坯方法对成品质量有明显影响,因此,制坯要采用细灰注模、冲压成型的工艺,核心的质量控制参数是坯体密度和保证坯体内无空气。控制的方法如下:灰的平均粒径控制在20μm左右,冲头压强为100MPa,坯体密度为1.6g/cm3,模具内应施加26kPa的真空度,以保证坯体内空气可顺利释放。
用重金属污泥制砖的种类和工艺主要有三种。
a.重金属污泥和黏土等材料混合后高温烧结,制备烧结青砖效果最好,因青砖的浸出毒性低。
b.重金属污泥和煤渣等材料混合后可制得煤渣砖。
c.污泥灰和水泥等材料混合后制备免烧砖。
另外,重金属污泥和水泥等材料混合后制备免烧砖。利用污泥制备烧结砖的主要优点为:烧结之后,可以将污泥中的重金属固定;污泥烧失量大,烧结后砖体呈多孔结构,隔热、隔声,透气性好,砖体较轻。其缺点是污泥和粉煤灰都属于瘠料,难以单独混合成型。在污泥掺量不太高,加入大量黏土的情况下,才有可能达到有效成型,但黏土消耗多,造成黏土资源紧缺。
2.2.1.4 成品砖的质量检测
(1)抗压强度 抗压强度是衡量制砖性能的最为重要的指标之一,是污泥资源化制砖的决定性指标,是污泥建材极为重要的性质。砖样由污泥和黏土以及其他原料以不同质量分数经拌和、陈化、制坯、干燥、烧结而成,其强度主要受到污泥掺量、烧结温度的影响。另外,制砖的抗压强度对重金属的溶出率有很大的影响,抗压强度高,固化效果好,重金属的浸出率就相对较低。制砖的抗压强度主要依赖于污泥的含量。按照《烧结普通砖》(GB/T 5101—1998)的标准,红砖的抗压强度为10MPa。可采用《水泥胶砂强度检验方法》(GB/T 17671—1999)测试固化砖块抗压强度。
(2)浸出要求 成品砖是将重金属污泥中的重金属包埋在砖体中,在使用过程中,其中的重金属不能浸出。因此需将成品砖做浸出试验,其浸出液中的重金属含量必须符合《危险废物鉴别标准 浸出毒性鉴别》(GB 5085.3—1996)标准。
2.2.2 电镀污泥制陶粒
陶粒,作为一种建筑用轻骨料,具有较小的密度和较高的强度以及高比表面积,广泛应用在建筑材料、农业园艺、水处理等方面。陶粒的化学成分中要求SiO2、Al2O3的含量要高,最开始陶粒种类主要就是黏土陶粒、粉煤灰陶粒和页岩陶粒三种,都是用黏土、页岩等比较特定的几种原料资源,而目前这些天然资源储量逐年减少,质量也在不断下降,因此,以工业污泥为主料,通过加入一定量的添加剂、黏结剂制备陶粒的研究越来越受到重视。
(1)陶粒的性质 通常来说,陶粒本身具有的特殊结构,主要体现在陶粒的表层和内部,而且这个结构可以通过控制制备工艺参数进行调整,进而获得所需要的性能。由于这个原因,其自身具有一些优良的特性。
① 轻质 相对致密的壳层结构和疏松多孔的内部结构,使得陶粒的堆积密度一般小于1100kg/m3,特轻型陶粒的堆积密度更是小于300kg/m3。有研究表明,某标号普通混凝土密度为2600kg/m3,而同标号的粉煤灰陶粒混凝土的密度只有1600kg/m3。
② 保温、隔声 陶粒内部发达的孔结构决定了其具有良好的保温和隔声性能,通常用陶粒配制的混凝土热导率只有普通混凝土的1/3~1/2。
③ 吸水率可调 通过控制烧成工艺,可以制得表层具有致密釉质层的陶粒,阻碍了水分渗入的途径,使得陶粒具有较低的吸水率,也可以控制制备工艺条件,制得表面多孔的陶粒,这种陶粒就具有优异的蓄水性能,可以用于园艺方面。
(2)陶粒的应用 陶粒以其优异的性能以及种类的多样性,广泛地应用于如下几个方面。
① 建材方面的应用 这是陶粒使用量最大的应用方向,陶粒具备轻质、高强、隔声、保温、高耐火性和较低的吸水率,适合建材所要求,这样保证了制品具有优异的抗震性、耐火性、抗冻性、抗渗性以及抗碱集料反应的能力,因此陶粒在各类型的工业与民用建筑,如大厦、墙材、桥梁等方面有广泛应用。
② 工业方面的应用 由于烧胀型陶粒具有丰富的孔结构,能有效地吸声和保温,已经被广泛应用于保温吸声材料。陶粒具有的高比表面积,一般可作为路基材料、混凝土骨料或花卉覆盖料使用。
③ 水处理方面的应用 在水处理方面,陶粒作为过滤材料也得到了广泛的应用。如日本将其作为污水处理厂快速滤池的滤料,以代替目前常用的硅砂、无烟煤,取得了良好的效果。轻质陶粒作为快速滤池调料时,孔隙率大,不易堵塞,反冲洗次数少。因其相对密度较大,反冲洗时流失量少,滤料补充量和更换次数也比用普通滤料少。具有高开口率的烧胀型陶粒由于比表面积非常高,对污水的进化效率高,同时具有成本低、易清洗、可多次使用、生命周期长的特点,近来用陶粒作为生物脱臭反应器调料的研究较多,陶粒上挂的生物膜具有较高的微生物浓度,系统单位体积的处理能力大,耐冲击负荷能力强,是一种有发展前途的材料。
④ 园艺园林方面的应用 由于开口型烧胀陶粒质轻并具有良好的吸水保水性,可用于无土栽培,彩色的陶粒目前也开始应用于园林地面装饰方面。对于轻集料混凝土来说,可以选用不同类型的陶粒,配制后得到不同性能的混凝土。主要作为承重结构的混凝土都需要高性能的陶粒,这类陶粒的市场需求量大,有利于陶粒的消纳。
2.2.2.1 制备陶粒的原理
按照生产工艺来分,陶粒可分为免烧型和焙烧型两类。免烧型陶粒是利用水泥等物质作为胶结料,配以活性固体废弃物,经造粒、养护而成。这种陶粒不经过焙烧,一般来说其强度、密度、表面光洁度以及吸水率等物理性能指标均明显要比焙烧型陶粒差一些。焙烧型陶粒都要经过一个煅烧的过程,在此过程中,为了使陶粒烧胀或者致密,生料都会经过一个超过1000℃高温处理阶段。在高温条件下,原料中的有机物质和挥发分就会比较彻底地燃烧掉,形成CO2等物质散发到空气中,同时高温下形成的部分液相在冷却过程中会形成新的结晶或玻璃态,这个过程可将残留的无机有毒离子成分包裹在陶粒内部,形成比较稳定的结构,从而大大降低了重金属污泥中的有毒有害重金属的溶出量及溶出速率,减小了其对环境和人体的危害。
对于焙烧型,可根据其是否发生体积膨胀分为两种:烧胀型陶粒和烧结型陶粒。烧胀型陶粒由于体积膨胀,内部有许多封闭的孔结构,因而具有较小的堆积密度和很好的保温隔热特性,但其对原料种类和煅烧制度要求都相对较高。以目前我国的现状,烧结型陶粒主要是以粉煤灰或其他废弃物作为主要原料,配入一定的胶结料,经过造粒、焙烧而成的人造轻集料。通常内部不会发生较大的体积膨胀,孔结构较少,结构较致密,具有较光滑的表面形貌。
烧胀型陶粒和烧结型陶粒的主要区别就在于能否在高温时形成稳定的足够量的气体,同时出现液相,而且液相黏度正好适中,把生成的气体包裹在陶粒内部,使气体不至于逸出或生成量/逸出量平衡,这两个条件同时作用,使陶粒体积发生膨胀,最终形成多孔且孔隙分布均匀的内部结构。由此可见,陶粒若能焙烧膨胀必须同时具备两个条件:①高温下坯体能形成具有一定黏度的液相;②适宜的液相
黏度下,产生足够的气体。如果形成的液相黏度过大或者没有液相,成气成分形成的气体会在陶粒内部积聚,或者沿着陶粒内部的缝隙缺陷逸出,要不就会导致气孔内部气压增大,在一定程度上,会使陶粒爆裂;如果形成的液相黏度太小,就会导致形成的气体容易逸出,使气孔消失,不能形成有效的膨胀,而且还会导致陶粒间相互粘连,工业生产中产生结块结圈的情况。而且,陶粒表面和内部的液相黏度和表面张力也不能是相同的:陶粒表面需要黏度及表面张力较大,能有效包裹气体,并且尽量降低陶粒之间的粘连;陶粒内部黏度要相对较小,使生成的气体容易膨胀,形成气孔,并且分布均匀。
导致陶粒膨胀的主要因素主要有三种:一是成陶成分,如SiO2、Al2O3、Fe2O3;二是助熔剂,如Na2O、K2O、FeO等;三是气体物,如H2O、O2、CO2等。在不添加助胀剂的情况下,原料的化学成分如能控制在表2-2范围内,多数料球都能烧胀。
表2-2 制陶粒的原料化学成分

有研究表明,在Fe/C发泡体系中,陶粒内部是还原气氛,Fe2O3会被还原成FeO,表面上FeO在炉膛内的氧化气氛下,形成Fe2O3,其中,FeO是一种较好的熔剂型氧化物,能有效降低液相黏度,Fe2O3相对难熔,软化黏度较高。这两种氧化物的相互转化,正好符合以上的要求。发气成分不断地生成气体,液相又具有合适的黏度,这两个膨胀的条件同时具备,即大量生成的气体不断逸出的趋势与液相在比较大的表面张力作用下对气体逸出的阻碍同时作用,就使得体积膨胀的过程得以成功进行。
目前对于陶粒膨胀模式的观点主要有以下几种。
(1)静态膨胀模式 早期认为,熔融坯体产生的液相会有一定的黏度,在这个黏度下,发气成分产生的气体不断膨胀,但膨胀的气体压力小于液相的表面张力,陶粒得以膨胀而不破裂。这个理论的提出,初步解释了双因素作用使陶粒发生了膨胀,但是却有很大的缺陷,例如,不能解释陶粒表面开口孔的形成原因以及实际所需发气成分量远大于理论需要量。所以,根据这些实际情况,接着有人提出了第二种模式。
(2)动态膨胀模式 这种模式认为,由于实际的发气成分要远大于理论需要量,因此,在膨胀阶段,液相具有一定的黏度,气体的逸出也是不断进行着,这两个行为处于动态的平衡,从而保证了液相内部含有一定量的气体,使陶粒达到一定的膨胀率。但这也存在矛盾:气体的持续逸出会导致坯体内部出现连通孔,而且冷却后陶粒表面肯定存在大量开口孔,这两个因素会严重影响陶粒的质量。而在大多数膨胀良好的陶粒上,是不存在这两个问题的。
(3)新的膨胀模式 早期动态平衡、后期静态平衡模式,这是近些年提出的新膨胀模式。这个理论建立在前两个传统理论之上,它指出了在膨胀的早期阶段,由于出现的液相量较少,表面张力较大,内部气压较大,处于这个阶段的气体逸出量很大,使得坯体得到了较好的膨胀。随着高温阶段的持续,液相量出现得越来越多,较难熔的硅铝质开始熔融,熔融液开始变得均化,液相黏度变大。同时,经过早期较剧烈的气体逸出,此时,坯体内部气体的生成速率也变得稳定,内部气压也逐渐稳定下来,慢慢的,内部气压与液相的表面张力达到平衡,此时,液相使得坯体表面开口孔开始闭合,内部气孔细化,达到了静态膨胀阶段。最终冷却后,生产出膨胀优良的陶粒。根据以上膨胀理论和膨胀模式的分析,显然若想取得良好的膨胀,必须有合适的发气成分。目前对膨胀的研究表明,发气成分总体上分为四类:碳酸盐类(主要是CaCO3、MgCO3等)、硫化物类(主要是硫铁化物、硫等)、氧化铁类、碳类。它们在加热条件下会发生特定的化学反应生成气体的情况如下。
① 碳酸盐的分解反应
CaCO3→CaO+CO2↑(850~900℃)
MgCO3→MgO+CO2↑(400~500℃)
② 硫化物的氧化还原反应
FeS2→FeS+S↑(近900℃)
S+O2→SO2↑
4FeS2+11O2→2Fe2O3+8SO2↑[氧化气氛(1000±50)℃]
2FeS+3O2→2FeO+2SO2↑
③ 氧化铁的氧化还原反应(1000~1300℃)
2Fe2O3+C→4FeO+CO2↑
2Fe2O3+3C→4Fe+3CO2↑
Fe2O3+C→2FeO+CO↑
Fe2O3+3C→2Fe+3CO↑
④ 碳质的氧化还原反应(400~800℃)
C+O2→CO2↑
2C+O2→2CO↑(缺氧条件下)
C+CO2→2CO↑(缺氧条件下)
另外,还有研究认为火成岩矿物在高温下也能释放自身的结晶水,形成水蒸气,从而达到发气膨胀的目的。综合以上分析,烧胀陶粒的成气过程与成气成分非常复杂,在不同温度阶段会生成不同的气体。但是,在温度≤1000℃时,碳酸盐的分解已经结束,硫化物的反应也几乎结束,陶粒颗粒表面上的碳质的氧化还原反应也已经结束。因此,当温度>1000℃时,只剩下部分残留在陶粒内部的炭粒和氧化铁没有反应,正好在这个阶段,随着温度的上升,液相开始出现,陶粒表面和内部逐渐软化。当液相黏度合适的时候,由氧化铁和炭粒发生反应,在陶粒内部生成的气体,使得陶粒发生膨胀,体积变大。有人认为,是由于这个时候铁质元素和残炭发生反应,生成O2造成的,可是根据以上国内的研究可以推断,CO和CO2应该是陶粒发生膨胀的主要原因,即使在高温下生成了O2,也会重新发生反应,氧化C等物质。这个结论也经许多科研人员的试验,证实碳铁反应生成的CO是陶粒发生膨胀的主因。
2.2.2.2 陶粒制备工艺
重金属污泥制轻质陶粒工艺流程如图2-5所示。铬渣与脱水的城市污泥即干污泥一起,并且加入适当的黏土即高岭土和黑黏土,根据一定的配比,混合加水搅拌加入成型模具中,经干燥、预热、焙烧、冷却等工序后,可制得陶粒。加入的干污泥中含有大量的有机物质,燃烧热值在10000J/g左右,用于制陶粒可节省能源。

图2-5 重金属污泥制轻质陶粒工艺流程
下面对几个关键工序进行说明。
(1)干燥 为防止污泥在干燥过程中结成大块,应采用旋转干燥器,热风进口温度为800~850℃,污泥经干燥后,含水率从80%下降到5%~10%。由于干燥器内装有破碎搅拌装置,污泥块大小一般在10mm左右。干燥器的排气进入脱臭炉,干燥热源来自部分燃烧炉的排气和烧结炉的排气,不需要外界补充热源。
(2)焙烧 燃烧在理论空气比(约0.25)下进行,使污泥中的有机成分分解,大部分成为气体,一部分以固定碳的形式残留。燃烧炉内温度控制在700~750℃,燃烧的排气中含有许多未燃成分,送到排气燃烧炉再燃烧,产生的热风作为污泥干燥热源。燃烧后的污泥固定碳含量为10%~20%,热值为1256~7536kJ/m3。
(3)造粒 燃烧过的污泥中掺入少量干燥污泥,调节物料含水率至20%~30%,混合后造粒。造粒物料中必须含碳,如此烧结过程中由于燃烧产生的气体从粒子内部向外部逸出,使烧结成品形成许多小孔,质量小。
(4)烧结 烧结陶粒的强度和相对密度,与烧结温度、烧结时间和产品中残留碳含量有关。烧结温度以1000~1100℃为宜,超出此温度范围,陶粒强度降低。残留碳含量越多,强度越低,因此希望控制在0.5%~1.0%的范围内,此时陶粒强度为1.5~2.0kgf/cm2。陶粒的相对密度随烧结温度的升高而减小。在上述烧结温度范围内,其相对密度为1.6~1.9,烧结时间为2~3min。轻质陶粒的组成见表2-3。
表2-3 轻质陶粒的组成

2.2.2.3 研究现状
在海滩淤泥中掺加30%电镀污泥,并且在1200℃下可煅烧成满足工艺要求的陶粒。其中铜、锌的固化率达到100%,镍、铬的固化率与浸出液的种类有关,重金属的固化率按铜(锌)、镍、铬的顺序降低。重金属在蒸馏水或饱和Ca(OH)2溶液中的浸出浓度均满足《危险废物鉴别标准 浸出毒性鉴别》(GB 5085.3—1996)对危险废物规定的浸出液最高允许浓度值。
以电镀污泥、粉煤灰为原料,添加生活污泥和广西白泥制出了符合工艺的陶粒。因此认为适量加入广西白泥,既可以增加配料的塑性,又可以降低烧成温度,降低成本;掺生活污泥,主要是有助于气孔的形成,这对吸水率及陶粒的强度有重要影响。
此外,污泥与粉煤灰混合烧结制陶粒,每生产1m3陶粒,可处理含水80%的污泥0.24t(折成干泥0.048t),同时还可以处理粉煤灰0.72t。这不仅可大量处理污泥和粉煤灰,而且处理成本也大大低于焚烧处理,是一种优良的建材产品和处理技术。