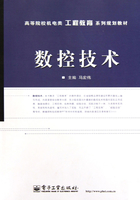
1.3 数控技术的应用与发展
1.3.1 数控技术的发展历程及趋势
从1947年美国人帕森(John C. Parson)提出用电子装置控制坐标镗床来精确制作直升机叶片样板的方案,并于1952年与麻省理工学院合作研制成功世界上第一台三坐标数控铣床开始,在电子、计算机等技术的推动下,半个多世纪以来数控技术发展迅速。在体系结构上,数控系统经历了NC(硬线数控)、CNC(计算机数控)和目前的PC-NC(PC 数控)三个阶段,如图1-7所示。从硬件角度看,数控系统经历了八代发展,NC阶段以电子管、晶体管和小规模集成电路应用为标志,经历了三代,特点是完全由硬件逻辑电路构成的专用硬件数控系统;CNC阶段是以小型计算机、微机、超大规模集成电路、32位微机应用于数控系统为标志,经历了四代;而PC-NC阶段是借助PC丰富的软硬件资源,构建基于PC的数控系统。

图1-7 数控系统的发展历程
随着先进生产技术的发展,要求现代数控机床向高速度、高精度、高可靠性、智能化、开放式和更完善的功能方向发展。
1)高速度、高精度化
数控机床高速切削和高速插补进给的目标是在保证加工精度的前提下,提高加工速度。这不仅要求数控系统的处理速度快,同时还要求数控机床具有大功率和大转矩的高速主轴、高速进给电动机、高性能的刀具和稳定的高频动态刚度。
高精度包括高进给分辨率、高定位精度和重复定位精度、高动态刚度、高性能闭环交流数字伺服驱动系统等。数控机床由于装备有新型的数控系统和伺服驱动系统,使机床的分辨率和进给速度达到0.1μm(24m/min),1μm(100~240m/min),现代数控系统已经逐步由16位CPU过渡到32位CPU。日本产的FANUCl5系统开发出64位CPU系统,能达到当最小移动单位0.1μm时,最大进给速度为100m/min。FANUCl6和FANUCl8采用简化与减少控制基本指令的RISC(Reduced Instruction Set Computer)精简指令计算机,能进行更高速度的数据处理,使一个程序段的处理时间缩短到0.5ms,连续lmm移动指令的最大进给速度可达到120m/min。
日本交流伺服电动机已装上每转可产生 100万个脉冲的内藏位置检测器,其位置检测精度可达到0.01mm/脉冲及在位置伺服驱动系统中采用前馈控制与非线性控制等方法。在补偿技术方面,除采用齿隙补偿、丝杠螺距误差补偿、刀具补偿等技术外,还开发了热补偿技术,以减小由热变形引起的加工误差。
2)开放式
要求新一代数控机床的控制系统是一种开放式、模块化的体系结构,即系统的构成要素应是模块化的,同时各模块之间的接口必须是标准化的;系统的软件、硬件构造应是“透明的”、“可移植的”;系统应具有“连续升级”的能力。
为满足现代机械加工的多样化需求,新一代数控机床机械结构更趋向于“开放式”。机床结构按模块化、系列化原则进行设计与制造,以缩短供货周期,最大限度地满足用户的工艺需求。数控机床的很多部件的质量指标不断提高,品种规格逐渐增加,机电一体化内容更加丰富,因此专门为数控机床配套的各种功能部件已完全商品化。
3)智能化
所谓智能化数控系统,是指具有拟人智能特征的数控系统。智能数控系统可通过对影响加工精度和效率的物理量进行检测、建模、提取特征,从而自动感知加工系统的内部状态及外部环境,快速地做出实现最佳目标的智能决策,对进给速度、切削深度、坐标移动、主轴转速等工艺参数进行实时控制,使机床的加工过程处于最佳状态。
在数控系统中可引进自适应控制技术。数控机床中因工件毛坯余量不匀、材料硬度不一致、刀具磨损、工件变形、润滑或冷却液等因素的变化将直接或间接影响加工效果。自适应控制是在加工过程中不断检查某些能代表加工状态的参数,如切削力、切削温度等,通过评价函数计算和最佳化处理,对主轴转速、刀具(或工作台)进给速度等切削用量参数进行校正,使数控机床能够始终在最佳的切削状态下工作。
可设置故障自诊断功能。当数控机床工作过程中出现故障时,控制系统能自动诊断,并立即采取措施排除故障,以适应长时间在无人环境下的正常运行要求。
可应用图像识别和声控技术。该技术使机床自己辨别图样,并自动地运用数控加工的智能化技术和根据人的语言声音对数控机床进行自动控制的智能化技术。
4)复合化
复合化加工指在一台机床上一次装夹便可以完成多工种、多工序的加工。通过缩短装卸刀具、装卸工件、调整机床的辅助时间,实现一机多能,从而最大限度地提高机床的开机率和利用率。
20世纪60年代初期,在一般数控机床的基础上开发了数控加工中心(MC),即自备刀库的自动换刀数控机床。在加工中心机床上,工件一次装夹后,机床的机械手可自动更换刀具,连续地对工件的各加工面进行多种工序加工。目前,加工中心的刀库容量可多达120把左右,自动换刀装置的换刀时间为l~2s。在加工中心中,除了镗铣类加工中心和车削类车削中心外,还出现了集成型车/铣加工中心、自动更换电极的电火花加工中心和带有自动更换砂轮装置的内圆磨削加工中心等。
随着数控技术的不断发展,打破了原有机械分类的工艺划分界限,出现了相互兼容、扩大工艺范围的趋势。复合加工技术不仅是加工中心、车削中心等在同类技术领域内的复合,而且正向不同类技术领域内的复合方向发展。
5)高可靠性
高可靠性的数控系统是提高数控机床可靠性的关键。选用高质量的印制电路和元器件,对元器件进行严格地筛选,建立稳定的制造工艺及产品性能测试等一整套质量保证体系。在新型的数控系统中采用大规模、超大规模集成电路实现三维高密度插装技术,进一步把典型的硬件结构集成化,制成专用芯片,提高了系统的可靠性。
现代数控机床均采用CNC系统,数控系统的硬件由多种功能模块制成,对于不同功能的模块可根据机床数控功能的需要选用,并可自行扩展,组成满意的数控系统。在CNC系统中,只要改变一下软件或控制程序,就能制成适应各类机床不同要求的数控系统。
现代数控机床都装备有各种类型的监控、检测装置,并且具有故障自动诊断与保护功能。能够对工件和刀具进行监测,当发现工件超差、刀具磨损或破裂时,能及时报警,给予补偿,或对刀具进行调换,具有故障预报和自恢复功能,以保证数控机床长期可靠地工作。数控系统一般能够对软件、硬件进行故障自诊断,能自动显示故障部位及类型,以便快速排除故障。此外,系统还具有增强保护功能,如行程范围保护功能、断电保护功能等,以避免损坏机床和报废工件。
6)多种插补功能
数控机床除具有直线插补、圆弧插补功能外,有的还具有样条插补、渐开线插补、螺旋线插补、极坐标插补、指数曲线插补和圆柱插补等。
7)友好的人机界面
现代数控机床具有丰富的显示功能,大多数系统都具有实时图形显示、PLC 梯形图显示和多窗口的其他显示功能;丰富的编程功能,像会话式自动编程功能、图形输入自动编程功能,有的还具有 CAD/CAM功能;方便的操作,有引导对话方式帮助操作者很快熟悉操作,设有自动工作手动参与功能;根据加工的要求,各系统都设了多种方便于编程的固定循环;伺服驱动系统数据和波形的显示,参数的自动设定;系统具有多种管理功能,刀具及其寿命的管理、故障记录、工作记录等;PLC程序编制方法增加,目前有梯形图编程(Ladder Language Program)方法和步进顺序流程图编程(Step Sequence Program)方法,现在越来越广泛地用C语言编写PLC程序;帮助功能,系统不但显示报警内容,而且能指出解决问题的方法。