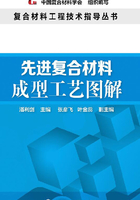
2.2 热隔膜
复合材料梁结构外形狭长、结构复杂,很难应用自动铺放技术,为了使这些大尺寸梁构件的生产也能享受自动化带来的好处,航空工业界的工程师把铺叠过程分成两个阶段:首先通过自动铺带机铺叠出正确形状及铺层的平板叠层,平板的厚度一般在1~5mm之间。然后将平板叠层转移到热隔膜成型机上,使其整体贴合模具,然后再封装固化。
图2-4为热隔膜成型原理图。在热隔膜成型过程中,平板叠层被置于两个可以自由变形的隔膜之间,隔膜被夹持在模具的边缘,首先把双隔膜之间抽成真空以便提供一个夹持平板叠层的压力,并将平板叠层和隔膜组装在真空箱上,然后在平板叠层上面进行红外加热,到达工艺温度时开始对真空箱抽真空,两隔膜之间的平板叠层受大气压力会缓慢贴合到模具表面。该成型工艺的工序类似于片状热塑性塑料的热成型过程,只是热隔膜成型的坯件是由平板叠层预浸料和隔膜共同组成的,隔膜通常是高温可变形材料,如聚酰亚胺薄膜或橡胶薄膜。在成型过程中,被夹持在真空箱边缘的隔膜处于拉伸状态,因此薄膜和平板叠层之间存在相互摩擦作用,这有助于使平板叠层保持张力,从而防止纤维在成型过程中发生屈曲和褶皱。当成型过程结束之后,制件在大气压力下冷却到预浸料软化温度以下,最后卸压并从模具上剥去隔膜取出制件。

图2-4 热隔膜成型原理图
热隔膜成型技术(Hot-diaphragm Forming)已经用于A400M的机翼梁生产。A400M的每个机翼的翼梁分成两段制造,前翼梁分成12m和7m两段,后翼梁分成14m和5m两段,构件的尺寸比较大,如果仍然采用手工铺叠,效率太低,铺叠率一般只有0.75kg/h,因此在生产中将应用铺带机进行铺叠,随后用热隔膜成型出“C”形截面梁,铺叠率能达到25kg/h。为成型出“C”形截面梁,平板叠层被送到由英国Aeroform公司提供的热隔膜成型机上成型。为了便于抽真空,平板叠层夹在两个由杜邦公司提供的卡普顿(Kapton)聚酰亚胺薄膜制成的隔膜之间,隔膜之间密封且抽真空,然后在平板叠层上面进行红外加热,直到将温度升到60℃,这样可以保证平板叠层均匀加热到同一温度,然后缓慢对两隔膜间平板叠层加压,并使其与模具贴合形成机翼梁的内表面。在30min内“C”形截面梁成型完成后,便可去除卡普顿薄膜,将“C”形截面梁转移到殷钢制成的阳膜上,最后封装进热压罐固化(图2-5)。

图2-5 热隔膜成型“C”形截面梁
传统手工铺覆异型件,当铺层厚度大于0.25m时,需要2~3天。而采用热隔膜机,可缩短梁类零件加工周期20%,降低成本30%。而且当铺层厚度大于0.25m时,采用热隔膜预成型机还可有效地减少打褶和纤维屈曲。采用预成型的另一个意义在于,通过将固化分为两步,可以有效地保证精度及合适地控制翘曲。
热隔膜成型已成功地应用于波音777长桁和V22长桁的生产,A400M的机翼前梁也用了此工艺方法生产。
A400M机翼前梁是在英国GKN公司生产的,被称为第一个用热隔膜成型的最大、最关键部件。GKN公司为此投入了140万英镑向西班牙订购了一台11轴、20m长的高速铺带机,使工时比原来手工铺层提高50倍,成本降低30%,不仅提高了质量、紧密度,还减少了无损检测时间。首先在该机上将CYTEC公司提供的预浸料铺成平的层压件,然后将该层压件移至Aeroform公司提供的热隔膜成型机上,置于两层由Dupot Electronic Technologies公司提供的Kapton Polyimide Film(一种聚酰亚胺薄膜)隔膜之间,隔膜中间抽真空,从上面开始缓慢加温(红外线加温)1h,直到温度全部达到60℃,然后再抽真空,将隔膜压紧夹住层压件,均匀压到模具上,约20min结束,保证“C”形梁的内型正确。最后取下预成型件,撕去隔膜(隔膜报废),将预成型件转移到固化工装上,装夹好,送入热压罐固化。
Accudyue公司生产专门的桁条铺带机,可成型30cm宽、11m长的层压件,铺层速度为100ft/min(30.48m/min),边缘平齐度为0.018in(0.457mm),切割精度为0.030in(0.762mm),有塔式装卸装置,可自动更换材料。
波音777和V22的长桁铺层后用热隔膜成型,克服了用老办法成型时的表面皱褶及其他缺陷。其中V22用的是正向成型法,而波音777采用的是反向成型法,即将材料置于模具下部,隔膜又置于材料下部,抽真空后通过隔膜向上将材料包向模具,补加工或需添补之处在进入热压罐前在夹具上解决。